
2390
.pdfХорошие теплофизические свойства, малая плотность и высокая теплостойкость эпоксидных пенопластов позволяют считать их перспективными материалами для теплоизоляции пропарочных камер.
Сферопласты образуют особую группу газонаполненных пластмасс, состоящих из полимерной матрицы и полых сферических частиц наполнителя из стекла, металла, полимера и керамики. Хотя сферопласты обладают высокими теплогидроизоляционными свойствами, применять их для теплоизоляции камер нецелесообразно из-за дефицитности наполнителей.
На основе совмещения эпоксидного пенопласта с крупнопористым заполнителем может быть создан эффективный теплогидроизоляционный материал – полимербетон, сохраняющий высокие теплозащитные свойства в паровоздушной среде с температурой 80…100 0С. С помощью этого материала можно покрывать внутреннюю поверхность камер без дополнительных паро- и гидрозащиты. Оптимальная толщина пенополимербетонной облицовки составляет 50мм, что позволит снизить агрегатный расход тепловой энергии почти вдвое. Пенополимербетон плотностью 280…380 кг/м3 имеет коэффициент теплопроводности 0,11…0,13 Вт/(м·0С) и водопоглощение 3…6 %.
3.3. Кассетные установки
Кассетные установки – это стационарные разъемные вертикально установленные формы-кассеты из металла или железобетона, в которых формуют и подвергают тепловой обработке панели внутренних стен и перекрытий, лестничные марши и площадки, балконные плиты и другие изделия.
Кассеты состоят из станины, механизмов перемещения, дожима и распорных рычагов (рис. 3.10). Форма-кассета состоит из ряда отсеков, образованных стальными вертикальными стенками, причем отсеки, используемые для формования бетона, чередуются с отсеками для пара (паровая рубашка). Крайние отсеки теплоизолируют. По конструкции разделительные стенки могут быть гибкими (из металлических листов толщиной 24 мм) или жесткими (в виде пространственных металлических коробов). К ним крепятся борта из уголков, образующих торцевые стенки и днище отсеков. Сборка и разборка отсеков производится при помощи специального механизма, а извлечение изделий из отсеков – мостовым краном. Уплотнение бетонной смеси в кассете осуществляется вибраторами, укрепленными по бокам наружных и в торцах внутренних стенок, или глубинными вибраторами.
89
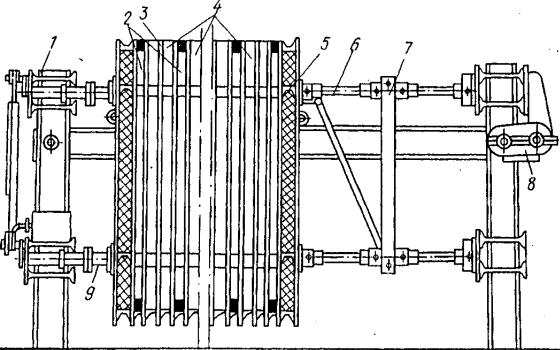
Рис. 3.10. Механизированная кассетная установка Гипростройиндустрии:
1 станина; 2 разделительная стенка; 3 отсек для формования панелей; 4 отсек для пара; 5 фиксирующие упоры; 6 крайняя утепленная стенка; 7 механизм сжатия кассеты; 8 привод; 9 упорный дожимной винт
Интенсивная теплоотдача греющей среды (пара, паровоздушной смеси, горячей воды и др.) достигается многократной циркуляцией и устройством узких тепловых отсеков с зигзагообразными перегородками. Теплоноситель не должен загрязнять стенок отсеков, поскольку это снижает коэффициент теплоотдачи. По той же причине из нижней части тепловых отсеков постоянно удаляется конденсат.
Тепловые отсеки рассчитаны на давление до 0,12…0,15 МН/м2. Большее давление требует значительного увеличения расхода металла. В железобетонных кассетных установках давление пара достигает 0,2 МН/м2.
Пространство и стенки теплового отсека надо нагревать равномерно, со скоростью, обеспечивающей высокое качество изделий. Недостаток пара в тепловом отсеке приведёт к расслоению среды (скоплению пара высокой температуры в верхней зоне отсека и менее нагретого – в нижней). Эжекторная система пароснабжения (рис. 3.11) тщательно перемешивает пар с воздухом и создает паровоздушную смесь одинаковой температуры по высоте кассеты.
90
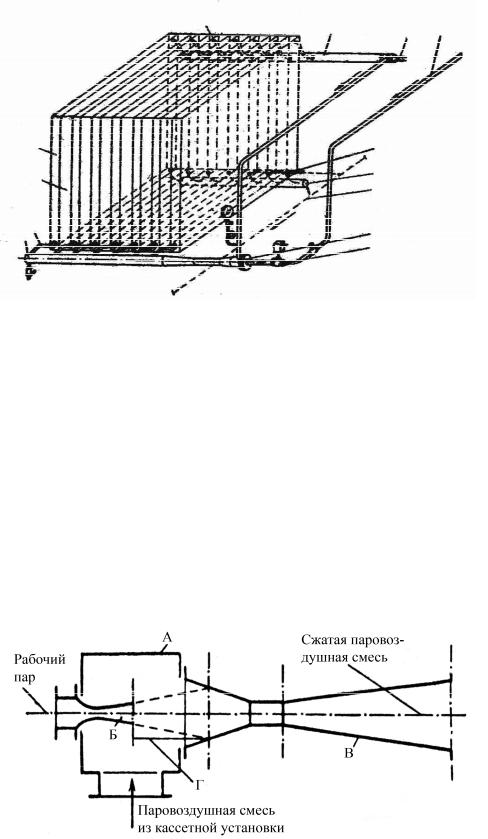
3
5 |
6 |
7 |
8
1
9
2
10
3 |
11 |
4
12
Рис. 3.11. Схема эжекторного пароснабжения кассеты: 1 паровая рубашка; 2 изделие; 3 резиновый шланг; 4 коллектор на вводе пара; 5
отсасывающий коллектор; 6 датчики температуры; 7 паропровод; 8
обратный клапан; 9 сборник-конденсатор; 10 конденсатопровод; 11 эжектор; 12 регулирующий клапан
Теплоносителем здесь служит паровоздушная смесь значительно меньшей температуры, чем чистый насыщенный пар. Получают его смешиванием чистого насыщенного пара с воздухом и паровоздушной смесью, отсасываемой из верхней зоны теплового отсека специальным коллектором. Применение эжекторной системы позволяет снизить расход чистого насыщенного пара и автоматически регулировать режим тепловой обработки по средней температуре паровоздушной смеси в коллекторе.
Паровоздушная смесь образуется в пароструйном эжекторе (рис.
3.12).
2 |
4 |
|
3 |
||
|
1
1 3
2 |
4 |
Рис. 3.12. Схема пароструйного эжектора: А корпус; Б рабочее сопло; В диффузор; Г камера смешения
91
Пароструйный эжектор состоит из следующих основных частей: корпуса А, образующего приемную камеру, куда поступает паровоздушная смесь, отсасываемая из паровых рубашек кассетной установки; рабочего сопла Б, монтируемого в приемной камере, и примыкающего к ней диффузора В. Рабочее сопло может быть выполнено суживающимся или расширяющимся в зависимости от отношений давлений в выходном сечении рабочего сопла к начальному. Если это отношение больше критического, то сопло должно быть суживающимся, в противном случае расширяющимся (сопло Лаваля). Диффузор образуется двумя обратными конусами с переходной цилиндрической частью горловиной. Диффузор и рабочее сопло должны располагаться строго по одной оси.
Объем, в котором происходит смешение рабочего пара и отсасываемой паровоздушной смеси, называется камерой смешения. Камера смешения Г начинается сразу на выходе сопла в сечении 1 1. Конец камеры смешения и начало камеры сжатия в сечении 2 2. В сечении 4 4 конец камеры сжатия, сечение 3 3 переход цилиндрического участка диффузора к расходящемуся конусу диффузора.
Изготовление изделий в кассетных формах обеспечивает высокую точность сборных деталей и хорошее качество поверхности. Формование изделий в вертикальном положении позволяет сократить производственные площади по сравнению с формованием в горизонтальных формах; готовые изделия имеют гладкие поверхности, почти не нуждаются в исправлениях; отклонение от геометрических размеров не превышает 1…5 мм по толщине и 5 мм по длине. Отпадает необходимость в виброплощадках, бетоноукладчиках, сложных быстроизнашивающихся формах и пропарочных камерах.
При изготовлении изделий в вертикальном положении требуется меньше арматуры и панели можно перевозить при распалубочной прочности бетона, т.е. 0,5 Rб.
Тепловлажностная обработка складывается из двух периодов: первый – прогрев, второй – изотермическая выдержка, после чего кассету разбирают, а изделия распалубливают. Масса сформованного бетона находится в кассете в замкнутом пространстве, что способствует более интенсивной тепловлажностной обработке. Открытой остается небольшая часть поверхности – 1,5…6 %. Это дает возможность применять интенсивную тепловую обработку бетона, не опасаясь быстрого испарения влаги из него и образования трещин. Температура бетона в кассетных установках достигает 100 С, в то время как в обычных камерах ямного типа она, как правило, не превышает 85…90 С. В кассетах изделие не охлаждают. Время тепловой обработки бетона в кассетах составляет 6…8 ч, поэтому выгружают изделия с прочностью 50…60 % проектной.
92
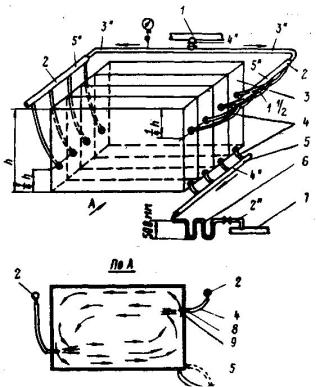
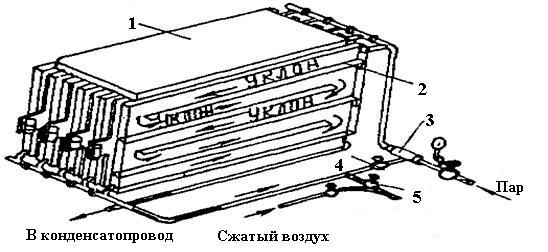
паром из конденсатопровода, не происходит превышения давления в паровых отсеках, где пар за счет энергии встречных струй равномерно распределяется и перемешивается с воздухом.
При внедрении этой системы потери тепла с пролетным паром сведены до минимума. Время термообработки сокращается до 7 ч в установках без разделительного листа, до 8…9 ч в установках с разделительным листом при толщине изделия 100…140 мм и до 11…12 ч при толщине изделий
160…180 мм.
Материальные затраты на переустройство только за счет экономии пара окупаются за 3…4 месяца.
Эжекторная схема теплоснабжения кассетно-формовочных установок дополнена тремя новыми элементами (рис. 3.14): автоматизированной стационарной крышкой для устранения потерь тепла и влаги через верхние пояса изделий и обеспечения набора прочности в районе грузовых петель, горизонтальными диафрагмами в паровых отсеках для обеспечения скорости движения пара и интенсификации теплоотдачи, газоструйным насосом для отсоса воздуха из паровых отсеков.
Рис. 3.14. Система пароснабжения кассетной установки при паровых отсеках с горизонтальными диаграммами: 1 – стационарная автоматизированная крышка; 2 – горизонтальная диафрагма; 3 – эжектор; 4 – вентиль; 5 – газоструйный насос
3.4. Пакетные установки
Для бескамерной тепловой обработки бетона наиболее широко применяют пакеты, установленные в штабель на специальном устройстве – пакетировщике (рис. 3.15). Он состоит из подъемного стола - траверсы 1, четырех гидродомкратов 2, направляющих колонн 3 и четырех упоровотсекателей 4. Работа пакетировщика заключается в следующем. На стол-
94
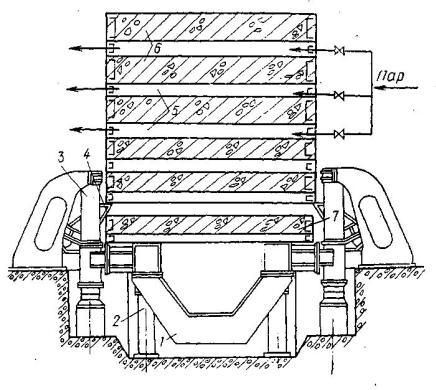
траверсу ставят термоформу со сформованным изделием 7, готовую к тепловой обработке. Включают гидродомкраты и поднимают стол-траверсу немного выше упоров-отсекателей. При этом упоры-отсекатели во время прохождения формы утапливаются. После того, как форма поднялась вверх, упоры-отсекатели под действием эксцентрично приложенной силы собственной массы возращаются в нормальное положение. Далее стол опускается, а форма с изделием остается на упорах и подключается к системе пароснабжения. Следующая форма с изделием поднимается аналогичным образом, только форма, стоящая на упорах, оказывается на уже поднятой. Пакетировщик рассчитан на одновременную обработку шести форм.
Рис. 3.15. Схема пакетировщика: 1 – подъемный стол-траверса; 2 – гидродомкраты; 3 – направляющие колонны; 4 – упорыотсекатели; 5 – паровые отсеки форм; 6 – нагреваемые изделия; 7 – изделие в форме, подготовленное к загрузке
Термоформу пакетировщика переоборудуют из обычной, жесткой стальной формы посредством приварки к каркасу поддона формы стального листа. Образующуюся под формой полость используют как нагревательный отсек. В нее подают пар и из нее отбирают конденсат. Схема пароснабжения пакетировщика показана на рис. 3.16, где для наглядности поддоны раздвинуты. Пар в полость каждого поддона-формы 4 подают, присоединяя к штуцеру формы гибкий шланг 3 от парораспределительной
95
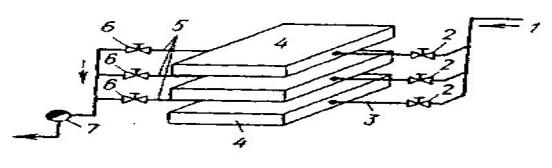
системы 1 и регулируют его подачу вентилями 2. Отбор конденсата осуществляется также с помощью шлангов 5, присоединяемых к штуцерам поддона формы. Открываются вентили 6, и конденсат через конденсатоотводчик 7 спускается в систему конденсатоотбора.
Тепловую обработку изделий проводят без предварительной выдержки. Каждое изделие, кроме верхнего, обогревается с двух сторон. Чтобы обеспечить оптимальные режимы тепловой обработки, на пакетировщике устанавливают регулятор программного регулирования температуры. Подъем температуры осуществляют до 90…95 °С за 2 ч. Однако прогрев изделий в таких формах неравномерен, в местах, удаленных от подачи пара, температура бетона на 30…40 °С в течение первых 2…3 ч меньше. Поэтому прочность на сжатие изделий, прошедших тепловую обработку в пакетировщиках, в разных точках бывает различной.
Несмотря на то, что для нагрева в пакетных установках применяют пока только пар, однако не исключается возможность обогрева и высококипящими органическими теплоносителями, масляными теплоносителями и др. Наиболее выгоден и целесообразен для пакетных установок переход на эжекционное пароснабжение с рециркуляцией части паровоздушной смеси, которое применяют для нагрева кассетных установок. Расход пара на обогрев термоформ составляет 200…300 кг на 1 м3 бетона.
Рис. 3.16. Схема пароснабжения пакетировщика: 1 – парораспределительная система; 2, 6 – вентили; 3, 5 – гибкие шланги; 7 – конденсатоотводчик
3.5.Малонапорные термоформы
Впоследнее время в связи с доказанной целесообразностью тепловлажностной обработки в среде с избыточным давлением начинают применять рекомендованные НИИЖБом малонапорные термоформы. Процесс тепловлажностной обработки в малонапорных термоформах коренным образом отличается от тепловой обработки в термоформах пакетировщика, где материал нагревается с двух сторон через стенки. В малонапорных термоформах материал нагревается непосредственно паром, который по-
96
дается в пространство, где находится распалубленное изделие и где оно одновременно обжимается созданным избыточным давлением.
Для тепловлажностной обработки в малонапорных термоформах используют тот же пакетировщик, что показан на рис. 3.15, и обычную стальную силовую форму-поддон, которую оборудуют двумя штуцерами, одним – для подвода пара, другим – для отбора конденсата. Тепловлажностной обработке в малонапорных термоформах подвергают изделия из жестких бетонных смесей после немедленной их распалубки. Для создания такой своеобразной малонапорной термоформы-камеры используют пространство под силовым поддоном фермы, в которое попадает распалубленное изделие, находящееся на другом силовом поддоне. С этой целью в пакетировщик (см. рис. 3.15) ставят силовой поддон без изделия и поднимают его, устанавливая на защелки. Далее поднимают силовой поддон уже с распалубленным изделием, затем следующий силовой поддон также с распалубленным изделием, потом следующий силовой поддон также с распалубленным изделием и так до шести поддонов, считая первый незагруженный. Таким образом на пакетировщике образуется пять малонапорных форм, где и проводится тепловлажностная обработка.
На рис. 3.17 показаны отдельно от пакетировщика три силовых поддона. Первый, свободный силовой поддон 6 показан сверху, так же как он и расположен в пакетировщике. Второй поддон 2 с изделием находится под ним, причем для герметизации между швеллерами-подставками первого поддона и второго поддона помещены прокладки 3. На втором поддоне находится распалубленное изделие 4, которое размещается в пространстве, образованном швеллерами-подставками первого поддона. Таким образом под швеллерами-подставками первого поддона и вторым поддоном образовалось пространство 5, где и размещается изделие, находящееся на втором поддоне. Ниже располагается третий поддон 1 с изделием 4. Подача пара 7 и отбор конденсата 8 в малонапорные камеры осуществляются так же, как и в пакетных установках (см. рис. 3.16).
Избыточное давление среды, окружающей изделие, до 0,03 МПа в таких малонапорных камерах создается за счет расширения паровоздушной смеси в замкнутом объеме и вследствие испарения влаги из бетона. Поскольку камера перед подачей в нее пара заполнена воздухом, который в процессе тепловлажностной обработки не удаляется, начальная относительная влажность в таких камерах достигает 40…50 %. В дальнейшем изза испарения влаги относительная влажность возрастает и за 2…2,5 ч с момента начала обработки достигает 90…95 %. Общая продолжительность обработки бетона в малонапорных термоформах составляет около 6…8 ч. Прочность пропаренного бетона в таких формах на 20…25 % выше проч-
97
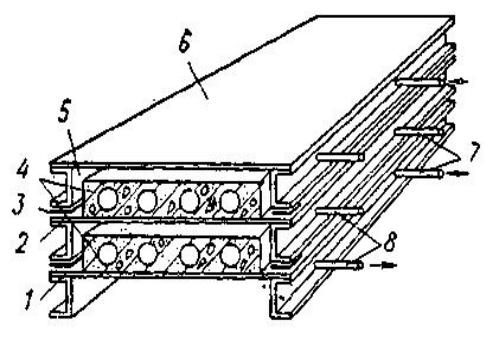
ности бетона, пропаренного при атмосферном давлении, повышается также и морозостойкость бетона.
Рис. 3.17. Изделие на силовом поддоне: 1 – третий поддон; 2 – второй поддон; 3 – прокладки; 4 – изделие; 5 – пространство для изделия; 6 – силовой поддон; 7 – подача пара; 8 – отбор конденсата
3.6. Автоклав
Автоклав (рис. 3.18) представляет собой цилиндрический горизонтальный сварной сосуд с открывающимися съемными крышками. Могут изготавливаться автоклавы с рабочим давлением от вакуума до 4 МПа и температурой нагрева до +380 °С, внутренним диаметром до 6000 мм.
Корпус автоклава состоит из сваренных между собой стальных оболочек. Крышки герметично закрываются с помощью быстродействующих затворов байонетного типа (рис. 3.19).
В соответствии со схемой можно выделить пять этапов автоклавной обработки запаривания.
98