
Методическое пособие 755
.pdf
тывать характер касания направляющих суппорта и станины и форму их изношенной поверхности по длине направляющих.
Рассмотрим для примера влияние износа направляющих строгального станка на точность обработки (рис. 126).
При обработке на строгальном станке деталей различной длины их устанавливают обычно в середине стола. Поэтому кривая распределения длин обработки является симметричной. Эпюра удельных давлений близка к прямоугольной, так как в тяжелых станках основное значение имеет вес стола и детали. Поэтому кривая изношенной поверхности направляющих имеет симметричную форму. Эта кривая по мере износа приближается к дуге окружности, так как только в этом случае возможно относительное перемещение стола по станине при условии касания сопряженных направляющих по всей длине. Определим, какие погрешности возникнут на детали при обработке ее на строгальном станке с изношенными направляющими. Если принять кривую U(x) за дугу окружности большего радиуса R, то направляющие стола будут иметь ту же форму по условию касания поверхностей.
Рис. 46. Влияние износа направляющих строгального станка на точность обработки
121

На детали вместо плоскости получается вогнутая поверхность, очерченная по дуге. Значение характеризует максимальное отклонение детали от заданной формы.
Найдем зависимость радиуса кривизны изношенной направляющей R от величины максимального износа . Как видно из схемы (рис. 126, б):
.
Учитывая малое значение угла , можно получить, что
;
и
,
где — длина направляющих станины, откуда
(19)
Аналогично можно найти зависимость между радиусом кривизны обработанной поверхности , погрешностью обработки
и длиной обрабатываемой детали
(19')
Заметим, что и
, как правило, значительно больше расстояния от направляющих до обрабатываемой поверхности h. Поэтому можно принять , и из уравнений (19) и (19') получаем
(20)
В этой формуле износ измеряется в вертикальной плоскости и в случае плоских направляющих равняется износу их поверхности U.
При применении V-образных направляющих (рис. 126, в) с углом основания их износ U связан с износом
зависимостью
Поэтому формула (20 ) принимает вид
(21)
Например, при = 0,3
,
= 45°,
= 0,5 мм получаем
= 0,064 мм.
Полученная формула (21) показывает, что точность обработки зависит от величины износа направляющих и длины обрабатываемых деталей.
Повышение износостойкости направляющих способствует длительному сохранению станком точности и виброустойчивости. На
122
практике применяют разнообразные методы повышения долговечности направляющих. Большое значение имеет правильный выбор материала направляющих (см. гл. 1, § 3), их смазка и конструктивные и эксплуатационные факторы, рассмотренные ниже.
5.6. Компенсация износа направляющих При износе направляющих возникают зазоры, которые сильно
влияют на виброустойчивость станка. Для их устранения применяют различные методы, основные из которых показаны на рис. 127.
Нерегулируемая планка 1 (рис. 127, а) требует периодической шабровки или шлифования поверхности a—b. Иногда применяют слоистые прокладки.
Регулируемые планки 2 и 3 (рис. 127, а и б), которые прикрепляются к салазкам штифтами, позволяют изменять зазор при помощи винтов. Такая конструкция имеет малую жесткость и, легко «перетянуть» планку, когда регулирование происходит на наиболее изношенных участках. Компенсация износа при помощи клиньев (рис. 127, в) имеет наибольшее применение. Уклон клиньев от 1:40 до 1:100. Недостаток конструкции — необходимость обрабатывать поверхность салазок под уклон.
Чтобы установить, где помещать регулируемые элементы, необходим анализ работы этого узла.
Для увеличения жесткости узла клин располагают обычно со стороны, противоположной действию силы. Однако смещение верхних салазок относительно нижних вызывает нарушение соосности приводного винта и гайки, изгиб винта и неравномерный износ этой пары. Для сохранения соосности винта и гайки необходимо иметь конструкцию, обеспечивающую регулирование положения винта или гайки при износе направляющих.
123
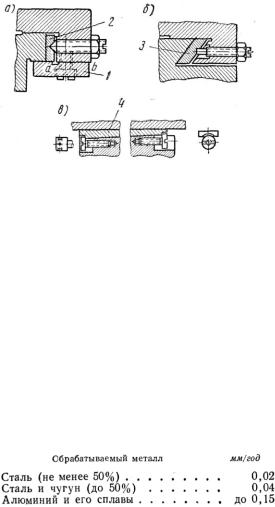
Рис. 47. Методы компенсации износа направляющих
Необходимо отметить, что полная компенсация износа возможна лишь при равномерном износе направляющих.
5.8. Рациональные условия эксплуатации направляющих
Условия эксплуатации сильно влияют на долговечность направляющих. Изоляция направляющих от попадания на них пыли из воздуха, кусочков обрабатываемого материала, абразивов оказывает сильное влияние на их износ.
Для направляющих токарных станков при легких условиях работы и наличии щитков (которые лишь частично защищают направляющие) скорость изнашивания имеет следующие наибольшие значения:
Из приведенных данных видно сильное влияние на износ обрабатываемого материала и необходимость введения более эффективных методов защиты направляющих, особенно при обработке таких материалов, как алюминий.
На рис. 48 показаны примеры защитных устройств для направляющих станков. Обычные щитки а предохраняют от попадания крупных частиц. Более совершенны щитки телескопического типа б, а для шлифовальных станков, где большое количество абразива нахо-
124

дится в воздухе, применяют щитки в виде гармоники (меха), выполненные из материи или заменителей кожи (рис. 128, в).
Иногда щитки выполняют неподвижными и вводят их в специальные пазы движущегося стола г. Применяют также эластичные стальные ленты д или специальные неметаллические ленты, которые при движении стола станка наматываются на барабан е и постоянно закрывают направляющие.
Рис. 48. Щитки для направляющих
Рис. 49. Уплотнение конструкции Кроме щитков, применяют различного рода уплотнения, не по-
зволяющие загрязнению проникать на поверхность трения.
125
Для уплотнений используют фетр, качественный войлок, маcлостойкую резину и другие материалы или их сочетание, а также выполняют различные лабиритные уплотнения.
Материал уплотнения изолирует поверхность трения от загрязнения и должен сохранять эту способность как можно дольше. На рис. 129 изображено рекомендуемое ЭНИМСом для тяжелых токарных и расточных станков уплотнение, которое применяется вместе со щитками, прикрепленными к салазкам.
Впереди уплотнения расположен скребок из бронзы 1, который предохраняет от попадания крупной стружки. Уплотнение комбинированное — из маслостойкой резины 2 и авиационного войлока 3. Скребок и уплотнение постоянно прижимаются к направляющим
пружинам 4. Давление на уплотнение 1—2 н/см2, на скребок 5—10 н/см2.
По сравнению с обычными уплотнениями из полугрубошерстного войлока это уплотнение снижает износ до двух раз.
Большое значение имеет смазка направляющих (см. § 1 этой главы) и выбор рациональных материалов для направляющих станины и суппорта (см. гл. 1, § 3).
5.4 ШПИНДЕЛЬНЫЕ УЗЛЫ СТАНКОВ 5.4.1. Шпиндели станков
1. Конструкция шпинделей и выбор типа привода на шпиндель Шпиндель — одна из наиболее ответственных деталей станка.
Он является последним звеном коробки скоростей, несущим заготовку или инструменты. От него во многом зависит точность обработки. Это заставляет предъявлять к шпинделю целый ряд дополнительных требований. Расчет и конструктивное оформление шпинделей имеют специфику по сравнению с обычными валами.
Конструкцию шпинделя определяют следующие факторы:
а) размер шпинделя, расстояние между опорами, наличие отверстия для пропуска материалов или других целей;
б) приводные детали (шестерни, шкивы) и их расположение на шпинделе;
в) тип подшипников, которые определяют посадочные места под них;
126
г) метод крепления патрона для детали или инструмента, что определяет конструкцию переднего конца шпинделя.
Конструкции шпинделей показаны на рис. 50, 54, 57. Передние концы их стандартизованы. Например, для токарных станков применяют резьбовой или фланцевый конец шпинделя.
На резьбовом конце можно быстрее закрепить патрон, однако резьба сравнительно быстро выходит из строя и тогда требуется ремонт всего шпинделя. Кроме того, имеется опасность самоотвинчивания патрона.
Фланцевый конец не имеет резьбы, а патрон крепится винтами на конусный буртик. Шпиндель имеет более сложную форму с откованным фланцем.
Весьма важным является выбор типа передачи на шпиндель (зубчатая или ременная передача), который зависит в первую очередь от его числа оборотов в минуту и от величины передаваемого усилия. Зубчатая передача более проста и компактна и передает значительные крутящие моменты. Однако из-за ошибок шага она не может обеспечить высокую чистоту обработки на шлифовальных, координатнорасточных, отделочно-токарных и других станках. В станках с переменными усилиями резания, например во фрезерных, при зубчатых передачах уменьшается плавность вращения шпинделя и возрастают динамические нагрузки в деталях коробки скоростей. Поэтому передача вращения шпинделю зубчатыми колесами применяется для числа его оборотов в минуту не выше 1500—2000.
В случае применения ременной передачи, как правило, не только увеличиваются габариты, но и усложняется конструкция. Ведомый шкив следует устанавливать на самостоятельные опоры, и, чтобы разгрузить шпиндель, надо производить натяжения ремня и т. д.
Но эти усложнения компенсируются теми преимуществами, которые обеспечивает ременная передача для быстроходных шпинделей. Плавность вращения шпинделей в случае ременного привода обеспечивает высокую чистоту обработки. Для фрезерных и других станков с прерывистым резанием применение ременной передачи снижает максимальные значения крутящих моментов. Это происходит вследствие податливости ременной передачи и мгновенного ее проскальзывания под воздействием удара, возникающего при врезании фрезы в металл.
127
Неравномерность вращения шпинделя при динамических нагрузках тем большая, чем меньше жесткость ременной передачи.
Жесткость ременной передачи с можно определить по формуле
, (1)
где R — радиус ведущего шкива;
F — площадь поперечного сечения ремня; L — длина ведущей ветви ремня;
Е — модуль упругости материала ремня на растяжение. Для привода шпинделя применяют как плоскоременные, так и клиноременные передачи. Их расчет производят по общепринятой методике. Характер нагрузки на шпиндель учитывают коэффициентом k, на который умножают значение окружного усилия: k = 1 при спокойной работе (токарные, сверлильные, шлифовальные станки); k = 1,25 при значительных колебаниях нагрузки (фрезерные, зубофрезерные станки) и k = 1,4 при ударной нагрузке (долбежные, зубодолбежные, строгальные станки). Ременный привод может обеспечивать число оборотов шпинделя до 6000 в минуту и выше, когда окружные скорости ремня достигают 60—100 м/сек. Однако для привода еще более скоростных шпинделей, например внутри-шлифовальных станков, ременная передача уже не может обеспечить передачу требуемых нагрузок, так как под ремнем создается «воздушный мешок» и возможна его неустойчивая работа.
128

Рис. 50. Электрошпиндель внутришлифовального станка
129

В этом случае привод шпинделя может осуществляться пневматической турбинкой до 100 тыс. об/мин или электрошпинделем, который применяется при числах оборотов до 150 000 в минуту и выше.
Высокочастотные электрошпиндели, к которым относятся асинхронные электродвигатели с короткозамкнутым ротором на 200— 800 гц, несущие шлифовальный круг, являются лучшим типом привода для быстроходных шпинделей внутришлифовальных станков. В высокоскоростных электрошпинделях внутришлифовальных станков (рис. 77) ротор 1 и шпиндель с шлифовальным кругом 2 балансируются при помощи грузиков 3 и 5. В прецизионных подшипниках качения предусмотрен предварительный натяг и выбор зазоров при помощи пружин 4 и 6. Для лучшего охлаждения электродвигателя имеется вентилятор 7. Электрошпиндель представляет собой самостоятельный узел, который легко заменяют и устанавливают на столе станка.
5.2.2. Расчет шпинделей на жесткость Шпиндели, как правило, рассчитывают на жесткость, и лишь
для тяжело нагруженных шпинделей производят поверочный расчет на прочность.
Шпиндель — тело сложной формы, а опоры шпинделей в зависимости от их типа создают различные условия для поворота шпинделя при его изгибе. Поэтому при расчете на жесткость шпиндель заменяют балкой на двух опорах, причем тип опоры выбирают в зависимости от типа подшипника (рис. 51).
Рис. 51. Расчетные схемы шпинделей
130