

Распиливание (рис. 9.1.ж) является разновидностью процесса резания.
В предприятиях общественного питания и пищевой промышленности находят применение все перечисленные способы измельчения. Для пластичных продуктов наиболее подходящим является способ измельчения резанием. Большинство пищевых продуктов пластичны, поэтому резанию уделим наибольшее внимание и время.
На процесс измельчения влияют следующие факторы: структура и физико-механические свойства обрабатываемого продукта; конструктивные и геометрические параметры режущего инструмента; техническое исполнение и состояние измельчающего оборудования.
Эффективность измельчения в значительной степени зависит от геометрии режущих инструментов и режимов обработки продукта.
Машины, предназначенные для измельчения продукта, можно подразделить на три основные группы: для дробления пищевых продуктов (размолочные механизмы и машины); для измельчения вареных овощей, мяса и др. (протирочные машины и механизмы), для резания продукта.
Общие требования, которым должна отвечать любая измельчительная машина, следующие: а) возможность изменения степени измельчения;
б) прочность и изностойкость рабочих органов, не допускающая попадание частиц инструмента в обрабатываемый продукт;
в) удалению обработанного продукта из рабочей зоны во избежание излишнего измельчения и лишних затрат энергии;
г) возможности замены рабочих органов; д) наличие предохранительных элементов в конструкции машины, исключающих производственный трав-
матизм; е) минимальная масса машины.
9.2. РАЗМОЛОЧНЫЕ МАШИНЫ И МЕХАНИЗМЫ
На предприятиях общественного питания применяются размолочные машины и механизмы, отличающиеся принципом действия и устройством рабочих органов: с конусными рабочими органами МС 12-15, МИП-II-I и импортный механизм Z-105 к английскому приводу MTR; дисковые МИК-60 и механизм МКК 120 к приводу MKN польского производства; вальцовые МС 12-40, МДП-II-I к приводам серии П, и импортный Z-101 к приводу английского производства MTR.
Механизмы с конусным рабочим органом предназначены для измельчения сухарей, специй и других твердых пищевых продуктов.
Механизм МС 12-15 (рис. 9.2) приводится в действие универсальным приводом ПМ-1,1. Механизм состоит из литого алюминиевого цилиндрического корпуса, наверху которого имеется загрузочная воронка, внутри корпуса расположены подвижный и неподвижный конусный жернов и питающий шнек, получающий вращение от приводного валика, на котором так же расположен и вращающийся жернов.
Рис. 9.2. Размолочный механизм МС 12-15: 1 – размолочный механизм; 2 – привод.
Опорами валика служат размещенные в корпусе радиально-упорные роликовые подшипники качения. К корпусу крепится стальной хвостовик, посредством которого механизм подсоединяется к горловине привода. Вращение на валик передается посредством шейки вала, имеющей выфрезерованные лыски, входящие в паз на ведущем валу привода. Шнек и жернов закрепляются на валу фасонной гайкой и воспринимают крутящий мо-
51
мент от вала посредством призматических шпонок. Шнек обеспечивает непрерывную подачу продукта к размолочным поверхностям жерновов, снабженных спиральными треугольными зубьями переменной высоты и образующими рабочий зазор между жерновами. Зазор регулируется осевым продольным перемещением не вращающегося жернова, осуществляемого при помощи регулировочной головки, расположенной на торце механизма. Изменение зазора позволяет увеличить степень измельчения продукта. Минимальный зазор между поверхностями составляет 0,2 мм. Направление вращения регулировочной гайки определяется закрепленными на торце корпуса надписями указателями «Крупно» или «Мелко».
Механизм МИП–II–I приводится в действие универсальным приводом П–II. Устроен аналогично рассмотренному механизму МС 12-15, но имеет некоторые конструктивные особенности, касающиеся подсоединения механизма к приводу.
Механизм Z-105 устроен аналогичным образом механизму МИП-II-I.
Дисковая машина МИК-60 предназначена для размола обжаренных зерен кофе, состоит из прямоугольного корпуса, в котором расположены электродвигатель привода с закрепленным прямо на его валу дисковым вращающимся жерновом. Электродвигатель установлен в корпусе машины на четырех амортизаторах. К верхнему торцу корпуса машины крепится загрузочная воронка, ниже которой расположены не вращающийся жернов с центральным проходным отверстием и механизм регулирования его положения относительно вращающегося жернова. Перемещение жернова происходит в осевом направлении, вертикально, при помощи регулировочной рукоятки, выведенной на боковую образующую корпуса и осуществляющей перемещение посредством винтовой пары, нажимающей на фланец жернова через цилиндрическую тарельчатую пружину, срабатывающую при попадании под зубья жерновов посторонних твердых предметов. При повороте рукоятки получает вращение резьбовая втулка, перемещающая фланец в осевом направлении по направляющим штырям, изменяя при этом зазор между зубьями жерновов. В горловине загрузочного бункера установлен постоянный магнит для улавливания ферромагнитных включений. Разгрузочная трубка снабжена электромагнитным вибратором, служащим для привода в действие вибрационного небольшого транспортера, выполняющего роль разгрузочного лотка. Разгрузка происходит в прижатый планкой зажима пакет, в который ссыпается измельченный кофе.
Механизм МКК-120 к приводу польского производства состоит из корпуса, в котором расположены червячный питающий шнек, получающий вращение от ведущего вала привода MKN. Хвостовик приводного валика опирается на два подшипника скольжения, расположенных в присоединительном хвостовике механизма. Сверху и снизу корпуса размещены два чашеобразных бункера, служащие для загрузки исходного и разгрузки обработанного продукта. Червячный шнек предварительно измельчает продукт, окончательно измельчение осуществляется между жерновами. Регулирование степени помола производится специальной гайкой, расположенной на торце механизма.
Вальцовый механизм МС 12-40 предназначен для дробления ядер орехов и растирания мака. Он выполнен в виде прямоугольного корпуса, внутри которого расположены загрузочный бункер с питающим валиком, ниже которого расположена рабочая камера. В камере имеются два вращающихся гладких ролика, зазор между поверхностями которых регулируется в пределах 0-2,5 мм с помощью двух рукояток, установленных на передней стенке. Вращение от вала привода передается стационарно расположенному валу, затем посредством зубчатой передачи размолочному и питающему валикам. Опорные подшипники скольжения изготовлены из графитопластика и не требуют постоянной смазки. Размолочные валки вращаются в разные стороны с различным числом обротов (170 и 200 об/мин). В нижней части корпуса по касательной к цилиндрической поверхности валков установлены два скребка, очищающих поверхность валков от прилипших частиц продукта. Продукт из бункера в определенном количестве, зависящем от зазора между поверхностью питающего валка и шибером, подается к размолочным валкам. Для крупного помола зазор между валками регулируется в пределах до 1,5 мм, для растирания мака зазор должен быть не более 0,2 мм.
Механизм МДП–II–I имеет конструкцию, аналогичную рассмотренной. Основное отличие – способ крепления к присоединительной горловине привода П – II. Кроме того, механизм имеет меньшие габариты и массу.
Механизм Z-101 имеет аналогичное устройство.
9.3. ПРОТИРОЧНЫЕ МАШИНЫ И МЕХАНИЗМЫ
На предприятиях общественного питания широко используются протирочные машины и механизмы, необходимые для протирания вареных овощей, отварной печени, творога и других продуктов. Находят применение в производстве машина МП–800, механизмы МС 4–7-8-20, МОП-II-I к приводам производства России, MKZ – 120 к универсальному приводу польского производства, Z-103 к универсальному приводу английского производства.
Машина МП-800 состоит из корпуса, в котором расположены рабочая камера, передаточный механизм и привод. Внутри рабочей камеры имеется протирочное сито, перфорированное круглыми отверстиями небольшого диаметра, приводной валик, передающий вращение ротору с протирочными лопастями, закрепленному посредством шпонки и резьбового соединения на валу. Сито сменное, применяется с различным диаметром перфорирующих его поверхность отверстий, в зависимости от обрабатываемого продукта. Лопасти и валик приводятся во вращение от ведомого шкива клиноременной передачи, ведущий шкив которой находится непосредственно на валу реверсивного электродвигателя привода.
52
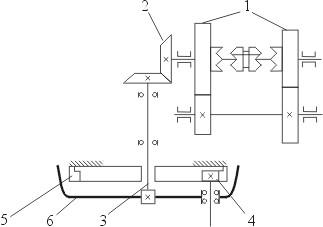
Загрузочный бункер установлен непосредственно над рабочей камерой, на корпусе и крепится к нему двумя откидными болтами с гайками – барашками. На боковой стенке камеры имеется люк, во время работы машины закрываемый крышкой, служащий для выброса отходов продукта, остающихся после протирки. Крышка поворотная, расположена на оси, прикрепленной к корпусу, запирается эксцентриковым зажимом. При выбросе отходов крышку открывают, производят реверсирование двигателя, ротор начинает вращаться в противоположном направлении и происходит выброс отходов под действием центробежных сил.
Регулирование зазора между неподвижной решеткой и вращающимся ротором производится при помощи промежуточного стакана, который одевается на вал и фиксируется винтом. На этом же стакане, укрепленном на валу посредством фасонной гайки, на двух шипах укреплен сбрасыватель, служащий для удаления обработанного продукта в лоток выгрузки,
Угол наклона лопастей ротора выбран таким образом, что при вращении в рабочем направлении (по часовой стрелке) продукт прижимается к протирочному ситу, а при вращении в противоположном – отходы перемещаются вверх по наклонной поверхности лопасти, поднимаются вертикально по камере и выбрасываются в открытый люк.
Ротор для протирания косточковых плодов состоит из двух частей, упруго соединенных в одно целое. Нижняя часть имеет ступицу с упруго присоединенными обрезиненными пальцами, служащими для протирания продуктов, верхняя часть представляет собою лопасти выбрасывателя отходов, которые могут проворачиваться относительно ступицы.
Внизу, на корпусе через шарнирное устройство крепится подставка для размещения емкости под обработанный продукт, устанавливаемая в двух положениях в зависимости от высоты емкости.
При вращении ротора по часовой стрелке лопасти выбрасывателя отводятся от упругих пальцев и не мешают обработке. При вращении против стрелки лопасти выбрасывателя проворачиваются до тех пор, пока не совместятся с упругими пальцами и не начнут выбрасывать отходы протирки в открытый люк.
Многоцелевой механизм МС 4-7-8-20 применяется в основном для взбивания и перемешивания продуктов, но может и настроен для протирания вареных продуктов. Механизм состоит из корпуса, в котором размещены редуктор конический, коробка скоростей с двумя цилиндрическими парами зубчатых колес, механизм управления коробкой скоростей, сменные бачки и приспособления, рабочие органы. К корпусу коробки скоростей прифланцован хвостовик, посредством которого происходит крепление механизма к горловине привода. В расточку хвостовика и корпуса вставлен вал, опирающийся на подшипники скольжения и имеющий две закрепленных на нем шестерни, получающих вращение через шпонки на валу. Шестерни входят в зацепление с колесами на ведомом валу, расположенному выше в корпусе механизма. Колеса находятся на валу свободно, без шпоночного соединения, имеют на торцах кулачки, которыми могут зацепляться с промежуточной втулкой, управляемой рукояткой с вилкой, перемещающей в продольном направлении втулку. Втулка соединена с валом при помощи шпоночного соединения, скользит по валу и соединяет то одно колесо с валом для передачи крутящего момента, то другое, по желанию оператора. На концевой шейке этого вала находится, укрепленная с помощью шпоночного соединения коническая зубчатая шестерня, входящая в зацепление с коническим колесом, расположенным на вертикальном валу привода планетарной головки вращения рабочего инструмента в виде лопастей, перемешивающих и перемещающих по плоскости сита продукт. Вращение от вертикального вала передается корпусу планетарной головки, имеющей прилив с расточкой, в которой расположены два радиальных шарикоподшипника, служащих опорами рабочего валика с имеющейся на верхней его шейке цилиндрической шестерней, входящей в зацепление с неподвижным зубчатым колесом внутреннего зацепления.
Рис. 9.3. Многоцелевой механизм МС4-7-8-20:
1 – коробка скоростей; 2 – коническая передача; 3 – вертикальный вал; 4 – сателлит; 5 – колесо «солнце»; 6 – крышка водило
53

Шестерня обкатывается по колесу и получает вращение вокруг своей оси и за счет обкатывания – вращение вокруг главной, центральной оси. Это же движение совершает рабочий инструмент, соединенный с валиком посредством реечного зубчатого зацепления выполненного на половине выфрезерованной шейки валика и рабочего инструмента, соединение поддерживается при помощи накидной втулки.
Снизу к корпусу прикреплен кронштейн, на который устанавливают сменные бачки или обечайку для обрабатываемых продуктов. Для протирания продуктов к редуктору подсоединяют протирочную лопасть и перфорированную обечайку, внутри которой и происходит обработка. Обечайка выполнена из нержавеющей стали. В обечайку вставлено сито с отверстиями диаметром 3 мм. Для протирания супов в обечайку дополнительно вставляют вкладыш, а к валу прикрепляют волосяную протирочную щетку. Сверху к обечайке приварены ушки, которые, зацепляясь за уголок на вкладыше, предохраняют его от проворачивания.
При протирании и перемешивании вареного картофеля рукоятка переключателя скоростей устанавливается в положение «Медленно», при протирании супа – в положение «Быстро». В первом положении рукоятки протирочные лопасти вращаются вокруг главной оси с частотой 0,76 с-1 (46 об/мин), при втором положении рукоятки вращение происходит с частотой 1,4 с-1 (85 об/мин); вокруг собственной оси вращение происходит с частотой 4,7 с-1 (282 об/мин) и 5,58 с-1 (335 об/мин) соответственно.
Механизм МОП-II-I cостоит из корпуса, в котором расположены конический мультипликатор, сменное приспособление для обработки продукта, загрузочное устройство. Мультипликатор состоит из алюминиевого корпуса, прифланцованного хвостовика, пары конических зубчатых колес, валов и крепежных деталей.
Рис. 9.4. Овощерезательно-протирочный механизм МОПII-1.
Горизонтальный вал, являющийся приводным, получает вращение от вала универсального привода, опирается на два радиально-упорных роликоподшипника, на его концевой шейке расположено коническое зубчатое колесо, входящее в зацепление с конической шестерней на концевой шейке вертикального вала. На другой концевой шейке этого вала находится шип и крепежная шейка, на которую надевается ротор с протирочными лопастями, аналогичным по конструкции ротору машины МП-800, рассмотренной выше. Устанавливаемая сверху загрузочная воронка крепится двумя откидными винтами. При выполнении протирочных операций устанавливается протирочное сито с отверстиями диаметром 2 или 5 мм. Лопастной ротор жесткий, служит для протирания продуктов, имеет две лопасти, обеспечивающие прижатие продукта к поверхности сита. Выбрасывается обработанный продукт прикрепленным к валу сбрасывателем, устанавливаемым ниже поверхности сита.
Механизм MKZ-20 польского производства предназначен для протирания супов и вареных овощей, приготовления картофельного пюре. Механизм состоит из корпуса, в котором расположен конический редуктор и прикрепленный снизу бачок для обработки продуктов. На дне этого бачка закреплено сито; являющиеся сменным рабочим инструментом, диаметр отверстий в них может быть 3 или 6 мм. На вертикальном рабочем валу над ситом укреплены подпружиненные протирочные лопасти. Загрузка бачка производится примерно до половины объема.
Механизм Z-103 английского производства имеет аналогичную конструкцию.
9.4. ОБОРУДОВАНИЕ ДЛЯ ПРИГОТОВЛЕНИЯ ПЮРЕОБРАЗНЫХ ПРОДУКТОВ
Для получения пюреобразных продуктов на предприятиях общественного питания применяются разнообразные по конструкции машины, которые можно классифицировать по устройству, как:
1)машины с высокочастотным перепадом нормальных знакопеременных напряжений растяжения-сжатия, возникающих в продукте, в сочетании с касательными напряжениями среза и сдвига;
2)машины, работающие по принципу протирочных – продукт разрезается кромками отверстий сита и продавливается через них;
3)машины, в которых продукт раздавливается вращающейся лопастью и перемешивается.
54
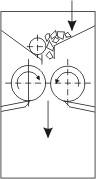
Машины первой группы предназначены для тонкого, диетического измельчения продуктов в виде пищевых паст из творога, вареных овощей, круп, мяса, рыбы.
Машины второй группы предназначены для приготовления пюре из вареных продуктов.
Машины третьей группы предназначены для приготовления картофельного пюре непосредственно в котле. К машинам первой группы относится МИВП, ко второй группе – все протирочные машины, рассмотрен-
ные ранее, к третьей группе - машины МКП-60 и МКП-250.
Машина МИВП предназначена для тонкого измельчения вареных продуктов: мяса, рыбы, овощей, круп, печени и творога с величиною частиц не более 0,5 мм. Продукт измельчается за счет высокочастотных колебаний, возникающих при изменении зазора между зубьями ротора и статора при быстром вращении ротора, при этом положительное влияние на измельчение оказывает наличие истирания продукта их ребристой поверхностью. Машина состоит из корпуса, в котором размещены статор, имеющий внутреннюю коническую поверхность с зубьями треугольного профиля, расположенными по образующим конуса, и конический ротор, закрепленный прямо на валу электродвигателя, упруго подвешенному к корпусу машины. Положение статора по высоте определяет величину зазора между зубьями ротора и статора, определяющего размер обработанных частиц. Статор легко вставляется, фиксируется и вынимается из корпуса. Положение по высоте определяется ступенчатым кольцом, находящимся в расточке корпуса под фланцем статора. Кольцо расположено на трех опорных штифтах и, вследствие ступенчатой поверхности, может устанавливаться на различной высоте, изменяя ступени помола продукта – 0,2; 0,4 и 0,6 мм. На роторе имеются три участка с переменным профилем канавок: для грубого помола; среднего и тонкого измельчения продукта. Каждая часть отличается одна от другой размером и количеством полуцилиндрических канавок. В первой части этих канавок 56, во второй – 80, в третьей – 120. Канавки расположены под острым углом к канавкам статора. Измельчение происходит при быстром изменении зазора между зубьями статора и ротора, приводящему к знакопеременным напряжениям растяжения и сжатия, возникающим в продукте. Измельченный продукт поступает через разгрузочное отверстие машины, прикрываемое специальным лотком, в приемную тару.
Протертые продукты должны составлять однородную массу пастообразного вещества; наличие крупинок непротертого продукта не допускается. Степень измельчения для 80 % обработанных частиц должна быть не более 0,25 мм по наибольшему размеру, остальные 20 % должны иметь наибольший размер не более 0,5 мм.
Машина МКП-60 предназначена для приготовления картофельного пюре непосредственно в пищеварочных котлах. В комплект машины входит пищеварочный котел КПЭ-60 и подкатный привод, закрепленный на маневренной тележке с тремя колесами. На тележке установлено устройство, фиксирующее ее возле котла. На тележке имеется так же специальная стойка с приводом ПМ 1,1, от которого происходит вращение рабочего инструмента, помещаемого в котел для перемешивания пюре. Инструмент выполнен в виде сварной лопасти, состоящей из ряда горизонтально расположенных планок, соединенных между собой вертикальной рамкой, имеющей форму внутренней конфигурации котла. Инструмент подсоединяется к вертикальному приводному валу конического редуктора, получающему вращение от привода, посредством быстро разъемной накидной муфты. Поперечные пластины лопасти заточены и согнуты под определенным углом.
После того, как картофель будет сварен до готовности, а отвар слит, тележку с приводом вручную подкатывают к котлу, привод с помощью имеющегося маховика и винтовой передачи поднимают вверх в крайнее положение, устанавливают лопасть, опускают ее в котел, закрывают крышкой котел и включают привод. Через 2,5 мин работы вливают все полагающиеся по рецепту компоненты и продолжают перемешивать еще 2,5 мин. Общее время работы привода – 5 мин. После окончания работы снимают с котла крышку, лопасть, нажимом на педаль отсоединяют тележку от упора котла и откатывают ее в сторону.
Машина МКП-250 отличается от МКП-60 наличием планетарного вращения лопасти. Для приготовления и взбивания 200 кг вареного картофеля требуется 15 мин. В остальном конструктивное устройство и эксплуатация аналогичны машине МКП-60.
9.5.ЭКСПЛУАТАЦИЯ ИЗМЕЛЬЧИТЕЛЬНЫХ МАШИН И МЕХАНИЗМОВ
Перед началом работы сменных механизмов проверяют правильность их сборки и настройки, затем надежность закрепления их в гнезде привода, опробуют работу машины или привода механизма на холостом ходу, после чего загружают подготовленный к измельчению продукт и начинают обработку.
В механизме МДП-II-I для получения крупного помола зазор между поверхностями валков должен составлять 1,5 мм, при растирании мака – 0,25 мм. Изменение зазора происходит при вращении управляющей рукоятки вокруг собственной оси. Рабочие валки сменные.
Рис. 9.5. Механизм МДП-II-1.
Для крупного помола ядер орехов (частицы размером 6-12 мм) устанавливают рифленый валок с 15 крупными канавками, для среднего помола (4-8 мм) – валок с 26 средними канавками, и для мелкого помола (менее 4 мм) – валок с 40 мелкими канавками, при этом продукт предварительно измельчается на валках крупного помола. Для растирания орехов или мака используют гладкие валки, для очистки их поверхности от налипающих крошек продукта имеются в машине скребок.
Вмашине МИК-60 для регулирования зазора между жерновами открывают откидную крышку, снимают загрузочный бункер, отпустить стопорный винт, фиксирующий кольцо на резьбовой втулке. Поворот кольца осуществляют при помощи специальной рукоятки, устанавливая необходимую степень помола. После этого, загружают в бункер зерна кофе, а на разгрузочную трубу надевают пакет, прижимают его к трубе и включают машину. Измельченный кофе лопастями выбрасывается в разгрузочную трубу и затем в вибрирующий лоток.
Вмеханизме МКК-120 для регулирования степени помола необходимо отвернуть звездообразную головку фиксирующего винта, поворотом гайки регулятора установить необходимый зазор между рабочими поверхностями мелющих органов.
Вмашине МП-800 при прекращении выхода обработанного продукта, останавливают работу машины и открывают крышку выходного лотка для полного удаления вручную протертого продукта. При протирании продуктов с большим количеством отходов, например, косточковых плодов, необходимо чаще удалять отходы из рабочей камеры. Для этого кнопкой «Стоп» останавливают машину, кнопкой «Отходы» реверсируют вращение двигателя, открывают поворотом эксцентриковой рукоятки боковой люк для выгрузки отходов, удерживают ее в таком положении до окончания выгрузки отходов. Закрывают крышку, останавливают двигатель, включают его в работу нажатием кнопки «Протирание» и продолжают обработку продукта.
Машину МИВП по окончании работы отключают от сети, снимают статор, регулирующее кольцо, лоток и ротор, проводят их санитарную обработку. Корпус машины обмывают водой, подаваемой шлангом от магистрали горячей воды, и затем протирают мягкой сухой тканью.
Механизм MKZ-20 закрепляют на универсальном приводе, подвешивают к его корпусу бачок с ситом, на вертикальный вал надевают протирочную лопасть, под бачок подставляют тару для обработанного продукта. Загружают на половину по емкости бачок и включают привод, начиная обработку продукта. Санитарная обработка производится так, как описано раньше, для других аналогичных механизмов.
При эксплуатации машин МКП-60 и МКП-250 необходимо знание устройства и правил эксплуатации котла КПЭ-60 или КПЭ-250. Нельзя включать котел при нарушении заземления, появления пара из пароводяной рубашки, неисправном двойном предохранительном клапане.
9.6. ОПРЕДЕЛЕНИЕ НЕКОТОРЫХ ОСНОВНЫХ ПАРАМЕТРОВ РАБОТЫ ОБОРУДОВАНИЯ
9.6.1. ОБОСНОВАНИЕ КОНСТРУКЦИИ И РЕЖИМА РАБОТЫ
Степень измельчения определяется отношением средних размеров куска продукта до измельчения к размерам после измельчения и определяется выражением
I = D/d ,
где I - степень измельчения;
D- размер частицы до измельчения, м;
d - размер частицы после измельчения, м.
Режим работы размолочных механизмов с горизонтальной осью вращения рабочих инструментов принимают таким, чтобы частицы продукта, поступившие на вращающийся жернов, не проходили далее под действием силы тяжести от собственного веса, а отбрасывались нормальной составляющей центробежной силы на неподвижный жернов. Под действием касательной составляющей центробежной силы частицы должны продвигаться к разгрузочному отверстию. Это возможно при выполнении условия
Ct > Gt +Cnf ,
где Ct - касательная составляющая центробежной силы, Н; Gt - касательная составляющая силы тяжести, Н;
Cn - нормальная составляющая центробежной силы, Н; f - коэффициент трения.
Подставив значение центробежной силы при среднем значении радиуса вращения частицы и принимая во внимание угловую скорость вращения продукта (необходимо учитывать проскальзывание продукта), получим угловую скорость вращения жерновов
n > 30 / (1-Kпр )[rср (1-f tg δ )]0,5,
где n – угловая скорость вращения жернова, об/мин;
56
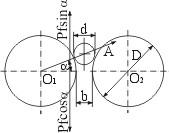
Кпр – коэффициент проскальзывания продукта;
rср – среднее значение радиуса нахождения частицы, м; δ - угол конусности вращающегося жернова.
Валки являются наиболее ответственным органом дробильных механизмов, поэтому их расчету уделим повышенное внимание. Они должны иметь форму цилиндра при строгой соосности опорных цапф. Валки следует балансировать и статически и динамически перед их сборкой. Валки изготавливают из чугуна, его шероховатая поверхность легко захватывает обрабатываемые частицы при попадании их в зазор между поверхностями валков. Рифление цилиндрических валков располагается по винтовой линии, так чтобы распределить нагрузку от давления обрабатываемого продукта во времени, не толчкообразно. По размерам и профилю зубья рифлей выполняют такими, чтобы продукт не западал между ними. Частицы продукта должны захватываться валками, для этого необходимо выполнение условия, как следует из рисунка 9.2.
Рис. 9.2. Расчетная схема дробильного механизма
Это условие можно выразить как
2P sinα < 2Pf cosα ,
Отсюда следует
f > sinα / cosα =tgα ,
Так как
f = tgα , то tgα < tg ρ ,
где ρ - угол трения; α - угол захвата.
Отсюда следует, что угол захвата должен быть меньше угла трения. Это возможно при межцентровом расстоянии валков и их минимальном диаметре, определяемых из выражения по рисунку 9.2.
D + b = (D +d)cosα ,
D = (d cosα - b)/( 1-cosα ).
Угол захвата при известном диаметре рабочих валков и их межцентровом расстоянии может быть определен по формуле
α =arccos (D +b)/(D +d).
Для успешной работы протирочных механизмов необходимо выполнение условия минимального воздействия на продукт вращающихся лопастей, следует добиваться измельчения продукта кромками отверстий в сите, при этом наблюдается высокое качество протертого продукта.
9.6.2. ОПРЕДЕЛЕНИЕ ПРОИЗВОДИТЕЛЬНОСТИ
В размолочных механизмах за один оборот вращающегося жернова измельчается количество продукта, находящееся в зазоре между жерновами. Для дисковых жерновов это количество равно
M = (D2max – D 2min ) b πγ /4.
Для конусных дисков
M = (Dmax + Dmin) bh πγ /2 sin δ ,
где Dmax - максимальный диаметр жернова, м; Dmin – минимальный диаметр жернова, м;
b - средняя величина зазора между жерновами, м; h - высота жернова, м;
57
δ- угол конусности.
γ- плотность продукта объемная, кг/м3.
При этих значениях обрабатываемой массы, производительность можно определить как
Q = Mn λ 3600, кг/час,
где λ - коэффициент заполнения продуктом зазора между жерновами.
Для дробильных механизмов производительность может быть определена по формуле, полученной из общепринятой при подстановке известных величин скорости прохождения продукта между валками, площади этого прохода
Q =π nсDLb γλ 3600, кг/час,
где L – длина валков, м;
nc – частота вращения стационарного валка, с-1;
λ - коэффициент заполнения зазора, зависящий от степени разрыхления продукта, равный 0,3. Производительность протирочных машин может быть определена из условия прохождения продукта через
сито за один оборот лопастного ротора в количестве, пропорциональном площади отверстий сита и толщине срезаемого слоя продукта. При этом производительность машины равна
Q = 900π D2 λ znc h γψ , кг/час,
где D – диаметр сита, м;
λ - коэффициент использования площади сита (при диаметре отверстий в сите 3 мм, коэффициент равен
0,32);
z – количество лопастей, шт;
nc – частота вращения лопастей, с-1;
h- толщина срезаемого слоя, 0,001-0,003 м;
γ- плотность обрабатываемого продукта, кг/м3;
ψ - коэффициент заполнения продуктом сита, 0,65 среднее значение.
9.6.3. ОПРЕДЕЛЕНИЕ МОЩНОСТИ ЭЛЕКТРОДВИГАТЕЛЯ ПРИВОДА В размолочных машинах, согласно теории П.А. Ребиндера, работа на измельчение будет равна Аоб = 3Ау iD2 Ka ,
где Ау – |
удельная работа на измельчение, Н/м; |
i - |
степень измельчения; |
D - средний исходный размер обрабатываемых частиц, м; |
|
Ка – поправочный коэффициент на неправильность формы кусочка продукта. |
Удельная работа на измельчение зависит от удельного сопротивления разрушению, рабочей высоты жерновов и определяется формулой
Ау = σ с h ϕ cosα , Н/м;
где σ с - удельное сопротивление разрушению при измельчении, равная 15 кПа для сухарей из пшеничной муки первого сорта;
h- рабочая высота жерновов, м;
α- угол конусности;
ϕ - коэффициент заполнения рабочей зоны продуктом, среднее значение 0,25.
При таких предположениях мощность измельчения конусными жерновами равна
N = 3 σ с h cosα i D2 n Ka ϕ / 1000η , кВт,
где -η - к.п.д. передаточного механизма.
Для дробильного механизма мощность равна
N = Кб (Np + Nи) / 1000 , кВт,
где Кб - коэффициент запаса мощности, среднее значение 1,1;
58
Np - составляющая мощности, необходимая для разрушения продукта раздавливанием-сжатием, Вт; Nи – составляющая мощности, необходимая для разрушения продукта истиранием-сдвигом, Вт.
Сила Р, возникающая при разрушении продукта нормальными усилиями, равна,
P =σ с Lb/cosα , Н,
где σ с - удельное сопротивление раздавливанию, для ядер орехов равно в среднем 1,4 МПа; L- рабочая длина валка, м;
Мощность раздавливания при этом равна
Np =σ с LcV1/cosα , Вт,
где V1 – c корость линейная поверхности быстро вращающегося валка, м/с.
Мощность, необходимая для разрушения продукта истиранием, равна
Nи = PfV2 (V1/V2 –1),
где V2 – скорость медленно вращающегося валка, м/с; f - коэффициент трения частиц продукта о валки.
Мощность электродвигателя протирочных машин может быть определена по формуле
N = (N1 + N2) /1000η , кВт,
где N1 - мощность, расходуемая на измельчение продукта кромками отверстий сита, Вт; N2 - мощность, расходуемая для продавливания через отверстия сита, Вт.
Первая составляющая мощности равна
N1 = q Kи Vо z ϕ Kпр Σ l Вт,
где q - удельное сопротивление измельчения продукта, для вареного картофеля 150 Нм; Kи - коэффициент использования длины кромок отверстий, среднее значение 0,3; Vo - усредненная окружная скорость лопасти, м/с;
z- количество лопастей, шт;
ϕ- коэффициент использования площади отверстий, среднее значение 0,6;
Kпр- коэффициент проскальзывания продукта, среднее значение 0,45; Σ l- общая длина кромок отверстий сита,
Вторая составляющая мощности равна
N2 = qoFoVzϕ , Вт,
где qo - удельное сопротивление продукта при продавливании через отверстия сита, для вареного картофеля 32 кПа;
Fo - площадь всех отверстий сита, м2;
V - скорость продавливания продукта через отверстия сита, м/с.
Мощность, необходимая для преодоления сил трения не рассчитывается, так как величина удельного сопротивления измельчению и продавливанию получена экспериментальным путем с учетом сил трения.
ЛЕКЦИЯ 10. РЕЖУЩЕЕ ОБОРУДОВАНИЕ. ТЕОРЕТИЧЕСКИЕ ОСНОВЫ ПРОЦЕССА РЕЗАНИЯ
План
10.1.Общие сведения
10.2.Виды режущих рабочих инструментов
10.3.Геометрические параметры режущих инструментов
10.4.Основные способы резания
10.5.Определение формы лезвия с постоянным коэффициентом скольжения
10.6.Определение усилий при резании
10.1. ОБЩИЕ СВЕДЕНИЯ
59

Режущее оборудование применяется при разрезании пластичных пищевых продуктов на ломтики, брусочки, кубики, кружочками и для шинкования. Разрезание продуктов осуществляется режущими инструментами, посредством которых происходит разделение исходного куска продукта на частицы заданных формы и размеров.
На предприятиях общественного питания резанию на машинах подлежат овощи, мясо, рыба, хлебобулочные изделия, гастрономические товары (колбасы различных сортов, ветчина, буженина, сыр и т.д.).
10.2. ВИДЫ РЕЖУЩИХ ИНСТРУМЕНТОВ
Продукты измельчают при помощи разнообразных легкосъемных (для облегчения процесса заточки) режущих инструментов (ножей, дисков, решеток и др.), имеющих в своем поперечном сечении по рабочему лезвию форму двухгранного клина, одностороннего или двухстороннего, изображенного на рисунке 10.1. Изредка находят применение в некоторых случаях в качестве режущих инструментов так же струны, имеющие круглое поперечное сечение.
а |
а) |
б) |
Рис. 10.1. Двухгранный клин а) - односторонний; б) – двухсторонний.
Основные термины и определения частей рабочего инструмента имеют наименования:
Опорная грань О – плоскость, которой клин опирается на продукт и скользит по его массиву (еще не измельченной части);
Рабочая или лицевая грань А – поверхность, составляющая острый угол с опорной гранью, по ней скользят и ею направляются отрезанные частицы продукта;
Угол заточки α - острый угол между опорной и рабочей гранями; Лезвие Л – режущая или рабочая кромка – находящаяся у вершины угла заточки линия пересечения рабо-
чей и опорной граней, практически – поверхность с очень малым радиусом кривизны, имеет множество микрозубцов;
Острота лезвия – удвоенный радиус кривизны.
Ножи с двухсторонней заточкой имеют две рабочих грани. Их можно рассматривать как два односторонних ножа, сложенных опорными гранями вместе.
Для осуществления процесса резания необходимо относительное перемещение ножа и продукта. Подвижным может быть нож или продукт, или оба одновременно. Необходимо устройство для фиксации продукта и подачи его под нож
10.3. ГЕОМЕТРИЧЕСКИЕ ПАРАМЕТРЫ РЕЖУЩИХ ИНСТРУМЕНТОВ
Измельчение продукта происходит с помощью режущей кромки инструмента, путем его вклинивания в массив и разделения на определенные частицы продукта. В процессе резания режущая кромка подвергается наибольшим изменениям: затуплению, изгибанию, выкрашиванию и др., вследствие чего изменяется качество измельчения и возрастают энергетические затраты. Грани инструмента при этом остаются практически нетронутыми. В то же время геометрические параметры инструмента влияют на износ режущей кромки, характер и качество измельчения. Наибольшая величина контактных усилий создается на режущей кромке, где и возникает наибольшая концентрация напряжений в продукте. Поэтому, при резании продукт вначале разрушается под действием режущей кромки инструмента и далее, по мере вклинивания его, в разрушении участвуют и грани инструмента. При свободном резании может образовываться опережающая трещина в массиве продукта (при резании малопластичных, охлажденных продуктов).
60