
2390
.pdfТепловой баланс кассеты, кДж/период
Период подогрева
1. Приход тепла:
1.1. Тепло сухой части бетона
Q1c Gц Gз ссt1 7433 69320 0,84 20 1289 450.
1.2. Тепло воды затворения
Q1в Gвсвt1 5582 4,185 20 467 213.
1.3. Тепло арматуры и закладных деталей
Q1a Gacat1 2500 0,46 20 23000 .
1.4. Тепло форм
Q1ф Gфcфt1 80000 0,46 20 736000.
1.5. Тепло экзотермии цемента при
t1 2 0,5 t1 t2 0,5(20 90) 55 oC
Q1э 0,0023Qэ28 В/ Ц 0,44t1 2 1Gц
0,0023 420 0,750,44 55 1,5 7433 591 942.
1.6.Тепло насыщенного пара
Qiп G1пiп ,
где G1п масса пара, поступившего в камеру за период подогрева, кг; iп энтальпия пара, поступившего в камеру за период подогрева, кДж/кг.
Суммарный приход тепла за период прогрева
6
Qприх Q1c Q1в Q1a Q1ф Q1э Q1п.
1
6
Qприх 1289450 467213 23000
1
736000 591942 Q1п 3107605 Q1п .
189
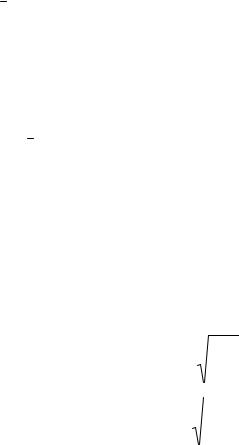
2. Расход тепла:
2.1. Тепло сухой части бетона
Q2c Gц Gз ссtIII 7433 69320 0,84 70,54 4547891,5. 2.2. Тепло на испарение части воды затворения
Q2исп Wi 2493 1,97t1 2 412 2493 1,97 55 1071756.
2.3. Тепло воды, оставшейся в изделиях к концу периода подогрева,
Q2в G2всвtIII 5170 4,194 70,54 1529335.
2.4. Тепло арматуры
Q2a Gacat2 2500 0,46 90 103500.
2.5. Тепло форм
Q2ф Gфсфt2 80000 0,46 90 3312000.
2.6. Тепло материалов элементов ограждений к концу периода прогрева
|
Qакк 7,2 i Fi t1 2 t1 |
|
|
. |
|
|
|
|
|
|
|
|
|
|
|||
|
|
|
|
ai |
|
|
|
|
Для стен Qаккст 7,2 0,045 (5,092 4,28) 55 20 |
1,5 |
|
|
5482. |
||||
0,00097 |
|
|
||||||
|
|
|
3,14 |
|||||
Для пола |
Qаккпол 0. |
|
|
|
|
|
|
|
Для крышки |
Qакккр 0. |
|
|
|
|
|
|
|
Таким образом, |
Q2акк Qаккст Qаккпол Qакккр 5482 0 0 5482. |
|||||||
2.7. Потери тепла |
в окружающую среду через ограждения камеры |
к концу периода подогрева
Qo.c 3,6 1 t1 2 t1 Fiki .
Для определения потерь тепла через наземную часть стены кассеты подсчитываем их площадь и коэффициент теплопередачи:
F Lk Hk 2 5.092 4.82 2 49,09м2 ;
kназ |
|
|
|
1 |
|
|
|
|
|
|
|
1 |
|
|
|
|
Вт |
|
|
|
|
|
|
|
|
|
|
|
|
|
|
0,28 |
|
. |
|||
|
1 |
|
i |
|
1 |
|
|
1 |
|
0,150 |
|
1 |
|
м2 о С |
||||
|
1 |
i |
2 |
45 |
0,045 |
5 |
|
|
|
|
||||||||
|
|
|
|
|
|
|
|
|
||||||||||
|
|
|
|
|
|
|
190 |
|
|
|
|
|
|
|
|

Тогда |
Q2о.с 3,6 1,5 55 20 49,09 0,28 2598. |
2.8. Тепло, уносимое конденсатом пара,
Q2конд iкондG2конд iконд G1п Gсв , здесь iконд 419,06 кДж/кг.
Масса пара, занимающая свободный объем камеры, кг,
Gсв пVсв 0,5977 18,46 11,03.
Следовательно, Q2конд iконд G1п 11,03 419,06G1п 4622,23.
Суммарный расход тепла в период подогрева
8
Qрасх 4547891,5 1071756 1529335 103500
1
3312000 5482 2598 419,06G1п 4622,23 10577184 419,06G1п.
Тепловой баланс камеры в период подогрева
|
6 |
|
8 |
||
|
|
Qприх Qрасх . |
|||
|
1 |
|
1 |
||
iп G1п 3107605 |
419 ,06G1п 10 577 184 . |
||||
G1п |
|
7 469579 |
3310 кг/период. |
||
2676 419,06 |
|||||
|
|
|
Удельный расход пара:
q1 G1n 3310 95кг/м3.
Vб 34,8
Период изотермического прогрева
3. Приход тепла:
3.1. Тепло экзотермии цемента
Q2э 0,0023Qэ28 В/ Ц 0,44t2 2Gц
0,0023 420 0,750,44 90 4 7433 2 274712.
3.2.Тепло сухой части бетона Q2с 4547891.
3.3. Тепло, аккумулированное ограждениями, Q2акк 5482.
3.4.Тепло пара, поступающего в камеру, Q2п iпG2п .
3.5.Тепло воды, оставшейся в изделиях Q2в 1529335.
191
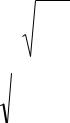
3.6.Тепло арматуры Q2а 103500.
3.7.Тепло форм Q2ф 3312000
Суммарный приход тепла в период изотермического прогрева
7
Qприх Q2э Q2c Q2акк Q2п Q2B Q2a Q2ф 2274712 4547891 5482
1
inG2n 1529335 103500 3312000 11772920 inG2n;
4. Расход тепла:
4.1. Тепло на подогрев изделий
Q4с Gц Gз ссt2 7433 69320 0,84 100 6447 252.
4.2. Тепло, аккумулированное кассетой,
|
|
Q |
|
|
7,2 F |
t |
|
t |
|
|
|
2 |
|
|
|
|
|
|
|
|
|
|
|
|
ai . |
|
|
|
|||||||
|
|
|
4акк |
|
i i |
|
2 |
|
1 |
|
|
|
|
||||
|
|
|
|
|
|
|
|
|
|
||||||||
Для стен |
Qст |
7,2 0,045 21,79 100 20 |
|
|
|
4 |
|
20467 |
. |
||||||||
|
|
|
|
|
|||||||||||||
акк |
|
|
|
|
|
|
|
|
|
|
0,00097 3,14 |
|
|
||||
|
|
|
|
|
|
|
|
|
|
|
|
|
|
|
|||
Для пола |
|
|
|
Qаккпол 0. |
|
|
|
|
|
|
|
|
|
|
|
||
Для крышки |
|
|
|
Qакккр |
0. |
|
|
|
|
|
|
|
|
|
|
|
|
Следовательно, Q4акк |
20467 0 0 20467. |
|
|
|
4.3. Тепло, потерянное в окружающую среду через ограждения, аналогично подсчету по п. 2.7 для периода подогрева:
Q4о.с. 3,6 2 2 1 Fi ki ,
Q4о.с. 3,6 4 100 20 43,59 0,28 14061. 4.4. Потери тепла с конденсатом
Q4конд iкондG4конд iконд G2п Gсв
419 G2п 11,03 419G2п 4622,23.
4.5.Тепло воды (аналогично 2.3)
Q4В G2B cB t4 5170 4,194 100 2168 298. 4.6. Тепло арматуры (см.2.4)
Q4а Gа cа t4 2500 0,46 100 115000.
192
4.7. Тепло форм (см.2.5)
Q4ф Gф cф t4 80000 0,46 100 3680000.
Суммарный расход тепла в период изотермического прогрева
7
Qрасх Q4c Q4акк Q4о.с. Q4конд .
1
7
Qрасх 6447252 20467 14061
1
419G2п 4622 216298 115000 3680000 12440456 419G2п .
Тепловой баланс камеры в период изотермического прогрева
|
11772920 iпG2п |
12 440 456 419G2п . |
||||||||
Откуда |
G2п iп |
419 667 536 . |
||||||||
|
G2п |
|
667536 |
|
|
|
296 кг/период. |
|||
|
2676 419 |
|||||||||
|
|
|
|
|
||||||
Удельный расход пара |
q2 |
G2n |
|
|
|
296 |
8,5кг/м3. |
|||
V |
|
34,8 |
||||||||
|
|
|
|
|
|
|
|
|||
|
|
|
|
б |
|
|
|
|
|
|
Тогда удельный расход пара при нормальных физических условиях на тепловую обработку 1м3 бетона составляет
q1 q2 95 8,5 103,5кг/м3.
Благодаря значительной экзотермии цемента и массивности конструкции кассеты пар в период изотермического прогрева можно не подавать, а проводить термосное выдерживание изделий.
3.18.3. Расчёт автоклава
Исходные данные:
Запроектировать установку для пропарки силикатобетонных изделий в автоклавах для завода мощностью 64 470 м3/год плотного бетона.
Дополнительные данные:
По изделиям:
стеновые панели из силикатобетона состава: В = 190 л/м3,
Gсух=1900 кг/м3, размером 2,9х2,7х0,24 м;
количество арматуры в изделии согласно нормам 20 кг/м3 бетона;
теплоемкость сухих составляющих бетона сб = 0,9 кДж/(кг·ºС);
193
влажность на входе в автоклав W1=10 %, при выходе W2=6 %, температура на входе в автоклав tн=20 ºС.
По режиму теплообработки:
загрузка 1 ч, подъем давления 5,5 ч, выдержка при максимальном давлении 5 ч, спуск давления 5,5 ч, охлаждение 2 ч, выгрузка 1 ч. Полное время оборота τц=20 ч: максимальное давление 1.2 МПа;
пар поступает в автоклав сухой насыщенный с давлением
р=1.3 МПа.
Прочие данные:
количество панелей в одной форме размером 6х2,76 – 2 шт.;
вес формы на 1 м3 бетона 1,2 т;
средняя максимальная температура автоклава tсрк=120 ºС при максимальной температуре пара в нем tк=188 ºС;
средняя температура автоклава в начале пропарки tсрн=40 ºС;
средняя температура наружной поверхности за период пропарки tст=40 ºС с учетом слоя изоляции, температура воздуха в цехе tц =15 ºС.
Технологический расчет
1. Режим рабочего времени завода принят трехсменный при пятидневной рабочей неделе по 2010 г.: 249 – 7 =242 рабочих суток (7 сут. – плановый ремонт при агрегатно-поточной технологии).
Количество рабочих часов 24·242=5808 ч. Часовая производительность цеха по бетону:
Gч=64 470/5808=11,1 м3/ч.
Объем одного изделия:
2,9х2,7·0,24=1,88 м3.
Производительность цеха по изделиям:
G’ч=11,1/1,88=5,9 шт/ч.
При расходе сухих составляющих 1900 кг/м3 масса их в одном изделии 1,88·1900=3572 кг. Масса воды в одном изделии 190·1,88=357 кг.
Часовая производительность завода по массе сухих составляющих:
G’’ч =5,9·3572=21 075 кг/ч.
Принимаем к установке проходной автоклав типа Л–330/8А со следующей технической характеристикой: длина корпуса 21 м, диаметр 3,6 м, рабочий объем Vа=235 м3, рабочее давление 1.3 МПа, ширина колеи 1524 мм, масса автоклава Gав=118,5 т. Автоклавная вагонетка для колеи 1524 мм типа К – 397/3. Длина платформы 6,7 м, ширина – 2,5 м, высота – 0,335 м,
194
масса – 2,5 т. Число вагонеток в одном автоклаве: 21/6,7=3 шт. Масса вагонеток Gв=7,5 т.
Определяем емкость одного автоклава при укладке изделий в формах на вагонетки. Панели устанавливают в следующем порядке: по ширине вагонетки – 1 шт., по длине – 2 шт., по высоте – 5 рядов по 2 шт., всего на вагонетке – 10 шт. изделий. Емкость автоклава:
l=10·3=30 шт.
Объем, занимаемый:
-изделиями Vи =1,88х30=56,4 м3;
-вагонетками-платформами Vв=0,34х2,5х6,7х3=17 м3.
Свободный объем автоклава Vсв= 234–(56,4+17)=160,6 м3.
Заполнение объема автоклава изделиями по коэффициенту заполне-
ния:
К=Vи/Vа=56,4/235х100=24 %.
Потребное число автоклавов для заданной производительности:
n=Gчτц/l=5,9х20/30=3,93≈4 шт.
Теплотехнический расчет
Составляем баланс тепла одного автоклава на период его работы и на всю массу загруженных изделий.
Приход тепла.
С паром давлением 1.3 МПа и энтальпией iп=2787 кДж/кг
(см. табл.П.17).
Qп=Gп·iп=Gп·2787 кДж.
Расход тепла за период
1. На нагрев сухих составляющих от 20 до 188 С, соответствующей температуре сухого насыщенного пара при конечном давлении в автоклаве 1.2 МПа. Количество сухих составляющих бетона в автоклаве
30·3572=107 160 кг;
Q1’=Gб·сб· (tк–tн)=107 160·0,9· (188 – 20)=162·105 кДж.
2. На нагрев влаги бетона от 20 до 188 С
Q2’=Gб·св·(W/100)·(tк–tн)=107 160·4,18·(10/100)·(188 – 20)=75,2·105 кДж.
3. На нагрев арматуры и форм от 20 до 188 С.
195
Количество арматуры в одном изделии из расчета 20 кг/м3 бетона составит 20х1,88=37,6 кг, во всей загрузке автоклава:
Gа=37,6·30=1128 кг.
Форма размером 6·2,78·0,24 (в чистоте) вмещает 2 изделия. Все формы устанавливаем из отношения ее массы к объему изделия, принятого равным 1,2 т/м3. Масса одной формы составит 1,88·2·1,2=4,5 т, при числе форм в автоклаве 15 шт. их масса равна
Gф=15·4500=67 500 кг.
Q’3=(Gа+Gф)са(tк-tн)=(1128+67 500) ·0,48 ·(188 – 20)=55,3 ·105 кДж.
4. На нагрев вагонеток с 15 до 188 С
Q’4=Gбса(tк-tц)=7500 ·0,48 ·(188-15)=62,3 ·105 кДж.
5. На аккумуляцию корпуса автоклава при нагреве его от 40
до 120 С:
Q’5=Gавса(tср к-tср н)=118 500·0,48·(120 – 40)=45,5·105 кДж.
6. Потери тепла во внешнюю среду поверхностью автоклава. Поверхность автоклава F=πDL=3,14·3,6·21=238 м2, температура по-
верхности стенки tст=40 С, суммарный коэффициент теплоотдачи по табл.П.29. αс=10,69 Вт/(м2 С). Время, в течение которого расходуется пар,
τ=10,5 ч.
Q’6= αс·(t ст-t ц)F·3.6· τ=10,69(40 – 15) ·238·3,6·10,5=24·105 кДж.
7. На испарение влаги из изделий.
Из практических данных заводов принимаем остаточную влажность изделий W2=6 %.
Q’7=2487·Gб(W1-W2)/100=2487·107 160·(10 – 6)/100=106,6·105 кДж.
8. Потери тепла с паром, оставшимся в свободном объеме автоклава при минимальном давлении 1.2 МПа с энтальпией 2784 кДж/кг,
Q’8=Vсв·ρп·iп=160,6·6,12·2784=27,4·105кДж.
9. Потери тепла с учетом утечки пара через неплотности. Коэффициент утечки пара k принимаем равным 0,05.
Q’9=kGпiп=0,05·Gп·2787=139·Gп кДж.
10. Потери тепла с конденсатом
Q’10=Gкcкtк=[Gп – (k·Gп+Vсв·ρп)]скtк=
=[Gп – (0,05·Gп+160,6·6,12)]4,18·100=397Gп – 4,1·105кДж.
196
Всего расход тепла:
∑Q’=498·105+536·Gп кДж/период.
Уравнение баланса тепла: 2787Gп=498·105+536Gп кДж.
Расход пара за период тепловой обработки:
Gп=498·105/2251=22 100 кг/период.
Расход пара на 1 м3 бетона: qп=22100/56,4=390 кг/м3.
Сводный тепловой баланс автоклавной установки представлен в табл. 3.15.
|
Сводная таблица баланса тепла автоклава |
Таблица 3.15 |
||
|
|
|||
|
|
|
|
|
|
Наименование статей баланса |
Количество тепла |
||
|
кДж/период |
|
% |
|
|
|
|
||
|
Приход тепла |
|
|
|
1. |
С паром Gп·iп=22 100·2787 |
616·105 |
|
100 |
|
Расход тепла |
|
|
|
1. |
На нагрев бетона |
162·105 |
|
26,3 |
2. |
На нагрев влаги бетона |
72,2·105 |
|
12,2 |
3. |
На нагрев арматуры и форм |
55,3·105 |
|
9,0 |
4. |
На нагрев вагонеток |
6,23·105 |
|
1,0 |
5. |
На аккумуляцию стенками автоклава |
45,5·105 |
|
7,4 |
6. |
Потеря тепла во внешнюю среду |
24·105 |
|
3,9 |
7. |
На испарение влаги из изделий |
106,6·105 |
|
17,3 |
8. |
Потеря тепла с паром, оставшимся в |
27,4·105 |
|
4,4 |
свободном объеме автоклава |
|
|
|
|
9. |
Потеря тепла с утечкой пара 22 100·139 |
30,7·105 |
|
5,0 |
10. Потеря тепла с конденсатом |
83,6·105 |
|
13,58 |
|
22 100·397–410 894 |
|
|
|
|
Невязка баланса |
0,53·105 |
|
0,08 |
|
|
Всего |
616·105 |
|
100 |
197
3.18.4. Расчет туннельной камеры
Исходные данные:
1.Годовая производительность конвейерной технологической линии
по выпуску плит перекрытий ……………………………...... Gгод=29 680 м3;
объёмом каждая……………………………………………........... Vи=1,15 м3.
2.Годовой фонд рабочего времени цеха по 2010 г…………...............
………………………………..……………249 – 13=236, Вр=236×24=5664 ч.
3.Цикл тепловлажностной обработки изделий ……………….………
………………………………………………… ц 1 2 3 3 6 2 11ч.
4. Температура:
начальная свежеотформованного бетона…………………………… tI=20 °С;
изотермической выдержки………………………………...………… t2=80 °С. 5. Расход материалов на 1 м3 бетона, кг: портландцемент М500
Ц=324, вода В=178, песок П=1873, арматура А=115,66, В/Ц=0,55. Плотность бетона…………………..……….…..……………... ρб=2490 кг/м3.
6.Масса формы-вагонетки………….………………….... GФ=7500 кг, размером ………………………………… ф bф hф 7,47 2,4 0,57 м.
7.В зоне подогрева расположены 12, а в зоне изотермической выдержки – 24 регистра глухого пара, состоящих из 15 труб диаметром
dТр=0,0735 м, длиной ТР 5 м каждый.
На расстоянии 2/3 длин зон подогрева и изотермической выдержки установлено по одной поперечной трубе с 24 отверстиями – перфорациями d0=3 мм для впуска острого пара. Давление пара в регистрах Pп=0,3 МПа при tп=133 °С (табл. П.17).
8.Коэффициенты: теплопередачи регистров Kрег=1,67 Вт/(м2·°С), теплоотдачи от среды ограждением камеры α1=139 Вт/(м2·°С) и от внешней поверхности ограждений в среду цеха α2=23,2 Вт/(м2·°С).
9.Ограждения камеры: стены – железобетонные ст = 0,4 м; пол – железобетонный пол = 0,14 м, по шлаковой подготовке с шл = 0,25 м ишл = 0,151 Вт/(м С); потолок – бетонная плита пот = 0,035 м, утепленная
шлаковой засыпкой шл = 0,25 м, с цементной стяжкой ц.с = 0,02 м. 10. Размеры камеры.
Количество изделий, размещаемых в камере:
n |
т.о |
|
Gгод |
ц |
|
19680 11 |
51шт. |
|||
V B |
p |
1,15 5664 |
|
|||||||
|
|
|
|
|||||||
|
|
|
и |
|
|
|
|
|
Размеры камеры при количестве ярусов nя 3:
198