
2390
.pdf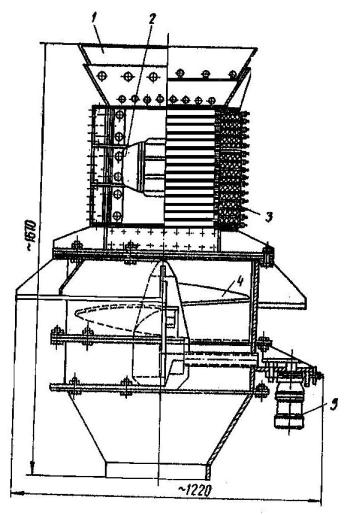
действия. В прокатной технологии, особенно нуждающейся в пароразогреве бетонной смеси, применяют смесители принудительного действия.
Метод 4. Электроразогрев бетонной смеси также относится к числу наиболее изученных методов получения теплого бетона. Известны порционный и непрерывный способы электроразогрева смеси с помощью электродных установок, расположенных непосредственно у места формования изделий. Для каждого конкретного случая рассчитывается своя установка периодического (бетоноукладчик или механизированный бункер с электродным устройством) или непрерывного действия (средства, транспортирующие бетонную смесь между электродами) (рис. 3.40 и 3.41).
Рис.3.40. Установка непрерывного действия для электроразогрева бетонной смеси производительностью 5…6 м3/ч: 1 – приемный бункер; 2 – вибратор; 3 – электродная камера; 4 – шнек; 5 – привод шнека
159
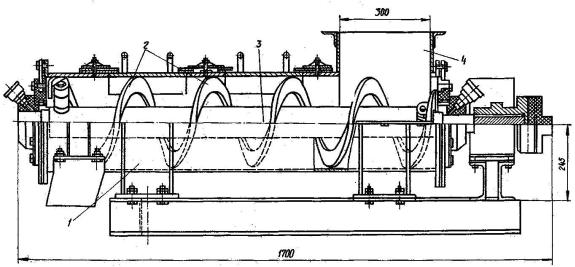
Рис. 3.41 Установка непрерывного действия для электроразогрева |
бетонной |
смеси с вращающимися электродами шнекового типа: 1– корпус; 2 – |
винтовые |
лопасти-электроды; 3 – вал из диэлектрика; 4 – приемное устройство |
|
Независимо от технического решения электроразогрева смеси метод требует повышенных электрических мощностей − на разогрев 1 м3 бетонной смеси с 20 до 60 °С в течение 10 мин требуется мощность 250 кВт. Нагрев бетонной смеси производится в течение 8…15 мин. Температура нагрева может достигать 50…80 °С. Для бетонов на цементах с высокой экзотермией и при толщине изделий 30…40 см нагрев можно ограничить температурой 50…60 °С. При быстром нагреве бетонной смеси до 50…70 °С тепловыделение гидратации цемента достигает большой величины. Вследствие этого температура бетона поддерживается на высоком уровне в течение 4…6 ч, а в течение 1,5…2 ч даже возрастает на 5…10 °С в зависимости от вида цемента, изделия и условий твердения.
Варианты технологических схем и оборудования для производства сборных железобетонных изделий на основе применения теплого бетона приведены в табл. 3.5. Рассмотренные в ней производственные варианты классифицированы по способам приготовления теплого бетона. Однако это не исключает возможности применения в условиях одного предприятия нескольких способов разогрева бетонной смеси. Возможно, например, сочетание централизованного разогрева заполнителей или смеси и децентрализованного разогрева бетонных смесей методами пароили электроразогрева.
160
|
|
|
|
|
|
Таблица 3.5 |
|
|
Варианты технологических схем и оборудования |
|
|||||
|
|
|
|
|
|
|
|
|
Организа- |
|
|
Обору- |
Матери- |
Оборудова- |
|
Способ |
|
|
дование |
ал, транс- |
ние для |
||
приго- |
ционный |
Пост |
|
для при- |
порти- |
транспорти- |
|
принцип |
Оборудование |
||||||
товления |
разо- |
готовле- |
руемый к |
ровки мате- |
|||
теплого |
получения |
грева |
для разогрева |
ния бе- |
месту |
риала к мес- |
|
бетона |
теплой |
|
|
тонной |
формова- |
ту формова- |
|
смеси |
|
|
|||||
|
|
|
смеси |
ния |
ния |
||
|
|
|
|
||||
1 |
2 |
3 |
4 |
5 |
6 |
7 |
|
Разогрев |
|
Бетоно- |
Теплообмен- |
|
|
|
|
воды и |
|
ные аппараты: |
|
Разогре- |
Бетонораз- |
||
инерт- |
|
смеси- |
бункера-нако- |
Бетоно- |
тая (теп- |
даточные |
|
Централи- |
тельное |
||||||
ных ма- |
зованный |
отделе- |
пители, емко- |
смеси- |
лая) бе- |
устройства, |
|
териалов |
|
ние |
сти порцион- |
тель БСО |
тонная |
бетоноук- |
|
(запол- |
|
ные, бето- |
|
смесь |
ладчики |
||
|
(БСО) |
|
|||||
нителей) |
|
носмесители |
|
|
|
||
Разогрев |
|
|
|
Бетоно- |
|
|
|
воды и |
|
Посты |
Емкости пор- |
Инертные |
Транспорте- |
||
|
смеси- |
||||||
инерт- |
Децентра- |
формо- |
ционные или |
тель ин- |
мате- |
ры |
|
ных ма- |
лизо- |
вания |
бетоносмеси- |
диви- |
риалы, |
ленточные, |
|
териалов |
ванный |
вода, це- |
|||||
изделий |
тели |
дуаль- |
водопровод |
||||
(запол- |
|
|
|
ный |
мент |
|
|
нителей) |
|
|
|
|
|
||
|
|
|
|
|
|
||
|
Децентра- |
|
|
|
|
Бетонораз- |
|
|
лизован- |
|
|
|
|
||
|
|
|
Бетоно- |
Холодная |
даточные |
||
|
ный разо- |
|
Электродное |
||||
|
То же |
смеси- |
бетонная |
устройства, |
|||
Электро- |
грев до ук- |
|
устройство |
тель БСО |
смесь |
бетоноук- |
|
разогрев |
ладки сме- |
|
|
|
|
ладчики |
|
бетонной |
си в форму |
|
|
|
|
||
|
|
|
|
|
|||
смеси |
То же по- |
Пост |
Электродное |
|
|
|
|
|
сле уклад- |
|
|
|
|||
|
прогре- |
устройство, |
То же |
То же |
То же |
||
|
ки смеси в |
||||||
|
форму |
ва |
индуктор |
|
|
|
|
|
|
|
|
|
|
||
Парора- |
|
Бетоно- |
Система па- |
|
Разогре- |
Бетонораз- |
|
зогрев |
Централи- |
смеси- |
роснабжения |
Бетоно- |
тая |
даточные |
|
бетонной |
зованный |
тель |
бетоносмеси- |
смеси- |
бетонная |
устройства, |
|
тель БСО |
бетоноук- |
||||||
смеси |
|
БСО |
теля |
|
смесь |
ладчики |
|
|
|
|
|
|
|
161
Окончание табл.3.5
1 |
2 |
3 |
4 |
5 |
6 |
7 |
|
|
Децентра- |
Посты |
|
Бетоно- |
|
|
|
|
лизо- |
фор- |
Бетоносмеси- |
смеси- |
Инертные |
Транспорте- |
|
|
ванный |
мова- |
тели индиви- |
тель |
ма- |
ры ленточ- |
|
|
разогрев |
дуальные с |
териалы, |
||||
|
ния |
индиви- |
ные, во- |
||||
|
до укладки |
изде- |
системой па- |
дуаль- |
вода, |
допровод |
|
|
смеси в |
роснабжения |
цемент |
||||
|
форму |
лий |
|
ный |
|
|
|
|
|
|
|
|
|
||
Парора- |
|
|
Бункер с уст- |
Бетоно- |
Холодная |
Бетонораз- |
|
зогрев |
|
|
ройством для |
смеси- |
бетонная |
даточные |
|
То же |
То же |
устройства, |
|||||
бетонной |
пенетрации |
тель |
смесь |
||||
|
|
бетоно- |
|||||
смеси |
|
|
пара |
БСО |
|
||
|
|
|
укладчики |
||||
|
|
|
|
|
|
||
|
Децентра- |
|
|
|
|
|
|
|
лизо- |
|
|
|
|
|
|
|
ванный |
Пост |
Паровая ка- |
|
|
|
|
|
разогрев |
про- |
То же |
То же |
То же |
||
|
мера |
||||||
|
до укладки |
грева |
|
|
|
||
|
|
|
|
|
|||
|
смеси в |
|
|
|
|
|
|
|
форму |
|
|
|
|
|
Высокопроизводительный завод с минимальными энерго- и фондоемкостью может быть создан на основе технологии тепловой обработки с применением теплого бетона и режима с ограниченным тепловым импульсом.
Выбор метода приготовления теплого бетона осуществляется по следующим критериям:
быстрота, уровень температуры и равномерность разогрева компонентов смеси и в целом ее массы;
минимум тепло- и влагопотерь;
эффективность и доступность по теплоносителю, виду энергии;
изученность, техническая проработанность, капиталоемкость;
технологичность для условий действующих и новых линий;
уровень механизации и автоматизации.
Согласно этим критериям получение теплого бетона в технологии изготовления железобетонных изделий возможно на основе различных методов паро- и электроразогрева. При этом в условиях одного производства возможно сочетание централизованного и децентрализованного приготовления теплого бетона. Для централизованного приготовления предлагается метод пароразогрева составляющих бетонной смеси: щебня, песка и воды.
162
Для децентрализованного приготовления на отдельных технологических линиях предлагаются методы электроили пароразогрева бетонной смеси.
Температурные характеристики бетонной смеси, достигаемые при разогреве ее компонентов, приведены в табл. 3.6.
|
|
Таблица 3.6 |
|
Температурные характеристики бетонной смеси |
|||
|
|
|
|
Разогреваемые компоненты |
Температура разогрева |
Температура бетонной сме- |
|
бетонной смеси |
компонентов смеси, °С |
си, °С |
|
Вода |
90 |
25…30 |
|
Вода |
90 |
35…40 |
|
Песок |
60…70 |
||
|
|||
Вода |
90 |
|
|
Песок |
60…70 |
45…50 |
|
Щебень |
60…70 |
|
Данные табл. 3.6 получены для бетона следующего состава (в кг/м3): цемент – 300, песок – 700, щебень – 1200, вода – 200. Начальная температура компонентов смеси 15 °С; средний КПД использования их тепла
0,6.
Разогретые инертные материалы загружают в бетоносмеситель, затем в процессе их перемешивания подают цемент и предварительно разогретую воду. Получаемая в смесителе теплая бетонная смесь распределяется по формовочным постам технологических линий.
Данные расчета удельной энергоемкости при приготовлении 1м3 теплого бетона приведены в табл. 3.7.
|
|
|
Таблица 3.7 |
Удельная энергоемкость при приготовлении теплого бетона |
|||
|
|
|
|
Разогреваемый ма- |
Масса, кг |
Температура разо- |
Расход тепловой |
териал |
|
грева, °С |
энергии с учетом |
|
|
|
теплопотерь, |
|
|
|
ГДж/м3 |
Щебень |
1200 |
70 |
0,104 |
Песок |
700 |
70 |
0,063 |
Вода |
200 |
90 |
0,104 |
Итого |
|
|
0,271 |
Разработка технологии производства железобетонных изделий с применением теплого бетона включает следующие этапы:
163
анализ исходной информации (номенклатура завода, вида и марки цементов и бетона, типы заполнителей, составы смесей и значения проектной прочности, подвижность смеси);
выбор способа разогрева, виды энергоносителя, оборудование;
определение параметров режима разогрева (время и температура разогрева);
оценка динамики подвижности теплой бетонной смеси, корректировка состава бетона;
выбор способа и технического решения догрева и термосной выдержки изделий с учетом времени укладки смеси и формования, модуля поверхности изделия, потерь тепла и влаги;
определение основных технологических параметров (времени термосной выдержки, остывания, технологического цикла для получения распалубочной прочности);
определение технико-экономических характеристик (оборачиваемости тепловых установок и форм, энерго- и материалоемкости, экологических характеристик, показателей экономической эффективности).
Физико-механические характеристики бетона, определяющие его плотность и долговечность, и технико-экономические показатели производства зависят от режима приготовления теплого бетона и тепловых условий последующей выдержки изделий с учетом состава бетона, вида цемента и подвижности бетонной смеси.
Для приготовления бетонных смесей, разогреваемых до температуры свыше 60 °С, целесообразно применить интенсивно твердеющие при кратковременной тепловой обработке высоко- и среднеалитовые, мало- и среднеалюминатные (С3А не более 10 %), рядовые и быстротвердеющие портландцементы марок 300…400.
При разогреве бетонных смесей до температуры менее 60 °С рекомендуются портландцементы, содержащие более 10 % активных минеральных добавок, повышающих водопотребность цемента, а также портландцементы и шлакопортландцементы с нормальной густотой теста более
27 %.
Портландцементы, содержащие С3А до 6 %, следует применять при разогреве бетонных смесей до 80 °С. При применении портландцементов, содержащих С3А более 6 %, и пуццолановых портландцементов максимальная температура разогрева смесей уточняется экспериментально.
Состав бетонных смесей, обеспечивающих требуемые подвижность разогретой смеси и прочность бетона при минимальном расходе цемента, определяется экспериментально с учетом оптимизации параметров режима тепловой обработки по методике ВНИИжелезобетона.
164
При оценке режимов тепловой обработки бетона с предварительным разогревом смеси учитываются следующие параметры: время начала разогрева, скорость (время) и температура разогрева бетонной смеси, длительность изотермической или термосной выдержки, начало и скорость остывания, время достижения нормативной прочности, полный цикл тепловой обработки.
Подвижность разогретой бетонной смеси во время укладки ее в форму и формования изделия должна соответствовать требованиям, предъявляемым к холодным (неразогреваемым) бетонным смесям. Экспериментально установлено, что потеря «подвижности смесей с осадкой конуса 3…12 см, разогретых до температуры 60…70 °С, после 20 мин выдержки составляет 1…4 см.
Для обеспечения подвижности, необходимой при укладке разогретой смеси, допускается повышение водосодержания смеси на 2…25 % в зависимости от температуры разогрева и марки бетона или применение по- верхностно-активных пластифицирующих добавок.
Наиболее простым способом, замедляющим загустевание разогретых смесей, является увеличение их водосодержания (табл. 3.8).
|
|
|
|
Таблица 3.8 |
|
Увеличение водосодержания теплых бетонов |
|
||
|
|
|
|
|
Температураразогре- |
Рекомендуемое увеличение расхода воды, %, для бетона марок |
|||
ва, °С |
100…150 |
200…250 |
|
300 |
До 50 |
2…3 |
3…5 |
|
5…8 |
55…70 |
5…10 |
10…15 |
|
– |
75…90 |
15…20 |
20…25 |
|
– |
Наименьшее водоцементное отношение бетонных смесей, подвергаемых предварительному разогреву, составляет 0,4…0,5.
Водопотребность бетонной смеси может быть определена по фор-
муле
Вр =Вн ((В/Ц+0,5)/(В/Ц +0,5/Кц)), |
(3.37) |
где В – расчетная водопотребность; Вн – водопотребность бетонной смеси исходного состава; Кц – коэффициент водопотребности цемента.
Коэффициенты водопотребности цементов различных групп в зависимости от температуры разогрева бетонной смеси, по данным Ю.П.Винарского, приведены в табл. 3.9.
Дополнительное количество воды для приготовления разогреваемых бетонных смесей в зависимости от содержания в цементе минерала С3А составляет для цементов: низкоалюминатных – 10 %, среднеалюминатных – 13 %, высокоалюминатных – 15 %.
165
|
Коэффициенты водопотребности цементов |
Таблица 3.9 |
|||
|
|
||||
|
|
|
|
|
|
Температура |
Выдержка пос- |
Коэффициент водопотребности цементов |
|||
ле разогрева, |
|
|
|
||
разогрева, °С |
Ц1 |
Ц2 |
Ц3 |
||
мин |
|||||
|
|
|
|
||
50 |
0 |
1,08 |
1,08 |
1,06 |
|
15 |
1,18 |
1,24 |
1,21 |
||
|
30 |
1,30 |
1,38 |
1,36 |
|
70 |
0 |
1,15 |
1,19 |
1,17 |
|
15 |
1,37 |
1,42 |
1,42 |
||
|
30 |
1,57 |
1,62 |
1,70 |
|
90 |
0 |
1,28 |
1,32 |
1,38 |
|
15 |
1,58 |
1,61 |
1,69 |
||
|
30 |
1,87 |
1,92 |
2,10 |
Примечание. Ц1, Ц2,Ц3 – группы цементов по коэффициенту эффективности при пропаривании.
Если с увеличением водосодержания и получением требуемой подвижности бетонной смеси не достигается заданная прочность, следует применять добавки, повышающие прочность бетона. Они вводятся с целью нейтрализации отрицательного влияния повышенного водосодержания на прочность бетона. К ним относятся нитрит-нитрат кальция (ННК), нитритнитрат хлорид кальция (ННХК), нитрат кальция, нитрат натрия, не вызывающие коррозию стали.
Известно, что повышение температуры резко увеличивает скорость гидратации минералов C3S и С3А, что способствует, с одной стороны, загустеванию бетонной смеси, а с другой, − ускоренному росту прочности бетона. Повышается активность воды, вязкость которой снижается более чем в 3 раза (от 1,005·10-3 до 0,283·10-3 Па·с) при увеличении температуры от 20 до 100 °С.
Температура разогрева смеси лимитируется ее подвижностью. Оптимальная температура разогрева составляет 50 °С при ОК = 0…1 см; 70 °С при ОК = 2…3 см; 90 °С при ОК = 8…10 см. Показано, что во всех случаях бетон в суточном возрасте достигает 70…90 % марочной прочности, а к 28 сут у всех цементов наблюдается прирост прочности по сравнению с бетоном нормального твердения.
Твердение бетона, отформованного из разогретых смесей, протекает при минимальных деструктивных процессах. Благодаря этому прочность бетона ускоренного твердения на 25…30 % выше прочности бетона того же состава, но твердеющего в нормальных условиях.
166
Однако с повышением температуры разогрева увеличиваются потери тепла и влаги и снижается подвижность смеси. Поэтому при разогреве смеси с осадкой конуса 6…8 см на портландцементе оптимальной температурой можно считать 70 °С. Для смеси на шлакопортландцементе температура разогрева может быть повышена до 80…90 °С.
При использовании разогретых бетонных смесей необходимо сокращать интервал времени между приготовлением и укладкой теплого бетона. Он должен составлять при температуре разогрева смеси 50…70 °С соответственно 10…15 мин.
Об интенсивности остывания разогретой смеси в среде с температурой 20 °С при транспортировке и укладке можно судить по данным табл.3.10.
Таблица 3.10
Интенсивность остывания разогретой смеси
Температура разо- |
Скорость охлаждения смеси, °С/мин, при |
|||
транспортировке с помощью |
укладке и перегруз- |
|||
грева, °С |
бадьи, бункера, са- |
транспортерной |
||
ке |
||||
|
мосвала |
ленты |
||
|
|
|||
80 |
0,07 |
1,0 |
1,8 |
|
60 |
0,04 |
0,6 |
1,2 |
|
40 |
0,02 |
0,2 |
0,6 |
При использовании предварительно разогретых бетонных смесей эффект ускорения твердения бетона, обеспечивающий двух- и трехкратный оборот форм в сутки, возможен при условии минимальных технологических влаго- и теплопотерь и соблюдения необходимой длительности изотермической или термосной выдержки изделий.
Разогретые смеси целесообразно укладывать в предварительно подогретые или еще не остывшие формы с температурой не ниже 30 °С.
Термосная или изотермическая выдержка железобетонных изделий может осуществляться в камерах периодического и непрерывного действия, термоформах, термопакетах, кассетных установках или под термоколпаками. В качестве источника тепловой энергии могут быть использованы водяной пар, паровоздушная смесь, горячий воздух, электроэнергия, продукты сгорания природного газа, а также энергия возобновляемых источников.
Изделия значительной толщины (Мn менее 10) можно выдерживать в условиях термоса, создаваемого утепленной формой или опалубкой при температуре воздуха не ниже 15 °С. Тонкостенные бетонные и железобетонные изделия (Мn более 10),при более быстром остывании которых эк-
167
зотермического тепла недостаточно для восполнения теплопотерь, должны выдерживаться в условиях активного термоса.
Продолжительность выдержки, определяющая фондоемкость тепловой обработки, зависит от вида цемента, марки бетона, распалубочной прочности, температуры и определяется как параметр режима с ограниченным тепловым импульсом. Искомое время ограничивается достижением максимальной скорости роста прочности на кривой кинетики твердения бетона. Прочность бетона, набираемая к этому времени, составляет 20…30 % от марочной. Дальнейшее твердение бетона может осуществляться вне тепловой установки при остывании в среде цеха с положительной температурой. При этом время достижения распалубочной прочности практически не увеличивается.
Уплотнение теплого бетона вибрацией на ранней стадии процессов структурообразования не вредит бетону, а, наоборот, упрочняет его. Уплотнение смеси рекомендуется производить в конце формирования структуры, когда имеется возможность разрушить рыхлую гидроалюминатную структуру и тем самым увеличить прочность бетона.
Заметное увеличение механической прочности бетона наблюдается при приложении вибрационного воздействия между началом и концом схватывания.
С.В.Шестоперов, предложивший способ повторного вибрирования, установил, что с помощью такого способа можно увеличить механическую прочность почти в 1,5 раза, а водонепроницаемость в 2 раза. Эти результаты подтверждают эффективность уплотнения бетона на определенной стадии структурообразования, достижение которой ускоряется разогревом бетонной смеси.
Оптимальным временем виброуплотнения бетонной смеси является момент завершения формирования пространственного каркаса коагуляционной структуры. Глубокая научная проработка технологии получения теплого бетона позволяет создавать на основе этого метода новые интенсивные малоэнергоемкие технологии изготовления железобетонных изделий. Средние значения продолжительности тепловой обработки бетона на цементах 2 группы при различных способах нагрева бетона представлены в табл. 3.11.
Из данных табл. 3.11 следует, что эффект интенсификации твердения бетона выражается в 1,5…2-кратном сокращении цикла термообработки по сравнению с традиционным паропрогревом. При этом уровень технологических энергозатрат сводится до 0,25…0,40 ГДж/м3, а КПИ энергии повышается до 0,80…0,85. Производственный эффект выражается достижением двух-, трехкратной оборачиваемости тепловых установок и форм за сутки.
168