
- •Травматизм непроизводственного характера по Донецкой области
- •Таблица 1.3
- •Отклонения травматизма от среднегодовых
- •Годы
- •СПИСОК ЛИТЕРАТУРЫ
- •Список литературы
- •Измерения шума на рабочих местах.
- •Нормирование шума.
- •3.5.4.1. Действие электрического тока на организм человека
- •Рис. 3.5.4. Прикосновение в трёхфазной сети с изолированной нейтралью
- •Таким образом напряжение на корпусе
- •Рисунок 4.В2. Система управления охраной труда
- •ДОПОЛНЕНИЯ И ИЗМЕНЕНИЯ
- •ДОПОЛНЕНИЯ И ИЗМЕНЕНИЯ
- •Обвалы и обрушения
- •Принято
- •Согласовано
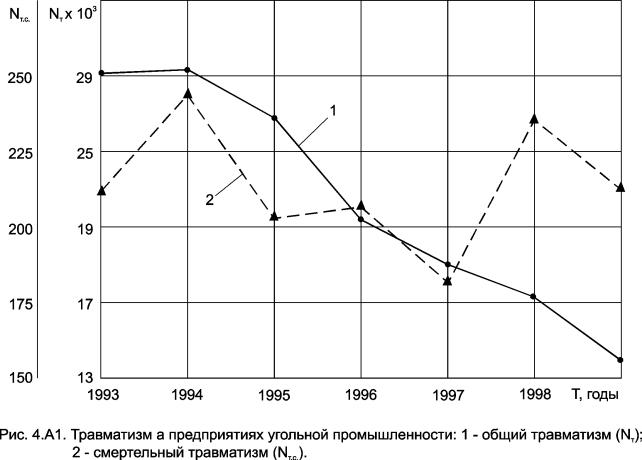
Динамика общего (1) и смертельного (2) травматизма представлена на
рис.4.А1. На две особенности динамики следует обратить внимание. Во-первых, совершенно очевидно как уменьшение во времени общего
травматизма, так и отсутствие такового по смертельному травматизму.
Во-вторых, подтверждается мысль, высказанная при изложении курса БЖД, о том, что не следует идентифицировать изменение смертельного травматизма с общим, помня о том, что последний безусловно самый тревожный.
В соответствии с изложенным в главе 3 понятиями об опасных производственных факторах назовем их для угольной промышленности с
указанием значимости по годам (табл.4.А1).
Таблица 4.А1.
Сведения о травматизме в шахтах.
№№ |
Опасный производственный |
Уровень травматизма, %: годы |
||||
п/п |
фактор |
|
|
|
|
|
1989 |
1990 |
1996 |
1997 |
|||
|
|
|||||
|
|
|
|
|
|
|
1. |
Обвалы и обрушения |
32,5 |
31,4 |
26,6 |
25,5 |
|
2. |
Транспортные средства и |
29,7 |
29,1 |
24,1 |
18,4 |
|
подземные установки |
||||||
3. |
На машинах и механизмах |
11,0 |
8,1 |
6,6 |
6,1 |
|
|
|
|
|
|
|
|
|
|
228 |
|
|
|
Продолжение таблицы 4.А1.
№№ |
Опасный производственный |
Уровень травматизма, %: годы |
||||
п/п |
фактор |
|
|
|
|
|
1989 |
1990 |
1996 |
1997 |
|||
|
|
|||||
|
|
|
|
|
|
|
4. |
При внезапных выбросах |
3,7 |
3,7 |
2,5 |
2,3 |
|
|
угля и газа |
|
|
|
|
|
5. |
При взрывах газа и пыли, |
2,3 |
9,6 |
2,8 |
3,4 |
|
удушья, отравления |
||||||
|
При взрывных работах и |
|
|
|
|
|
6. |
обращении со взрывчатыми |
2,1 |
2,2 |
0,7 |
1,1 |
|
|
материалами |
|
|
|
|
|
7. |
Электротравматизм |
1,6 |
1,6 |
3,2 |
6,9 |
На две основные особенности сведений табл.4.А1. необходимо обратить внимание.
Во-первых травматизм за 1989 и 1990 г.г. представлен в целом по шахтам СССР, разумеется, включая шахты Украины.
Во-вторых, сведения о травматизме систематизировались и анализировались, в том числе и за 1995-1999 г.г. МакНИИ (заведующий отделом общей безопасности, кандидат технических наук Лёвкин Н.Б.) До 1992 г. Минуглепром СССР ежегодно и за пятилетия издавал для служебного пользования обзоры «Состояние и причины производственного травматизма на предприятиях Минуглепрома», которые были использованы при анализе.
Рассмотрим травматизм по опасным производственным факторам.
1.Из данных табл. 4.А1 следует, что травматизм от обвалов и обрушений остается продолжительное время наиболее высоким среди опасных производственных факторов (ОПФ). Из общего числа случаев при обвалах и обрушениях примерно 65-66% приходится на очистные забои. На забои подготовительных выработок и на протяжение действующих подготовительных выработок соответственно приходится 22-23% и 12-15%. Последние происходят в основном при перекреплении.
Одной из основных причин травматизма в лавах является применение индивидуальной крепи. Оно наряду с несовершенством или недостаточным количеством крепи нередко обусловливает чуть ли не массовые нарушения паспортов управления кровлей и крепления. Различные нарушения паспортов крепления по этой причине отмечаются почти в 80% несчастных случаев, происшедших в очистных забоях. В них можно было бы сократить травматизм за счет применения комплексов оборудования с механизированными крепями. Наиболее эффективными являются современные комплексы со щитовыми крепями, что подтверждают данные табл.4.А2.
229
Таблица 4.А2. Распределение несчастных случаев (н/с) на шахтах Западных районов за период 1984-1989 г.г.
Технологическая схема выемки |
Удельный вес, % |
Условный показатель, |
|
|
|
|
нс/добыча |
|
н/с |
добыча |
|
Узкозахватная с |
|
|
|
механизированной крепью (КМЗ). |
39,5 |
69,3 |
0,57 |
Узкозахватная с индивидуальной |
|
|
|
крепью. |
37,6 |
16,3 |
2,31 |
Из данных табл.4.А2 следует, что в случае применения механизированных крепей количество н/с на 1 т добычи может быть снижено
влавах почти в 4 раза.
Вочистных забоях, оснащенных индивидуальной крепью, самой опасной является зона изгиба конвейера, где вместе с примыкающей к ней зоной управления комбайном происходит более 40% н/с. Около 30% н/с происходит на концевых участках лав (ниши, сопряжения) и остальные 30% - на протяжении лавы.
Основными организационными причинами травматизма от обвалов и обрушений в очистных забоях являются: - нарушения паспортов крепления и управления кровлей; - нарушения технологии ведения горных работ; - несоответствие паспортов крепления и управления кровлей горногеологическим условиям применения.
Травматизм в подготовительных выработках, как уже указывалось, связан непосредственно с их проведением, а также имеет место на протяжении. Происходит он в первую очередь из-за нарушений конструкций крепи, ее некачественной установки, отсутствия временной крепи, оставления пустот за крепью. Опасность последнего нарушения особенно велика, т.к. незаложенные пустоты в дальнейшем не только способствуют деформациям крепи, но и являются очагами местных и слоевых скоплений метана. Наличие незаполненных пустот за крепью по мнению комиссий, расследовавших аварии, явилось причиной более 80% всех смертельных н/с от обрушений в подготовительных забоях и на протяжении выработок.
На сопряжениях подготовительных выработок с очистным забоем породы обрушаются в результате значительных обнажений кровли. Причины последних – большое расстояние от крепи до средств охраны выработок, снятие у окна лавы большого числа ножек крепи и несвоевременное их восстановление, некачественное крепление концевого участка лавы.
Впоследние годы (1999-2000) было установлено, что в основе самой природы обрушений в подавляющем числе случаев находится расслоение
230
пород кровли пласта. Первородная особенность осадочного массива, каковым является угленосный массив, - слоистость, слоистость и ещё раз слоистость. Даже когда речь идёт не о глинистых или песчано-глинистых сланцах, а о песчанистых сланцах и даже песчаниках, то и в них нередко есть тонкие прослои глинистых материалов, которые располагаются между различными по мощности слоями массивного песчаника.
Втечении многих десятилетий прежде геомеханические процессы – явления, происходящие при проведении подготовительных выработок и выемке угля в лавах, рассматривались и оценивались с позиций величины, распределения и перераспределения напряжений, обусловливающих возникновение и развитие деформаций. Ученые рассматривали эти деформации как результат возникновения и действия напряжений на контуре, вокруг и впереди выработки.
Вдевяностые годы Донецкий государственный технический университет (ДонГТУ) развивает новое представление о природе разрушения осадочного массива, находящегося вблизи и на некотором расстоянии от искусственных
полостей – горных выработок, в том числе в зонах влияния над - или подработки. В его основе находится положение о том, что трехосное сжатие является естественным для осадочных пород. Непосредственной причиной их разрушения являются деформации упругого восстановления, упругого последействия и обратной ползучести, возникающие как при так и после проведения выработок и направленные в стороны образованных полостей.
Для подтверждения высказанной гипотезы рассмотрен был травматизм, зарегистрированный на шести шахтах ПО «Снежноеантрацит».
Из общего числа 2051 н/с на долю горнорабочих и проходчиков приходится 1202, т.е. почти 60%. Травматизм от обвалов и обрушений составил 748 случаев – 36% от общего за 5 лет, а на самой глубокой шахте
«Заря» (1200 м) даже 46,8%.
На четырех шахтах из шести («Восход», «Миусская», «Снежнянская» и «Ударник») травматизм от обрушений в среднем за 5 лет составил около 30% (29,4%). На первых двух из них разрабатываются запасы антрацитов, ранее оставленные в целиках. Травматизм при этом за десятилетний период уменьшился на 18% по сравнению с обычной разработкой, но травматизм от обрушений при отработке целиковых запасов возрос в 1,5 раза. Анализ особенностей названных обрушений привел к выводу о том, что их причиной является расслоение песчанистых слоев пород, между которыми залегают глинистые прослои. Расслоение песчанистых слоев происходит со временем под действием деформаций обратной ползучести глинистых прослоев, возникающих и развивающихся вследствие разгрузки последних. Над целиками сформировались за многие годы (десятилетия) дополнительные «очаги» обрушений-расслоений вокруг ранее пройденных подготовительных
231
выработок (уклонов).
Высказанная гипотеза была подтверждена экспериментально и позволила заключить, что такие условия вполне могут быть отнесены к классическим для применения штанговой (анкерной) крепи.
Две особенности характеризуют ее использование.
Во-первых, тот факт, что расслоение пород уже давно произошло, обусловливает применение облегченных конструкций анкерной крепи, ориентированных перпендикулярно слоям песчано-глинистых разностей. Безусловно желательным является наряду с закреплением анкерной крепи по всей длине, подача в шпуры под невысоким давлением скрепляющих растворов, которые будут проникать в массив по ориентированным по напластованию трещинам.
Во-вторых, ранее произошедшее расслоение может обусловить обрушения – отрыв слоев по какой-то ближайшей (ближайшим) трещинам. Очевидно, что в штреках и на их сопряжениях с лавами пластов небольшой мощности (порядка метра) длина анкерной крепи может быть только ограниченной (ориентировочно 2,0 м). Но тогда совсем не исключено, что анкерная крепь может «выйти – закончиться» на одном и том же прослое глинистого сланца, что обусловит обрушение скрепленных ею отдельных песчанистых слоев. Чтоб исключить подобные обрушения, необходимо применение анкерной крепи неодинаковой длины, когда различие будет находиться в пределах 0,3-0,5 м.
Пока нельзя считать доказанной сформулированную гипотезу: именно потому она так и названа. Но простота, очевидная физическая сущность вполне позволяет рекомендовать её не только для практического применения, но и для размышлений будущим специалистам. Одновременно следует отметить, что будущие размышления вполне распространяются и на нынешних специалистов, ибо открывают целое направление разработки и внедрения новых технических решений. Например, расслоения пород кровли пластов происходит как в течение буквально первых нескольких часов (десятков минут) после очередного подвигания забоя, так и в течение нескольких десятков месяцев. Следовательно, оно будет совсем различным по опасности как для призабойной части выработок, так и для выработок уже пройденных, в т.ч. таким, к которым лавы будут приближаться позже или значительно позже при столбовых системах разработки.
2. Травматизм на транспортных средствах и подъёмных установках продолжительное время остается на втором месте и приближается к 20-30%. Из общего числа н/с в 1989 г. почти 76% случаев зарегистрировано на рельсовом транспорте, 13% - не ленточных конвейерах и 11% на подъемных установках. Преобладающее число н/с, связанных с этим видом транспорта, произошло при локомотивной и канатной откатке. Основными причинами
232
травматизма при локомотивной откатке были: - ошибки при управлении электровозами (≈ 19%); - передвижение трудящихся на грузовых транспортных средствах (≈ 14%); - пешее передвижение по шахтным выработкам (11%); - сход с рельсов подвижного состава и последующая постановка его на рельсы (≈ 24%); - удары пострадавших о предметы, загромождающие габариты выработки или пути (≈ 20%). Травматизм при управлениями электровозами наряду с нарушениями трудовой дисциплины и техники безопасности машинистами связан с несовершенством конструкции применяемых на шахтах электровозов АМ-8Д и 2АМ-8Д, вынуждающих высовываться или даже выходить из кабин.
На протяжении горизонтальных выработок к несчастным случаям приводят наезды транспортных средств на передвигающихся людей, травмирование их сошедшими с рельсов вагонетками, электровозами. Все это становится возможным из-за очень высокого и всё увеличивающегося процента выработок, находящихся в неудовлетворительном состоянии (размерам и зазорам).
К основным организационным причинам н/с относятся:
-нарушения принятой технологии перевозки грузов – 18%;
-несовершенство технологии выполнения транспортных работ – 49%;
-невыполнение нормативов содержания рельсовых путей подвижного состава и выработок – 36%.
Кним же, но допущенными горнорабочими, относится управление машинами лицами, не имеющими на это право; превышение количества вагонов, прицепляемых к тяговому канату или электровозу; невыполнение правил безопасной постановки подвижного состава на рельсы; использование для передвижения по выработкам транспортных средств, не предназначенных для перевозки людей.
В целом в обзорах констатируется, что характер технических причин
остается постоянным на протяжении многих лет. Нет необходимости в поиске новых технических решений. Следовательно, необходимо только повышение производственной дисциплины.
На ленточных конвейерах 55% н/с произошло при езде на грузовых конвейерах, при переходе через ленточный конвейер без использования переходных мостиков, а также при выполнении работ людьми, находившимися на ленте конвейера. С выполнением монтажных и ремонтных работ на конвейерах связано 22% НС.
Организационные причины на конвейерном транспорте проявились в 99% н/с – это убедительнейшее доказательство крайней необходимости повышения производственной дисциплины.
3. При эксплуатации выемочных машин более 90% н/с связано с тремя группами причин: - воздействие режущих органов (≈ 40%); - прижатием
233
корпусом комбайна и элементами машин (≈ 35%); - порывами и колебаниями тяговых цепей (около 15%).
При эксплуатации забойных скребковых конвейеров н/с почти в 80% случаев происходили из-за травмирования при доставке материалов и оборудования по ставу конвейера (≈ 35%), срыва и смещения приводных и натяжных головок (≈ 25%), прижатия элементами конвейеров (≈ 20%).
При эксплуатации механизированных крепей большая часть (75%) н/с произошла при прижатии элементами секций, при поломке и ремонте крепей.
Впервые в общей совокупности н/с предложили выделить группу травматизма от непрофессионализма. Она включает случаи травматизма, когда рабочий «оступился, подскользнулся, упал, уронил, при погрузке, при разгрузке, при доставке, при соединении, разъединении» и т.д. и т.п. Смысл термина из-за очевидности в разъяснениях не нуждается. Причина таких случаев заключается в отсутствии профессионального отбора трудящихся и в недостаточной обученности рабочих. Иногда, может быть, в недисциплинированности, небрежности, безответственности. Но, по нашему мнению, такая категория травматизма со временем, после дополнительного осмысливания, осуждения должна приобрести официальный статус в промышленности, частности угольной, ибо будет способствовать снижению производственного травматизма. К более или менее существенным можно отнести две разновидности неоднозначности отнесения несчастных случаев к предложенной группе производственного травматизма. Первая состоит в том, что при повышении уровня механизации, сложности горно-геологических условий, снижения уровня организации охраны труда значимость травматизма от непрофессионализма может возрастать. Это вполне естественно, и выход здесь реальный и простой – лучше отбирать пригодных для работы в угольной (так же как и других) отрасли, лучше их обучать.
Вторая относится к возникающей, нередко кажущейся, неоднозначности решений об отнесении несчастных случаев к этой категории. Например, рабочий травмировал руку, прицепляя секцию КМ-103 к конвейеру. Травма получена не при работе машины или механизма, поэтому и должна относится к группе непрофессионализма. К ней же следует относить некоторые несчастные случаи, происходящие и по другим опасным производственным факторам.
Своеобразным подтверждением сущности и необходимости самого серьезного внимания к травматизму от непрофессионализма является, например, тот факт , что потеря трудоспособности при н/с по этим причинам, например, на ш. «Восход» По «Снежноеантрацит» за 10 последних лет оказалась только в 1,6 раза меньше, чем при травматизме от обрушений, машин и механизмов.
234
4.Вопросы природы формирования выбросоопасности, механизма возникновения и развития вопросов угля, породы и газа; сущности способов прогноза выбросоопасности и способов предотвращения выбросов угля, породы и газа являются, пожалуй, наиболее сложными вопросами горной науки. Именно поэтому их изучение, рассмотрение излагаются в отдельных, специальных публикациях, перечень последних из которых был приведен в главе 3. Считая вполне уместным его повторение, приводим две публикации
[1,2].
5.Основными причинами образования опасных концентраций метана в горных выработках были нарушения нормального режима проветривания, в том числе с учетом накопления метана в выработанном пространстве (6575%); невыполнение мероприятий, предусмотренных для предотвращения местных скоплений метана: купола, пустоты за крепью, пространство между корпусом комбайна и забоем (около 20%).
Однако надо всегда помнить, что взрывы невозможны при отсутствии источников воспламенения. Основными источниками воспламенения метана, взрывов метана и пыли было электрооборудование, взрывные работы, фрикционное искрение.
При несчастных случаях, связанных с удушьем, смерть наступает от недостатка кислорода во вдыхаемом воздухе вследствие замещения его метаном. Все такие случаи явились следствием организационных причин, в числе которых и передвижение в загазированных выработках без предварительного замера содержания метана в рудничной атмосфере.
Основные требования к проветриванию подземных выработок и пылегазовому режиму содержатся в ПБ, описаны в учебниках по рудничной аэрологии, в том числе приведенном в главе 3.
6.Количество несчастных случаев с ВМ при ведении взрывных работ и обращении длительное время держится в отрасли примерно на одном уровне
–2,0-2,2%.
Изучение организационных причин травматизма показывает, что основную долю среди них занимает нахождение посторонних лиц и лиц, проводящих взрывные работы, в опасной зоне. Это свидетельствует о том, что взрывные работы в ряде случаев в нарушение требований «Единых правил безопасности при взрывных работах» ведутся без удаления лиц, не связанных со взрывными работами, из опасной зоны, без выставления или неправильного выставления постов охраны и предупредительных знаков, а также при нахождении мастеров-взрывников и лиц сменного технического надзора, присутствующих при взрывных работах, на расстояниях от взрываемого забоя менее, чем это предусмотрено нормативными документами. Последнее подтверждается тем, что среди пострадавших около 30% мастеров-взрывников, ИТР и горных мастеров.
235
В числе организационных причин находится заряжание шпуров без применения забойки; отсутствие водораспылительных завес при ведении взрывных работ, особенно в тупиковых забоях; выдача мастерам – взрывникам невыполнимых нарядов на смену.
Вторая группа причин травматизма связана с техническими средствами выполнения взрывных работ. Травматизм по этой группе причин обусловлен высокой чувствительностью электродетонаторов к механическим воздействиям, их недостаточной безотказностью. Вследствие этого травматизм от перебуривания и механического воздействия на заряды в отдельные периоды времени превышает 20%.
На травматизм от механического воздействия на отказавшие заряды влияет в основном качество применяемых электродетонаторов.
Рекомендации комиссий, расследовавших соответствующие аварии, содержат в частности, необходимость применять резцы и коронки для бурения шпуров диаметром большим, чем диаметр применяемых патронов ВВ не менее чем на 5 мм при бурении по углю и не менее 3 мм при бурении по породе. Обращается особое внимание на использование всех нормативных способов для обнаружения и ликвидации отказов зарядов ВВ, о которых студентам известно из ранее прочитанных дисциплин.
7. Количество пострадавших от электротока в подземных выработках шахт отрасли находится примерно на одном уровне на протяжении последних
20 лет.
Установлено, что все случаи поражения электрическим током в сетях 660 В происходили при преднамеренно выведенной из строя защиты от токов утечки (реле утечки). Таким образом, отключение реле утечки и продолжительная работа шахтных сетей без защиты, как и в прошлые годы, продолжают иметь место, чем создаются опасные условия труда для горнорабочих.
Подавляющее число электротравм (более 90%) на предприятиях отрасли произошло при прикосновении к токоведущим частям, находящимся под напряжением, остальные – при прикосновении к корпусам электрооборудования, оказавшимся под напряжением из-за повреждения изоляции. Электротравмы по организационным причинам, как и в предыдущие годы, значительно преобладают над электротравмами по техническим причинам. Наибольшую повторяемость имеют следующие организационные причины:
несоблюдение мероприятий безопасности при работе в электроустановках;
нарушение средств защиты от поражения электрическим током; умышленное отключение аппарата защиты от поражения электрическим
током.
236
Таким образом, основными причинами электротравматизма в отрасли остаются причины организационного порядка, главными из которых являются нарушения установленного порядка производства работ в электроустановках, несоблюдение мероприятий безопасности, недостаточный технический надзор и нарушение средств защиты от поражения электрическим током.
8. В общем перечне (табл. 4.А1) ОПФ не содержатся подземные пожары. Последние занимают особое место не столько по травматизму, сколько по громадному материальному ущербу, к которому они приводят. Вопросы эти будут излагаться особо, в 4.А4.
4.А2. Минимальное число несчастных случаев, достаточное для достоверного анализа травматизма.
Известно, что на каждой шахте, в производственном объединении по добыче угля, отрасли в целом число несчастных случаев ото дня ко дню изменяется совершенно незакономерно.
В теории вероятности есть общие решения, направленные на определение такого объема выборки, который обеспечивает минимальную величину ошибки. Но в ветви горной науки, относящейся к охране труда и требующей первоочередного решения, находятся, например, задачи определенного общего числа н/с, необходимого для достоверной оценки изменения их числа в течение года, отдельных месяцев, или изменения травматизма по определенному опасному производственному фактору в какой-либо ограниченный период времени и т.п. Конкретных численных решений для названных и им подобных задач пока нет, поэтому предлагается следующий методический прием решения задач названного типа.
На первом этапе подсчитывается общий, подземный травматизм за последние 10 лет и сравнивается между собой травматизм за первые и вторые 5 лет. Если он различается не более чем на 10%, в дальнейшем все расчеты ведутся для последнего периода времени. Теперь для каждого из пяти последних лет рассчитываются ежемесячные отклонения от среднегодового числа н/с - ∆Х, %.
Точность измерений в горном деле различными специалистами без каких-либо строгих обоснований принимается самая разная: от 15 до 25-30%. Считаем вполне допустимым при решении задач, относящихся к безопасности труда, выбрать – остановиться на 20% точности определений.
Сначала расчеты выполняются для ежемесячных отклонений от среднегодовых и устанавливается для каждого года максимальное (±) отклонение, ∆Xmax , %. Затем такие же расчеты производятся для отклонений
средних двух и трехмесячных значений от среднегодовых и таких же отклонений от среднегодового их числа за 2,3 – 5 лет. Тот период времени.
237

Для которого отклонение числа н/с от среднегодового не превышало 20%, принимается за базовый. Он понимается как период времени, в течение которого произошло такое число н/с, которое может рассматриваться как достаточное, Nд , для надёжного (представительного) анализа изменений
травматизма по конкретной задаче. Из сказанного следует, что за методическую основу решения задачи принят период времени, но только потому, что он позволяет переходить к численному значению, основанному на количестве н/с, происходящих ежемесячно в годовые отрезки времени.
В теории вероятностей при оценке численности собственно случайной выборки (И.Г. Венецкий, Г.С. Кильдышев. Теория вероятностей и математическая статистика. – М.: Статистка 1975. – 264 с.) считают возможным использование величины коэффициента вариации, рассчитываемого по формуле
V = |
δ |
100 % , |
(4.А3) |
|
X |
||||
|
|
|
|
Σ(X - |
|
)2 |
|
|
где δ = |
X |
и n - число измерений. |
|||
n |
|||||
|
|
Если V < 10%, то это указывает на слабую колеблемость признака, от 10 до 20% - на значительную колеблемость и выше 20% - на сильную колеблемость. Учитывая фактическую высокую изменчивость число н/с на шахтах, при обосновании их числа, необходимого для достоверного анализа, одновременно с расчетом максимальных отклонений оценивали по (4.А2) величины коэффициентов вариации.
Понятно, что предпочтительными являются случаи, когда V ≤ 10%. Но следует учитывать реальность фактов двух разновидностей. Во-первых, весьма существенный разброс данных, даже если рассматривать месячные изменения числа н/с. Во-вторых, значительную колеблемость фактических (экспериментальных) данных по теории вероятностей, который характеризуется широким диапазоном изменения коэффициентов вариации: 10 – 20%. Если ограничиться диапазоном 10 – 15%, можно рассчитывать на вполне приемлемую колеблемость, находящуюся между слабой и значительной.
Результаты расчетов, выполненных для шахты «Восход» ПО «Снежноеантрацит», доказывают методическую обоснованность подхода к решению обсуждаемой задачи по двум положениям.
1. Хорошо подтверждается справедливость одного из основных положений теории вероятностей, заключающееся в том, что увеличение объема случайной статистической выборки приводит к увеличению ее надежности – представительности. Средний коэффициент вариации максимальных отклонений от среднегодовых в выборках по 3 месяца за 5 лет
238
(28,2%) по сравнению с выборками по одному месяцу за эти же годы (67,8%) уменьшился в 2,4 раза.
2. Для четырех лет из пяти ∆Xmax при трехмесячной выборке не
превосходил 20%. Среднемесячное значение н/с пятилетнего периода времени для этой выборки изменялось от 6,3 до 11,1 в среднем составило 8,2 и вполне может быть округлено до 8,0.
Учитывая то положение, что средняя статистическая величина всегда является наиболее надежной из всей совокупности, она и принимается в качестве базисной.
В дальнейшем те же величины рассчитывались для средних значений н/с за 1,2 и 3 месяца за 2 года (1998-1997 г.г.), три года (1998-1996 г.г.)…пять лет (1998-1994 г.г.). Среднемесячное значение н/с изменялось от 7,2 до 8,4, в среднем составило 7,8, т.е. вновь те же самые 8,0.
Средние абсолютные значения величин коэффициентной вариации максимальных отклонений от среднегодовых в выборках по 1,2 и 3 месяца уменьшились примерно в 1,5 раза и при этом подтвердилась уже обнаруженная тенденция уменьшения коэф. вариации при увеличении выборки от 1 мес. (44,5%) до трех месяцев (17,9%), т.е. вновь уменьшение весьма существенное: в 2,5 раза.
При выборках, соответствующих трехмесячным, округлению н/с за 4 года соответствовал уже V = 13,0%, а за пятилетний суммарный период времени всего V = 6,7%.
По изложенной методике был рассмотрен травматизм за последние 5 лет на всех шахтах ПО «Снежноеантрацит»: «Восход», «Заря», «Миусская», «Северная», «Снежнянская» и «Ударник».
Анализ результатов расчетов приводит к заключению, что при рассмотрении месячных выборок в двух случаях из пяти имело место ∆Xmax > 20% (1996 и 1997 г.г.). Следовательно, месячное число н/с может
приниматься в качестве базисного. Но таких месячных выборок три (1994, 1995 и 1998 г.г.), а ежемесячное число н/с неодинаково: 37,2; 37,6 и 34,3. Очевидно, что для повышения надежности анализа должно быть принято среднее из трех число н/с, т.е. 36.
Допустимость и надежность использования месячной выборки, вопервых, вполне доказывает тот факт, что рассчитанные коэф. вариации за различные по продолжительности периоды времени (от двух до пяти лет) во всех случаях были менее 15% и средний он составил 13,1%. Во-вторых, это позволяет сравнить травматизм завершившегося месяца с аналогичным месяцем предыдущего года, с предыдущим месяцем этого года и т.п. Результаты сопоставления, выполненного для каждого из месяцев всех пяти лет в целом по всем шахтам производственного объединения (360 шахтомесяцев), позволяют утверждать, что прогнозирование числа
239

несчастных случаев на следующий месяц, а тем более квартал, полугодие, не сопровождается ошибками, превышающими ± 15%. Следовательно, такой прогноз может быть отнесен к достаточно надежным. Но одновременно необходимо отметить и подчеркнуть, что прогноз не может относиться к взрывам метановоздушной смеси по двум причинам:
- их нет в перечне аварий за пять лет; - прогноз взрывов метановоздушной смеси в шахтах – это вопрос особый, решение которого возможно только при выполнении специального, очень непростого исследования.
Однако вполне удовлетворительное применение методики для анализа травматизма на шахтах ПО «Снежноеантрацит» может быть следствием совпадения базисного числа н/с с месячным. Очевидно поэтому, что методику выбора числа несчастных случаев, необходимого для достоверного анализа, следует совершенствовать. Необходимость уточнения в первую очередь обусловливается тем, что как бы помесячная оценка базисного числа н/с является по существу дискретной и потому может привести к значительному её завышению. Покажем это, в частности, на конкретном примере приведенного обоснования принятия в качестве базисной месячного числа н/с. Предположим (что в общем случае совсем не исключено) приемлемым окажется число н/с не в месячной, а двухмесячной выборке, т.е. уже 72, что почти в 2 раза больше.
Такой резкий неоправданный рост н/с в базисной выборке недопустим, поэтому расчет должен уточняться следующим образом.
На рис. 4.А2 представлены построенные по данным о травматизме на шахтах
240
ПО «Снежноеантрацит» зависимости ∆Xmax , V, числа несчастных случаев N
от исходной временной выборки (месячной – I, двухмесячной – II …). Теперь методика уточненного использования выбора числа н/с сводится к следующему поэтапному расчету.
На первом этапе, как и прежде, рассчитываются ∆Xmax и V для
месячных, двух- и трехмесячных периодов времени, анализируется возможность выбора в качестве базисного месячного числа н/с. Если она подтверждается, расчет на этом заканчивается, а если нет, переходят к выполнению исследования второго этапа.
Строятся зависимости аналогичные 1 и 3 (рис. 4.А2.) и по ним при условии, что ∆Xmax < 20% не менее чем в трех случаях из пяти, а V ≤ 15% для любых нескольких лет выбирается число н/с в интервале между одним и двумя месяцами. Не исключаем возможность и того, что это будут II и III месяцы.
4.А3. Запыленность атмосферы и профессиональные заболевания.
Практически все технологические процессы не только в угольной промышленности, в других отраслях народного хозяйства, связанных с дроблением твердого сырьевого материала или обработкой твердых материалов (производство цемента, обработка гипса, приготовление топлива, добыча и обработка камней, деревообработка, металлообработка и т.п.), сопровождаются образованием пыли. Под пылью понимается совокупность тонкодисперсных твердых частиц органического, минерального или технологического происхождения. По своим свойствам она относится к коллоидным системам. Согласно учению о коллоидах система, где одно из веществ раздроблено и распределено в виде более или менее мелких частиц внутри другого вещества, имеющего непрерывное строение, называется дисперсной. Раздробленное вещество называют дисперсной фазой системы, а вещество, имеющее непрерывное строение, - дисперсионной средой. Следовательно, если перенести эти понятия на пыль, пылинки являются дисперсной фазой системы, а воздух, в котором они находятся, дисперсионной средой. Если дисперсная фаза представлена частицами размером 10-7 – 10-9 м, они называются золем. Если дисперсионной средой является воздух, то такая система называется аэрозолем. Аэрозолем являются пыль, туман, дым.
Однако в практике этим термином называют и более грубодисперсные системы, в которых могут некоторое время находиться во взвешенном состоянии твердые частицы размером от 10-5 до 10-7 м. Частицы размером более 10-5 м выпадают из воздуха. Пыль, осевшая на поверхностях, называется аэрогелем.
В различных отраслях промышленности приняты разные подходы к
241
разделению твердых частиц по крупности. Наиболее простым по физическому смыслу и соответствующим выпадению твердых частиц из воздуха является отнесение их к размерам до и после 10-5 м.
Наличие пыли в воздухе характеризуется ее концентрацией, которую в зависимости от методов измерения запыленности делят на 3 вида: - массовая: мг (г) пыли на единицу объема воздуха (м3); - счетная: количество твердых частиц (шт) на единицу объема воздуха (м3) и объемная: объем пыли (м3) на единицу объема воздуха (м3). Почти исключительно применяемой на практике является первая – мг/м3.
В зависимости от местоположения технологического оборудования у объектов пылеобразования (в целом, пылевыделение) пылевой аэрозоль может образовываться как внутри производственных помещений (в выработках шахт), так и находиться за их пределами ( на прилегающих территориях).
Существенное значение при оценке свойств пыли (пожароопасности, силикозоопасности и т.п.) имеет значение ее дисперсный состав, т.е. количественное соотношение частиц различной крупности. Пыль, образующаяся в промышленных условиях, полидисперсна, т.е. размеры ее частиц колеблются в широких пределах.
За 10-летний период с 1985 по 1995 год уровень профзаболеваемости возрос примерно в 10 раз. В 1995 году темпы роста замедлились и показатель прироста составил 1,2 раза. В 1996 году профессиональная заболеваемость снизилась в 1,8 раза по сравнению с 1995 годом, в 1997 году профессиональная заболеваемость в области сохраняется на уровне 1996 года. Областной показатель на 1000 осмотренных составил в 1995 – 6.3, в 1996 – 3.6, в 1997 – 3.5. Профессиональная заболеваемость в угольной промышленности в 1996 году составила 6.7 на 1000 осмотренных, что почти в 2 раза ниже показателя 1995 года (13.0), в 1997 – 6.1.
За период с 1994 года по 1997 год по области отмечается уменьшение направленных в клинику пациентов (с 54 до 26 тысяч человек) и лиц с впервые установленными профессиональными заболеваниями (с 4337 до
1403).
Число рабочих с впервые установленными профессиональными заболеваниями значительно превышает число служащих и ИТР с таковыми. Соотношение между рабочими и пенсионерами по возрасту, длительно неработающими на момент признания профзаболевания, составляет примерно 3:1 за анализируемый период.
При общем снижении профессиональной заболеваемости в области наиболее высокий ее уровень, превышающий как областные так и отраслевые показатели, сохраняется в городах Горловка, Селидово, Красноармейск, Шахтерск, Донецк. Удельный вес профзаболеваний, впервые
242
установленных работникам угольной промышленности, составляет 93%.
В структуре профзаболеваний ведущее место занимают болезни органов дыхания: пневмокониоз – 35,5% и хронический бронхит – 24,4%. на третьем месте хронический пояснично-крестцовый радикулит – 15,8%, на четвертом – вибрационная болезнь (14,5%).
Периодические медицинские осмотры шахтеров осуществляются в соответствии с Приказом №45 министерства здравоохранения Украины от 21.03.94 г. Они проводятся на базе лечебно-профилактических учреждений врачебными бригадами и по обращаемости.
Сущность воздействия пыли как источника профессиональной вредности на организм человека в несколько упрощенной с точки зрения медицинской редакции может быть представлена следующим образом.
Различают два вида дыхания, под которым понимается усвоение кислорода всеми клетками организма и выделение из них углекислоты как результата окислительных процессов: внешнее (легочное) и внутреннее (тканевое).
Признаки совершенно специфичной болезни легких, получившей название пневмокониоз, обнаружили еще при исследовании мумий, извлеченных из египетских пирамид. Основоположники промышленной гигиены Агрикола (XVI век) и Ромаццини (XVII век), исследовавшие заболевание, вызванное вдыханием запыленным воздухом, назвали его (как и М. Ломоносов в России) горной болезнью.
Так что такое, всё-таки, пневмокониоз? Пневмокониоз (от греч. пневмон – легкие и конио – пыль) – это группа заболеваний легких, относящихся к профессиональным болезням. Термин впервые был предложен в 1866 г. немецким врачом Ценкером. Известно, что пыль может вызывать глазные, кожные заболевания, болезни верхних дыхательных путей и легких. Особое в этом перечне место занимают ядовитые пыли. Но среди них особое место занимают пневмокониозы, к числу которых относятся силикозы, антракозы (от греч. антрак – уголь), абестозы, цементозы, табакозы и т.п.
Дыхательная поверхность легких составляет в среднем примерно 50 м2. Процесс потребления кислорода в них осуществляется многочисленными альвеолами, площадь поверхности каждой из которых составляет около 0,3 мм2, т.е. их в легких около 200 млн. Альвеола (лат.) – это своеобразный желобок, выемка: как бы пузырек в легких на разветвлениях бронхов, обвитый сетью капилляров.
Пока нет общепринятой классификации пыли по крупности в связи с вредностью пыли. Но установлено, что пыль размером более 10 мкм (10-6 м) практически задерживается в носоглотке, размером менее 5 мкм поступает в легкие, из которых 0,4-2 мкм особенно опасны.
243
В легких есть своеобразные санитары – фагоциты (буквально: пожирающая клетка), которые как бы обволакивают, захватывают пылевые частички и по лимфатическим каналам выносят эти пылинки. При значительной запыленности фагоциты не «справляются с работой», часть из них погибает, а пылинки остаются в легких. Скопление пыли приводит к развитию пылевого фиброза (буквально: волокнообразованию). Происходит замещение (омертвление) альвеол и легочной ткани, делающее попадание кислорода в кровь не только затруднительным, но и невозможным. Наиболее опасной формой пневмокониоза является силикоз, развивающийся при наличии в пыли свободной двуокиси кремния.
Но вместе с тем Донецкий НИИ гигиены труда и профзаболеваний, изучавший зависимость патогенного действия угля на легкие в зависимости от минералогического, дисперсного состава угля и степени метаморфизма, пришел к новому и несколько неожиданному результату, отличающемуся от общепринятого. Оказалось, что наибольшая связь частоты заболеваний пневмокониозом (примерно 70%) имеет место с выходом летучих веществ угля (Vdax , %), а не с содержанием свободной двуокиси кремния или зольности.
Различают период дорентгеновского развития пневмокониоза, когда признаки фиброза не обнаруживаются, и период его проявления. В первый период, характеризующийся катаральным бронхитом с появлением микрофлоры, заболевание имеет обратимый характер. Но сам пневмокониоз неизлечим, поэтому первостепенное значение имеет его профилактика, в том числе периодические медикосанитарные осмотры.. Наблюдательные, достаточно опытные рентгенологи при наличии нескольких снимков вполне могут во временной динамике обнаружить (предположить) первый период заболевания.
Мероприятия по предупреждению заболеваний пневмокониозом разделяются на 3 группы. I. Инженерно-технические: - предупреждение пылеобразования; - пылеподавление; - изоляция образующейся пыли; - удаление пыли. II. Медикосанитарные: - периодические осмотры; - электроаэрозольная терапия. III. Социально-правовые: сокращение продолжительности работы в запыленных условиях; - дополнительные отпуска; - специальное питание; - введение норм на запыленность воздуха. Содержание угольно-породной пыли в составе которой свободного кремнезема от 10 до 70%, - 2 мг/м3, а если менее 2% - 10 мг/м3.
4.А3.1. Горючие и взрывчатые свойства пылевых смесей.
Большую опасность в отношении горения, взрыва и разрушений представляет пыль, находящаяся в воздухе. В соответствии с ранее сказанным в дальнейшем будет подразумеваться пыль в состоянии аэрозоля.
244
Химическая реакция между газом и твердым веществом протекает на поверхности последнего. Скорость такой реакции зависит от величины поверхности соприкосновения реагирующих веществ. В зависимости от величины линейной скорости распространения реакции в том или ином объеме различают горение (скорость не более 10 м/с), дефлаграцию (скорость не превышает скорости звука) и взрыв (скорость равна или больше скорости звука). Особенность горения состоит в том, что условия, необходимые для быстрого протекания реакции, созданы ею самой. Эти условия заключаются либо в высокой температуре, либо в высокой концентрации активных продуктов, ускоряющих (катализирующих) реакцию. Для воспламенения пыли необходимы два условия: достаточное количество кислорода и нагрев частиц горючих веществ до определенной температуры.
Различают два режима протекания реакции: диффузионный (скорость реакции определяется молекулярной или турбулентной диффузией исходных компонентов) и кинетической (скорость процесса горения определяется скоростью протекания химической реакции). Определение режима протекания реакции обязательно при решении задачи взрывчатости пыли. С учетом фазового состояния горючего вещества и окислителя различают 3 вида горения:
- горение газообразных горючих (система газ-газ) – гомогенное горение; - горение твердых и жидких горючих (система твердое тело – газ или жидкость – газ) – гетерогенное горение; - горение взрывчатых веществ (конденсированная система).
На взрывчатость угольной, серной, сульфидной и др. пыли влияет ее химический состав; дисперсность (сила взрыва достигает максимума чаще всего при крупности (диаметре) пылинок менее 10-5 – 10-6 м; влажность пыли: чем она больше, тем ниже вероятность взрыва, который при некоторых значениях влажности становится невозможным. Роль влаги двояка: во-первых, она способствует коагуляции мелких частиц в более крупные, во-вторых, происходит уменьшение теплового баланса.
Существенное влияние на степень взрывчатости пыли оказывает состав атмосферы, в которой происходит взрыв. Наличие в ней органических частиц, катализаторов и т.п. способствует как взрывчатости, так и мощности взрыва.
Согласно тепловой теории взрыв пыли можно представить следующим образом. За счет тепла источника воспламенения пылинки нагреваются и при этом выделяются взрывчатые продукты нагрева, образующие вокруг пылинок газовую оболочку. Как только концентрация газов в этой оболочке достигнет взрывоопасных значений, происходит ее воспламенение. Тепловой импульс от горящих частиц за счет излучения и теплопроводности
245
передается к негорящим, которые воспламеняются и являются источником воспламенения для следующих. При этом происходит увеличение температуры за счет того, что выделяющееся при реакции окисления тепло не успевает отводиться в окружающую среду. Это вызывает ускорение течения реакции и создает условия для развития быстрого лавинообразного процесса горения, т.е. взрыва.
В бывшем СССР традиционно в течение многих лет (десятилетия) взрывчатость пыли изучалась в курсах вентиляции (аэрологии), а пыль как профессиональная вредность – в курсах охраны труда. Такое разделение не являлось результатом анализа методических особенностей преподавания названных курсов. Считая его ошибочным, рассчитываем на ликвидацию разделения в будущем, но пока рекомендуем студентам при изучении этих вопросов обращаться к уже называвшемуся в главе 3 учебнику К.З. Ушакова
[3].
4.А4. Предупреждение и ликвидация пожаров в угольных шахтах.
4.А4.1. Понятие о подземном пожаре и места их возникновения.
Поземный пожар – это пожар, возникающий непосредственно в горных выработках и в массиве полезного ископаемого.
Признаками подземного пожара являются появление в горных выработках шахт открытого огня, раскаленного угля, дыма, запаха гари или продуктов возгонки угля, объемной доли водорода 0,1% и выше, оксида углерода свыше 0,0017%; повышения температуры воздушного потока, боковых пород и воды. К подземным пожарам относятся также случаи горения в устьях стволов, шурфах и штольнях, надшахтных зданиях и сооружениях, если продукты горения или огонь проникают в шахту при нормальном или реверсивном вентиляционном режиме.
Пожары в шахте возникают и развиваются при совместной реализации трех обязательных условий: наличии горючего материала, возникновении теплового импульса и способности окружающей среды поддерживать горение. По тепловому импульсу пожары подразделяются на экзогенные и эндогенные. Экзогенными называются пожары, возникшие от внешнего источника теплоты, а эндогенными - от самовозгорания угля в результате окислительных процессов в полезном ископаемом.
Степень развития пожара экзогенного происхождения может быть охарактеризована следующими стадиями:
зарождение , скрытое развитие и разгорание, которые характеризуются нарастанием количества сгорающего в единицу времени материала и расхода кислорода воздуха на горение;
развившийся пожар, когда практически полностью расходуется
246
кислород на горение и при постоянном расходе воздуха сгорает постоянное количество горючего материала;
затухание, которое характеризуется нарастанием в продуктах горения концентрации кислорода и снижением концентрации углеродосодержащих газов.
В развитии эндогенного пожара различают следующие стадии: самонагревание угля протекает в интервале температур от 20…50 °С до
критической 70…140 °С. Продолжительность данной стадии определяется инкубационным периодом самонагревания угля;
ранняя стадия самовозгорания угля характеризуется интервалом температур от критической до температуры воспламенения летучих веществ (для каменного угля 300 – 350 °С, тощих углей 650 – 800 °С);
стадия горения угля характеризуется температурой, превышающей температуру воспламенения летучих веществ.
Самовозгорание угля происходит при определенном притоке воздуха к угольному скоплению, который равен 0,1 – 0,9 м3/мин на 1 м 2 площади поперечного сечения выработанного пространства. При меньшем значении расхода воздуха его недостаточно для развития процесса окисления угля, а при большем – происходит вынос за счет конвекции образовавшейся теплоты. Наиболее пожароопасны утечки воздуха 0,3 – 0,4 м3/мин на 1 м 2. При доле кислорода в воздухе менее 12% процесс окисления угля настолько замедляется, что самонагревание угля не происходит.
Все угольные шахты содержат в большем или меньшем количестве различные горючие материалы, которые могут явится объектом пожара в результате неправильного или небрежного ведения горных работ.
В подземных выработках горение даже сравнительно незначительных количеств какого-либо вещества (уголь, древесина, конвейерная лента и т.д.) может привести к гибели людей. Кроме того, современные угольные шахты являются опасными по метану и поэтому каждый пожар при определенных условиях может привести к взрыву метановоздушной смеси.
Наиболее сложны в ликвидации и приносят значительные материальные убытки пожары в выработанных пространствах действующих и отработанных участков. Зачастую эти пожары связаны с самовозгоранием угля. Повышенной возгораемостью обладают бурые, газовые и длиннопламенные угли. В меньшей степени – угли средних стадий метаморфизма (коксующие и жирные).
Более трети пожаров связано с горением оболочек кабелей и электрических машин. Каждый пятый пожар вызван горением конвейерной ленты. Необходимо упомянуть также о таких объектах пожара, как обтирочные материалы, спецодежда (особенно старая промасленная) и различные отбросы в горных выработках.
247
Как возможные объекты пожара весьма опасны метан и угольная пыль, особенно в смеси с резиновой крошкой и минеральным маслом.
Крепежный лес – наиболее распространенный горючий материал в горных выработках. При определенных условиях крепь горит независимо от того, в каком она состоянии: сухая или мокрая, старая, сломанная и расщепленная от действия горного давления (костры и клети, настилы, затяжки и пр.) или неповрежденная (стойки, верхняки, распорки). Крепь горит в горных выработках, в закрепном и выработанном пространствах.
Легковоспламеняющимся материалом, способствующим возникновению или распространению пожара, могут быть различные виды жидкого горючего и минеральных масел, в особенности, если они хранятся в выработках без соблюдения необходимых мер предосторожности.
Известны случаи, когда пожары возникают при ведении взрывных работ вследствие выгорания зарядов взрывчатых веществ, воспламенения метана и угольной пыли.
Объектами горения неоднократно были: штабели угля, отвалы пустых пород с примесью углистых сланцев угля, лесные склады, постройки низкой степени огнестойкости, различные материалы и сооружения на поверхности, способные воспламеняться. Возникнув на поверхности, пожар или продукты горения проникают в подземные выработки и распространяются по ним.
При несоблюдении необходимых мер безопасности на любом участке шахты существует угроза пожара. Важно знать, какие места чаще всего подвержены пожарам, чтобы особенно тщательно наблюдать за ними.
Статистические данные говорят о том, что места возникновения пожаров эндогенного и экзогенного происхождения различны. Так, более половины эндогенных пожаров произошло в выработанном пространстве действующих и отработанных очистных забоев (табл.4.А3). Четвертая часть пожаров связана с самовозгоранием угля за крепью горных выработок. В последние годы значительно уменьшилось количество эндогенных пожаров в охранных и барьерных целиках, так как охранные целики для поддержания горных выработок на пластах самовозгорающегося угля, как правило, не оставляют.
Большая часть пожаров экзогенного происхождения сосредоточена в горизонтальных горных выработках (табл.4.А4). Несколько меньше пожаров возникает в наклонных выработках. От 6 до 10% пожаров происходит в тупиковых горных выработках, очистных забоях, камерах и на объектах поверхности.
248
Места возникновения эндогенных пожаров. |
Таблица 4.А3. |
||
|
|
|
|
Место |
|
% |
|
Выработанное пространство: |
|
|
|
действующего очистного забоя |
|
26,5 |
|
отработанного очистного забоя |
|
26,0 |
|
Угольные охранные целики |
|
3,5 |
|
За крепью горных выработок: |
|
|
|
магистральных и участковых |
|
16,2 |
|
тупиковых |
|
8,7 |
|
Прочие |
|
19,1 |
|
Места возникновения экзогенных пожаров. |
Таблица 4.А4. |
||
|
|
|
|
Место |
|
% |
|
Вертикальные выработки |
|
3,1 |
|
Горизонтальные выработки |
|
33,2 |
|
Наклонные выработки |
|
28,9 |
|
Тупиковые выработки |
|
6,0 |
|
Очистные забои |
|
6,8 |
|
Камеры |
|
8,5 |
|
Объекты на поверхности шахт |
|
9,1 |
|
Прочие |
|
4,4 |
4.А4.2. Причины пожаров.
Изучение причин подземных пожаров позволяет установить определенную их зависимость от геологических условий залегания пластов и физико-химического состава углей, методов ведения горных работ и от применяемых при разработке материалов и оборудования. Однако полное выявление этих причин весьма сложно, и пожары, причины которых не установлены, составляют около 20%.
Каждый четвертый пожар вызван самовозгоранием угля. Основными причинами эндогенных пожаров (табл.4.А5) являются оставление угля в зонах геологических нарушений, барьерных целиках, при неполной выемке мощности, в местах завалов и газодинамических явлений. Развитию процессов самовозгорания способствуют утечки воздуха. Они обусловлены некачественной или несвоевременной изоляцией отработанных участков, выработанных пространств действующих участков и невыполнением мероприятий по профилактике самовозгорания угля в барьерных целиках, зонах геологических нарушений и газодинамических явлений.
249
Причины возникновения эндогенных пожаров. |
Таблица 4.А5. |
|
|
|
|
П р и ч и н а |
|
% |
Оставление угля: |
|
|
охранные, барьерные целики |
|
15,1 |
зоны геологических нарушений |
|
27,7 |
неполная выемка по мощности |
|
38,7 |
прочие места |
|
18,5 |
Утечки воздуха: |
|
|
несвоевременная изоляция отработанного участка |
|
11,6 |
некачественная изоляция отработанного участка |
|
23,7 |
некачественная или несвоевременная изоляция действующего |
|
|
забоя |
|
31,8 |
невыполнение намеченных мероприятий в зоне |
|
|
геологического |
|
12,7 |
нарушения |
|
20,2 |
прочие |
|
|
Причиной около 40 % пожаров экзогенного происхождения (табл.4.А6) является короткое замыкание в электрических сетях. Происходит оно вследствие перегрузки, уменьшения сопротивления изоляции обмоток из-за попадания воды или масла под изоляцию кабеля, механических повреждений его, нарушения теплового режима эксплуатации оборудования (заштыбовка конвейеров, отсутствие крыльчатки вентилятора обдува двигателя и т.д.).
Загорание в пусковом оборудовании, контролирующих аппаратах и приспособлениях возникает при их эксплуатации с нарушенной защитой, при неудовлетворительном состоянии контактной группы, нарушении взрывозащищенности корпуса.
Причины возникновения экзогенных пожаров. |
Таблица.4.А6. |
|
|
|
|
П р и ч и н а |
|
% |
Короткое замыкание в электрических сетях |
|
36,7 |
Трение: |
|
|
конвейерных лент |
|
20,8 |
исполнительных органов машины |
|
5,4 |
других объектов |
|
7,1 |
Нарушение правил безопасности при ведении: |
|
|
взрывных работ |
|
6,2 |
огневых работ |
|
3,3 |
Не установлена |
|
20,5 |
Более 30% пожаров вызвано трением канатов о шпалы и элементы крепи, конвейерных лент о приводные и натяжные барабаны, неисправные
250
ролики, а также исполнительных органов машин и механизмов.
Особую опасность представляют пожары, связанные с нарушением правил безопасности при ведении взрывных и огневых работ. Примером может служить одна из крупнейших катастроф на шахтах Украины. Она произошла на шахте им. Н.П. Баракова в Краснодоне, где при ведении огневых работ с грубыми нарушениями правил безопасности произошло загорание редуктора на баллоне с кислородом, что в дальнейшем привело к взрыву пылевоздушной смеси и послужило причиной многочисленных человеческих жертв.
Отсюда следует, что эксплуатация современных энергонасыщенных угольных шахт требует самого тщательного и добросовестного выполнения всех противопожарных правил установки и обслуживания всего комплекса выемочных, подготовительных транспортных машин и механизмов.
4.А4.3. Предупреждение подземных пожаров, способы и средства тушения.
Комплекс мероприятий, направленных на предупреждение пожаров и ограничение их размеров, называется пожарной профилактикой.
Задачи пожарно-профилактических мероприятий разнообразны, но в основном заключаются в следующем.
1.Мероприятия, устраняющие непосредственные или возможные причины пожаров. Эти мероприятия в свою очередь могут быть подразделены на группы:
воздействие на технологический процесс в целях пожарной безопасности (применение наиболее безопасных в пожарном отношении систем разработки, полнота выемки угля и т.д.);
мероприятия технического характера (например, правильный монтаж электрооборудования, применение исправных машин и механизмов);
мероприятия организационного порядка (соблюдение правил пожарной безопасности при ведении взрывных и огневых работ, транспортирование и хранение горючих веществ и т.д.).
2.Мероприятия, ограничивающие распространение возникшего пожара, - применение несгораемых и трудносгораемых конструкций, материалов и веществ, пожарных перемычек, несгораемых дверей и ляд и т.д.
3.Мероприятия, обеспечивающие успешную эвакуацию людей из застигнутых пожаром горных выработок, - создание необходимого количества запасных выходов из любой горной выработки, их рациональное расположение и устройство, снабжение работающих самоспасателями и т.п.
4.Мероприятия, обеспечивающие быстрое и своевременное развёртывание тактических действий горноспасательных и вспомогательных
251
команд при тушении пожаров, - создание специальных проходов к труднодоступным местам, оборудование пожарных складов, содержание в исправном состоянии пожарного трубопровода, заполненного водой с заданными параметрами, и пр.
Тушение подземных пожаров производится следующими основными способами:
непосредственным воздействием на очаг пожара огнетушащими средствами (активный способ);
изоляцией пожарного участка от действующих выработок специальными изолирующими сооружениями (перемычками, рубашками и др.);
комбинированным способом (например, локализация очага пожара в результате временной изоляции пожарного участка с последующим воздействием на очаг пожара огнетушащими средствами, создание инертной среды, затопление пожарных выработок водой, заиливание).
Непосредственное тушение очагов пожара обычно применяется в начальный период горения, а также во всех случаях, когда имеются безопасные подступы к очагу и в достаточном количестве пожаротушащие средства. Этот способ характеризуется непосредственным или дистанционным воздействием на очаг пожара различными огнетушащими средствами. Его успешному применению в подземных условиях способствует возможность в начальный период приблизиться к очагу пожара со стороны поступающей струи воздуха.
Изоляция заключается в ограничении доступа воздуха к очагу пожара путем возведения изолирующих пожарных перемычек, закрывания дверей, полков, ляд и др. Этот способ применяют в тех случаях, когда отсутствуют безопасные подступы к очагу пожара. В пожарном участке произошел взрыв горючих газов и нельзя безопасно его проветрить, суммарная доля горючих газов в пожарном участке достигла 2% при большой доле кислорода и предотвратить дальнейшее накопление горючих газов невозможно, имеющиеся средства пожаротушения не дают должного эффекта, непосредственное тушение огнетушащими средствами экономически нецелесообразно.
Комбинированный способ применяется в тех случаях, когда невозможно потушить пожар активным способом или снизить концентрацию кислорода на аварийном участке до безопасного значения. Комбинирование различных способов и средств пожаротушения наиболее эффективно при ликвидации широко распространившихся пожаров.
Для тушения подземных пожаров применяются разнообразные по физико-химическому составу, эффективности и воздействию пожаротушащие средства, выбор которых зависит от вида горящего
252
материала, горно-технических и горно-геологических условий, режима проветривания пожарного участка, степени распространения пожара, наличия безопасных подступов к очагу горения и др.
Применяемые пожаротушащие средства по своему физическому состоянию подразделяются на жидкие (вода, заливочная пульпа), пенные (химическая, воздушно-механическая и газомеханическая пена), газообразные (диоксид углерода, азот, парогазовая смесь) и сыпучие (огнетушащие порошки, инертная пыль и песок).
Вода – наиболее распространенное и эффективное средство, применяемое для тушения пожаров в шахтах, особенно в начальный период их развития. Она является одним из лучших хладоагентов. На поверхности каждой шахты должно быть оборудовано не менее двух наполненных водой утепленных пожарных резервуаров вместимостью не менее 250 м3. Около пожарных резервуаров устраиваются насосные станции. Подача пожарных насосов должна быть не менее 0,022 м3/с (80 м3/ч). От пожарных резервуаров к каждому стволу шахты и между зданиями и сооружениями прокладывается утепленный трубопровод диаметром между зданиями не менее 100 мм и не менее 150 мм – к стволам.
В подземных выработках шахт для борьбы с пожарами и пылью должны быть проложены объединенные пожарно-оросительные трубопроводы. С поверхности шахты в горные выработки вода подается по двум магистральным трубопроводам – рабочему и резервному. Для снижения давления воды должны применяться редукционные устройства, располагаемые на отводах магистральных пожарно-оросительных трубопроводов. Сеть пожарно-оросительного трубопровода в подземных выработках должна состоять из магистральных участковых линий, диаметр которых – соответственно не менее 150 и 100 мм. Концы участковых пожарно-оросительных трубопроводов должны отстоять от забоев подготовительных и очистных выработок не более чем на 40 м и оборудованы пожарными кранами, у которых размещается ящик с двумя пожарными рукавами и пожарным стволом.
Давление воды на выходе из пожарных кранов должно быть при нормируемом расходе воды на подземное пожаротушение 0,6 – 1,5 МПа. На участках трубопроводов, где давление превышает 1,5 МПа, перед пожарными кранами устанавливают устройства, обеспечивающие снижение давления.
Пожарно-оросительный трубопровод оборудуется пожарными кранами с однотипными соединительными головками, имеющими диаметр не менее
70мм, которые должны быть размещены:
ввыработках с ленточными конвейерами – через 50 м, при этом дополнительно по обе стороны от приводной станции конвейера на
253

расстоянии 10 м устанавливаются два пожарных крана. Рядом с пожарными кранами должен находиться пожарный рукав длиной 20 м и ствол;
по обе стороны от всех камер, в которых хранятся или используются горючие материалы, а также ходка в склад взрывчатых материалов – на расстоянии 10 м. Рядом должен находиться ящик с пожарным рукавом и ствол;
у пересечений и ответвлений подземных выработок;
вгоризонтальных и наклонных выработках, не имеющих пересечений
иответвлений, соответственно через 200 и 100 м;
ввыработках околоствольного двора, где нет камер, – через 100 м, а также с каждой стороны стволов на сопряжениях с выработками;
у погрузочных пунктов лав со стороны свежей струи воздуха и на вентиляционных штреках не далее 20 м от выхода из очистного забоя;
втупиковых выработках при длине более 500 м – через 50 м, при меньшей длине – через 100 м.
Все ленточные конвейеры в горных выработках должны быть оборудованы стационарными установками пожаротушения. В настоящее время ленточные конвейеры оборудуются установками водяного пожаротушения УВПК. Существует несколько модификаций этой установки. Установка УВПК состоит (рис.4.А3) из задвижки I, запорно-пускового устройства 2, распределительного трубопровода 3, II распылителей 4, трех тепловых датчиков 5. Температура срабатывания тепловых датчиков 47 или 72 °С. Длина защищаемой ленты – не менее 20 м.
Установки УВПК оснащаются распылителями воды РВ. Распылитель
254
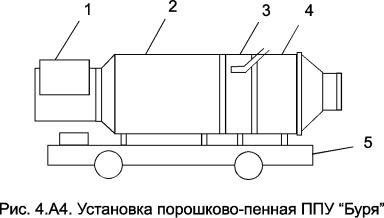
имеет простую конструкцию и состоит из металлического корпуса и изготовленного из термостойкого пластика диспергатора. Он обеспечивает стабильную сплошную конусную струю тонкораспыленной воды длиной до 6 м при давлении 0,6 МПа.
Воздушно-механические, газомеханические и твердеющие пены находят все более широкое применение для борьбы с подземными пожарами.
Пена – двухфазная (газожидкостная) система с определенной устойчивостью структуры, массы и объема. Жидкая фаза пены представляет собой водный раствор поверхностно-активного вещества (пенообразователя) или водный раствор синтетической смолы с пенообразователем и отвердителем, а газовая фаза – воздух или инертный газ (азот, парогазовая смесь, углекислый газ или продукты горения). Для тушения и локализации пожаров в газовых шахтах используется в основном газо-механическая (инертная) и твердеющая пены.
Газо-механическая пена образуется при подаче водного раствора пенообразователя на сетку, через которую продувается воздух (газ), эжектируемый за счет энергии воды или принудительно подаваемый. Применяется также бессеточный способ получения пены в пожарных рукавах или трубопроводах при одновременной подаче в них водного раствора пенообразователя и газа в строго определенных соотношениях.
Подразделения военизированной горноспасательной службы оснащены следующими пенными средствами тушения подземных пожаров.
Высокопроизводительная порошково-пенная установка ППУ «Буря» (рис.4.А4) предназначена для дистанционного тушения пожаров пеной и порошком в горизонтальных, наклонных и вертикальных выработках, проветриваемых за счет общешахтной депрессии, а также в тупиковых выработках протяженностью до 250 м.
ППУ можно доставлять по горным выработкам с площадью сечения не менее 3,3 м2 (ширина выработок – не менее 1,8 м, высота – не менее 1,8 м), оборудованных колеей 900 мм. У места установки ППУ по выработке должно проходить не менее 10 м3/с воздуха. Производительность установки:
255
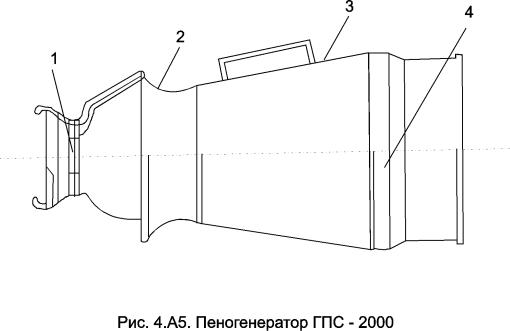
по пене 8,3…10,0 м3/с при кратности пены 40…70, по порошку 5,0 кг/с. Установка «Буря» (рис.4.А4) состоит из вентилятора 2, соединенного
через воздухораспределитель 3 с пеногенератором 4. На входе вентилятора установлена порошковая приставка-бункер I, в которую порошок подается из заводской тары. Указанное оборудование, а также ящик для ЗИП размещены на раме 5 шахтной вагонетки ВГ-3,3.
ППУ может обеспечить подачу пены в очагу горения непосредственно по горным выработкам и по вентиляционным трубам и поэтому комплектуется самоуплотняющейся воздухонадувной перемычкой.
Для получения пены средней кратности применяется ежекционный пеногенератор ГПС-2000. Пеногенератор позволяет получать пену кратностью 70…100 с производительностью 0,033 м3/с. пеногенератор (рис.4.А5) состоит из центробежной форсунки I, конфузора 2, диффузора 3 и пакета пеногенерирующих сеток 4.
Для предотвращения, локализации и тушения пожаров от самовозгорания скоплений угля в выработанном пространстве очистных забоев предназначена пеногенераторная установка УПГВ. Установка позволяет получать газомеханическую и воздушно-механическую пену и транспортировать ее под давлением по трубопроводам на расстояние более 200 м. Производительность установки 0,066 м3/с пены кратностью 150…175.
Установка позволяет обеспечить устойчивый процесс получения пены высокой кратности, ее транспортирование под давлением по трубопроводам малого диаметра в труднодоступные места выработанного пространства, заполнения куполов и пустот горных выработок.
Для предотвращения пожаров эндогенного происхождения путем подачи под давлением газомеханической пены в труднодоступные места
256
применяют пеногенератор высоконапорный трубный ПВТ. Он монтируется непосредственно на трубопроводе. Существует три его модификации для трубопроводов 3.4 и 6 дюймов.
Заполнение куполов и пустот за крепью горных выработок, изоляция выработанного пространства, возведение изолирующих перемычек и рубашек производится твердеющей пеной на основе синтетических смол. Для выполнения этих работ применяют установку ТП. Она представляет собой систему инжектов для подсоса синтетической смолы с пенообразователем и кислотного отвердителя с последующим их смешиванием и вспениванием сжатым воздухом в пеногенераторе. Производительность установки ТП 0,02…0,03 м3/с при кратности пеномассы
15…30.
Формирование пеномассы происходит в пожарном рукаве длиной не менее 25 м, по которому ее подают к месту заполнения перемычек, пустот, куполов и др. Пеномасса через определенное время твердеет.
В качестве первичных средств пожаротушения применяется огнетушатель пенный унифицированный ОПУ-10, который предназначен для тушения горящей конвейерной ленты и других материалов, трудноподдающихся тушению порошковыми огнетушителями (пожары классов А и В), за исключением щелочных металлов, которые горят без доступа воздуха, а также электроустановок, находящихся под напряжением.
Одним из эффективных методов предотвращения взрывов при тушении подземных пожаров является общая инертизация шахтной среды за счет замещения воздуха, поступающего к очагу горения, инертным газом. В качестве инертных газов могут быть использованы азот, углекислый газ, а также парогазовые смеси, которые получают непосредственно в горных выработках путем сжигания углеводородного топлива с специальных установках – генераторах инертных газов.
Генераторы инертных газов применяются на шахтах наиболее часто. При пожарах на участках с метановыделением до 8 м3/мин используются генераторы ГИГ-4 производительностью 340 м3/мин парогазовой смеси. При пожарах в высокопроизводительных добычных участках (метановыделение до 30 м3/мин) используются генераторы ГИГ-1500 с регулируемой производительностью 800…1500 м3/мин парогазовой смеси, что позволяет инертизировать шахтный воздух пожарных участков без существенного изменения установившегося режима проветривания.
Генератор ГИГ-1500 (рис.4.А6) состоит из последовательно состыкованных посредством быстроразъемных соединений следующих основных узлов: турбореактивного двигателя 2 типа Ж-701, испарителя топлива 3, двухсекционной камеры дожигания 4, камеры охлаждения 5 с пеногенерирующим устройством и водоотделителем.
257
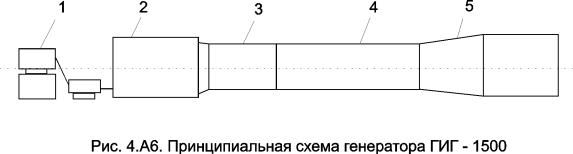
Запуск генератора и управление его работой производятся дистанционно с пульта управления I. При работе генератора выхлопные газы из турбореактивного двигателя, имеющие температуру 693…733 К и долю кислорода 17…18 % подаются в испаритель топлива. туда же вводится топливо, которое в потоке газа в виде топливовоздушной смеси поступает в камеру дожигания, где происходит дальнейшее выгорание кислорода. Из камеры дожигания газы, содержащие не более 3 % кислорода при температуре 2073…2173 К, поступают в камеру охлаждения, в которой в процессе испарения воды снижается температура газов и образуется парогазовая смесь с температурой 353…363 К.
Порошковая пожарная техника и огнетушащий порошок широко применяются в угольных шахтах. Это объясняется возможностью тушения всех видов горящих материалов (твердых, жидких, газообразных и электрооборудования под напряжением до 1140 В), пригодностью к длительному хранению огнетушащего порошка и использованию при температуре до 50 °С до минус 50 ° С. Применение огнетушащих порошков обеспечивает дистанционное объемное тушение очага пожара.
Действие огнетушащих порошков основано на проявляющихся одновременно изолирующем, ингибирующем и охлаждающем эффектах.
Вугольных шахтах чаще всего применяют огнетушащий порошок П- 2АП на основе аммофоса с добавкой компонентов, улучшающих его физические свойства.
Вкачестве первичных средств пожаротушения в основном применяются огнетушители ОП-10Ф вместимостью 10 л. Огнетушитель
обеспечивает тушение модельного очага пожара класса В (бензин А-76 на площади не менее 5,75 м2).
Наиболее часто подразделениями военизированной горноспасательной службы применяется огнетушитель порошковый ОПШ-100. Вместимость
корпуса 100 л. Огнетушащая способность при тушении бензина А-76 – не менее 15 м2 площади. Огнетушитель обеспечивает непосредственное тушение пожаров в начальной стадии их развития и дистанционное тушение развившихся пожаров.
Для дистанционного тушения пожаров в тупиковых выработках
258

огнетушащим порошком применяют устройство подачи порошка «Вихрь-Т». Оно предназначено для подачи порошка в воздушный поток, создаваемый вентилятором местного проветривания ВМ-6 или ВМЦ-8. Устройство «Вихрь-Т» обеспечивает подачу 1 кг/с огнетушащего порошка на расстояние до 400 м по трубам диаметром 600 или 800 мм вентилятором ВМ-6.
Устройство «Вихрь-Т» (рис.4.А7) состоит из конфузора I, бункера 2, диффузора 3 и вентилятора 4.
Использование перечисленных средств позволяет существенно сократить количество подземных пожаров и повысить уровень противопожарной устойчивости шахт.
4.А5. План ликвидации аварий на шахте.
Многие из перечисленных аварий практически тем успешнее ликвидируются, чем лучше шахта подготовлена к возможности их возникновения. Именно поэтому в соответствии с Правилами безопасности в угольных шахтах и Инструкций к ним [4] для каждой действующей, реконструируемой и строящейся шахты составляет план ликвидации аварий (в дальнейшем ПЛА).
ПЛА разрабатывается на каждые 6 месяцев главным инженером шахты и командиром обслуживающего шахту горноспасательного взвода, согласовывается с командиром горноспасательного взвода, согласовывается с командиром военизированного горноспасательного отряда (отдельного взвода) ГВГСС и утверждается техническим руководителем объединения (самостоятельной шахты) за 15 дней до ввода в действие.
ПЛА должны предусматриваться мероприятия, которые осуществляются немедленно при обнаружении аварии и обеспечивают:
спасение людей, застигнутых аварией; ликвидацию аварии и
259
предупреждение ее развития.
С целью разработки включаемых в позиции мероприятий по спасению людей, ликвидации и предупреждению развития аварий перед составлением плана проверяется:
-обеспеченность шахты, горизонтов, горных выработок запасными выходами, пригодность их для передвижения людей, прохода горноспасателей в респираторах и транспортирования пострадавших;
-соответствие времени движения по загазированным выработкам сроку защитного действия принятых на шахте самоспасателей;
-наличие, состояние и расположение средств спасения горнорабочих (места группового хранения самоспасателей, пункты переключения в резервные самоспасатели и др.), подготовленность работников к их использованию;
-ожидаемая газовая обстановка на участках в случае отключения дегезационной системы;
-время загазирования тупиковых забоев в случае остановки ВМП;
-устойчивость вентиляционных струй в выработках при воздействии тепловой депрессии пожара, выполнимость намеченных мер по предотвращению самопроизвольного опрокидывания вентиляционной струи и обеспечению устойчивого аварийного режима проветривания.
Выбор вентиляционных режимов и мер по обеспечению устойчивости проветривания производится с учетом депрессионной съемки.
-состояние вентиляционных устройств, в том числе исправность реверсивных устройств главных вентиляционных установок, возможность выполнения предусматриваемых планом вентиляционных режимов;
-наличие и состояние средств оповещения об аварии;
-размещение пунктов вспомогательной горноспасательной команды и расстановка членов ВГК в шахте, соответствие численности расчету, их подготовленность;
-водоснабжение, обеспеченность шахты средствами пожаротушения и их состояние, подготовленность работников к их применению.
По материалам проверок устанавливаются зоны поражения при пожарах, взрывах, внезапных выбросах, обрушениях, прорывах воды, проникновениях ядовитых химических веществ и др., определяется зона реверсирования вентиляционной струи, производится оценка пожарной опасности горных выработок и, при необходимости, разрабатываются дополнительные меры по повышению пожарной безопасности.
ПЛА разрабатывается в соответствии с ожидаемой ситуацией в шахте на момент ввода его в действие. Предусмотренные планом технические средства и материалы для осуществления мероприятий по спасению людей и ликвидации аварий должны быть в исправном состоянии и необходимом
260
количестве, а лица, ответственные за выполнение мероприятий, и исполнители должны уметь ввести их в действие.
Ответственность за правильное составление плана ликвидации аварий и его соответствие действительному положению в шахте несут главный инженер шахты и командир обслуживающего шахту горноспасательного взвода.
ПЛА должен содержать:
оперативную часть: обязанности лиц, участвующих в ликвидации аварий, и порядок их действия;
список должностных лиц и учреждений, которые должны быть немедленно извещены об аварии;
основные правила поведения (действия) работников шахты при авариях;
указания по ликвидации последствий аварийных ситуаций (загазирование, обрыв клети, поражение электротоком и др.), разрабатываемые в соответствии с типовыми указаниями по ликвидации последствий аварийных ситуаций.
К оперативной части плана ликвидации аварий должны быть приложены следующие документы:
- схема вентиляции шахты. На схему вентиляции дополнительно наносятся время загазирования (при остановке ВМП) тупиковых выработок до предельно допустимой концентрации, пункты ВГК, схема дегазационных трубопроводов с указанием мест установки задвижек, контрольноизмерительных устройств;
- схема (план) горных выработок и план по верхности с нанесением пожаротушения, средств оповещения об аварии, средств группового спасения рабочих при авариях, принципиальной схемы подачи воды в шахту из водоемов, резервуаров и других источников, подъездных путей к стволам, шурфам;
- планы горных работ по пластам или горизонтам с нанесением направления движения воздуха, мест установки телефонов и их номеров.
ПЛА состоит из позиций. В одну позицию включается одна или несколько сопряженных горных выработок, если для этих выработок соблюдаются следующие условия:
предусматривается одинаковый аварийный режим проветривания; применяются одинаковые мероприятия по спасению людей; совпадают маршруты движения горноспасательных отделений и
порядок выполняемых работ.
На участках, на видных местах в нарядных должны быть вывешены правила поведения (действий) работников участка при авариях и конкретные маршруты их выхода в соответствии с ПЛА.
261
Изучение ПЛА инженерно-техническими работниками шахты производится под руководством главного инженера после согласования плана с ГВГСС, при этом изучаются также «Обязанности должностных лиц, участвующих в ликвидации аварий, и порядок их действий».
Позиции оперативной части составляются для следующих видов аварий: пожар, взрыв, внезапный выброс, прорыв воды (пульпы) и затопление; горный удар; обрушение угля (породы); аварийные ситуации (загазирование, остановка вентилятора главного проветривания, застревание клети или обрыв каната, общее отключение электроэнергии).
Взависимости от характера и места возникновения аварии, опасности
ееразвития в позициях плана предусматриваются следующие основные мероприятия по спасению людей, ликвидации и предупреждению развития аварий:
немедленный вызов обслуживающего шахту взвода ГВГСС производится при любой из перечисленных аварий независимо от ее размеров;
принимаемый аварийный вентиляционный режим должен, как правило, обеспечивать выход людей по незагазированным выработкам и быть устойчивым. При выборе вентиляционного режима необходимо учитывать следующее.
При взрывах газа и угольной пыли, внезапных выбросах сохраняется существующее до аварии направление вентиляционной струи, предусматривающее способы увеличения подачи воздуха на аварийные участки.
При пожаре в надшахтных зданиях, стволах, околоствольных дворах, по которым поступает свежий воздух, предусматривается реверсирование вентиляционной струи.
При пожаре в газообильном тупиковом забое необходимо сохранить нормальный режим его проветривания.
Для случаев пожара в других выработках следует сохранить нормальный режим работы вентиляторов главного проветривания. В зависимости от вида и места возникновения аварии, газовыделения на аварийном участке и др. может предусматриваться уменьшение или увеличение расхода воздуха, остановка вентиляторов, закорачивание или местное реверсирование струи воздуха.
При взрывах электроэнергия в шахту должна отключаться.
При реверсивном режиме проветривания подача электроэнергии в шахту должна прекращаться. Допускается подача электроэнергии в шахту на отдельные ее выработки (кроме очистных и подготовительных) для обеспечения быстрого и безопасного выезда людей из шахты. Отключение электроэнергии в этих случаях производится после полного вывода людей.
262
При пожарах, внезапных выбросах в пределах участков прекращается подача электроэнергии на эти участки и по пути движения исходящих из них струй воздуха.
При пожаре в надшахтных зданиях стволов (шурфов) с исходящей струей и других надшахтных сооружениях, в камерах, проветриваемых обособленной струей воздуха (электровозный гараж, склад ВМ и др.), подача электроэнергии прекращается только на эти объекты.
При пожарах в выработках с исходящей струей прекращается подача электроэнергии только в эти выработки.
При пожаре в газообильной тупиковой выработке прекращается подача электроэнергии в аварийную выработку. Но сохраняется на проветривающий ее вентилятор.
При использовании в горных выработках пневматической энергии должна обеспечиваться подача сжатого воздуха в шахту при всех видах аварий.
Все лица, работающие в шахте, должны быть оповещены о происшедшей аварии. В первую очередь оповещаются люди аварийных и угрожаемых участков.
При взрывах газа и угольной пыли, в случае реверсирования вентиляторов главного проветривания, а также при пожарах в шахтах, имеющих только два выхода на поверхность, должен предусматриваться вывод из шахты всех людей.
При пожарах в шахтах, имеющих более двух запасных выходов на поверхность, если сохранен нормальный режим проветривания, вывод людей должен предусматриваться из всех выработок и участков, в которые поступают продукты горения, и из угрожаемых участков.
Участок относится к угрожаемому, если в результате аварии возможно его загазирование или если остается один выход из него.
Для ускорения эвакуации людей из аварийного участка (шахты) следует использовать все виды подземного транспорта, доставляющие людей к местам работ. Этот же транспорт используется и для передвижения отделений ГВГСС и членов ВГК к месту аварии.
В позициях оперативной части плана должны быть указаны инженерно-технические работники шахты, ответственные за выполнение мероприятий и исполнители.
4.Б. Охрана труда в черной металлургии
Ежегодно почти 17 тыс. человек становятся инвалидами вследствие травм и профзаболеваний. Численность пенсионеров по трудовому увечью в 1996 г. превысила 150 тыс. человек. Общая сумма расходов на финансирование профессиональных льготных пенсий и пенсий по трудовому
263
увечью, возмещению убытков потерпевшим на производстве сегодня составляет 10 – 15% фонда оплаты труда в промышленности. Около трети несчастных случаев на производстве происходит вследствие неудовлетворительных знаний работниками требований безопасности. Поэтому в отрасли действует система управления охраной труда (СУОТ) с целью снижения травматизма и улучшения условий труда, действующая в соответствии с законом Украины «Об охране труда». На уровне министерства создана служба охраны труда, входящая в состав министерства труда и социальной политики Украины. На предприятиях черной металлургии для обеспечения функционирования СУОТ создаются и действуют следующие службы: служба охраны труда (в соответствии с ДНАОП 0.00-4.21-93); лаборатории, которые осуществляют контроль за наличием вредных производственных факторов на рабочих местах; газоспасательная служба, обеспечивающая безопасность работ с повышенной опасностью. Администрация предприятия назначает должностных лиц, обеспечивающих решение конкретных вопросов охраны труда, утверждает инструкции об их обязанностях, правах и ответственности за выполнение возложенных на них функций по обеспечению безопасных и безвредных условий труда. На предприятиях черной металлургии создаются постоянно действующие комиссии по исследованию условий труда, аттестации рабочих на соответствие нормативным актам об охране труда в сроки, установленные ДНАОП 0.05-8.04-92, и по устранению причин, вызывающих несчастные случаи и профессиональные заболевания. Контроль за соблюдением норм и правил по охране труда осуществляет департамент по надзору за охраной труда, типовое положение о котором утверждено Кабинетом Министров Украины 6.06.2000 г., №925.
4.Б1. Профилактика производственного травматизма в черной металлургии
Производство чугуна, стали и проката на предприятиях черной металлургии связано с высотемпературной переработкой большого количества материалов (руды, кокса, агломерата, окатышей, чугуна, флюсов, стали, проката и др.), поэтому в производственных помещениях возможно появление опасных и вредных производственных факторов, приводящих к травматизму и профессиональным заболеваниям. Состояние травматизма по Донецкой области на предприятиях черной металлургии приведено в таблице 4.Б1 за период с 1993 по 1999 г.
264
Таблица 4.Б1 Травматизм на предприятиях черной металлургии Донецкой области
Годы |
1993 |
1994 |
1995 |
1996 |
1997 |
1998 |
1999 |
|
Общий травматизм, чел |
1038 |
1006 |
923 |
851 |
784 |
710 |
598 |
|
Смертельный |
37 |
25 |
29 |
27 |
37 |
30 |
17 |
|
травматизм, чел |
||||||||
|
|
|
|
|
|
|
Данные таблицы 4.Б1 показывают, что как общий травматизм, так и смертельный имеет тенденцию к снижению. Это можно объяснить действием принятых мероприятий по снижению травматизма и спадом производства. Однако уровень общего травматизма в отрасли за последние два года остается довольно высоким, что приводит к значительным потерям как финансовым, так и потерям рабочего времени (таблицы 4.Б2). Так, несмотря на то, что средняя длительность нетрудоспособности, приходящаяся на один несчастный случай, в 1999 г. снизилась на 11,8% по сравнению с 1998 г., величина штрафов, наложенных на предприятия за допущенные несчастные случаи, возросла на 33,8%. Это свидетельствует о том, что, несмотря на
снижение общего травматизма, потери предприятий растут.
Таблица 4.Б2 Анализ общего травматизма по Донецкой области на предприятиях
черной металлургии за 1998 и 1999 г.г.
Показатели/год |
1998 |
1999 |
Среднесписочное количество работающих, чел |
184912 |
187533 |
Количество пострадавших |
710 |
598 |
Количество человеко-дней нетрудоспособности |
33404 |
24808 |
Коэффициент частоты травматизма |
3,84 |
3,19 |
Показатели/год |
1998 |
1999 |
Коэффициент тяжести травматизма |
47,05 |
41,48 |
Коэффициент производственных потерь |
180,67 |
132,32 |
Сумма штрафов за допущенные случаи, тыс. грн |
390,4 |
522,4 |
Распределение несчастных случаев в доменном цехе по причинам за двенадцатилетний период времени следующее по [5]: технические причины – 29,5%, организационные – 66,1% и санитарно-гигиенические – 4,4%.
Распределение несчастных случаев по месту происшествия: рудный двор – 5,2%; механизмы загрузки доменных печей – 12,7%; доменная печь – 44,4%; устройства для уборки чугуна и приготовления заправочных материалов – 16,3%; воздухонагреватели, пылеуловители и технологические коммуникации – 2,4%; железнодорожные пути доменного цеха – 3,9%; устройства для уборки и переработки шлака – 3,6%; мастерские, вспомогательные и бытовые помещения – 8,1%; прочие – 3,4%.
265
Распределение несчастных случаев по стадиям технологического процесса следующее: прием и загрузка шихты – 14,9%; выплавка чугуна, выпуск чугуна и шлака – 41,7%; обслуживание воздухонагревателей, пылеуловителей, промпроводок – 1,1%; разливка чугуна на разливочных машинах – 11,2%; ремонт ковшей, работы на складе холодного чугуна – 1%; приготовление заправочных материалов – 0,9%; уборка и переработка шлака
– 2,5%; ремонтно-вспомогательные работы – 18,9%; работы в мастерских и прочее – 7,8%.
Распределение несчастных случаев по основным профессиям: рабочие места по приемке и загрузке шихты (машинисты вагоноопрокидывателей, рудных кранов, вагон-весов, мотористы, рабочие бункеров и др.) – 16,0%; рабочие места по обслуживанию печей и воздухонагревателей (горновые, газовщики, водопроводчики печи, мастера и др.) – 42,8%; рабочие места по обслуживанию разливочных машин, ремонту ковшей (желобщики, машинисты кранов, ковшевые и др.) – 12,7%; ремонтно-вспомогательные работы – 18,6% (в том числе слесари по ремонту печи и воздухонагревателя – 4,8%, слесари по ремонту разливочных машин – 1,4%); электрики – 3,5%; работы в мастерских цеха – 2,6%; прочие профессии – 3,8%. Анализ показывает, что почти третья часть всех несчастных случаев (32,3%) произошла с горновыми, хотя горновые составляют только 15% всех работающих в доменном цехе. Горновые были травмированы на литейном дворе при выполнении основной работы: на технологических операциях -70% всех несчастных случаев, при производстве подъемно-транспортных работ – 15%. Это свидетельствует о том, что профессия горновых связана с повышенной опасностью. Помимо горновых, по числу травм выделяются водопроводчики печи, а также газовщики и мастера доменной печи. Значительная часть травм произошла с ремонтно-вспомогательным персоналом (18,6%). Чаще всего встречаются ожоги – 32,7%, ушибы – 25,1%, переломы – 15,9% и раны – 13,2%.
Вэлектросталеплавильном цехе чаще всего несчастные случаи происходят при отборе проб, транспортировке корзины со скрапом, при скачивании шлака и выпуске стали. Только 11 основных технологических операций охватывают 62% общего числа случаев травматизма. Анализ несчастных случаев в разливочном пролете сталеплавильного цеха показал, что 40% случаев травматизма связано с использованием кранов и транспортировке изложниц, слитков и ковшей с жидкими сталями и шлаками.
Вкузнечно-прессовом цехе было получено следующее статистическое распределение: 27% – ранения и ушибы; 10% – ожоги. Анализ показал, что наиболее высокому риску подвергаются пескоструйщики, обслуживающий персонал прессов и манипуляторов, кузнецы, шлифовщики, машинисты манипуляторов. Из общего числа несчастных случаев 50% относится к
266
транспортировке, 27% – к обслуживанию и контролю и 19% – к ремонту, зачистке, устранению неполадок и реконструкции.
Таким образом, на основании проведенного анализа можно сделать вывод о том, что травматизм на предприятиях черной металлургии происходит при выполнении основных и вспомогательных технологических операций из-за неудовлетворительной организации работ; низкой трудовой дисциплины, снижения требовательности со стороны руководителей и должностных лиц за соблюдением законодательства и правил по охране труда; нарушений требований безопасности при выполнении ремонтных работ и при эксплуатации оборудования, а также при ведении технологических процессов производства и обработки стали, чугуна.
Опасными основными факторами на предприятиях черной металлургии при производстве чугуна, стали и проката являются [13]:
движущиеся и вращающиеся части машин и механизмов; расплавленный металл и шлак, а в прокатных цехах – нагретый под обработку давлением металл; повышенная температура наружной поверхности технологического оборудования; наличие опасного электрического тока; возможность взрыва при контакте расплавленного металла или шлака с водой или влажными сыпучими материалами; возможность образования взрывоопасных газовоздушных смесей и их взрыва; выбросы металла или шлака при обработке чугуна или стали в ванне печи или ковше при бурном протекании процессов; прорыв металл через кладку печи; обрушение свода или кладки печи; нарушение герметичности водо-охлаждаемых кожухов печей; наличие большого количества масла и возможность его воспламенения; возможность воспламенения электрооборудования, работающего в тяжелых микроклиматических условиях. Особую опасность представляет в электросталеплавильных цехах возможность возгорания печного трансформатора короткой линии, питающей электроды печи; вращающиеся рабочие валки с их захватывающей способностью, что создает опасность при обслуживании прокатных станов; окалина, разлетающаяся по цеху с большой скоростью при задаче металла в черновые клети обжимных прокатных станов; наличие грузоподъемного оборудования и большого грузопотока перемещаемых материалов в опасном состоянии (расплавленного и нагретого металла, крупногабаритного и тяжелого оборудования и др.).
Многие из этих факторов создают возможность не только травмирования персонала, но и возникновения аварийных ситуаций, вероятность перерастания которых в чрезвычайные ситуации техногенного характера весьма большая. Основную опасность представляют в черной металлургии технологические взрывы. Взрывы, возникающие в ходе технологического процесса производства металлов и сплавов, называют
267
технологическими. К ним относятся: взрывы при контакте расплавленного металла или шлака с водой; взрывы газопаро и пылевоздушных смесей; взрывы порошков металлов и сплавов. Возможность возникновения взрыва существует во всех основных металлургических цехах. Так, в доменном цехе взрывы могут произойти при контакте расплавленного металла и шлака с водой, при отводе доменного газа и подводе природного газа и пылеугольного топлива в доменную печь. В сталеплавильном производстве возможны взрывы при контакте расплавленного металла или шлака с водой, взрывы газов, порошков металлов – раскислителей, экзотермических смесей, утепляющих засыпок и др. В прокатном производстве возможны взрывы паров смазочных материалов, газо-воздушных смесей в нагревательных и термических печах и др.
При контакте расплавленного металла или шлака с водой происходит взрыв, что объясняется физико-химическими свойствами воды. В этом случае протекают следующие процессы:
−испарение воды с увеличением объема и давления;
−диссоциация воды с разложением на водород и кислород;
−взаимодействие паров воды с железом, сопровождавшееся выделением
водорода, который при определенных условиях может образовывать взрывчатую смесь с воздухом.
Воспламенение этой смеси приводит к взрыву, энергия которого изменяется в широких пределах в зависимости от многих факторов (например, массы воды, массы металла, условий контакта и др.). При этом следует учитывать, что взрыв происходит только при взаимодействии жидких фаз расплавленного металла и шлака с водой. В твердом состоянии, даже при температуре, близкой к температуре солидуса, такой контакт к взрыву не приводит.
В доменном производстве взрывы при контакте расплавленного металла или шлака с водой возникают при прогаре стенок горна или лещади, в зонах леток. Особенно опасны взрывы в фурмах, шлаковых фурмочках и шлаковых ковшах. Взрывы в фурмах сопровождаются раскрытием горна и выбросом через фурменное отверстие на рабочую площадку раскаленных материалов доменной плавки (кокса, газов, шихтовых материалов и др.), которые в атмосфере воспламеняются и горят. Взрывы в фурмах происходят по двум причинам: из-за повышения давления пара, образовавшегося внутри полости фурмы, при нарушении охлаждения фурмы; из-за возникновения взрывоопасных газо-воздушных смесей в канале фурмы при несоответствии давления дутья и газов в доменной печи (при этом нагретые горючие газы из доменной печи проникают в канал фурмы, по которому подается в печь нагретый воздух, и это приводит к взрыву). Анализ аварий в доменном цехе показал, что аварии, связанные с кожухом доменной печи составляют 12% от
268
всех аварий; с охладительной арматурой печи – 44%, с воздухопроводами и газопроводами – 13%.
Взрывы в сталеплавильном производстве, вызываемые водой или влажными материалами (шихтой, ломом, рудой и т.д.) при загрузке в печь являются наиболее частыми. Поэтому для предотвращения данной категории взрывов необходимо все материалы и оборудование подвергать специальной подготовке (в том числе просушке, прогреву и др.). Для этого необходимо соблюдать требования [6-9].
4.Б2. Проблемы физиологии, гигиены труда и производственной санитарии в отрасли
Агломерационное производство характеризуется повышенной запыленностью в связи с переработкой сыпучих материалов. Так, в корпусе вагоноопрокидывателя при выгрузке исходных материалов запыленность воздуха в рабочей зоне составляет 12 – 46 мг/м3 (ПДК равно 4 мг/м3), в отделении распределения материалов – 65 – 180 мг/м3, в отделении измельчения и дробления – 60 – 600 мг/м3, в отделении смешивания – 16 – 200 мг/м3. При сбрасывании пирога в хвостовой части ленты на колосниковый грохот выделяется пыль, и ее концентрация в рабочей зоне изменяется от 160 до 1300 мг/м3. Обильное пылевыделение наблюдается в процессе сортировки агломерата на грохотах (до 5000 мг/м3) и при погрузке в вагоны. Концентрация пыли над вагонами составляет 2,5 – 4,9 г/м3. Валовое количество пыли при погрузке составляет в среднем 3360 кг/ч. На участке спекания в рабочую зону кроме пыли могут попадать продукты горения (окись углерода и сернистый ангидрид). Интенсивность теплового облучения на рабочих местах аглофабрики изменяется от 0,35 до 7 кВт/м2, что значительно превышает допустимый уровень (0,14 кВт/м2). Наиболее шумоопасным и виброопасным оборудованием на аглофабриках являются грохота, дробилки, эксгаустеры, питатели и смесители, уровни звуковой мощности которых изменяются от 98 до 115 дБА. Параметры микроклимата также не соответствуют требуемым нормам по температуре, влажности и скорости движения воздуха. Так, например, на участке спекания она выше допустимых норм, а на участках дробления и смешивания – ниже норм.
Доменное производство характеризуется наличием таких вредных факторов на рабочих местах, как запыленность, загазованность, тепловые воздействия и шум. Запыленность на основных рабочих местах может составлять: на участке шихтоподачи от 2 до 586 мг/м3; на литейном дворе при выпуске чугуна и шлака – от 2 до 256 мг/м3, при ремонте главного желоба – от 3 до 540 мг/м3. Загрязнение воздуха токсичными газообразными веществами (окисью углерода и сернистым газом) возможно на рабочей площадке при обслуживании доменной печи, на литейном дворе и на
269
колошниковых площадках. Концентрация сернистого газа составляет в среднем 19 мг/м3, а окиси углерода – до 40 мг/м3. Только на колошниковых площадках может быть значительное содержание окиси углерода, поэтому там возможно лишь кратковременное пребывание людей без защитной аппаратуры. Расплавленные чугун и шлак, нагретые поверхности оборудования создают соответствующий нагревающий микроклимат на рабочих местах. Так, интенсивность тепловых излучений на рабочих местах литейных дворов составляет 0,7 – 14 кВт/м2, а на рабочей площадке у доменной печи – 0,35 – 5,6 кВт/м2. Температура воздуха в теплый период года на рабочих местах у доменной печи может достигать 35 – 46оС при относительной влажности 20 – 50%. Уровень шума на рабочих местах превышает допустимые значения и зависит от применяемого оборудования. Наиболее шумоопасным и виброопасным оборудованием в доменном цехе являются инерционные грохота, клапаны «Снорт», газовые горелки воздухонагревателей, вибропитатели, фурмы доменных печей. Уровни звуковой мощности данного оборудования изменяются от 101 до 121 дБА.
Сталеплавильное производство характеризуется наличием таких вредных факторов на рабочих местах, как запыленность, загазованность, тепловые воздействия и шум. В связи с тем, что на предприятиях черной металлургии возможно применение мартеновского, конвертерного и электроплавильного способов производства стали, проанализируем все эти способы.
Основные загрязнители воздуха рабочей зоны в мартеновском производстве – это пыль и окись углерода. Запыленность на основных рабочих местах может составлять: на шихтовом дворе при разгрузке исходных материалов от 15 до 450 мг/м3 (ПДК равно 4 мг/м3), в разливочном пролете – от 18 до 80 мг/м3, в печном пролете – от 4,5 до 8,5 мг/м3. Следует отметить, что приведенные данные по печному пролету характеризуют состояние атмосферы цеха без применения кислорода для продувки ванны печи. Применение кислорода для интенсификации плавки (продувки ванны) в цехах, где нет резервов для увеличения пропускной способности дымовых трактов, обусловливает резкое увеличение неорганизованных выбросов в рабочую зону печного пролета. При применении двухванных печей запыленность в печном пролете цеха увеличивается примерно в 4 раза. Концентрация окиси углерода в рабочей зоне может составлять: в печном пролете 0,02 – 0,03 мг/л (ПДК оксида углерода равно 0,02 мг/л), в отделении смазки изложниц – 0,2 – 0,7 мг/л, на дворе и зложниц – 0,01 – 0,02 мг/л. Следует отметить, что в отделении смазки изложниц выделяются также пары тяжелых углеводородов (нефтепродуктов) в количестве 60 – 70 кг/ч. Тепловые воздействия в мартеновском цехе определяются наличием расплавленного металла и нагретых поверхностей технологического
270
оборудования. Интенсивность тепловых излучений на рабочих местах в печном пролете составляет 0,18 – 14,7 кВт/м2, на завалочной машине при загрузке печи – 0,7 – 6,3 кВт/м2, на задней площадке у сталевыпускного отверстия – 1,4 – 14 кВт/м2. Температура воздуха в теплый период года на рабочих местах у мартеновской печи может достигать 35 – 37оС, а у задней стенки при выпуске стали – и 45оС. Основными источниками шума в мартеновском производстве является мартеновская печь и оборудование, обеспечивающее ее работоспособность. Уровни звуковой мощности данного оборудования изменяются от 102 до 111 дБА.
Основные загрязнители воздуха в рабочей зоне в конвертерном производстве – это пыль, окись углерода и сернистый газ. Средние удельные величины вредных выбросов в помещение конвертерного цеха равны (в граммах на тонну стали): пыли – до 200, оксида углерода – от 100 до 360, сернистого газа – от 30 до 220. В миксерном отделении выделяется окись углерода и пыль в среднем соответственно в количествах 366 и 50 г/т чугуна. В отделении смазки изложниц выделяются также пары тяжелых углеводородов (нефтепродуктов) в количестве 60 – 70 кг/ч. Таким образом, все выполняемые в конвертерном цехе технологические, ремонтные и вспомогательные операции сопровождаются выделением пыли. В шихтовом отделении и в галереях шихтоподачи воздух загрязнен известняковой и рудной пылью, в миксерном отделении – графитовой и железорудной пылью, выделяющейся из миксеров и ковшей с чугуном. В конвертерном отделении пыль и дым выделяется при заливке чугуна и загрузке шлакообразующих в конвертер. Интенсивность тепловых излучений на рабочих местах в конвертерном отделении составляет 0,35 – 16,8 кВт/м2. Наибольшая интенсивность тепловых излучений (до 16,8 кВт/м2) отмечается при замере температуры, взятии пробы стали, наблюдения за выпуском стали и разделки сталевыпускного отверстия. В кислородно-конвертерных цехах основными источниками шума являются циркуляционные насосы, эксгаустеры, воздуходувки. Выпуск пара из котла-утилизатора также сопровождается выделением шума. Уровни звуковой мощности данного оборудования изменяются от 96 до 125 дБА.
Основные загрязнители воздуха в рабочей зоне в
электросталеплавильном производстве – это пыль, окислы углерода, азота и серы, а также цианиды и фториды. Средние удельные величины вредных выбросов из дуговых электросталеплавильных печей в помещение цеха равны (в граммах на тонну стали): пыли – до 2600, оксида углерода – до 540, окислов азота – до 108, окислов серы – до 0,6, цианидов – до 11,4 и фторидов
– 0,25. Пыль содержит окислы железа (от 53 до 80%), марганца (до 11%), кальция (до 6%) и магния (до 3%). Пыль представляет опасность для работающих, т.к. по фракционному составу эта пыль содержит около 80%
271
пылинок с размерами менее 7 мкм. Интенсивность тепловых излучений на
рабочих местах у электросталеплавильных |
печей составляет 0,35 |
– |
14,0 кВт/м2. Наибольшая интенсивность |
тепловых излучений |
(до |
14,0 кВт/м2) отмечается при осмотре подины и заправки печи перед загрузкой лома, а также при скачивании шлака. Температура воздуха в теплый период года на рабочих местах у печи может достигать 35 – 40оС. В электросталеплавильных цехах основными источниками шума являются сами дуговые печи и молота. Уровни звуковой мощности данного оборудования изменяются от 115 до 126 дБА. В дуговых электросталеплавильных печах шум дуги является основной составляющей уровня звуковой мощности печи. Шумообразование при горении дуги связано с пульсацией ее столба из-за колебаний температуры. Наибольший шум появляется в период плавки при расплаве шихты. Уровни звуковой мощности электропечей зависят от их емкости, состава расплавляемой шихты и подводимой к электродам мощности. Для печей емкостью 100 тонн уровни шума в среднем на 5 дБА больше, чем печей емкостью 40 т. Уменьшение уровня звука при плавлении мелкой шихты (по сравнению с плавлением крупной шихты) составляет 10 дБА и объясняется увеличением стабильности горения дуги в результате более равномерного и быстрого разогрева шихты. Возрастание подводимой к электродам мощности в 4 раза повышает уровень шума печи на 17 дБА. Так, с ростом мощности трансформатора с 25 до 32 МВА уровень звука 100 тонной дуговой печи увеличится на 5 – 7 дБА. Поэтому современная тенденция к увеличению мощности печных трансформаторов ведет к повышению шума печей [10].
Прокатное производство характеризуется сложностью и разнообразием механического оборудования и технологическими процессами, поэтому количество и уровень производственных факторов зависит от типа стана и условий обработки металла (состава механического оборудования, калибровки, скорости прокатки, уровня механизации и автоматизации и др.). Различают процессы горячей и холодной обработки металла давлением. К горячей прокатке относятся обжимные (блюминги, слябинги), сортовые (крупно-, средне и мелкосортные) и листовые (толсто- и тонколистовые) станы.
На станах горячей прокатки можно выделить два основных участка: отделение нагревательных устройств и становый пролет, где установлены рабочие клети.
Отделение нагревательных устройств характеризуется наличием таких вредных факторов на рабочих местах, как запыленность, загазованность, тепловые воздействия и шум. Основные загрязнители воздушной среды печных отделений – это пыль и окись углерода. Общее удельное количество окиси углерода, выделяемого технологическим
272
оборудованием в рабочую зону, может составлять до 200 г/т проката, а пыли
– до 16 г/т сортового проката и до 0,27 г/м2 прокатываемого листа. По фактическим замерам содержание окиси углерода на рабочих местах нагревальщика металла составляет в среднем, 13,4 мг/м3, а содержание железорудной пыли – 11,8 мг/м3. Интенсивность тепловых излучений на открытых рабочих местах у нагревательных устройств составляет: на блюминге 0,35 – 15,4 кВт/м2, в сортопрокатных цехах 0,17 – 14,0 кВт/м2 , в рельсобалочных цехах 1,05 – 16,1 кВт/м2 , в листопрокатных цехах 1,75 – 17,7 кВт/м2. Температура воздуха в рабочей зоне печных отделений достигает 40оС, а влажность обычно бывает не выше 34%. Основными источниками шума на участках нагрева являются сами нагревательные колодцы или печи, печные вентиляторы и транспортное оборудование. Уровни звуковой мощности данного оборудования изменяются от 103 до 114 дБА.
На участке прокатного стана основным загрязнителем воздушной среды является пыль. Источником пыли является прокатываемый металл и рабочие клети. Вторичная окалина в очаге деформации срывается рабочими валками и выбрасывается в атмосферу цеха, а также выделяется пыль при порезке раската и его транспортировке. Часть этой пыли (10 – 20%) удаляется из цеха через вытяжные аэрационные фонари, а остальная пыль находится в помещении цеха во взвешенном состоянии, а также осаждается на строительных конструкциях цеха и оборудовании. Общее удельное количество пыли, выделяющееся в отделение стана, составляет: для обжимных станов (блюмингов, слябингов и рельсобалочных) – до 80 г/т прокатываемого металла; для сортовых станов – до 100 г/т; для листовых станов – до 100 г/т или до 1,8 г/м2 прокатываемого листа. Интенсивность тепловых излучений на открытых рабочих местах у рабочих клетей составляет: на блюминге 0,18 – 14 кВт/м2, в сортопрокатных цехах 0,36 – 9,1 кВт/м2 , в рельсобалочных цехах 0,1 – 4,9 кВт/м2 , в листопрокатных цехах 0,35 – 7,0 кВт/м2. Интенсивность тепловых излучений на рабочих местах операторов постов управления может составлять 0,05 – 2,1 кВт/м2. Температура воздуха в рабочей зоне у прокатных станов достигает 32 – 36оС. Основными источниками шума на станах горячей прокатки являются рабочие клети, машины огневой зачистки, ножницы для резки проката, рольганги и холодильники. Уровни звуковой мощности данного оборудования изменяются от 97 до 127 дБА. При этом на обжимных станах уровень шума может достигать 127 дБА, на сортовых – 125 дБА, на листовых – 121 дБА.
Современный цех холодной прокатки листовой стали состоит из травильного, прокатного, термического и отделочного отделений. Характерной особенностью процесса холодной прокатки является: рулонный способ производства; непрерывность технологических операций (травление,
273
прокатка, дрессировка, отжиг, нанесение покрытий); возможность автоматизации технологических процессов, что приводит к существенному повышению безопасности.
На участке подготовки металла к холодной прокатке могут возникать следующие вредные факторы: повышенная температура воздуха (из-за наличия нагретых рулонов листовой полосы и работы непрерывного травильного агрегата), а также пары кислот, повышенный уровень шума
(механического, ударного и аэродинамического происхождения) и возникновение статического электричества (при промасливании поверхности травленых полос электростатическим методом). Источниками шума является все механическое оборудование участка подготовки (разматыватель рулонов, стыкосварочный агрегат, агрегаты поперечной и продольной резки листа, агрегат непрерывного травления, сушильное устройство, петлевой накопитель, приемный карман и др.), а также воздуходувки. Уровни звуковой мощности данного оборудования изменяются от 111 до 122 дБА.
В становом пролете установлены рабочие клети (двух-, четырех- и многовалковые). Благодаря высокой механизации и автоматизации непрерывные станы холодной прокатки обеспечивают безопасность труда персонала, ручной труд практически отсутствует. Однако, возможны механические порезы конечностей острыми кромками полосы как в процессе прокатки, так и при обрыве полосы из-за повышения натяжения между клетями (особенно на заправочной и рабочих скоростях) или же на сварных швах при плохой зачистке грата на гратоснимателе. Основные вредные факторы в становом пролете: пары смазочно-охлаждающей эмульсии
(которая испаряется из поверхности листа при прокатке и при неэффективной работе местных отсосов возможна повышенная концентрация этих паров в рабочей зоне) и повышенный уровень шума. Уровни звуковой мощности оборудования станового пролета изменяются от 113 до 126 дБА. Замеры уровня шума на постоянных рабочих местах стана 2000 показали, что лишь при холостом ходе шум ниже допустимых значений. На заправочной, рабочей и повышенной скоростях прокатки уровень шума изменяется в пределах от 90 до 103 дБА (нормативное значение – 80 дБА). Исследование уровней виброскорости и виброускорения на рабочих местах стана показало, что измеренные значения равны 82 – 91 дБ при норме 92 – 107 дБ (на частотах от 2 до 63 Гц). Поэтому эти уровни вибрации вполне безопасны для персонала станов холодной прокатки. После прокатки полосу сматывают в рулоны. Среднемассовая температура смотанной полосы в рулон составляет, например, для автолиста 350оС. Поэтому выделяется значительное количество теплоты, что требует применения средств теплозащиты.
274
Термическую обработку полосы применяют для придания металлу заданных механических и других свойств, нужной структуры и снятия внутренних напряжений. Для этого применяют агрегаты термической обработки (башенные и протяженные горизонтальные печи непрерывного действия, а также колпаковые печи периодического действия), в которых процесс осуществляется при температурах 720 – 850оС. На участке термической обработки могут возникать следующие вредные производственные факторы:
−при травлении (обезжиривании) применяют (в том числе и при электролитическом обезжиривании) кислоты, щелочи, растворы
тринатрийфосфата, эмульгаторы ОП-7, полиметилсилоксановой жидкости и др. при температурах 65 – 85оС, поэтому возможны выделения паров этих веществ в производственное помещение;
−при электролитическом обезжиривании к ванне подключают ток промышленной частоты, возможно поражение электрическим током. Необходимы меры пор электрической безопасности;
−так как в агрегатах термической обработки применяют защитные атмосферы, содержащие водород, то камеры выдержки этих агрегатов при нарушении герметичности могут быть причиной взрыва;
−в отделении термической обработки температура воздуха рабочей зоны в теплый период года выше допустимых норм, а в холодный период – соответствует нормам;
−так как в нагревательных печах применяют электрический нагрев, то возможно поражение электрическим током;
−при охлаждении полос применяют вентиляторы, подающие охлаждающую среду с большой скоростью, поэтому возникает повышенный уровень шума. Источниками шума являются вентиляторы и вакуумные насосы.
Уровни звуковой мощности оборудования термического участка изменяются от 93 до 116 дБА.
Отделение отделки листовых материалов и нанесения покрытий включает разнообразное оборудование окончательной отделки готовой продукции, упаковки и сдачи ее на склад. Операции отделки проводят на дрессировочных станах, режущих агрегатах, правильных и промасливающих машинах, чистильно-моечных машинах, агрегатах нанесения покрытия и травления, контрольно-перемоточных агрегатах, установках для упаковки металла и его взвешивания. Основными производственными факторами, действующими на персонал отделений отделки, могут быть:
повышенная температура воздуха в рабочей зоне (до 35оС) на участках нагрева полос при проведении горячего цинкования или лужения полос; пары кислот и щелочей в агрегатах обработки в горячем щелочном растворе и травлении в растворах соляной и серной кислотах; пары олова и
275
цинка, которые выделяются через неплотности в агрегатах покрытия; пары полимерных красок, которые выделяются при распылении этих красок или наклеивания пленок; при электролитическом покрытии возможно поражение электрическим током; большое количество паров растворителя полимерных красок в сушилке, которое также образует взрывоопасную смесь с воздухом и может быть причиной взрыва; при смотке готовых полос возможно образование статического электричества. Напряженность этого поля не превышает 500 кВ/м, однако при этом с повышением скорости смотки возможно появление искровых разрядов; повышенный уровень шума (до 107 – 109 дБА) на рабочих местах.
На участках ковки и штамповки основными производственными факторами являются:
повышенная температура воздуха в рабочей зоне и пониженная влажность;
высокая интенсивность тепловых излучений; загазованность и запыленность воздуха (железорудная пыль, окись углерода, дым и др. вещества); высокая физическая нагрузка, особенно при ручной ковке; шум и вибрация.
Условия труда на этих участках относятся к условиям горячих цехов. Отличительной особенностью ковки и штамповки является высокий уровень шума и вибрации, т.к. технологический процесс основан на ударном действии. При этом вибрация в основном действует на руки человека, вызывая локальное действие, что является основной причиной возможного возникновения вибрационной болезни. Уровни звуковой мощности данного оборудования изменяются от 117 до 140 дБА. Основными источниками шума, излучаемого прессами и молотами, является вибрация их станины и маховика. Причина этих вибраций – удары во всех подвижных сочленениях пресса или молота, возникающих в момент включения и в начале движения кривошипно-шатунного (или эксцентрикового) механизма. Процесс взаимодействия штампа или молота с металлом (заготовкой) также носит ударный характер, что усиливает шум. При штамповке или ковке уровни шума прессов или молотов на средних и высоких частотах возрастают в среднем на 8 дБА по сравнению с уровнем шума на холостом ходу.
Таким образом, приведенный анализ условий труда показывает, что на рабочих местах в основных переделах черной металлургии возникают следующие вредные факторы: пыль (угольная, железосодержащая, силикатная, графитовая); газообразные вещества (оксид углерода, сероводород, оксид азота и др.); парообразные вещества (пары кислот, щелочей, нефтепродуктов, едкого натра и др.); повышенная температура воздуха и пониженная влажность; высокая интенсивность тепловых излучений; шум и вибрация; высокая интенсивность физической нагрузки;
276
напряженная поза и монотонность труда. По сумме этих показателей (по результатам аттестации рабочих мест по условиям труда в соответствии с ДНАОП 0.05-8.04-92) условия труда на основных рабочих местах (агломератчиков, горновых, сталеваров, нагревальщиков, вальцовщиков, кузнецов и др.) относят к особо вредными и особо тяжелыми условиями труда. Поэтому для данной категории работающих предоставляются следующие льготы и компенсации: льготное пенсионное обеспечение по спискам №1 и 2 за счет средств госбюджета; доплаты за вредные условия труда от 12 до 24 % от тарифа на оплату труда; дополнительные дни к отпуску от 7 до 14 дней в соответствии с ДНАОП 0.05-5.02-77 и ДНАОП 0.05-8.03-74; а также молоко или пектиновые вещества (соки). Кроме этого отмечаются случаи досрочного выхода на пенсию в результате полученного профессионального заболевания в связи с засорением легких пылью, шумовой болезнью, действием вибрации и тепла. Все эти дополнительные расходы увеличивают себестоимость продукции и негативно влияют на экономические показатели работы предприятий черной металлургии.
4.Б2.1. Улучшение состояния производственной среды, снижение тяжести и напряженности трудового процесса
Общие требования. Площадки для строительства металлургических предприятий надлежит выбирать и размещение на них зданий и сооружений следует предусматривать как в соответствии с требованиями ДНАОП 0.03- 3.01-71 и СНиП II-89-80, так и ДНАОП 0.03-1.23-82 «Санитарные правила для предприятий черной металлургии №2527-82». При проектировании предприятий черной металлургии следует предусматривать зонирование территории. В производственной зоне следует выделять группы производств: коксохимическое, доменное, сталеплавильное (включая отделения непрерывной разливки стали), прокатное, трубное. Размеры санитарнозащитной зоны выбираются в соответствии с требованиями ДНАОП 0.03- 3.01-71. Коксохимическое, доменное и сталеплавильное производство, склады следует располагать к другим производствам (прокатные, трубные цехи, ремонтные службы и т.д.) с подветренной стороны с учетом «розы ветров». «Роза ветров» должна быть направлена вдоль прокатных цехов от склада готовой продукции к заготовочному стану, стрипперному отделению, сталеплавильному цеху и отделению непрерывной разливки стали. Основные производства черной металлургии имеют, как правило, одноэтажную конструкцию. В этих зданиях следует предусматривать пролеты 24, 30 и 36 м. Допускается применять пролеты 27 и 33 м для главных зданий конверторных цехов и зданий прокатных станов для сокращения излишков производственных площадей. Шаг основных колонн производственных зданий с мостовыми кранами рекомендуется принимать равным 12 м. Для
277
цехов основных переделов надлежит предусматривать функциональное разделение проемов на световые и аэрационные, при этом рекомендуется для целей аэрации применять поворотные створки (щиты облегченного типа), а для естественного освещения – неоткрывающиеся остекленные оконные переплеты. Посты управления должны быть оборудованы устройствами, обеспечивающими необходимые санитарно-гигиенические условия на рабочих местах. Вспомогательные помещения основных цехов, как правило, следует размещать в отдельно стоящих зданиях. При этом отапливаемые переходы из доменных и сталеплавильных цехов во вспомогательные здания следует проектировать надземными над уровнем рабочих площадок; из прокатных и трубных цехов, как правило, – подземными. Над участками цехов и емкостями с расплавленным металлом не допускается устройство внутреннего отвода вода. Полы на участках зданий прокатных и трубных цехов, подвергающиеся значительным механическим воздействиям, следует проектировать из стальных штампованных перфорированных плит. Подверженные воздействию теплового излучения конструкции в зонах разливки, транспортировки и обработки расплавленного или раскаленного металла, а также колонны у крюковых конвейеров проволочных станов и вблизи участка выдачи горячих рулонов листовых станов следует защищать экранами или эффективной теплоизоляцией. К этим участкам относят рабочие площадки литейного двора, сталеплавильных цехов над местами установки сталевозов и шлаковозных чаш, места под выпуском и разливкой ферросплавов и т.п. Для защиты заглубленных помещений (машинные залы, маслоподвалы, насосные, коммуникационные туннели и др.) от грунтовых вод должны применяться преимущественно дренажи. Гидроизоляцию следует предусматривать в тех случаях, когда устройство дренажей технически невозможно или экономически нецелесообразно.
Требования к доменному производству. При проектировании зданий литейных дворов доменных печей следует предусматривать полную механизацию работ по обслуживанию печи. Электротехнические помещения управления системами загрузки, печью и воздухонагревателями следует размещать о одном здании. Несущие конструкции комплекса доменной печи следует в основном проектировать стальными с учетом возможности их монтажа укрупненными блоками. Использование воздухонагревателей в качестве опоры для конструкций здания воздухонагревателей не допускается. Кровлю зданий комплекса доменной печи следует проектировать с уклоном 45о. В наружных стенах здания литейного двора и поддоменника следует проектировать на уровне пола рабочих площадок устройство аэрационных проемов, закрываемых в холодный период года.
Требования к сталеплавильному производству и непрерывной разливке стали (НРС). Конвертерные отделения и отделения НРС следует размещать в
278
отдельных зданиях для обеспечения естественной вентиляции. Конвертерные отделения с конвертерами малой емкости (до 100 т) или с одним-двумя конвертерами большой емкости следует по возможности блокировать с отделениями НРС. Конвертерное и миксерное отделения целесообразно размещать в одном здании. Миксерное отделение предпочтительно располагать со стороны заливочного пролета для сокращения ширины этого пролета (при транспортировке ковшей с чугуном в цех по поперечным железнодорожным путям). Рабочие площадки следует проектировать блочнощитовой конструкции. Перекрытие рабочих площадок, расположенных выше основной рабочей площадки конвертерных цехов, следует проектировать в виде металлических решеток. На конвертерной и разливочной площадках для отдыха работающих следует предусматривать специальные помещения, защищенные от шума и обеспеченные вентиляцией.
Требования к производству проката и труб. Вспомогательные мастерские (вальцешлифовальная, подшипниковая, ремонтная и др.) следует блокировать с прокатными и трубопрокатными цехами при условии обеспечения необходимой аэрации этих цехов. Расположение этих мастерских в зоне печей, рабочих клетей и раскатных полей не допускается. Указанные мастерские для листопрокатных, рельсобалочных и крупносортных цехов следует располагать в отдельных зданиях, соединенных закрытыми галереями со становыми пролетами. Цехи горячей прокатки для производства сортового проката целесообразно проектировать в параллельно расположенных зданиях с поперечными пролетами для складов заготовок и различными складами готовой продукции в торцах пролетов (с образованием полузамкнутых дворов). Прокатные (в первую очередь с мелкосортными, среднесортными и проволочными станами) цехи следует проектировать с приподнятой линией прокатки и устройством цокольных этажей. Во всех случаях следует, как правило, проектировать устройство подземных технических этажей. В технических этажах размещают различные подсобные помещения (маслоподвалы, вентиляционные камеры, насосные и др.). В цехах горячей прокатки необходимо предусматривать аэрационные фонари для естественной вентиляции и механическими системами для нормализации параметров микроклимата и удаления вредностей. Электромашинные помещения следует проектировать без аэрационных фонарей и устройств для обеспечения естественного бокового освещения. Остекление постов управления должно быть наклонным для улучшения обзора и предотвращения образования бликов. Остекление со стороны источников инфракрасного излучения (например, нагревательные печи, прокатные станы, рольганги и др.) должны быть охлаждаемыми. В прокатных цехах для безопасного передвижения людей устраивают проходы, переходные мостики и туннели. Выходы из туннелей должны быть расположены вне зоны
279
действия мостовых станов. Полы в прокатных цехах выполняют из прочных, износостойких материалов и должны быть ровными и нескользкими.
Требования к вентиляции производственных помещений предприятий черной металлургии. Вентиляцию, отопление и кондиционирование воздуха производственных зданий и сооружений (включая кабины крановщиков, помещения пультов управления и другие изолированные помещения) следует проектировать с обеспечением на постоянных рабочих местах и в рабочей зоне нормальных параметров микроклимата, а также концентрации вредных веществ в воздухе. Для ассимиляции тепловых избытков в помещениях следует предусматривать естественную вентиляцию (аэрацию). Количество воздуха, необходимого для обеспечения норм в рабочей зоне, следует определять расчетом: для помещений с тепловыделениями – по количеству избытков явного тепла; для помещений с тепло- и влаговыделениями – по количеству избытков явного тепла, влаги и скрытого тепла с проверкой на предупреждение конденсации влаги на поверхностях строительных конструкций и оборудования; для помещений с газовыделением – по количеству выделяющихся вредностей с условием обеспечения предельно допустимых концентраций. Количество выделяющихся в помещения вредных производственных веществ, тепла и влаги следует принимать по данным замеров или по расчетным данным. Для закрытых помещений (например, постов управления) и локализованных источников выделений (например, травильных ванн) применяют механическую вентиляцию. Определение количества воздуха для помещений предприятий черной металлургии по кратности воздухообмена нормами не допускается
4.Б3. Пожарная безопасность
Наличие на объектах черной металлургии большого количества легковоспламеняющихся и горючих жидкостей и газов, а также кокса, угля, мазута и других горючих материалов, хранящихся, транспортируемых и используемых в различных технологических процессах, создает потенциальную опасность загораний, пожаров и взрывов. Поэтому проблема обеспечения взрывной и пожарной безопасности объектов черной металлургии является весьма актуальной и имеет большое народнохозяйственное значение. Возникновение пожара на производстве наносит большой урон не только коллективу цеха и предприятия, где произошел пожар, но и другим предприятиям, использующим продукцию (например, лист) в качестве исходной заготовки для производства готового изделия (например, труб большого диаметра).
Пожарную опасность представляют все основные производства предприятий черной металлургии. Определенную сложность на объектах
280
черной металлургии вызывает категорирование в соответствии с требованиями ОНТП 24-86 доменных, сталеплавильных, прокатных и других цехов, имеющих большие площади. В указанных цехах пожароопасные помещения (кабельные подвалы, маслоподвалы, туннели и т.д.), расположенные ниже нулевой отметки, как правило, занимают более 10% общей площади здания и значительно превышает 3500 м2. В связи с этим здание по пожарной опасности должно быть отнесено к категории В и выполнено не ниже II степени огнестойкости. В соответствии с СНиП 2.01.02-85 в зданиях II степени огнестойкости колонны должны иметь предел огнестойкости не менее 0,75 ч, что для цехов черной металлургии невыполнимо. Применение железобетонных колонн исключается из-за наличия мостовых кранов, создающих значительные нагрузки, а нанесение на металлические колонны огнезащитных покрытий дорого и практически невыполнимо из-за больших площадей цехов. Поэтому нормативными документами разрешено при определении категорий пожарной опасности цехов черной металлургии не включать площади пожароопасных подвальных помещений в состав общей площади цеха при условии выполнения следующих мероприятий:
−перекрытия над подвалом, включая его несущие конструкции, должно иметь предел огнестойкости не менее 2,5 ч;
−все пожароопасные помещения в подвале должны быть оборудованы установками автоматического тушения пожаров;
−в подвалах и туннелях перед лестницами, ведущими в помещения категории Г и Д первого этажа, следует предусматривать тамбур-шлюзы;
−противодымная вытяжная вентиляция из подвальных помещений должна иметь выбросы непосредственно наружу или через отдельные шахты,
имеющие предел огнестойкости не менее 1 ч.
При выполнении данных условий все основные цеха (доменные, сталеплавильные, прокатные и др.) относятся к категории Г. Однако по пожароопасным свойствам применяемых в помещениях веществ и материалов некоторые помещения могут иметь и более высокую категорию. Например, к категории А в черной металлургии относят станции получения защитного газа и ацетилена, компрессорные горючих газов, газоповысительные, газорегуляторные, газораспределительные пункты, установки термической обработки в среде взрывоопасного защитного газа, отделения восстановительного отжига металлических порошков в среде взрывоопасного газа-восстановителя и др. К категории Б в черной металлургии относятся производства, где применяются и образуются горючие пыли: отделение дробления угля, подземные углеприемные ямы, закрытые галереи для транспортировки угля, установки подачи ПУТ в печь, отделения приготовления экзотермических смесей, склады сажи, дробильные
281
цехи руды с содержанием серы более 12% и др. К категории В в черной металлургии относятся помещения, где применяют или хранят горючие вещества: склады мазута, масел, маслоподвалы, станции централизованной смазки, помещения масляных трансформаторов, маслоохладительные установки, маслотуннели, склады угля, бункерные эстакады с подбункерными помещениями доменных печей, отделения приготовления шихты, электрокабельные и электромашинные помещения и др. К категории Д в черной металлургии относятся склады руды (с содержанием серы до 12%), цехи мокрого обогащения руд, водонасосные, насосные грануляции шлака, цехи холодной обработки металла (кроме магния и титана), копровые цехи и др.
Пожарная опасность доменного производства характеризуется наличием горючих газов (коксового, доменного, природного), горючих жидкостей, кокса, а также применением пылеугольного топлива (ПУТ) для вдувания в горн доменной печи. Определенную опасность представляет наличие жидкого чугуна и шлака. Во избежание образования взрывоопасных смесей в межконусном пространстве загрузочного устройства в него должен подаваться пар или инертный газ. Подача пара или инертного газа в межконусное пространство должна быть сблокирована с загрузочным устройством так, чтобы без подачи пара (газа) в межконусное пространство механизмы загрузки не работали. Помещение, в котором расположена распределительная установка для вдувания ПУТ, должно иметь естественную и принудительную вентиляцию. Распределительная установка и пылепроводы должны быть оборудованы подводом инертного газа. Расходные емкости для ПУТ закрытого типа должны быть оборудованы предохранительными клапанами. Воздухонагреватели доменных печей должны быть оборудованы приборами контроля температуры кожуха в купольной и подкупольной частях. При нагреве кожуха до температуры выше 150оС немедленно должны быть приняты меры по устранению причин, приведших к его перегреву. На газопроводах воздухонагревателей ближе к горелкам должны устанавливаться автоматические быстродействующие клапаны безопасности, срабатывающие при падении газа или воздуха ниже установленных пределов. Клапаны должны быть сблокированы с сигнализаторами падения давления газа и воздуха. Сигнализаторы должны быть звуковые и световые. При нагреве воздухопроводов горячего дутья до температуры выше 200оС немедленно должны быть приняты меры по устранению причин, приведших к их перегреву. В течение всего режима горения должен осуществляться контроль за наличием пламени в камере горения. В случае отрыва или затухания пламени подача газа должна быть немедленно прекращена. Температура ПУТ в верхней части бункера должна контролироваться контрольно-измерительными приборами с подачей звукового и светового
282
сигналов при самовозгоравнии пыли в бункере. Вдувание ПУТ и мазута в доменную печь при неисправной отсекающей и запорной арматуре и неисправных контрольно-измерительных приборах запрещается. Доменные печи должны быть оборудованы приборами контроля температуры кожуха по всей высоте печи, показания которых должны быть выведены на пульт управления печью. Для контроля за прогаром воздушных фурм они должны быть оборудованы сигнализирующими устройствами. Работа на прогоревших фурменных приборах запрещается.
Пожарная опасность сталеплавильного производства характеризуется наличием большого количества жидкого металла, а также наличием горючих отходящих газов, кабельных коммуникаций, маслоподвалов и маслотуннелей. В сталеплавильных цехах могут происходить взрывы и выбросы жидкого металла в результате загрузки в сталеплавильные печи и конвертеры влажного металлолома и шихты. Загрузка металлолома, например, в конвертеры осуществляется одной или двумя порциями (совками) и сразу после этого производится заливка чугуна. После заливки чугуна вся масса металлолома оказывается под жидким чугуном, в результате чего происходит интенсивное испарение влаги и выброс расплавленного металла. Выбросы жидкого металла могут происходить также и в том случае, когда в жидкий металл вводят влажные раскислители и легирующие материалы. При прогаре футеровок сталеплавильных агрегатов и фурменных аппаратов также возникает вероятность взрыва с выбросом жидкого металла при контакте расплавленного металла с влажными материалами. При выбросе расплавленный металл может быть источником воспламенения горючих материалов и способствует снижению несущей способности конструкций здания цеха. Несмотря на то, что нормативными документами в зданиях IIIа степени огнестойкости допускается применение незащищенных металлических колонн, на объектах черной металлургии в местах возможного пролива (выброса) жидкого металла целесообразно производить защиту несущих металлических колонн на высоту 1,5 – 2,0 м от уровня пола. Защиту колонн целесообразно выполнять огнеупорным кирпичом или бетоном. Предел огнестойкости защищенной колонны должен быть 2 – 2,5 ч. Также нижняя часть здания сталеплавильного цеха должна быть выполнена из железобетонных панелей. Для обеспечения пожарной безопасности кабельного хозяйства необходимо, в первую очередь, предусмотреть мероприятия [11, 12], исключающие возможность попадания жидкого металла в кабельные и масляные подвалы и туннели, так как это неизбежно вызовет пожар, а, следовательно, и остановку всего производства. При проектировании сталеплавильных цехов необходимо уделять внимание взрывоопасным помещениям. Так, газоочистки технологических газов мартеновских, электросталеплавильных печей и конверторов расположены в
283
помещениях, относящихся к категории А в соответствии с ОНТП 24-86. Поэтому в них необходимо соблюдать все требования по обеспечению пожарной и взрывной безопасности, предусмотренные для взрывоопасных помещений. Следует отметить, что в электросталеплавильном производстве значительную пожарную опасность представляют печные масляные трансформаторы, которые располагают вблизи печей для того, чтобы кабельная линия от низкой стороны трансформатора до головки электродержателя была короткой. При этом кабели или гибкие ленты токопроводов защищают от действия прямого теплового излучения, например, применением асбестовых щитов, или даже применением водоохлаждаемых токопроводов. Наиболее опасными местами токопроводов являются контакты. Поэтому для снижения контактного переходного сопротивления эти соединения следует выполнять с помощью сварки. В качестве профилактических мероприятий в трансформаторных камерах необходимо предусматривать стационарные установки тушения пожара и автоматическую пожарную сигнализацию [11]. Пожаротушение устраивают не автоматического действия (из-за возможных ложных срабатываний, которые могут вызвать короткое замыкание на проходящих в камере голых шинопроводах). Установка пожаротушения имеет ручной дистанционный пуск. Пожарная сигнализация выдает сигнал на пульт управления печью и, как правило, в пожарное депо.
Пожарная и взрывная опасность прокатного производства на предприятиях черной металлургии определяется следующими факторами:
наличием широко развитой сети кабельного хозяйства; наличием большого количества масла в маслоподвалах (в них находятся резервуары для хранения масел, станции подачи технологической смазки (их производительность на крупных станах достигает 1200 л/мин и более), насосно-аккумуляторные станции для гидроприводов стана, станции густой смазки и другие агрегаты маслохозяйства); наличием сети масляных гидроприводов, в которых постоянно поддерживается избыточное давление масла около 20 МПа, обратных маслопроводов, а также машин для промасливания прокатанной полосы перед сматыванием ее в рулон; применением горючих (взрывоопасных) газов в нагревательных печах и колодцах, при резке металла (кроме того, взрывоопасный водород образуется в травильных ваннах при обработке металла); применением взрывоопасного защитного газа (водородно-азотной смеси) при отжиге металла в безокислительной среде (для приготовления защитного газа вблизи прокатного стана работает станция защитного газа, помещения которой взрывоопасны); применением огнеопасных лаков, красок и других горючих покрытий и огнеопасных растворителей при создании антикоррозионных, влагостойких, теплозащитных, декоративных и других
284
покрытий на изделиях готового проката; наличием нагретого металла на станах горячей прокатки.
С учетом больших площадей прокатных и трубных цехов особое внимание при проектировании должно уделяться мероприятиям по обеспечению безопасной эксплуатации людей в случае пожара. При размещении вспомогательных помещений в этих цехах выходы из них должны предусматриваться непосредственно в цех, а не через какие-либо рядом расположенные другие помещения (т.к. согласно СНиП 2.01.02-85 предусматривать выхода для эвакуации через два соседних помещения не допускается). При этом в число эвакуационных выходов не допускается учитывать ворота, предназначенные для въезда железнодорожного транспорта. Учитывают только специальные калитки, расположенные рядом с этими воротами. Мастерские ревизии подшипников относят к категории Б и классу зоны В-Iа. Постоянное наличие в мастерской ЛВЖ и горючих жидкостей предъявляет повышенные требования по обеспечению пожарной безопасности, изложенные в разделе 3.6. В помещении мастерской допускается наличие не более 30 м3 керосина. При этом все резервуары с керосином должны быть оборудованы несгораемыми крышками и аварийным резервуаром для слива жидкости в случае пожара. Мастерские ревизии подшипников, а также установки для промывки подшипников в керосине площадью 500 м2 и более должны оборудоваться автоматическими установками пожаротушения. При меньшей площади мастерских они должны оборудоваться автоматической пожарной сигнализацией. Пожарную опасность в прокатных и трубных цехах представляют термические печи. В качестве защитного газа в ряде случаев в них применяется водородно-азотная смесь (95% водорода и 5% азота). Помещения цехов, в которых расположены печи, работающие с использованием водорода, должны быть оборудованы автоматическими газосигнализаторами с устройством световой и звуковой сигнализации. Эти печи должны быть герметичными. Затворы колпаковых печей должны исключать возможность выхода водорода наружу и подсоса воздуха в рабочее пространство печи. Печь должна быть оборудована прибором, измеряющим расход водорода. При падении давления под муфелем или под колпаком (для вакуумно-водородных печей) должна автоматически прекращаться подача водорода и включаться продувка инертным газом. При этом должна срабатывать звуковая и световая сигнализация. Наличие большого количества масла на прокатных станах вызывает необходимость установки в непосредственной близости от станов стационарных или передвижных воздушно-пенных огнетушителей. Однако в настоящее время все большее распространение получает оборудование прокатных станов стационарными установками пожаротушения (пенными или углекислотными) с ручным и дистанционным включением. Данный вид
285
противопожарной защиты является наиболее эффективным и предпочтительным. Внутренний противопожарный водопровод в помещениях прокатных и трубных цехов следует предусматривать в соответствии с требовании СНиП 2.04.01-85 «Внутренний водопровод и канализация зданий».
4.Б4. Разработка планов ликвидации аварий
В соответствии с требованиями ДНАОП 0.00-4.33-99 «Положение по разработке планов локализации и ликвидации аварийных ситуаций и аварий» для основных цехов, где имеются потенциально опасные объекты, должны быть разработаны планы локализации и ликвидации аварийных ситуаций и аварий. Такими объектами на предприятиях черной металлургии являются доменные печи, сталеплавильные агрегаты, нагревательные печи. Так же необходимость составления таких планов возникает при эксплуатации систем водоснабжения и водоотведения на предприятиях черной металлургии, так как там возможны затопления помещений, особенно заглубленных перекачечных станций. План ликвидации аварий должен состоять из следующих основных частей:
−аналитическая часть, в которой содержится анализ опасностей, возможных аварий и их последствий;
−оперативная часть, которая регламентирует порядок взаимодействия и действий персонала, спецподразделений в условиях аварии;
−приложения, в котором имеются соответствующие приказы по
предприятию о назначении должностных лиц, несущих ответственность за организацию и проведение принятых мероприятий.
Основные мероприятия по составлению плана ликвидации аварии изложены в разделе 4.А5., т.к. в горной промышленности предупреждение аварий имеет особую актуальность.
4.В. Энергетическая промышленность
Внастоящее время в условиях внедрения рыночных отношений произошли кардинальные изменения между руководителем предприятия (собственником) и работником в вопросах безопасности труда. Принятый закон Украины «Об охране труда» определяет принцип полной ответственности собственника за создание безопасных и безвредных условий труда, полного возмещения ущерба лицам, потерпевшим от несчастных случаев на производстве или от профессиональных заболеваний, приоритета жизни работника перед результатами труда (раздел 3).
Впроцессе подготовки специалиста невозможно познакомить его со всей информацией по вопросам охраны труда, так же, как невозможно в полном объёме изложить её в учебном пособии в рамках утверждённой
286
программы. Новая информация об охране труда накапливается быстро, что вызывает необходимость следить, начиная со стадии проектирования, за изложением вопросов охраны труда, как в переиздаваемых правилах, инструкциях, так и в периодических изданиях, касающихся вопросов охраны труда в энергетике.
Работа по охране труда на электростанциях, подстанциях, в цехах, мастерских возложена на соответствующих руководителей. Все эти лица несут персональную ответственность за обучение рабочих безопасным приёмам обслуживания и ремонта оборудования, их исправное состояние, безопасное состояние рабочих мест, своевременное испытание электрооборудования, инструментов, инвентаря и др.
Директора, главные инженеры, начальники цехов, участков, дежурные инженеры, начальники смен, диспетчеры предприятия и района сети обязаны выполнять предписания по безопасности лично и контролировать их выполнение подчинённым персоналом.
С целью улучшения работы, направленной на предупреждение несчастных случаев и аварий на производстве, во всех звеньях производственного механизма организованы службы охраны труда, структура и численность которых зависит от численности работающих.
Система управления охраной труда (СУОТ) является органической составной частью общей системы управления деятельностью производства. Объектом управления охраной труда является деятельность функциональных служб и структурных подразделений предприятия по обеспечению безопасных и здоровых условий труда на рабочих местах, производственных участках, в цехах и на предприятии в целом.
Управление охраной труда осуществляют руководители цехов, участков и служб. Ответственным за организацию и функционирование СУОТ являются руководители энергопредприятий по выработке, распределению и потреблению электроэнергии и их подразделений. Основную организационно-методическую работу по управлению охраной труда, подготовку управленческих решений и контроль за их реализацией ведет служба охраны труда, непосредственно подчиняющаяся руководителю предприятия.
Задачи охраны труда решаются на каждой ступени управления и передаются в виде управляющего воздействия от руководителя предприятия к бригадам (рис. 4.В1). Действия исполнителей контролируются по линии администрации и службами охраны труда, а по линии общественного контроля – профсоюзами.
В комплексе задач СУОТ рассматривают три основные направления:
287
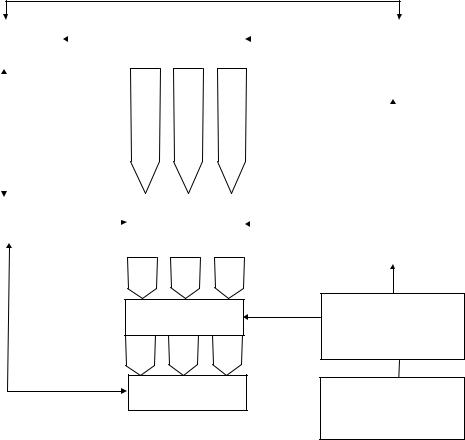
1.нормативно-техническая документация (НТД) – совершенствование норм и правил, инструкций, внедрение ССБТ, разработка стандартов предприятий;
2.условия труда – совершенствование безопасности средств производства и технологических процессов, санитарно-гигиенических условий; обеспечение средствами индивидуальной защиты создание оптимальных режимов труда и отдыха и т.д.;
3.кадры – обучение работающих, пропаганда охраны труда, воспитание кадров и укрепление дисциплины, организация лечебнопрофилактического обслуживания, предоставление работающим льгот и компенсаций за вредные и тяжелые условия труда.
Внешняя информация
|
Служба ОТ |
|
|
|
Руководитель |
|
|
Профсоюзный |
|
|||||
|
предприятия |
|
|
|
предприятия |
|
|
комитет |
|
|||||
|
|
|
|
|
|
|
|
|
|
|
|
|
|
|
|
|
|
|
|
|
|
|
|
|
|
|
предприятия |
|
|
|
|
|
|
|
|
НТД |
.Услов |
Кадры |
|
|
||||
|
|
|
|
|
|
|
|
|||||||
|
|
|
|
|
|
|
|
|
|
|||||
|
|
|
|
|
|
|
|
|
|
|||||
|
|
|
|
|
|
|
|
|
|
|||||
|
|
|
|
1 |
труда |
|
|
|
|
|
|
|
||
|
|
|
|
|
|
|
|
|
|
|
|
|
|
|
|
|
|
|
|
|
|
|
|
|
|
|
Профкомы |
|
|
|
Службы ОТ |
|
|
|
Руководитель |
|
|
|
|
|||||
|
|
|
|
|
|
подразделений |
|
|||||||
|
подразд. |
|
|
|
структурных |
|
|
|
|
|
||||
|
|
|
|
|
|
|
||||||||
|
|
|
|
|
|
|
|
|
|
|||||
|
|
|
|
|
|
подразделени |
|
|
Комиссия по ОТ |
|
||||
|
|
|
|
|
|
|
|
|
|
|||||
|
|
|
|
|
|
|
|
|
|
|
|
|
|
|
1 |
2 |
3 |
II ступень
Участки, цехи
1 |
2 |
3 |
Бригады
Уполномоченные
трудовых коллективов
I ступень
Уполномоченный
трудового
коллектива
Рисунок 4.В1. Организация административного и общественного контроля охраны труда
Задачи СУОТ решаются через основные функции управления, в результате чего формируется управляющее воздействие на объект управления
– охрану труда (рис. 4.В2).
Учет и анализ позволяют определить уровень охраны труда и эффективность функционирования СУОТ. Состояние ОТ как объекта управления характеризуется: наличием оптимальных условий труда, уровнем
288