
Монография MMK Metalurji
.pdf1.5.3 Стан горячей прокатки
Листовой широкополосный стан горячей прокатки «1750» предназначен для производства полос из низкоуглеродистого и низколегированного металла, смотанных в рулоны.
Горячекатаная полоса может иметь следующие размеры: толщина 1,0…20,0 мм – из низкоуглеродистого металла; толщина 1,2…12,7 мм – из низколегированного металла; ширина – 800…1570 мм.
Рулоны из горячекатаной полосы имеют: наружный диаметр – 1200…2000 мм; внутренний диаметр – 762 мм; вес рулона – до 30 т.
В состав стана горячей прокатки (рисунки 1.46 и 1.47) входит следующее оборудование:
Черновая группа клетей:
–вертикальная клеть с валками диаметром 580…640 мм
иприводом от двух электродвигателей мощностью 120 кВт каждый;
–устройство для гидросбива окалины №1, обеспечивающее давление воды до 380 бар;
–две клети кварто:
первая клеть с рабочими валками диаметром 980…
1050 мм и приводом мощностью 6600 кВт;
вторая клеть R2 с рабочими валками диаметром 730… 810 мм и приводом мощностью 7800 кВт; диаметр опорных валков составляет 1320…1450 мм; клеть оснащена системами положительного и отрицательного изгиба, сдвижки рабочих валков.
Чистовая группа клетей:
–барабанные ножницы;
–устройство для гидросбива окалины №2, обеспечивающее давление воды до 380 бар;
–две клети кварто с рабочими валками диаметром 730… 810 мм, диаметр опорных валков 1320…1450 мм и привод мощностью 9500 кВт для каждой клети;
–две клети кварто с рабочими валками диаметром 560… 630 мм, диаметр опорных валков 1320…1450 мм и привод мощностью 8500 кВт для каждой клети;
–система ламинарного охлаждения полосы с 21 коллектором типа «водяная стена»;
61
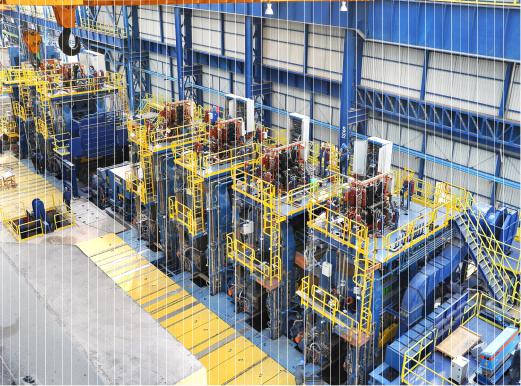
62
Рисунок 1.46 – Черновая и чистовая группы клетей стана горячей прокатки
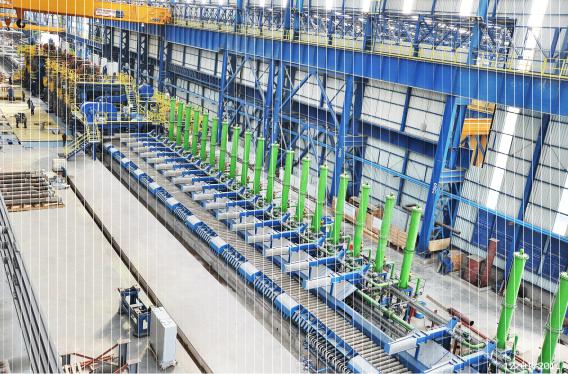
63
Рисунок 1.47 – Общий вид стана горячей прокатки
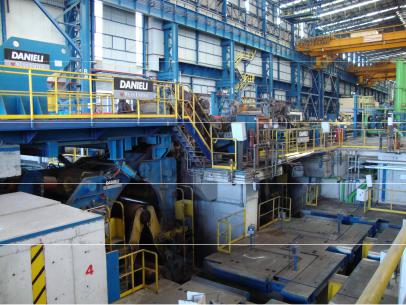
– гидронажимные устройства на всех четырех клетях, системы технологической смазки, положительного и отрицательного изгиба, сдвижки рабочих валков.
Группа моталок, состоящая из двух подпольных моталок, обеспечивающих смотку рулонов с наружным диаметром до
2000 мм (рисунок 1.48).
Рисунок 1.48 – Участок смотки полосы прокатного стана
Уборочная группа для осмотра, взвешивания, маркировки и обвязки рулонов, оборудованная конвейерами с шагающими балками, линией инспекции полосы и отбора проб, машинами для радиальной обвязки рулонов и обвязки по образующей, станции взвешивания рулонов, маркировщиков по образующей и торцевой поверхности рулонов.
Вальцешлифовальная мастерская, электромастерская.
64
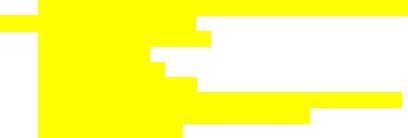
ГЛАВА 2 ТЕХНОЛОГИЧЕСКИЙ ПРОЦЕСС ПРОИЗВОДСТВА
2.1Технология выплавки стали
Вдуговой сталеплавильной печи выплавка стали возможна по двум вариантам:
Первый вариант – с загрузкой металлической шихты на «сухую» подину, очищенную от остатков шлака и металла предыдущей плавки. Данный вариант используется после замены подины, эркерного устройства и в случае необходимости осмотра состояния подины и пористых пробок для продувки металла инертными газами.
Второй вариант – с загрузкой металлической шихты на жидкий металл предыдущей плавки («болото») в количестве около 50 т.
Весь процесс выплавки стали в печи условно можно разделить на несколько периодов:
– подготовка печи к плавке;
– загрузка шихты;
– плавление шихты;
– окислительный период;
– выпуск металла из печи, обработка шлакообразующими материалами, раскисление, легирование;
– слив и уборка шлака.
2.1.1Подготовка печи к плавке
После окончания каждой плавки производится осмотр состояния футеровки стен, шлакового пояса, центральной части свода, подины, сталевыпускного отверстия печи. В процессе эксплуатации печи контролируется состояние водоохлаждаемых элементов печи, электрододержателей, шлангов подачи воды на охлаждение, короткой сети, гидрошлангов, шлангов подвода энергоносителей к газокислородным горелкам.
Сразу после окончания выпуска металла и закрытия эркера на горячую футеровку стен и откосов печи при помощи специальной машины подаются огнеупорные материалы – производится заправка печи. Порог рабочего окна очищается от остатков шлака и заправляется.
65
Проверяется отсутствие течи воды из водоохлаждаемых элементов (свода, водоохлаждаемых панелей и др.).
Включение печи производится только при исправных футеровке, системе охлаждения печи, гидравлике, газоочистке, механическом и электрическом оборудовании. В процессе выплавки запрещается отключать блокировки основного и вспомогательного оборудования, узлов и механизмов ДСП.
Проверяется состояние эркерного узла для выпуска металла из печи и в случае необходимости производится его замена. Перед заменой эркерного узла для обеспечения полного слива металла и шлака из печи обеспечивается общая масса плавки (с учетом оставшегося «болота») не более 225 т. На последних двух-трех плавках перед заменой производится максимально возможный слив печного шлака.
При необходимости перепускаются или заменяются электроды. После замены электродов перед включением тока производится выравнивание всех электродов для того, чтобы зажигание электрических дуг произошло практически одновременно.
Перед началом плавки проверяется наличие материалов в бункерах и углеродсодержащих материалов в угольных диспенсерах.
2.1.2 Загрузка шихты
Шихтовые и вспомогательные материалы, используемые в процессе выплавки стали, должны соответствовать по качеству действующим стандартам и техническим условиям.
Вметаллической шихте не допускается наличие токонепроводящих предметов (бетонных плит, шлака и т.д.), мусора, цветных металлов (меди, никеля, хрома, свинца, олова), а также взрывоопасных веществ, закрытых сосудов (баллонов и т.д.).
Вкачестве шлакообразующих материалов используется свежеобожженная или доломитизированная известь и известняк.
Рекомендуемый состав применяемой извести:
Содержание |
Известь |
|
компонента, % |
свежеобожженная |
доломитизированная |
CaO |
не менее 93 |
не менее 60,9 |
MgO |
не более 0,37 |
не более 32,2 |
Fe2O3 |
не более 1,0 |
не более 1,5 |
66
Влажность |
не более 1,0 |
не более 0,3 |
Известь должна иметь фракцию 20…50 мм.
Химический состав раскислителей и легирующих должен соответствовать требованиям действующих стандартов и технических условий. Фракция используемых ферросплавов должна составлять 20…50 мм.
Алюминий используется в виде чушек (пирамидок) массой 4…16 кг, прессованных брикетов или дроби диаметром 4…
25мм.
Вкачестве углеродсодержащих материалов используются: для науглероживания металла в ДСП – кокс фракцией 25…
50мм с содержанием углерода не менее 86%, серы, влаги, летучих – не более, соответственно, 0,75; 6,0 и 1,5 %;
для вспенивания шлака в печи – углеродсодержащий материал с содержанием углерода не менее 85 %, серы, влаги, летучих – не более 1,0; 0,7 и 2,0 %; фракцией от 0,3 до 1,0 мм (не более 30 %) и от 1 до 3мм – 70 %.
Чистота кислорода для продувки составляет не менее 99,5 %, давление кислорода в магистрали – не менее 12 bar (11,84 атм). Давление аргона и азота в магистрали не менее
12bar, а природного газа – 2,5…3 bar.
Основной вариант выплавки стали предусматривает использование в металлической шихте 80 % металлического лома и 20 % чушкового чугуна. При необходимости выплавки стали с содержанием меди не более 0,25% доля чушкового чугуна в шихте увеличивается до 30 % и более.
Первая плавка после «холодного» ремонта проводится только с использованием 100 % металлического лома. Для предотвращения повреждения неспеченной поверхности подины на начальной плавке первую корзину загружают легковесным скрапом. Крупногабаритный тяжеловесный лом не используется.
Шихта перед загрузкой в печь обязательно провешивается. Данные по составу и массе металлошихты в корзине заранее передаются диспетчером шихтового двора сталевару электропечи.
Масса металлической шихты, загружаемой в печь на плавку, составляет не более 280 т без учета «болота». После слива печи «насухо» производится увеличение массы шихты на 50 т.
Металлическая шихта из-за невысокой насыпной плотности лома, как правило, загружается в печь двумя, а иногда и тремя корзинами. Для быстрого наведения шлака в печи в со-
67
став первой корзины вводится 2…3 т извести. В случае неисправности конвейера тракта подачи сыпучих материалов количество извести в первой корзине увеличивается до 6 т.
Загрузка печи проводится следующим образом:
Свод печи приподнимается и отводится в сторону. Машинист крана располагает корзину с металлической шихтой над печью таким образом, чтобы при загрузке не повредить элементы конструкции печи и уменьшить возможные выбросы из печи металла и шлака. Во избежание разрушения огнеупоров подины на дно первой корзины укладывается легковесный лом.
На первой плавке после холодного ремонта для предотвращения повреждения неспеченной поверхности подины по всей площади набивки укладываются металлические листы толщиной 1…3 мм.
Машинистом крана производится медленное раскрытие корзины. После того, как первая порция металлошихты попадает в печь, корзина медленно поднимается вверх до полного раскрытия челюстных затворов с одновременным освобождением ее от металлолома (рисунок 2.1). Во время загрузки печи технологический персонал находится в безопасной зоне.
Для осаживания металлолома, выступающего за пределы верхнего среза кожуха печи, используется загрузочная бадья. Опускание свода на неочищенное от скрапа верхнее водоохлаждаемое кольцо кожуха печи запрещается.
При необходимости очистка верхнего края ДСП проводится вручную, при этом персонал, производящий очистку, приступает к работе только после отвода бадьи из рабочей зоны печи.
2.1.3 Плавление шихты
После окончания загрузки шихты в печь и отвода в сторону загрузочной корзины свод поворачивается в исходную позицию и опускается, через отверстия в нем в печь вводятся электроды и производится включение печи. Между электродами и металлической шихтой зажигаются электрические дуги и начинается процесс плавления шихты (рисунок 2.2).
Дуговая сталеплавильная печь может работать в ручном и автоматическом режимах. В зависимости от конкретных условий данной плавки: состояния печи, количества и состава шихты, при работе в автоматическом режиме выбирается необходимый
68
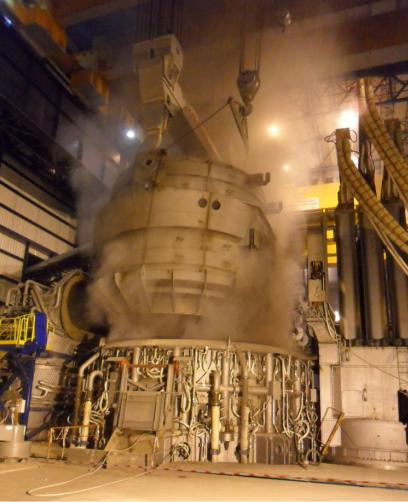
Рисунок 2.1 – Загрузка на «сухую» подину печи металлической шихты из первой корзины
69
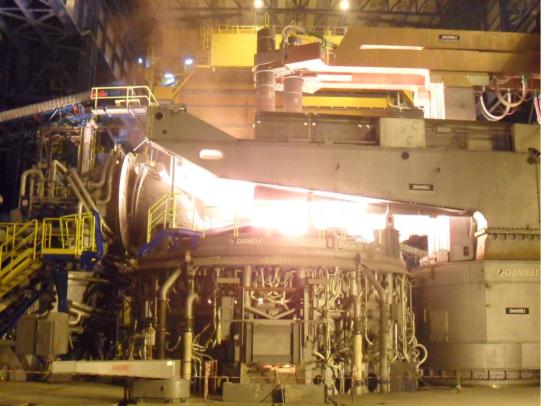
70
Рисунок 2.2 – Плавление шихты