
Методическое пособие 590
.pdfметрологический контроль параметров каждого изъятого изделия. Определяют количество дефектных изделий и это количество сравнивают с числами A0 и
A1. На основании сравнения дают заключение о годности или дефектности всей партии изделий по следующей схеме:
d A0 |
– партия изделий качественная; |
(3.12) |
A0 d A1 – партия изделий считается не плохой; |
(3.13) |
|
d A1 |
– партия изделий считается дефектной. |
(3.14) |
Пример определения качества партии изделий по методу однократной
выборки
Задание. Партия изготовленных изделий, качество которых необходимо проконтролировать, состоит из N 50 штук. Производитель и заказчик договорились, что если в изготовленной партии изделий содержится не более q0 0.1 дефектных изделий, то партия считается качественной. Если в изготовленной партии изделий содержится более q1 0.2 дефектных изделий,
то партия считается бракованной. Если в изготовленной партии изделий содержится более q0 0.1 и менее q1 0.2 дефектных изделий, то партию можно считать удовлетворительного качества. Поставщик согласен на риск
0.15, а заказчик согласен на риск 0.15. Определить приемочное A0 и
браковочное A1 числа дефектных изделий в выборке объемом n 20 изделий.
Сделать вывод о качестве партии изделий на основании количества дефектных изделий d* 4, выявленных в результате метрологического контроля выборки.
Массив исходных данных для выполнения задания содержится в табл. 3.2.
40
Решение
Партия изготовленных изделий не большая N 100, а относительный
объем выборки велик nN 0.4, то контроль необходимо проводить, исходя из
гипергеометрического распределения, т.е. расчеты проводить по формулам
(3.2) и (3.3).
I.Определяются исходные данные, необходимые для решения задачи:
N 50 – объем изготовленной партии; n 20 – объем выборки;
q0 0.1 – значение границы, определяющей изготовленную партию
изделий, как качественную;
q1 0.2 – значение границы, определяющей изготовленную партию изделий, как дефектную;
D0 n q0 |
50 0.1 5 – максимальное число дефектных изделий в |
качественной партии;
D1 n q1 50 0.2 10 – минимальное число дефектных изделий в не
качественной партии;
0.15 – риск производителя;
0.15 – риск заказчика.
II.Для определения приемочного числа A0 дефектных изделий в
выборке воспользуемся табл. 3.1, из которой определим номера формул,
соответствующие диапазону значений исходных величин. Из табл. 3.1 видно,
что для представленных выше данных необходимо применить формулы (3.2) и (3.3). Для определения приемочного числа воспользуемся формулой (3.2) В
этой формуле произведем суммирование вероятностей гипергеометрического распределения до тех пор, пока накопленная вероятность не приблизится к величине
P(d A0 ) 1 1 0.1 0.9. |
(3.15) |
41
Величины вероятностей для каждого d определится из следующих
соотношений: |
|
|
|
|
|
|
|
|
|
|
|
|
|
|
|
|
|
|
P(d 0) |
|
|
C0 |
|
C20 0 |
|
|
|
1 3169870830126 |
|
0.067; |
(3.16) |
||||||
|
|
5 |
|
50 5 |
|
|
|
|
|
|
||||||||
|
|
|
C5020 |
|
47129212243360 |
|
|
|||||||||||
|
|
|
|
|
|
|
|
|
|
|
|
|
|
|||||
P(d 1) |
C1 |
C20 1 |
|
5 2438362177020 |
|
0.258; |
(3.17) |
|||||||||||
5 |
|
50 5 |
|
|
|
|
|
|
||||||||||
|
|
|
C5020 |
|
47129212243360 |
|
|
|||||||||||
|
|
|
|
|
|
|
|
|
|
|
|
|
||||||
P(d 2) |
|
|
|
|
C2 |
C20 2 |
|
|
10 1715884494940 |
0.364; |
(3.18) |
|||||||
|
|
|
5 |
|
50 5 |
|
|
|
|
|
|
|||||||
|
|
C5020 |
|
47129212243360 |
|
|||||||||||||
|
|
|
|
|
|
|
|
|
|
|
|
|
||||||
P(d 3) |
|
C3 |
|
C20 3 |
|
|
|
10 1103068603890 |
0.234; |
(3.19) |
||||||||
|
5 |
|
50 5 |
|
|
|
|
|
|
|
||||||||
|
|
C5020 |
|
|
47129212243360 |
|
||||||||||||
|
|
|
|
|
|
|
|
|
|
|
|
|||||||
P(d 4) |
|
|
|
|
C4 |
C20 4 |
|
|
|
5 646626422970 |
0.069. |
(3.20) |
||||||
|
5 |
|
50 5 |
|
|
|
|
|||||||||||
|
|
C5020 |
|
47129212243360 |
|
|||||||||||||
|
|
|
|
|
|
|
|
|
|
|
|
|
|
|
Суммирование значений из (3.16)…(3.20) и сравнение со значением (3.15)
проводим в следующем порядке: P(d<=0) = 0.067 < 0.9;
P(d<=1) = 0.067 + 0.258 = 0.325 < 0.9;
P(d<=2) = 0.067 + 0.258 + 0.364 = 0.689 < 0.9;
P(d<=3) = 0.067 + 0.258 + 0.364 + 0.234 = 0.923 > 0.9;
P(d<=4) = 0.067 + 0.258 + 0.364 + 0.234 + 0.069 = 0.992 > 0.9.
Принимая во внимание условие (3.4), определяем, что A0 3.
III.Для определения браковочного числа A1 дефектных изделий в
выборке также воспользуемся табл. 3.1, из которой видно, что для представленных выше данных необходимо применить формулы (3.2) и (3.3).
Для определения браковочного числа воспользуемся формулой (3.3). В этой формуле произведем суммирование вероятностей гипергеометрического распределения до тех пор, пока накопленная вероятность не приблизится к величине
42
P(d A1) 0.1. |
|
|
|
|
|
|
|
|
(3.21) |
|||||
Величины |
|
|
вероятностей для каждого d определится |
из следующих |
||||||||||
соотношений: |
|
|
|
|
|
|
|
|
|
|
|
|
|
|
P(d 0) |
|
|
C0 |
C20 0 |
|
|
|
1 137846528820 |
0.003; |
(3.22) |
||||
|
10 |
50 10 |
|
|
|
|
|
|||||||
|
|
C20 |
47129212243360 |
|
|
|||||||||
|
|
|
|
|
|
|
|
|
|
|
||||
|
|
|
|
50 |
|
|
|
|
|
|
|
|
|
|
P(d 1) |
C1 |
C20 1 |
|
|
10 131282408400 |
|
0.028; |
(3.23) |
||||||
10 |
50 10 |
|
|
|
|
|
|
|
||||||
|
C5020 |
47129212243360 |
|
|
|
|||||||||
|
|
|
|
|
|
|
|
|
|
|||||
P(d 2) |
|
|
C2 |
C20 2 |
|
|
|
45 113380261800 |
0.096. |
(3.24) |
||||
|
10 |
50 10 |
|
|
|
|
|
|
||||||
|
C5020 |
|
47129212243360 |
|
||||||||||
|
|
|
|
|
|
|
|
|
||||||
Суммирование значений из (3.22)…(3.24) и сравнение со значением (3.21) |
||||||||||||||
проводим в следующем порядке: |
|
|
|
|||||||||||
P(d<=0) = 0.003 < 0.1; |
|
|
|
|
|
|
|
|||||||
P(d<=1) = 0.003 + 0.028 = 0.031 < 0.1; |
|
|
|
|||||||||||
P(d<=2) = 0.003 + 0.028 + 0.096 = 0.127 > 0.1. |
|
|||||||||||||
Принимая во внимание условие (3.4), определяем, что |
A1 1 2 или |
|||||||||||||
A1 3. |
|
|
|
|
|
|
|
|
|
|
|
|
|
|
В данном примере приемочное и браковочное числа получились
одинаковыми A0 A1 3. Но предполагается, что был проведен
метрологический контроль каждого изделия выборки объёмом n 20, и было
выявлено |
d* 4 |
дефектных изделий. На основании |
условия |
3.14 партия |
|||||||
изделий признается дефектной, так как |
d* 4 A 3 . |
|
|
|
|
||||||
|
|
|
|
|
|
|
1 |
|
|
|
|
|
|
|
|
|
|
|
|
|
|
Таблица 3.2 |
|
|
|
|
|
Значения исходных данных |
|
|
|
|
|||
|
|
|
|
|
|
|
|
|
|
|
|
№ п/п |
|
N |
n |
q0 |
|
q1 |
|
|
|
|
d* |
1 |
|
60 |
15 |
0.15 |
|
0.25 |
0.1 |
|
0.1 |
|
2 |
2 |
|
80 |
20 |
0.10 |
|
0.20 |
0.08 |
|
0.12 |
|
3 |
3 |
|
300 |
50 |
0.05 |
|
0.10 |
0.1 |
|
0.1 |
|
4 |
4 |
|
200 |
10 |
0.08 |
|
0.10 |
0.15 |
|
0.1 |
|
3 |
5 |
|
600 |
40 |
0.10 |
|
0.20 |
0.12 |
|
0.12 |
|
8 |
6 |
|
150 |
15 |
0.08 |
|
0.10 |
0.08 |
|
0.08 |
|
5 |
7 |
|
70 |
20 |
0.08 |
|
0.15 |
0.1 |
|
0.1 |
|
2 |
8 |
|
400 |
40 |
0.10 |
|
0.20 |
0.08 |
|
0.08 |
|
4 |
|
|
|
|
43 |
|
|
|
|
|
Окончание табл. 3.2
№ п/п |
N |
n |
q0 |
q1 |
|
|
d* |
9 |
1500 |
80 |
0.08 |
0.10 |
0.12 |
0.12 |
9 |
10 |
200 |
8 |
0.05 |
0.10 |
0.05 |
0.05 |
6 |
11 |
50 |
20 |
0.12 |
0.24 |
0.12 |
0.12 |
2 |
12 |
180 |
20 |
0.15 |
0.20 |
0.08 |
0.1 |
2 |
13 |
250 |
20 |
0.08 |
0.10 |
0.1 |
0.1 |
4 |
14 |
300 |
70 |
0.05 |
0.09 |
0.12 |
0.15 |
4 |
15 |
120 |
15 |
0.12 |
0.24 |
0.08 |
0.12 |
3 |
16 |
200 |
15 |
0.18 |
0.25 |
0.15 |
0.1 |
5 |
17 |
600 |
50 |
0.10 |
0.20 |
0.12 |
0.12 |
7 |
18 |
150 |
15 |
0.08 |
0.10 |
0.05 |
0.05 |
3 |
19 |
70 |
10 |
0.08 |
0.15 |
0.12 |
0.12 |
3 |
20 |
400 |
30 |
0.10 |
0.20 |
0.08 |
0.1 |
4 |
21 |
2000 |
10 |
0.15 |
0.25 |
0.12 |
0.12 |
5 |
22 |
500 |
20 |
0.10 |
0.20 |
0.08 |
0.08 |
6 |
23 |
180 |
40 |
0.05 |
0.10 |
0.1 |
0.1 |
3 |
24 |
250 |
50 |
0.08 |
0.10 |
0.08 |
0.08 |
3 |
25 |
300 |
50 |
0.10 |
0.20 |
0.05 |
0.07 |
4 |
Оформление отчета
Отчет составляется по установленной форме и должен содержать
следующие пункты:
цель работы;
краткую теоретическую часть с расчётными формулами;
условие задания;
решение с пояснениями и формулами, написанными в буквенном и численном виде;
вывод.
44
Практическая работа № 4
ОЦЕНКА ОПТИМАЛЬНОЙ ТОЧНОСТИ ИЗМЕРЕНИЯ
Цель работы – изучить методику выбора оптимальных средств измерения для диагностического обследования технических устройств, приобрести навыки использования номограмм в решении технических задач.
Краткие теоретические положения
Высокая точность и достоверность результатов измерения требует дорогостоящих средств измерения, а использование менее точных приборов и соответственно более дешёвых вызывает увеличение расходов на техническое обслуживание и ремонт технических устройств.
Существуют два подхода к решению задачи выбора оптимальной погрешности измерения параметров технических устройств. Первый подход базируется на использовании технико-экономического критерия выбора оптимальной погрешности измерения параметров технических устройств. Второй подход является метрологическим подходом, основанном на коэффициентах влияния диагностических и структурных параметров.
Целевая функция, определяющая удельные издержки при оптимальной средней квадратической погрешности измерения параметра состояния, имеет вид
(4.1) где G – целевая функция минимума удельных издержек, связанных с измерением параметра технического устройства; B – суммарные издержки на измерение параметра состояния в зависимости от среднеквадратической погрешности ; C – средние дополнительные издержки на один межконтрольный период на предупредительное восстановление и устранение
45
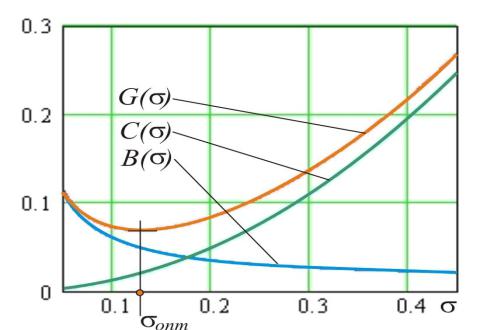
последствий отказа в зависимости от среднеквадратической погрешности измерения .
Задача определения минимальных затрат для измерительных процедур можно представить в виде
G min B C .
На рис. 4.1 показан качественных график изменения целевой функции,
издержек на измерение параметров состояния и дополнительных издержек в зависимости от среднеквадратической погрешности.
Рис. 4.1. Удельные издержки как функции оптимальной среднеквадратической погрешности измерения параметра технического устройства
Суммарные |
издержки |
B |
обратно |
пропорциональны |
||
среднеквадратической погрешности и могут быть выражены формулой |
||||||
B b |
L |
, |
|
|
|
(4.2) |
|
|
|
|
|||
|
|
|
|
|
где b и L – постоянные величины, определяемые на основе статистических данных; – среднеквадратическая погрешность процесса измерения.
46

Дополнительные |
издержки |
C , |
наоборот, |
с |
увеличением |
среднеквадратической |
погрешности |
|
возрастают |
и |
определяются |
соотношением |
|
|
|
|
|
C 0.256 10 4 C 2 , |
|
|
|
(4.3) |
|
где – нормированный показатель, определяемый |
по |
номограммам, |
представленным на рис. 4.2, рис. 4.3, рис. 4.4, рис. 4.5; C – средние издержки на предупредительные операции восстановления значения параметра технического устройства до номинального значения.
Рис. 4.2. Номограмма для определения нормированного показателя при A0 2.0 и коэффициенте вариации v 0.1; 0.2; 0.4; 0.5; 0.6; 1.0
47

Рис. 4.3. Номограмма для определения нормированного показателя при A0 3.0 и коэффициенте вариации v 0.1; 0.2; 0.3; 0.5; 0.6; 0.7; 1.0
Рис. 4.4. Номограмма для определения нормированного показателя при A0 5.0
и коэффициенте вариации v 0.1; 0.2; 0.4; 0.5; 0.6; 0.7; 0.8; 1.0
48

Рис. 4.5. Номограмма для определения нормированного показателя при
A0 10.0 и коэффициенте вариации v 0.1; 0.2; 0.4; 0.5; 0.6; 0.7; 0.8; 1.0
Подставив в целевую функцию (4.1) соотношения (4.2) и (4.3), получим
G b L 0.265 10 4 C 2 . (4.4)
Минимальное значение целевой функции найдем через процедуру дифференцирования
d G 0 d
или
L 0.53 10 4 C 0,
2
откуда получаем оптимальное значение среднеквадратической погрешности процесса измерения
onm 3 |
104 L |
. |
(4.5) |
|
0.53 C |
||||
|
|
|
49