
Аксенов А. А. Технология конструкционных материалов
.pdf
110
Рис. 6.5. Углы резца в статике
У токарного резца различают главные и вспомогательные углы, которые рассматривают, исходя из следующих условий: ось резца перпендикулярна к линии центров станка; вершина резца находится на линии центров станка; совершается главное движение резания.
Передний угол γ измеряют в главной секущей плоскости между следом передней поверхности и следом плоскости, перпендикулярной к следу плоскости резания, проходящей через режущую кромку. С увеличением переднего угла уменьшается деформация срезаемого слоя, так как инструмент легче врезается в материал, снижаются силы резания и расход мощности. Одновременно улучшаются условия схода стружки, а качество обработанной поверхности заготовки повышается. Чрезмерное увеличение угла γ приводит к снижению прочности и жесткости главной режущей кромки, увеличению износа вследствие выкрашивания, ухудшению условий теплоотвода от режущей кромки. При обработке заготовок из хрупких и твердых материалов для повышения прочности и стойкости резца следует назначать меньшие значения угла γ , иногда – отрицательные. При обработке заготовок из мягких и вязких материалов угол γ увеличивают.
111
Главный задний угол α измеряют в главной секущей плоскости между следом плоскости резания и следом главной задней поверхности. Наличие угла α уменьшает трение между главной задней поверхностью инструмента и поверхностью резания заготовки, что уменьшает износ инструмента по главной задней поверхности. Чрезмерное увеличение угла α приводит к снижению прочности режущей кромки. Угол α назначают, исходя из величины упругого деформирования материала обрабатываемой заготовки.
Вспомогательный задний угол α1 измеряют во вспомогательной секущей плоскости между следом вспомогательной задней поверхности и следом плоскости, проходящей через вспомогательную режущую кромку перпендикулярно к основной плоскости. Наличие угла α1 уменьшает трение между вспомога-
тельной задней поверхностью инструмента и обработанной поверхностью заготовки.
Угол заострения β – угол между следами передней и задней поверхно-
стей. Определяется как β = 90 −(γ +α).
Угол резания δ – угол между следом передней поверхности и следом плоскости резания. Определяется по формуле δ = 90 −γ .
Углы резания и заострения являются зависимыми от переднего и заднего, но применяются как определяющие при инженерных расчетах резания конкретных материалов.
Угол в плане ϕ – угол между проекцией главной режущей кромки на ос-
новную плоскость и направлением движения подачи – оказывает значительное влияние на шероховатость обработанной поверхности. С уменьшением угла ϕ шероховатость обработанной поверхности снижается. Одновременно увеличивается активная рабочая длина главной режущей кромки. Сила и температура резания, приходящиеся на единицу длины кромки, уменьшаются, что снижает износ инструмента. С уменьшением угла ϕ возрастает сила резания, направ-
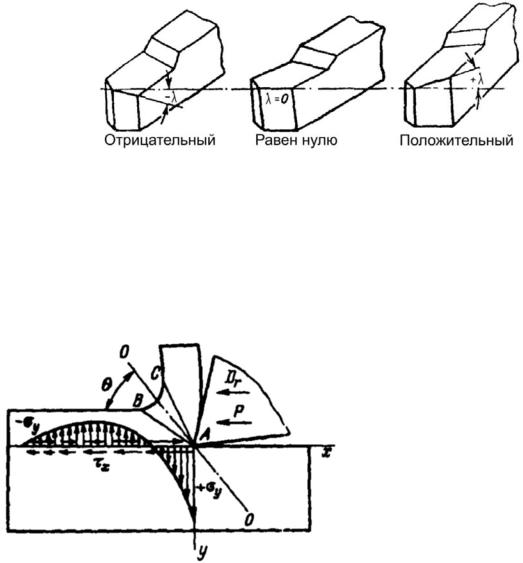
112
ленная перпендикулярно к оси заготовки и вызывающая ее повышенную деформацию, а также возможно возникновение вибраций в процессе резания, снижающих качество обработанной поверхности.
Вспомогательный угол в плане ϕ1 – угол между проекцией вспомогатель-
ной режущей кромки на основную плоскость и направлением обратного дви-
жения подачи. С уменьшением угла ϕ1 шероховатость обработанной поверхно-
сти снижается, увеличивается прочность вершины резца, снижается его износ.
Угол наклона режущей кромки λ – угол в плоскости резания между ре-
жущей кромкой и основной плоскостью. Угол λ влияет на направление схода стружки; бывает отрицательным и положительным (рис. 6.6).
Рис. 6.6. Угол наклона режущей кромки
6.2 ФИЗИЧЕСКАЯ СУЩНОСТЬ ПРОЦЕССА РЕЗАНИЯ
Стружкообразование. Резание металлов – сложный процесс взаимодействия режущего инструмента и заготовки, сопровождающийся определенными физическими явлениями. Упрощенно процесс резания можно представить по следующей схеме. В начальный момент процесса резания, когда движущийся резец под действием силы резания Р (рис. 6.7) вдавливается в
Рис. 6.7. Упругонапряженное состояние металл, в срезаемом слое возни-
металла при обработке резанием
113
кают упругие деформации. При движении резца они, накапливаясь по абсолютной величине, переходят в пластические. В прирезцовом срезаемом слое материала заготовки возникает сложное упругонапряженное состояние: в плоскости, перпендикулярной к траектории движения резца, возникают нормальные напряжения σy , а в плоскости, совпадающей с траекторией движения резца, –
касательные напряжения τx . В точке приложения действующей силы значение
τx наибольшее, а по мере удаления от точки A τx уменьшается. Нормальные напряжения σy вначале действуют как растягивающие, затем они уменьшают-
ся и переходят в напряжения сжатия. Таким образом, срезаемый слой металла находится под действием давления резца, касательных и нормальных напряжений.
Сложное упругонапряженное состояние металла приводит к пластической деформации, а ее рост – к сдвиговым деформациям, т.е. к смещению частей кристаллитов относительно друг друга. Сдвиговые деформации происходят в зоне стружкообразования ABC , причем деформации начинаются по плоскости AB и заканчиваются по плоскости AC , в которой завершается разрушение кристаллитов, т.е. скалывается элементарный объем металла и образуется стружка. Далее процесс повторяется и образуется следующий элемент стружки.
Условно считают, что сдвиговые деформации происходят по плоскости
ОО, которую называют плоскостью сдвига. Она располагается под углом
θ≈300 к направлению движения резца. Угол θ называют углом сдвига. Нали-
чие поверхности сдвига в процессе стружкообразования и положение ее в пространстве установлены русскими учеными И.А. Тиме и К.А. Зворыкиным. Срезанный слой металла дополнительно деформируется вследствие трения стружки о переднюю поверхность инструмента.
При резании металлов образуется стружка, которую разделяют на сливную, стружку скалывания (суставчатую) и надлома.

114
Сливная стружка, появляющаяся при резании пластичных металлов, представляет собой сплошную ленту длиной до нескольких метров с гладкой прирезцовой стороной. На внешней ее стороне видны слабые пилообразные зазубрины.
Стружка скалывания, образующаяся при резании металлов средней твердости, представляет собой ленту длиной 15…20 мм с гладкой прирезцовой стороной, на внешней стороне с ярко выраженными зазубринами.
Стружка надлома образуется при резании хрупких металлов и состоит из отдельных, не связанных между собой элементов. Вид образующейся стружки зависит от физико-механических свойств металла обрабатываемой заготовки, режима резания, геометрических параметров режущего инструмента, применяемых в процессе резания смазочно-охлаждающих средств.
Вид образующейся стружки влияет на износ инструмента, шероховатость обработанной поверхности, силу резания. От вида стружки зависит возможность ее автоматического отвода из зоны резания и транспортирования. Чтобы перевести стружку из одного состояния в другое в конструкции режущего инструмента вводят стружколомательные устройства, пороги, разделительные канавки. Однако все применяемые мероприятия не решают проблем удаления стружки от заготовок и со станка, ее транспортирования и дальнейшей переработки.
Стружка, образующаяся в процессе резания, подвергается значительному пластическому деформированию, в результате которого происходят ее укорочение и утолщение. Эти изменения стружки состоят в том, что длина стружки оказывается меньше длины обработанной поверхности, а толщина – больше
толщины среза. Изменение размеров стружки характеризуется усадкой ξ = lстр.
lзаг.
и коэффициентом усадки K = ξ1 стружки. Чем пластичнее металл заготовки,
тем больше значение усадки стружки. Для заготовок из хрупких металлов ξ

115
близка к 1, а для заготовок из пластичных металлов ξ доходит до 5…7. Усадка стружки зависит от физико-механических свойств обрабатываемого металла, режима и условий резания, геометрических параметров инструмента.
Силовое взаимодействие инструмента и заготовки. Деформирование и срезание с заготовки слоя металла происходят под действием внешней силы резания, приложенной со стороны инструмента к обрабатываемой заготовке. Направление вектора силы совпадает с вектором скорости главного движения резания v . Работа, затрачиваемая на деформирование и разрушение материала за-
готовки (Pv), расходуется на упругое и пластическое деформирование метал-
ла, его разрушение, на преодоление сил трения задних поверхностей о заготовку и стружки о переднюю поверхность лезвия инструмента.
В результате сопротивления металла процессу деформирования возникают активные силы, действующие на режущий инструмент. Реактивные силы – это силы упругого ( Рy1 и Py 2 ) и пластического ( Pn1 и Pn 2 ) деформирования,
векторы которых направлены перпендикулярно к передней и задней поверхностям лезвия резца (рис. 6.8, а). Наличие нормальных сил обусловливает возник-
новение сил трения ( F1 и F2 ), направленных по передней и задней поверхно-
стям лезвия инструмента. Указанную систему сил приводят к равнодействующей силе резания:
P = Py1 + Py 2 + Pn1 + Pn 2 + F1 + F2 . |
(6.5) |
Рис. 6.8. Силы, действующие на резец (а), и разложение силы резания на составляющие (б) при обработке заготовки на универсальном токарном станке

116
Считают, что точка приложения силы резания P находится на главной режущей кромке инструмента (рис. 6.8, б). Абсолютное значение, точка приложения и направление равнодействующей силы резания в процессе обработки переменны. Это можно объяснить неоднородностью структуры материала заготовки, переменной поверхностной твердостью материала заготовки, непостоянством срезаемого слоя металла, наличием штамповочных и литейных уклонов, изменением углов γ и α в процессе резания. Для расчетов используют не рав-
нодействующую силу резания, а ее составляющие, действующие по трем взаимно перпендикулярным направлениям – координатным осям металлорежущего станка. Обозначения составляющих силы резания приведены по ГОСТ 25762-83 для универсального токарного и других станков (для станков с ЧПУ действует международный стандарт ISO 841, в котором приняты другие обозначения осей координат).
Главная составляющая силы резания для токарных станков Pz действует в плоскости резания в направлении главного движения резания по оси z . По этой силе определяют крутящий момент на шпинделе станка, эффективную мощность резания, деформацию изгиба заготовки, изгибающий момент, действующий на стержень резца, а также ведут динамический расчет механизмов ко-
робки скоростей станка. Радиальная составляющая силы резания Py действует в плоскости xOy перпендикулярно к оси заготовки, по которой определяют ве-
личину упругого отжатия резца от заготовки и деформацию изгиба заготовки в плоскости xOy . Осевая составляющая силы резания Px действует в плоскости xOy вдоль оси заготовки, по которой рассчитывают механизм подачи станка, а
также изгибающий момент, действующий на стержень резца.
При условии, |
что |
Pz > Py |
> Px , и учитывая их экспериментально полу- |
|||
ченное соотношение как 1:0,45:0,35, равнодействующая сил резания, Н |
||||||
P = P2 |
+ P2 + P2 = |
P2 |
+(0,45P )2 |
+(0,35P )2 |
=1,14P . (6.6) |
|
z |
y |
x |
z |
z |
z |
z |

|
|
|
117 |
|
|
|
|
|
|
Силу Pz определяют по эмпирической формуле, Н |
|
||||||
|
P = C |
P |
t xPz s yPz |
vnPz k |
M |
, |
(6.7) |
|
|
z |
|
|
|
P |
|
||
|
|
z |
|
|
|
|
|
|
|
|
|
|
|
|
|
z |
|
где CP – коэффициент, учитывающий физико-механические свойства материа- |
||||||||
|
z |
|
|
|
|
|
|
|
ла обрабатываемой заготовки; kM P |
– коэффициент, учитывающий факторы, не |
|||||||
|
z |
|
|
|
|
|
|
|
вошедшие в формулу, значения углов резца, материал резца и т.д. |
|
|||||||
|
Значения коэффициентов CP |
|
и kM |
P |
, а также показателей степеней |
xP , |
||
|
z |
|
|
|
|
|
z |
|
|
|
|
|
z |
|
|
|
|
yP |
и nP даны в справочниках для конкретных условий обработки. Зависимо- |
|||||||
z |
z |
|
|
|
|
|
|
|
сти силы Pz от разных факторов приведены на рис. 6.9, из их анализа можно сделать вывод, что наибольшее влияние на возрастание силы Pz оказывает уве-
личение глубины резания, меньшее влияние – увеличение подачи, а при увеличении скорости резания и угла ϕ (с 300 до 600) уменьшается усилие резания.
Рис. 6.9. Графические зависимости силы Pz |
от глубины резания t (а), подачи s (б), |
|
скорости резания v (в) и главного угла в плане ϕ (г) |
|
|
Крутящий момент на шпинделе станка, Н м |
|
|
МКР = |
Pz DЗАГ . . |
(6.8) |
|
2 |
|
Эффективной мощностью называют мощность, расходуемую на процесс деформирования и срезания с заготовки слоя металла. При точении цилиндрической поверхности на токарно-винторезном станке эффективная мощность, кВт
|
118 |
|
|
|
|
|
Ne = |
Pz v |
= |
Px nsПР |
, |
(6.9) |
|
60 103 |
60 106 |
|||||
|
|
|
|
где n – частота вращения заготовки, мин-1. Мощность электродвигателя станка, кВт
N |
|
= |
Ne |
, |
(6.10) |
|
|
||||
|
Э |
|
η |
|
где η – КПД механизмов и передач станка.
Наростообразование при резании металлов. При обработке пластич-
ных металлов резанием на передней поверхности лезвия инструмента образуется металлический наплыв, который называют наростом. Это сильно деформированный металл высокой твердости, структура которого отличается от структур обрабатываемого металла и стружки.
Образование нароста объясняется тем, что геометрическая форма инструмента не идеальна для обтекания ее металлом. При некоторых условиях обработки силы трения между передней поверхностью инструмента и частицами срезаемого слоя металла становятся больше сил внутреннего сцепления, и при определенных температурных условиях металл прочно закрепляется на передней поверхности лезвия инструмента.
В процессе обработки резанием размеры и форма нароста непрерывно меняются в результате действия сил трения между отходящей стружкой и внешней поверхностью нароста. Частицы нароста периодически уносятся стружкой, переходят на обработанную поверхность заготовки, иногда нарост целиком срывается с передней поверхности инструмента и тут же вновь образуется (рис. 6.10, а). Объясняется это тем, что нарост находится под действием силы трения F , сил сжатия P1 и P2 , силы растяжения Q (рис. 6.10, б). С изме-
нением размеров нароста меняется соотношение действующих сил. Когда сум-
ма сил P1 , P2 и Q становится больше силы трения F , происходит разрушение

119
и срыв нароста. Частота срывов нароста зависит от скорости резания и достигает нескольких сотен в секунду.
Рис. 6.10. Схемы образования и разрушения нароста (а) и силы, действующие на нарост (б)
Нарост существенно влияет на процесс резания и качество обработанной поверхности заготовки, так как при его наличии меняются условия стружкообразования.
Положительное влияние нароста состоит в том, что при его наличии меняется форма передней поверхности лезвия инструмента, это приводит к увеличению главного переднего угла, а следовательно, к уменьшению силы резания. Вследствие высокой твердости нарост способен резать металл. Нарост удаляет центр давления стружки от главной режущей кромки, в результате чего уменьшается износ режущего инструмента по передней поверхности лезвия. Нарост улучшает теплоотвод от режущего инструмента.
Отрицательное влияние нароста состоит в том, что он увеличивает шероховатость обработанной поверхности. Частицы нароста, внедрившиеся в обработанную поверхность, при работе детали с сопрягаемой деталью вызывают повышенный износ пары. Вследствие изменения наростом геометрических параметров режущего инструмента меняются размеры обрабатываемой поверхности в поперечных диаметральных сечениях по длине заготовки, и обработанная поверхность получается волнистой. Из-за изменения переднего угла инструмента меняется сила резания, что вызывает вибрацию узлов станка и инструмента, а это, в свою очередь, ухудшает качество обработанной поверхности.