
дп
.pdf
Химические процессы, протекающие в солоде при сушке, не одинаковы на различных её стадиях и у разных типов солода. Содержание крахмала, пентозанов и клетчатки изменяется незначительно, количество же
инвертного сахара существенно снижается.
Основные реакции, приходящие к образованию меланоидинов,
протекают в химической фазе сушки при температуре 80-95°С.
Меланоидины образуются в основном за счет серосодержащих аминокислот,
обладающих большой активностью, например серина.
Процесс меланоидинообразования можно изобразить следующим
уравнением (рисунок 5): |
|
|
|
|
|
|
NH |
2 O = C – H |
N = C – H |
||||
|
|
|
|
|
|
|
R – C – H |
(CHOH)3 |
R – C – H (CHOH)3 |
||||
|
|
|
|
|
|
|
COOH |
CH2OH |
COOH CH2OH |
||||
Аминокислота |
Пентоза |
Меланоидины |
Рисунок 5 - Уравнение меланоидинообразования
Вхимической фазе сушки солода протекает также процесс
терморасщепления углеводов, который приводит к появлению таких окрашенных продуктов, как карамели. Карамелизованные вещества придают пиву горький вкус жженого солода и сильно повышают цветность готового продукта. Меланоидины сообщают пиву характерные вкус и аромат,
повышают её пеностойкость. Они обладают кислой реакцией, что положительно сказывается на кислотности солод, а благодаря их восстановительным свойствам обеспечивается хорошая коллоидная стойкость пива.
Процесс сушки влияет на количество растворимых веществ в солоде,
т.е на выход экстракта. С повышением температуры и длительности сушки выход экстракта уменьшается. От температуры сушки солода зависят также свойства меланоидинов, влияющих на аромат, пенообразование,
пеностойкость и стойкость пива.
|
Лист |
ТГТУ ДП 240902.001 ПЗ |
28 |
Изм. Лист № докум. Подпись Дата |
|

9.Охлаждение высушенного солода – это теплообменный процесс,
который служит для удаления тепла из толщи материала. Благодаря чему
над солодом можно проводить дальнейшие технологические операции
(солод охлаждают до температуры 35 °С).
10.Обработка солода звуком. Этот процесс направлен на улучшения амилолитической активности солода, который проводится при частоте
звуковых колебаний 3070 Гц и амплитуде 100%.
11.Отбивка ростков высушенного солода – это механическая обработка, технологическая цель которой заключается в освобождение солода от ростков. Солодовенные ростки имеют горький вкус, который
неблагоприятно влияет на качество пива. Удаление ростков проводят на
специальных росткоотбойных машинах или в процессе транспортирования солода, после чего направляют на аспирационное устройство для их разделения.
12.Отлежка солода. |
Выдержка |
|
свежевысушенного солода |
|
|
|
|
||
производится в течение 3-4 недель. К |
этому времени |
происходит |
||
|
|
|
|
|
инактивация ферментов, |
увеличивается |
влажность и |
количество |
растворимых азотистых веществ, улучшается амилолитическая активность солода. Также солод нельзя сразу направлять на производство пива, потому что при его дроблении чрезмерно измельчается эндосперм и оболочка, что может вызывать недостаточно полное осахаривание и затруднение фильтрование заторов.
13.Хранение солода осуществляют при температуре от 10 до 30ºС в тех же условиях, что и ячмень.
2.4 Продуктовый расчет солодовенного производства Исходные данные: годовая мощность проектируемого производства
100 тыс. т солода в год. Число рабочих дней для башни элеватора и
|
Лист |
ТГТУ ДП 240902.001 ПЗ |
29 |
Изм. Лист № докум. Подпись Дата |
|

солодовенного производства 330. Прием зерна продолжается 120 дней.
Продуктовый расчет выполняется на 1 тонну очищенного ячменя с дальнейшим пересчетом на годовую, а затем суточную производительность
[14].
Для получения 1000 кг очищенного ячменя (Gо. я) требуется товарного ячменя:
Gт. я. = 100∙100/(100 – е1)=1000∙100/(100 – 12,4) = 1141,55 кг. (2.4.1)
где е1 – сумма отходов ячменя при отчистки и сортировке она составляет
12,4 мас.%.
Определяем объем товарного ячменя (в м3) при его насыпной
плотности 630 кг/м3: |
|
|
|
|
Vт. я. = Gт. я./ рт. я. = 1141,55/630=1,81 м3. |
|
(2.4.2) |
||
Находим массу ячменя (в кг) – схода с сита 2,2∙20 мм (III сорта): |
||||
GIII c = (Gт. я. – 100) ∙е2/е1= (1141,55 – 1000)∙6,2/12,4 = 70,76 кг. |
(2.4.3) |
|||
где е2 – процент отходов ячменя III сорта 6,2%. |
|
|
||
Объём ячменя III |
сорта |
при насыпной плотности ячменя 520 кг/м3 |
||
будит равен: |
|
|
|
|
VIII с = GIIIс/ рIII с = 70,76/520=0,14 м3. |
|
(2.4.4) |
||
Находим массу зерновых отходов и она будит равна: |
|
|||
Gз. о = (Gт. я. – 1000) ∙е3/е1=(1141,55 – 1000) ∙4,2/12,4=47,9 кг. (2.4.5) |
||||
где е3 – процент отходов ячменя III сорта 4,2%. |
|
|
||
Следовательно, |
объем |
зерновых отходов |
при их |
насыпной |
плотности 500 кг/м3 будет равен: |
|
|
||
Vз.о. = Gз.о../ рз.о.= 47,9/500= 0,096 м3. |
|
(2.4.6) |
Масса сорных отходов равна:
Gс. о = (Gт. я. – 1000)∙е4/е1= (1141,55-1000) ∙1,6/12,4=18,26 кг, (2.4.7)
где е4 – процент сорных отходов 1,6%.
|
Лист |
ТГТУ ДП 240902.001 ПЗ |
30 |
Изм. Лист № докум. Подпись Дата |
|

Тогда объем сорных отходов при их насыпной плотности 400 кг/м3
равен: |
|
Vс.о. = Gс.о../ рс.о.=18,26/400=0,046 м3. |
(2.4.8) |
Количество сухих веществ ячменя, поступающих для замачивания, |
|
вычисляем по формуле: |
|
GСВ=Gо. я∙.(100 – Wо. я.)/100= 1000∙ (100 – 14,7)/100=853 кг, |
(2.4.9) |
Wо.я.-влажность очищенного ячменя 14,7 мас. %. |
|
Определяем массу замоченного ячменя: |
|
Gз. я.= GСВ∙(100 – е5)/(100 – Wз. я.)= |
|
=853∙(100 – 1,6)/(100 – 43)=1472,55 кг, |
(2.4.10) |
где е5 – потери сухих веществ при замачивании на сплав 1% и на выщелачивание 0,6%; Wз. я. – влажность замоченного ячменя 43%.
Объем замоченного ячменя будет равен: |
|
Vз.я=Gз.я/рз.я=1472,55/660=2,23 м3, |
(2.4.11) |
где рз.я. – насыпная плотность замоченного зерна 660 кг/м3. |
|
Находим массу воздушно-сухого сплава по формуле: |
|
Gс. в-с=Gо.я∙е6=1000∙0,01=10 кг, |
(2.4.12) |
где е6 – процент воздушно-сухого сплава 1 мас. %.
Соответственно, объем воздушно-сухого сплава при насыпной
плотности 400 кг/м3 равен: |
|
Vc. в-с.=Gc. в-с./рс. в-с.=10/400=0,025 м3. |
(2.4.13) |
Далее определяем массу влажного сплава по формуле: |
|
Gс.вл=(1000 – Wс.вл) ∙Gс. в-с/(1000 – Wс. вл)= |
|
=(1000-150) ∙10/(1000 – 300)=12,14 кг, |
(2.4.14) |
где Wс. в-с – влажность воздушно-сухого сплава 15 мас. %; Wс. вл –
влажность влажного сплава 30 мас. %.
Объем при насыпной плотности влажного сплава 500 кг/м3 будет
равен: |
|
Vс. вл=Gс. вл/рс. вл=12,14/500=0,024 м3. |
(2.4.15) |
Лист
Изм. Лист |
№ докум. |
Подпись Дата |
ТГТУ ДП 240902.001 ПЗ |
31 |

Массу свежепроросшего солода Gз.с. определяем по формуле: Gз.с.=GСВ∙ (100 – е5 – е7)/(100 – Wз.с)=
=853∙ (100 – 1,6 – 5,7)/(100-30)=1129,62 кг. (2.4.16)
где е7 – процент потерь сухих веществ на дыхание при проращивании зерна
5,7 мас. %, Wз. с – влажность свежепроросшего солода 42 мас. %.
Тогда, объем свежепроросшего солода будет равен: |
|
Vз. с= Gз.с./рз. с=1129,62/370=3,05 м3, |
(2.4.17) |
где рз.с – насыпная плотность свежепроросшего солода 370 кг/м3. |
|
Масса свежевысушенного солода будет равна: |
|
Gс. с=GСВ∙ (100 – е5 – е7 – е8)/(100 – Wс.с)= |
|
=853∙ (100 – 1,6 – 5,7 – 4,3)/(100 – 3)=777,37 кг, |
(2.4.18) |
где е8 – процент потерь на ростки 4,3 мас. %; Wс с.=влажность |
|
свежевысушенного солода 3 мас. %. |
|
Объем свежевысушенного солода равен: |
|
Vc. c= Gс. с/рс. с=777,37/510=1,52 м3, |
(2.4.19) |
где рс. с – насыпная плотность свежевысушенного солода 510кг/м3. |
|
Определяем массу отлежавшегося солода по формуле: |
|
Gо. с= Gс. с∙ (100 - Wс. с)/(100 – Wо. с)= |
|
=777,37∙ (100 – 3)/(100 – 5,17)=795,16 кг, |
(2.4.20) |
где Wо. с – влажность отлежавшегося солода 5,17 мас. %.
Соответственно, объем отлежавшегося солода будет равен:
Vо. с= Gо. с/ро. с=795,16/530=1,5 м3, |
(2.4.21) |
где ро. с – насыпная плотность отлежавшегося солода 530 кг/м3.
Находим |
массу товарного |
солода после хранения и полировки по |
|
формуле: |
Gт. с= Gо. с∙ |
(100 – е9 – е10)/100= |
|
|
=795,16∙ (100 – 0,07 – 0,55)/100=790,23 кг, |
(2.4.22) |
где е9 – процент потерь солода при хранении на элеваторе 0,07 мас. %; е10 –
процент потерь солода при полировки 0,55 мас. %.
|
Лист |
ТГТУ ДП 240902.001 ПЗ |
32 |
Изм. Лист № докум. Подпись Дата |
|

Масса ростков на реализацию будет равна:
Gр= е11∙ (100 – Wо. я)/(100 – Wр)= 43∙ (100 – 14,7)/(100 – 10)=40,75 кг, (2.4.23)
где е11 – процент отходов на образование ростков (4,3 мас. %); Wр –
влажность ростков (10 мас. %).
Далее определяем потери ячменя при разгрузке и хранении по
формуле: |
Gп.=Gт. я∙ е12/100+Gо.я∙ е13/100= |
|
|
=1141,55∙0,15/100+1000∙0,09/100=2,6кг, |
(2.4.24) |
где е12 – процент потерь ячменя при разгрузке 0,15 мас. %; е13 – процент потерь ячменя при хранении на складе 0,09 мас. %. [14].
|
|
|
Для определения годовой потребности ячменя и производительности |
|||||||||||||||||||||||||
|
на каждой стадии пользуемся формулой: |
|
|
|
|
|
|
|
|
|
|
|||||||||||||||||
|
|
|
|
|
|
|
|
|
Gг.п.я=Gя∙100 т, |
(2.4.25) |
|
|
|
|
||||||||||||||
|
где 100 – годовая мощностью завода. |
|
|
|
|
|
|
|
|
|
|
|
|
|
||||||||||||||
|
|
|
Для нахождения суточной потребности ячменя и производительности |
|||||||||||||||||||||||||
|
используем формулу: |
|
|
|
|
|
|
|
|
|
|
|
|
|
|
|
|
|
|
|
|
|||||||
|
|
|
|
|
|
|
|
|
Gс.п.я.= Gг.п.я/330 т, |
(2.4.26) |
|
|
|
|
||||||||||||||
|
где 330 – количество рабочих дней в году. |
|
|
|
|
|
|
|
|
|
|
|||||||||||||||||
|
|
|
Полученные данные сводим в таблицу 6 столбец 4 и 5. |
|
|
|
|
|||||||||||||||||||||
|
|
|
Таблица 6 - Материальный баланс при производстве солода |
|||||||||||||||||||||||||
|
|
|
|
|
|
|
|
|
|
|
|
|
|
|
|
|
|
|
|
|
|
|
|
|
|
|
||
|
|
|
|
|
|
|
|
|
|
|
|
|
|
|
|
|
|
|
|
|
|
|
|
|
|
|
||
|
|
|
|
|
|
|
|
|
Масса продукта, кг |
|
|
Масса продукта, т |
|
|||||||||||||||
|
N0 |
|
|
Продукт |
|
|
|
|
|
|
|
|
|
|
|
|
|
|
|
|
|
|
|
|
|
|
|
|
|
|
|
|
|
|
|
|
|
|
|
|
|
|
|
|
|
|
|
|
|
|
|
|
|
|
|
||
|
|
|
|
|
|
|
|
отсортированного |
|
|
|
|
|
|
солодатоварного |
|
|
|
На 100 000 т товарного солода в |
|
|
|||||||
|
|
|
|
|
|
|
|
|
|
|
|
|
|
|
|
|
|
|
|
|
||||||||
|
|
|
|
|
|
|
|
кг1000на |
очищенногои |
ячменя |
|
|
|
|
кг1000на |
|
|
|
|
год |
|
|
|
|
||||
|
|
|
|
|
|
|
|
|
|
|
|
|
|
|
|
|
|
|
|
|
|
|
|
|
|
|||
|
|
|
|
|
|
|
|
|
|
|
|
|
|
|
|
|
|
|
|
|
в сутки |
|
|
|
в год |
|
|
|
|
|
|
|
|
|
|
|
|
|
|
|
|
|
|
|
|
|
|
|
|
|
|
|
(330 дней) |
|
|
|
|
|
|
|
|
|
|
|
|
|
|
|
|
|
|
|
|
|
|
|
|
|
|
|
|
|
|
|
||
|
|
|
|
|
|
|
|
|
|
|
|
|
|
|
|
|
|
|
|
|
|
|
|
|
|
|||
|
|
|
|
|
|
|
|
|
|
|
|
|
|
|
|
|
|
|
|
|
|
|
|
|
|
|
|
|
|
1 |
|
|
2 |
|
|
|
|
3 |
|
|
|
|
|
4 |
|
|
5 |
|
|
|
6 |
|
|
|
|||
|
|
|
|
|
|
|
|
|
|
|
|
|
|
|
|
|
|
|
|
|
|
|
|
|||||
|
1 |
|
|
Товарный ячмень |
|
|
|
1142 |
|
|
|
|
1442 |
|
437 |
|
|
|
144200 |
|
|
|
||||||
|
|
|
|
|
|
|
|
|
|
|
|
|
|
|
|
|
|
|
|
|
|
|
|
|
|
|||
|
2 |
|
|
Очищенный и |
|
|
|
1000 |
|
|
|
|
1263 |
|
381 |
|
|
|
126300 |
|
|
|
||||||
|
|
|
отсортированный |
|
|
|
|
|
|
|
|
|
|
|
|
|
|
|||||||||||
|
|
|
|
|
|
|
|
|
|
|
|
|
|
|
|
|
|
|
|
|
|
|
|
|
||||
|
|
|
|
ячмень |
|
|
|
|
|
|
|
|
|
|
|
|
|
|
|
|
|
|
|
|
|
|||
|
|
|
|
|
|
|
|
|
|
|
|
|
|
|
|
|
|
|
|
|
|
|
|
|
|
|
|
|
|
Лист |
ТГТУ ДП 240902.001 ПЗ |
33 |
Изм. Лист № докум. Подпись Дата |
|

Окончание таблицы 6
|
1 |
|
|
2 |
|
|
3 |
|
|
4 |
|
|
5 |
|
|
6 |
|
|
|
|
|
|
|
|
|
|
|
|
|
|
|
|
|
|
|
|
|
|
|
|
|
|
|
|
|
|
|
|
|
|
|
|
|
|
3 |
|
|
Ячмень – сход с |
|
71 |
|
90 |
|
27 |
|
9000 |
|
||||
|
|
|
сита с ячейками |
|
|
|
|
|
|||||||||
|
|
|
|
|
|
|
|
|
|
|
|
|
|
|
|
|
|
|
|
|
|
2,2∙20 мм |
|
|
|
|
|
|
|
|
|
|
|
|
|
|
|
|
|
(III сорт) |
|
|
|
|
|
|
|
|
|
|
|
|
|
|
|
|
|
|
|
|
|
|
|
|
|
|
|
|
|
|
|
|
4 |
|
|
Зерновые отходы |
|
48 |
|
61 |
|
19 |
|
6100 |
|
||||
|
|
|
|
|
|
|
|
|
|||||||||
|
|
|
|
|
|
|
|
|
|
|
|
|
|
|
|
|
|
|
5 |
|
|
Сорные отходы |
|
19 |
|
23 |
|
7 |
|
2300 |
|
||||
|
|
|
|
|
|
|
|
|
|||||||||
|
|
|
|
|
|
|
|
|
|
|
|
|
|
|
|
|
|
|
6 |
|
|
Замоченный |
|
1473 |
|
1860 |
|
564 |
|
186000 |
|
||||
|
|
|
ячмень |
|
|
|
|
|
|||||||||
|
|
|
|
|
|
|
|
|
|
|
|
|
|
|
|
|
|
|
|
|
|
|
|
|
|
|
|
|
|
|
|
|
|
|
|
|
7 |
|
|
Воздушно-сухой |
|
10 |
|
13 |
|
4 |
|
1300 |
|
||||
|
|
|
сплав |
|
|
|
|
|
|||||||||
|
|
|
|
|
|
|
|
|
|
|
|
|
|
|
|
|
|
|
|
|
|
|
|
|
|
|
|
|
|
|
|
|
|
|
|
|
8 |
|
|
Влажный сплав |
|
12 |
|
16 |
|
6 |
|
1600 |
|
||||
|
|
|
|
|
|
|
|
|
|||||||||
|
|
|
|
|
|
|
|
|
|
|
|
|
|
|
|
|
|
|
9 |
|
|
Свежепроросший |
|
1130 |
|
1427 |
|
432 |
|
142700 |
|
||||
|
|
|
солод |
|
|
|
|
|
|||||||||
|
|
|
|
|
|
|
|
|
|
|
|
|
|
|
|
|
|
|
|
|
|
|
|
|
|
|
|
|
|
|
|
|
|
|
|
|
10 |
|
|
Свежевысушен- |
|
778 |
|
982 |
|
300 |
|
98200 |
|
||||
|
|
|
ный солод |
|
|
|
|
|
|||||||||
|
|
|
|
|
|
|
|
|
|
|
|
|
|
|
|
|
|
|
11 |
|
|
Отлежавшийся |
|
795 |
|
1004 |
|
304 |
|
100400 |
|
||||
|
|
|
солод |
|
|
|
|
|
|||||||||
|
|
|
|
|
|
|
|
|
|
|
|
|
|
|
|
|
|
|
12 |
|
|
Товарный солод |
|
791 |
|
998 |
|
303 |
|
99800 |
|
||||
|
|
|
|
|
|
|
|
|
|
|
|
|
|
||||
|
13 |
|
|
Ростки |
|
41 |
|
52 |
|
16 |
|
5200 |
|
||||
|
|
|
|
|
|
|
|
|
|
|
|
|
|
|
|
|
|
|
14 |
|
|
Потери при |
|
3 |
|
4 |
|
2 |
|
400 |
|
||||
|
|
|
хранении |
|
|
|
|
|
|||||||||
|
|
|
|
|
|
|
|
|
|
|
|
|
|
|
|
|
2.5 График технологического цикла производства
График технологического цикла разработан для производственной линии пивоваренного ячменного солода мощностью 100 тыс. т/год на основе часового материального баланса, подобранного оборудования и его технических характеристик. Предприятие работает в три смены продолжительностью по восемь часов. Разработанный график технологических процессов представлен на рисунке 6.
|
Лист |
ТГТУ ДП 240902.001 ПЗ |
34 |
Изм. Лист № докум. Подпись Дата |
|

Рисунок 6 - График технологических процессов производства солода В графе «Всего» указана масса перерабатываемого сырья и готовой
продукции. По горизонтальной оси графика указана длительность операций. Исходя из производственного опыта действующего предприятия,
продолжительность технологических операций: приемка ячменя - 3ч,
предварительная очистка –3 ч, основная очистка – 2 ч, замачивание ячменя –
2 сут, проращивание ячменя – 5 сут, сушка свежепроросшего солода – 20 ч,
охлаждение свежевысушенного солода – 0,5 ч, отбивка ростков солода – 3 ч.
2.6 Подбор и расчет технологического оборудования для производства солода
Расчет аппарата для замачивания Для замачивание пивоваренного ячменя используют или замочный
аппарат с коническим днищем, или плоским днищем и включающая группу
|
Лист |
ТГТУ ДП 240902.001 ПЗ |
35 |
Изм. Лист № докум. Подпись Дата |
|

из цилиндро-конических замочных аппаратов. Для достижения
равномерного и быстрого замачивания ячменя в больших объемах рекомендуется использовать замочный чан с плоским днищем.
Определяем количество, вместимость и основные конструктивные
параметры замочных аппаратов |
для солодовенного |
производства |
||||
мощностью 100 тыс. т. в год. |
|
|
|
|
||
|
Суточная производительность солодовенного производства по товар- |
|||||
ному солоду при 330 рабочих сутках в год равна: |
|
|||||
|
|
Gтс=П/N=100000/330 = 303 т/сут, |
(2.6.1) |
|||
|
|
|
||||
где |
П |
— мощность солодовенного производства, т/г; |
N |
— количество |
||
рабочих суток солодовни в год при трехсменной работе, сут. |
|
|||||
|
Количество замочных аппаратов при двухсуточном замачивании и |
|||||
максимально возможной вместимости замочного аппарата будет равно: |
||||||
|
|
n=Gоя∙tз/Gя=381∙2/381 = 2 шт, |
(2.6.2) |
где tз — продолжительность замачивания ячменя, сут; Gя— масса очи-
щенного и отсортированного ячменя, загружаемого в один замочный
аппарат, т. |
|
|
|
|
|
|
|
|
|
Уточненная масса очищенного и отсортированного ячменя, |
|||||||
загружаемого в один замочный аппарат: |
|
|
|
|||||
|
Gя=Gоя∙t3/n=381∙2/2 = 381 т. |
|
(2.6.3) |
|||||
|
Объем очищенного и отсортированного ячменя, загружаемого в один |
|||||||
замочный аппарат определяем по формуле: |
|
|
|
|||||
|
|
|
|
|
|
|||
|
Va =Gя /pя =381/0,65 = 585,4 м3 , |
(2.6.4) |
||||||
где |
— насыпная плотность зерна, кг/м ( = 0,65 т/м3). |
|
|
|||||
|
Полная вместимость замочного аппарата равна: |
|
|
|
||||
|
|
|
|
|
||||
|
Vп=kз∙Vа=1,5∙585,4 = 878,1 |
м3 , |
|
|
|
(2.6.5) |
||
где |
кз — коэффициент |
запаса |
вместимости |
замочного |
аппарата, |
|||
учитывающий увеличение |
объема |
замоченного |
зерна на |
40...45% и |
|
Лист |
ТГТУ ДП 240902.001 ПЗ |
36 |
Изм. Лист № докум. Подпись Дата |
|
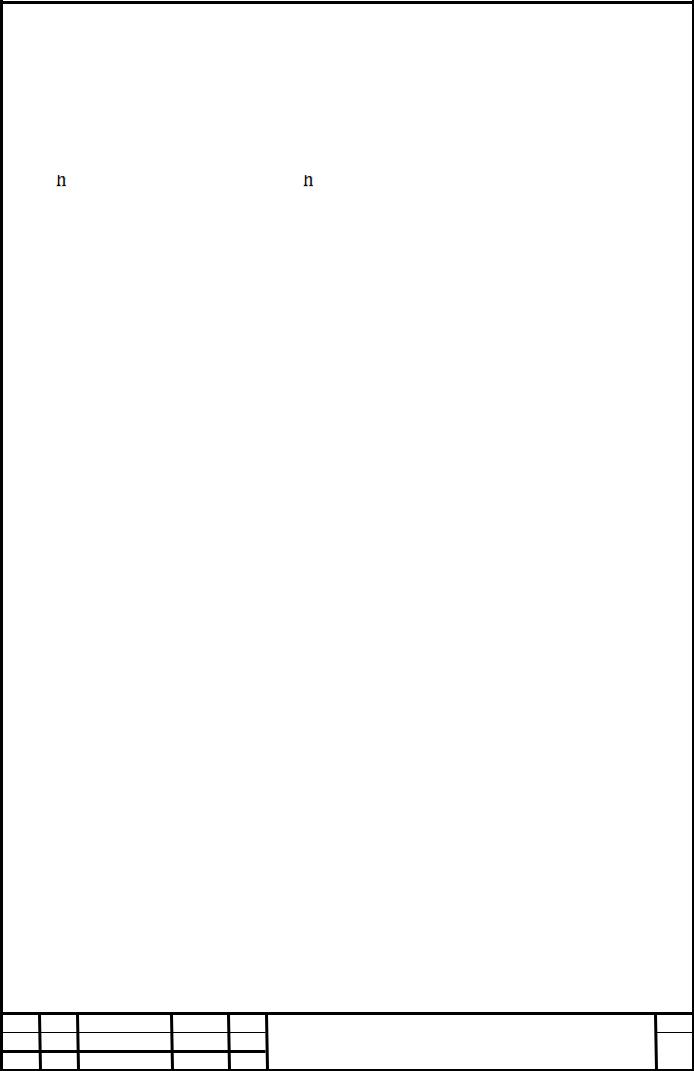
увеличение вместимости еще на 5...10% для предохранения от выброса зерна
и воды при мойке и перекачке зерна через центральную трубу ( |
= 1,5). |
|
|||
Площадь решетки замочного аппарата равна: |
|
|
|
||
S=Vп/h=878,1/3 = 292,7 м2, |
|
|
|||
|
(2.6.6) |
|
|||
— высота предельного слоя, |
= 3 м. |
|
|
|
|
После проведенных расчетов выбираем 2 замочных чана системы |
|||||
Lausmann с техническими характеристиками (табл. 7) [15]. |
|
|
|
||
Таблица 7 - Техническая характеристика замочного чана |
|
|
|
||
|
|
|
|
|
|
Показатели |
|
Значения |
|
|
|
Вместимость, м3 |
|
900 |
|
|
|
Диаметр, м |
|
15 |
|
|
|
Высота, м |
|
5 |
|
|
|
Мощность вентилятора, м3/т*ч |
|
200 |
|
|
|
Число оборотов вентилятора, об/мин |
|
0-1500 |
|
|
|
Расчет солодорастильного аппарата ящечного типа Для проращивания ячменя используют солодорастильное
оборудование барабанного, ящичного типа (прямоугольного или круглого сечения), солодорастильный аппарат типа передвижная грядка, а также солодовни башенного и шахтного типа. Для производства был выбран солодорастильный аппарат ящичного типа (прямоугольного сечения),
который имеет ряд преимуществ:
- высокая производительность;
-равномерное развитие солода;
-легко доступен для осмотра и контроля.
Основные геометрические параметры отдельно стоящих солодорастильных аппаратов ящичного типа определяют, исходя из объема замоченного ячменя, единовременно загружаемого в них [16].
|
Лист |
ТГТУ ДП 240902.001 ПЗ |
37 |
Изм. Лист № докум. Подпись Дата |
|