
Монография MMK Metalurji
.pdf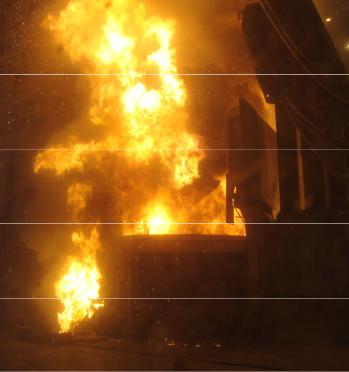
профиль работы печи. Профили работы «холодная» печь используются при вводе печи в работу после холодного ремонта или ее простоя продолжительностью более трех часов. Профили работы «горячая» печь применяются при бесперебойной работе агрегата.
В период плавления шихты все инжекционные устройства работают в режиме «горелка».
По мере расплавления шихты первой корзины в печь по тракту подачи сыпучих материалов подается 2...3 т извести. После расплавления шихты из первой корзины производится подвалка шихты второй корзиной (рисунок 2.3).
Рисунок 2.3 – Подвалка шихты в печь второй корзиной
Во второй корзине вместе с ломом находится еще 2…3 т извести. Кроме извести для увеличения стойкости футеровки
71
печи может осуществляться добавка материалов, содержащих оксид магния, из расчета получения содержания MgO в шлаке не менее 6 %.
Период заканчивается после полного расплавления шихтовых материалов и получения в печи жидкого металла, находящегося под слоем шлака.
2.1.4 Окислительный период
Главной задачей окислительного периода плавки является снижение содержания углерода и фосфора в металле с синхронным нагревом металла до требуемой температуры.
Окисление примесей расплава осуществляется путем продувки ванны газообразным кислородом через инжекционные устройства, работающие в режиме «фурма». Расход кислорода и продолжительность продувки устанавливаются в автоматическом режиме согласно выбранному профилю ведения плавки.
Для экранирования электрических дуг производится вспенивание шлака путем вдувания в печь через инжекторы углеродсодержащего материала и кислорода. В случае неисправности угольного инжектора или невозможности обеспечения требуемого уровня вспенивания шлака введение углеродсодержащих материалов осуществляется по тракту сыпучих материалов. Для этого углеродсодержащий материал вводится порциями по 100 кг вместе со свежеобожженной известью порциями по
500кг.
Впроцессе окислительного периода скачивается часть шлака через порог рабочего окна при наклоне печи на угол, равный 4 ° (рисунки 2.3 и 2.4). Это необходимо для удаления продуктов окисления фосфора.
Новый шлак наводится путем присадки извести в печь по тракту. Суммарный расход извести на плавку составляет не менее 9 т из расчета получения основности шлака – величины отношения содержания оксида кальция к содержанию оксида кремния в шлаке, не менее 1,9.
Для осуществления эффективной дефосфорации металла его температура не должна превышать 1580 °С.
Продувка металла кислородом обычно ведется до получения содержания углерода 0,03…0,07 %. Определение содержания углерода в металле проводится при помощи комбинированной системы измерения температуры и окисленности жидко-
72
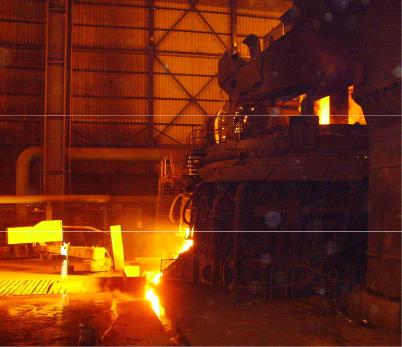
Рисунок 2.3 – Скачивание шлака из печи
го металла «Celox Multi-Lab». При получении окисленности металла 1000 ppm и более, продувка ванны кислородом прекращается. Для подогрева металла включается ток и подача кислорода с одновременным включением угольных инжекторов до достижения заданной температуры металла.
Температура металла, выпускаемого из ДСП для ковшевой обработки на установке «печь-ковш» равняется 1600… 1630 °С ина вакууматоре– 1660…1680°С.
Втечение всего периода расплав продувается аргоном через донные блоки печи.
Вконце окислительного периода отключаются электронагрев и инжекционные устройства, отбираются пробы металла и шлака на полный химический анализ, измеряется температура металла (рисунок 2.5).
73
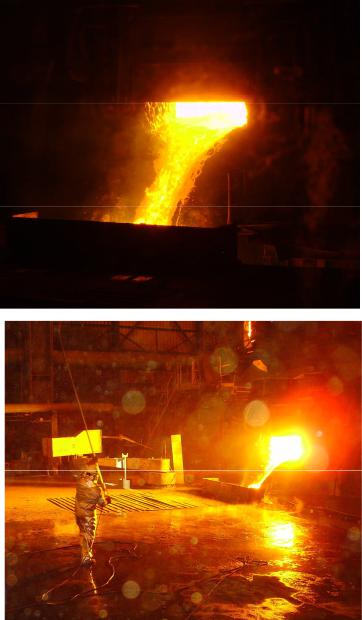
Рисунок 2.4 – Вид скачиваемого из печи шлака
Рисунок 2.5 – Подготовка к измерению температуры металла
74
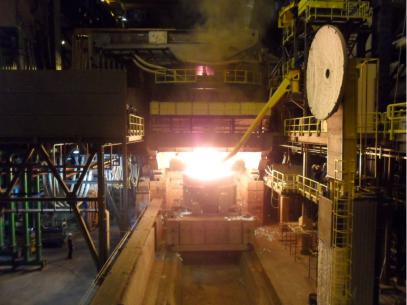
2.1.5 Выпуск металла, раскисление, легирование, обработка шлакообразующими материалами
Выпуск металла из печи производится после получения результатов анализа проб металла и измерения температуры, соответствующих выплавляемой марке стали.
Для осуществления выпуска металла печь наклоняют в сторону эркерного устройства и производится открытие сталевыпускного отверстия эркера.
Выпуск металла осуществляется в сталеразливочный ковш, разогретый на установке высокотемпературного нагрева или в «горячий» оборотный ковш (рисунок 2.6).
Рисунок 2.6 – Выпуск металла из печи в сталеразливочный ковш
Сталеразливочный ковш оборудован системой для донной продувки с быстроразъемными соединениями, которые должны быть исправными и иметь обратные клапана. Футеровка ковша предварительно прогревается до красного каления. Верхний
75
край ковша должен быть чистым. Сталеразливочный ковш заранее устанавливается под печь к моменту расплавления шихты, аргонопроводы подключаются к быстроразъемным соединениям.
Выпуск металла проводится с полной отсечкой печного шлака. При ведении процесса с «болотом» в печи оставляется до 50 т металла со шлаком. Количество металла и шлака, остающегося в печи, определяется по разности между массой шихты и массой металла в сталеразливочном ковше, а также визуально.
Попадание печного шлака в стальковш не допускается. Наполнение ковша металлом производится до уровня, находящегося на 400 мм ниже верхнего его края, для предотвращения выплесков металла и шлака при транспортировке.
Длительность выпуска металла из ДСП составляет 2… 6 мин. После более продолжительного выпуска производится осмотр сталевыпускного отверстия и, при необходимости, его чистка.
Раскисление и легирование металла в сталеразливочном ковше осуществляется в процессе выпуска металла из печи с использованием как кусковых материалов, подаваемых из бункеров по тракту, так и чушкового или кускового алюминия, вводимых в ковш вручную.
При наполнении ковша металлом в количестве 25…30 т в ковш вводится 150…200кг алюминия. После наполнения сталеразливочного ковша на третью часть присаживаются ферромарганец, силикомарганец, ферросилиций, затем – шлакообразующие материалы: известь и плавиковый шпат в количестве 1500 и 250 кг соответственно, углеродсодержащий материал и алюминий. Расход раскислителей и легирующих добавок определяется из расчета получения среднего содержания элементов в стали заданной марки.
2.1.6 Слив и уборка шлака
После окончания выпуска металла в печи оставляется до 50 т металла с небольшим количеством шлака. Лишний шлак удаляется из печи после закрытия эркера путем наклона агрегата в сторону рабочего окна. Шлак через порог открытого окна сливается под печь. Под печкой на нулевой отметке шлак оса-
76
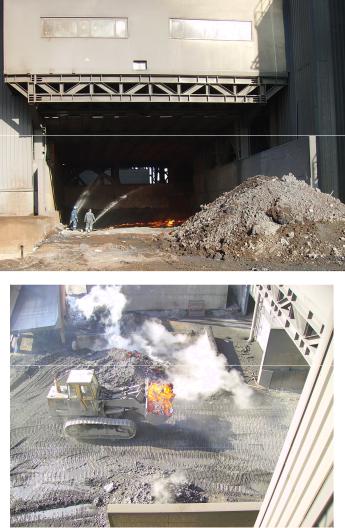
живается водой и собирается бульдозерами с погрузкой в специальный короб (рисунки 2.7 и 2.8).
Рисунок 2.7 – Охлаждение слитого под печь шлака
Рисунок 2.8 – Уборка шлака
77
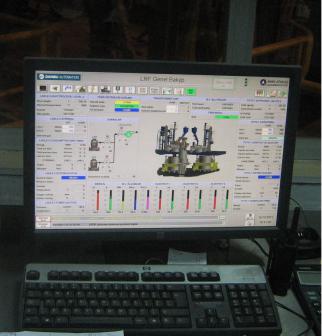
2.2Технология ковшевой обработки стали
2.2.1Технология обработки стали на установке «печь-ковш»
Вслучае поступления на участок ковшевой обработки стали ковша с металлом, находящимся под слоем шлака толщиной более 200 мм, производится удаление его избыточного количества. Для этого сталеразливочный ковш краном помещается в наклоняющийся стенд установки скачивания шлака. После наклона ковша шлак снимается с поверхности расплава машиной скребкового типа.
После скачивания шлака сталеразливочный ковш краном перемещается на один из сталевозов участка ковшевой обработки стали. Поступивший сталеразливочный ковш устанавливается на сталевоз установки «печь-ковш» (рисунок 2.9).
Рисунок 2.9 – Управление и контроль за процессом ковшевой обработки на установке «печь-ковш»
78
К продувочным устройствам ковша присоединяются шланги для подачи аргона. Подсоединение пробок стальковша к за- порно-регулирующей арматуре производится с помощью специальных быстроразъемных соединений с обратными клапанами. Продувка металла в ковше аргоном начинается с расходом до 1200 л/мин на пробку. Сталевоз передвигается под крышку установки, после чего крышка опускается на ковш.
Визуально через рабочее окно оценивается интенсивность перемешивания металла по величине буруна, после чего проводится корректировка расхода газа. Расход газа должен обеспечивать интенсивное перемешивание металла, но без оголения зеркала металла и выплесков из ковша. При слабом перемешивании металла на максимально установленном расходе аргона продувка осуществляется через байпас.
С целью снижения насыщения металла азотом во время обработки под крышкой создается избыточное давление путем регулирования клапана газохода, что визуально определяется выделением пыли и газа из-под крышки и в отверстия для электродов. Рабочее окно в процессе обработки металла должно быть закрыто.
Продолжительность открывания рабочего окна (рисунок 2.10) для корректировки интенсивности продувки металла, измерения температуры и отбора проб должна быть минимальной. Производится измерение температуры и окисленности металла, а также определяется толщина слоя шлака при помощи металлической трубки, погружаемой в расплав и выдерживаемой короткое время. На трубке измеряется расстояние от отгоревшего конца до границы налипшего на нее шлака.
Дальнейшая корректировка металла по температуре производится из расчета получения в конце обработки температуры, заказанной мастером МНЛЗ.
После усреднительной продувки аргоном в металл при помощи трайб-аппарата вводится алюминиевая катанка и отбирается проба металла. Расход алюминиевой катанки определяется в зависимости от значения измеренной окисленности металла. При невозможности введения алюминиевой катанки используется чушковый алюминий.
Для нагрева металла и (или) разжижения шлака электродный портал опускается в рабочую позицию и производится вклю-
79
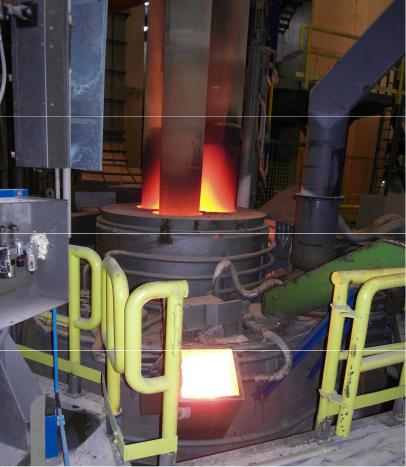
Рисунок 2.10 – Вид крышки установки «печь-ковш» с открытым рабочим окном
чение установки на расчетное время. Максимальная скорость нагрева металла равняется 4,5° С/мин. Если в процессе нагрева отмечается повышенный шум, то снижается расход продувочного газа или уменьшается рабочая ступень трансформатора, или в ковше дополнительно наводится шлак. Для наведения шлака в
80