
Аксенов А. А. Технология конструкционных материалов
.pdf90
Волочение труб можно выполнять без оправки (для уменьшения внешнего диаметра) и с оправкой (для уменьшения внешнего диаметра и толщины стенки). На рис. 5.7, б показана схема волочения трубы 1 на короткой удерживаемой оправке 3. В этом случае профиль полученной трубы определяется зазором между волокой 2 и оправкой 3. Поскольку тянущая сила, приложенная к заготовке, необходима не только для деформирования металла, но и для преодоления сил трения металла об инструмент, эти силы трения стараются уменьшить применением смазки и полированием отверстия волоки.
Обычно для получения необходимых профилей требуется деформация, превышающая допустимую за один проход, поэтому применяют волочение через ряд постепенно уменьшающихся по диаметру отверстий. Но, поскольку волочение осуществляют в условиях холодной деформации, металл упрочняется. Для восстановления пластичности упрочненный волочением металл подвергают промежуточному отжигу. Обычно его производят после трехкратного волочения.
Волочением обрабатывают различные марки стали, цветные металлы и их сплавы. Сортамент изделий, изготовляемых волочением, очень разнообразен: проволока диаметром 0,002…5 мм и фасонные профили (призматические и фасонные направляющие; сегментные, призматические и фасонные шпонки; шлицевые валики, опорные призмы, ножи и т.д.). Волочением калибруют стальные трубы диаметром от капиллярных до 200 мм, стальные прутки диаметрами 3…150 мм. Поскольку волочение производят в условиях холодной деформации, оно обеспечивает высокую точность размеров (стальная проволока диаметром 1…1,6 мм имеет допуск 0,02 мм), низкую шероховатость поверхности, получение очень тонкостенных профилей.
Волоку изготовляют из инструментальных сталей, металлокерамических сплавов и технических алмазов (для волочения профилей менее 0,2 мм). Волочение производят на барабанных (волочение проволоки, труб небольшого диа-
91
метра, наматываемых на бунты) и цепных (волочение прутков и труб, которые нельзя наматывать в бунты) станах.
Производство гнутых профилей. При изготовлении прокаткой фасонных профилей невозможно получить стенки толщиной менее 2..3 мм. В то же время по требуемой прочности в конструкциях такая толщина нередко завышена. Кроме того, горячекатаные профили имеют технологические напуски (внутренние радиусы скругления, уклоны), увеличивающие их массу. Фасонные тонкостенные профили, легкие, но жесткие, весьма сложной конфигурации и большой длины можно получать методом профилирования листового материала в холодном состоянии. Процесс профилирования прокаткой на профилегибочных станах заключается в постепенном изменении формы сечения плоской заготовки до требуемого профиля при последовательном прохождении полосы или ленты через несколько пар (6…20 и более) вращающихся фигурных роликов. При данном методе площадь поперечного сечения и толщина исходной полосы или ленты практически не изменяются, т.е. происходит только последовательная гибка полосы или ленты в поперечном сечении.
На рис. 5.8, а показано последовательное изменение плоской заготовки до требуемого профиля на профилегибочном стане. Число пар роликов, необходимое для изготовления того или иного профиля, зависит от сложности его конфигурации. Заготовкой при изготовлении гнутых профилей может быть лента или полоса из стали или цветных металлов толщиной 0,3…10 мм. Форма гнутых профилей (рис. 5.8, б) может быть и относительно простой (профиль открытого типа) и весьма сложной (профили полузакрытого и закрытого типов, профили с наполнением).
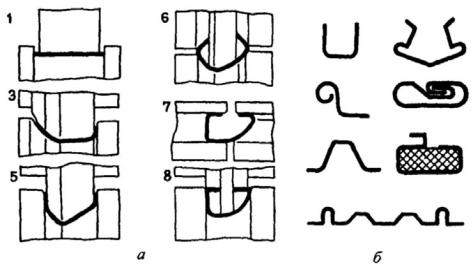
92
Рис. 5.8. Последовательность профилирования на профилегибочном стане (а) и примеры гнутых профилей (б):
1, 3, 5 – 8 – номера пар роликов (пары роликов 2 и 4 на рисунке не показаны)
Указанным способом получают большое количество изделий для машиностроения, автомобильной и авиационной промышленности, строительных конструкций.
5.2 ИЗГОТОВЛЕНИЕ ПОКОВОК МАШИНОСТРОИТЕЛЬНЫХ ДЕТАЛЕЙ
Виды поковок. Поковкой называют заготовку детали, полученную ковкой или штамповкой. Поковки могут быть сгруппированы по признакам, определяющим технологию их изготовления. Такими признаками являются масса, конфигурация, марка сплава и тип производства.
Масса поковок, которая может быть от сотен граммов до сотен тонн, определяет тип заготовки, вид деформации и схему деформирования. Исходными заготовками являются слитки (для получения поковок от нескольких сотен килограмм) или сортовой прокат круглого, квадратного или прямоугольного сечения.
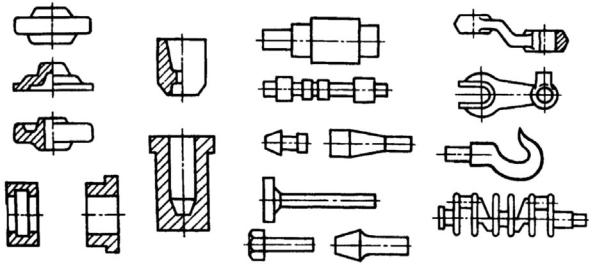
93
Рис. 5.9. Виды машиностроительных поковок
Поскольку при горячей деформации давления, необходимые для формоизменения нагретого металла, ниже, чем при холодной деформации, последняя используется для поковок малой массы (1 кг и менее).
Изготовление поковок может осуществляться по схемам свободного пластического течения между поверхностями инструмента или затекания металла в полость штампа. Для заполнения полости штампа необходимо давление, значительно превышающее давление при свободном пластическом течении металла. Вследствие этого поковки большой массы затруднительно изготовлять штамповкой. Для тяжелых поковок (массой ориентировочно 1…250 т) единственно возможным способом изготовления является ковка – вид горячей обработки металлов давлением, при котором деформирование производят последовательно на отдельных участках заготовки. Металл свободно течет в стороны, не ограниченные рабочими поверхностями инструмента, в качестве которого применяют плоские или фигурные (вырезные) бойки, а также различный подкладной инструмент. Таким образом, при ковке используют универсальный (годный для изготовления различных поковок) инструмент, в то время как для штамповки требуется специальный инструмент – штамп, изготовление которого при небольшой партии одинаковых поковок экономически невыгодно. Поэтому в
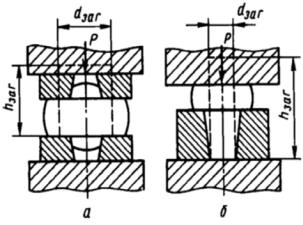
94
единичном и мелкосерийном производствах ковка обычно экономически более целесообразна.
Ковка. Процесс ковки состоит из чередования в определенной последовательности основных и вспомогательных операций. Каждая операция определятся характером деформирования и применяемым инструментом.
К основным операциям ковки относятся осадка, протяжка, прошивка, от-
рубка и гибка. |
|
Осадка – операция уменьше- |
|
ния высоты заготовки при увеличе- |
|
нии площади ее поперечного сечения |
|
(рис. 5.10, а). Осаживают заготовки |
|
между бойками или подкладными |
|
плитами. Разновидностью осадки яв- |
|
ляется высадка, при которой металл |
|
осаживают лишь на части длины за- |
Рис. 5.10. Схемы осадки в кольцах (а) |
готовки (рис. 5.10, б). |
и высадки (б) |
Протяжка – операция удлинения заготовки или ее части за счет уменьшения площади поперечного сечения (рис. 5.11, а). Ее производят последовательными ударами или нажатиями на отдельные участки заготовки, примыкающие один к другому, с подачей заготовки вдоль оси протяжки и поворотами ее на 900 вокруг этой оси. Чем меньше подача при каждом нажатии, чем интенсивнее удлинение. Однако при слишком малой подаче могут получиться зажимы (рис. 5.11, б). Протягивать можно плоскими (рис. 5.11, а) и вырезными (рис. 5.11, в) бойками.
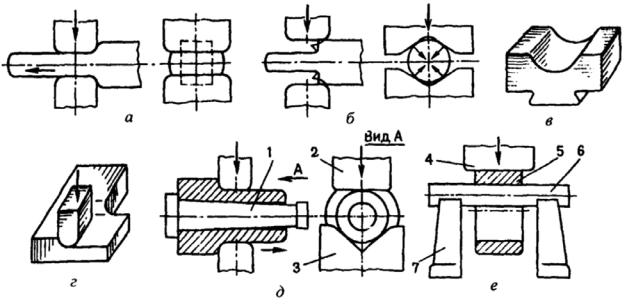
95
Рис. 5.11. Схемы протяжки и ее разновидностей
Разгонка – операция увеличения ширины части заготовки за счет уменьшения ее толщины (рис. 5.11, г).
Протяжка с оправкой – операция увеличения длины пустотелой заготовки за счет уменьшения толщины ее стенок (рис. 5.11, д).
Раскатка на оправке – операция одновременного увеличения наружного и внутреннего диаметров кольцевой заготовки за счет уменьшения толщины ее стенок. После каждого нажатия заготовку поворачивают относительно оправки
(рис. 5.11, е).
Прошивка – операция получения полостей в заготовке за счет вытеснения металла (рис. 5.12, а). Прошивкой можно получить сквозное отверстие или углубление (глухая прошивка). Инструментом для прошивки служат прошивни (рис. 5.12, в) сплошные и пустотелые (последними прошивают отверстия большого диаметра, т.е. 400…900 мм). При сквозной прошивке сравнительно тонких поковок применяют подкладные кольца (рис. 5.12, б).
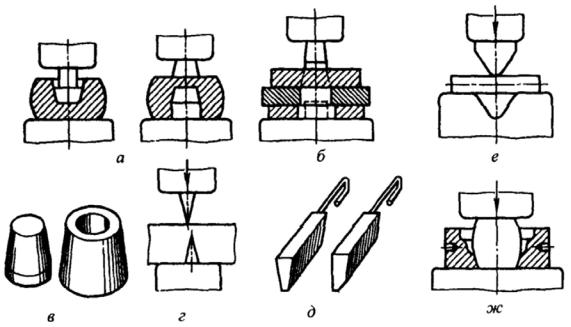
96
Рис. 5.12. Схемы операций ковки:
а– двусторонняя прошивка; б – сквозная прошивка; в – прошивни; г – отрубка;
е– гибка; ж – штамповка в подкладных штампах
Отрубка – операция отделения части заготовки по незамкнутому контуру путем внедрения в заготовку деформирующего инструмента – топора (рис. 5.12, г). Отрубку применяют для получения из заготовок большой длины нескольких коротких, для удаления излишков металла на концах поковок, а также прибыльной и донной частей слитков и т.п. Инструментами для отрубки служат топоры различной формы (рис. 5.12, д).
Гибка – операция придания заготовке изогнутой формы по заданному контуру (рис. 5.12, е). Этой операцией получают угольники, скобы, крючки, кронштейны и т.п. Гибка сопровождается искажением первоначальной формы поперечного сечения заготовки и уменьшением его площади в зоне изгиба, называемым утяжкой. Для компенсации утяжки в зоне изгиба заготовке придают увеличенные поперечные размеры.
Перечисленными операциями ковки трудно изготовить поковки с относительно сложной конфигурацией. Поэтому при изготовлении небольшой партии таких поковок применяют так называемую штамповку в подкладных штампах (рис. 5.12, ж). Подкладной штамп может состоять из одной или двух частей, в

97
которых имеется полость с конфигурацией поковки или ее отдельного участка. В подкладных штампах можно изготовлять головки гаечных ключей, головки болтов, диски со ступицей, втулки с буртом и другие поковки.
Оборудование для ковки выбирают в зависимости от режима ковки данного материала или сплава, массы поковки и ее конфигурации. Необходимую мощность оборудования обычно определяют по приближенным формулам или справочным таблицам. Ковку выполняют на ковочных молотах (деформация в тысячные доли секунды) или ковочных гидравлических прессах (деформация в десятки секунд).
Горячая объемная штамповка. В зависимости от типа штампов выделяют штамповку в открытых и закрытых штампах.
Штамповка в открытых штампах, или облойная штамповка
(рис. 5.13, а), характеризуется переменным зазором между подвижной и неподвижной частями штампа. В этот зазор вытекает часть металла – облой, который закрывает выход из полости штампа и заставляет остальной металл целиком заполнить всю полость. В конечный момент деформирования в облой выжимаются излишки металла, находящиеся в полости, что позволяет не предъявлять высоких требований к точности заготовок по массе. Облой затем обрезается в специальных штампах. Данным видом штамповки можно получать поковки практически всех типов.
Рис. 5.13. Схемы штамповки в открытых и закрытых штампах: 1 – облойная канавка
98
Штамповка в закрытых штампах, или безоблойная штамповка
(рис. 5.10, б), характеризуется тем, что полость штампа в процессе деформирования остается закрытой. Зазор между подвижной и неподвижной частями штампа при этом постоянный и небольшой, так что образование облоя в нем не предусмотрено. Устройство таких штампов зависит от типа машины, на которой штампуют. Например, нижняя половина штампа может иметь полость, а верхняя – выступ (на прессах), или наоборот (на молотах). Закрытый штамп может иметь не одну, а две взаимно перпендикулярные плоскости разъема, т.е. состоять из трех частей (рис. 5.10, в).
При штамповке в закрытых штампах необходимо строго соблюдать равенство объемов заготовки и поковки, иначе при недостатке металла не заполняются углы полости штампа, а при избытке размер поковки по высоте будет больше требуемого. Следовательно, в этом случае процесс получения заготовок усложняется, поскольку отрезка заготовок должна обеспечивать высокую точность. Как правило, штамповкой в закрытых штампах получают осесимметричные поковки типа втулок, колес и стаканов.
Существенным преимуществом штамповки в закрытых штампах является уменьшение расхода металла, поскольку нет отхода в облой. Поковки, полученные в закрытых штампах, имеют более благоприятную структуру, так как волокна обтекают контур поковки, а не перерезаются в месте выхода металла в облой. При штамповке в закрытых штампах металл деформируется в условиях всестороннего сжатия при больших сжимающих напряжениях, чем в открытых штампах. Это позволяет получать большие степени деформации и штамповать малопластичные сплавы.
Оборудованием для горячей объемной штамповки являются: молоты (паровоздушные штамповые молоты с массой падающих частей 630…25000 кг, штампуют за несколько ударов), горячештамповочные кривошипные прессы (штампуют за один ход, поэтому производительность выше молотов, усилия составляют 6,3…100 МН, но заготовка перед штамповкой должна быть полно-
99
стью очищена от окалины), горизонтально-ковочные машины (создают усилие 31,5 МН), гидравлические прессы (усилие 750 МН) и машины для специализированных процессов штамповки (изотермическая штамповка). Процессы штамповки на этих машинах имеют свои особенности, обусловленные устройством и принципом их действия.
Для получения поковок также применяются методы штамповки на ковочных вальцах, штамповки на ротационно-ковочных машинах, поперечноклиновой прокатки, раскатки кольцевых заготовок на раскатных станах и горячей накатки зубчатых колес.
Жидкая штамповка. Это технологический процесс получения заготовок деталей, при котором кристаллизация жидкого металла, залитого в полость инструмента, происходит под высоким давлением. Это обеспечивает повышение коэффициента теплоотдачи и, следовательно, скорости охлаждения, поэтому структура металла получается более мелкозернистой, чем в отливках.
Холодная объемная штамповка. Это штамповка без предварительного нагрева заготовки. При этом отсутствует окисление металла на поверхности, что обеспечивает хорошее качество поверхности детали и высокую точность размеров. Основные разновидности холодной объемной штамповки – холодное выдавливание, холодная высадка и холодная штамповка в открытом штампе.
При холодном выдавливании заготовку помещают в полость, из которой металл выдавливают в отверстия, имеющиеся в рабочем инструменте. Производится выдавливание на кривошипных или гидравлических прессах в штампах, рабочими частями которых являются пуансон и матрица. Различают прямое, обратное, боковое и комбинированное выдавливание.
Холодную высадку выполняют на специальных холодновысадочных автоматах. Пруток или проволока подается в штамп, поперечным движением ножа отрезается заготовка требуемой длины и с помощью специального механизма последовательно переносится в позиции штамповки, на которых из заготовки