
ТСС
.pdf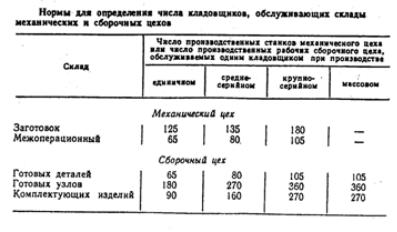
Σ = ( Ц ∙ (∑ ) ∙ П)/60 ∙
=1
где TЦ - средняя продолжительность одного транспортного цикла, мин; ∑=1( ) - суммарный годовой грузопоток, перерабатываемый данным видом транспорта, тонн или количество поддонов; КП - число транспортных операций в технологическом процессе перемещения; - масса груза или количество поддонов, перемещаемых транспортным средством за один цикл.
При определении КП необходимо иметь в виду, что при приеме груза погрузчик осуществляет транспортные операции дважды – сначала для разгрузки на площадку ВХ, а затем для перемещения поддона на приемный стол накопителя; штабелер при одноадресном цикле работы совершает два перемещения: сначала при загрузке, а затем при выгрузке, при двухадресном цикле средняя длительность цикла перемещения зависит от скорости штабелера, числа секций и ярусов хранения и составляет, например, при одноадресном цикле работы 1,2 ÷ 1,6 мин при высоте склада 10 м и числе секций 30 ÷ 50.
1.3.5.Расчет числа работающих на складе
Число кладовщиков в складах механического цеха определяют при укрупненном расчете в зависимости от числа производственных станков в складах сборочного цеха - в зависимости от числа производственных рабочих по нормам, приведенным в таблице 4.
Таблица 4. Нормы для определения числа кладовщиков.
Число рабочих в смену, обслуживающих разгрузочный участок склада, при детальном расчете определяют по числу транспортных единиц:
= М ∙
где nМ - число рабочих, обслуживающих один механизм (nМ = 2 для мостового крана (крановщик и стропальщик); nМ = 1 для крана-штабелера, управляемого с пола или из кабины; nМ = 1,5 для электропогрузчиков при перемещении деталей и заготовок в таре (в том числе один рабочий зарядной станции на два электропогрузчика)).
Число рабочих, занятых сортировкой, комплектованием или укладкой деталей в ориентированном виде в кассеты, определяют по норме переработки грузов одним рабочим склада в смену, составляющей 1 ÷ 1,5 Т.
21
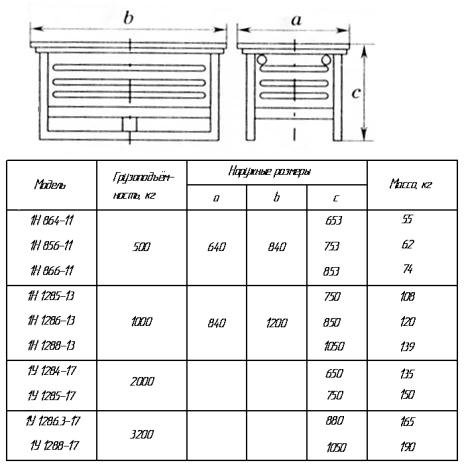
1.3.6. Классификация производственной тары.
Признаки классификации тары:
-по функциям, выполняемым в процессе товарного обращения; делят на транспортную и технологическую (спутники, паллеты);
-по назначению; делят на универсальную и специализированную; -по кратности использования; делят на многооборотную, возвратную и разового
использования; -по материалу; изготавливают из дерева, металла, полимеров или комбинированную;
-по конструкции; делят на ящичную, стоечную и плоскую; -по конструктивным особенностям; делят на разборную, неразборную, складную,
разборно-складную, со съемными деталями.
Параметры и конструкции ящичной тары показаны на рисунке 18 и в таблице 5.
Рис. 18. Конструкция ящичной тары.
Таблица 5. Параметры ящичной тары.
1.3.7. Классификация стеллажей – складов.
Фронтальные стеллажи представляют собой рамы с продольными балками, на которых хранятся поддоны. Оптимальными являются варианты таких стеллажей с расположение 2-3 поддонов на секцию. Доступ к поддонам обеспечен с фронтальной стороны.
Достоинства данного типа стеллажей:
-независимость от номенклатуры грузов; используются для средней и широкой номенклатуры грузов;
-простота и удобство доступа к каждой хранящейся паллете; -простота конструкции.
22
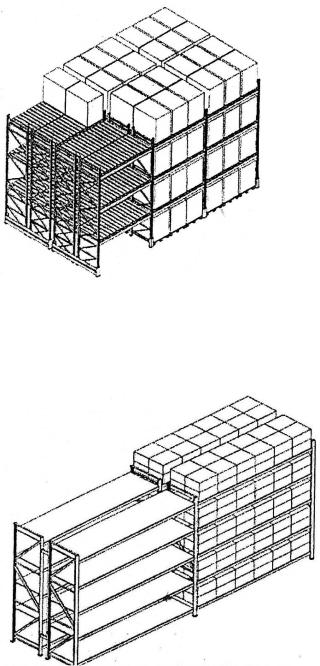
Недостатки стеллажей:
-нерациональное использование складских помещений из-за широких проходов для подъемно-транспортного оборудования.
Глубинные стеллажи (рис. 19) – груз загружается по горизонтальным направляющим внутрь глубины стеллажа; ширина прохода между стеллажами составляет 1350 мм. Для того чтобы выгрузить внутренние паллеты, необходимо сначала выгрузить внешнюю паллету. Эффективность использования объема помещения в данных стеллажах на 25% выше, чем во фронтальных, и составляет до 50-60% от площадисклада. Глубинные стеллажи наилучшим образом подходят для изделий узкой номенклатуры или для хранения однотипных изделий.
Рис. 19. Фронтально-глубинные стеллажи.
Стеллажи полочной конструкции (рис. 20) делят на две подгруппы: рамной и стоечной конструкции. Стоечная конструкция используется при небольших нагрузках, рамная – для средних и высоких нагрузках – до 600 кГ на полку. Предназначены для хранения изделий, не упакованных на паллеты (в различных коробках, ящиках и другой фасовочной таре).
Рис. 20. Стеллажи полочной конструкции.
23
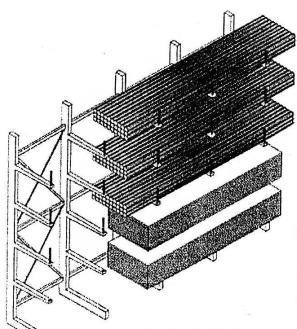
Консольные стеллажи (рис. 21) предназначены для хранения длинномерных или крупногабаритных грузов, конструктивно они представляют собой стойку на опоре и прикрепленные к стойке консоли.
Рис. 21. Консольные стеллажи.
Многоуровневые стеллажные системы (стеллажи мезонины) имеют широкую функциональность, позволяют создать индивидуальную конфигурацию.
1.4. Проектирование отделения по подготовке производственных (транспортных) партий
Комплектация грузов является ответственным этапом в технологическом процессе складирования и состоит в совокупности операций по перемещению грузов с разных мест хранения в одно место накопления для формирования транспортной (производственной) партии.
Детали, полуфабрикаты и готовые изделия доставляются к основному оборудованию с помощью транспортной системы в специальной таре, поддонах, кассетах, спутниках, паллетах или без использования перечисленных средств. Для обеспечения необходимого количества этих средств их необходимо складировать, кроме того для установки и фиксирования изделий, например, на спутниках и паллетах, используется универсальносборная оснастка (УСО).
Освободившиеся спутники, паллеты с УСО и другую тару перед складированием разбирают, моют и консервируют. Для выполнения этих работ в складских системах предусматривают следующие отделения:
сборки и разборки технологической оснастки;
установки и съема изделий;
мойки и консервации технологической оснастки.
1.4.1.Проектирование отделения сборки и разборки технологической оснастки
24
А. Функции этого отделения следующие:
хранение оборотного запаса производственной тары;
хранение оборотного запаса элементов УСО;
комплектация элементов УСО и установка их на тару (на спутники, кассеты, поддоны и паллеты);
своевременное обеспечение тарою рабочих мест по комплектации производственной партии, установки и съема изделий;
разборки УСО;
своевременная передача элементов УСО на мойку и консервацию.
Б. Оборудование для проведения работ в отделении
В отделении используют поворотные столы, слесарные верстаки, манипуляторы и другие подъемно-транспортные средства.
В. Расчет числа слесарей-сборщиков
Число рабочих определяется по формуле:
= (( ∙ ОП)/ФЭР) ∙ КВ
где NT – количество производственной тары, на которую устанавливается УСО, шт/год; tОП – время выполнения операций по сборке и разборке оснастки (принимается равным 1,35 … 6,6 часа в зависимости от группы сложности УСО); ФЭР – эффективный годовой фонд времени работы рабочего, час; КВ – коэффициент, учитывающий вспомогательные работы.
При укрупненных расчетах число комплектовщиков рассчитывается по нормам в зависимости от массы перерабатываемых грузов за смену: 1 комплектовщик на 1…1,5 тонны груза.
Г. Расчет числа элеваторных стеллажей для УСО
Для хранения УСО часто используют элеваторные стеллажи. Их число рассчитывают по формуле:
ЭУ = (( ∙ )/ ) ∙ КХ
где NTО – количество оборотной тары, шт; g – 0.1 т – масса одного комплекта УСО; Q = 10 т – вместимость одного элеваторного стеллажа; КX = 0,6 – доля УСО, находящаяся на хранении. Число элеваторных стеллажей для хранения производственной тары (спутники, паллеты, поддоны) NЭT – определяют по аналогичной формуле, но принимают среднюю массу одного спутника g = 0,3 т, а массу поддонов выбирают по справочным таблицам.
Д. Площадь, занимаемая элеваторными стеллажами FЭ
Определяется по формуле:
Э = ( ЭУ + ЭТ) ∙ 1
25
где f1 = 10 кв.м - производственная удельная площадь, занимаемая стеллажом.
Общая площадь отделения сборки и разборки технологической оснастки вычисляют по формуле:
= (Э + (Ф ∙ 2/СБ)
где f2 = 16 кв.м - производственная удельная площадь, занимаемая одним рабочимсборщиком или комплектовщиком; nсб – количество сборщиков.
1.4.2.Проектирование отделения установки и съема изделий
А. Функции отделения установки и съема изделий:
установка, выверка и закрепление изделий на спутниках, укладка в кассеты и в поддоны;
своевременное обеспечение производственных участков спутниками с установленными на них заготовками и полуфабрикатами, кассетами или поддонами;
снятие полуфабрикатов с технологической оснастки после изготовления:
своевременная отправка полуфабрикатов на складское хранение;
отправка технологической оснастки на разборку.
Б. Оборудование для проведения работ в отделении.
В этом отделении обычно устанавливают сборочные поворотные столы, манипуляторы, роликовые конвейеры приводного и неприводного типа, кантователи, слесарные верстаки, разметочные и контрольно-измерительные машины, подъемно-транспортные средства.
В. Расчет числа работающих и площади отделения.
Расчет ведут по приведенным выше формулам.
1.4.3.Отделение мойки и консервации технологической оснастки
А. Функции отделения:
промывка, сушка и пассивирование элементов УСО и спутников;
своевременная передача очищенных элементов УСО и спутников на хранение, в отделение сборки и разборки технологической оснастки.
Б. Оборудование для проведения работ в отделении
В отделении располагают моечную машину, сушильную камеру, пассивировочную камеру для гальванического покрытия чугунных деталей.
26

В. Количество работающих в отделении.
Укрупненно количество работающих определяют по нормам в зависимости от массы перерабатываемых грузов за смену – 1 рабочий на 1,0 … 1,5 тонны груза.
Г. Площадь отделения мойки и консервации оснастки
Площадь принимается равной 80 – 100 кв. м
1.5. Проектирование подсистемы хранения полуфабрикатов и изделий
Эта подсистема включает межоперационные склады, склады готовых деталей и изделий. Межоперационные склады обеспечивают хранение заделов, необходимых на различных технологических операциях в непоточном производстве. Они могут входить в общую структуру централизованного склада, могут быть частью автоматизированных транспортно-накопительных систем, а также могут являться автономными на участках изготовления деталей. Выбор варианта должен быть тесно увязан с выбором транспортной системы цеха.
Рис. 22. Принципиальная схема организации мелкосерийного и среднесерийного производства с применением АТСС.
Пример схемы организации мелкосерийного и среднесерийного производства с применением автоматизированной транспортно-складской системы (АТСС) показан на рисунке 19. Стеллажный автоматизированный склад 7 обслуживается краном-штабелером 13. Заготовки в зону приема и комплектации доставляются электрогрузовозом с прицепной тележкой 6, входящей в состав подвесной транспортной системы 12 с автоматическим адресованием. Межоперационную передачу грузов на станочных линиях 5 осуществляют быстроходные рельсовые каретки-операторы 10 с автоматическим адресованием по командам диспетчера с пульта 11. Диспетчер имеет двустороннюю связь с каждым рабочим местом. Межоперационные заделы хранят либо на приемных столах у рабочих мест, либо возвращают на склад 7. Детали в таре передает каретка-оператор на участок контроля 4 и далее - подвесной электрогрузовоз - на площадку 3 приема комплектации и выдачи склада 2
27
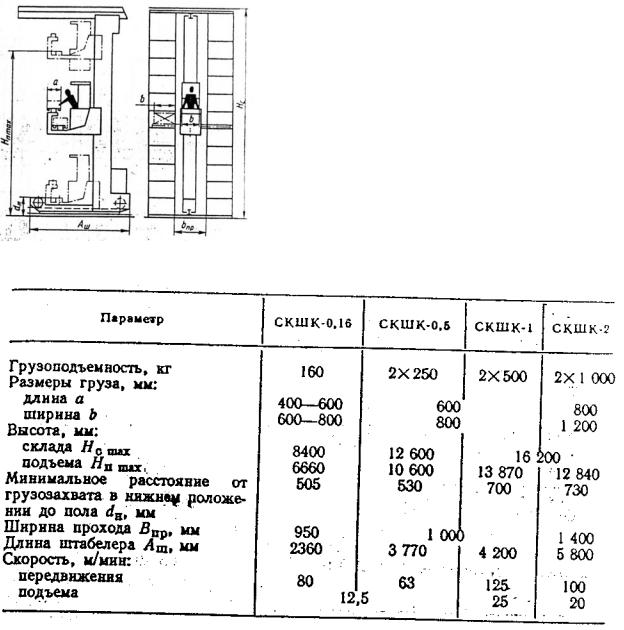
готовых деталей. Склад готовых деталей оборудован автоматизированным краномштабелером 13 и комплектовочным краном-штабелером 8. В сборочный цех 1 скомплектованные детали передаются подвесной транспортной системой с автоматическим адресованием 9.
В складах готовых деталей, особенно в единичном и мелкосерийном производстве, при большом объеме работ по подбору комплектов деталей для сборки изделий на участках комплектования используют обычные краны-штабелеры. Но больший эффект складских работ в таких складах получают при использовании специальных комплектовочных кранов. На рисунке 20 приведена схема, а в таблице 6 - основные параметры этих кранов.
Рис. 23. Габаритная схема и параметры стеллажных комплектовочных кранов-штабелёров
Таблица 6. Основные параметры комплектовочных кранов-штабеллёров.
Склады для хранения готовых узлов в сборочных цехах непоточного производства обычно совмещают со складом готовых деталей. Склад комплектующих изделий (подшипники, электрооборудование, прокладки, узлы) при получении их по кооперации со стороны
28
целесообразно размещать смежно со складом готовых деталей, однако в условиях массового производства его размещение должно быть связано с расположением главного конвейера и магистральных проездов для подвоза изделий.
Расчета площади, выбор параметров складов и используемых транспортных средств ведут по методике изложенной в разделе 1.3, и нормам из таблиц, приведённых ранее. Массу полуфабрикатов готовых деталей при этом принимают на 10% больше массы готовых деталей.
Склад готовых изделий обычно является общезаводским и в состав сборочного цеха не входит. На склад готовые изделия поступают после приемки ОТК завода и Государственной приемки.
1.6. Проектирование подсистемы хранения технологической оснастки и вспомогательных материалов
В механических и сборочных цехах предусматривают кладовые для хранения специальных приспособлений, участок сборки и хранения универсально-сборочных приспособлений (УСП) универсально-сборочной или переналаживаемой оснастки (УСПО), кладовые вспомогательных (хозяйственных и обтирочных) материалов.
Площадь указанных кладовых и участков определяют по нормам, приведенным в таблицах ранее, на один производственный станок механического цеха или на одного производственного рабочего сборочного цеха ( отделения). Следует иметь в виду, что меньшие значения приведенных норм даны для наибольшего габаритного размера производственных станков до 1800 мм или массы собираемых изделий (для кладовых сборочного цеха ) до 0,2 т. Наибольшие значения относятся к станкам с наибольшими габаритным размером до 8000 мм и массой собираемых изделий более 50 т. Промежуточные значения получают интерполированием.
Обычно самостоятельные кладовые приспособлений и инструментальной оснастки создают в цехах единичного, средне- и мелкосерийного производства при числе основных производственных станков более 50 единиц, а в цехах крупносерийного и массового производства - при числе этих станков более 200. В противном случае создают общую кладовую инструментов и приспособлений.
При определении числа кладовщиков исходят из того, что один кладовщик обслуживает следующее число производственных станков механического цеха: в единичном и мелкосерийном производстве - 35 - 40, в среднесерийном - 55 – 65, в крупносерийном - 75 – 85, в массовом - 95 – 105. Аналогичные нормы установлены для определения числа кладовщиков кладовых приспособлений сборочного цеха. Один кладовщик обслуживает следующее число производственных рабочих сборочного цеха: в единичном и мелкосерийном производстве - 47 - 53, в среднесерийном - 53 - 60, в крупносерийном - 67 – 73, в массовом - 73 – 80. В обязанности кладовщиков кроме получения, выдачи и хранения приспособлений входит также комплектация оснастки в соответствии с технологическим процессом. Оснастку и техническую документацию доставляют к станкам, рабочим местам и диспетчерским пунктам механизированных участков с помощью электротележек и других средств малой механизации.
29
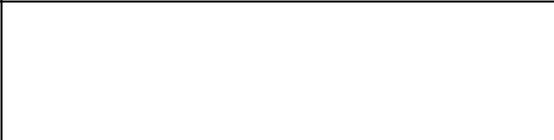
При проектировании участка УСП или УСПО необходимо знать число сборно-разборных приспособлений, собираемых на участке в течение года:
ПР = ОП ∙
где Nоп – число операций, выполняемых в цехе за год с использованием универсальной оснастки (обычно операции, выполняемые на станках сверлильно-расточной группы); m – среднее число запусков заготовок в год.
Один слесарь собирает за год до 1000 компоновок УСП или УСПО. При обслуживании участка одним слесарем его площадь должна быть не менее 20 кв. м, при обслуживании двумя и более слесарями площадь определяется из расчета 12 – 20 кв. м площади на одного слесаря. Размещают участок УСП или УСПО обычно рядом со складом (кладовой) приспособлений и оборудуют стеллажами для хранения элементов оснастки, а также рабочими столами для сборки приспособлений по числу слесарей.
1.7 Построение накопительной системы на производственных участках.
Накопительная система (НС) предназначена для размещения в ней задела полуфабрикатов с целью обеспечения загрузки основного оборудования.
Вместимость НК определяется колебаниями продолжительности выполнения операций технологического процесса, вероятность отказов элементов производственной системы.
В качестве накопительных систем могут использоваться: межоперационная транспортная система; стеллажи межоперационных складов; ложки и магазины; тактовые и поворотные столы; бункеры и накопительные ячейки и др.
Эффективность НС зависит не только от их вместимости, но и от их структурной схемы и надежности работы.
Структурные схемы возможны двух типов: транзитная и тупиковая. Накопители функционируют и при исправном состоянии производственной системы. Остановка же накопителя приводит к остановке работы всех последующих звеньев производственной системы, например, участков автоматической линии.
Накопительные системы транзитного типа применяют в основном при изготовлении деталей типа тел вращения. В линиях изготовления сложных деталей (напр., корпусных), а также при использовании спутников и паллет используют НС тупикового типа.
Классификация НС
НС
|
навалом |
|
в ориентированном пространстве |
|||
способ ориентирования |
|
способ размещения |
||||
контактный |
бесконтактный |
кассетный |
поддоны |
спутники |
||
|
с активным |
электро- |
пневмати |
устройства приема изделий |
||
вибрационный |
|
|
|
|||
вращением |
магнитные |
ческие |
тиберные |
дисковые |
координатн |
|
|
|
|
|
ые столы |
||
|
|
|
|
|
|
30