
- •Частина 1. Основні поняття про виріб, виробничий і технологічний процесах. Поняття про якість приладів.
- •1.1. Види виробів.
- •1.2. Види конструкторських документів.
- •1.3. Основні етапи проектування приладів.
- •1.4. Виробничий і технологічний процеси. Структура технологічного процесу.
- •1.5. Типи виробництва
- •1.8. Поняття про якість приладів. Загальні стани.
- •1.9. Продуктивність механічної обробки.
- •1.10. Економічний аналіз технологічних процесів
- •1.11. Загальна характеристика методів виробництва і питома вага окремих методів.
1.8. Поняття про якість приладів. Загальні стани.
Згідно з Гостом 15.467-70 під якістю приладів розуміється сукупність властивостей продукції(приладу), що обумовлюють їх придатність задовольняти певні потреби відповідно до її призначення.
Властивість приладу - це об'єктивна особливість продукції приладобудівного виробництва, що проявляється при її створенні і експлуатації. До властивостей приладів можна віднести точність, стабільність, економічність, надійність роботи виробу та ін.
Кількісною характеристикою властивостей приладів, що входять до складу її якості(стосовно певних умов її створення і експлуатації) являється показник якості приладів.
Одиничний показник якості - це показник якості приладу, що відноситься тільки до однієї з його властивостей. Наприклад, одиничним показником якості підсилювачів низької частоти будуть: коефіцієнт нелінійних спотворень, виражений у відсотках; нерівномірність частотної характеристики і динамічний діапазон, виражені в децибелах та ін.
Комплексним показником якості продукції називається такий показник якості продукції, який відноситься до декількох її властивостей. За допомогою цього показника можна в цілому охарактеризувати якість того або іншого приладу. Різновидом комплексного показника якості, що дозволяє з економічної точки зору визначити оптимальну сукупність властивостей виробу, є інтегральний показник якості. Це комплексний показник якості, який відбиває співвідношення сумарного корисного ефекту від експлуатації і сумарних витрат на створення і експлуатацію приладу.
Для визначення відносної характеристики якості приладу використовують базовий показник якості, прийнятий за початковий при порівняльних оцінках якості.
Відносною характеристикою якості продукції заснованої на порівнянні сукупності показників її якості з відповідною сукупністю базових показників, являється рівень якості приладів.
Основні групи показників якості.
Якість продукції не є результатом тільки виробничого процесу, воно формується на усіх етапах створення і споживання виробу - проектування, виготовлення і експлуатації.
Оскільки якість розглядається як міру відповідності властивостей виробу вимогам споживача, то вона визначається на усіх етапах, де враховуються потреби споживача, визначаються і реалізуються властивості виробу.
Нині показники якості рекомендується класифікувати по наступних восьми групах:
1. Показники призначення, які визначають корисний ефект від використання приладу за призначенням і сфера його застосування. До них відносяться показники, використовувані для класифікації за призначенням, характеризуючі конструкцію приладу, його технічну досконалість, склад, структуру, транспортабельність(наприклад, точність, коефіцієнт нелінійних спотворень, динамічний діапазон, смуга відтворних частот, вихідна потужність, к.п.д., маса, габаритні розміри і тому подібне).
2. Показники надійності і довговічності, які характеризують безвідмовність, ремонтопридатність, сохраняемость і довговічність приладу визначається ГОСТ 133777-75.
3. Показники технологічності, що характеризують ефективність конструктивно-технологічних рішень для забезпечення високої продуктивності праці при виготовленні і ремонті приладу. До цих показників відносяться: коефіцієнт сборности виробів, коефіцієнт раціонального використання матеріалів, а також питомі показники трудомісткості виробництва. Терміни і визначення технологічності конструкції наводяться в ГОСТ 18831-73.
4. Ергономічні показники, що характеризують систему «людина-виріб-середовище». Для багатьох приладів такі показники є одними з основних.
Ергономічні показники можна класифікувати як:
гігієнічні показники(рівні оснащеності, температури, вологості, тиску, напруженості магнітного і електричного полів, запиленої, випромінювання, шуму, вібрації і перевантаження);
антропометричні показники(відповідність конструкції виробу розмірам тіла людини і його окремих частин, розподіл ваги людини);
фізіологічні і психофізіологічні показники(відповідність конструкції виробу силовим можливостям людини, швидкісним можливостям, зоровим, психофізіологічним, слуховим і дотиковим);
психологічні показники (відповідність виробу можливостям сприйняття і переробки інформації, закріплюваним і знову формованим навичкам людини при користуванні виробом.
5. Естетичні показники, що характеризують художність, виразність і оригінальність форми виробу, гармонійність і цілісність конструкції виробу середовищу і стилю, колірне і декоративне рішення виробу, художнє рішення упаковки і тому подібне
Основний закон художнього конструювання можна сформулювати таким чином: нерозривний зв'язок функції, конструкції і форми, або інакше єдність функціонального, конструктивного і естетичного.
6. Показники стандартизації і уніфікації характеризують міру використання в конкретному виробі стандартизованих деталей, складальних одиниць, блоків і рівень уніфікації складових частин виробу. Для його оцінки використовуються такі характеристики, як коефіцієнт уніфікації, коефіцієнт вживаності, коефіцієнт повторюваності та ін.
7. Патентно-правові показники, що характеризують міру патентного захисту і патентної чистоти виробів.
При визначенні цих показників, враховуються наявність у виробі вітчизняних винаходів, що захищаються авторськими свідоцтвами і патентами за кордоном і наявності реєстрації промислового зразка і товарного в Україні і країнах передбачуваного експорту. Для об'єктивнішого визначення патентно-правових показників слід враховувати нерівноцінний техніко-економічний ефект від впровадження цих винаходів, міра і час популярності технічних рішень, закладених у виробі; значущість порушуваних патентів для виробу в цілому.
8. Економічні показники характеризують витрати на проведення науково-технічних і дослідно-конструкторських робіт, пов'язаних з розробкою цього виробу, а також економічну ефективність експлуатації.
Це особливий вид показників, що оцінюють ремонтопридатність продукції, її технологічність, рівень стандартизації і уніфікації і патентну чистоту.
Точність - це міра відповідності виготовленого параметра виробу заданому параметру. Розрізняють задану, отриману і очікувану точність. Також розрізняють способи отримання необхідної точності : 1 - послідовного отримання на заготівлі заданої точності, 2 - автоматичного отримання заданої точності.
Поняття про якість поверхні.
Експлуатаційні характеристики деталей(зносостійкість, стійкість проти корозії, міцність, величина сил тертя та ін.) значною мірою залежать від якості поверхні.
Під якістю поверхні деталей розуміють физико-механическое і геометричний стан поверхні.
З физико-механической точки зору якість поверхні визначають відхилення фізичних і механічних властивостей поверхневого шару металу від його властивостей в середині деталі. При кожному методі обробки відбувається зміна поверхневого шару. Так при різанні виникають структури, мікротвердості(міра і глибина наклепання), виникає залишкова напруга.
В процесі різання відбувається пластична деформація шару металу і зміна структури. Метал в результаті пластичної деформації стає зміцненим: збільшується міцність і з'являється залишкова напруга. Міра зміцнення і глибина зміцненого шару залежать від методу обробки, режиму різання, геометрії стану(гострота) робочої кромки інструменту і властивостей початкового металу, швидкості різання. Міру зміцнення і глибину зміцненого шару обробленої поверхні визначають шляхом виміру мікротвердості на поверхні зрізу приладом ПМТ-3.
Ці виміри показують, що при усіх методах механічної обробки в поверхневому шарі виникає зміцнення:
Метод обробки |
Міра зміцнення
|
Глибина зміцненого шару, мкм |
Свердління і зенкерування |
160-170 |
80-200 |
Розгортання |
- |
до 300 |
Потягування |
150-200 |
20-75 |
Зубофрезерование і зубодолб. |
160-200 |
120-150 |
Фрезерування торців |
140-160 |
40-100 |
Фрезерування циліндричне |
120-140 |
40-80 |
Точіння |
140-180 |
20-60 |
Шліфування кругле вуглецевій сталі: а) загартованою; б) незагартованою |
125-130 140-160 |
20-40 30-60 |
Шліфування плоске |
150 |
16-35 |
Притирання пастами ГОИ |
112-117 |
3-7 |
Знак залишкової напруги залежить від режиму і методу обробки. Так при обточуванні з малою швидкістю в поверхневому шарі виникає стискуюча напруга, а при великих швидкостях що розтягують. При виборі режимів різання слід враховувати, що залишкова напруга стискування в поверхневому шарі збільшує втомну міцність, розтягування - знижують. Внутрішня напруга може з часом призводити до зміни форми деталі. При гарячій обробці(гаряче штампування, литво, плющення) поверхневий шар обезуглероживается на глибину 50-200 мк, у холоднотягнутої сталі, що калібрується, спостерігається часткове зневуглецювання до 70 мк. Зневуглецювання поверхневого шару має місце і при різанні, коли виникають значні температури(наприклад, шліфування).
З геометричної точки зору якість поверхні оцінюється наступними параметрами:
- макронерівністю
- хвилястістю
- мікронерівністю(шорсткістю).
Під макронерівністю розуміють одиничні, такі, що не повторюються регулярно відхилення поверхні від номінальної форми з малою висотою і дуже великим числом(для циліндричних деталей - овальність перерізу, криволінійність, ограновування, конусність, бочкоподібність, выгнутость і так далі).
Хвилястість - періодичне чергування виступів і западин, викликані нерівномірністю процесу різання(вібрацією).
Мікронерівність(шорсткість) - дійсний стан поверхні на малій її ділянці(1 кв. мм).
Шорсткість поверхні(ГОСТ 2789-73). Параметри шорсткості поверхні(рис.1) :
- середнє арифметичне відхилення профілю(100-0,008 мкм)
- висота нерівностей профілю по десяти точках(1600-0,025 мкм)
- найбільша висота нерівностей профілю(1600-0,025 мкм)
- середній крок нерівностей(12,5-0,002 мкм)
- середній крок нерівностей по вершинах(12,5-0,002 мм)
- відносна опорна довжина профілю _, _- значення рівня перерізу профілю.
Г
раничні
значення параметрів вказані вище в
дужках. При необхідності встановлюють
напрям нерівностей поверхні.
Рис.1 - Параметри шорсткості поверхні
,
де _ - базова довжина.
-
сума
середніх арифметичних абсолютних
відхилень точок п'яти найбільших
мінімумів і п'яти найбільших максимумів
в межах базової довжини:
,
де _ - відхилення п'яти найбільших максимумів профілю;
-
відхилення
п'яти найбільших мінімумів профілю.
Позначення шорсткості поверхні.
На місці цифр на малюнку робляться наступні написи:
(1)- параметр шорсткості поверхні по ГОСТ 2789-73;
(2)- вид обробки поверхні та ін. вказівки;
(3)- базова довжина по ГОСТ 2789-73;
(4)- умовні позначення напряму нерівностей.
Вживані знаки:
-
вид
обробки конструктором не встановлюється;
-
поверхня,
утворена видаленням шару металу(точіння,
шліфування, труїть та ін.);
-
поверхня
утворена без видалення шару металу(литво,
обробка тиском та ін.) або поверхня, що
не обробляється по цьому кресленню. _
не пишеться в позначенні.
Причини виникнення мікронерівностей.
Мікронерівність - основний параметр, що робить найбільш різнобічний вплив на експлуатаційні характеристики деталей приладів. Мікронерівність характеризується заввишки гребінців. На висоту мікронерівностей роблять вплив:
геометричні параметри інструменту(рис.2);
швидкість різання і подання;
установка інструменту відносно осі обертання.
Рис.2 - Вплив геометричних параметрів інструменту на висоту мікронерівностей
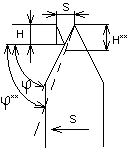
-
кути
різця в плані головний і допоміжний,
-
головне
різальне лезо
-
допоміжне
різальне лезо.
Різальні кромки зв'язані радіусом _. Висота мікронерівностей H пов'язана з кроком подання S. Кути _ значною мірою впливають на мікронерівності. Зі збільшенням _ висота мікронерівностей збільшується, зі зменшенням - зменшується.
Величини _ впливають на сили різання. Чим менше _, тим більше сили різання і навпаки. У свою чергу сили різання також впливають на мікронерівності, оскільки при різних силах заготівля отримує різний прогин.
При необхідності отримання точінням мінімальних мікронерівностей треба прагнути до того, щоб ((0. Припуск на обробку в цьому випадку має бути мінімальним.
2. Вплив швидкості різання.
В
плив
швидкості різання на чистоту поверхні
пов'язаний з утворенням наросту на
різці. Наріст зі збільшенням швидкості
до деякої величини збільшується, а при
подальшому збільшенні швидкості
зменшується. Швидкість, при якій виникає
найбільша величина наросту, називається
критичною. Для сталей вона дорівнює
15-30 м/сек. Відповідно до збільшення
наросту на різці збільшуються сили
різання, що прогинає оброблювану
заготівлю, завдяки чому збільшується
висота мікронерівностей.
При швидкості V>Vкр наріст не устигає утворюватися і майже не утримується на різці.
3. Вплив установки інструменту відносно осі обертання.
Вершина різця повинна встановлюватися на осі обертання, при іншому положенні вершини різця збільшуються сили різання, і погіршується поверхня зразка.
Якість поверхні встановлюється на основі ГОСТ 2789-73.
Кількісно воно визначається одним з наступних параметрів :
а) середнім арифметичним відхиленням _=100.0,08 мкм;
б) висотою нерівностей _=1600.0,025 мкм;
=1600..0,025
мкм;
=12,5..0,002
мкм;
=12,5..0,002
мкм
Мал. 4 - Кількісне визначення якості поверхні
Середнім арифметичним відхиленням профілю _ називається середнє арифметичне відстаней(y1, y2, y3,...,yn) точок виміряного профілю до його середньої лінії m - n(рис.4).
Середня лінія m - n ділить виміряний профіль таким чином, що в межах базової довжини L сума квадратів відстаней(y1, y2, y3,...,yn) точок профілю до цієї лінії мінімальна. При визначенні положення середньої лінії допускається наступна умова: в межах базової довжини L площі по обох сторонах лінії m - n до лінії профілю рівні між собою
.
Середнє арифметичне відхилення профілю _ до среднeй лінії підсумовується без урахування знаку алгебри :
.
Висота нерівностей _ - ця середня відстань між тими, що знаходяться в межах базової довжини L п'ятьма вищими точками виступів і п'ятьма нижчими точками западин, виміряне від лінії, паралельної середньої лінії m - n(рис.4).
.
Стандартом встановлені 14 класів чистоти поверхні. Найгрубіший клас чистоти 1й клас - (1, самий високоякісний - _=0,003 мкм. Шорсткість грубіше за 1-й клас позначається знаком_, над яким вказується висота нерівностей в мікронах. Для 1-го класу _=300 мкм і _=80 мкм; для 14-го класу _=0.05 мкм і _=0.01 мкм. Гостом визначаються величини для оцінки мікронерівностей (класу чистоти), так 6-12 класів визначаються по _, а 1-5 і 13-14 по _. Це пояснюється тим, що при визначенні чистоти користуються різними приладами, що дають залежно від вимірюваних величин різну погрішність. Прилади дозволяють записати у збільшеному масштабі профіль поверхні - профилограмму поверхні. Для визначення мікронерівностей застосовують контактні прилади (оптико-механические профілографи, електродинамічні, п'єзоелектричні і індуктивні профілографи) і безконтактні (інтерференційні, подвійні, мікроскопи, мікроскопи порівняння) прилади.
При проектуванні технологічних процесів слід користуватися відповідними матеріалами, в яких вказаний клас чистоти поверхні залежно від службового призначення деталі, і даними про те, яка чистота поверхні може бути отримана при застосуванні того або іншого виду і режиму обробки.