
2390
.pdfПериод изотермического прогрева
3. Приход тепла, кДж/ч:
3.1. Тепло экзотермии цемента
Q3э=0,0023Qэ28(В/Ц)0,44t11τ11Gц= =0,0023·420·0,60,44·100·3·600=139 104.
3.2. Тепло острого пара
Q3п=G3п(i1 ik)= G3п ·2261.
Суммарный приход тепла в зоне изотермического прогрева
2
Q3прих Q3э+Q3п =139 104+2261 G3п .
1
4. Расход тепла, кДж/ч:
4.1.Тепло смеси, заполняющей свободный объем, остается в камере, поэтому в расходной статье не учитываем.
4.2.Тепло, потерянное через ограждения камеры:
Q4ст=3,6kстFст(t4 to.c)=3,6·1,04·352,5·(100 20)=105 581,
где Fст=(2·Lк+2Вк)НII=(2·28,4+2·2,79)· 5,65=352,5 м2;
kст= |
|
|
|
|
1 |
|
|
|
|
|
|
|
|
|
|
|
1 |
|
|
|
|
1,04. |
|
|
|
ст |
ут |
|
1 |
|
|
1 |
|
0,17 |
|
0,05 |
|
|
1 |
|
|||||||
1 |
|
|
|
|
|
|
|
|
|
|
|
||||||||||||
|
|
|
|
|
|
|
|
|
|
|
|
|
|
|
|
|
|
|
|
|
|||
|
1 |
ст |
ут |
2 |
52 |
1,56 |
0,063 |
23,2 |
|
|
|||||||||||||
|
|
|
|
|
|
|
|
|
Q4пот=3,6kпотFпот(t4 to.c)=3,6·0,61·79,2·(100 20)=13 914,
где Fпот=Lк/2·Вк =28,4·2,79=79,2 м2;
kпот= |
|
|
1 |
|
|
|
|
|
|
|
1 |
|
|
|
|
0,61. |
|
|
|
ут |
|
1 |
|
|
1 |
|
0,1 |
|
|
1 |
|
||||
|
1 |
|
|
|
|
|
|
|
|
|
|
||||||
|
1 |
ут |
2 |
52 |
0.063 |
23,2 |
|
|
|||||||||
|
|
|
|
|
|
|
Q4огр= Q4ст +Q4пот=105 581+13 914=119 495. 4.3. Нагрев сухой части изделий на (100 – 72,8)=27,2 0С
Q4с=(Gз+Gц)сс·27,2=(600+4094)0,84·27,2=107 249.
219
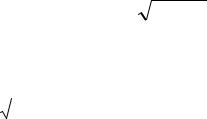
4.4. Нагрев оставшейся в бетоне воды до 100 0С
Q4в=Gв`·св·27,2=310·4,2·27,2=35 414.
Суммарный расход тепла в период изотермического прогрева
4
Q4 расх Q4огр.+Q4с+Q4в=119 495+107 249+35 414=262 158.
1
Тепловой баланс зоны изотермического прогрева
2 4
Q3прих Q4расх .
1 1
139 104+2261Gзп=262 158;
2261Gзп=12 054;
Gзп=54кг/ч.
Q3кал=1 648 762.
Удельный расход пара на нагрев изделий в зоне изотермического прогрева
q |
2 |
|
Qзп |
|
54 |
26кг/м3. |
V |
|
|||||
|
|
2,12 |
|
|||
|
|
|
б |
|
|
|
Удельный расход пара в зоне подогрева и изотермического прогрева q q1 q2 92 26 118кг/м3.
Часовой расход пара по вертикальной камере составит
D=G1п+G3п=196+26=222 кг/ч.
Диаметр магистрального трубопровода (см. 3.18.1) d |
4S / , |
где сечение паропровода S D/3600 п ; ρп – плотность пара, кг/м3; ω –
скорость движения пара в паропроводе 20…30 м/с, тогда при D=222 кг/ч,
ρп=1,12 кг/м3 и ω=20 м/с:
S=222/3600·1,12·20=0,003 м2, d |
|
|
4 0,003/ =0,06 м. |
3.18.7. Расчет пакетировщика
Задание и исходные данные. Запроектировать установку для тепловлажностной обработки железобетонных изделий в пакетах термоформ для завода производительностью 29 тыс.м3 бетона в год.
Дополнительные данные. По изделиям: плиты покрытий размером 5,8×2,6×1,0 м; влажность 6 %; плотность бетона 2000 кг/м3, теплоемкость бетона 0,9 кДж/(кг·0С), стали – 0,48 кДж/(кг·0С), температура при входе на
220
термообработку 20 0С, расход цемента 400 кг/м3 бетона, марка цемента М400, водоцементное отношение В/Ц=0,3.
По режиму термообработки: подъем температуры до 100 0С в течение 2 ч, изотермическая выдержка 3,5 ч. Пар из паропровода поступает с давлением 0,2 МПа и влажностью 15 %.
Прочие данные: расход арматуры на 1 м3 бетона 90 кг, вес термоформы 4,5 т, размер термоформы по изделию, глубина парового пространства 0,2 м, средняя температура наружной поверхности формы 40 0С. Температура конденсата 80 0С, воздуха в цехе 15 0С.
Технологический расчет
Режим рабочего времени завода при пятидневной неделе и двухсменной работе по 8 ч составляет 249 сут (по 2010 г.). Плановые остановки для конвейерной линии 13 сут, затем сокращенные на 1 ч предпраздничные дни (5 дней по 2010 г).
Тогда количество рабочих часов: 16×236 – 5=3771 ч. Часовая производительность завода Gч=29 000/3771=7,7 м3 бетона в час.
Объем одного изделия 5,8×2,6×0,1=1,52 м3. Производительность завода G’ч=7,7/1,52=5,06 шт/ч.
При плотности бетона 2000 кг/м3 масса одного изделия составит
1,52·2000=3040 кг.
Производительность завода 5,06·3040=15 400 кг/ч.
Количество термоформ с плитами в пакете принимаем равным 7. При времени теплообработки 5,5 ч часовая производительность одного пакетировщика составляет
G ' |
7 |
1,27 шт/ч, G 1,27 1,52 1,96 м3 /ч, |
|
5,5 |
|||
ч |
|
||
|
|
Gч '' 1,27 3040 3861кг/ч. |
Количество пакетировщиков для заданной производительности заво-
да равно п = 5,06/1,27 = 4,01шт.
К установке принимаем 4 пакетировщика емкостью 7 изделий.
Теплотехнический расчет
Составляем баланс тепла на 1 ч работы аппарата с целью определения расхода пара.
Часовой приход тепла (кДж/ч)
1. С паром
Q1 Gnix ,
221
где Gп – часовой расход пара, принятый за неизвестную величину; ix – энтальпия пара со степенью сухости, х =1 – 0,15=0,85,
ix=i/+rx=504+2002·0.85=2394 кДж/ч.
i/ и r – энтальпия жидкости и теплота парообразования.
По паровым таблицам при Р=0,2 МПа (см. табл. П.17).
Q1 Gn 2394.
2. От экзотермических реакций твердения цемента (кДж/кг цемента):
Qэ.ц 0,0023Qэ28(В/ Ц)0,44tср.б ,
где Qэ28 – тепловыделение цемента в зависимости от марки М400,
Qэ28=418 кДж/кг; tcр.б=(tн+ tк)0,5=(20+100)0,5=60 0С; τ – время тепловой обработки, τ=5,5 ч;
Qэ.ц=0,0023·418·0,30,44·60·5,5=184 кДж/кг.
При расходе цемента на 1 м3 бетона Gц=400 кг тепловыделение бетона за час составит
Q |
|
Qэ.цVбGц |
|
184 1.96 400 |
26200кДж/ч. |
|
|
||||
э.б |
|
|
|
5.5 |
|
|
|
|
|
Всего приход тепла:
Q1 Qэ.ц Gп 2394 26 103 кДж/ч.
Часовой расход тепла
1. На прогрев бетона от 20 до 100 0С
Q1/ Gб// сб (tk tн ) 3861 0,9(100 20) 278 103 кДж/ч,
где G//б – часовая производительность по массе бетона, G//б=3861 кг; сб – теплоемкость бетона, сб=0,9 кДж/(кг·0С); tк и tн – конечная и начальная температуры бетона, tк =100 0С и tн=20 0С.
2. На нагрев арматуры и форм:
q2/ (Gарм Gф )gб/ сарм(tk tн )
(4500 136)1,27 0,48(100 20) 226 103 кДж/ч,
где Gарм – масса арматуры в одном изделии, Gарм=1,59·90=136 кг; Gф – вес одной термоформы, кг; G/б – часовая производительность пакетировщика, шт.; са – теплоемкость стали, са=0,48 кДж/(кг·ºС); tк и tн – конечная и начальная температуры арматуры и формы, ºС.
222
3. На нагрев влаги бетона: |
|
|
|
|
|||||
Q3/ Gб// |
|
|
св (tk |
tн ) 3861 |
|
6 |
4,18(100 20) 77,2 103 |
кДж/ч, |
|
100 |
100 |
||||||||
|
|
|
|
|
где ω – влажность бетона, %.
4. Потери тепла (кДж/ч) во внешнюю среду через боковые стенки паровой полости и бортоснастки:
Q4/ с (tст tв )F 3.6,
где αс – суммарный коэффициент теплоотдачи, для металлической стенки с температурой 400С принимают αс=10,69 Вт/(м·0С) (см. табл. П.29); F – боковая поверхность ограждения – определяем по произведению периметра сторон на высоту всех термоформ; глубина паровой полости составляет 0,2 м, толщина изделия 0,1 м, высота всех термоформ (0,2+0,1)·7=2,1 м;
F=(5,8·2+2,6·2)2,1=35,28 м2;
Q/4=10,69 (40-15)35,28·3,6=34·103 кДж/ч.
5. Потери тепла с конденсатом. В конденсат превращается весь пар, отдавший свое тепло. Ввиду герметичности паровых рубашек утечка пара отсутствует:
Q/5=Gncktk=Gn·4,18·80=Gп354,
где ск– теплоемкость воды, ск=4,18 кДж/(кг·0С); tк – температура конденсата, 0С.
Уравнение баланса тепла: 2394Gn+26,2·103=278·103+226·103+77,2·103+34·103+354Gп,
отсюда Gn =589·103/2040=288,0 кг/ч.
Расход пара на 1м3 бетона 288/1,96=147 кг/м3.
Баланс тепла пакетировщика сведен в табл. 3.16.
|
|
Таблица 3.16 |
|
Сводный баланс тепла пакетировщика |
|
||
|
|
|
|
Статья баланса |
Количество тепла |
||
|
|
||
кДж/ч |
% |
||
|
|||
|
|
|
|
Часовой приход тепла |
|
||
|
|
|
|
1. С паром |
691·103 |
96,4 |
|
2. От экзотермических реакций |
26·103 |
3,6 |
|
Всего |
717·103 |
100 |
|
223 |
|
|
|
|
|
Окончание табл. 3.16 |
|
|
Часовой расход тепла |
|
|
|
|
|
|
|
|
1. |
На нагрев бетона |
278·103 |
|
39 |
2. |
На нагрев арматуры и форм |
226·103 |
|
31,3 |
3. |
На нагрев влаги бетона |
77,2·103 |
|
10,8 |
4. |
Потери тепла во внешнюю среду |
34·103 |
|
4,7 |
5. |
Потери тепла с конденсатом |
102·103 |
|
14,2 |
Невязка баланса |
-200 |
|
0,0021 |
|
|
|
|
|
|
|
Всего |
717·103 |
|
100 |
Тепловой баланс пакетировщика соблюдается.
224
4. ЭКОЛОГИЧЕСКИЕ ПРОБЛЕМЫ ИСПОЛЬЗОВАНИЯ ТЕПЛА
4.1. Токсичность продуктов сгорания
Продукты сгорания оказывают определяющее влияние на энергетические и экономические показатели различных теплотехнических установок.
Однако помимо этих продуктов при сгорании образуется и ряд других веществ, которые вследствие их малого количества не учитываются в энергетических расчетах, но определяют экологические показатели топок, печей, тепловых двигателей и других устройств современной теплотехники.
В первую очередь к числу экологически вредных продуктов сгорания следует отнести так называемые токсичные газы.
Токсичными называют вещества, оказывающие негативные воздействия на организм человека и окружающую среду. Основными токсичными веществами являются оксиды азота NO, оксид углерода СО, различные углеводороды СН, сажа и соединения, содержащие свинец и серу.
Оксиды азота. Если температура превышает 1500 К, то азот и кислород воздуха вступают в химическое взаимодействие по цепному механизму, образуется главным образом оксид азота NO, который затем в атмосфере окисляется до диоксида NO2.
Образование NO увеличивается с ростом температуры газов и концентрации кислорода и при данной температуре не зависит от углеводородного состава топлива.
Зависимость образования NO от температуры создает определенные трудности с точки зрения увеличения термического КПД теплового двигателя. Например, при увеличении максимальной температуры цикла Tz до 3000 К термический КПД цикла Карно ηtk и Отто ηto возрастает соответственно до 0,9 и 0,66, но расчетная максимальная концентрация NO в продуктах сгорания достигает при этом 10 000 ррm, или 1,1 % по объему (рис. 4.1).
225
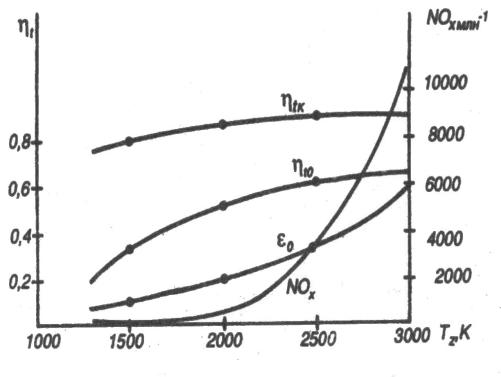
Рис. 4.1. Влияние Тz на образование NOx, термический КПД цикла Карно ηск Отто ηю (To=288, λ0=3,5)
Находящийся в атмосфере NO2 представляет собой газ красноватобурого цвета, обладающий при больших концентрациях удушливым запахом.
NO2 оказывает негативное воздействие на слизистые оболочки глаз и носа, а также на нервную систему человека.
Оксид углерода СО образуется во время сгорания при недостатке кислорода или при диссоциации CO2.
Основное влияние на образование СО оказывает состав смеси: чем она богаче, тем выше концентрация СО.
Оксид углерода – бесцветный и не имеющий запаха газ. При вдыхании вместе с воздухом он интенсивно соединяется с гемоглобином крови, что уменьшает ее способность к снабжению организма кислородом. Симптомы отравления организма газом – головная боль, сердцебиение, затруднение дыхания и тошнота.
Углеводороды СН состоят из исходных или распавшихся молекул топлива, которые не принимали участия в сгорании. Углеводороды появляются в отработавших газах (ОГ) двигателей внутреннего сгорания вследствие гашения пламени вблизи относительно холодных стенок камеры сгорания, в «защемленных» объемах, находящихся в вытеснителях и в
226
зазоре между поршнем и цилиндром над верхним компрессионным кольцом.
В дизелях углеводороды образуются в переобогащенных зонах смеси, где происходит пиролиз молекул топлива. Если в процессе расширения
вэти зоны не поступит достаточное количество кислорода, то СН окажется
всоставе ОГ.
Количество различных индивидуальных углеводородов, входящих в эту группу токсичных веществ, превышает 200. В тех концентрациях, в которых СН содержится в воздухе, например, в зонах с интенсивным движением автотранспорта, они не приносят непосредственного вреда здоровью человека, однако могут вызывать реакции, которые ведут к образованию соединений, вредных даже при незначительной концентрации.
Так, углеводороды под действием солнечных лучей могут взаимодействовать с NOх, образуя биологически активные вещества, которые раздражающе действуют на органы дыхательных путей и вызывают появление так называемого смога.
Особое влияние оказывают выбросы бензола, толуола, полициклических ароматических углеводородов (ПАУ) и в первую очередь бензопирена C20H12. Эта группа высокотоксичных веществ образуется в результате пиролиза легких и средних фракций топлива при температуре 600...700 К. Такие условия возникают вблизи холодных поверхностей цилиндра при наличии там несгоревших углеводородов. Количество ПАУ в ОГ тем больше, чем выше концентрация в топливе бензола. ПАУ относятся к так называемым канцерогенным веществам, они не выводятся из организма человека, а со временем накапливаются в нем, способствуя образованию злокачественных опухолей.
Сажа представляет собой твердый продукт, состоящий в основном из углерода. Кроме углерода в саже содержится 1..3 % (по массе) водорода.
Сажа образуется при температуре выше 1500 К в результате объемного процесса термического разложения (пиролиза) при сильном недостатке кислорода. Образование сажи зависит от температуры и давления газов, а также от вида топлива. При одинаковом количестве атомов углерода по степени увеличения склонности к образованию сажи углеводороды располагаются следующим образом: парафины, олефины, ароматики.
Наличие сажи в ОГ дизелей обуславливает черный дым на выпуске. Сажа представляет собой механический загрязнитель носоглотки и легких. Большая опасность связана со свойством сажи накапливать на поверхности своих частиц канцерогенные вещества и служить их переносчиком.
Сажа – не единственное твердое вещество, содержащееся в ОГ. Другие твердые вещества образуются из содержащейся в топливе серы, а также в виде аэрозолей масла и несгоревшего топлива. Все вещества, которые
227
оседают на специальном фильтре при прохождении через него ОГ, получили общее название – частицы.
Содержание в ОГ продуктов неполного сгорания (СО, СН и сажи) нежелательно не только из-за их токсичности, но и потому, что при неполном сгорании топлива недовыделяется часть тепла, а это обуславливает ухудшение экономических показателей тепловых установок.
Свинец и сера. Примерно 50...70 % свинца, находящегося в бензине (мазуте), попадает вместе с ОГ в атмосферу в форме свинцовых солей, т.е. в виде частиц диаметром меньше 1 мкм. Эти частицы проникают в организм человека вместе с воздухом и через кожу. Соединения свинца очень ядовиты и не выводятся из организма, накапливаясь в нем. Они негативно воздействуют на центральную нервную систему, вызывая нервные и психические расстройства.
Сера, содержащаяся в дизельном топливе, мазуте и угле, выбрасывается в атмосферу после сгорания этих топлив в форме диоксида SO2, который очень вреден для растений, способствует возникновению «кислотных» дождей.
Присутствие в ОГ соединений свинца и серы делает невозможным использование каталитических нейтрализаторов, предназначенных для снижения токсичности ОГ.
Некоторые токсичные вещества после того, как они попадают в атмосферу в составе продуктов сгорания, претерпевают дальнейшие преобразования. Например, при наличии в атмосфере углеводородов (или их радикалов), оксидов азота и оксида углерода при интенсивном ультрафиолетовом излучении солнца образуется озон О3, являющийся сильнейшим окислителем и вызывающий при соответствующей концентрации ухудшение самочувствия людей.
При высоком содержании в малоподвижной и влажной атмосфере NO2, О3 и СН возникает туман коричневого цвета, который получил название «смог» (от английских слов Smoke – дым и fog – тупая). Смог является смесью жидких газообразных компонентов, он раздражает глаза и слизистые оболочки, ухудшает видимость на дорогах. Основными источниками выброса токсичных продуктов сгорания являются автомобили, промышленность, тепловые и электрические станции. В некоторых городах содержание в атмосфере токсичных продуктов сгорания превышает предельно допустимую концентрацию в несколько десятков раз.
Для борьбы с этим злом в большинстве стран мира приняты соответствующие законы, ограничивающие допустимое содержание токсичных веществ в продуктах сгорания, выбрасываемых в атмосферу.
Выполнение предписываемых соответствующими законами норм разрешенного максимального выброса стало одной из центральных задач
228