
ЛАБ.ПРАКТИКУМ (ИвТИ-2006)
.pdf3. Произвести технологический расчет трепальной машины МТ, определив скорость основных рабочих органов машины, вытяжки, степень трепания и производительность машины.
Основные сведения
Для изучения кинематической схемы снимают ограждения и открывают все футляры передач к отдельным органам машины.
Прежде чем начертить кинематическую схему, подробно изучают передачи ко всем органам машины, соблюдая определенную последовательность. Все передачи разделяют на две группы. К первой группе относят передачи к разрыхляющим и всасывающим органам, не связанным с питанием (ножевой барабан, трепало, вентилятор и скатывающие валы). Ко второй группе — передачи к органам, связанным с питанием машины или продвижением продукта (питающие цилиндры, педальный цилиндр, сетчатые барабаны, съемные цилиндры, плющильные валы и т. д.).
Рабочие органы первой группы работают непрерывно, органы же, связанные с питанием машины или продвижением продукта, останавливаются под действием соответствующих механизмов.
При изучении передачи движения органам машины должно быть обращено внимание на последовательность пуска и останова машины, включение и переключение механизмов, а также назначение сменных шестерен и блоков.
В кинематических схемах все рабочие органы условно изображают в виде прямоугольников и вместе с элементами передачи движения располагают в плоскости чертежа.
Машина МТ имеет 10 электродвигателей. Электродвигатели Д1 и Д1 (рис.35) работают в паре попеременно. Также попеременно работают электродвигатели Д2 и Д2′. Переключение электродвигателей в каждой из этих пар осуществляется автоматически, в зависимости от уровня заполнения волокном первого и соответственно промежуточных бункеров машины. В передаче имеется девять сменных шкивов (D1 – D3), семь сменных шестерен (z1—z7), с помощью которых устанавливают необходимую скорость разрыхляющих и питающих органов вентиляторов, вытяжку продукта, производительность машины, линейную плотность, длину и массу холста и степень трепания. Ниже приведены параметры сменных элементов передачи.
Шкив |
D1 |
|
D2 |
D3 |
|
D4 |
D5 |
Диаметр шкива, мм |
224, 250 |
125, 140, |
125, 140, |
160, 180, |
140, 160, |
||
|
|
|
160, 180 |
160, 180 |
200, 224 |
180 |
|
Шкив |
D6 |
|
D7 |
|
|
D8 |
D9 |
Диаметр шкива, мм |
160,180, 200, |
|
160,180, 200, |
125, 140, |
200, 224, |
||
|
224 |
|
224 |
|
|
160 |
250 |
Сменная шестерня |
z1 |
|
|
z2 |
|
|
z3 |
Число зубьев |
18, 21, 24, 27 |
|
61, 58, 55, 52 |
|
36, 38, 41, 43 |
||
Сменная шестерня |
z4 |
|
z5 |
|
|
z6 |
z7 |
Число зубьев |
43, 41, 38, 36 |
35, 37, 39, 40, |
44, 42, 40, |
16, 17, 18 |
|||
|
|
|
42, 44 |
39, 37, 35 |
|
Методические указания
Методика составления кинематической схемы При составлении кинематической схемы руководствуются следующими
методическими указаниями.
Вначале составляют план схемы. На листе миллиметровой бумаги намечают по ходу технологического процесса все органы машины в виде прямоугольников, длина которых означает ширину, высота—диаметр рабочих органов. Соотношение высот прямоугольников должно соответствовать действительному соотношению диаметров. Например, высота прямоугольника, изображающего сетчатые барабаны, должна быть больше, чем высота прямоугольника, изображающего питающие цилиндры, так как диаметр сетчатых барабанов больше диаметра питающих цилиндров.
Прямоугольники следует располагать так, чтобы между теми органами машины, где имеется большая шестеренная передача, расстояние было равно 10-20 мм. Расстояние между остальными прямоугольниками в зависимости от масштаба может быть от 2 до 5 мм.
От прямоугольников сверху и снизу листа бумаги оставляют место для пяти линий передачи; при этом шестеренную передачу располагают на первых линиях, т. е. ближе к прямоугольникам, а ременную — на последних.
В зависимости от масштаба между шестеренными передачами оставляют от 2 до 5 мм, такой же интервал следует оставлять между первой шестеренной передачей и прямоугольниками.
Чертить кинематическую схему следует в той же последовательности, что и при изучении передач.
Для технологического расчета в кинематической схеме проставляют диаметры шкивов и числа зубьев шестерен, отмечают места выключения отдельных узлов машины, храповые муфты, а также сменные шестерни и блоки, которые меняют в зависимости от заправки машины и ее скоростного режима.
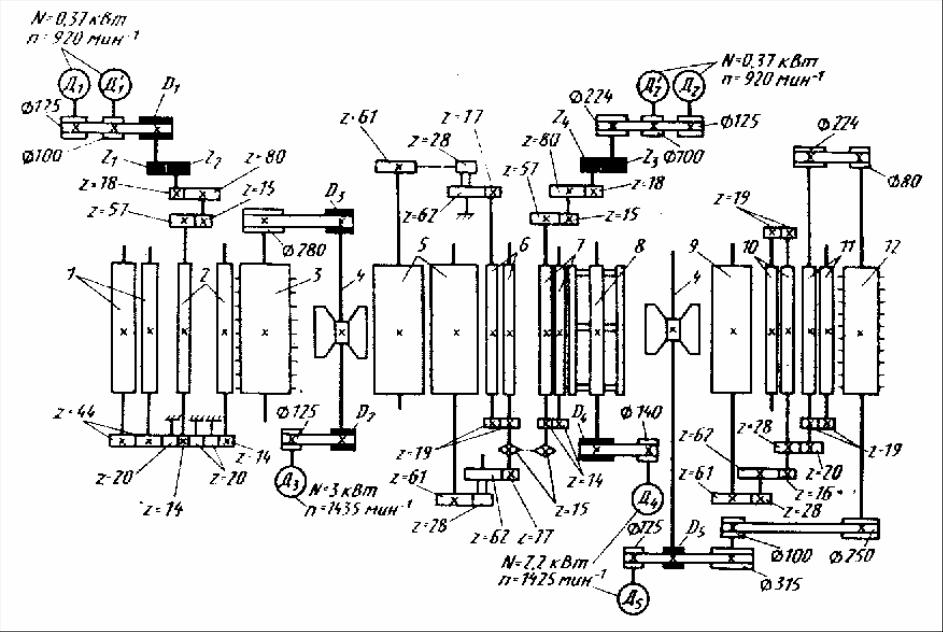
Рис. 35. Кинематическая схема трепальной машины МТ
150
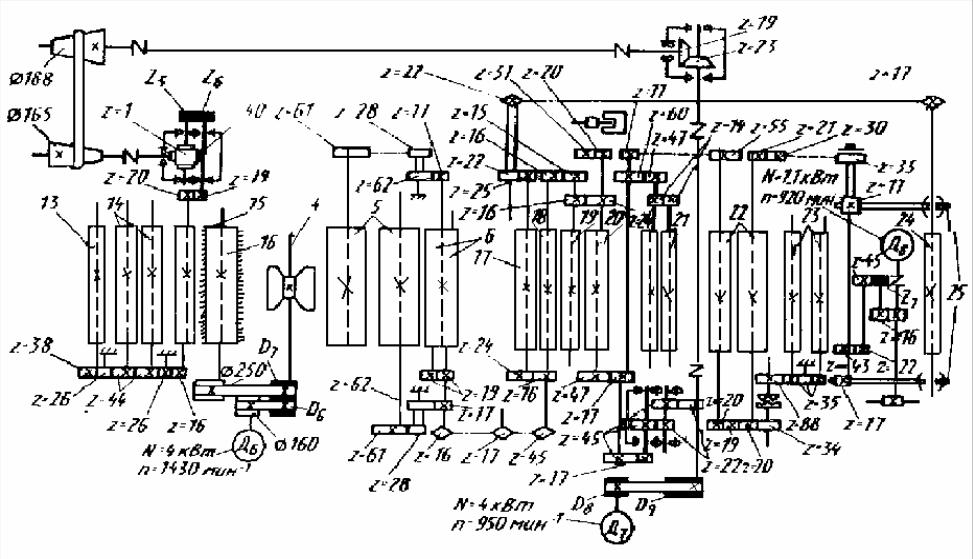
Рис. 35 (окончание):
1 - выпускные цилиндры 160 мм; 2 - питающиецилиндры 71 мм; 3 - барабан 610 мм; 4 - роторвентилятора 400 мм; 5 – сетчатые барабаны 540 мм; 6 - съемныецилиндры 71 мм; 7 - питающиецилиндры 55 ммпланочноготрепала;8 - планочное трепало 406 мм; 9 -сетчатый барабан (тихоходный); 10 - съемныецилиндры; 11 -питающиецилиндрыколковогобарабана;12 – колковыйбарабан 406 мм; 13 - поддерживающий цилиндр 106 мм; 14 - выпускныецилиндры 71 мм; 15 - педальный цилиндр 71 мм; 16 - игольчатое трепало 406 мм; 17 -первый(верхний)
плющильныйвал 186,5 мм; 18 -второйплющильныйвал 128,5 мм; 19третийплющильныйвал 24,5 мм; 20 - четвертыйплющильный вал 190,5 мм; 21 - самогрузные валы; 22 - скатывающие валы230 мм; 23 – валы механизмаобмотки 100 мм; 24 – нажимнойвал 144 мм; 25 – зубчатыерейки
151

Значение сменных шестерен и шкивов Скорость рабочих органов машины, вытяжка, длина и линейная плотность
холста, степень трепания и производительность машины зависят от числа зубьев сменных шестерен и от диаметра сменных шкивов и блоков.
В зависимости от линейной плотности вырабатываемого холста, состава смеси, степени рыхления и смешивания, а также влажности хлопкового волокна устанавливают скоростной режим, который обеспечивал бы выработку холстов высокой ровноты.
Расчет частоты вращения рабочих органов. Частоту вращения отдельных рабочих органов машины можно определить по кинематической схеме, используя передаточные числа. Передаточное число равно отношению угловых скоростей или частот вращения органов, связанных передачей. Так, если частота вращения трепала nт = 817 мин-1, а вентилятора nв = 1430 мин-1, то передаточное число от трепала к вентилятору nв/nт = 1430/817 = 1,75.
Искомая частота вращения n2 какого-либо органа, известная частота вращения n1 другого органа и передаточное число i1-2 от органа с известной частотой вращения к органу, частота вращения которого определяется, связаны соотношением
n2 = n1i1−2 .
Частоту вращения отдельных органов рассчитывают по передаче от вала электродвигателя или от главного вала машины. Однако искомая частота вращения может быть определена и по частоте вращения любого другого органа передачи, если известна схема связывающей их передачи.
При гибких передачах (клиноременных, тесемочных и им подобных) в расчет вносят поправку на скольжение. При отставании ведомого шкива, например на 1%, коэффициент скольжения равен η = 1−1/100 = 0,99 . Так, при диаметрах шкивов
Dв = 140 мм, D9 = 250 мм и η = 0,99 частота вращения скатывающего вала
ncк = 950 0,99 140 22 22 17 17 = 14,7 (мин-1). 250 45 45 45 55
Расчет вытяжки. Волокнистый поток, движущийся в машине, вследствие разницы в линейных скоростях подачи (питания) и выхода (выпуска) удлиняется и делается тоньше. Мерой удлинения продукта в процессе переработки является вытяжка. Вытяжку определяют как отношение окружной скорости выпускных органов к окружной скорости подающих органов:
Е = υ вып /υ пит .
Если нет потерь материала, вытяжка равна также отношению линейной плотности входящего продукта (слоя) Твх к линейной плотности выходящего продукта (слоя) Твых, умноженному на число сложений т. Если при этом масса материала уменьшается из-за выпадения сорных примесей и некоторого количества волокон в отходы, то вытяжка
153

Е = Твх (100 − у) /(Твых 100),
где у - процент отходов.
Утонение продукта
U = E(100 − y) /100.
Общую вытяжку на трепальной машине определяют как отношение окружной скорости скатывающих валов к окружной скорости выпускных цилиндров
приемного бункера машины, т. е. Е = υ 22 /υ 1 .
Общая вытяжка может быть также определена как произведение частных вытяжек, т. е. вытяжек между отдельными рабочими органами.
Вытяжку по передачам можно определить и не зная окружных скоростей соответствующих органов машины. Для этого используем нижеприведенную формулу и выразим в ней линейные скорости питания и выпуска как произведения длины окружности соответствующих органов на частоту их вращения:
Е = υ вып /υ пит = π dвыпnвып /(π dпитnпит ) ;
Е= dвып iпит−вып , dпит
где iпит−вып - передаточное число от питающего (подающего) органа к
выпускающему: iпит−вып = nвып / nпит .
Таким образом, для определения вытяжки между двумя органами машины по передаче движения необходимо диаметр выпускающего органа разделить на диаметр подающего органа и умножить на передаточное число от подающего органа к выпускающему. Так, частная вытяжка между педальным цилиндром и скатывающими валами трепальной машины МТ при среднем положении ремня на
конических барабанчиках при z5 = 39 и z6 = 40 зуб. равна
е = dск iпед−ск ; dпед
е = |
230 20z6 40 165 19 22 22 17 17 |
= 2,76 |
z6 |
; |
|
71 19z5 1 188 23 45 45 45 55 |
z5 |
||||
|
|
|
е = 2,76 40 / 39 = 2,83.
Эта частная вытяжка может быть установлена в пределах 2,19-3,47.
154
Степень трепания. Косвенной мерой оценки интенсивности воздействия трепальных органов на материал может быть показатель степени трепания. Степень трепания — это число ударов бил или колков, приходящихся на единицу массы обрабатываемого материала:
S −α nT 100 /(υ nTc ),
где S - степень трепания, ударов на 1 г;
a - число бил (колков) на трепале (барабане); nТ - частота вращения трепала (барабана), мин-1;
υ n - скорость подводимого слоя, м/мин;
Тс - линейная плотность слоя, текс.
Степень трепания можно регулировать двумя способами: изменять скорость треплющих органов ( nT ) или изменять скорость подачи к ним материала (υ n ).
Примерная степень трепания для тонковолокнистого хлопка - от 0,84 до 0,96 ударов на 1 г, а для средневолокнистого хлопка низших сортов - от 0,87 до 1,13.
Расчет производительности трепальной машины. Производительностью машины (или выпуска) называется количество продукции, выпускаемое в единицу времени (в час или смену). Различают производительность по массе продукции (в килограммах) и линейную (в метрах или километрах) в единицу времени. Так, если кипоразрыхлитель за 8ч переработал 4 кипы по 200 кг каждая, то его производительность –
800 кг : 8 = 100 кг/ч.
Производительность машин, кг/ч, выпускающих продукт определенной формы (например с холстовых трепальных машин), определяют по скорости выпуска и линейной плотности продукта. За один оборот скатывающие валы
навивают на скалку (выпускают) холст длиной π dcк.в , где dcк.в - диаметр скатывающих валов, мм. Длина холста, выпущенного за 1 мин, равнаπ dcк.вnск.в , где ncк.в - частота вращения скатывающих валов, мин-1. За 1 ч (60 мин) машина выпустит холст длиной
L = π dcк.в nск.в 60 /106 (км).
Это линейная производительность машины, км/ч. Она может быть пересчитана на весовую производительность:
L = π dcк.в nск.вТх 60 /106 (кг/ч),
где Tх - линейная плотность холста, текс.
По данной формуле определяют теоретическую производительность без учета перерывов в работе машины при ее остановах для чистки, смазки, мелкого ремонта, удаления отходов из-под машины. Эти простои снижают производительность машины. Поэтому норму производительности машины определяют путем умножения теоретической производительности машины на коэффициент полезного
155
времени (КПВ). Допустим, что трепальная машина при частоте вращения скатывающих валов 15 мин-1 и их диаметре 230 мм выпускает холст, масса 1 м которого равна 400 г. Простои трепальной машины на текущий ремонт составляют 5 мин, время на чистку сетчатых барабанов - 20 мин за 8 ч работы.
Теоретическая производительность машины: - линейная
L = 3,14 230 15 60 /106 = 0,65км / ч = 10,83м/мин;
- весовая
ПТ = 3,14 230 15 60 400000 /109 = 260 кг/ч.
Определяем КПВ. Полезное время за смену (480 мин) составляет 455 мин, или коэффициент полезного времени
Кп.в = (480 − 25)/480 = 0,947.
Норма производительности машины
Н= ПТ Кп.в ;
Н= 260 0,947 = 246,5 кг/ч.
Определяя производительность машины в среднем за длительный планируемый период, учитывают не только текущие простои, но и плановые остановы оборудования на средний и капитальный ремонты, генеральную чистку машин бригадой чистильщиков и по другим организационным причинам. Так, если простои на капитальный ремонт составляют 2%, на средний - 0,5%, на генеральную чистку с разборкой и чисткой передней зоны машины, проверкой и чисткой регулятора 1 раз в месяц и общую чистку всей машины 1 раз в неделю - 3 %, то всего плановые простои составят 2 + 0,5 + 3 = 5,5%. Тогда коэффициент работающего оборудования (КРО)
Кр.о = 1− р /100;
Кр.о = 1− 5,5 /100 = 0,945.
Произведение КПВ и КРО называют коэффициентом использования машины
КИМ
Ки.м = Кп.в Кр.о ;
Ки.м = 0,947 0,945 = 0,885.
156
Средняя плановая производительность машины
Пп = НК р.о = ПТ Ки.м ;
Пп = 246,5 0,947 = 218 кг/ч;
Пп = 260 0,885 = 218 кг/ч.
Замасливание и эмульсирование волокна Хлопковое волокно замасливают и эмульсируют, чтобы сохранить природные
жировосковые свойства волокна при обработке его на машинах и уменьшить отрицательное влияние статического электричества, возникающего на волокне при трепании, на технологический процесс. Замасливание - это операция, при которой в массу хлопкового волокна вводится замасливатель. В качестве замасливателя используют минеральные масла: трансформаторное, велосит Л или велосит Т, веретенное (специально обработанное) и т. п.
Эмульсирование применяют при переработке хлопкового волокна с влажностью менее 7%. Эмульсирование - это операция, при которой в волокнистую массу вводится эмульсия из замасливающих веществ и воды в количестве до 2 % массы волокна. Масло составляет 0,2-0,4 % массы волокна.
Форсунки для эмульсирования могут быть размещены перед плющильными валами трепальной машины или в трубопроводе, идущем к бункерам чесальных машин.
На предприятиях составляется план технологического контроля производства с указанием исполнителей по каждому разделу.
Постоянный и периодический технический контроль осуществляют инженерно-технический персонал предприятия, работники отдела технического контроля и фабричной лаборатории в соответствии с инструкциями и методиками.
В сортировочно-трепальном цехе контролируют:
-состав сортировки, соблюдение графика расхода сырья и правил смешивания;
-разводки между рабочими органами и их скорости;
-степень разрыхления волокнистого материала;
-количество и качество отходов, выделяющихся на машинах;
-эффективность очистки волокна каждой машиной или раз-рыхлительно- очистительным агрегатом;
-структуру холстов и качество их намотки;
-линейную плотность холстов (взвешивая все холсты);
-квадратическую неровноту холстов (неровнота холстов не должна превышать при выработке пряжи I сорта - 1,2%, II сорта - 1,5% и III сор-та - 1,9 %).
Эффективность очистки
Э= 100Sм / Sв (%),
157
где Sм - количество сорных и жестких примесей в отходах, получен-
ных из 1 т переработанной смеси на данной машине (или на агрегате), кг;
Sв - количество сорных и жестких примесей в 1 т переработанной смеси, кг.
7.ОПРЕДЕЛЕНИЕ СТЕПЕНИ РАЗРЫХЛЕНИЯ ВОЛОКНА, ВЛИЯНИЯ СТЕПЕНИ НАПОЛНЕНИЯ ВОЛОКНОМ РЕЗЕРВНОГО БУНКЕРА ТРЕПАЛЬНОЙ МАШИНЫ НА КАЧЕСТВО ХОЛСТА. АНАЛИЗ УГАРОВ ИЗ-ПОД РАЗРЫХЛИТЕЛЬНО-ТРЕПАЛЬНОГО АГРЕГАТА
Цель лабораторной работы
1.Определить степень разрыхления волокна двумя методами: по объемной массе и средней массе клочка волокна.
2.Изучить влияние степени наполнения волокном резервного бункера трепальной машины на качество холста.
3.Произвести анализ угаров из-под машин разрыхлительно-трепального агрегата и сравнить расчетную и фактическую длину холста.
Задание
1.Определить степень разрыхления волокна по объемной массе в зонах агрегата: после кипоразборщика, осевого чистителя, в приемном бункере трепальной машины, в резервном бункере трепальной машины, а также в холсте.
2.Определить степень разрыхления волокна по средней массе клочка волокна
взонах агрегата: после кипоразборщика, осевого чистителя, в приемном бункере трепальной машины, в резервном бункере трепальной машины.
3.Исследовать влияние степени наполнения волокном резервного бункера трепальной машины на линейную плотность, массу и неровноту холста по четырем вариантам наполнения резервного бункера: 1) на ¼ объема, 2) на ½ объема, 3) на ¾ объема, 4) на полный объем.
4.Определить место выделения и виды угаров.
5.На приборе ПЗС определить состав угаров (волокно и сорные примеси) из угарных камер трепальной машины: закрытой и открытой камер под ножевым барабаном, камеры трехбильного планочного и игольчатого трепал.
6.Определить органолептическим способом длину волокна в угарах, взятых из камер, указанных в п. 5.
7.Сравнить фактическую длину холста, полученного на трепальной машине, с расчетной.
Основные сведения
Волокно поступает на прядильные фабрики в спрессованном виде - кипах. Объемная масса хлопковой кипы достигает 600—650 кг/м3. Разрыхление волокна является одним из процессов, с которого начинается обработка волокнистого материала.
158