
Аксенов А. А. Технология конструкционных материалов
.pdf160
Дифференциальное деление применяют в тех случаях, когда нельзя подобрать на лимбе окружность с требуемым числом отверстий для простого деления. При этом способе заготовку поворачивают на требуемый угол вращением рукоятки относительно вращающегося делительного лимба 5, который получает вращение от шпинделя 4 через сменные зубчатые колеса (рис. 7.11, б). При этом справедливо равенство
n = |
40 = n +n |
, |
(7.11) |
||
|
z |
1 |
2 |
|
|
|
|
|
|
|
где n1 – вращение рукоятки относительно делительного лимба; n2 = iz – вра-
щение лимба, соответствующее повороту заготовки на 1z оборота ( z – задан-
ное число делений; i – передаточное число сменных зубчатых колес). Вращение рукоятки
n = |
N |
, |
(7.12) |
|
zПР |
||||
1 |
|
|
||
|
|
|
где zПР – приближенное число делений, близкое к заданному и позволяющее использовать способ простого деления.
Преобразуя формулу (7.12), получим
40 |
40 |
|
i |
или i = |
40(zПР |
− z) |
|
|
z |
= zПР |
+ |
|
zПР |
|
. |
(7.13) |
|
z |
|
Передаточное число i может быть положительным или отрицательным, поэтому при положительном передаточном отношении вращения делительного лимба и рукоятки совпадают, а при отрицательном – они вращаются в разные стороны.
В качестве вспомогательного инструмента применяют фрезерные оправки для закрепления фрез и передачи крутящего момента от шпинделя станка на фрезу. Базой для закрепления фрезы на оправке может быть ее центровое отверстие или хвостовик (конический или цилиндрический). По способу закрепления в первом случае фрезы называют насадными, во втором – хвостовыми.
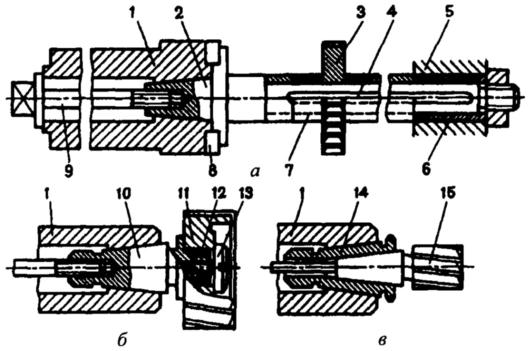
161
На рис. 7.12, а показана оправка 2 для закрепления цилиндрических и дисковых фрез 3. Фрезу насаживают на оправку и соединяют с ней посредством шпонки 4. Требуемое положение фрезы на оправке обеспечивается установочными кольцами 7. Коническим хвостовиком оправку вставляют в коническое отверстие шпинделя 1 и закрепляют затяжным болтом 9. От проворачивания оправку удерживают сухари 8. Другой конец оправки входит в подшипник 6 и серьги 5.
Рис. 7.12. Схемы установки и закрепления фрез на станке
Короткие концевые оправки (рис. 7.12, б) используют для закрепления торцовых и дисковых фрез. Коническим хвостовиком 10 оправку закрепляют в шпинделе 1, а на другом конце оправки крепят насадную фрезу 11 с помощью шпонки 12 и винта 13.
Фрезы с коническим хвостовиком 15 закрепляют в коническом отверстии шпинделя 1 непосредственно или через переходные втулки 14 (рис. 7.12, в).
Схемы обработки заготовок на фрезерных станках. Горизонтальные плоскости фрезеруют на горизонтально-фрезерных станках цилиндрическими фрезами (рис. 7.13, а) и на вертикально-фрезерных станках торцовыми фрезами (рис. 7.13, б). В большинстве случаев плоскости удобнее обрабатывать торцо-

162
выми фрезами вследствие большей жесткости их закрепления в шпинделе и более плавной работы, так как число одновременно работающих зубьев торцовой фрезы больше числа зубьев цилиндрической фрезы.
Вертикальные плоскости фрезеруют на горизонтально-фрезерных станках торцовыми фрезами (рис. 7.13, в) и торцовыми фрезерными головками, а на вертикально-фрезерных станках концевыми фрезами (рис. 7.13, г).
Рис. 7.13. Схемы обработки заготовок на фрезерных станках
Наклонные плоскости фрезеруют торцовыми (рис. 7.13, д) и концевыми фрезами на вертикально-фрезерных станках, у которых фрезерная головка со шпинделем поворачивается в вертикальной плоскости. Наклонные плоскости небольшой ширины можно фрезеровать на горизонтально-фрезерных станках дисковой одноугольной фрезой (рис. 7.13, е).
Комбинированные поверхности фрезеруют набором фрез (рис. 7.13, ж) на горизонтально-фрезерных станках. Точность взаиморасположения обработанных поверхностей зависит от жесткости крепления фрез по длине оправки и диаметров фрез (отношение диаметров не более 1,5).
Уступы и прямоугольные пазы фрезеруют концевыми (рис. 7.13, з) и дисковыми (рис. 7.13, и) фрезами на вертикально- и горизонтально-фрезерных
163
станках. Применение дисковых фрез целесообразнее, так как они имеют большее количество зубьев и допускают работу с большими скоростями.
Фасонные пазы фрезеруют фасонной дисковой фрезой (рис. 7.13, к), угловые пазы – одноугловой и двухугловой (рис. 7.13, л) фрезами на горизон- тально-фрезерных станках.
Клиновой паз фрезеруют на вертикально-фрезерном станке за два прохода; прямоугольный паз – концевой фрезой, затем скосы паза одноугловой фрезой (рис. 7.13, м). Т-образные пазы (рис. 7.13, н), которые широко применяются в автомобилестроении, фрезеруют обычно за два прохода: вначале паз прямоугольного профиля – концевой фрезой, затем нижнюю часть паза – фрезой для Т-образных пазов (хвостовой фрезой).
Шпоночные пазы фрезеруют концевыми или шпоночными (рис. 7.13, о) фрезами на вертикально-фрезерных станках. Фрезерование шпоночной фрезой обеспечивает получение более точных размеров паза, что определяет посадочные размеры шпонки и сопрягаемых деталей.
Фасонные поверхности незамкнутого контура с криволинейной обра-
зующей и прямолинейной направляющей фрезеруют на горизонтально- и вер- тикально-фрезерных станках фасонными фрезами соответствующего профиля (рис. 7.13, п). Данный способ целесообразен для обработки узких и длинных фасонных поверхностей; широкие профили обрабатываются набором фрез.
7.4 ОБРАБОТКА ЗАГОТОВОК НА СВЕРЛИЛЬНЫХ СТАНКАХ
Сверление – распространенный метод получения отверстий в сплошном материале. Сверлением получают сквозные и несквозные (глухие) отверстия и обрабатывают предварительно полученные отверстия в целях увеличения их размеров, повышения точности и снижения шероховатости поверхности. Оно осуществляется при сочетании вращательного движения инструмента вокруг оси – главного движения резания и поступательного его движения вдоль оси –
164
движения подачи. Оба движения на сверлильном станке сообщают инструменту.
Процесс резания при сверлении протекает в более сложных условиях, чем при точении, так как в процессе резания затруднены отвод стружки и подвод охлаждающей жидкости к режущим кромкам инструмента. При отводе стружки происходит трение ее о поверхность канавок сверла и трение сверла о поверхность отверстия, в результате чего повышается деформация стружки и тепловыделение. На увеличение деформации стружки также влияет изменение скорости главного движения резания вдоль режущей кромки от максимального значения на периферии сверла до нулевого значения у центра.
Типы сверлильных станков. Их делят на несколько типов: настольносверлильные (для сверления отверстий диаметром до 16 мм); вертикальносверлильные и радиально-сверлильные (для сверления отверстий диаметром до 100 мм); горизонтально-сверлильные (для получения глубоких отверстий специальными сверлами). В автомобилестроении сверлильные станки используются во всем разнообразии, так как большинство деталей автомобиля имеют отверстия различных диаметров.
Конструкции сверлильных станков различных типов имеют много общего. На рис. 7.14 представлены основные типы сверлильных станков. На фундаментной плите 1 вертикально-сверлильного станка (рис. 7.14, а) смонтирована колонна 2, в верхней части которой расположена коробка скоростей 6 – она сообщает главное вращательное движение резания шпинделю с инструментом. Движение подачи инструмент получает через коробку подач 5, расположенную в кронштейне 4. Заготовку устанавливают на столе 3. Стол и кронштейн имеют установочные перемещения по вертикальным направляющим колонны 2. Совмещение оси вращения инструмента с заданной осью отверстия достигается перемещением заготовки.
На фундаментной плите 1 радиально-сверлильного станка (рис. 7.14, б) закреплена колонна 2 с поворотной гильзой 3, по которой перемещается в вер-

165
тикальном направлении и устанавливается в нужном положении с помощью механизма 5 траверса 4. По горизонтальным направляющим траверсы перемещается шпиндельная головка 6, в которой расположены коробка скоростей 7 и коробка подач 8. Шпиндель 9 с инструментом получает главное вращательное движение резания и движение вертикальной подачи. Заготовку закрепляют на столе 10 или непосредственно на фундаментной плите 1. Инструмент устанавливают в рабочее положение поворотом траверсы вместе с гильзой 3 и перемещением шпиндельной головки по направляющим траверсы.
Рис. 7.14. Основные типы сверлильных станков
На радиально-сверлильных станках обрабатывают отверстия, расположенные на значительном расстоянии друг от друга, в крупногабаритных и большой массы заготовках. Эти станки, в отличие от вертикально-сверлильных, обеспечивают (без изменения положения заготовки) совмещение осей режущего инструмента и обрабатываемых отверстий поворотом траверсы и перемещением шпиндельной головки вдоль траверсы.
Режущий инструмент. Сверла по конструкции и назначению подразделяют на спиральные, центровочные и специальные. На рис. 7.15, а представлено наиболее распространенное спиральное сверло, состоящее из рабочей части 6, шейки 2, хвостовика 4 и лапки 3. В рабочей части 6 различают режущую 1 и направляющую 5 части с винтовыми канавками. Шейка 2 соединяет рабочую часть сверла с хвостовиком 4, который необходим для установки сверла в

166
шпинделе станка. Лапка 3 служит упором при выбивании сверла из отверстия шпинделя.
Элементы рабочей части и геометрические параметры спирального сверла показаны на рис. 7.15, б. Сверло имеет две главные режущие кромки 11, образованные пересечением передних 10 и задних 7 поверхностей лезвия; поперечную режущую кромку 12 (перемычку) и две вспомогательные режущие кромки 9. На цилиндрической части сверла вдоль винтовой канавки расположены две узкие ленточки 8, обеспечивающие направление сверла при резании.
Рис. 7.15. Части, элементы и углы спирального сверла
Геометрические параметры сверла определяют условия его работы. Передний угол γ измеряют в главной секущей плоскости II-II, перпендикулярной к главной режущей кромке. Задний угол α измеряют в плоскости I-I, параллельной оси сверла. Особенностью геометрии сверл является то, что передний и задний углы в различных точках главной режущей кромки различны, т.е. у наружной поверхности сверла угол γ наибольший, а угол α наименьший;
ближе к оси сверла – наоборот. Угол при вершине сверла 2ϕ измеряют между главными режущими кромками; его значение различно в зависимости от обрабатываемого материала. Угол наклона поперечной режущей кромки ψ изме-
ряют между проекциями главной и поперечной режущих кромок на плоскость,

167
перпендикулярную к оси сверла. Угол наклона винтовой канавки ω измеряют по наружному диаметру. С увеличением угла ω увеличивается передний угол; при этом облегчается процесс резания и улучшается выход стружки.
Зенкерами (рис. 7.16) обрабатывают отверстия в литых или штампованных заготовках, а также предварительно просверленные отверстия. В отличие от сверл, зенкеры снабжены тремя или четырьмя главными режущими кромками и не имеют поперечной кромки. Режущая часть 1 выполняет основную работу резания; калибрующая часть 5 служит для направления зенкера в отверстии и обеспечивает необходимые точность и шероховатость поверхности (2 – шейка; 3 – лапка; 4 – хвостовик; 6 – рабочая часть). По виду обрабатываемых отверстий зенкеры делят на цилиндрические (рис. 7.16, а), конические (рис. 7.16, б) и торцовые (рис. 7.16, в). Они бывают цельные с коническим хвостовиком (рис. 7.16, а, б) и насадные (рис. 7.16, в).
Рис. 7.16. Инструменты для обработки отверстий на сверлильных станках: а, б, в – зенкеры; г, д, е – развертки; ж – метчик
Развертками окончательно обрабатывают отверстия. По форме обрабатываемого отверстия различают цилиндрические (рис. 7.16, г) и конические (рис. 7.16, д) развертки. Они имеют от 6 до 12 главных режущих кромок, распо-

168
ложенных на режущей части 7 с направляющим конусом. Калибрующая часть 8 направляет развертку в отверстии и обеспечивает необходимые точность и шероховатость поверхности. По конструкции закрепления развертки делят на хвостовые и насадные. На рис. 7.16, е показана машинная насадная развертка с механическим креплением режущих пластинок в корпусе.
Метчик применяют для нарезания внутренних резьб. Он (рис. 7.16, ж) представляет собой винт с прорезанными прямыми или винтовыми канавками, образующими режущие кромки. Рабочая часть метчика имеет режущую 9 и калибрующую 10 части. Метчик закрепляют в специальном патроне.
Схемы обработки заготовок на сверлильных станках. На сверлильных станках выполняют следующие операции.
Сверление сквозного отверстия – режущим инструментом служит спиральное сверло (рис. 7.17, а).
Рис. 7.17. Схемы обработки заготовок на сверлильных станках
Рассверливание – процесс увеличения диаметра ранее просверленного отверстия сверлом большего диаметра (рис. 7.17, б). Диаметр отверстия под рассверливание выбирают так, чтобы поперечная режущая кромка в работе не участвовала – в этом случае уменьшается осевая сила.
169
Зенкерование – обработка предварительно полученных отверстий для придания им более правильной геометрической формы, повышения точности и снижения шероховатости многолезвийным режущим инструментом – зенкером
(рис. 7.17, в).
Развертывание – окончательная обработка цилиндрического или конического отверстия разверткой (обычно после зенкерования) в целях получения высокой точности и малой шероховатости обработанной поверхности (рис. 7.17, г, д).
Цекование – обработка торцовой поверхности отверстия торцовым зенкером для достижения перпендикулярности плоской торцовой поверхности к его оси (рис. 7.17, е).
Зенкованием получают в имеющихся отверстиях цилиндрические или конические углубления под головки винтов, болтов, заклепок и других деталей. На рис. 7.17, ж, з показано зенкование цилиндрического углубления цилиндрическим зенкером и конического углубления коническим зенкером.
Нарезание резьбы – получение на внутренней цилиндрической поверхности с помощью метчика винтовой канавки (рис. 7.17, и).
Получение отверстия сложного профиля с помощью комбинированного режущего инструмента показано на рис. 7.17, к – представлен комбинированный зенкер для обработки цилиндрической и конической поверхностей.
7.5 ОБРАБОТКА ЗАГОТОВОК НА СТАНКАХ СТРОГАЛЬНО-ПРОТЯЖНОЙ ГРУППЫ
Характеристика метода строгания. Технологический метод формооб-
разования поверхности заготовок строганием характеризуется наличием двух движений: возвратно-поступательного резца или заготовки (скорость главного движения резания) и прерывистого прямолинейного движения подачи, направленного перпендикулярно к вектору главного движения резания. Разновидно-