
Аксенов А. А. Технология конструкционных материалов
.pdf70
мированные зерна. Так как в равномерном температурном поле скорость роста зерен по всем направлениям одинакова, то новые зерна, появляющиеся взамен деформированных, имеют примерно одинаковые размеры по всем направлениям. Данное явление называется рекристаллизацией. Для чистых металлов она начинается при абсолютной температуре, равной 0,4 абсолютной температуры плавления металла. Рекристаллизация протекает с определенной скоростью, причем время, требуемое для нее, тем меньше, чем выше температура нагрева деформированной заготовки.
При температурах ниже температуры начала рекристаллизации наблюдается явление, называемое возвратом. При возврате (отдыхе) форма и размеры деформированных, вытянутых зерен не изменяются, но частично снимаются остаточные напряжения. Эти напряжения возникают из-за неоднородного нагрева или охлаждения (при литье и обработке давлением), неоднородности распределения деформаций при пластическом деформировании и т.д. Остаточные напряжения создают системы взаимно уравновешивающихся сил и находятся в заготовке, не нагруженной внешними силами. Снятие остаточных напряжений при возврате почти не изменяет механические свойства металла, но влияет на некоторые его физико-химические свойства. Так, в результате возврата значительно повышаются электрическая проводимость, сопротивление коррозии холоднодеформированного металла. Формоизменение заготовки при температуре выше температуры рекристаллизации сопровождается одновременным протеканием упрочнения и рекристаллизации.
Горячей деформацией называют деформацию, характеризующуюся таким соотношением скоростей деформирования и рекристаллизации, при котором рекристаллизация успевает произойти во всем объеме заготовки и микроструктура после обработки давлением оказывается равноосной, без следов упрочнения (рис. 4.1, б). Если металл по окончании деформации имеет структуру со следами упрочнения, то такая деформация называется неполной горячей. Она
71
приводит к получению неоднородной структуры, снижению механических свойств и пластичности, поэтому обычно нежелательна.
При горячей деформации пластичность примерно в 10 раз больше, чем при холодной деформации, а отсутствие упрочнения приводит к тому, что сопротивление деформированию (предел текучести) незначительно изменяется в процессе обработки давлением. Поэтому горячую деформацию целесообразно применять при обработке труднодеформируемых, малопластичных металлов и сплавов, а также заготовок из литого металла (слитков). В то же время при горячей деформации окисление заготовки идет более интенсивно (на поверхности образуется слой окалины), что ухудшает качество поверхности и точность получаемых размеров.
Холодная деформация без нагрева заготовок позволяет получать большую точность размеров и лучшее качество поверхности по сравнению с обработкой давлением при достаточно высоких температурах. Следовательно, обработка давлением без специального нагрева заготовки позволяет сократить продолжительность технологического цикла, облегчает использование средств механизации и автоматизации и повышает производительность труда.
При обработке давлением слитков, загрязненных неметаллическими включениями (обычно располагающихся по границам кристаллитов), они вытягиваются в виде волокон по направлению наиболее интенсивного течения металла. Эти волокна выявляются травлением и видны невооруженным глазом в форме так называемой волокнистой макроструктуры (рис. 4.2, а). Полученная в результате обработки давлением литого металла волокнистая макроструктура не может быть разрушена ни термической обработкой, ни последующей обработкой давлением. Последняя в зависимости от направления пластического течения металла может изменить направление и форму волокон макроструктуры.
Металл с ярко выраженной волокнистой макроструктурой (горячекатанные стали) характеризуется анизотропией механических свойств. При этом показатели прочности (предел текучести, временное сопротивление и др.) в раз-
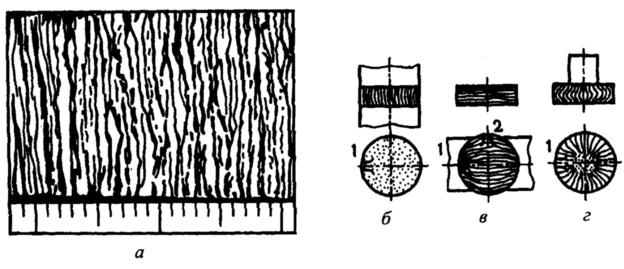
72
ных направлениях отличаются незначительно, а показатели пластичности (относительное удлинение, ударная вязкость и др.) вдоль волокон выше, чем поперек их.
Рис. 4.2. Макроструктура металла после обработки давлением
Так как направление волокон зависит от направления течения металла, при деформировании заготовки в готовой детали желательно предусмотреть благоприятное с точки зрения ее эксплуатации расположение волокон. При этом общие рекомендации следующие: необходимо, чтобы наибольшие растягивающие напряжения, возникающие в деталях в процессе работы, были направлены вдоль волокон, а если какой-либо элемент этой детали работает на срез, то желательно, чтобы перерезывающие силы действовали поперек волокон; необходимо, чтобы волокна подходили к наружным поверхностям детали по касательной и не перерезались наружными поверхностями детали. Выполнение этих требований не только повышает надежность детали (в том числе и при динамическом нагружении), но и улучшает другие эксплуатационные характеристики (сопротивление истиранию и др.).
Возможность воздействия обработкой давлением на расположение волокон, а следовательно, и на свойства деталей можно проиллюстрировать следующим примером. В зубчатом колесе, изготовленном резанием из круга (рис. 4.2, б) растягивающие напряжения, возникающие при изгибе зуба 1 под дейст-
73
вием сопряженного колеса, направлены поперек волокон, что понижает их надежность. При горячей штамповке зубчатого колеса из полосы (рис. 4.2, в) волокна по-разному ориентированы в различных зубьях относительно наибольших растягивающих напряжений: в зубе 1 – вдоль волокон, а в зубе 2 – поперек. Следовательно, зубья оказываются неравнопрочными. При изготовлении зубчатого колеса осадкой (рис. 4.2, г) из заготовки круга волокна получают почти радиальное направление. В этом случае все зубья равнопрочны, а наибольшие растягивающие напряжения, возникающие при изгибе, направлены вдоль волокон.
4.2 ВЛИЯНИЕ УСЛОВИЙ ДЕФОРМИРОВАНИЯ НА ПРОЦЕСС ОБРАБОТКИ МЕТАЛЛОВ ДАВЛЕНИЕМ
При пластическом деформировании металла действующие давления зависят от соответствующих пластических деформаций. При холодной деформации растет величина необходимых для этого напряжений и уравновешивающих их в каждый момент времени внешних сил, прикладываемых к деформируемому телу. Характер зависимости давления от деформации и их предельные значения зависят от свойств металла и условий деформирования.
С повышением температуры увеличиваются значения максимального относительного удлинения и максимально достижимых деформаций, а сопротивление деформированию уменьшается. Таким образом, при деформировании стали, нагретой до температуры 1200 0С, можно достичь большего формоизменения при меньшей приложенной силе, чем при деформировании холодной стали. У всех металлов и сплавов при повышении температуры увеличивается пластичность и уменьшается сопротивление деформирования в случае выполнения ряда требований, предъявляемых к процессу нагрева. Так, каждый металл должен быть нагрет до вполне определенной максимальной температуры. Если нагреть, например, сталь до температуры, близкой к температуре плавле-
74
ния, наступает пережог, выражающийся в появлении хрупкой пленки между зернами металла вследствие окисления их границ. При этом происходит полная потеря пластичности. Пережог исправить нельзя, пережженный металл может быть отправлен на переплавку.
Ниже зоны температур пережога находится зона температур перегрева. Явление перегрева заключается в резком росте размеров зерен. Вследствие того, что крупнозернистому аустениту, как правило, соответствует крупнозернистая структура после перекристаллизации (феррит + перлит или перлит + цементит), механические свойства изделия, полученного обработкой давлением из перегретой заготовки, оказываются низкими. Брак по перегреву в большинстве случаев можно исправить отжигом.
Максимальную температуру нагрева, т.е. температуру начала горячей обработки давлением, следует назначать такой, чтобы не было пережога и перегрева. Обычно эта температура принимается на 100…200 0С ниже температуры критической точки солидуса. В процессе обработки нагретый металл обычно остывает, соприкасаясь с более холодным инструментом и окружающей средой. Поэтому заканчивать горячую обработку давлением следует также при вполне определенной температуре, ниже которой пластичность вследствие упрочнения падает (не успевает произойти рекристаллизация) и в изделии возможно образование трещин. Поэтому температура окончания обработки давлением в горячем состоянии принимается выше температуры рекристаллизации на 50…100 0С.
Каждый металл и сплав имеют свой строго определенный температурный интервал горячей обработки давлением; например, алюминиевый сплав АК4 – 350…470 0С; медный сплав БрАЖМц – 750…900 0С; титановый сплав ВТ8 – 900…1100 0С. Для углеродистых сталей температурный интервал можно определить по диаграмме состояния железо-углерод. С увеличением содержания углерода он сужается от 1300…700 0С для малоуглеродистой стали до 1080…870 0С для стали У11 (рис. 4.3).
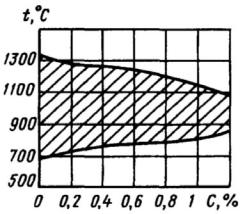
75
Заготовка должна быть равномерно нагрета по всему объему до требуемой температуры. Разность температур по сечению заготовки приводит к тому, что вследствие теплового расширения между более нагретыми поверхностными слоями металла и менее нагретыми внутренними слоями возникают напряжения. Последние тем больше, чем больше разность температур по сечению заготовки, и могут возрасти настолько, что в центральной зоне с растягивающими напряжениями при низкой пластичности металла образуются трещины. Разность температур по сечению увеличивается с повышением скорости нагрева, поэтому существует допустимая скорость нагрева. Наибольшее время требуется для нагрева крупных заготовок из высоколегированных сталей из-за их более низкой теплопроводности. Например, время нагрева слитка массой около 40 т
из легированной стали составляет более 24 ч. |
|
Однако с увеличением времени |
|
нагрева увеличивается окисление по- |
|
верхности металла, так как при высоких |
|
температурах металл активнее химиче- |
|
ски взаимодействует с кислородом воз- |
|
духа. В результате на поверхности |
|
стальной заготовки образуется окалина |
|
(слой, состоящий из оксидов железа |
Рис. 4.3. Температурный |
Fe2O3, Fe3O2, FeO). Кроме потерь ме- |
интервал нагрева углеродистых |
сталей в зависимости |
|
талла на окалину последняя, вдавлива- |
от содержания углерода |
|
ясь в поверхность заготовки при деформировании, вызывает необходимость увеличения припусков на механическую обработку. Окалина увеличивает износ деформирующего инструмента, так как ее твердость значительно больше твердости горячего металла. При высоких температурах на поверхности стальной заготовки интенсивно окисляется не только железо, но и углерод – происходит обезуглероживание, которое иногда достигает толщины 1,5…2 мм. Для умень-
76
шения окисления заготовки нагревают в нейтральной или восстановительной атмосфере.
Влияние температуры металла на практике нельзя рассматривать в отрыве от скоростных условий деформирования. Скорость деформирования при горячей деформации должна обеспечивать полное протекание процесса рекристаллизации. Поэтому для некоторых особо чувствительных к увеличению скорости деформирования сплавов, например алюминиевых и магниевых, горячее деформирование рекомендуется осуществлять на гидравлических прессах, а не на молотах.
Большое влияние на величину предельной деформации оказывает схема напряженного состояния. Наибольшая предельная деформация достигается при отсутствии растягивающих напряжений и увеличении сжимающих. В этих условиях (схема неравномерного всестороннего сжатия) даже хрупкие материалы типа мрамора могут получать пластические деформации. Пластичность при прочих равных условиях определяется схемой напряженного состоянии, различной в разных процессах и операциях обработки давлением. Вследствие этого для каждых операций, металла и температурно-скоростных условий существуют свои определенные предельные деформации.
4.3 КЛАССИФИКАЦИЯ ПРОЦЕССОВ ОБРАБОТКИ МЕТАЛЛОВ ДАВЛЕНИЕМ
Пластическое деформирование в обработке металлов давлением осуществляется при различных схемах напряженного и деформированного состояний, при этом исходной заготовкой могут быть объемное тело, круг, лист. По назначению процессы обработки металлов давлением группируют следующим образом:
– для получения изделий постоянного поперечного сечения по длине (прутков, проволоки, лент, листов), применяемых в автомобилестроении или в
77
качестве заготовок для последующего изготовления из них деталей обработкой резанием с использованием предварительного пластического формоизменения или без него; основными разновидностями таких процессов являются прокатка, прессование и волочение;
– для получения деталей или заготовок (полуфабрикатов), имеющих приближенные формы и размеры готовых деталей и требующих обработки резанием лишь для придания им окончательных размеров и получения поверхности заданного качества; основными разновидностями таких процессов являются ковка и штамповка.
Основными схемами деформирования объемной заготовки можно считать сжатие между плоскостями инструмента, ротационное обжатие вращающимися валками, выдавливание металла из полости инструмента и волочение, при котором в качестве заготовки может быть использован только круг.
Сжатие между плоскостями инструмента – осадка – характеризуется свободным пластическим течением металла между поверхностями инструмента (рис. 4.4, а, в). Схема напряженного состояния – всестороннее неравномерное сжатие из-за наличия сил трения на контакте между инструментом и заготовкой. С уменьшением коэффициента трения и увеличением относительной высоты заготовки схема напряженного состояния приближается к линейному сжатию. Однако относительная высота (отношение высоты заготовки к ее меньшему поперечному размеру) не может быть больше предельного значения, равного 2,5…3, из-за опасности потери устойчивости и изгиба. Схема свободного течения металла при сжатии между плоскостями инструмента лежит в основе операций ковки, а также имеет место во многих способах объемной штамповки.
Деформация при свободном течении металла характеризуется степенью деформации, %
h0 |
(4.1) |
|
ε = ln h 100, |
||
|
||
1 |
|
|
где h0 и h1 – соответственно высота заготовки до и после деформации. |
|
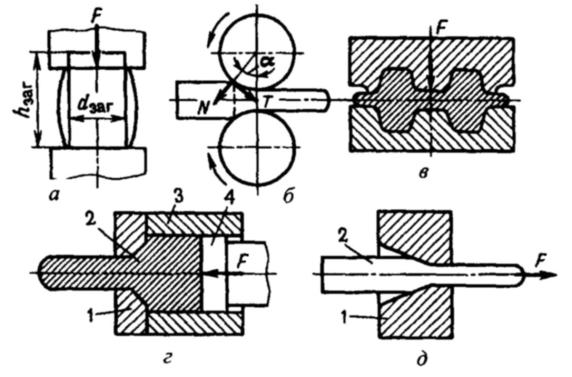
78
Ротационное обжатие вращающимися валками (рис. 4.4, б) обусловли-
вается силой трения между вращающимся инструментом и заготовкой, благодаря которым последняя перемещается в зазоре между валками, одновременно деформируясь. Эта схема лежит в основе прокатки, а также может быть использована в ряде способов получения поковок: поперечно-клиновой прокатке, вальцовке, раскатке.
Рис. 4.4. Основные схемы деформирования в обработке металлов давлением
Для осуществления процесса необходима определенная величина сил трения. На заготовку со стороны валков действуют нормальные силы N и сила трения T (рис. 4.4, б). Спроецировав эти силы на горизонтальную ось, можно записать условие захвата металла валками (по отношению к одному валку, так как система симметрична):
N sinα <T cosα. |
(4.2) |
Угол α называется углом захвата. Выразив силу трения как T = fN , где
f – коэффициент трения, и подставив это выражение в формулу (4.2), получим sinα < f cosα или
εН |
= |
(h0 −h1 ) |
100. |
(4.4) |
|
||||
|
|
h0 |
|
Площадь поперечного сечения заготовки в процессе деформирования всегда уменьшается. Поэтому для определения деформации (особенно, когда обжатие по сечению различно) используют показатель, называемый вытяжкой:
|
μ = |
l1 |
= F0 , |
(4.5) |
|
|
|
||||
|
|
l |
0 |
F |
|
|
|
|
1 |
|
|
где l0 |
и F0 – первоначальные |
длина и площадь поперечного |
сечения; |
||
l1 и F1 |
– те же величины после прокатки. Для прокатки величина вытяжки со- |
||||
ставляет обычно 1,25…1,6. |
|
|
|
Выдавливание металла (рис. 4.4, г) через отверстие заданного сечения в матрице 1 происходит вследствие его сжатия в замкнутой полости, образуемой контейнером 3, матрицей 1 и пуансоном 4, поэтому схема неравномерного всестороннего сжатия реализуется здесь полнее, чем в других процессах. Длина выдавленной части относится к перемещению пуансона 4 как площадь поперечного сечения исходной заготовки 2 к площади выдавленной части. Чем больше это отношение (так называемая величина вытяжки, которая составляет от 8 до 50), тем больше значение суммарного сжимающего напряжения, развиваемого в металле при выдавливании. Схема выдавливания характерна для таких видов обработки металлов давлением, как прессование, горячая и холодная штамповка.