
Аксенов А. А. Технология конструкционных материалов
.pdf20
Процесс выплавки стали осуществляют в несколько этапов:
а) расплавление шихты и нагрев ванны жидкого металла. На этом этапе происходит окисление железа и окисление примесей по реакциям
Fe + ½O2 = FeO + Q; 2FeO + Si = SiO2 +2Fe + Q1; 5FeO + 2P = P2O5 + 5Fe + Q2; FeO + Mn = MnO + Fe + Q3;
б) «кипение» металлической ванны. Этот процесс происходит при более высоких температурах, чем на первом этапе, по реакции
FeO + C = CO + Fe – Q4.
Образующаяся окись углерода выделяется из жидкого расплава, вызывая «кипение» ванны, при котором уменьшается содержание углерода до требуемого. Здесь же происходит удаление серы из металла и перевод ее в шлак. Этот этап является основным в процессе выплавки стали;
в) раскисление стали – заключается в восстановлении оксида железа, растворенного в расплаве. Сталь раскисляют двумя способами: осаждающим и диффузионным. Осаждающее раскисление осуществляется введением в жидкую сталь растворимых раскислителей (ферромарганца, ферросилиция, алюминия). В результате восстанавливается железо и образуются оксиды MnO, SiO2, Al2O3, которые удаляются в шлак. Диффузионное раскисление осуществляется раскислением шлака, т.е. раскислители в размельченном виде загружают на поверхность шлака, и они раскисляют железо и уменьшают его содержание в шлаке. Второй способ раскисления повышает качество стали.
В зависимости от степени раскисленности выплавляют спокойные (при полном раскислении), кипящие (в печи раскислена не полностью, и процесс продолжается при затвердевании слитка) и полуспокойные (промежуточная раскисленность) стали.
Легирование стали осуществляют введением ферросплавов или чистых металлов в необходимом количестве в расплав.
21
Основными способами выплавки стали в настоящее время являются: конвертерный (55 %), мартеновский (20 %) и в электропечах (25 %).
Конвертерный способ получения стали. Сущность конвертерного про-
изводства стали заключается в том, что жидкий чугун продувают кислородом. Выделяющееся тепло при окислении обеспечивает нагрев до 1600 0С.
Начало конвертерного производства было положено в 1856 г. Г. Бессемером (конвертор с кислой футеровкой динасовым кирпичом), а в 1878 г. С. Томас предложил конвертер с основной футеровкой (обожженный доломит). В настоящее время бессемеровский и томасовский процессы с подачей воздуха заменены кислородно-конвертерным процессом с подачей сжатого кислорода. Впервые продувка расплавленного чугуна кислородом сверху в конвертере с основной футеровкой была осуществлена в СССР в 1933 г. инженером Н.И. Мозговым, а в промышленных масштабах этот процесс впервые был осуществлен в 1952 г. в Австрии.
Кислородный конвертер (рис. 1.5) – это сосуд грушевидной формы 2, корпус которого сварен из листовой стали толщиной от 50 до 100 мм. Внутренняя футеровка корпуса, как правило, двухслойная толщиной 700…1000 мм, изготовленная из основных огнеупорных материалов (магнезита и доломита). Стойкость рабочего слоя составляет 400…600 плавок. Конвертер имеет опорный пояс 3 с цапфами, расположенными в подшипниках опор. Для поворота конвертера предусмотрен механизм привода 4, при помощи которого конвертер может поворачиваться в обе стороны на любой угол. Сверху через горловину в рабочее пространство конвертера входит водоохлаждаемая кислородная фурма 1. Вместимость конвертера от 70 до 350 т расплавленного чугуна.
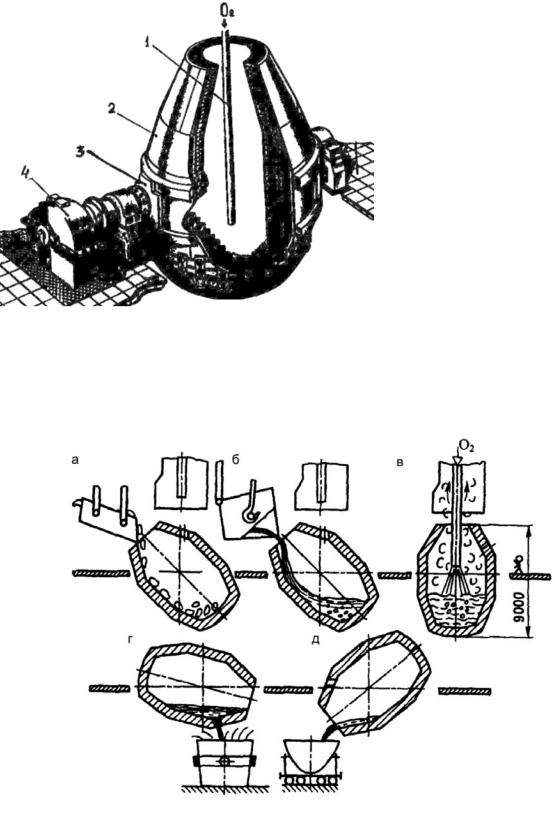
22
Шихтовыми материалами кислородноконвертерного процесса являются жидкий передельный чугун, стальной лом (не более 30 %), известь для наведения шлака и железная руда.
Основные периоды процесса плавки: загрузка
Рис. 1.5. Устройство кислородного конвертера скрапа (рис. 1.6, а); заливка чугуна при температуре
1250…1400 0С (рис. 1.6, б); кипение ванны расплава (рис. 1.6, в); выпуск стали в ковш, где она раскисляется (рис. 1.6, г); слив шлака (рис. 1.6, д).
Рис. 1.6. Последовательность технологических операций при выплавке стали в кислородных конвертерах
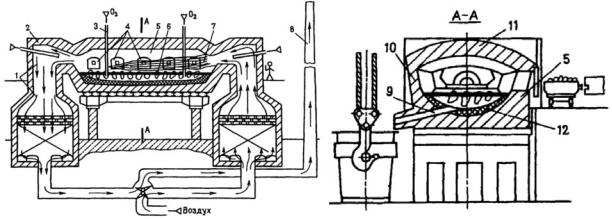
23
При выпуске стали из конвертера ее раскисляют в ковше осаждающим методом, затем из конвертера сливают шлак. В кислородных конвертерах выплавляют конструкционные и низколегированные стали с различным содержанием углерода, кипящие и спокойные. Легирующие элементы вводят в ковш, расплавив их в электропечи, или твердые ферросплавы вводят в ковш перед выпуском в него стали. Плавка в конвертерах вместимостью 130…300 т заканчивается через 25…30 мин.
Мартеновское производство стали. Мартеновская печь – это пламенная отражательная регенеративная печь, которая имеет рабочее плавильное пространство (рис. 1.7), ограниченное снизу подом 12, сверху сводом 11, а с боков передней 5 и задней 10 стенками. Под имеет форму ванны с откосами по направлению к стенкам печи. Футеровка печи может быть основной (магнезитовый кирпич) или кислой (динасовый кирпич). В передней стенке печи имеются загрузочные окна 4 для подачи шихты и флюса, а в задней – отверстие 9 для выпуска готовой стали. Головки 2 служат для смешивания топлива (мазута или газа) с воздухом и подачи этой смеси в плавильное пространство.
В нашей стране работают мартеновские печи вместимостью от 200 до 900 т жидкой стали.
Рис. 1.7. Схема мартеновской печи
Для подогрева воздуха и газа при работе на низкокалорийном газе печь имеет два регенератора 1. Регенератор – это камера, в которой размещена на-
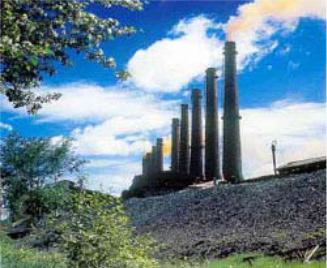
24
садка (огнеупорный кирпич, выложенный в клетку), где газы ее нагревают до температуры 1250…1280 0С.
|
Через один из регенераторов, |
|||
|
например правый, подают воздух, |
|||
|
который, проходя через насадку, |
|||
|
нагревается |
до |
температуры |
|
|
1100…1200 0С и поступает в го- |
|||
|
ловку печи, где смешивается с то- |
|||
|
пливом. В результате на выходе из |
|||
|
головки 2 образуется факел 7, на- |
|||
|
правленный |
на металлошихту 6. |
||
Рис. 1.8. Мартеновский цех |
Отходящие |
газы |
проходят |
через |
Нижнетагильского металлургического |
противоположную |
головку |
(ле- |
|
комбината |
вую), очистительные устройства (шлаковики) и направляются во второй (левый) регенератор, нагревая его насадку. Охлажденные газы покидают печь через дымовую трубу 8. После охлаждения правого регенератора включают клапаны, и поток газов в печи изменяет направление.
Факел имеет температуру 1750…1800 0С и нагревает рабочее пространство печи и шихту. Он способствует окислению примесей шихты при плавке.
В зависимости от состава шихты различают:
–скрап-процесс, при котором шихта состоит из стального лома (скрапа) и 25…45 % чушкового передельного чугуна;
–скрап-рудный процесс, при котором шихта состоит из жидкого чугуна (55…75 %), скрапа и железной руды.
Наибольшее количество стали производят скрап-рудным процессом в мартеновских печах с основной футеровкой, что позволяет переделывать в сталь различные шихтовые материалы.
25
Получение стали в электропечах. Электропечи используют для выплавки конструкционных, высоколегированных, инструментальных, специальных сплавов и сталей. Используют дуговые и индукционные электропечи.
К основным достоинствам электропечей относятся: быстрый нагрев металла; малый угар легирующих элементов; точная регулировка температуры; более полное раскисление расплава.
Дуговая плавильная печь (рис. 1.9) работает на трехфазном переменном токе и имеет три цилиндрических электрода 9 из графитизированной массы.
Электрический ток от трансформатора мощностью от 25 до 45 кВт А через кабель 7 подводится к электродержателям 8, а через них – к электродам 9 и ванне расплава. Между электродом и металлической шихтой 3 возникает электрическая дуга. Рабочее напряжение 160…600 В, сила тока 1…10 кА. Во время работы печи длина дуги регулируется автоматически, путем перемещения электродов. Стальной кожух 4 печи футерован огнеупорным кирпичом 1 – основным или кислым. Под 12 печи выкладывают огнеупорной массой. Плавильное пространство ограничено стенками 5, подом 12 и сводом 6 из огнеупорного кирпича. Свод печи выполняется съемным. Ход плавки контролируется через рабочее окно 10. Выпуск готовой стали осуществляется через выпускное отверстие по желобу 2 в ковш. Печь имеет привод 11 для наклона в сторону рабочего окна или желоба.
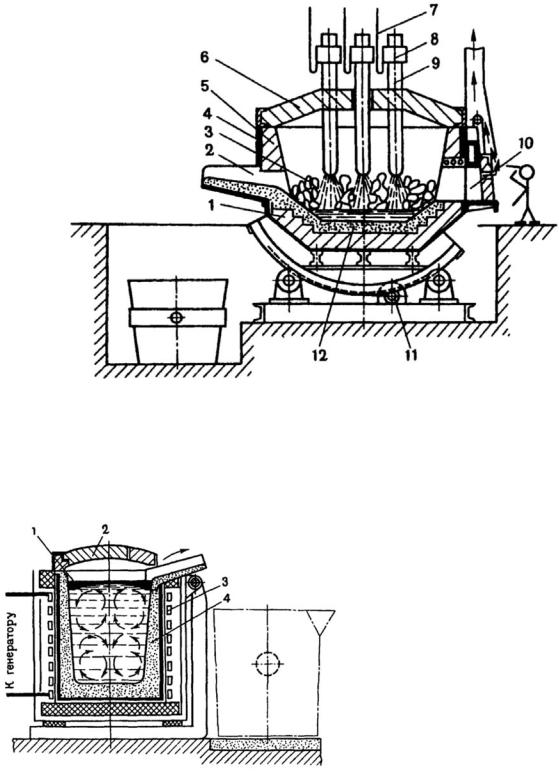
26
Рис. 1.9. Схема дуговой плавильной печи
Индукционная тигельная плавильная печь (рис. 1.10) состоит из водоох-
лаждаемого индуктора 3, внутри которого находится тигель 4 с металлической
|
шихтой. Через индуктор от |
|||
|
генератора |
промышленной |
||
|
частоты (50 Гц) или от генера- |
|||
|
тора |
высокой |
частоты |
|
|
(500…2500 Гц) проходит од- |
|||
|
нофазный |
переменный ток, |
||
|
который |
создает |
переменный |
|
|
магнитный поток в кусках ме- |
|||
Рис. 1.10. Схема индукционной тигельной |
талла. Переменный магнит- |
|||
|
|
|
|
|
плавильной печи |
ный поток наводит в металле |
вихревые токи, нагревающие металл 1 до расплавления и необходимых температур перегрева. Тигель изготовляют из кислых (кварцит) или основных (магнезитовый порошок) огнеупо-
27
ров, вместимость которого 0,06…25 т. Для уменьшения потерь теплоты печь имеет съемный свод 2.
Индукционные печи имеют преимущества перед дуговыми: в них отсутствует электрическая дуга, что позволяет выплавлять сталь с низким содержанием углерода, газов и малым угаром элементов.
28
2. ЛИТЕЙНОЕ ПРОИЗВОДСТВО
Литейное производство – отрасль машиностроения, технологическими процессами которой получают литые заготовки (отливки) и детали машин лесного комплекса и других отраслей промышленности. Литейное производство – один из наиболее распространенных методов формообразования заготовок. Оно позволяет получать отливки практически не ограниченных габаритных размеров и массы из всех сплавов.
Исторические данные. Литейное производство является одним из старейших методов. До 14 века литьем производили медные и бронзовые изделия, предметы домашнего обихода, украшения, стрелы. В 15 веке появился чугун, из которого с 1445 г. начали отливать трубы, с 1469 – гири для весов. Первый литейный завод в России был построен в 1479 г. и назывался «Пушечная изба».
В 1585 г. пушечный мастер Андрей Чохов отлил из бронзы «Царь пушку» массой 39 т. В 1735 г. московский литейщик Иван Моторин отлил из бронзы величайший в мире «Царь колокол» массой 196 т. В 1777 г. отлили «Медный всадник», имеющий толщину стенок отливки 7,5 мм и стоящий на двух опорах. В 1873 г. в Перми была получена отливка массой 620 т (шабот молота).
Сущность современного литейного производства заключается в приго-
товлении расплавленного металла необходимого качества и заливке его в специальную литейную форму. При охлаждении жидкий металл затвердевает и в твердом состоянии сохраняет конфигурацию той полости, в которую он был залит. Для изготовления отливок применяют множество способов литья: в песчаные формы, в оболочковые формы, по выплавляемым моделям, в кокиль, под давлением, центробежное литье и пр.
Классификация отливок. По условиям эксплуатации независимо от способа изготовления различают отливки общего (не рассчитываемые на прочность), ответственного (рассчитываемые на прочность и работающие при статических нагрузках) и особо ответственного (рассчитываемые на прочность и
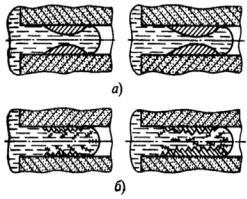
29
работающие при циклических и динамических нагрузках) назначения.
В зависимости от способа изготовления, массы, конфигурации поверхностей, максимальных габаритных размеров, толщины стенок, количества стержней, назначения и особых технических требований отливки делят на шесть групп сложности и 22 класса точности.
2.1ЛИТЕЙНЫЕ СВОЙСТВА МЕТАЛЛОВ И СПЛАВОВ
Клитейным свойствам относят технологические свойства металлов и сплавов, которые проявляются при заполнении формы, кристаллизации и охлаждении отливок в форме. Наиболее важные: жидкотекучесть, усадка, склонность сплавов к ликвации, образованию трещин, поглощению газов, пористости.
Жидкотекучесть – способность металлов и сплавов течь в расплавленном состоянии по каналам литейной формы, заполнять ее полости и четко воспроизводить контуры отливки. Зависит от температурного интервала кристаллизации,
свойств формы, вязкости и поверхностного натяжения расплава. Чистые металлы и эвтектические сплавы (рис. 2.1) обладают лучшей жидкотекучестью
(до 60…80 % твердой фазы), чем сплавы, образующие твердые растворы и затвердевающие в интервале температур (до 20…30 % твердой фазы). Повышение температуры заливки и температуры литейной формы увеличивает жидкотекучесть. Сплавы, склонные к повышенному окислению с образованием сплошной и прочной оксидной пленки, обладают пониженной жидкотекуче-