
Аксенов А. А. Технология конструкционных материалов
.pdf150
ной линейки. Сквозные отверстия на токарно-винторезных станках растачивают проходными расточными резами (рис. 7.7, д), глухие – упорными (рис. 7.7,
е).
С поперечным движением подачи на токарно-винторезных станках обтачивают кольцевые канавки (рис. 7.7, з) прорезными резцами, фасонные поверхности (рис. 7.7, и) – фасонными стержневыми резцами, короткие конические поверхности – фаски (рис. 7.7, к) – широкими резцами. Для отрезки деталей от заготовки (рис. 7.7, л) используют отрезные резцы с наклонной режущей кромкой, что обеспечивает после отрезания чистый торец на готовой детали; для подрезания торцов (рис. 7.7, н) – специальные подрезные резцы.
На токарно-винторезных станках обработку отверстий производят сверлами (рис. 7.7, м), зенкерами и развертками. Обработку конусных поверхностей средней длины с любым углом конуса (рис. 7.7, ж, о) при вершине производят с наклонным движением подачи резцов при повороте верхнего суппорта.
7.3 ОБРАБОТКА ЗАГОТОВОК НА СТАНКАХ ФРЕЗЕРНОЙ ГРУППЫ
Фрезерование – один из высокопроизводительных и распространенных методов обработки поверхностей заготовок многолезвийным режущим инструментом – фрезой. Технологический метод формообразования поверхностей фрезерованием характеризуется главным вращательным движением инструмента и обычно поступательным движением подачи.
На фрезерных станках обрабатывают горизонтальные, вертикальные и наклонные плоскости, фасонные поверхности, уступы и пазы различных профилей. Особенностью процесса фрезерования является прерывистость резания каждым зубом фрезы, который находится в контакте с заготовкой и выполняет работу резания только на некоторой части оборота, а затем вращается, не касаясь заготовки, до следующего врезания.

151
На рис. 7.8 показаны схемы фрезерования плоскости цилиндрической (а) и торцовой (б) фрезами. При цилиндрическом фрезеровании плоскостей работают зубья, расположенные на цилиндрической поверхности фрезы, а при торцовом фрезеровании плоскостей – зубья, расположенные на цилиндрической и торцовой поверхностях фрезы.
Рис. 7.8. Схемы фрезерования цилиндрической (а) и торцовой (б) фрезами против движения подачи (в) и по направлению движения подачи (г):
1 – заготовка; 2 – фреза
Фрезерование в зависимости от направления вращения фрезы можно осуществлять двумя способами:
– встречное фрезерование, когда направление скорости движения подачи противоположно направлению скорости главного движения резания (рис. 7.8, в). При данном способе фрезерования нагрузка на зуб фрезы возрастает от нуля до максимума, при этом сила, действующая на заготовку, стремится оторвать ее от стола, что приводит к вибрациям и увеличению шероховатости обработанной поверхности. Встречное фрезерование обеспечивает подход фрезы к твердому поверхностному слою снизу и отрывание стружки в точке В, но также и наличие начального скольжения зуба по наклепанной поверхности, образованной предыдущем зубом;
152
–попутное фрезерование, когда направления скоростей движения подачи
иглавного движения резания совпадают (рис. 7.8, г). Здесь зуб фрезы сразу начинает срезать слой максимальной толщины и подвергается максимальной нагрузке. Это исключает начальное проскальзывание зуба, уменьшает износ фрезы и шероховатость обработанной поверхности, но при данном способе фрезерования увеличивается себестоимость процесса.
Крежиму резания при фрезеровании относят скорость главного движения резания v , подачу s, глубину резания t , ширину фрезерования В. Скорость главного движения резания соответствует окружной скорости вращения фрезы, м/с
v = |
πDn |
, |
(7.8) |
|
1000 |
|
|
где D – диаметр фрезы, мм; n – частота вращения фрезы, с-1.
Подача при фрезеровании – величина перемещения обрабатываемой заготовки в минуту (мм/мин), за время углового поворота фрезы на один зуб (мм/зуб) или за время одного оборота фрезы (мм/об). Глубина резания (мм) – расстояние между обрабатываемой и обработанной поверхностями. Ширина фрезерования (мм) измеряется в направлении, параллельном оси фрезы при цилиндрическом фрезеровании и перпендикулярном к направлению движения подачи при торцовом фрезеровании.
Типы фрезерных станков. Фрезерные станки по конструкции многообразны. Выпускают универсальные, специализированные и специальные фрезерные станки.
К универсальному виду оборудования относят консольные горизонталь-
но- и вертикально-фрезерные станки (рис. 7.9, а и б); они имеют много общих узлов. В станине 1, по вертикальным направляющим которой перемещается консоль 7 с коробкой подач 8, размещена коробка скоростей 2. Заготовка устанавливается на столе 4 в тисках или приспособлении и может перемещаться в трех направлениях: продольном (перемещение стола по направляющим салазок
153
6), поперечном (перемещение салазок по направляющим консоли) и вертикальном (перемещение консоли по направляющим станины).
На горизонтально-фрезерном станке хобот 3 служит для закрепления подвески 5, поддерживающей конец фрезерной оправки. Станки, имеющие поворотную плиту, которая позволяет поворачивать рабочий стол в горизонтальной плоскости на требуемый угол, называют универсальными.
На вертикально-фрезерном станке шпиндельная головка 3 может поворачиваться в вертикальной плоскости.
Крестовый стол вертикально-фрезерного бесконсольного станка с ЧПУ
(рис. 7.9, в) имеет перемещение по двум взаимно перпендикулярным координа-
там x′ (перемещение стола 3 по салазкам 2) и y′ (перемещение салазок 2 по направляющим станины 1). По третьей координате z′ движение обеспечивается перемещением шпиндельной головки 4 по направляющим стойки 5. Обработку заготовок на фрезерных станках с ЧПУ производят попутным и встречным фрезерованием с одинаковой точностью, так как в коробках подач предусмотрено устройство для выбора зазоров. Программированные перемещения заготовки относительно инструмента одновременно по нескольким координатам позволяют получать сложные фасонные поверхности.

154
Рис. 7.9. Основные типы фрезерных станков
Продольно-фрезерные станки предназначены для обработки заготовок больших масс и размеров (типа станин, корпусов, коробок передач, рамных конструкций и т.п.). Их строят одно- и двухстоечными с длиной стола 1250…12000 мм и шириной 400…5000 мм. На рис. 7.9, г показан продольнофрезерный двухстоечный станок. Стол 2 станка, на котором устанавливают заготовку, имеет только одно продольное перемещение по направляющим стани-
155
ны 1. На каждой стойке 4 расположены фрезерные головки 3, которые могут перемещаться по их направляющим вверх и вниз. В верхней части стойки соединены поперечиной 6, что повышает общую жесткость станка. По вертикальным направляющим стоек перемещается траверса 5. Шпиндель каждой фрезерной головки может выдвигаться в осевом направлении на 100…200 мм.
На фрезерных станках непрерывного действия фрезеруют плоские по-
верхности при обработке больших партий заготовок по методу непрерывного торцового фрезерования. Их подразделяют на карусельно-фрезерные и бара- банно-фрезерные.
Карусельно-фрезерный станок показан на рис. 7.9, д. На станине 1 смонтирована стойка 2, по вертикальным направляющим которой перемещается фрезерная головка 3 с двумя шпинделями, один из которых предназначен для чистовой обработки. На круглом столе 4 (карусели) с вертикальной осью вращения в приспособлениях устанавливают заготовки. Круглый стол имеет салазки 5 для установки его на направляющих станины. Заготовки устанавливают и снимают со стола без остановки станка; фрезерование ведется непрерывно при медленно вращающемся столе.
Особенностью барабанно-фрезерных станков является наличие барабана с горизонтальной осью вращения. На гранях барабана в приспособлениях устанавливают заготовки, которым медленным вращением барабана сообщают движение круговой подачи. Станки имеют одну или несколько головок.
Копировально-фрезерные станки предназначены для обработки фасонных поверхностей сложного профиля. Различают контурное и объемное фрезерование. Контурное фрезерование применяют для получения плоских фасонных поверхностей замкнутого криволинейного контура с прямолинейной образующей (например, плоских кулачков, шаблонов и т.п.). Объемное фрезерование применяют для получения объемных фасонных поверхностей (например, лопаток турбин, пресс-форм и т.п.).
156
На рис. 7.9, е показан копировально-фрезерный станок полуавтомат для объемного фрезерования. По направляющим станины 1 в продольном направлении перемещается вертикальный стол 6, на котором устанавливают приспособления для закрепления заготовки и копира. На стойке 2 смонтирована фрезерная головка 3, перемещающаяся по вертикальным направляющим стойки. Фрезерная головка и жестко скрепленное с ней следящее устройство 4 со щупом 5 могут перемещаться вдоль оси шпинделя. Во время работы станка щуп 5 с силой 1,5…2 Н прижимается к копиру. При изменении силы в следящем устройстве 4 возникают электрические сигналы, которые управляют движением фрезерной головки и обеспечивают движение поперечной (следящей) подачи фрезы в соответствии с профилем копира. Движение вертикальной подачи фрезерной головки остается постоянным по величине и направлению в пределах заданного контура.
Обработку пространственно-сложных поверхностей (объемное фрезерование) производят параллельными рабочими ходами – строчками, каждая из которых представляет собой контурное фрезерование. Объемное фрезерование наиболее успешно осуществляется на фрезерных станках с ЧПУ, на которых информация требуемой траектории инструмента записана на программоносителе, а не считывается каждый раз с устанавливаемого на полуавтомат копира.
На базе фрезерных станков с ЧПУ выпускают многоцелевые станки, предназначенные для комплексной обработки корпусных деталей с четырех сторон без переустановки. На рис. 7.9, ж представлен многоцелевой фрезерно- сверлильно-расточной станок. По горизонтальным направляющим станины 1 перемещается поворотный стол 6, осуществляющий продольное и поперечное перемещения по координатам x′ и y′. По вертикальным направляющим стой-
ки 2 перемещается шпиндельная бабка 5 (движение подачи по координате z′). В инструментальном магазине 4 находятся разнотипные инструменты, необходимые для обработки данной заготовки, которые по программе подаются автоматической рукой 3 в шпиндель и в нем закрепляются.

157
Типы фрез и технологическая оснастка фрезерных станков. В зави-
симости от назначения и вида обрабатываемых поверхностей различают цилиндрические (рис. 7.10, а), торцовые (рис. 7.10, б, з), дисковые (рис. 7.10, в), концевые (рис. 7.10, г), угловые (рис. 7.10, д), шпоночные (рис. 7.10, е) и фасонные (рис. 7.10, ж) фрезы. У цилиндрических и дисковых односторонних фрез режущие зубья расположены на наружной поверхности цилиндра; у дисковых двусторонних, торцовых насадных, концевых и шпоночных фрез – на наружной цилиндрической поверхности и на одном из торцов; у дисковых трехсторонних фрез – на двух торцах и на наружной цилиндрической поверхности.
Рис. 7.10. Типы фрез
Фрезы бывают цельные (рис. 7.10, б–ж) или сборные (рис. 7.10, а, з), а их режущие кромки могут быть прямые (рис. 7.10, д) или винтовые ( рис. 7.10, а). Форма зуба фрез может быть остроконечной (рис. 7.10, и) или затылованной (рис. 7.10, к). У остроконечных зубьев передняя и задняя поверхность лезвия плоские, а у затылованных – передняя поверхность плоская, задняя выполнена по спирали Архимеда.
158
Цельные фрезы изготавливают из инструментальных сталей. У сборных фрез зубья (ножи) выполняют из быстрорежущих сталей или оснащают пластинами из твердых сплавов и закрепляют в корпусе фрезы пайкой или механически. Торцевые фрезы изготовляют с механическим креплением ножей из композитов.
Для закрепления заготовок на фрезерных станках применяют универсальные приспособления, к которым относят прихваты, угольники, призмы, машинные тиски и т.п. При обработке большого числа одинаковых заготовок изготовляют специальные приспособления, пригодные только для установки и закрепления этих заготовок на данном станке. Важным приспособлением фрезерных станков является делительная головка, которая служит для периодического поворота заготовок на требуемый угол (изготовление многогранников, зубчатых колес и т.п.) или для непрерывного их вращения при фрезеровании винтовых канавок.
Делительная головка (рис. 7.11) состоит из корпуса 1, делительного лимба 5, поворотного барабана 2 и шпинделя 4 с центром. В корпусе на шпинделе жестко закреплено червячное колесо, находящееся в зацеплении с червяком (обычно передаточное число червячной передачи 1/40). Вращение шпинделя на требуемый угол осуществляют рукояткой 6 с помощью лимба 5. Для удобства отсчета используют раздвижной сектор 7. На шпинделе 4 закреплен лимб 3 для непосредственного деления заготовки на части.
Универсальные делительные головки позволяют осуществлять деление непосредственным, простым и дифференциальным способами.
При непосредственном способе деления червяк выводят из зацепления с червячным колесом и поворачивают заготовку на требуемый угол вращением лимба 3.
При простом способе деление производят при закрепленном лимбе 5. Шпиндель с заготовкой поворачивают вращением рукоятки через включенную
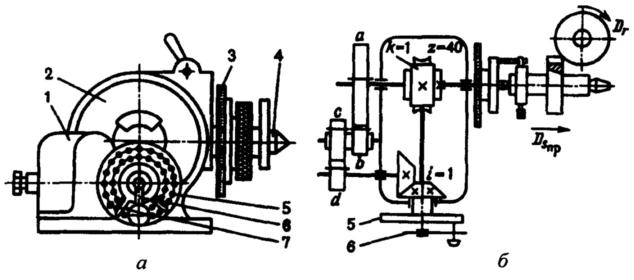
159
червячную передачу. Число оборотов рукоятки n , необходимое для поворота заготовки на 1z часть оборота,
n = |
N |
= |
40 |
, |
(7.9) |
|
z |
|
z |
|
|
где N – характеристика делительной головки – число оборотов рукоятки, необходимое для поворота заготовки на 3600; z – число частей, на которое необходимо разделить заготовку.
Если z < 40, то |
40 |
>1, тогда |
|
|
|
|
|
z |
|
|
|
|
|
|
|
40 |
= A + a |
= A + ma |
, |
(7.10) |
|
|
z |
b |
mb |
|
|
где A – число целых оборотов рукоятки; a и b – числитель и знаменатель правильной простой дроби; m – общий множитель дроби, который выбирают так,
чтобы произведение mb представляло собой число отверстий, имеющихся на одной из окружностей лимба 5. Следовательно, для поворота заготовки на 1z
часть необходимо рукоятку 6 повернуть на A полных оборотов и на ma деле-
ний по окружности лимба 5 с mb делениями.
Рис. 7.11. Универсальная делительная головка, настроенная на дифференциальное деление