
ТСС
.pdf
Пример схемы планировки автоматизированного склада тупикового типа показан на рис. 12:
Рис.12. Пример схемы планировки автоматизированного склада тупикового типа.
Обозначения к рисунку 12:
1.- заготовки, полуфабрикаты;
2.- участок временного хранения;
3.- конвейер приема поддонов;
4.- кран-штабеллер;
5.- участок комплектования;
6.- площадка временного хранения;
7.- контора;
8.- цеховой конвейер;
9.- стол участка комплектования;
10.- конвейер-накопитель;
11.- конвейер;
12.- кран-балка;
13.- передаточные устройства;
14,15,16 - участки распределительного конвейера.
«З» Заготовки (1) поступают на участок ВХ (2) или непосредственно на конвейер приема поддонов (3), где загружаются в тару, и далее на один из участков 14, 15 и 16 распределительного конвейера. После поворота поддон с заготовками попадает на одно из передаточных устройств 13 в зоне обслуживания каждого штабеллера, а затем штабеллером 4 перемещается в ячейку склада.
Для комплектования партии запуска поддон с заготовками доставляется штабеллером 4 к устройству передачи 13, а далее с помощью конвейера 10, 11 на участок 5 комплектования. На столе 9 участка 5 операторы склада формируют в поддоне производственную партию. Поддон с оставшимися заготовками возвращается в ячейку склада. Поддон с партией
11
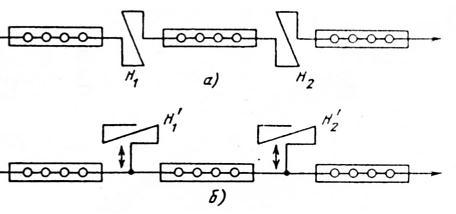
заготовок передают на площадку 6 временного хранения для отправки на участки механической обработки.
Загрузку и выгрузку поддонов осуществляют напольными погрузчиками или подвесной кран-балкой 12. Поддоны с заготовками, не требующими комплектования, попадают на выходной конвейер-накопитель и далее на площадки ВХ отправляемых грузов. Отсюда заготовки цеховым конвейером 8 передают на участки и линии обработки.
Циклы работы крана-штабеллера:
одноходовой цикл (перемещение к заданной ячейке, загрузка или выгрузка; возврат к устройству передачи поддонов);
двухходовой цикл (подача поддона на штабеллер, перемещение к свободной ячейке, выгрузка поддона, перемещение к другой ячейке, захват поддона; перемещение в исходное положение, укладка поддона в передающее устройство).
1.2.7.Накопительные подсистемы на производственных участках
Для уменьшения потерь производительности из-за неритмичности работы и отказов отдельных элементов технологических систем на производственных участках предусматривают накопители. Эффективность накопительных систем зависит от их структурной схемы, вместимости и надежности работы.
Возможны две структурные схемы накопителей (рис. 13): транзитная и тупиковая. Через накопители транзитной схемы проходит весь поток заготовок. Однако при остановке накопителя прекращается работа двух смежных участков. Тупиковые накопители включаются в действие только при останове смежного участка производственной системы, поэтому надежность этого типа накопителей выше.
Рис.13. Структурные схемы накопительных систем:
а) транзитного типа; б) тупикового типа.
Транзитные типы накопителей применяют для простых деталей, например типа тел вращения. В линиях изготовления корпусных деталей, а также при использовании спутников и кассет для транспортирования деталей используют накопители тупикового типа.
В качестве накопителей могут использоваться различные конструкции: межоперационные транспортные системы, стеллажи, лотки, магазины, тактовые или поворотные столы, бункеры, накопительные ячейки и т.п.
Полуфабрикаты могут размещаться в накопителях либо навалом, либо в ориентированном виде. В последнем случае полуфабрикаты размещают в таре-кассетах, поддонах или спутниках. Автоматизированный накопитель деталей и заготовок в таре показан на рис. 14.
12

Рис.14. Автоматизированный накопитель деталей и заготовок в таре.
Для ориентирования изделий, поступающих навалом, используются бункеры-накопители. Одна из таких конструкций накопителя показана на рис. 15. От электродвигателя 1 через редуктор 8, кривошип 7 и шатун 6 возвратно-поступательное движение передается плоскому шиберу 5. Шибер воздействует на кольца 4 в бункере 3 и направляет их в щель, образованную шибером 5 и стенкой 2. По наклонному дну 9 кольца поступают к выходному окну 10, где стоит подпружиненная собачка 12, которая позволяет изделию поштучно выкатываться в штанговый подъемник.
13
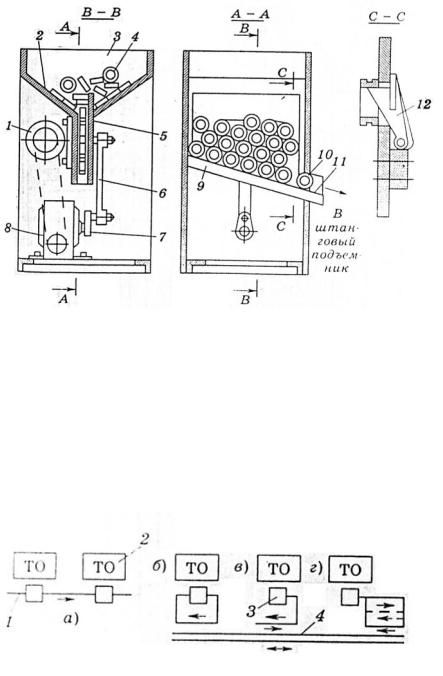
Рис.15. Бункер-накопитель.
Структурные схемы функционирования накопителей зависят от способа транспортирования изделий, их числа и номенклатуры. Типовые схемы функционирования накопителей приведены на рис. 16. Схема на рис.16 а) (транзитная схема) используется при условии, что вместимость участка 1 конвейера между технологическим оборудованием достаточна для обеспечения необходимого задела. При недостаточной вместимости используют дополнительные встроенные накопители кольцевого (рис.16 б)), тупикового (рис.16 в)) и комбинированного (рис.16 г)) типов. В последней схеме происходит циркуляция изделий в накопителе и возможна выдача любого изделия на технологическое оборудование.
Рис.16. Типовые схемы функционирования накопителей: а) транзитного типа; б) кольцевого типа; в) тупикового типа; г) комбинированного типа.
Варианты планировочных решений размещения накопителя в виде складской цеховой системы зависят от компоновки размещения технологического оборудования. На рис. 17 показаны варианты планировочных решений. Т-образное планировочное решение характеризуется наличием транспортных систем доставки изделий из складской системынакопителя 3 к технологическому оборудованию 1, а также загрузочных устройств 4. Вариант кольцевого решения требует кольцевого размещения не только склада 3, но и транспортной системы 2. Линейная планировка обеспечивается транспортной системой 3, при остановке по техническим причинам любого технологического оборудования 1, 2 накопительная складская система 4 с помощью транспортного робота загружает работающее оборудование полуфабрикатами. Цифрой 5 обозначена позиция линии, где контролируется выходящая с линии продукция.
14

Рис.17. Варианты планировочных решений складской системы: а) Т- образная; б) кольцевая; г) линейная
В производственном процессе накопители могут выполнять следующие функции: -принимать изделия с предыдущего основного оборудования и выдавать их на
последующее – работа на накопление; -выдавать полуфабрикаты на последующее основное оборудование и не принимать с
предыдущего – работа на расход; -принимать изделия с предыдущего оборудования и посылать их на последующее,
т.е. работать напрямую, причем темп приема и выдачи может быть разный при смене производительности технологического оборудования.
Накопители большой вместимости располагают между механообрабатывающим и термическим оборудованием, поскольку механообрабатывающие участки работают чаще в две смены, а термические – непрерывно.
Впоточном производстве накопители практически не устанавливают между основным оборудованием, их чаще всего размещают в начале и конце поточной линии, а также между участками линии.
Внепоточном производстве накопители обычно размещают после группы основного оборудования или около каждого оборудования, т.к. из-за широкой номенклатуры изготавливаемых изделий постоянно изменяется продолжительность выполнения технологических операций, а это приводит к необходимости наличия накопителей для обеспечения равномерности загрузки основного оборудования.
15

1.3 Расчет основных параметров складов.
Склады проектируют в одну стадию (рабочий проект) или в две стадии (проект и рабочая документация).
Рабочий проект выполняют обычно в два этапа. На первом этапе определяют техническую возможность и экономическую целесообразность основных технологических, объемнопланировочных и конструктивных решений по складу и составляют смету. На втором этапе разрабатывают рабочие (монтажные) чертежи склада.
На первом этапе выполняют:
-выбор возможных конкурентно-способных вариантов склада по способам складирования, параметрам складского здания, компоновкам технологических участков и склада в целом, типу и основным характеристикам складской тары, стеллажного и штабелирующего оборудования, технологии, механизации, организации и автоматизации работ;
-технологические расчеты по складу (емкость, параметры грузовых потоков, приемноотправных экспедиций, внутрискладского транспорта, производительности и потребного количества подъемно-транспортного оборудования и т.д.);
-выбор технологии и организации складских работ, порядок переработки грузов и документов;
-расчёт технико-технологических показателей и сравнение их с соответствующими номативными показателями.
После утверждения принятых технических решений по первому этапу разрабатывают:
-рабочие (монтажные) чертежи расположения оборудования (планы, разрезы, виды);
-ведомости покупного оборудования;
-технологические карты, определяющие содержание операций на складе, их трудоемкость, способы и последовательность выполнения;
-должностные инструкции складских работников.
1.3.1. Детальный расчет складов.
Расчет параметров складской системы начинают с выбора нормы запаса хранения (таблица
2).
Зная норму запаса хранения в днях, определяют запас хранения соответствующей группы грузов (т) по формуле:
∙= 365
где - годовое поступление груза соответствующего наименования, т/год;
- норма запаса хранения, дни.
При выборе основных параметров складской системы необходимо учитывать
характеристики грузов:
-габаритные размеры;
-геометрическую форму;
16
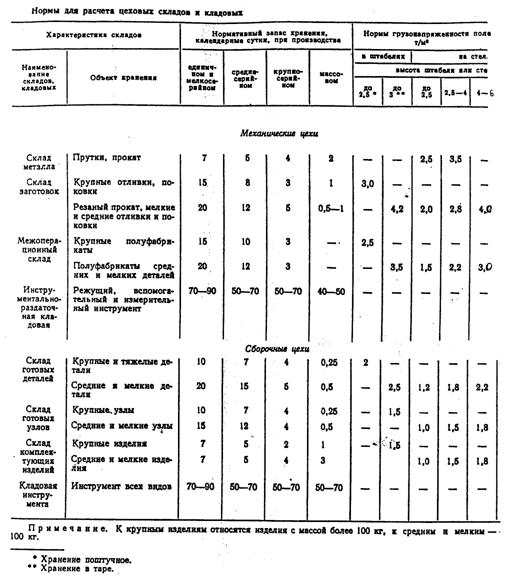
-массу;
подверженность повреждениям;
-необходимость пространственной ориентации при хранении и перемещении;
-строительные характеристики здания.
Перечисленные характеристики влияют на тип, количество и параметры складского оборудования. На выбор последнего влияют также выбранный технологический процесс переработки грузов, количество перерабатываемого груза, периодичность его поступления и отправления.
Таблица 2. Нормы для расчёта цеховых складов и кладовых, определения числа кладовщиков.
Далее осуществляют выбор типа и параметров производственной тары, при этом возможны следующие варианты:
-тип и параметры тары известны, т.к. грузы поступают в таре;
17
-тип и параметры тары неизвестны, но есть рекомендации по использованию унифицированной тары, например, накопителей;
-тип и параметры тары неизвестны, однако ограничений выбора нет.
После выбор типа и параметров тары рассчитывают необходимое число единиц тары для размещения необходимого запаса по каждой группе заготовок:
= |
|
, где - средняя вместимость тары. |
|
|
|
⁄ |
|
|
|||
|
|
|
|
|
|
|
|
|
|
|
|
Среднюю вместимость тары определяют по максимальной грузоподъемности тары |
, с |
||||
|
|
|
|
|
|
учетом коэффициента использования ее по грузоподъемности по формуле: |
|
||||
|
|
|
|
|
|
|
|
|
= |
∙ |
|
|
|
|
|
|
|
Число стеллажей рассчитывают следующим образом: |
|
||||
|
|
|
|
|
|
|
|
|
|
|
|
|
|
|
|
|
|
|
|
= ∑ ⁄ |
|
||
|
|
|
|
Я |
|
|
|
|
|
|
=1
где m - число групп грузов, хранящихся на складе; Я - число ярусов стеллажа.
Необходимо установить число ярусов по высоте здания. Высоту яруса стеллажа можно определить, зная высоту и толщину тары (для плоского поддона) или сумму высоты ножек поддона и толщины его настила (для стоечных и ящичных поддонов), собственную высоту груза C , зазор e между верхом нижнего поддона (для стоечных и ящичных поддонов) и лежащего на нем груза (для плоских поддонов) до низа опорной поверхности следующей по высоте тары с грузом, по формуле: CЯ = + C + e.
Для бесполочных стеллажей принимают e = 60 - 100 мм, для каркасных e = 110 - 220 мм (в зависимости от толщины полки), а при штабельном хранении e = 0.
Высота складского помещения в зоне хранения грузов HX определяется стандартными строительными размерами здания.
Число ярусов определяют по формуле:
Я = ε {(HX - hH – hB) / CЯ} + 1
где hH -высота нижнего яруса над полом; hB расстояние по высоте от низа строительных конструкций покрытия здания до опорной поверхности верхнего яруса стеллажей или штабеля (для стеллажных кранов-штабелеров hB =1,5 м; для мостовых кранов-штабелеров hB
= 1,8 ÷4,1 м).
При использовании мостовых кранов-штабелеров, напольных штабелеров и погрузчиков принимают высоту уровня первого яруса над полом hH =0, т.к. нижняя тара устанавливается на пол.
При применении стеллажных кранов-штабелеров высоту hH рассчитывают так:
hH = dH + λ + e0
где dH - минимальное приближение грузозахвата крана-штабелера к уровню опорной
поверхности стеллажей; λ - зазор между низом тары и верхней поверхностью грузозахвата; e0 - высота ножек тары.
Число рядов в зоне хранения:
y= Zст / Z
18
где Z – число единиц тары, размещаемой в одной секции данного типа стеллажа
Длина стеллажей, занятых грузами в зоне хранения, рассчитывают по следующим формулам:
-для без полочных стеллажей: = = ( + 2 + )
-для каркасных стеллажей: = ( ⁄ Д) (Д ∙ + (Д + 1) ∙ + )
где A - длина ячейки стеллажа; a - длина грузовой единицы (размер вдоль зоны хранения); X - толщина стоек стеллажей; PД - количество тары по длине ячейки каркасного стеллажа (PД = 2÷3 при установке тары длинной стороной вдоль стеллажей и PД = 3 ÷ 4 при установки их длинной стороной вглубь стеллажа); λ - зазоры между грузовыми единицами или между грузовой единицей и стойкой стеллажа.
По числу стеллажей устанавливают полезную площадь склада для хранения грузов SСК путем планировки выбранного количества стеллажей с учетом используемого транспортного оборудования и размещения приемно-передаточных столов и рабочих мест.
1.3.2. Укрупненный расчет параметров складов
При укрупненном проектировании площадь складов определяют на основании нормативных данных о запасах хранения грузов (заготовок, полуфабрикатов и готовых деталей до сборки), используя технико-экономические показатели аналогичных складов:
= (Σ ∙ )/(Д ∙ ∙ П)
где m∑ - масса грузов, проходящая через цех в течение года, т; t - нормативный запас хранения грузов на складе, календарные дни; Д - число календарных дней в году; q - средняя грузонапряженность площади склада, т/кв.м.
= ТАБЛ ∙
где qтабл - типовая норма из таблиц; K - коэффициент, зависящий от типа производства: для единичного и мелкосерийного K = 0,8; для среднесерийного - K = 1; для крупносерийного - K = 1,1; для массового - K = 1,2.
KП - коэффициент использования площади, который учитывает наличие переходов для транспортных средств и площадок приема, комплектации и выдачи грузов: для напольного конвейера KП = 0,25 ÷ 0,3; для стеллажного и мостового крана-штабелера KП =
0,35 ÷ 0,4,
Типовые нормы для проектирования цеховых складов представлены в таблице 3.
19

Таблица 3. Нормы для расчёта площади кладовых цеха.
1.3.3. Расчет общей площади СС
Общая площадь склада дополнительно включает площадь временного хранения принимаемых и отпускаемых грузов, площадь подъездных путей, проходов, проездов и служебных помещений.
Площадь участков временного хранения грузов SВХ определяют по формуле:
= ( Г ∙ ∙ )/(253 ∙ )
где mГ - масса поступающих за год (отправляемых) грузов, т; КН - коэффициент неравномерности поступления (КН = 1,3) и отпуска (КН = 1,5) грузов; t - время нахождения груза на площадке (t = 2 – 3 дня); - грузонапряженность приемной и отпускной площадок, принимаемая равной половине средней грузонапряженности склада q:
= ( Я ∙ ∙ )/
где Z - число поддонов, размещаемых в одной ячейке; Zя - число рабочих ярусов по высоте; fC - площадь, занимаемая одной секцией стеллажа, кв.м.
1.3.4.Расчет числа транспортных машин
Количество транспортных машин периодического действия для выполнения операций перемещения грузов на складе определяют по формуле:
= Σ/(Ф ∙ )
где tC∑ - суммарное время работы транспортного средства для перемещения годового объема груза,т; Ф0 - эффективный годовой фонд времени работы штабелера или другой транспортной машины; КН - коэффициент использования транспортного оборудования, принимаемый равным 0,8.
Суммарное время транспортных операций на перемещение годового объема груза транспортом данного вида:
20