
Методическое пособие 755
.pdf
ет прямую, параллельную оси абсцисс. Если на станке обрабатывают различные детали (рис. 121, а), то кривая распределения будет отражать перемещения суппорта при обработке этих деталей и, следовательно, характер загрузки станка.
Рис. 42. Расчетная схема для определения формы изношенной поверхности направляющих
Если, например, на токарном станке обтачивают в центрах валики различной длины с равной вероятностью обточки валика определенной длины, то кривая распределения принимает вид, указанный на рис. 121, б.
Необходимо отметить, что при обработке разнообразных деталей на универсальных станках распределение длин обработки происходит по законам теории вероятностей для больших чисел.
При определении формы изношенной поверхности направляющих станины и суппорта примем следующие обозначения (рис. 122):
— искомая величина линейного износа направляющих станины
по длине х;
;
— искомая величина линейного износа направляющих суппорта
по длине l;
;
L — максимальный ход суппорта;
111
— длина направляющих суппорта;
— уравнение эпюры удельных давлений;
— кривая распределения общего пути трения, условно отнесенная к левой точке суппорта;
s — путь трения, который проходит каждая точка направляющих суппорта за рассматриваемый промежуток времени;
k — коэффициент абразивного изнашивания, показывающий величину линейного износа (мк) при действии удельного давления, равного 1 н/см2, на протяжении пути трения, равном 1 км для данной пары материалов при данных условиях изнашивания;
— коэффициент износа материала станины;
— коэффициент износа материала суппорта. Рассмотрим методику определения функций
и
, исходя из сделанных выше предпосылок [57]. Функция U(l) определяется просто, так как каждая точка направляющей суппорта изнашивается на протяжении всего пути трения s и на нее действует постоянное удельное давление, определяемое уравнением
. Поэтому кривая износа подобна эпюре удельных давлений и выражается уравнением
(11)
Однако основное значение в потере станком точности и виброустойчивости имеет форма изношенной поверхности направляющих станины, определяемая функцией . Для отыскания этой функции рассмотрим, как изнашивается участок направляющих станины с координатой х (рис. 122). При перемещении суппорта этот участок станины изнашивается под действием удельных давлений, определяемых той частью эпюры
, которая при перемещении суппорта проходит над участком с координатой х. Каждый элемент эпюры удельных давлений с координатой l изнашивает направляющую станины на величину, пропорциональную pdl=f(l)dl.
Чтобы определить элементарный износ dU, вызванный воздействием pdl, необходимо определить ту часть общего пути трения, которую проходит элемент эпюры давлений pdl при изнашивании участка направляющих с координатой х. Для этого воспользуемся кривой распределения . Так как уравнение этой кривой характеризует перемещение левой точки суппорта с
, то для точки суппорта с координатой l уравнение кривой принимает вид
и доля пути трения, приходящаяся на точку с координатой х, равна
.
112

Поэтому износ в точке х от воздействия элемента эпюры удельных давлений pdl
.
Чтобы определить износ в точке х от воздействия всего участка эпюры удельных давлений от до
, необходимо просуммировать элементарные участки pdl в указанных пределах
(12)
Формула (12) является общей для различных случаев. При этом пределы интегрирования определяются в зависимости от того, какой участок эпюры удельных давлений воздействует на точку станины с координатой х (табл. 7).
Таблица 2
Например, при , постоянном ходе суппорта, т. е.
, и треугольной эпюре удельных давлений
для участка I получаем уравнение изношенной поверхности
.
В формуле (12) отражено влияние основных факторов на форму изношенной поверхности направляющих:
k — износостойкости материалов и условий изнашивания; s — интенсивности работы оборудования во времени; — конструкции суппорта в смысле расположения сил (характер эпюры) и усилий обработки (величина удельных давлений);
(x) — технологических процессов обработки, осуществляемых на станке.
113

Пользуясь полученной формулой, можно проанализировать влияние отдельных факторов на величину и характер U(x) и в каждом конкретном случае указать наиболее эффективные пути для уменьшения величины износа и получения более равномерной формы изношенной поверхности, которая непосредственно влияет на точность обработки, виброустойчивость суппорта и возможность компенсации износа.
Сделанные выводы показывают, что изменять форму изношенной поверхности направляющих можно не только путем изменения конструкции станка, но и путем правильного проектирования технологических процессов обработки и рациональной загрузки станка.
Для увеличения срока службы направляющих универсальных станков с большим ходом суппорта () необходимы правильная загрузка станка и такие приемы работы, которые обеспечивают более равномерный износ направляющих. Нецелесообразно загружать станок изготовлением небольших деталей, которые можно обработать на станке меньших размеров. При больших ходах суппорта форма изношенной поверхности направляющей приближается к форме кривой распределения ходов суппорта (рис. 43, а).
Для увеличения срока службы направляющих станков с малым ходом () необходим равномерный характер эпюры удельных давлений, который зависит главным образом от конструктивной формы суппорта и его направляющих. При эксплуатации станка эпюра удельных давлений может быть частично изменена при помощи различной установки инструмента в резцедержавке.
Рис. 43. Влияние удельных давлений и распределения ходов суппорта на форму изношенной поверхности направляющих
114
При малых ходах суппорта форма изношенных направляющих приближается к форме эпюры удельных давлений (рис. 123, б).
Таким образом, определение формы изношенной поверхности направляющих позволяет учесть влияние на их износ не только удельного давления, но и всех других основных факторов.
4. Специфика расчета круговых направляющих скольжения В первом приближении круговые направляющие скольжения
можно рассчитывать по среднему удельному давлению р и максимальной окружной скорости скольжения umax.
Средние удельные давления подсчитывают с учетом веса всех вращающихся частей (узла планшайбы, обрабатываемой детали) и вертикальных составляющих сил резания.
Для чугунных направляющих планшайб допустимое значение принимается равным: при диаметре планшайб до 3м рдоп = 30—40
н/см2; при диаметре планшайб свыше 3м рдоп = 15—20 н/см2.
Низкие удельные давления выбирают из условия уменьшения скорости изнашивания направляющих. Увеличение скорости скольжения имеет положительное значение для обеспечения жидкостного трения, но может способствовать появлению нежелательных форм износа при смешанном трении. В последнем случае следует ограничивать vmaх значениями 3—3,5 м/сек в случае применения текстолита и цветных сплавов
Износ направляющих кругового движения в случае эксцентричной нагрузки равномерен по окружности для вращающейся планшайбы и неравномерен для направляющих станины. Направляющие планшайбы изнашиваются равномерно потому, что каждый их участок испытывает одинаковые удельные давления, проходя за каждый оборот под линией действия максимальной нагрузки (рис. 124).
115

Рис. 44. Износ направляющих кругового движения Рис. 45. Расчетная схема для определения гидродинамической
силы при работе планшайбы
Наоборот, направляющие станины испытывают неодинаковую нагрузку, и в зоне действия силы резания наблюдается их наибольший износ.
В результате при износе направляющих планшайба стремится занять наклонное положение, что отражается на точности обработки.
Угол наклона можно подсчитать по методике определения формы изношенной поверхности на основании исходных законов изнашивания для данной пары материалов (см. гл. 2). Получена следующая формула для определения угла наклона планшайбыдля плоских круговых направляющих при абразивных закономерностях изнашивания
(13)
где k — коэффициент абразивного изнашивания направляющих станины [аналогично значению k в формуле (12)], см2/н;
Р — вертикальная нагрузка на планшайбу, н; n — число оборотов планшайбы, об/мин;
а — ширина направляющих, см; — эксцентриситет приложения силы, см;
t — время работы планшайбы, мин.
116

Формула (13) показывает, что угол поворота планшайбы увеличивается с течением времени и его значение зависит от режимов работы (Р; n) и эксцентриситета нагрузки. При широких направляющих угол поворота планшайбы меньше.
При высоких скоростях вращения планшайб в направляющих скольжения может возникнуть жидкостное трение, которое обеспечивает длительную работу направляющих без износа.
Недостатком в этом случае является «всплывание» планшайб, так как толщина масляного слоя зависит от нагрузки и числа оборотов. Это может повлиять на точность обработки. Для создания гидродинамического эффекта на направляющих станины выполняют специальные скосы (рис. 125); каждый сегмент направляющей состоит из горизонтального I и наклонного II участков.
На основании гидродинамической теории можно найти поддерживающую силу масляного слоя, действующую в каждом сегменте.
С учетом несущей способности наклонного горизонтального участка гидродинамическую поддерживающую силу в одном сегменте можно подсчитать по формуле [40].
, (14)
где — динамическая вязкость масла при данной температуре (для круговых направляющих до 40°), н•сек/м2;
v — скорость скольжения, м/сек;
l, b — размеры участка (рис. 125, а, и б), мм; h—толщина масляного слоя, мм.
Критическое (минимально допустимое) значение h можно принимать = 0,07 — 0,10 мм (нижние значения при температурах до
40°);
— коэффициент, учитывающий боковое исте-
чение;
— коэффициент, учитывающий работу наклонного и горизонтального участков.
Наибольшее значение будет при
, т. е. при более длинном скосе. Однако лучше принимать
, так как в случае смешанного трения значительную часть нагрузки воспринимают го-
117
ризонтальные участки сегмента. В этом случае . Оптимальное значение глубины клинового скоса
.
Общая поддерживающая сила на направляющих равна сумме сил, действующих в каждом сегменте.
Если действительная толщина масляного слоя меньше критической, то масляный слой воспринимает только часть общей нагрузки, а ее остальная часть воспринимается непосредственно соприкасающимися горизонтальными участками.
Приведенную формулу можно применять и при расчете на жидкостное трение направляющих прямолинейного движения при высоких скоростях движения (столы продольно-строгальных станков).
На работу направляющих кругового движения оказывают влияние и температурные деформации. Исследования, проведенные ЭНИМСом совместно с Коломенским заводом тяжелого станкостроения, показывают, что плоские круговые направляющие в сочетании со шпинделем в подшипниках качения лучше V-образных направляющих со шпинделем в подшипниках скольжения, так как при этом температурные деформации и износ меньше влияют на потерю точности и работоспособности.
При V-образных направляющих температурные деформации планшайбы приводят к возрастанию давлений на внутренней крутой направляющей и возможности появления задиров и заклинивания.
Вводя специальные ребра между направляющей и противоположными стенками планшайбы, можно увеличить теплоотвод от направляющих и уменьшить температурные деформации.
5.5. Расчет направляющих качения
Расчет направляющих качения, как правило, производят на основании формул для контактных напряжений и деформаций по теории Герца—Беляева.
Для шариковых направляющих эти формулы принимают вид: для наибольшего напряжения в зоне контакта
(15)
для контактной деформации (сближение шара с плоскостью)
118
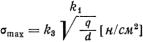
, (16)
где Р — усилие, действующее на один шарик, н; d — диаметр шарика, мм;
и
— коэффициенты, зависящие от модуля упругости и коэффициента Пуассона.
Для стальных направляющих = 22•103;
= 0,9; для чугунных направляющих = 16•103;
= 1,2. Для роликовых направляющих
(17)
, (18)
где q — нагрузка на единицу длины ролика, н/мм.
Для стальных направляющих = 870 и для чугунных
= 680. Среднее значение коэффициента
= 0,06.
При определении нагрузок на каждый шарик или ролик направляющих качения следует учитывать возможную неравномерность нагрузки из-за неодинакового размера тел качения и нелинейности плоской направляющей. Так как точность направляющих качения ниже, чем подшипников качения, неравномерность нагрузки соответственно выше.
Форма изношенной поверхности планок и направляющих, между которыми помещены тела качения, в первом приближении можно подсчитать по тем же зависимостям, что и для плоских направляющих [формула (12)], так как характер передачи нагрузок по длине направляющих сохраняется.
При работе направляющих качения желательно создать условия для более длительной их работы с малым износом (смятием) и большим сроком службы до наступления усталости поверхностных слоев у тел качения.
Поэтому допускаемые напряжения, выбираемые по общим правилам, занижаются и составляют, например, для роликовых направ-
ляющих точных станков (координатно-расточных, шлифовальных)
10—15 кн/см2.
С точки зрения контактной жесткости направляющие скольжения и шариковые направляющие качения примерно равноценны. Но на жесткость направляющих качения сильное влияние оказывает предварительный натяг.
119
С увеличением натяга жесткость направляющих сначала резко увеличивается, а затем, по достижении определенной величины
натяга, изменяется незначительно. Дальнейшее увеличение натяга не вызывает существенного повышения жесткости. Тяговые усилия, наоборот, до некоторой величины натяга изменяются незначительно, а по достижении определенного предела резко увеличиваются.
Поэтому имеется область оптимального натяга, при котором жесткость направляющих достаточно высока, а тяговые усилия невелики.
Жесткость направляющих качения без предварительного натяга наиболее употребительной формы (комбинированных из призматической и плоской) в среднем на 25—50% меньше жесткости направляющих скольжения такой же формы.
Жесткость направляющих качения лучших форм с предварительным натягом (при оптимальной его величине) превышает жесткость направляющих скольжения смешанного трения в направлении действия силы натяга в 3—10 раз.
Эксперименты показывают, что направляющие качения позволяют осуществлять малые установочные перемещения с высокой точностью. При достаточно высокой жесткости привода (выше 30— 40 н/мк) погрешность установки характеризуется величинами порядка 0,1—0,2 мк. При малой жесткости привода точность установки понижается [37].
§ 3. Основные методы повышения долговечности направляю-
щих
1. Влияние износа направляющих на точность обработки Износ направляющих станков изменяет первоначальную траек-
торию движения изделия или инструмента, что искажает получаемую форму изделия.
При определении погрешности обработки, возникающей при износе направляющих станка, необходимо связать износ некоторых граней с отклонением траектории движения инструмента или детали от прямолинейного движения и затем установить влияние отклонения на форму и размер обрабатываемого изделия. При этом следует учи-
120