
Neftegazovoe_stroitelstvo_2005
.pdf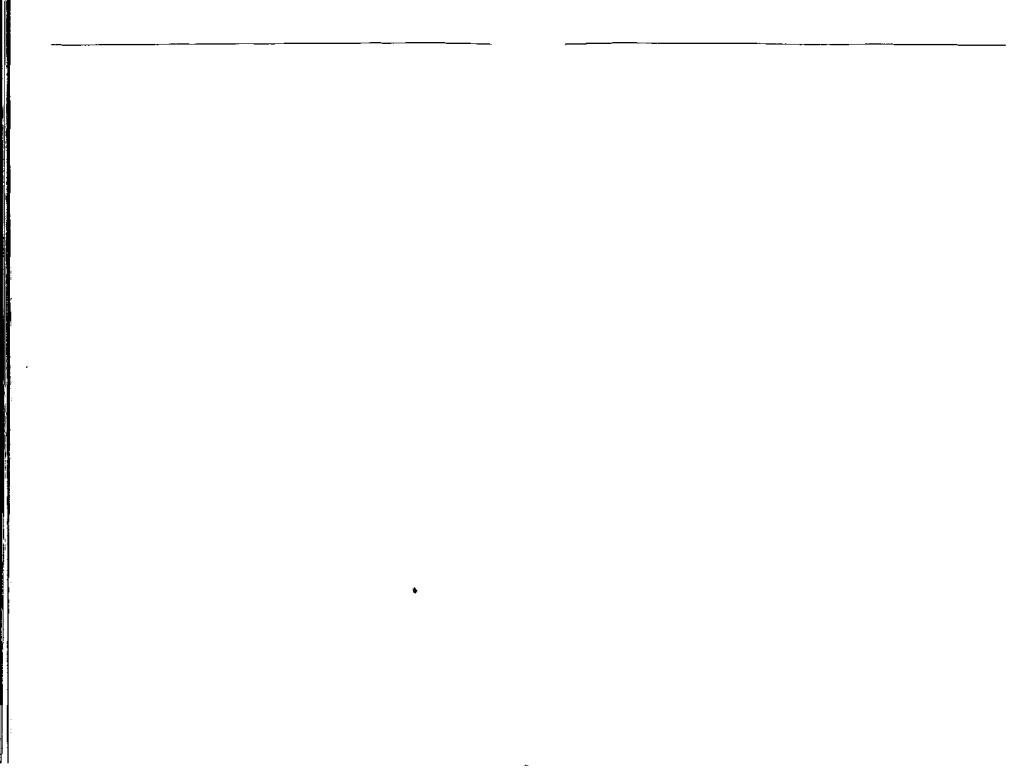
444 |
Часть III. Сооружение морских трубопроводов |
нарно, то навивка трубопровода осуществляется на судне, пришвартованном у береговой базы, где наращивают трубопровод;
•трубоукладочное судно идет в район трубоукладки. Во время перехода можно проводить контроль навивки трубопровода, состоящий в продувке и опрессовке трубопровода водой;
•конец трубопровода крепят к стояку платформы или сваривают с концом уже проложенного участка трубопровода;
•трубоукладочное судно перемещается по трассе и укладывает трубопровод. Развиваясь с барабана, трубопровод проходит через выпрямляющее устройство и по роликовой дорожке спускается через кормовой слип в воду.
Растягивающее усилие, необходимое при укладке, создается совместной работой натяжителя и механизма привода барабана.
В основное технологическое оборудование трубоукладочных судов барабанного типа входят натяжитель, выпрямляющее устройство и барабан с трубопроводом.
16.5. СВАРКА МОРСКИХ ТРУБОПРОВОДОВ
Ручные методы сварки МТ. При сооружении подводных переходов магистральных нефтегазопроводов широкое применение получила ручная электродуговая сварка. Этот метод сварки ввиду специфических особенностей строительно-монтажных работ продолжает применяться в условиях Каспийского моря при прокладке морских трубопроводов.
Технологии автоматической сварки МТ. Применение автоматических методов сварки при строительстве морских трубопроводов обусловлено прежде всего необходимостью обеспечения высокого качества сварных соединений в связи со сложностью условий эксплуатации и ремонта.
Соединения труб при строительстве могут выполняться с использованием различных организационных схем, например:
•с предварительной сваркой труб в двухили четырехтрубные секции, которые затем сваривают в непрерывную нитку;
•сваркой отдельных труб в непрерывную нитку.
Сварка выполняется одним из следующих способов:
•автоматическая или полуавтоматическая сварка в среде защитного газа плавящимся или неплавящимся электродом;
•автоматическая или полуавтоматическая сварка самозащитной проволокой с принудительным или свободным формированием металла шва;
Глава 16. Монтаж морских трубопроводов |
445 |
•ручная сварка электродами с покрытием основного типа или с целлюлозным покрытием;
•электромонтажная сварка непрерывным оплавлением с послесварочной термической обработкой.
При сварке двухили четырехтрубных секций на вспомогательной линии может применяться также автоматическая сварка под флюсом.
Перед началом работ принятые к использованию способы сварки, сварочное оборудование и материалы должны быть аттестованы в присутствии представителей Заказчика на трубоукладочном судне. Сварщики должны быть аттестованы в соответствии с действующими нормами. Сварщики, выполняющие сварку под водой, должны пройти обучение и специальную аттестацию в камере под давлением с имитацией условий работы на дне моря.
Кольцевые сварные соединения подвергают 100% радиографическому контролю с дублированием 20% стыков автоматизированным ультразвуковым контролем с записью результатов контроля. При толщине стенки свыше 25 мм 100% ультразвуковой контроль является обязательным.
Приемка сварных соединений производится в соответствии с требованиями технических условий на сварку и неразрушающий контроль труб, включающих нормы допустимых дефектов в сварных швах.
16.6. ИЗОЛЯЦИЯ И БЕТОНИРОВАНИЕ СТЫКОВ ПОДВОДНЫХ ТРУБОПРОВОДОВ
Как показала практика, себестоимость заполнения технологических разрывов высокопрочным быстросхватывающимся бетоном не превышает затрат в случае применения в тех же целях пенополиуретана или мастик. Бетон более пригоден для использования в морской среде без опасности его разрушения и обеспечивает надежную защиту сварных стыков труб. По своим прочностным и весовым характеристикам применяемый бетон отвечает всем требованиям и является экологически безопасным по отношению к чувствительным экосистемам морских акваторий.
Применение высокопрочного быстросхватывающегося бетона для заполнения разрывов пригружающего покрытия позволяет достичь оптимального распределения напряжений на стыках и повысить их защищенность.
Уретановые составы, используемые в качестве добавок к бетонной смеси, не всегда пригодны для использования в морской среде, осо-
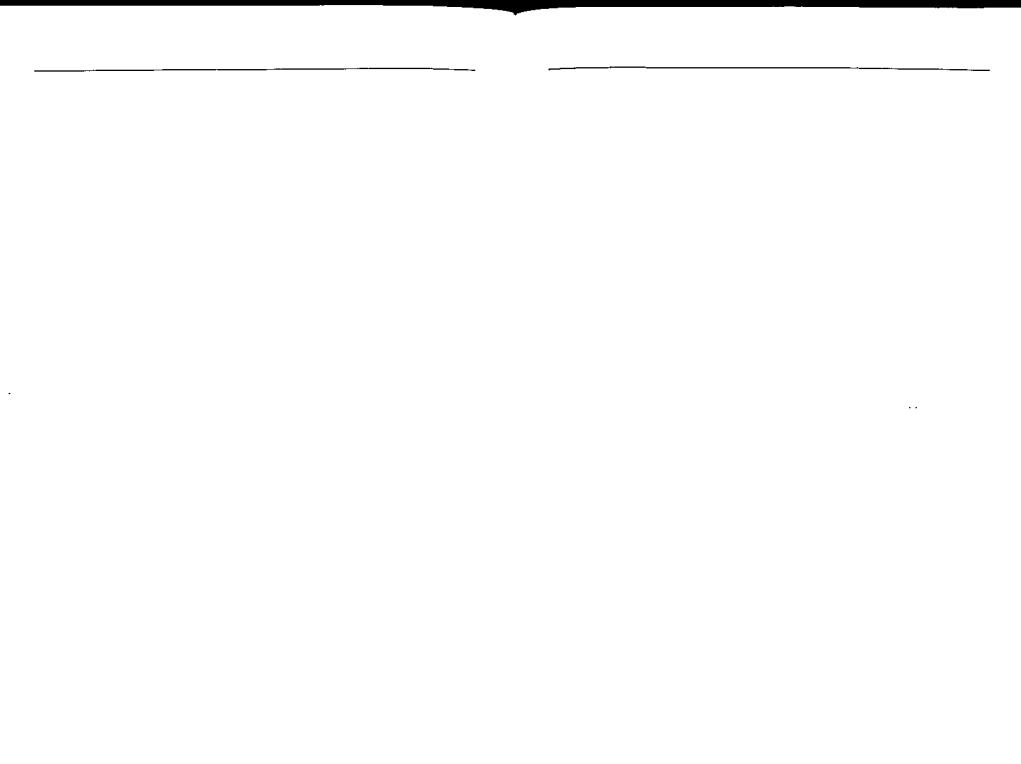
446 Часть III. Сооружение морских трубопроводов
бенно при длительном сроке службы трубопровода, который может достигать 80 лет. Полиуретановые пенопласты характеризуются слишком малой плотностью, а утяжеленные уретановые композиции представляют потенциальную биологическую опасность и не полностью совместимы с антикоррозионной изоляцией труб.
Поэтому при сооружении подводных трубопроводов нередко применяют высокопрочный быстросхватывающийся серобетон, разработанный и запатентованный Горным бюро США. Патентованный серобетон представляет собой цементный состав на основе модифицированной серы с обычными наполнителями. Бетонную смесь выпускают в гранулированном виде и расфасовывают в мешки с грузовыми петлями для удобства перевалки с помощью кранов или погрузчиков, оборудованных вилочными захватами. Поскольку гранулы нечувствительны к погодным условиям, то не требуется предусматривать специальные мероприятия по перевалке и хранению бетонной смеси.
Технология бетонных работ заключается в следующем. Гранулы бетонной смеси через бункер загружают в битумный котел и нагревают до температуры плавления, составляющей 115—120 °С. Такая температура не опасна для муфт с термоусадкой и антикоррозионной пленки, используемых для изоляции сварных швов. Для нанесения покрытия из высокопрочного быстросхватывающегося бетона на монтажные стыки труб можно применять оборудование, используемое при работах с горячими мастиками.
После расплавления гранул бетонную смесь заливают в многоразовую опалубку, установленную вместе с арматурой над обетонируемым стыком трубопровода. Во избежание образования пустот бетон уплотняют с помощью вибраторов. После заполнения формы бетоном для ускорения отвердения смеси поверх нее обычно устанавливают охлаждающий водяной кожух, который затем удаляют.
На процесс отвердения уходит от 4 до 10 мин, после чего бетон приобретает прочность на сжатие порядка нескольких тысяч кПа, а еще через час — твердость, соответствующую твердости бетонного покрытия труб из портландцемента. %
16.7. МЕТОДЫ И ОБОРУДОВАНИЕ ДЛЯ ЗАГЛУБЛЕНИЯ ПОДВОДНЫХ ТРУБОПРОВОДОВ
Трубопроводы, прокладываемые по морскому дну без заглубления, в большей степени подвержены воздействиям подводных течений и коррозии, чем заглубленные в грунт.
Глава 16. Монтаж морских трубопроводов |
447 |
В настоящее время используютдва основных метода заглубления подводных трубопроводов в грунт. Первый аналогичен наземному: морской трубопровод укладывают в заранее разработанную траншею, которую затем засыпают. Недостаток этого метода заключается в том, что земснаряды не могут быть применены при работе на глубинах более 20 м.
При втором способе трубопровод укладывают непосредственно на дно, а специально оборудованное судно следует вдоль этой трассы, размывая и отсасывая из-под него грунт при помощи мощных струйных насосов с давлением около 100 кг/см2. Основной недостаток этого способа заключается в необходимости использования судов со сложным автоматизированным оборудованием, стоимость сооружения и эксплуатации которых высока из-за узкой области их применения.
В последнее время широкое применение получил взрывной метод, который позволяет образовывать траншеи протяженностью 1000—2000 м и глубиной около 2 м. Этот метод применяют самостоятельно и в сочетании с первым при разработке скальных и труднодоступных участков трассы. Окончательная доводка траншеи осуществляется грейферным земснарядом. Засыпка траншеи в этих случаях производится при помощи специального устройства, буксируемого по дну, фунтом, извлеченным на первом этапе работ.
Технология заглубления подводных трубопроводов, предварительно проложенных по дну водоема, включает в себя следующие операции:
•спуск рабочего органа или всего трубозаглубительного агрегата на трубопровод;
•предварительную установку агрегата на трубопроводе;
•пуск механизмов для разработки грунта и заглубления агрегата
сего установкой в рабочее положение;
•пуск ходовых и грунторазрабатывающих механизмов агрегата и заглубление трубопровода;
•повторные (при необходимости) проходы агрегата с реверсированием направления его движения для заглубления трубопровода на требуемую величину;
•демонтаж трубозаглубителя с трубопровода и его подъем на базовое судно.
Одним из основных параметров, определяющих универсальность трубозаглубителя, возможную глубину работы и сложность его конструкции, является степень его автономности при работе. По этому параметру трубозаглубители можно подразделить на следующие классы:
1.Грунтозаборные устройства, конструктивно связанные с судномносителем жесткой рамой, по которой производится подача рабочей жидкости или транспортировка разработанного грунта.
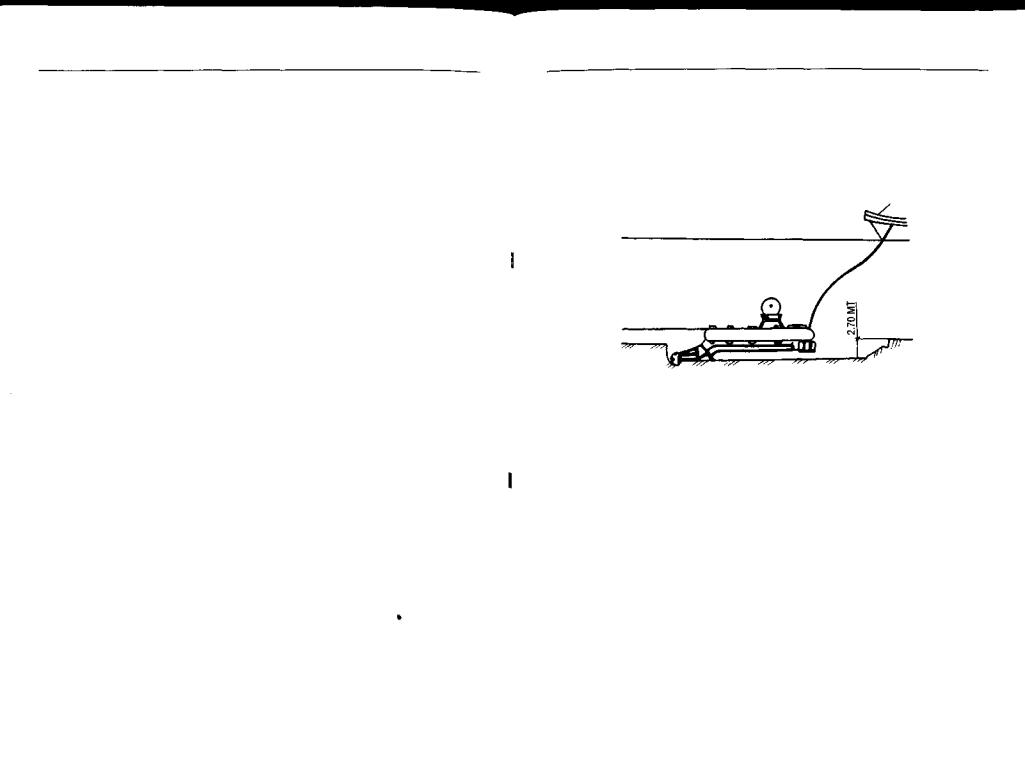
448 |
Часть III. Сооружение морских трубопроводов |
2.Грунтозаборные устройства, конструктивно не связанные с суд- ном-носителем; спуск их на трубопровод производится с борта судна-носителя.
3.Автономные земснаряды с погружным гидроили электроприводом рабочих устройств и движителей.
Трубозаглубители подразделяются по следующим принципам действия: разработка грунта под трубопроводом и его транспорт к надводному суднудля дальнейшей доставки к месту отвала; разработка и отвал грунта непосредственно за бровку траншеи; изменение физикомеханических характеристик грунта путем его псевдоразжижения подачей большого количества воды в грунтовой массив или ликвидации структурных связей между частицами грунта за счет приложения к нему вибрационных нагрузок.
В последнем случае грунт проявляет тиксотропные свойства, обеспечивающие погружение трубопровода до более плотного слоя грунта или до момента прекращения воздействия на грунтовой массив. По способу воздействия на грунтовой массив при его разработке трубозаглубители делятся на агрегаты с механическими, гидравлическими и гидропневматическими рыхлителями. Грунт из траншеи удаляется путем гидромониторного размыва; размывом грунта гидропневматической струей; всасыванием разрыхленного грунта гидроэжектором, пневмоэжектором или землесосами.
Земснаряды. Земснарядфирмы «Sub Sea oil Services» —S.S.O.S. (Италия), также называемый S-23, общей длиной 17 м может работать на глубине до 60 м. Для транспортировки земснаряд может быть разобран на отдельные блоки, наибольший из которых весит 35 т (рис. 16.7.1).
Земснаряд S-23 оборудован средствами плавучести, благодаря которым его можно буксировать на место производства работ и погружать на дно путем заполнения водой балластных резервуаров. Отрицательную плавучесть земснаряда, который на воздухе весит 61т, можно регулировать в пределах от 0 до 50 т.
Земснаряд S-23 объединяет свойства бульдозера и водолазного колокола. На понтоне, имеющем затопляемые продольные отсеки, смонтирована сферическая водолазная камера, из которой водолаз осуществляет контроль и управление производством подводно-техни- ческих работ. Внутри камеры поддерживают нормальное атмосферное давление. Механическую работу под водой и разработку траншеи вдоль трассы осуществляют фрезерным рыхлителем, который при помощи кронштейна закреплен на переднем конце понтона. Рыхлитель может перемещаться в вертикальном или горизонтальном направлении, обеспечивая глубину прорези от 0 до 2,4 м и ширину от 1,8
Глава 16. Монтаж морских трубопроводов |
449 |
до 4,5 м. Фрезерный рыхлитель спроектирован для образования прорези с наклонными стенками в дне из мягкого грунта. Рабочая скорость движения снаряда составляет 128 м/ч, производительность по грунту в зависимости от его вида — до 250 м3/ч. Снаряд S-23 перемещают по дну при помощи двух лебедок и тяговых тросов, прикрепленных к якорям или сваям. Данный способ перемещения можно использовать при любом рельефе дна.
Рис. 16.7.1. Земснаряд S-23
Снаряд S-23 обслуживает надводное судно, оснащенное генератором. Силовой кабель, магистраль воздухоснабжения и коммуникационный кабель, соединяющие S-23 с судном, скреплены вместе.
Для заглубления трубопроводов, предварительно проложенных по дну, итальянская компания «Sub Sea Oil Services» разработала подводный земснаряд В-70. В отличие от S-23 для его установки не требуется обслуживающий персонал. Машину собирают на трубопроводе, лежащем на дне моря. При помощи затопляемых отсеков салазки машины устанавливают над трубопроводом таким образом, чтобы обеспечить возможность разработки под ним грунта посредством 4 фрезерных рыхлителей, расположенных подтрубопроводом по обе стороны от его продольной оси. Разрабатываемый грунт удаляют по дополнительному трубопроводу с помощью сжатого воздуха. Разработке грунта способствуют водяные сопла, установленные вокруг рыхлителей. Компрессор расположен на борту вспомогательного судна, которое служит также для перемещения снаряда В-70 при помощи тягового троса и лебедки с гидравлическим приводом. Скорость перемещения над трубопроводом может достигать 30 м/ч.
Компанией «American Marine and Mashinery» (США) разработан земснаряд с поднимаемой домкратами рабочей платформой, предна-
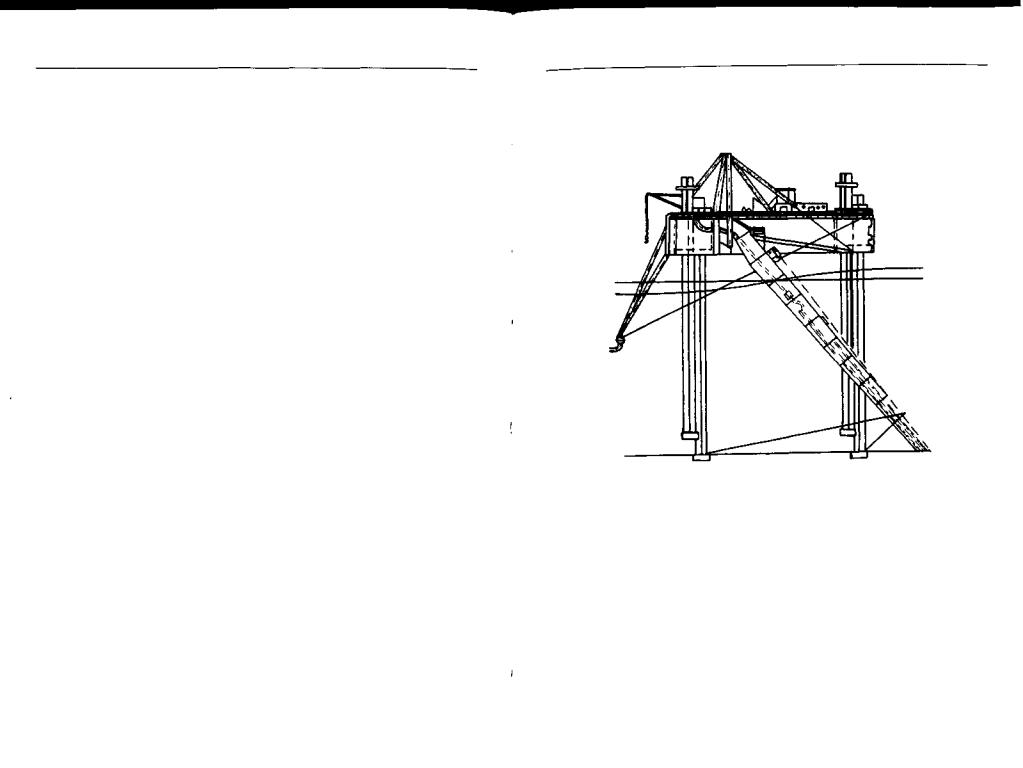
450 |
Часть III. Сооружение морских трубопроводов |
значенный для работы в зоне прибоя. Земснаряд снабжен опорами высотой Эми может работать на глубинах до 6 м. Нижний корпус установлен на восьми тракторных колесах, обеспечивающих перемещение земснаряда вдоль разрабатываемого котлована без опускания платформы на домкратах. Дизельный двигатель мощностью 500 л. с. приводит в движение установленный на палубе насос с трубопроводами диаметром 25 см.
Траншеекопатели. В ФРГ разработан подводный траншеекопатель, предназначенный для работы на глубинах до 4800 м. Траншеекопатель смонтирован на гусеничном ходу и связан шлангом с промежуточной подводной станцией, расположенной на глубине 48,0 м. Вынимаемый из траншеи грунт поступает в промежуточную станцию, а оттуда его перекачивают на вспомогательное надводное судно.
На ходовой части траншеекопателя установлена кабина управления контрольными приборами, системой освещения и телекамерой. К кабине присоединена стрела длиной 15 м с укрепленной на ней землесосной или режущей головкой. Поворачивая кабину, можно подготовить траншею шириной до 20 м. Подъем и опускание стрелы с землесосной головкой осуществляют гидравлическим приводом.
Внутри промежуточной станции, выполненной в виде вертикальной капсулы длиной 25 м, поддерживают атмосферное давление. Капсулу располагают таким образом, чтобы пульпа поступала только за счет перепада гидростатического напора. В промежуточной станции происходит разделение грунта и воды, которые затем подают на надводное судно.
В основании капсулы расположена балластная цистерна, при помощи которой капсулу можно поднимать и опускать на любую заданную глубину. С траншеекопателем капсула соединена силовыми кабелями и проводами системы управления. С надводным судном капсула связана трубопроводом для подачи разработанного грунта на поверхность и трубопроводами большого диаметра, обеспечивающими доступ в капсулу обслуживающего персонала, а также подачу необходимых материалов. По этим же трубопроводам проходят силовые кабели и коммуникации.
Платформы. Голландской фирмой «I. H.C.Holland» создан проект шагающей платформы, предназначенной для дноуглубительных работ в условиях, когда плавучий земснаряд не способен их выполнить из-за сильных волн и течений.
L-образный понтон имеет три опоры. Подъемная рама разрыхлителя прикреплена так, что может поворачиваться между двумя сторонами понтона. Поворот рамы производится с помощью лебедок или
Глава 16. Монтаж морских трубопроводов |
451 |
стальных канатов, а ее подъем и спуск — с помощью гидравлических цилиндров (рис. 16.7.2). Грунтовой насос установлен внутри рамы разрыхлителя. Понтон имеет машинное отделение, рабочее место для ремонта разрыхлителя, бункер, склад и жилые помещения.
Рис.16.7.2. Общий вид шагающей платформы с механическим разрыхлителем
Платформа предназначена для разработки грунта на максимальной глубине 25 м; ширина прорези грунта при одном проходе равна 41 м.
Устройство разрыхлителя рассчитано на большие напряжения, что позволяет эффективно разрабатывать грунт, состоящий из уплотненного песка, глины и скальных пород. В мягком грунте производительность можно увеличить установкой большого разрыхлителя.
Платформа перемещается при помощи трех двойных роторных свай. Максимальная скорость ее передвижения около 8,80 м/ч. Наибольшая длина L-образного понтона 30 м. Рама разрыхлителя в поднятом положении выступает на 22 м. Длина опоры 38 м. При глубине всасывания 25 м и проникании разрыхлителя на 2 м платформу можно поднять на 4 м выше уровня воды. Грунтовой насос и разрыхлитель приводятся в действие электродвигателем мощностью 500 л.с.
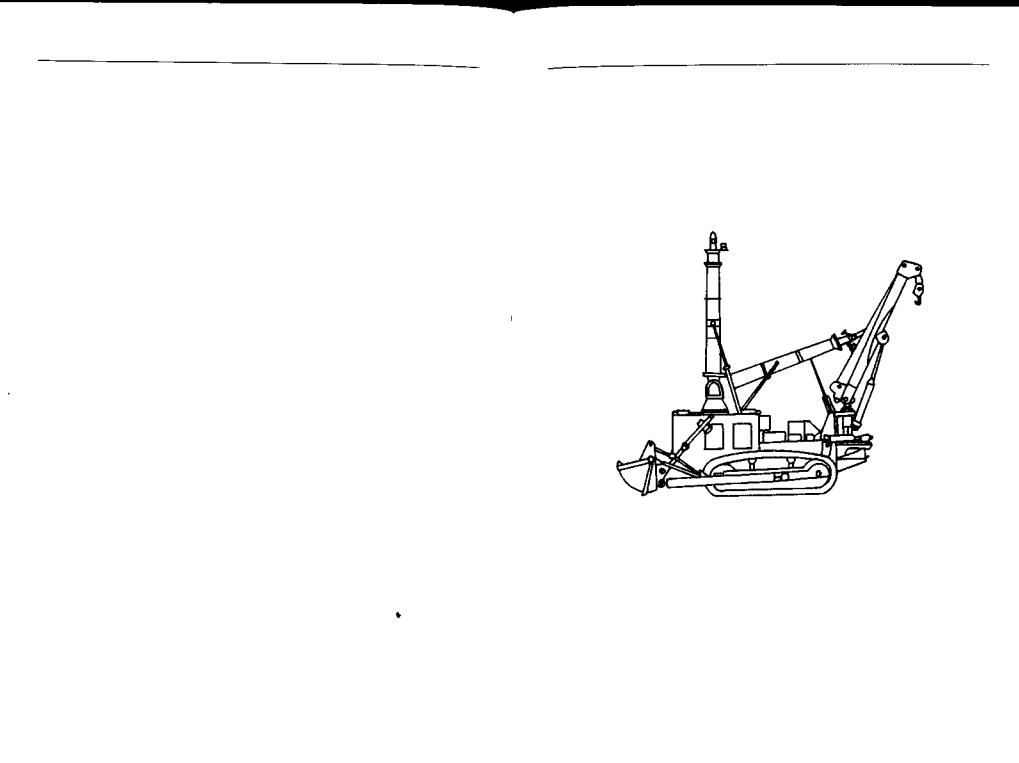
452 |
Часть III. Сооружение морских трубопроводов |
Буровзрывной метод. При разработке подводных траншей в скальных породах морского дна часто применяют буровзрывной метод. Однако в сложных условиях приливных течений и волнений моря не всегда возможно проведение буровых работ со специальных судов. В таких случаях приходится находить новые решения и создавать специальные технические средства.
По заказу компании ARAMCO фирма DRENCO (ФРГ) предложила способ разработки скальной породы на дне моря при помощи буровзрывных работ и черпания.
С учетом неблагоприятных метеорологических условий в районе строительства была применена самоподнимающаяся платформа. Корпус платформы представляет собой сварную конструкцию, опирающуюся на 3 опоры решетчатого типа. На нижнем конце опоры смонтирован резервуар диаметром 5,5 м и высотой 3,0 м. Буровые станки установлены на двух вращающихся консолях длиной 38 м, представляющих собой спаренные балки коробчатого сечения. Опорой консолей служит стальная конструкция высотой 23 м с двумя поворотными мачтами. На этих мачтах установлено по два гидроцилиндра, обеспечивающих поворот консолей на 180°. Общий вес платформы, включая опоры, дополнительные устройства для буровых станков, консоли и надстройки, составляет около 770 т.
Буровой станок смонтирован на подвижнойтележке с электрическим приводом. Тележка может перемещаться по всей длине консоли. Буровая колонна, состоящая из обсадной трубы, жестко соединенной с буровой тележкой и подвешенной внутри нее на тросе буровой штангой, проходит сквозь 1,5-метровую щель между коробчатыми балками. Буровая колонна имеет переменное сечение: в верхней части диаметр 550 мм, в средней — 380 мм. Нижняя часть длиной 3 м и диаметром 185 мм снабжена кольцевой буровой коронкой. Для дробления керна внутри обсадной трубы вращается тяжелая буровая штанга длиной 6 м и весом 1,8 т. Штанга, подвешенная на тросе, может передвигаться независимо от обсадной трубы. Трехступенчатая буровая коронка штанги в процессе бурения опережает обсадную трубу примерно на 20 см. Крутящий момент обсадной трубы передается на коронку штанги через три косых захвата.
После достижения заданной глубины бурения буровую штангу поднимают и открывают загрузочный клапан в обсадной трубе. В освобожденную полость обсадной трубы опускается взрывной заряд весом 12,5 кг. После подъема обсадной трубы примерно на 4,5 м над уровнем дна приводят в действие электрический запал.
После взрыва буровой станок переводится в следующую позицию поворотом консоли или передвижением буровой тележки. Время бу-
Глава 16. Монтаж морских трубопроводов |
453 |
рения одного шпура в зависимости от глубины бурения и крепости породы составляет 10—15 мин. С одной позиции можно пробурить до 440 шпуров, что соответствует 2400 м2 взрываемой поверхности.
Черпание раздробленной скальной породы производили землечерпалкой, подготовленной для работы на большой глубине при значительных нагрузках.
Подводный бульдозер. Японской компанией «Komatsu» разработан подводный бульдозер, который может успешно работать на глубинах до 60 м (рис.16.7.3).
Рис.16.7.3.Подводныйбульдозер«Komatsu»
Бульдозер оснащендвигателем с турбонадувом модели «Komatsu S6D155». В отличие от двигателя стандартного исполнения были модифицированы вентилятор и воздухопровод, а также установлен воздушный компрессор, обслуживающий систему управления.
Большая мощность и тяжелый вес машины в целом обеспечивают высокую производительность разработки выемок с перемещением большого количества грунта.
Для предотвращения уноса перемещаемого грунта водой подводный бульдозер оснащен фартучным устройством для захвата и перемещения грунта. В корпусах силовой линии (гидротрансформатор, коробка передач, карданная передача и т. д.) предусмотрен регулировочный механизм, с помощью которого автоматически создают внут-
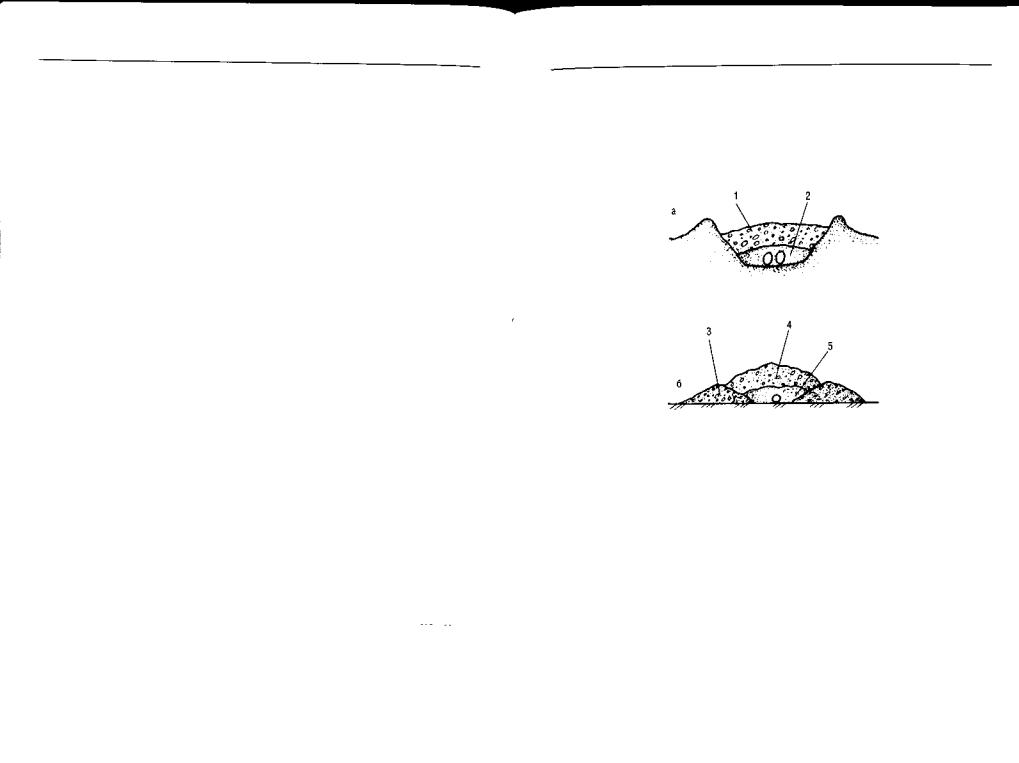
454 |
Часть III. Сооружение морских трубопроводов |
|
реннее давление, равное наружному давлению воды 0,3-0,45 кг/см2 для защиты уплотнений и предупреждения попадания воды.
Плужные устройства. Применение плужных устройств является одним из наиболее распространенных способов заглубления морских трубопроводов. При этом обеспечивается высокая производительность и минимальное воздействие на окружающую среду, так как разрабатываемый грунт располагается на бровках траншеи и не рассеивается в воде.
При укладке трубопровода с трубоукладочного судна плужное устройство можно протаскивать непосредственно этим же судном.
Если у трубопровода бетонное покрытие отсутствует, то для исключения повреждения изоляции трубопровод должен располагаться над плугом. Во избежание появления вертикальной составляющей тягового усилия, действующего на плут, увеличивают длину провисающего участка укладываемого трубопровода путем создания дополнительного натяжения или оснащения понтонами.
Прокладка трубопровода с заглублением в грунт может осуществляться также способом протаскивания трубопровода по дну моря, вблизи дна или в виде упругоискривленной змейки. При этом плуг устанавливают перед оголовком протаскиваемой плети трубопровода. Может быть также использована прокладка трубопровода путем протаскивания длиномерной плети с одновременным заглублением
вдно.
16.8.ЗАСЫПКА МОРСКИХ ГАЗОПРОВОДОВ
На рис. 16.8.1 изображены возможные схемы защитной засыпки трубопроводов.
Технология подачи и точного размещения частиц твердых пород на дне моря основана на применении труб специальной конструкции для засыпки таких материалов с борта судна. Конструкция системы, оснащенная видеокамерами и импульсными приемопередатчиками, позволяет следовать вдоль трассы подводных трубопроводов, уложенных на глубинах до 160 м. С помощью этой системы можно не только точно разместить материал засыпки, но и регулировать е?о толщину.
Метод засыпки песком и частицами твердых горных пород можно использовать также для снижения теплоотдачи продуктов, транспортируемых по магистральным трубопроводам и по выкидным линиям между подводными скважинами и установками по переработке.
В качестве примера можно привести нефтяное месторождение Несс в Северном море, эксплуатируемое фирмой Mobil North Sea Ltd,
Глава 16. Монтаж морских трубопроводов |
455 |
на котором трубопроводы первоначально не были изолированы, а лишь уложены в траншеи, отрытые траншеекопателем на гусеничной тележке. После начала эксплуатации из-за низкой температуры потока (6°С) на стенках трубопроводов стал осаждаться парафин и увеличилась вязкость нефти, было отмечено снижение добычи, сопровождавшееся резким падением давления в системе.
Рис. 16.8.1. Защитные насыпи над трубопроводами; а — для морского трубопровода, уложенного в траншею; б — для морского незаглубленного трубопровода; 1 — слой из частиц твердой породы; 2 — слой песка; 3 — бермы из частиц твердой породы; 4 — защитный слой из частиц твердой породы; 5 — песчаная смесь
В соответствии с технико-экономическим обоснованием для обеспечения защиты и теплоизоляции трубопроводов была применена засыпка песком и гравием. С учетом использования существующей траншеи слой засыпки включал в себя 0,3 м песка и 0,5 м отсортированной горной породы. Для выполнения работ выбрали судно Seaway Sandpiper, оборудованное специальной трубой для точного размещения материала засыпки.
Фактическая длительность работ составила 30 суток. Всего было уложено 28 500 т песка и 3120 т горной породы. В течение недели после завершения работ температура продукции на выходе из трубопровода увеличилась до 23°С. При дальнейшей эксплуатации температура колебалась в диапазоне 19—24°С. Таким образом были решены проблемы отложения парафина и высокой вязкости нефти.
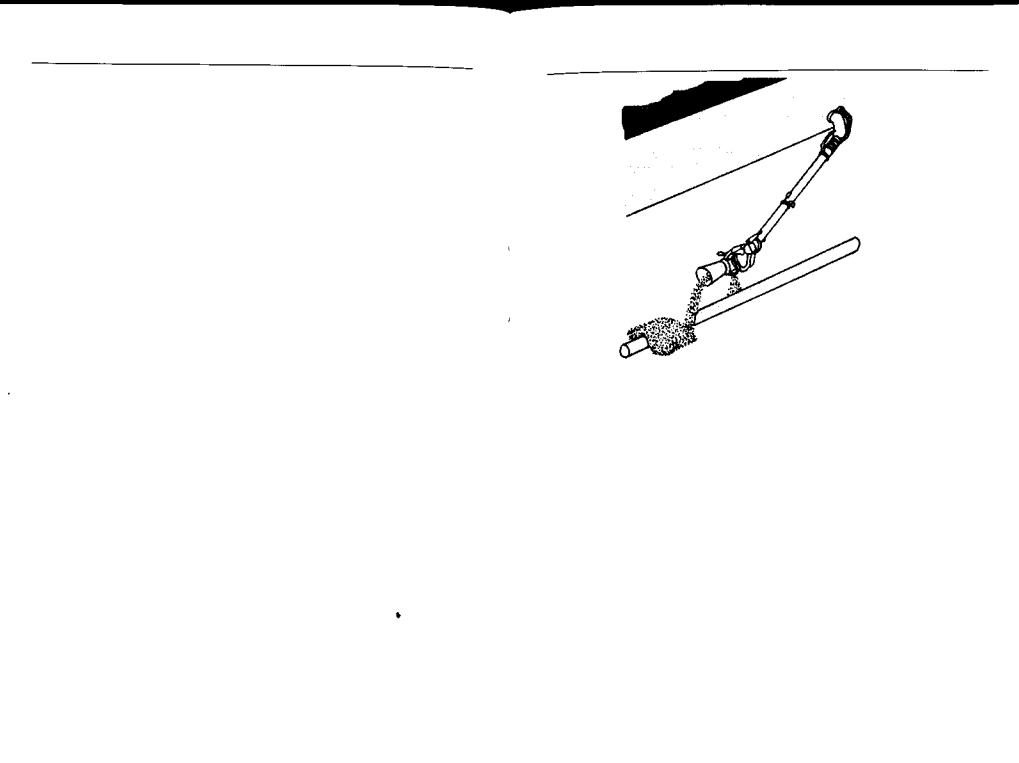
456 |
Часть III. Сооружение морских трубопроводов |
Используется следующая последовательность проведения операций:
1.Предварительное обследование.
2.Укладка бермы с двух сторон и исследование ее после возведения.
3.Размещение изоляционного слоя.
4.Обследование с помощью дистанционного подводного аппарата (ДПА).
5.Укладка защитного слоя.
6.Окончательный осмотр.
Система для засыпки грунта включала в себя сборку из полиэтиленовых труб, которую опускали непосредственно над трубопроводом. Процесс засыпки регулировался специальным модулем на конце трубы, состоящим из видеокамеры, гидролокаторов-профилеметров двойного сканирования иприемопередатчиков системыподводнойнавигации. Все устройства, относящиеся к оборудованию и радионавигационным системам, имели связь с центральным пультом управления судном.
В ходе выполнения технологических операций можно использовать различные конструкции трубных систем для подачи материала для засыпки под воду. Известна конструкция фирмы Hollandsche Aanneming Maatschappij, разработанная для точной отсыпки гравия и твердых пород для оснований и трубопроводов при глубине воды от 20 до 160 м.
Телескопическую трубу, изображенную на рис. 16.8.2, устанавливают на земснаряде. Труба состоит из трех секций труб длиной 43 м и двух секций длиной 3 и 15 м (в зависимости от глубины воды). Основным узлом является 2,5-м раструб на конце засыпной трубы, оснащенной эхолотом, вертикальным и горизонтальным угломерами.
Перед началом работ производят предварительный осмотр трассы и определяют положение судна относительно трубопровода с помощью ДПА, оснащенного комплектом различного оборудования, включая устройство слежения, гидролокаторы и видеокамеры.
Затем земснаряд фиксируют на рабочем месте с помощью системы динамического позиционирования, после чего телескопическую засыпную трубу опускают таким образом, чтобы раструб находился на расстоянии 5 м над рабочей зоной.
Для точного размещения материала засыпки вдоль намеченной трассы на земснаряде монтируют устройство автоматического слежения, встроенное в систему динамического позиционирования.
Гравий, поднятый с морского дна, имеет обычно округлые кромки, что снижает риск повреждения трубопроводов. Получаемая смесь гравия с водой проходит калибровку на борту земснаряда.
Глава 16. Монтаж морских трубопроводов |
457 |
Рис. 16.8.2. Телескопическая засыпная труба
16.9. ОБРАБОТКА ВНУТРЕННЕЙ ПОВЕРХНОСТИ МОРСКИХ ТРУБОПРОВОДОВ
На практике нередко требуется проложить морской трубопровод, предназначенный для транспортирования двухфазного потока при повышенных температурах. Рабочую поверхность такого трубопровода необходимо защитить от воздействия агрессивной среды. В таких случаях, помимо использования специальных сталей и применения ингибиторов, во время эксплуатации системы внутреннюю поверхность трубопроводов нередко покрывают тонкой прочной пленкой на основе эпоксидной смолы.
Компания «Оксидентал петролеум» в британском секторе Северного моря уложила 18 км трубопроводов диаметром 152 и 254 мм, покрытых подобным образом. Технологический процесс нанесения внутреннего покрытия заключался в использовании застывающей жидкой эпоксидной смолы и применении установки электроподогрева. В процессе работ было предусмотрено обеспечение равной температуры на всем протяжении трубопровода в процессе очистки и нанесения покрытия.
Покрытие внутренней поверхности труб выполняли в условиях, когда температура окружающего воздуха часто опускалась ниже ми-
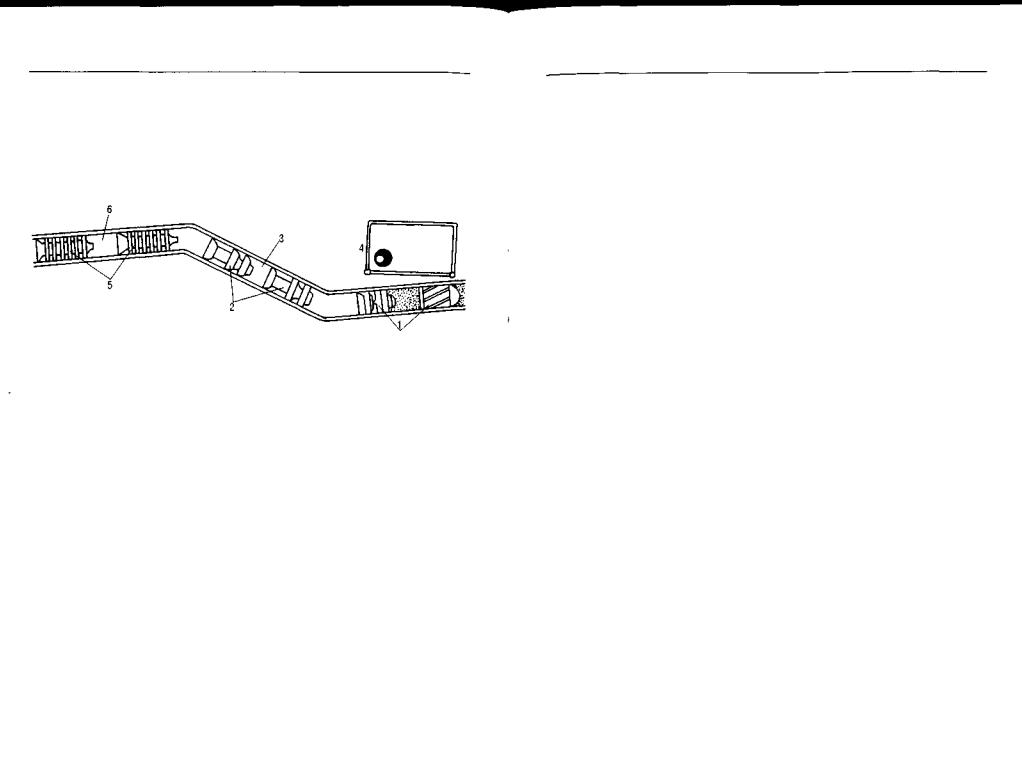
458 |
Часть III. Сооружение морских трубопроводов |
нимальной температуры застывания эпоксидной смолы ( + 7°С). По этой причине трубопроводы нагревали до температуры 20—25°С, что повышало эффективность процесса очистки и уменьшало время, требуемое для застывания смолы.
Оба трубопровода были уложены в общем несущем кожухе наружным диаметром 711 мм, в начале и конце которого трубы были закреплены общей стальной переборкой.
Рис. 16.9.1. Механическая и химическая очистка трубопровода путем пропускачерезнегоманжетныхи щеточныхскребковиразделителей с целью последующего нанесения внутреннего покрытия: 1 — механическиеманжетныеи щеточныескребки;2 —очистныепоршни; 3 — реагент для химической очистки; 4 — установка подогрева; 5 — поршни для нанесения покрьипия; 6 — жидкая эпоксидная смола
На начальном участке системы смонтировали устройства запуска и приема поршней, а на противоположном конце трубопроводы соединили так, что образовалась петля. Все элементы, контактировавшие с трубами, равномерно нагревались.
Для эффективного нанесения противокоррозионного покрытия была необходима предварительная подготовка поверхности. В целях качественной подготовки металла механическую обработку объединили с химической, что обеспечило очистку стенок труб от ржавчины, окалины, продуктов коррозии и т. д. До начала механической очистки через трубопроводы пропустили пенопластовые поршни и промыли их полость водой для предварительного удаления растворимы^ веществ.
Затем через трубопроводы пропускали состав из пенопластового поршня, пластиночного и щеточного скребков со скоростью, достаточной для удержания твердых частиц в виде суспензий. Очистка производилась многократно, пока загрязненность полости твердыми частицами не снизилась до приемлемого уровня.
Химическая очистка заключалась в прокачке через трубопроводы смесей соляной кислоты и ингибиторов, размещенных между скребка-
Глава 16. Монтаж морских трубопроводов |
459 |
ми. Интервалы времени между операциями варьировались, чтобы обеспечить разъедание кислотой окалины и других загрязнителей. Из отработанной кислоты отбирали пробы с целью определения момента, когда содержание твердых частиц достигло требуемого значения. Степень чистоты внутренней поверхности трубопровода также проверяли визуально с помощью видеокамер, вмонтированных в инспекционный поршень.
После химической очистки через трубопровод порциями пропускали фосфорную кислоту, удаляли остаточный раствор и промывали водой с заданным значением рН и добавкой химреагентов, после чего провели испытания на содержание хлоридов на стенках.
Для осушки трубопроводов через них пропускали растворители, а затем скребки с плотными манжетамидо полногоудаления свободной воды. После чего закачивали сухой, очищенный от масла сжатый воздух.
Двухкомпонентная эпоксидная смола, предназначенная для нанесения на стенки труб, находилась между двумя поршнями, проталкиваемыми в трубопроводе сжатым воздухом. Для достижения требуемой толщины покрытия поршни пропускали по трубопроводам несколько раз. Скорость перемещения поршней определяли по расходу смолы и путем прямых измерений на концах трубопроводов. В конечной стадии покрытие выдерживали до полного застывания.
Таким образом, за счет использования нагревательной электроустановки удалось обеспечить не только эффективную и ускоренную химическую очистку, но и быстрое высыхание внутреннего эпоксидного покрытия. Как показали дальнейшие испытания, качество покрытий, нанесенных непосредственно в уложенных трубопроводах, близко к качеству покрытий, нанесенных в заводских условиях. При этом покрытие изолирует и область сварных швов, чего нельзя добиться при использовании труб только с заводским покрытием.
16.10. МОНТАЖ ПОДВОДНОЙ ЗАПОРНОЙ АРМАТУРЫ
В ряду мер по обеспечению безопасности морских трубопроводов важное место занимают правильный выбор, установка и эксплуатация автоматических отсечных клапанов и других запорных систем.
Главную защиту от прорывов нефти и газа над уровнем моря обеспечивают отсечные клапаны на стояках.
Нормы проектирования предписывают размещать клапан на стояке как можно ниже, но при этом выше расчетного уровня гребней штормовой волны. Клапан должен иметь механическое управление, работоспособность которого необходимо регулярно проверять.
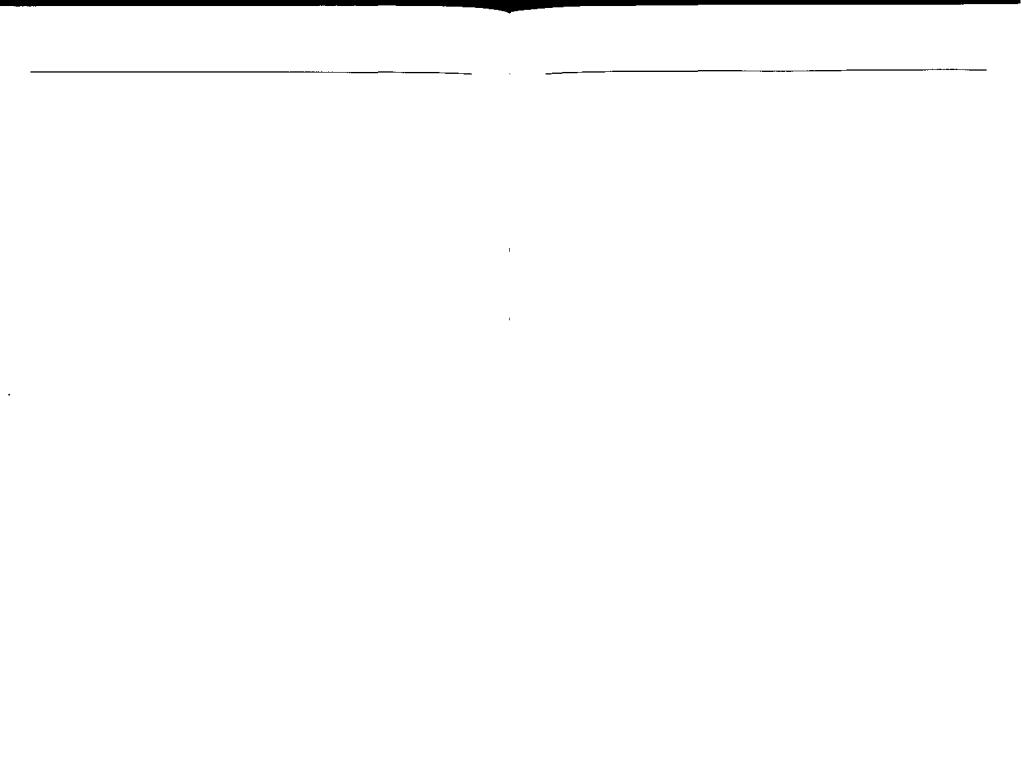
460 |
Часть III. Сооружение морских трубопроводов |
Сам отсечной клапан и относящиеся к нему средства управления должны быть защищены от поломок и огня, а система управления должна быть устроена таким образом, чтобы клапан закрывался автоматически при аварийном сигнале или при неполадках в системе. Необходимо предусматривать также пульты ручного закрывания клапанов для дублирования системы автоматики.
На многих морских трубопроводах, прежде всего на газопроводах, устанавливают также подводные отсечные клапаны. При этом в первую очередь в случае аварии следует закрывать отсечной клапан на стояке, а подводный клапан обеспечивает дополнительную защиту на случай аварии клапана на стояке.
Место размещения подводных отсечных клапанов определяют с учетом следующих факторов:
•эффективной площади излучения огненного факела;
•времени стечения продукта;
•работы системы управления;
•защиты отсечного клапана;
•монтажа и ремонта.
Сучетом производительности трубопровода и возможного объема утечки продукта подводный отсечной клапан располагают как можно ближе к платформе, но вне предполагаемой зоны огненного факела.
Большинство подводных отсечных клапанов располагают в 150—400 м от платформ. Это расстояние принято на основе анализа риска для платформ на основе следующих соображений:
•зона в радиусе 500 м от платформы обычно обозначена как «зона исключительных интересов», что запрещает рыболовство и деятельность третьих сторон;
•данное расстояние вне предела досягаемости посторонних предметов;
•огненный факел, который может возникнуть из-за разрыва трубопровода, минимально угрожает платформе;
•количество продукта в трубопроводе и стояке между клапаном и
платформой относительно невелико;
• клапан можно закрыть за 5—20 с; t
• монтаж отсечного клапана можно производить на безопасном расстоянии от платформы.
Из разных типов клапанов для работы в качестве отсечных чаще всего используют шаровые краны, обратные клапаны и задвижки.
Обвязка подводного трубопровода, как правило, включает в себя хотя бы один или несколько клапанов. При этом один из них обычно работает как отсечной, а остальные используют при ремонте. На одном и том же
Глава 16. Монтаж морских трубопроводов |
461 |
трубопроводе могут быть одновременно установлены шаровые краны, обратные клапаны и задвижки. В зависимости от конструкции отсечной клапан можно ремонтировать без затопления трубопровода, или только при частичном его затоплении, сводя к минимуму длительность и стоимость ремонта и связанные с ремонтом расходы.
Системауправления подводными клапанами должна предусматривать:
•стыковку клапана с надводной системой аварийной остановки;
•включение подачи энергии к исполнительному механизму клапана;
•наблюдение и извещение о поступлении энергии к клапану;
•наблюдение и извещение о положении подводного клапана. Дляуправления подводной запорной арматурой используютдва основ-
ных типа исполнительных механизмов:
•одинарного действия, когда гидравлический привод перемещает клапан только в одном направлении, одновременно сжимая возвратную пружину, которая перемещает клапан в противоположном направлении после снятия давления гидравлической жидкости;
•двойного действия, когда гидравлический привод перемещает клапан в обоих направлениях.
Самым распространенным источником энергии для работы клапана является гидравлическая жидкость. Ее подают под высоким давлением с надводной гидравлической установки через кабель-трос, подведенный к исполнительному механизму клапана. Для дублирования можно использовать гидроаккумуляторы.
В качестве гидравлической жидкости используют минеральные масла с биоразлагаемыми добавками или обычную воду. Гидравлическая жидкость на масляной основе более вязкая, чем вода, поэтому в данном случае применяют трубы большего диаметра. Для больших расстояний более высокая стоимость труб для масляной гидравлической жидкости может окупаться за счет более надежной работы.
Типовая система управления подводной запорной арматурой имеет следующие коммуникации:
•главная линия подачи гидравлической жидкости;
•линия возврата гидравлической жидкости (в системе двойного действия);
•пилотная линия гидравлической жидкости для клапана-защелки;
•запасная линия;
•скрученные и экранированные электрические парные провода для передачи данных о давлении в аккумуляторе и о положении клапана;
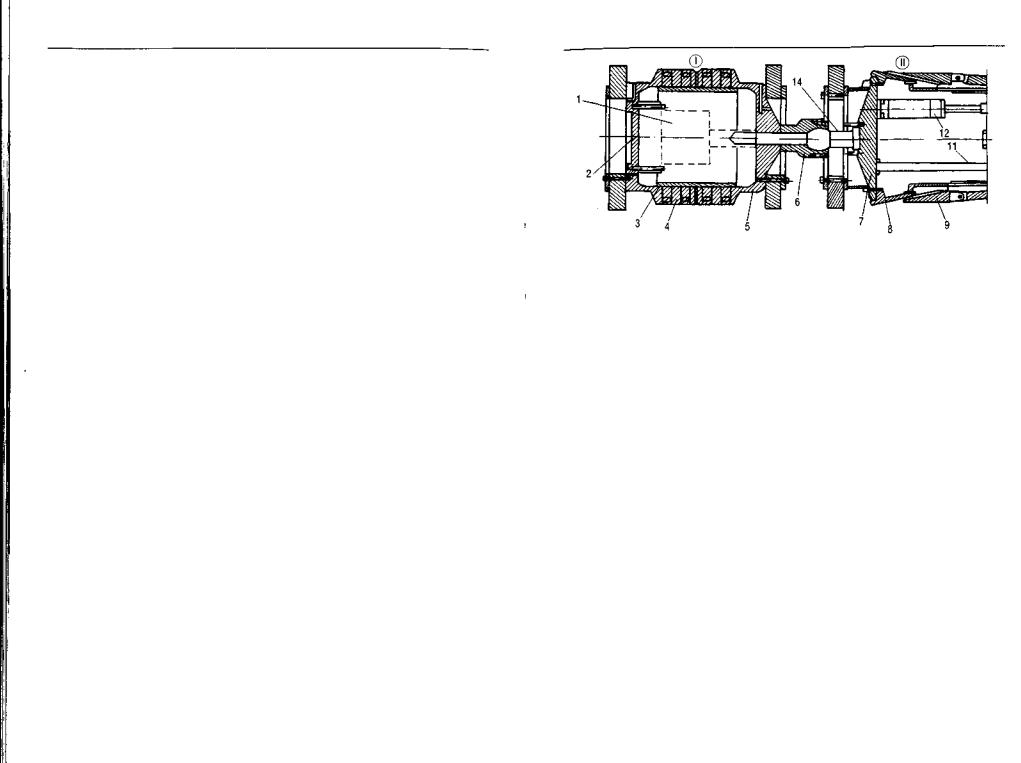
462 |
Часть III. Сооружение морских трубопроводов |
•запасные скрученные и экранированные электрические парные провода;
•кабель-трос, армированный двойной стальной проволокой на всю длину для защиты и повышения устойчивости.
Клапанный узел защищают от повреждений крышкой, изготовленной из труб или профилированной стали. Боковые стенки и верх крышки могут быть выложены панелями, изготовленными из стальных плит, решеток или их сочетания. Крышку жестко соединяют с опорной рамой или ставят свободно. Обычно опорную раму и защитную крышку устанавливают отдельно с помощью водолазного судна, но с учетом возможности одновременного подъема всего узла.
На действующих трубопроводах установка клапанов должна отвечать следующим условиям:
•минимальная длительность остановки трубопровода;
•отказ от сброса давления из трубопровода;
•частичное заполнение линии водой или вообще отказ от него;
•обеспечение безопасности персонала при монтаже.
Сцелью уменьшения потерь монтаж клапанов на действующем трубопроводе проводят во время ежегодного остановочного ремонта.
Для сохранения давления в трубопроводе при производстве работ необходимы установки пробки высокого давления. Надувные пробки выдерживают перепад давления до 1,5 МПа, для более высоких давлений применяют механические пробки. Самой совершенной считают гидравлическую пробку (рис. 16.10.1), рассчитанную на трубопроводы диаметром от 250 до 1220 мм и имеющую надежный механизм двойного уплотнения.
Гидравлическую пробку под давлением воды запускают в трубопровод через узел запуска поршня, а следят за ее перемещением с помощью кабель-троса, длина которого может достигать 450 м. Когда пробка достигает заданного места, с помощью гидравлики приводят в действие салазки и уплотнения, после чего снижают давление воды, и обратное давление газа прочно запирает салазки.
Другим способом отключения частей трубопровода является использование ледяных пробок. Для этого между двумя разделительными устройствами закачивают порцию воды, после чего передвигают ее в ремонтируемый участок. Затем воду замораживают с помощью «ошейника» из жидкого азота, создавая неподвижную ледяную пробку, длина которой может или должна в 2—3 раза превышать диаметр трубопровода. При проведении сварки под водолазным колоколом такой способ не применяют.
Глава 16. Монтаж морских трубопроводов |
463 |
Рис. 16.10.1. Двухмодульная гидравлическая пробка: I — уплотнительный модуль; II —модуль салазок; 1 — блок цилиндра; 2 — нажимная головка; 3 — опорное кольцо; 4 — уплотнения; 5 — опорная головка для шара; 6 — гнездо для шара; 7 — головка модуля салазок; 8 — корпусной блок; 9 — салазки; 10 — привод салазок; 11 — блок пружин;12—цилиндры;13—головка,направляющаяпробкупотрубе; 14 — шаровой шарнир
16.11. ОЧИСТКА ПОЛОСТИ И ИСПЫТАНИЕ ТРУБОПРОВОДОВ
Морские трубопроводы подвергают гидростатическим испытаниям после укладки на дно в соответствии с требованиями технических условий на испытания и ввод в эксплуатацию, разрабатываемых в составе проекта.
Перед гидростатическими испытаниями производят очистку и контроль внутренней полости трубопровода с применением поршней, оснащенных контрольно-измерительными приборами.
Минимальное давление при гидростатических испытаниях на прочность принимают в 1,25 раза выше расчетного давления, причем кольцевые напряжения во время испытаний не должны превышать 0,96 от предела текучести металла труб. Трубопровод выдерживают под давлением не менее 8 ч.
Трубопровод считается выдержавшим испытания, если в течение последующих 4 ч в нем не было зарегистрировано падение давления. Герметичность морского трубопровода проверяют после испытаний на прочность и снижения испытательного давления до расчетного значения в течение времени, необходимого для осмотра.