
Монография MMK Metalurji
.pdf2.3.2 Процесс разливки стали
Разогретый промежуточный ковш на тележке перемещается из резервной позиции в рабочую. Производится центровка погружных разливочных стаканов относительно вертикальной оси кристаллизаторов, ковш опускается до достижения рабочего уровня стаканов. Расстояние от верхней части выходного отверстия стакана до верха рабочих плит кристаллизатора при отливке сляба шириной до 1350 мм должно составлять 290 +/-2мм, а для сляба большей ширины – 260+/-2мм. Положение стакана контролируется Т-образным шаблоном.
Включается подача воды на кристаллизаторы и охлаждение оборудования.
Сталеразливочный ковш с металлом краном устанавливается на поворотный стенд (рисунок 2.14). По громкоговорящей связи передается сообщение «Металл на подъемно-поворотном стенде». На ковш устанавливается гидроцилиндр шиберного затвора, магнитный детектор шлака, подсоединяются шланги подачи воздуха на коллектор охлаждения шиберного затвора и подается воздух на охлаждение гидроцилиндра. При помощи гидравлического манипулятора сталеразливочный ковш накрывается крышкой.
По команде с пульта управления стенд с ковшом поворачивается на 180 ° в положение разливки. При помощи манипулятора к стакану-коллектору шиберного затвора приставляется защитная труба и включается подача аргона в верхнюю часть полости защитной трубы. Открытие шиберного затвора производится при готовности режима «Автостарт», что свидетельствует о готовности ручья к разливке. Стартовая смесь шиберного затвора сталеразливочного ковша должна обеспечить открытие шиберного затвора с подачей жидкого металла в промежуточный ковш. В случае отсутствия металла защитная труба снимается, шиберный затвор открывается полностью и канал стакана ковша прожигается кислородом. После наполнения промежуточного ковша до рабочего уровня – не менее 45 т, шиберный затвор закрывается, устанавливается защитная труба и разливка продолжается. Нижний конец защитной трубы должен быть погружен в металл на глубину не менее 350 мм.
При поступлении металла в промежуточный ковш (рисунок 2.15) по громкоговорящей связи делается объявление: «Металл в промежуточном ковше».
91
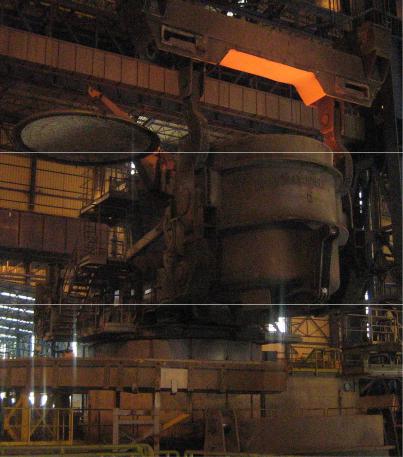
Рисунок 2.14 – Установка сталеразливочного ковша с металлом на поворотный стенд МНЛЗ
В процессе наполнения промежуточного ковша на «зеркало» металла подается шлакообразующая смесь (ШОС), выполняющая функции теплоизоляции металла, защиты его от вторичного окисления кислородом воздуха и поступления из него азота, асиммиляции всплывающих шлаковых включений. На МНЛЗ используются следующие смеси: «Repartect SPH-B 795»,
92
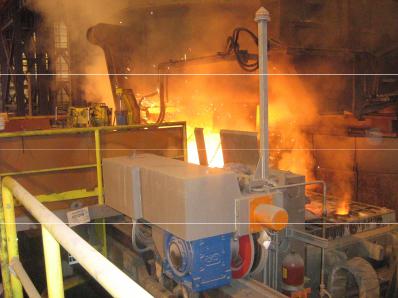
Рисунок 2.15 – Поступление жидкого металла в промежуточный ковш МНЛЗ
«GLUTIN SLAG CAM» и «GLUTIN RS-6». Расход смеси произво-
дится в соответствии с годовыми нормами расхода вспомогательных материалов для МНЛЗ.
В процессе разливки контролируется покрытие «зеркала» металла в промежуточном ковше для недопущения оголения металла.
При достижении массы металла в промежуточном ковше значения установки «Вес металла промковша при запуске», равного 20 т, автоматически приподнимаются стопорные стержни промежуточного ковша и начинается наполнение металлом кристаллизаторов в автоматическом режиме по заданному графику.
Продолжительность наполнения кристаллизатора составляет от 30 до 40 секунд в зависимости от сечения отливаемого сляба.
При подъеме металла до уровня начала разливки, находящегося на расстоянии 210 мм от верха медных плит кристал-
93
лизатора, автоматически запускается механизм качания кристаллизатора и привод вытягивания сляба с подачей воды на вторичное охлаждение. Начальная скорость вытягивания заготовки равняется 0,8 м/мин, она постепенно увеличивается до 3,0 м/мин, при которой производится отделение затравки от сляба.
После закрытия жидким металлом верхних отверстий погружного стакана в кристаллизатор подается стартовая ШОС «Start 304», а через 20…30 секунд рабочая ШОС фирм
«METALLURGICA» или «STOLLBERG» в соответствии с группой марок стали. Шлакообразующая смесь в кристаллизаторе по сравнению с ШОС в промежуточном ковше имеет очень важную дополнительную функцию – является смазкой, затекая в зазор между затвердевшей корочкой сляба и медными пластинами кристаллизатора. Расход ШОС для кристаллизатора по ходу разливки должен соответствовать годовым нормам расхода вспомогательных материалов для МНЛЗ.
После отдачи ШОС в кристаллизатор проверяется образование гарнисажа на поверхности жидкого металла. При необходимости производится разрушение или удаление гарнисажа при помощи металлического стержня. Заглубление металлического стержня в металл не допускается во избежание повреждения затвердевающей корочки сляба.
Впроцессе установившейся разливки контролируется состояние ШОС в кристаллизаторе. Поверхность слоя ШОС в кристаллизаторе должна быть темного цвета, толщина слоя - около 40 мм над поверхностью металла. Подача смеси производится мелкими порциями так, чтобы не происходило оголение металла. Грубые шлаковые корки удаляются при помощи металлического прута.
При установившемся режиме разливки рабочий уровень металла в кристаллизаторе находится на расстоянии 85 мм от его верха (рисунок 2.16).
После отделения затравки при отливке слябов шириной более 1350 мм производится опускание в ручном режиме погружного стакана до нижнего уровня – 290 мм, затем включается автоматический режим его перемещения.
Впроцессе разливки металла одного ковша три раза замеряется температура металла в промежуточном ковше. Замер осуществляется погружной термопарой через отверстие в крышке ковша. Термоблок погружается в расплав на глубину не ме-
94
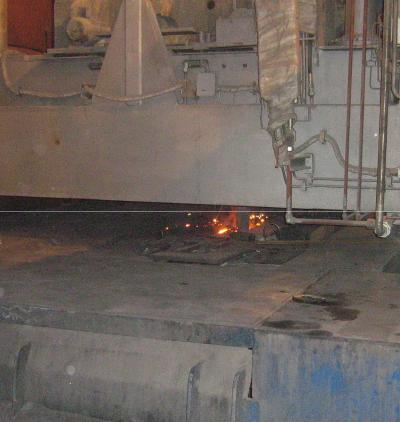
Рисунок 2.16 – Вид верхней части погружного стакана и покровного шлака на зеркале металла в кристаллизаторе
нее 400 мм с поворотом против часовой стрелки на угол примерно 20..30 °. Первый замер температуры производится после наполнения ковша до рабочего уровня при массе стали в нем не менее 36 т. Второй и третий замеры температуры осуществляются после разливки половины металла из сталеразливочного ковша и 80 % (но не менее 30 т) соответственно.
Рекомендуемая температура металла в промежуточном ковше должна превышать температуру ликвидус разливаемой стали на 20…30 °С.
95
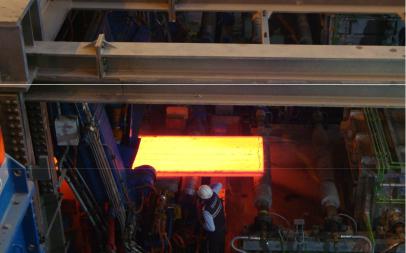
После каждого замера температуры металла в промежуточном ковше корректируется скорость вытягивания сляба из кристаллизатора, зависящая как от температуры металла, так и от группы марок стали, размеров сечения слябовой заготовки, содержания серы в металле.
Отбор двух проб металла (основной и контрольной) для определения химического анализа и назначения стали на конкретную марку производится из в промежуточного ковша после разливки примерно 50 % металла плавки пробоотборником типа ПМ.
Маятниковыми ножницами вытягиваемый из кристаллизатора непрерывнолитой сляб разделяется на мерные длины (ри-
сунок 2.17).
Рисунок 2.17 – Вид головной части сляба на выходе из маятниковых ножниц
При окончании разливки металла из сталеразливочного ковша закрытие шиберного затвора производится в автоматическом режиме при наличии 40 % количества шлака в объеме металла струи, определяемого при помощи детектора шлака. С помощью манипулятора отсоединяется защитная труба от коллектора шиберного затвора ковша. Ковш разворачивается стендом в резервную позицию.
96
В случае неработоспособности системы отсечки шлака необходимо визуально контролировать появление шлака из сталеразливочного ковша в промежуточном ковше при остаточном весе металла в сталеразливочном ковше около 15 т. Шлак из сталеразливочного ковша всплывает в районе защитной трубы и имеет более высокую температуру, чем теплоизолирующая смесь промежуточного ковша. При всплытии шлака шиберный затвор сталеразливочного ковша немедленно закрывается.
Со сталеразливочного ковша снимается крышка при помощи гидравлического привода. Закрывается подача воздуха, подаваемого на охлаждение шиберного затвора, снимается гидроцилиндр шиберного затвора и магнитный детектор шлака. Разливочным краном опорожненный сталеразливочный ковш снимается с поворотного стенда.
Для исключения попадания шлака из промежуточного ковша в кристаллизатор вследствие образования воронки разливка ведется до минимального уровня металла в промежуточном ковше, равного 200 мм. При этом масса остатка металла в ковше составляет 6 т.
Окончание разливки может осуществляться в автоматическом и ручном режимах. Скорость вытягивания сляба из кристаллизатора снижается с рабочей до величины, зависящей от толщины отливаемой заготовки.
2.3.3. Разливка стали методом «плавка на плавку»
Методом «плавка на плавку» или сериями разливается сталь либо одной марки или разных марок с небольшим отклонением по химическому составу металла. Допускаются следующие отклонения по химическому составу металла смежных в серии плавок:
по содержанию углерода – не более 0,04%; по содержанию марганца – не более 0,15%.
Очередной в серии сталеразливочный ковш с металлом устанавливается в резервную позицию на поворотный стенд не позднее, чем за 10 минут до окончания разливки металла из предыдущего сталеразливочного ковша. При развороте стенда полный ковш оказывается в рабочей позиции над промежуточным ковшом, а опорожненный ковш – в резервной позиции.
Перед сменой сталеразливочного ковша на момент закрытия его шиберного затвора масса металла в промежуточном
97
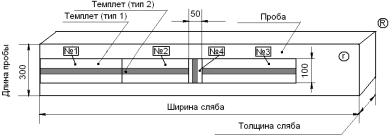
ковше должна составлять 48…52 т. Минимальная масса металла в промежуточном ковше к моменту начала поступления в него металла очередной плавки составляет 25 т. Продолжительность прекращения поступления металла в промежуточный ковш не должна превышать трех минут. В данный промежуток времени допускается кратковременное снижение скорости вытягивания сляба из кристаллизатора.
При разливке стали методом «плавка на плавку» первый замер температуры металла в промежуточном ковше производится после полного обновления металла в промежуточном ковше.
Количество плавок в серии определяется, в первую очередь, состоянием погружного разливочного стакана и стопорных стержней промежуточного ковша. При наличии износа стакана в районе шлакового пояса или его прогара, а также в случае некрытия стопора, разливка серии прерывается.
Для оценки качества макроструктуры непрерывнолитого сляба осуществляется вырезка проб металла. Маятниковыми ножницами от заготовки отрезается проба длиной 300 мм. При разливке стали методом «плавка на плавку» отбирается одна проба от сляба в середине серии.
Газовым резаком из отобранной пробы металла в соответствии со схемой, представленной на рисунке 2.18, вырезаются первичные темплеты (тип 1). В макролаборатории из них изготавливаются вторичные темплеты (тип 2), подвергаемые металлографической оценке.
Рисунок 2.18 – Схема вырезки темплетов из пробы металла для оценки качества макроструктуры сляба
98
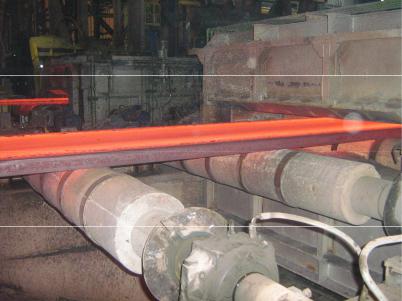
2.4 Технология нагрева слябов перед прокаткой
Технологический процесс нагрева сляба перед горячей прокаткой [14] состоит из следующих операций:
– подача сляба в туннельную печь (рисунок 2.19);
Рисунок 2.19 – Подача тонкого сляба в туннельную печь
–нагрев сляба внутри печи до требуемой температуры начала черновой прокатки;
–выдача нагретого сляба на рольганг перед черновой группой клетей прокатного стана (рисунок 2.20).
Режим нагрева обеспечивается контролем температуры по зонам и скоростью транспортировки сляба.
Контролируемым технологическим параметром качества нагрева является температура сляба на выходе из туннельной печи, измеряемая при помощи пирометра.
Температура нагрева сляба на выходе из туннельной печи изменяется в интервале 1070…1170 °С в зависимости от марки стали.
99
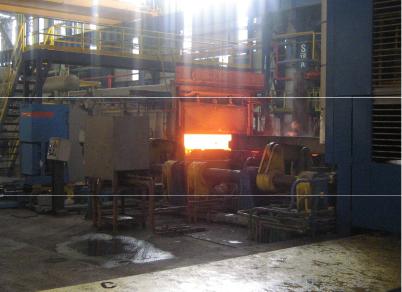
Рисунок 2.20 – Выдача нагретого сляба на рольганг перед черновой группой клетей прокатного стана
Для достижения заданной температуры нагрева сляба выполняется установка и корректировка температурного режима по зонам туннельной печи.
Основными режимами работы рольганга туннельной печи являются следующие:
–«к стану»;
–«удержание»;
–«осцилляция».
Режим «к стану» используется для эксплуатации печи в обычном режиме для синхронизации скорости сляба на входе в туннельную печь со скоростью вытягивания из кристаллизатора МНЛЗ, передачи отрезанного сляба к выходу из печи, отправки сляба на прокатный стан.
Режим «удержание» применяется при продолжении приема слябов, поступающих с МНЛЗ, без передачи их на стан для синхронизации скорости сляба на входе в туннельную печь со скоростью МНЛЗ, удержания сляба в зоне выгрузки печи в ре-
100