
- •ВВЕДЕНИЕ
- •Основные свойства металлов
- •Измерение твердости по методу Роквелла
- •Испытание твердости по методу Виккерса
- •Структурный анализ металлов и сплавов
- •Макроструктурный анализ металлов
- •Микроструктурный анализ сплавов
- •Порядок выполнения работы
- •Характеристика структурных составляющих
- •Правило концентраций и отрезков
- •Характеристики сталей
- •Классификация, маркировка углеродистых сталей
- •Характеристики чугунов
- •Серые чугуны
- •Ковкие чугуны
- •Белые чугуны
- •Высокопрочные чугуны
- •Порядок выполнения работы
- •Контрольные вопросы и задания
- •Термическая обработка стали
- •Превращения, происходящие в стали при охлаждении
- •Выбор скорости охлаждения детали
- •Определение структуры углеродистой стали после закалки
- •Выбор температуры закалки
- •Отпуск углеродистых сталей
- •Порядок выполнения работы
- •Контрольные вопросы
- •Маркировка легированных сталей
- •Назначение легирующих элементов и их влияние на свойства стали
- •Классификация сталей
- •Классификация по назначению
- •Классификация конструкционных сталей
- •Структура легированных сталей после термической обработки
- •Конструкционная сталь 30ХГСА
- •Быстрорежущая сталь Р6М5
- •Износостойкая сталь 110Г13Л
- •Порядок выполнения работы
- •Контрольные вопросы и задания
- •Медные сплавы
- •Алюминиевые сплавы
- •Порядок выполнения работы
- •Краткие теоретические сведения
- •Отжиг дуралюмина
- •Закалка и старение дуралюмина
- •Порядок выполнения работы
- •Контрольные вопросы и задания
- •Общие сведения о процессах листовой штамповки
- •Расчет диаметра заготовки
- •Определение номинальных размеров рабочих частей вырубного штампа
- •Определение усилий вырубки
- •Выполнение расчетов и эксперимента по операции вытяжки при изготовлении детали
- •Определение необходимого количества операций вытяжки
- •Определение номинальных размеров рабочих частей вытяжного штампа
- •Определение усилий вытяжки
- •Содержание отчета по лабораторной работе
- •Контрольные вопросы
- •Выбор методов и способов производства заготовок объемной штамповкой
- •Определение класса точности поковки
- •Определение группы стали
- •Определение степени сложности поковки
- •Определение исходного индекса
- •Определение допусков на размеры поковки
- •Назначение напусков
- •Разработка чертежа холодной поковки
- •Разработка чертежа горячей поковки
- •Порядок выполнения работы
- •Контрольные вопросы и задания
- •Приложение
- •Электрическая сварочная дуга, ее характеристики
- •Режимы ручной дуговой сварки
- •Электроды для ручной дуговой сварки
- •Определение технологических коэффициентов и выбор оптимального режима сварки
- •Оборудование, инструмент и приспособления для проведения экспериментальной части лабораторной работы
- •Порядок выполнения экспериментальной части работы
- •Контрольные вопросы и задания
- •Основные способы литья
- •Разработка чертежа отливки
- •Расчет литниковой системы
- •Порядок выполнения работы
- •Библиографический список
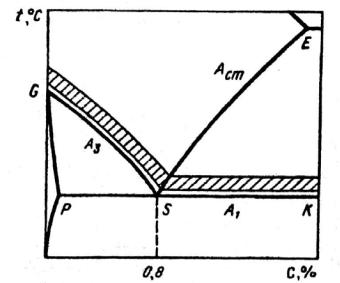
Выбор температуры закалки
|
И |
Д |
|
Рис. 3.12. Температуры нагрева углеро- |
|
дистых сталей под закалку: заштрихова- |
|
на область оптимальных температур |
|
А |
|
На практике температура закалки определяется по диаграмме со- |
стояния Fe – Fe3C в зависимости от содержания углерода (рис. 3.12). Температура закалки доэвтектоидных сталей (С < 0,8%) – tзак = А3 + (30 - 50)
ºC, а для заэвтектоидной стали (С > 0,8%) – tзак=А1 + (30 - 50) ºC. Критическая температура А1 располагается на линии PSK (727 ºC), а температура
А3 |
– на линии GS диаграммы состояния. |
|
|
|
б |
|
Отпуск углеродистых сталей |
|
|
и |
|
А1 |
Сущность отпуска – нагрев закаленной стали до температуры ниже |
|
(727 ºC), выдержка и охлаждение с любой скоростью. Вид отпуска и его |
||
|
С |
|
назначение определяются температурой нагрева. |
||
|
Низкий отпуск (150 – 250) ºC применяется для повышения твердости |
и износостойкости поверхностного слоя деталей, испытывающих трение в процессе работы (зубья зубчатых колес, кулачки распределительных валов, режущий и измерительный инструмент и т.д.). В процессе нагрева закаленной стали из мартенсита выделяется часть углерода в виде Fe2C. Уменьшение количества растворенного углерода снижает тетрагональность мартенсита, внутренние напряжения и твердость. Структура стали после низкого отпуска – мартенсит отпуска (рис. 3.13, а).
Средний отпуск (300 – 500) ºC используется для получения в деталях высокого предела упругости, текучести (пружины, рессоры, мембраны и
32
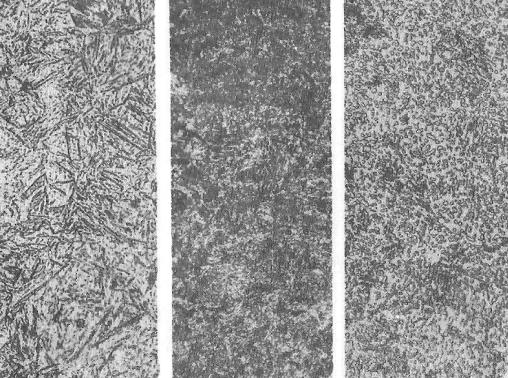
т.д.). При нем завершается распад мартенсита, из которого выделяется весь избыточный углерод. Образовавшаяся механическая смесь феррита и цементита имеет зернистое строение (рис. 3.13, б) и называется трооститом отпуска. Полностью снимаются внутренние напряжения, вызванные мартенситным превращением.
|
|
|
|
|
|
И |
|
|
|
|
|
|
Д |
|
|
|
|
|
|
А |
|
|
|
|
|
б |
|
|
|
||
а |
и |
|
|
|
в |
||
Рис. 3.13. Микроструктуры отпущенной стали (0,6% С), х 500: а – мартенсит отпуска; |
|||||||
|
б – троост |
т отпуска; в – сорбит отпуска |
|
||||
|
С |
|
|
|
|
|
|
Высокий отпуск (550 – 680) ºC служит для получения хорошего сочетания прочностных и вязкостных свойств в деталях, работающих на ударные, знакопеременные, вибрационные и циклические нагрузки (валы, зубчатые колеса, шатуны двигателей и т.д.). В указанном интервале температур ферритно-цементитная смесь троостита отпуска коагулирует с образованием более крупной зернистой ферритно-цементитной смеси, называемой сорбитом отпуска (рис. 3.13, в). Закалку и высокий отпуск называют улучшением, а стали, подвергаемые улучшению, называются улучшаемыми. Обычно они содержат (0,3 – 0,5)% С (стали 30, 35, 40, 45, 50).
Порядок выполнения работы
1. Изучить теорию процессов термического упрочнения с анализом микроструктур.
33
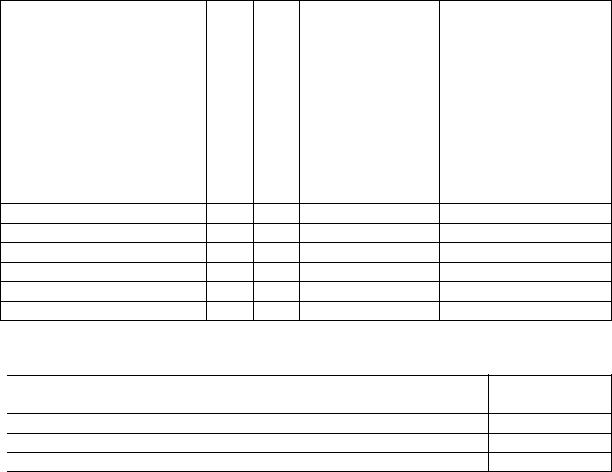
2.Определить структуру стали (марка выбирается по указанию преподавателя из приложения) после ее непрерывного охлаждения по диаграмме распада аустенита. При этом необходимо ответить на вопросы, приведенные в конце приложения.
3.Образцы из различных сталей нагреть в электропечи до соответствующей температуры закалки и охладить каждый в воде, минеральном масле или на воздухе. Замерить твердость образцов после охлаждения и определить структуру. Занести данные в табл. 3.2.
Таблица 3.2. Свойства сталей до и после закалки
Марка стали |
Предполагаемыеструктуры |
после закалки |
% С |
Исходнаяравновесная структура |
Твердостьв состоянии |
поставки НВ, МПа |
Критическаяточка под |
закалку |
Структура нагрева под закалку |
Температуранагрева под закалку, °C |
Температуранагрева |
печи, °C |
Время нагрева |
и выдержки, мин |
Среда охлаждения |
||||
|
|
|
|
|
|
|
|
|
|
|
|
|
|
Д |
И |
||||
20 |
Мз |
|
|
|
|
|
|
б |
|
|
|
|
|||||||
|
|
|
|
|
|
|
|
|
|
|
|
|
|||||||
45 |
Мз |
|
|
|
|
|
|
|
|
А |
|
|
|
|
|
|
|||
У8 |
Мз |
|
|
|
и |
|
|
|
|
|
|
||||||||
У8 |
Тз |
|
|
|
|
|
|
|
|
|
|||||||||
|
|
|
|
|
|
|
|
|
|
|
|
|
|
||||||
У8 |
Сз |
|
|
|
|
|
|
|
|
|
|
|
|
|
|
||||
У12 |
Мз |
|
|
|
|
|
|
|
|
|
|
|
|
|
|
|
|
||
|
|
|
|
|
С |
|
|
|
|
|
|
|
|
|
|
||||
Таблица 3.3. Твердость |
структура стали после отпуска |
|
|||||||||||||||||
Марка |
|
% С |
Температура |
|
Время выдержки |
Твердость стали |
|||||||||||||
стали |
|
|
|
отпуска, ºC |
|
при отпуске, мин |
|
|
|
|
|
||||||||
У8 |
|
|
|
|
|
|
|
|
|
|
|
|
|
|
|
|
|
|
|
У8 |
|
|
|
|
|
|
|
|
|
|
|
|
|
|
|
|
|
|
|
У8 |
|
|
|
|
|
|
|
|
|
|
|
|
|
|
|
|
|
|
Скорость охлаждения детали, °C /с |
Твердость после закалки HRC |
Структура после закалки |
|
|
|
Структура
стали
4.Закаленные образцы из стали У8 (HRC 60–65) подвергнуть отпуску при температурах 200, 400, 600 ºC с охлаждением на воздухе. Замерить твердость образцов после отпуска. Определить структуру. Полученные данные занести в табл. 3.3.
5.Сделать выводы по проделанным экспериментам, построить в масштабе зависимости: а) твердости после закалки от содержания углеро-
да при Vохл = const; б) твердости после закалки от скорости охлаждения де-
тали при% С = const.
34
Контрольные вопросы
1.В чем состоит цель и сущность закалки?
2.Что такое перлит, сорбит, троостит, бейнит, мартенсит?
3.В чем заключается условие закалки?
4.От чего зависит скорость охлаждения детали и критическая скорость закалки стали?
5.Какова температура закалки стали в зависимости от содержания углерода в стали?
6.В чем заключается причина возникновения паровой пленки вокруг детали при ее погружении в охлаждающую жидкость во время закалки. Как устранить паровую пленку?
7.Какова структура стали после закалки?
8.В чем заключаются цель и сущность отпуска?
9.Каковы назначение, температура, скоростьИохлаждения и структура низкого отпуска?
10.Каковы назначение, температураД, скорость охлаждения и структура среднего отпуска?
11.Каковы назначение, температура, скорость охлаждения и структура высокого отпуска? Аб
1. |
Вал редуктора з стали 50. |
|
2. |
Пружина з стали 65. |
|
3. |
Зубья зубчатого колеса з стали 30 . |
|
4. |
Кулачок распределительногои |
вала из стали 45. |
5. |
Рессора из стали 55. |
|
6. |
Буксирный крюк из стали 40. |
|
7. |
СверлоСиз стали У10А. |
|
8. Рабочая часть сверла из стали У12А. 9. Коленчатый вал из стали 35.
10. Мембрана из стали 60.
11. Шарик для пресса Бринелля из стали У9А. 12. Шарик шарикоподшипника из стали У11А. 13. Рабочая часть зубила из стали У8А.
14. Шаровая опора из стали 35.
15. Ось из стали 60.
16. Втулка из стали У10А.
17. Втулка из стали У7А.
35