
Аксенов А. А. Технология конструкционных материалов
.pdf60
смотря на это, газовая сварка нашла широкое применение в автомобилестроении.
Другие способы термической сварки: электронно-лучевая сварка (для расплавления металла используется электронный луч); лазерная сварка (для расплавления металла применяется лазерный луч).
3.3 ТЕРМОМЕХАНИЧЕСКИЕ И МЕХАНИЧЕСКИЕ ВИДЫ СВАРКИ
Контактная сварка. Она относится к термомеханическому виду сварки и производится кратковременным нагревом места соединения без оплавления или с оплавлением и с последующей осадкой разогретых заготовок. Характерной особенностью данных процессов является пластическое деформирование, в ходе которого формируется сварное соединение.
Стыковая сварка – разновидность контактной сварки, при которой заготовки свариваются по всей поверхности соприкосновения. Свариваемые заготовки закрепляют в зажимах стыковой машины (рис. 3.11). Зажим 3 установлен на подвижной плите 4, перемещающейся в направляющих, зажим 2 укреплен на неподвижной плите 1. Сварочный трансформатор соединен с плитами гибкими шинами и питается от сети через включающее устройство. Плиты перемещаются, и заготовки сжимаются под действием силы F , обеспечиваемой механизмом осадки. Различают сварку сопротивлением – с разогревом стыка до пластического состояния и последующей осадкой – и сварку оплавлением – с разогревом торцов заготовок до оплавления и последующей осадкой. При стыковой сварке сопротивлением заготовки должны быть очищены от оксидных пленок и торцы их плотно пригнаны друг к другу предварительной механической обработкой.
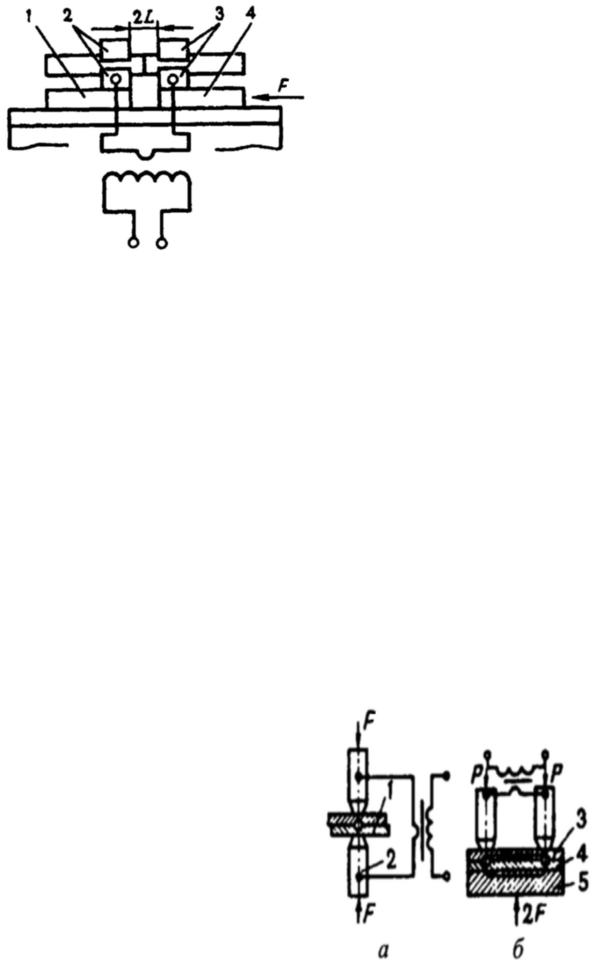
62
сторонней. При двусторонней сварке (рис. 3.12, а) две (или больше) заготовки 1 сжимают между электродами 2 точечной машины. При односторонней сварке (рис. 3.12, б) ток распределяется между верхним и нижним листами 3 и 4, причем нагрев осуществляется частью тока, протекающего через нижний лист. Для увеличения тока, проходящего через нижний лист, предусмотрена медная прокладка 5. Односторонней сваркой можно соединять заготовки одновременно двумя точками. Параметры режима точечной сварки: сила сжатия, плотность тока, время протекания тока.
Точечной сваркой изготавливают штампо-сварные конструкции при соединении отдельных штампованных элементов сварными точками (сборка кузовов на автомобилестроительных заводах и др.). Точечную сварку применяют для изготовления изделий из низкоуглеродистых, углеродистых, низколегированных и высоколегированных сталей, алюминиевых сплавов. Толщина свариваемых металлов составляет 0,5…5 мм.
Многоточечная контактная сварка – разновидность контактной сварки, когда за один цикл сваривается несколько точек. Многоточечную сварку выполняют по принципу односторонней точечной сварки на машинах, которые могут иметь от одной пары до 100 пар электродов (соответственно можно сваривать 2…200 точек за одну установку изделия). В массовом производстве (например, в автомобильной промышленности) применяют машины, работающие по заданной программе, производительность которых очень высока – до 1000 и более точек в минуту.
Шовная контактная сварка – разновидность контактной сварки, при которой между свариваемыми заготовками образуется прочное и плотное соединение. Электроды выполняют в виде плоских роликов, между которыми пропускают свариваемые заготовки. При движении роликов по заготовкам образуются перекрывающие друг друга точки, в результате чего получается сплошной герметичный шов. Шовную сварку, как и точечную, можно выполнять при двустороннем и одностороннем расположении электродов. Данная сварка – очень вы-

63
сокопроизводительный процесс, скорость его может достигать 10 м/мин. Особенно эффективно ее применение в массовом производстве листовых конструкций для получения прочных и герметичных швов (например, при изготовлении емкостей). Допустимая толщина свариваемых заготовок 0,3…3 мм.
Сварка трением. Она происходит в твердом состоянии при воздействии теплоты, возникающей при трении свариваемых поверхностей. Трение поверхностей осуществляется вращением или возвратно-поступательным перемещением сжатых заготовок (рис. 3.13). В результате нагрева заготовок от трения и сжатия происходит совместная пластическая деформация. Сварное соединение образуется вследствие возникновения металлических связей между чистыми контактирующими поверхностями свариваемых заготовок. Оксидные пленки на соединяемых поверхностях разрушаются в результате трения и удаляются в радиальных направлениях (за счет пластической деформации).
Рис. 3.13. Схемы сварки трением:
а – с вращением одной детали; б – с вращением обеих деталей; в – с вращающейся вставкой; г – с возвратно-поступательным движением одной детали
Требуемый нагрев заготовок для сварки обусловлен скоростью вращения. Для получения качественного соединения в конце процесса необходимы быстрое прекращение движения и приложение осадочного сдавливания. Поэтому параметры режима сварки трением (скорость относительного перемещения поверхностей, продолжительность нагрева, сила сжатия, величина осадки, т.е. пластической деформации) зависят от свойств свариваемого металла, площади сечения, конфигурации изделия.
64
Сваркой трением соединяют однородные и разнородные металлы и сплавы с различными свойствами (например, медь со сталью, алюминий с титаном и др.). Соединения получают с достаточно высокими механическими свойствами. В промышленности сварку трением применяют при изготовлении режущего инструмента, различных валов, штоков с поршнями, пуансонов и т.п. При сварке трением по сравнению с контактной стыковой сваркой снижаются затраты энергии в 5…10 раз.
Ультразвуковая сварка. Данная сварка относится к процессам, в которых используют давление и взаимное трение в свариваемых поверхностях. Силы трения возникают в результате действия на заготовки, сжатые осевой силой F , механических колебаний с ультразвуковой частотой, для получения которых используют магнитострикционный эффект, основанный на изменении размеров некоторых материалов под действием переменного магнитного поля. Изменения размеров магнитострикционных материалов очень незначительны, поэтому для увеличения амплитуды и концентрации энергии колебаний, а также для передачи механических колебаний к месту сварки используют волноводы, в большинстве случаев сужающейся формы.

65
При ультразвуковой сварке (рис. 3.14) свариваемые заготовки 5 размещаются на опоре 6. Наконечник 4 рабочего инструмента 3 соединен с магнитострикционным преобразователем 1 через трансформатор 2 продольных упругих колебаний, представляющий собой вместе с рабочим инструментом волновод.
Нормальная сжимающая сила F создается моментом М в узле колебаний, в результате чего в тонких слоях контактирующих поверхностей создаются сдвиговые деформации, разрушающие поверхностные пленки. Тонкие поверхностные слои металла на-
греваются, металл в этих слоях немного размягчается и под действием силы F пластически деформируется. При сближении поверхностей на расстояние действия межатомных сил между ними возникает прочная связь. Сравнительно небольшое тепловое воздействие на свариваемые материалы обеспечивает минимальные изменения их структуры, механических и других свойств. Например, при сварке меди температура в зоне контакта не превышает 600 0С, а при сварке алюминия – 200…300 0С. Это особенно важно при сварке химически активных металлов.
Данный способ сварки позволяет получать соединения разнородных материалов. Ультразвуковую сварку применяют в приборостроении, радиоэлектронике, авиационной промышленности. Особенно широкое применение она находит при сварке пластмасс.
Диффузионная сварка. При диффузионной сварке соединение образуется в результате взаимной диффузии атомов в поверхностных слоях контактирующих материалов, находящихся в твердом состоянии. Диффузионные процессы в поверхностных слоях заготовок протекают достаточно активно при нагреве до температур рекристаллизации и давления, необходимого для пласти-
66
ческого деформирования микровыступов и их смятия с целью обеспечения физического контакта по всей поверхности.
Диффузионную сварку в большинстве случаев выполняют в вакууме, однако она возможна в атмосфере инертных и защитных газов. Свариваемые заготовки 3 (рис. 3.15) устанавливают внутри охлаждаемой металлической каме-
ры 2, в которой создается вакуум 133 (10-3…10-5) Па, и нагревают с помощью вольфрамового или молибденового нагревателя либо индуктора ТВЧ 4. Все вводы в камеру (5 – к вакуумному насосу, 6 – к высокочастотному генератору и др.) хорошо герметизируются. С целью ускорения процесса в камеру может быть введен электронный луч, позволяющий нагревать заготовки с еще более высокими скоростями, чем при использовании ТВЧ. Обычно такой нагрев применяют при диффузионной сварке тугоплавких металлов и сплавов.
После того как достигнута требуемая температура, к заготовкам прикладывают с помощью механического 1, гидравлического или пневматического устройства небольшое сжимающее давление (1…20 МПа) в течение 5…20 мин.
Диффузионной сваркой можно соединять металлы и сплавы, керамические материалы в однородных и разнородных сочетаниях независимо от их термомеханических свойств и взаимного смачивания, получая при этом прочные соединения без какого-либо изменения физико-механических свойств. Полученные соединения после сварки, как правило, не нуждаются в последующей механической обработке. Данную сварку применяют в космической технике и радиоэлектронике, в самолетостроении, приборостроении, в пищевой, автомобильной и других отраслях промышленности.

67
Рис. 3.15. Схема диффузионной сварки в вакууме
Этот способ используют для сварки деталей и узлов вакуумных приборов, высокотемпературных нагревателей, при производстве инструмента и т.д. Единственным недостатком диффузионной сварки является низкая производительность и высокая себестоимость процесса.
Другие способы сварки: высокочастотная сварка (нагрев ТВЧ до пластического состояния с последующим сжатием, приводящим к образованию соединения); сварка взрывом (использование направленного (кумулятивного) взрыва с внешней стороны заготовок).
68
4. ОСНОВЫ ОБРАБОТКИ МЕТАЛЛОВ ДАВЛЕНИЕМ
Обработка давлением – технологический процесс формоизменения заготовки за счет пластической деформации в результате воздействия на деформируемое тело (заготовку) внешних сил. Этот процесс является высокопроизводительным, малоотходным и отличается большой экономичностью и высоким выходом годных изделий с повышенными механическими свойствами. В настоящее время давлением обрабатывается более 90 % выплавляемой стали, свыше 60 % цветных металлов и сплавов. Данным способом можно изготовить детали самых разных размеров (от 2 мкм (фольга) до нескольких метров) и весом (от нескольких грамм до сотен тонн).
Технологические процессы обработки металлов давлением включают: прокатку, волочение, прессование, ковку, штамповку, специальные процессы (отделочные и упрочняющие виды обработки пластическим деформированием металла).
4.1 ФИЗИКО-МЕХАНИЧЕСКИЕ ПРОЦЕССЫ ПРИ ОБРАБОТКЕ МЕТАЛЛОВ ДАВЛЕНИЕМ
Твердые металлические тела под действием внешних сил изменяют свои размеры и форму – деформируются. Различают упругие и пластические деформации, причем всякая пластическая деформация сопровождается упругой.
При упругих деформациях деформируемое тело полностью восстанавливает исходную форму и размеры после снятия внешних сил, а при пластических деформациях изменение формы и размеров, вызванное действием внешних сил, сохраняется и после прекращения действия этих сил. Упругая деформация характеризуется смещением атомов относительно друг друга на величины, меньшие межатомных расстояний, и после снятия внешних сил они возвращаются в свое исходное положение. При пластических деформациях атомы смещаются

69
относительно друг друга на расстояния, большие межатомных, и после снятия внешних сил не возвращаются в свое положение, а занимают новые положения равновесия.
Влияние обработки давлением на структуру и свойства металла. Из-
менение структуры и свойств металла при обработке давлением определяется температурно-скоростными условиями деформирования, в зависимости от которых различают холодную и горячую деформации.
Холодная деформация характеризуется изменением формы зерен, которые вытягиваются в направлении наиболее интенсивного течения металлов (рис. 4.1, а). Здесь формоизменение сопровождается изменением механических и физико-механических свойств металла. Это явление называют упрочнением (наклепом). Изменение механических свойств состоит в том, что при холодной пластической деформации по мере ее увеличения возрастают характеристики прочности, в то время как характеристики пластичности снижаются.
Рис. 4.1. Схемы изменения микроструктуры металла при деформации: а – холодной; б – горячей
Изменения, внесенные холодной деформацией в структуру и свойства металла, являются необратимыми. Они могут быть устранены, например, с помощью термической обработки (отжигом). В этом случае происходит внутренняя перестройка, при которой за счет дополнительной тепловой энергии увеличивается подвижность атомов. В твердом металле без фазовых превращений из множества центров растут новые зерна, заменяющие собой вытянутые, дефор-