
Основы проектирования машин / ГЛАВА 4.2.1 СОЕДИНЕНИЯ С НАТЯГОМ
.pdf
ГЛАВА 4.2.1 СОЕДИНЕНИЯ С НАТЯГОМ.
Соединения этого типа воспринимают внешнюю нагрузку за счет сил трения, создаваемых в контакте собранных деталей вследствие натяга. В свою очередь натяг достигается за счет разности посадочных размеров вала и сопряженного с ним отверстия. С помощью натяга обычно соединяют детали с цилиндрическими (реже - коническими) поверхностями контакта.
Сборка такого соединения может быть выполнена:
•запрессовкой под прессом;
•нагревом либо охлаждением одной из деталей;
•гидрозапрессовкой, т.е. нагнетанием масла под давлением в зону контакта с целью снижения силы запрессовки.
Соединение с натягом относится к разряду полуразъемных, которые допускают разборку, но в исключительных случаях, так как она может привести к частичному разрушению поверхности.
Любой вид внешней нагрузки, приложенной к соединению, методами механики может быть приведен к совокупности следующих четырех силовых факторов, действующих в лежащей на оси соединения точке симметрии:
•результирующая осевая сила Fa , приложенная в направлении оси вращения;
•результирующий момент вращения T ;
•суммарная радиальная сила Fr ;
•суммарный момент изгиба M .
Пример такого соединения для общего случая нагружения приведен на рис. 4.2.1a,b. На рис. 4.2.1a дана
также кривая распределения давления p на поверхности контакта вследствие натяга, рассчитанная методами теории упругости (очевидно, что вследствие различий в жесткости давления по краям будет меньше, чем в
центре).
|
|
|
|
|
|
|
|
|
|
|
|
|
|
|
|
|
|
|
|
|
|
|
|
|
|
|
|
|
|
|
|
|
|
|
|
|
|
|
|
|
|
|
|
|
|
|
|
|
|
|
|
|
|
|
|
|
|
|
|
|
|
|
|
|
|
|
|
|
|
|
|
|
|
|
|
|
|
|
|
|
|
|
|
|
|
|
|
|
|
|
|
|
|
|
|
|
|
|
|
|
|
|
|
|
|
|
|
|
|
|
|
|
|
|
|
|
|
|
|
|
|
|
|
|
|
|
|
|
|
|
|
|
|
|
|
|
|
|
|
|
|
|
|
|
|
|
|
|
|
|
|
|
|
|
|
|
|
|
|
|
|
|
|
|
|
|
|
|
|
|
|
|
|
|
|
|
|
|
|
|
|
|
|
|
|
|
|
|
|
|
|
|
|
|
|
|
|
|
|
|
|
|
|
|
|
|
|
|
|
|
|
|
|
|
|
|
|
|
|
|
|
|
|
|
|
|
|
|
|
|
|
|
|
|
|
|
|
|
|
|
|
|
|
|
|
|
|
|
|
|
|
|
|
|
|
|
|
|
|
|
|
|
|
|
|
|
|
|
|
|
|
|
|
|
|
|
|
|
|
|
|
|
|
|
|
|
|
|
|
|
|
|
|
|
|
|
|
|
|
|
|
|
|
|
|
|
|
|
|
|
|
|
|
|
|
|
|
|
|
|
|
|
|
|
|
|
|
|
|
|
|
|
|
|
|
|
|
|
|
|
|
|
|
|
|
|
|
|
|
|
|
|
|
|
|
|
|
|
|
|
|
|
|
|
|
|
|
|
|
|
|
|
|
|
|
|
|
|
|
|
|
|
|
|
|
|
|
|
|
|
|
|
|
|
|
|
|
|
|
|
|
|
|
|
|
|
|
|
|
|
|
|
|
|
|
|
|
|
|
|
|
|
|
|
|
|
|
|
|
|
|
|
|
|
|
|
|
|
|
|
|
|
|
|
|
|
|
|
|
|
|
|
|
|
|
|
|
|
|
|
|
|
|
|
|
|
|
|
|
|
|
|
|
|
|
|
|
|
|
|
|
|
|
|
|
|
|
|
|
|
|
|
|
|
|
|
|
|
|
|
|
|
|
|
|
|
|
|
|
|
|
|
|
|
|
|
|
|
|
|
|
|
|
|
|
|
|
|
|
|
|
|
|
|
|
|
|
|
|
|
|
|
|
|
|
|
|
|
|
|
|
|
|
|
|
|
|
|
|
|
|
|
|
|
|
|
|
|
|
|
|
|
|
|
|
|
|
|
|
|
|
|
|
|
|
|
|
|
|
|
|
|
|
|
|
|
|
|
|
|
|
|
|
|
|
|
|
|
|
|
|
|
|
|
|
|
|
|
|
|
|
|
|
|
|
|
|
|
|
|
|
|
|
|
|
|
|
|
|
|
|
|
|
|
|
|
|
|
|
|
|
|
|
|
|
|
|
|
|
|
|
|
|
|
|
|
|
|
|
|
|
|
|
|
|
|
|
|
|
|
|
|
|
|
|
|
|
|
|
|
|
|
|
|
|
|
|
|
|
|
|
|
|
|
|
|
|
|
|
|
|
|
|
|
|
|
|
|
|
|
|
|
|
|
|
|
|
|
|
|
|
|
|
|
|
|
|
|
|
|
|
|
|
|
|
|
|
|
|
|
|
|
|
|
|
|
|
|
|
|
|
|
|
|
|
|
|
|
|
|
|
|
|
|
|
|
|
|
|
|
|
|
|
|
|
|
|
|
|
|
|
|
|
|
|
|
|
|
|
|
|
|
|
|
|
|
|
|
|
|
|
|
|
|
|
|
|
|
|
a) |
|
|
|
|
|
|
|
|
|
|
b) |
|
|
|
Рис. 4.2.1
Расчет соединения с натягом по критерию несдвигаемости. Несущая способность соединения с натягом зависит как от величины, так и характера внешней нагрузки. Например, при приложении осевой силы натяг может быть недостаточным, что приведет к сдвигу поверхностей в контакте. Для соединения это недопустимо, поэтому критерием расчета его несущей способности является отсутствие сдвига, т. е. критерий несдвигаемости. Такой же используется в случае приложения момента вращения.
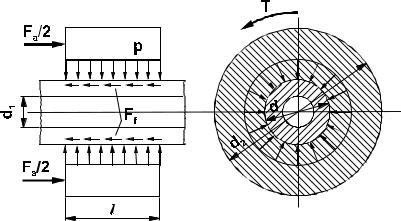
Рис. 4.2.2
В качестве примера расчета соединения с натягом по критерию несдвигаемости рассмотрим контакт двух деталей цилиндрической формы (рис. 4.2.2). Для того чтобы обеспечить отсутствие сдвига, необходимо, чтобы сила трения в контакте была больше, чем приложенная внешняя результирующая сдвигающая нагрузка. Сила
трения Ff определяется по формуле
Ff = ∫pfdA
A , (4.2.1)
где p - давление на поверхности контакта, dA и A - площадь элементарной площадки и полная площадь
поверхности в контакте, f - коэффициент трения в контакте.
Дальнейшее рассмотрение основано на предположении о постоянстве давления в точках контакта, которое диктуется двумя обстоятельствами: во-первых, фактическая эпюра распределения давлений при больших натягах мало отличается от постоянной; во-вторых, расчет фактической картины распределения требует использования численных методов, которые трудно осуществить практически.
Итак, полагаем, что на поверхности контакта за счет натяга создано постоянное давление |
p . Тогда в |
|
результате интегрирования из (4.2.1) получаем |
|
|
Ff |
= pfπdl |
(4.2.2) |
|
. |
Здесь d и l - соответственно диаметр цилиндрической поверхности и осевая протяженность контакта.
Очевидно, что условие несдвигаемости при приложении осевой силы Fa с учетом (4.2.2) запишется как
Ff = pfπdl ≥ Fa , |
|
|||
откуда |
|
|
|
|
p ≥ |
FaK s |
= p |
|
|
|
|
|
||
|
πdlf |
0 |
|
|
|
|
, |
(4.2.3) |
|
|
|
|
где p0 - максимально допустимое значение давления, при котором нет неупругих относительных перемещений собранных деталей после приложения к ним внешней нагрузки; Ks - коэффициент запаса сцепления.
Если соединение воспринимает момент вращения T , то условие несдвигаемости приобретает вид

pπdlf |
d |
≥T |
|
2 |
|||
|
, |
||
или |
|
|
p ≥ |
2TK s |
= p |
|
|
|
|
|
||
|
πd2lf |
o |
|
|
|
|
. |
(4.2.4) |
|
|
|
|
При одновременном действии осевой силы Fa и момента вращения T расчет несдвигаемости рекомендуется выполнять так же, как для случая нагружения эффективной осевой силой Fs , величина которой
определяется в результате векторного сложения внешней осевой Fa |
и окружной Ft |
(от момента вращения) сил, |
|||||
а именно |
|
|
|
|
|
|
|
Fs = (Fa )2 +(Ft |
)2 , |
Ft |
= |
2T |
|
||
|
|
|
|
|
|
d , |
|
так что максимально допустимое давление в контакте равно |
|
|
|
|
|
|
|
p = |
|
FsK s |
|
|
|
|
|
|
πdlf |
|
|
|
|||
0 |
|
. |
|
(4.2.5) |
|||
|
|
|
|
|
|
Из неравенств (4.2.3) - (4.2.4) видно, что несущая способность соединения с натягом при заданных
материалах и геометрии деталей прямо пропорциональна коэффициенту трения f , поэтому результат расчета во многом зависит от правильности его выбора. Между тем задача выбора сложна, так как значение коэффициента
трения f зависит от многих факторов, и прежде всего от:
•технологии сборки;
•вида материала;
•чистоты обработки поверхности и наличия погрешности формы;
•давления в контакте;
•наличия на поверхности смазки.
Обычно при расчете соединений используют среднее значение коэффициента трения. Для определения
числовых значений трения f можно воспользоваться данными таблицы 4.2.1, в которой приведены значения коэффициента трения в случае соединения с валом, изготовленным из стали.
Таблица 4.2.1: Усредненные значения коэффициентов трения при расчете посадок с натягом
Способ |
|
|
Алюминиевые и |
|
|
сборки |
Сталь |
Чугун |
магниевые |
Латунь |
Пластмассы |
соединения |
|
|
сплавы |
|
|
|
|
|
|
|
|
Механический |
0,06 - 0,13 0,07 - 0,12 |
0,02 - 0,06 |
0,05 - 0,1 |
0,4 - 0,5 |
|
Тепловой |
0,14 - 0,16 |
0,07 - 0,09 |
0,05 - 0,06 |
0,05 - 0,14 |
- |
К погрешности расчета приводит и тот факт, что давление по длине вала непостоянно. Неравномерность распределения давления существенно зависит от длины контакта, фактической геометрии деталей в соединении и погрешностей формы поверхностей сопряжения. Следует отметить, что учет вышеуказанных факторов достаточно сложен и не может быть реализован в рамках принятых допущений (см. приведенную на рис. 4.2.1 кривую распределения контактных давлений, полученную методами теории упругости).
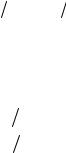
В конечном итоге общая ошибка, допущенная в результате описанного расчета, в случае статического нагружения может быть скомпенсирована за счет правильного выбора коэффициента запаса сцепления, который
можно принимать равным K s =12, ÷1,4 .
В случае переменного нагружения при выборе f необходимо учитывать то обстоятельство, что натяг в соединениях, к которым приложена переменная нагрузка, ослабевает с течением времени. Происходит это потому,
что переменный характер напряжений в контакте вызывает перераспределение давлений и, как следствие, их уменьшение. Подробно усталостные явления в контакте не изучены, а потому при расчетах для случая
переменного нагружения рекомендуется уменьшить значения коэффициента трения примерно на 30 −40 %. Отметим, что в связи с ослаблением натяга в течение времени действия переменной нагрузки при таких режимах
лучше использовать другие, более надежные методы крепления, которые будут описаны ниже.
Перейдем теперь к задаче подбора посадки. Как уже говорилось выше, требуемое значение контактного давления в соединении должно быть обеспечено натягом, полученным за счет разности диаметров вала и отверстия. Более подробно эта задача рассмотрена в главе 2.8. Там получена зависимость (2.8.20), связывающая давление и натяг для контакта двух толстостенных цилиндров. В принятых здесь обозначениях она имеет вид
po = |
|
δc |
|
|
|
|
|
|
|
d(C |
E +C |
02 |
E |
2 |
) |
|
, |
( 4.2.6) |
|
|
|
01 1 |
|
|
|
||||
где δc - расчетный натяг; E1, E2 - модули упругости двух сопряженных деталей; |
|
C01, C02 - |
|||||||
некоторые постоянные величины, зависящие от геометрии и механических характеристик материалов и |
|||||||||
рассчитываемые по формулам |
|
|
|
|
|
|
|
|
|
C01 = (d 2 +d12 ) (d 2 −d12 )−µ1; |
|
||||||||
C02 = (d22 +d 2 ) (d22 −d 2 )+µ2 . |
|
Для дальнейшего рассмотрения введем, помимо расчетного натяга δc , понятие измеренного натяга δi . Физический смысл этого понятия состоит в следующем. Любая поверхность после механической обработки имеет
микронеровности, высота которых зависит от чистоты обработки этой поверхности. Численной характеристикой
оценки чистоты обработки поверхности, как было отмечено в главе 1.2 , является параметр Ra . Величина измеренного натяга должна быть уменьшена на величину поправки на шероховатость, так как несущая способность
погрешного слоя (под погрешным слоем понимается такой поверхностный слой поверхности, для которого не соблюдается условие сплошности) много ниже, чем сплошного материала. С учетом сказанного величина
измеренного натяга δi складывается из расчетного δc и поправки |
u на шероховатость: |
|
|
δi |
=δc +u . |
|
( 4.2.7) |
Величину поправки u рекомендуется определять по формуле |
|
|
|
u = 5,5(Ra1 + Ra2 ) |
, |
( 4.2.8) |
|
|
|
где Ra1 и R a2 - средние арифметические отклонения профиля микронеровностей посадочных поверхностей. По величине измеренного натяга подбирается посадка с последующей проверкой статической прочности
соединяемых деталей.
Вопрос расчета напряжений, возникающих в результате сборки, был рассмотрен ранее в главе 2.8 , здесь лишь отметим, что прочность двух сопряженных деталей считается удовлетворительной, если эквивалентные
напряжения σe1 и σe2 наиболее нагруженных точек не превышают пределов текучести σr1 и σr2 материалов рассматриваемых сопряженных деталей. При этом условие прочности вала имеет вид

|
|
|
|
|
|
σe1 ≤σr1 , |
(4.2.9) |
а условие прочности детали с отверстием |
|
||||||
|
|
|
|
|
|
σe2 ≤σr 2 . |
(4.2.10) |
|
|
|
|
|
|
|
|
|
|
|
|
|
|
|
|
|
|
|
|
|
|
|
|
|
|
|
|
|
|
|
|
|
|
|
|
|
|
|
|
|
|
|
|
|
|
|
|
|
|
|
|
|
|
|
|
|
|
|
|
|
|
|
|
|
|
|
|
|
|
|
|
Рис. 4.2.3
Эпюры напряжений сопряженных деталей (рис. 4.2.3) показывают, что наибольшие напряжения возникают на внутренней поверхности детали с отверстием. Согласно (2.8), наибольшие эквивалентные напряжения равны:
σe2 =σt −σn = |
2 po |
|
|
|
1 −(d d |
2 |
)2 |
|
|
|
|
. |
Тогда условие прочности (4.2.10) записывается в форме неравенства
2 po |
|
|
≤σ |
|
|
|
1 −(d d |
2 |
)2 |
r 2 |
(4.2.11) |
||
|
||||||
|
|
|
. |
Для вала проверка прочности в подавляющем большинстве случаев лишена смысла, так как напряжения на валу меньше, чем на сопряженной детали, кроме того, сам вал изготавливается из более прочного материала. В том случае, если такая необходимость есть, для проверочного расчета следует использовать формулу (2.8.16).
Расчет соединения с натягом из условия нераскрытия. Еще одним важным критерием расчета соединения с натягом является условие нераскрытия стыка.
Нагрузка в виде радиальной силы и момента изгиба может привести к появлению в соединении с натягом
некоторого зазора. Поскольку такое положение недопустимо, следует определить максимальный натяг p0 , при котором не происходит возникновения зазора. Такой расчет на нераскрытие стыка можно выполнять отдельно для
случая приложения радиальной силы Fr и для случая нагружения моментом изгиба M . При условии комбинированного нагружения искомый результат получается суммированием отдельных компонент.
а) Случай радиального нагружения.
Расчетная схема, принятая для рассматриваемого варианта нагружения, изображена на рис. 4.2.4.
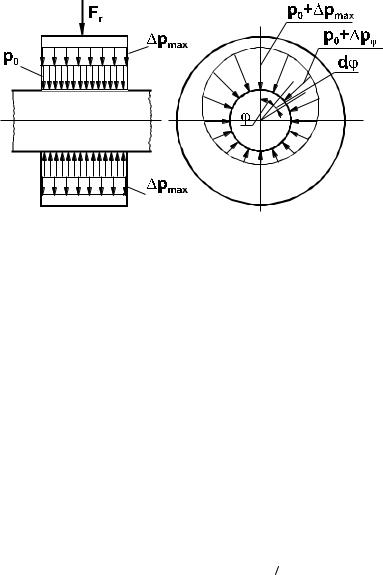
Рис. 4.2.4
После приложения рабочей нагрузки Fr в зоне контакта происходит перераспределение давлений. Для того чтобы получить числовые характеристики, описывающие закон распределения давлений по находящейся в
контакте поверхности площади A , можно воспользоваться уравнением равновесия. С этой целью под углом ϕ
выделяем элементарную площадку, опирающуюся на угол |
dϕ |
, давление на которой |
∆pϕ |
. Спроектировав |
||
|
|
|||||
нормальные силы, действующие на элементарные площадки, на направление приложения внешней нагрузки, |
||||||
получаем |
|
|
|
|
|
|
Fr = ∫∆pϕ |
d2 |
lcosϕdϕ |
|
(4.2.12) |
||
|
A |
|
|
. |
|
Если пренебречь погрешностями изготовления, а сопряженные детали считать абсолютно жесткими, то распределение давлений по дуге контакта может быть описано законом косинуса:
∆pϕ |
= ∆pmax cosϕ |
( 4.2.13) |
|
, |
где ∆pmax - давление на наиболее нагруженной площадке. После подстановки (4.2.13) в ( 4.2.12) имеем
|
dl |
π 2 |
|
|
Fr = 4∆pmax |
∫cos2ϕdϕ |
|
|
|
2 |
|
|
||
|
|
o |
. |
(4.2.14) |
Вычисляя интеграл в правой части (4.2.14) и разрешая полученное уравнение относительно ∆pmax ,
получаем выражения для наибольшего ∆pmax и текущего ∆pϕ давлений:
∆p |
max |
= |
|
2Fr |
; |
∆p |
ϕ |
= |
2Fr cosϕ |
|
|
|
πdl |
πdl |
. |
(4.2.15) |
|||||||||
|
|
|
|
|
||||||||
|
|
|
|
|
|
|
|
|
|
С учетом (4.2.15) окончательное выражение для описания условия нераскрытия при радиальном нагружении цилиндрического соединения с натягом принимает вид
∆p ≡ ∆p = |
2Fr |
≤ p |
|
|
π d l |
|
|||
max |
F |
0 |
(4.2.16) |
|
|
|
|
. |
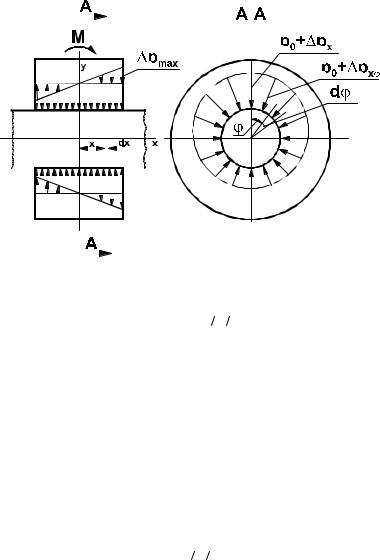
Из условия (4.2.16) и определяется то начальное давление p0 , которое не приведет к появлению зазоров в соединении с натягом.
б) Случай нагружения изгибающим моментом. При такой внешней нагрузке предполагается линейное распределение удельного давления по длине (рис. 4.2.5). Если под углом ϕ на расстоянии x выделить
элементарную площадку размером |
dxdϕ |
и обозначить давление на ней через |
∆pxϕ |
, то элементарный момент |
|||||||||||||||||||||||||||||||
|
|
|
|
|
|
|
|
|
|
||||||||||||||||||||||||||
dM i от выделенной площадки определится выражением |
|
|
|
|
|
|
|
|
|
|
|
|
|
|
|
||||||||||||||||||||
|
|
|
|
|
|
|
|
|
|
|
|
|
|
|
|
|
|
|
|
dM i = ∆pxϕ |
d |
x cosϕdϕdx |
|
|
|
|
|
|
|
||||||
|
|
|
|
|
|
|
|
|
|
|
|
|
|
|
2 |
. |
|
|
|
(4.2.17) |
|||||||||||||||
|
|
|
|
|
|
|
|
|
|
|
|
|
|
|
|
|
|
|
|
|
|
|
|
|
|
|
|
|
|
||||||
|
|
|
|
|
|
|
|
|
|
|
|
|
|
|
|
|
|
|
|
|
|
|
|
|
|
|
|
|
|
|
|
|
|
|
|
|
|
|
|
|
|
|
|
|
|
|
|
|
|
|
|
|
|
|
|
|
|
|
|
|
|
|
|
|
|
|
|
|
|
|
|
|
|
|
|
|
|
|
|
|
|
|
|
|
|
|
|
|
|
|
|
|
|
|
|
|
|
|
|
|
|
|
|
|
|
|
|
|
|
|
|
|
|
|
|
|
|
|
|
|
|
|
|
|
|
|
|
|
|
|
|
|
|
|
|
|
|
|
|
|
|
|
|
|
|
|
|
|
|
|
|
|
|
|
|
|
|
|
|
|
|
|
|
|
|
|
|
|
|
|
|
|
|
|
|
|
|
|
|
|
|
|
|
|
|
|
|
|
|
|
|
|
|
|
|
|
|
|
|
|
|
|
|
|
|
|
|
|
|
|
|
|
|
|
|
|
|
|
|
|
|
|
|
|
|
|
|
|
|
|
|
|
|
|
|
|
|
|
|
|
|
|
|
|
|
|
|
|
|
|
|
|
|
|
|
|
|
|
|
|
|
|
|
|
|
|
|
|
|
|
|
|
|
|
|
|
|
|
|
|
|
|
|
|
|
|
|
|
|
|
|
|
|
|
|
|
|
|
|
|
|
|
|
|
|
|
|
|
|
|
|
|
|
|
|
|
|
|
|
|
|
|
|
|
|
|
|
|
|
|
|
|
|
|
|
|
|
|
|
|
|
|
|
|
|
|
|
|
|
|
|
|
|
|
|
|
|
|
|
|
|
|
|
|
|
|
|
|
|
|
|
|
|
|
|
|
|
|
|
|
|
|
|
|
|
|
|
|
|
|
|
|
|
|
|
|
|
|
|
|
|
|
|
|
|
|
|
|
|
|
|
|
|
|
|
|
|
|
|
|
|
|
|
|
|
|
|
|
|
|
|
|
|
|
|
|
|
|
|
|
|
|
|
|
|
|
|
|
|
|
|
|
|
|
|
|
|
|
|
|
|
|
|
|
|
|
|
|
|
|
|
|
|
|
|
|
|
|
|
|
|
|
|
|
|
|
|
|
|
|
|
|
|
|
|
|
|
|
|
|
|
|
|
|
|
|
|
|
|
|
|
|
|
|
|
|
|
|
|
|
|
|
|
|
|
|
|
|
|
|
|
|
|
|
|
|
|
|
|
|
|
|
|
|
|
|
|
|
|
|
|
|
|
|
|
|
|
|
|
|
|
|
|
|
|
|
|
|
|
|
|
|
|
|
|
|
|
|
|
|
|
|
|
|
|
|
|
|
|
|
|
|
|
|
|
|
|
|
|
|
|
|
|
|
|
|
|
|
|
|
|
|
|
|
|
|
|
|
|
|
|
|
|
|
|
|
|
|
|
|
|
|
|
|
|
|
|
|
|
|
|
|
|
|
|
|
|
|
|
|
|
|
|
|
|
|
|
|
|
|
|
|
|
|
|
|
|
|
|
|
|
|
|
|
|
|
|
|
|
|
|
|
|
|
|
|
|
|
|
|
|
|
|
|
|
|
|
|
|
|
|
|
|
|
|
|
|
|
|
|
|
|
|
|
|
|
|
|
|
Рис. 4.2.5
Величина полного момента получается интегрированием (4.2.17) по поверхности контакта:
|
|
|
|
|
l 2π 2 |
|
|
|
|
|
d |
|
|
|
|
||
|
|
|
|
M =8 ∫ ∫∆pxϕ |
|
|
|
xcosϕdϕdx |
|
||||||||
|
|
|
|
|
|
2 |
(4.2.18) |
||||||||||
|
|
|
|
|
o o |
|
|
|
|
|
|
|
|
. |
|||
Величину |
∆pxϕ |
можно выразить через наибольшее давление |
∆p |
|
|
||||||||||||
|
|
|
|
|
max . Принимая во внимание линейный |
||||||||||||
|
|
|
∆p |
= ∆p |
|
2x |
|
|
|
|
|
|
|
|
|
|
|
|
|
|
|
|
|
|
|
|
|
|
|
|
|
|
|
||
характер распределения давлений по длине, |
x |
max l , и косинусоидальный (4.2.13) - по дуге, имеем |
|||||||||||||||
|
|
|
|
∆p |
= ∆p |
2x |
cosϕ |
|
|
||||||||
|
|
|
|
|
|
|
|
||||||||||
|
|
|
|
xϕ |
|
max |
|
l |
|
. |
|
(4.2.19) |
|||||
Выражение (4.2.18) с учетом ( 4.2.19) может быть переписано в виде |
|
|
|||||||||||||||
|
|
|
|
l 2π 2 |
|
dx2 |
|
|
|
||||||||
|
|
|
M = 8 ∫ |
∫∆pmax |
cos2 |
ϕdϕdx |
|
||||||||||
|
|
|
|
|
|||||||||||||
|
|
|
|
o |
o |
|
|
|
l |
. |
(4.2.20) |
||||||
|
|
|
|
|
|
|
|
|
|
|
|
После интегрирования из (4.2.20) получаем
∆p |
= |
12M |
≡ ∆p |
|
|
||||||
|
|
|
|
||||||||
|
max |
|
π d l2 |
|
M |
. |
(4.2.21) |
||||
|
|
|
|
|
|
|
|
|
|
||
В случае одновременного приложения силы и момента условие нераскрытия, используя принцип |
|
||||||||||
суперпозиции, можно записать в форме |
|
|
|
|
|
|
|
|
|
|
|
po −∆pF − ∆pM |
≥ 0 , |
(4.2.22) |
|||||||||
или |
|
|
|
|
|
|
|
|
|
|
|
|
|
2F |
|
12 M |
|
|
|||||
p0 |
≥ |
|
|
+ |
|
|
|
|
Kc |
|
|
πdl |
|
πdl |
2 |
|
|||||||
|
|
|
|
|
|
, |
(4.2.23) |
где p0 - начальное давление, при котором в наиболее удаленных точках при приложении внешней нагрузки не
появятся участки, свободные от нормальных давлений; Kc - коэффициент запаса по нераскрытию.
В заключение отметим, что выбор критерия расчета может быть сделан из сравнения значений величин натяга, рассчитанных по условиям отсутствия сдвига и нераскрытия. Окончательный расчет ведется по наибольшему из полученных давлений.
Кроме цилиндрических, с натягом могут быть установлены и конические соединения. При этом для малых углов конуса коническое соединение заменяется эквивалентным цилиндрическим, диаметр которого равен среднему диаметру конического соединения. В этом случае коническое соединение рассчитывается по той же методике, что и цилиндрическое. Такой подход к решению этой задачи будет оправданным в той степени, в которой угол конуса можно считать малой величиной.
Способы сборки соединения. Сборка соединений с натягом может быть выполнена:
•запрессовкой деталей под прессом (для цилиндрических соединений);
•тепловым способом (для цилиндрических и конических соединений).
При расчете прессового соединения определяется усилие пресса Fao , необходимое для осуществления сборки. Очевидно, что
|
Fao ≥ πdlpo f . |
(4.2.24) |
Здесь f - коэффициент трения при запрессовке (табл. 4.2.2). |
|
|
Таблица 4.2.2: Средние значения коэффициента трения при запрессовке |
|
|
Материал деталей соединения |
f |
|
Сталь - сталь |
0,20 |
|
Сталь - чугун |
0,14 |
|
Сталь - бронза, латунь |
0,10 |
|
Чугун - бронза, латунь |
0,08 |
|
При сборке соединения с использованием температурного деформирования определяют либо температуру t1 охлаждения внутренней детали (вала), либо температуру t2 нагрева внешней детали (отверстия). Выражение для определения t1 имеет вид
t1 = 20 − δi + ∆
dα , (4.2.25)
где α - коэффициент линейного расширения; ∆ - технологический зазор, необходимый для облегчения сборки
(табл. 4.2.3).
Температура t2 рассчитывается по формуле
t2 |
= 20 + |
δi + ∆ |
|
|
|
dα . |
(4.2.26) |
Таблица 4.2.3: Рекомендуемые значения ∆
d, мм |
30...80 |
80...180 |
180...400 |
∆ , мкм |
10 |
15 |
20 |
|
|
|
Заметим, что температурная сборка нагревом не всегда может быть реализована, так как при высокой температуре внутри металла могут произойти структурные превращения, которые, в свою очередь, способны вызвать изменение механических свойств материала.