
2553
.pdf11.5. Расчет шатунных болтов
На шатунные болты действует статическая нагрузка– растяжение, вызываемая силой предварительной затяжки и переменной нагрузки от сил инерции.
Pjp Pjnг (mшк mкр)r 2 ,
где r – радиус кривошипа.
Величина суммарной силы, нагружающей болт:
P P |
P ; |
P |
m(1 )P ; |
m 2,5 3; |
0,2 0,25 |
||||||||||
б из |
jp |
п.з |
|
|
|
jp |
|
|
|
|
|
|
|||
где – коэффициент нагрузки резьбового соединения. |
|||||||||||||||
Максимальное напряжение шатунногоболтавычисляютпоформуле: |
|||||||||||||||
|
|
max |
|
Pб |
и |
|
|
Pб |
; |
|
min |
|
Pп.з |
, |
|
|
|
||||||||||||||
|
|
|
F |
max |
|
F |
|
|
F |
||||||
|
|
|
|
|
б |
|
|
|
ор |
|
|
|
|
б |
|
Fб и Fор – площади сечения по максимальному сечению и по внут-
реннему диаметру резьбы. Запас прочности:
n |
|
|
|
|
|
1 |
2 |
, |
|
K |
|
а |
m |
||||
|
|
|
|
|
|
|
||
|
|
|
|
|
|
|
|
0,2; =0,8‒0,9; =1; К =4;
1 180 250 – углеродистая сталь;
1 340 380 – легированная сталь.
Материал шатунных болтов ст. 35Х, 40Х, 35ХМА, 37ХН3А. Для форсированных двигателей 18ХНВА, 18ХНМА, 40ХНМА.
12. РАСЧЕТ КОЛЕНЧАТОГО ВАЛА НА ПРОЧНОСТЬ
Анализ поломок коленчатых валов показывает, что в большинстве случаев излом имеет усталостный характер и вызывается высокими переменными напряжениями кручения и изгиба.
Разрушения начинаются у краев масляных отверстий или у галтелей. Приближенные методы расчета основаны на определении допускаемых напряжений и не учитывают усталостную прочность материала, поэтому расчет желательно производить по методу Киносошвили.
150
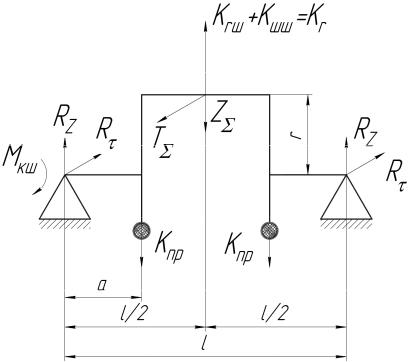
За расчетный режим принимается номинальный режим работы двигателя. Расчетные нагрузки определяют в динамическом расчете и, кроме того, на коленчатый вал действуют крутильные колебания. Расчет производят на схеме двухопорной балки (разрезной). Запасы прочности коренных шеек почти одинаковы как по разрезной, так и по неразрезной схемах. Запас прочности шатунных шеек на 5 – 8 % меньше, а для крайних щек на 30 – 40 %. Зная отклонения запасов прочности, можно последнее учесть при расчете.
12.1. Расчет коренных шеек
Рис. 70. Схема расчета коренных шеек
Коренные шейки подвергаются изгибу и кручению. Напряжение от изгиба не велико, и запас прочности с учетом изгиба на 2–3 % меньше, чем при расчете только кручения. Максимальные и минимальные значения крутящего момента находят из диаграммы тангенциальных сил (рис. 70) от одного цилиндра и для многоцилиндрового двигателя необходимо ввести коэффициенты:
а) для максимального крутящего момента K 2,15, для минимальных K 1,0 – для коренных шеек;
б) для шатунных шеек K 1,98,K 0,9.
151
|
|
Mкрmax Tmax r 2,15; |
Mкрmin |
1,0 Tmin r; |
||||||||||||||||
|
|
|
|
|
|
|
d |
3 |
|
|
|
|
4 |
|||||||
|
|
|
W |
|
|
|
1 |
dв |
|
|
. |
|||||||||
|
|
|
|
|
|
|||||||||||||||
|
|
|
|
16 |
|
|
|
d |
кш |
|
|
|
||||||||
|
|
|
|
|
|
|
|
|
|
|
|
|
|
|
|
|||||
|
Амплитуда напряжений и среднее напряжение: |
|||||||||||||||||||
|
|
|
max |
min |
|
; m |
max min |
. |
||||||||||||
|
|
|
2 |
|
|
|
|
|||||||||||||
|
|
|
|
|
|
|
|
|
|
|
1 |
|
|
|
2 |
|
||||
|
Запас прочности: n |
|
|
|
|
|
|
|
|
|
|
|
|
2,5 5. |
||||||
|
|
|
|
|
|
а |
m |
|
||||||||||||
|
|
|
|
|
|
|
K |
|
|
|
|
|
|
|||||||
|
|
|
|
|
|
|
|
|
|
|
||||||||||
|
|
|
|
|
|
|
|
|
|
|
|
|
|
|
|
|
|
|||
|
|
|
|
|
|
|
|
0,7 0,8; K 1,8 2,5; |
||||||||||||
0,1; |
0,6 0,8; |
|||||||||||||||||||
1 |
180 220 –углеродистая сталь; 1 |
280 320 – легирован- |
||||||||||||||||||
ная сталь. |
|
|
|
|
|
|
|
|
|
|
|
|
|
|
|
|
|
|
|
12.2. Расчет шатунных шеек
Шатунные шейки подвергаются кручению и изгибу. Расчет производят отдельно на кручение и на изгиб, так как действие max и min крутящих моментов и изгибающих не совпадают по времени. Наиболее нагруженная шатунная шейка располагается рядом с наиболее нагруженной коренной шейкой. Запас прочности от изгиба определяют, основываясь на значении изгибающих моментов в плоскости кривошипа MZ , и учитывают расположение масляного отверстия.
Центробежная сила, действующая на шатунную шейку:
|
|
|
|
|
K |
r |
(m |
|
m |
)r 2 ; |
|
|
|
|
||||||
|
|
|
|
|
|
|
шк |
|
|
шш |
|
|
|
|
|
|
|
|
||
Z |
|
P |
|
cos( ) |
|
;Z |
|
|
|
P |
|
cos( ) |
; |
|||||||
|
|
|
|
|
|
|
|
|
|
|||||||||||
|
max |
max |
cos |
|
|
min |
|
|
min |
|
cos |
|||||||||
|
|
|
Т max 1,98Tmax;Т min 0,9Tmin; |
|
|
|
||||||||||||||
|
|
R |
|
Z max Kr |
|
; R |
|
|
Z min Kr |
; |
||||||||||
|
|
|
|
|
|
|
|
|||||||||||||
|
|
Zmax |
|
|
2 |
|
|
Z min |
|
|
|
2 |
|
|
|
|
||||
|
|
|
|
|
|
|
|
|
|
|
|
|
|
|
|
|
|
|||
|
|
|
|
|
|
|
T |
|
|
|
|
|
|
T min |
|
|
|
|
||
|
|
|
R |
|
|
max |
|
; R |
|
|
|
. |
|
|
|
|||||
|
|
|
|
|
|
|
|
|
|
|
||||||||||
|
|
|
|
max |
|
2 |
|
|
|
min |
|
|
2 |
|
|
|
|
|||
|
|
|
|
|
|
|
|
|
|
|
|
|
|
|
|
|
|
Изгиб шатунной шейки в плоскости колена:
152

M |
|
R |
l |
; M |
|
R |
l |
. |
|
|
|
|
|||||
|
Z max |
Z max 2 |
Z min |
Z min 2 |
Изгиб шатунной шейки в перпендикулярной плоскости колена:
M |
|
R |
l |
;M |
|
R |
l |
. |
|
2 |
|
|
|||||
|
max |
max |
|
min |
min 2 |
Суммарный изгибающий момент:
M max MZ2max M 2max max ; M min
MZ2min M 2min .
Изгибающий момент в плоскости масляного отверстия:
M MZ cos M sin .
Напряжения от изгиба:
|
|
|
|
|
|
M |
max |
|
|
|
|
|
|
|
|
|
|
|
M |
min |
|
W |
|
|
|
|
d3 |
d |
в |
|
4 |
|||||||||||||||
|
max |
|
|
|
|
; |
|
|
min |
|
|
|
|
; |
|
|
|
|
|
|
|
1 |
|
|
. |
|||||||||||||||||||||
|
|
|
|
|
|
|
|
|
|
|
|
|
|
|
32 |
d |
||||||||||||||||||||||||||||||
|
|
|
|
|
W |
|
|
|
|
W |
|
|
|
|
|
изг |
|
|
|
|
|
|
||||||||||||||||||||||||
|
|
|
|
|
|
|
|
изг |
|
|
|
|
|
|
|
|
|
|
|
|
|
изг |
|
|
|
|
|
|
|
|
|
|
|
|
|
|
|
|
||||||||
|
|
|
|
|
|
|
|
|
|
|
|
|
|
|
|
|
|
|
|
|
|
|
|
|
|
|
|
|
|
|
|
|
|
|
|
|
|
|
||||||||
|
|
Запас прочности от изгибающего момента: |
|
|
|
|
|
|
|
|
|
|
||||||||||||||||||||||||||||||||||
|
|
|
|
|
|
|
|
|
n |
|
|
|
|
|
|
|
|
|
|
1 |
|
|
|
|
|
|
|
|
3 4; |
|
|
|
|
|
|
|
|
|||||||||
|
|
|
|
|
|
|
|
|
|
|
|
|
|
K |
|
|
|
|
|
|
|
|
|
|
|
|
|
|
|
|
|
|
|
|
|
|
||||||||||
|
|
|
|
|
|
|
|
|
|
|
|
|
|
|
|
|
|
|
|
|
|
а |
m |
|
|
|
|
|
|
|
|
|
|
|
||||||||||||
|
|
|
|
|
|
|
|
|
|
|
|
|
|
|
|
|
|
|
|
|
|
|
|
|
|
|
|
|
|
|
|
|
||||||||||||||
|
|
|
|
|
|
|
|
|
|
|
|
|
|
|
|
|
|
|
|
|
|
|
|
|
|
|
|
|
|
|
|
|
|
|
|
|
|
|
|
|
|
|
||||
|
|
|
|
|
|
|
max min |
; |
m |
|
max min |
. |
|
|
|
|
|
|||||||||||||||||||||||||||||
|
|
|
|
|
|
|
|
|
|
|
|
|
|
|
|
|
|
|
||||||||||||||||||||||||||||
|
|
|
|
|
|
|
|
|
|
|
|
|
|
2 |
|
|
|
|
|
|
|
|
|
|
|
|
|
|
K |
|
2 |
|
|
|
|
|
|
|
|
|
||||||
|
0,1; |
|
|
|
|
|
|
|
|
|
|
|
|
|
|
|
0,7 0,8; |
|
1,8 2,5; |
|
|
|
|
|
||||||||||||||||||||||
|
|
|
0,6 0,8; |
|
|
|
|
|
|
|||||||||||||||||||||||||||||||||||||
1 |
250 300 – углеродистая сталь; 1 |
350 500 – легированная |
||||||||||||||||||||||||||||||||||||||||||||
сталь. |
|
|
|
|
|
|
|
|
|
|
|
|
|
|
|
|
|
|
|
|
|
|
|
|
|
|
|
|
|
|
|
|
|
|
|
|
|
|
|
|
|
|
|
|
||
|
|
|
|
|
|
|
12.3. Расчет шатунных шеек на кручение |
|
|
|
|
|
||||||||||||||||||||||||||||||||||
|
|
|
|
max |
|
|
Mкр max |
; |
min |
|
|
Mкр min |
|
|
; W 2W |
M |
кр ; |
|
|
|||||||||||||||||||||||||||
|
|
|
|
|
|
|
|
|
||||||||||||||||||||||||||||||||||||||
|
|
|
|
|
|
W |
|
|
|
|
|
|
|
|
|
|
|
|
W |
|
|
|
|
|
|
|
|
|
|
|
изг |
|
|
|
||||||||||||
|
|
|
|
|
|
|
|
|
|
|
|
|
|
|
|
|
|
|
|
|
|
|
|
|
|
|
|
|
|
|
|
|
|
|
|
|
|
|
|
|
||||||
|
|
|
|
|
|
|
|
|
max min |
; |
m |
|
max min |
|
; |
|
|
|
|
|
|
|||||||||||||||||||||||||
|
|
|
|
|
|
|
|
|
|
|
|
|
|
|
|
|
|
|
|
|
||||||||||||||||||||||||||
|
|
|
|
|
|
|
|
|
|
|
|
|
|
2 |
|
|
1 |
|
|
|
|
|
|
|
|
|
2 |
|
|
|
|
|
|
|
|
|
||||||||||
|
|
|
|
|
|
|
|
|
|
|
n |
|
|
|
|
|
|
|
|
|
|
|
|
|
3 4 |
; |
|
|
|
|
|
|
|
|
||||||||||||
|
|
|
|
|
|
|
|
|
|
|
|
|
|
|
a m |
|
|
|
|
|
|
|
|
|
||||||||||||||||||||||
|
|
|
|
|
|
|
|
|
|
|
|
|
|
|
|
|
|
|
K |
|
|
|
|
|
|
|
|
|
|
|
|
|
|
|
||||||||||||
|
|
|
|
|
|
|
|
|
|
|
|
|
|
|
|
|
|
|
|
|
|
|
|
|
|
|
|
|
|
|
|
|
|
|
||||||||||||
|
|
|
|
|
|
|
|
|
|
|
|
|
|
|
|
|
|
|
|
|
|
|
|
|
|
|
|
|
|
|
|
|
|
|
|
|
|
|
|
|
|
|
|
|
|
153

0,1; 0,6 0,8; 0,7 0,8; K 1,8 2,5.
Общий запас прочности: n |
|
|
n n |
|
2,5 3,0. |
|
|
|
|
|
|||
n2 |
n2 |
|||||
|
|
|
|
|
|
|
12.4. Расчет щек на прочность
Щеки коленчатого вала подвергаются изгибу, растяжению, сжатию и кручению.
1. Расчет щеки на изгиб: а) в плоскости колена
|
|
|
M |
|
R |
|
а; |
|
|
|
M |
изг |
; R |
Z |
|
K |
r |
|
|
W |
вh2 |
|||||||||
|
|
|
изг |
Z |
изг |
|
|
|
|
|
|
; |
|
, |
||||||||||||||||
|
|
W |
|
|
|
2 |
|
|
6 |
|||||||||||||||||||||
|
|
|
|
|
|
|
|
|
|
|
|
Z |
|
|
|
|
|
|
изг |
|
||||||||||
|
|
|
|
|
|
|
|
|
|
|
|
|
изг |
|
|
|
|
|
|
|
|
|
|
|
|
|
|
|
||
где в – ширина щеки; h – толщина щеки. |
|
|
|
|
|
|
|
|
|
|
|
|||||||||||||||||||
|
изгmax |
|
Mизгmax |
; |
изгmin |
|
Mизгmin |
; |
|
|
max min |
; |
m |
|
max min |
|||||||||||||||
|
|
W |
|
|
|
|
W |
|
|
|
|
|
2 |
|
|
|
|
|
|
2 |
|
|||||||||
|
|
|
|
изг |
|
|
|
|
|
|
|
изг |
|
|
|
|
|
|
|
|
|
|
|
|
|
|
|
|
б) в плоскости перпендикулярной колену:
M |
|
R max c M |
|
|
|
|
|
R min c M |
|
||
изгmax |
изгкш |
;Mизгmin |
изг.кш ; |
||||||||
|
|
c r |
d |
ш.ш |
; W |
Bh2 |
|
||||
|
|
|
|
|
|
; |
|
||||
|
|
|
|
2 |
|
6 |
|
||||
|
|
|
|
|
|
изг |
|
|
|
в) растяжение или сжатие щеки:
сжmax |
|
RZ max |
; сжmin |
|
RZ min |
; Fщ b h – площадь щеки. |
F |
F |
|||||
|
|
изг |
|
|
щ |
|
По максимальным и минимальным значениям опорных реакций определяют max, min(как правило, в плоскости колена), находят амплитуду напряжения, среднее напряжение и запас прочности.
n |
|
|
|
|
1 |
|
3 4 |
. |
|
|
|
|
|||||
|
|
|
K |
a m |
||||
|
|
|
|
|
|
|||
|
|
|
|
|
|
|
|
|
Скручивание щеки происходит под действием реакции R : |
||||||||
|
|
|
|
Mкр R |
. |
|
Максимальное и минимальное значения крутящего момента определяют на основании диаграммы тангенциальных сил.
Mкр max 0,5T max a; Mкр min 0,5T min а.
Определяют max, , min m :
154

|
M |
кр |
;W |
bh |
2 |
|
f ( |
b |
|
|
|
|
|
|
; |
|
) 0,208 0,333 |
; |
|||
W |
|
|
||||||||
|
|
|
|
|
|
h |
|
n |
|
|
|
|
|
1 |
|
|
|
3 4 n |
|
n |
n |
|
2,5 3,0 |
. |
|
K |
|
|
|
|
|
|
|
|
|
|
|||||
|
|
|
|
|
|
|
|
2 |
||||||||
|
|
|
|
|
|
|
|
2 |
|
|
||||||
|
|
|
|
|
|
|
|
|
|
|
|
n |
n |
|
|
|
|
|
|
|
|
|
|
|
|
||||||||
|
|
|
а |
|
|
|
m |
|
|
|
|
|||||
|
|
|
|
|
|
|
|
|
|
|
|
|
|
|
|
13. СМЕСЕОБРАЗОВАНИЕ В КАРБЮРАТОРНЫХ ДВИГАТЕЛЯХ
Образование топливовоздушной смеси в карбюраторных двигателях происходит в системе впуска (в карбюраторе, во впускном трубопроводе, в цилиндре на такте всасывания и на такте сжатия) т.е. предшествует воспламенению.
Перед воспламенением желательно иметь однородную смесь паров топлива и воздуха. Получение однородной смеси затруднено малым промежутком времени (0,02 с. при n=3000 об/мин). Кроме того, соотношение полностью испарившегося бензина и воздуха при α=1 составляет 1:50, для природного газа 1:9.
Различают следующие системы внешнего смесеобразования:
1)карбюрация;
2)впрыск легкого топлива во впускной трубопровод;
3)форкамерно-фоскельное воспламенение;
4)газовые двигатели.
Факторы, влияющие на приготовление рабочей смеси:
1.Время.
2.Температура смеси, которая зависит от температуры окружающего воздуха, режима работы двигателя, степени подогрева и т.д. Увеличение температуры улучшает смесеобразование и повышается экономичность.
3.Свойства топлива, т.е. испаряемость.
4.Конструктивная схема двигателя (число карбюраторов и их конструкция, число цилиндров, впускной трубопровод, форма камеры сгорания).
5.Режим работы двигателя.
155
13.1.Требования к карбюратору
1.Обеспечить получение такого состава рабочей смеси α, чтобы получить наилучшие мощностные и экономические показатели работы двигателя на всех режимах.
2.Получение однородной смеси и равномерное её распределение по отдельным цилиндрам, чтобы улучшить экономичность и снизить токсичность двигателя.
3.Надежный пуск двигателя при различных условиях окружающей среды, а также устойчивая работа на холостом ходу.
4.Возможность изменения регулировки в зависимости от технического состояния двигателя и условий окружающей среды.
5.Сохранениеустановленнойрегулировкивтечениедлительноговремени.
6.Простота и надежность конструкции.
13.2.Физические основы смесеобразования
Топливо, попадая во впускной трубопровод, приобретает форму конуса. Угол конуса зависит от качества распыливания топлива и чем крупнее капли, тем больше они отжимаются к стенкам трубопровода за счет неравномерности скорости воздуха, что увеличивает угол конуса распыливания.
Увеличение угла конуса распыливания повышает возможность оседания топлива на стенки трубопровода в виде пленки. Пленка, попадая в цилиндр двигателя, смывает смазку с зеркала цилиндра, что усиливает износ цилиндра и, кроме того, увеличивается неравномерность состава рабочей смеси по цилиндрам, что ухудшает мощностные и экономические показатели работы двигателя. Если в распылитель карбюратора попадает воздух, распыливание топлива улучшается. Для этой цели применяют воздушные жиклеры.
13.3.Характеристика идеального карбюратора
испособы ее получения
Карбюратор, обеспечивающий оптимальную регулировку состава рабочей смеси, с помощью которой обеспечивается получение наилучших мощностных и экономических показателей работы двигателя на всех режимах, называется идеальным. Требования к идеальному карбюратору могут быть получены на основании регулировочных характеристик по составу смеси.
156
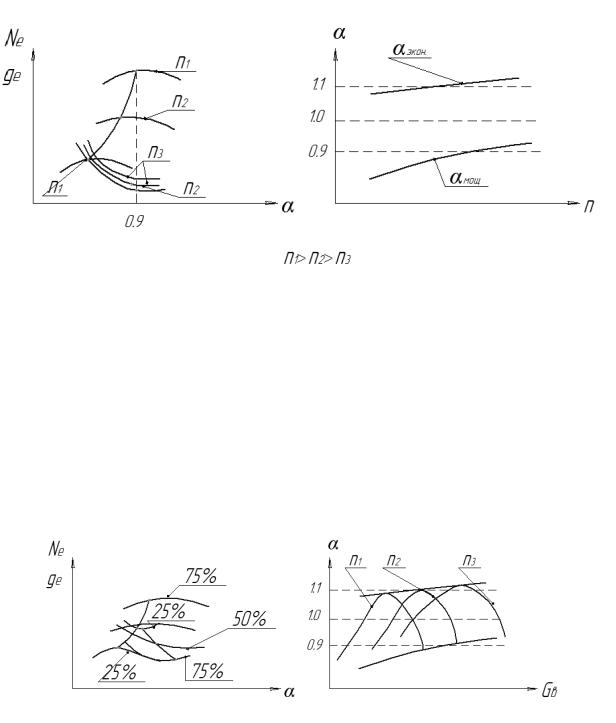
13.4. Скоростная характеристика по составу смеси
Представляет собой зависимость мощности и удельного расхода топлива от коэффициента избытка воздуха. Снимается для различных скоростных режимов. На основании этой характеристики строят зависимость коэффициента избытка воздуха от частоты вращения коленчатого вала (рис. 71).
Рис. 71. Характеристика идеального карбюратора и способы ее получения
13.5. Нагрузочная характеристика
Представляет собой зависимость мощности и удельного расхода топлива от коэффициента избытка воздуха. Снимается при различных положениях дросселя, но при постоянных оборотах. Характеристик снимается несколько (для различных оборотов) и на основании их получают характеристику, по которой определяют зону возможной регулировки карбюратора (рис. 72).
Рис. 72. Нагрузочная характеристика
157
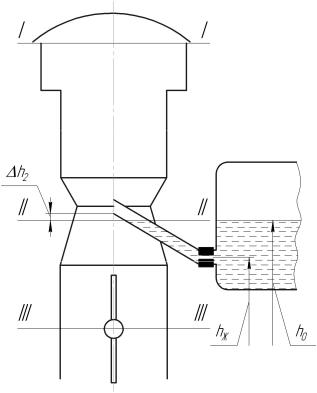
Режимы работы двигателя определяются в основном двумя параметрами – положением дроссельной заслонки и частотой вращения коленчатого вала, поэтому характеристику идеального карбюратора можно представить в виде ряда кривых GТ f (GB) и Т f (GB ) для различных скоростных режимов. Каждая кривая является идеальной нагрузочной характеристикой для данного скоростного режима. Верхняя огибающая кривая и нижняя ограничивают область возможной регулировки карбюратора.
13.6. Рабочий процесс элементарного карбюратора
Основой любого карбюратора является элементарный карбюратор. Для приближения его к идеальному применяют ряд систем, а поэтому изучение необходимо начинать с простейшего (рис. 73). Наибольшая скорость потока воздуха будет в сечение II–II, если диффузор имеет угол входа 30º, угол выхода 7º. В практике эти углы увеличивают для снижения высоты карбюратора. При этом наибольшее сжатие струи воздуха смещается от сечения II–II по ходу потока на 4– 5мм. Движение потока носит турбулентный характер, что улучшает распыливание топлива.
Рис. 73. Схема одножиклерного карбюратора
158
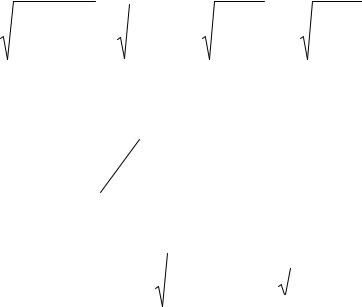
Из уравнения неразрывности потока имеем
Gв Wg fg 0 const ,
W – м/с; 0 – кг/м3; Gв – кг/с:
|
|
P W2 |
|
|
Pg |
|
Wg2 |
Wg2 |
|
|
|
|
|
||||||||
gh |
|
0 |
|
|
0 |
gh |
|
|
|
|
|
|
|
|
; |
|
|
|
; W 0; |
||
0 |
2 |
|
g |
2 |
2 |
|
|
|
|||||||||||||
0 |
|
|
g |
|
|
|
|
|
|
|
0 |
|
g |
0 |
|||||||
|
|
|
|
|
|
|
|
|
|
|
|
W2 |
|
|
|
|
|
||||
|
|
|
|
P P P |
|
(1 ) |
|
|
g |
; h h ; |
|
||||||||||
|
|
|
|
|
|
2 |
|
||||||||||||||
|
|
|
|
|
g |
0 |
g |
|
0 |
|
|
|
|
0 |
|
g |
|
|
Wg |
|
2 Pg |
|
|
1 |
|
|
2 Pg |
|
2 Pg |
, |
0(1 ) |
(1 ) |
|
0 |
0 |
|||||||
|
|
|
|
|
|
|
|
где – коэффициент скорости.
При отступлении от оптимальной формы диффузора происходит сжатие струи воздуха по отношению к площади диффузора.
|
fn |
С , |
|
|
|||||
|
fдиф |
|
|
||||||
где fn – площадь потока; |
fдиф – площадь диффузора, мин; C – ко- |
||||||||
эффициент сжатия. |
|
|
|
|
|
|
|
|
|
|
|
|
|
|
|
|
|
||
C g ;GВ |
g fg 0 |
2 Pg |
|
g fg |
|
. |
|||
|
2 Рg 0 |
||||||||
|
|||||||||
|
|
|
|
0 |
|
|
|
|
|
|
|
|
|
|
|
|
|
Коэффициент расхода воздуха g остается практически постоянным и только при малых разрежениях падает за счет увеличения толщины пограничного слоя. При уменьшении диаметра диффузора уменьшается Pg / PК за счет возрастания сопротивления. Для уве-
личения этого отношения применяют двойные и тройные диффузоры. При тройном диффузоре Pg / PК 2,5 2,6.
При этом кромку малого диффузора сдвигают по отношению с минимальным сечением большого диффузора на 4–5 мм. Суммарный
коэффициент расхода воздуха g у многодиффузорного карбюратора несколько ниже, поэтому общее проходное сечение увеличивают по сравнению с однодиффузорным карбюратором. У многодиффузорного карбюратора общая скорость потока несколько ниже, но расширяется диапазон изменения разрежений, где g почти не меняется
( g 0,7 0,9). Но значение g оказывает влияние на качество изго-
159