
Гацков Прогрессивные технологии изготовления деталей 2011
.pdf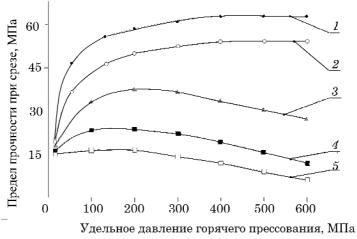
Рис. 4.27. Зависимость предела прочности при срезе бронзофторопласта от давления горячего прессования. Содержание фторопласта в % (об.):
1 – 20; 2 – 30; 3 – 40; 4 – 50; 5 – 60
Предел прочности при срезе повышается с увеличением давления горячего прессования до максимальных значений, соответствующих каждому материалу по содержанию фторопласта. Дальнейшее повышение давления горячего прессования снижает прочность материалов при срезе. Максимальные значения пределов прочности при срезе для материалов с меньшим содержанием фторопласта достигнуты при более высоких давлениях (зависимость 1 на рис. 4.27). С увеличением количества фторопласта в материалах значения давлений горячего прессования, при которых достигнуты максимальные значения пределов прочности, уменьшаются. Так, с увеличением количества фторопласта в материалах от 20 до 60 % значения давлений, соответствующие максимальным пределам прочности, уменьшаются с 600 до 200 МПа. Причем степень изменения характеристики прочности также зависит от содержания фторопласта в материалах. Прочность увеличивается в большей степени для материалов, содержащих меньшее количество фторопласта.
Такая зависимость предела прочности при срезе объясняется изменением соотношений суммарных энергий межчастичных свя-
81
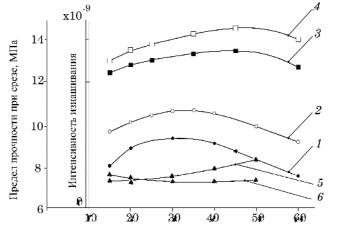
зей и внутренних напряжений, возникающих в результате горячего прессования.
На рис. 4.28 показаны выборочные зависимости предела прочности при срезе и интенсивности изнашивания материалов наполненного типа. Характер изменения приведенных характеристик материалов от давления горячего прессования и их численные значения зависят от количества наполнителя во фторопласте. Как и материалы каркасного типа, наполненные фторопласты достигают максимальных значений пределов прочности при давлениях, соответствующих содержаниям наполнителей (зависимости 1– 4).
Рис. 4.28. Зависимость характеристик фторопласта, наполненного бронзой, от давления горячего прессования при содержании бронзы:
1 – τср = 10 %; 2 – τср = 15 %; 3 – τср = 20%; 4 – τср = 25%; 5 – Ih = 10; 6 – Ih = 20
При увеличении количества наполнителя во фторопласте увеличиваются значения давлений горячего прессования, при которых достигнуты максимальные значения пределов прочности при срезе. Так, при изменении количества порошка бронзы от 10 до 25 % максимальные значения пределов прочности материалов достигнуты при соответствующих изменениях значений давлений в пределах от 25 до 40 МПа. При тех же значениях давлений горячего прессования материалы имеют наиболее высокую износостойкость (зави-
82
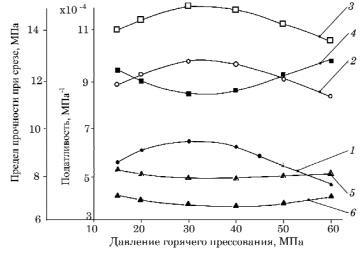
симости 5 и 6 на рис. 4.28). Причем характер изменения интенсивности изнашивания материалов, как и предела прочности при срезе, зависит от количества наполнителя.
Изменение характеристик материалов, наполненных никелем с содержанием последнего в пределах от 10 до 25 % от давления горячего прессования, представлено зависимостями 1–6 на рис. 4.29.
Рис. 4.29. Зависимости характеристик никель-фторопластовых материалов от давления горячего прессования (τср – 1; 2; 3 и ξt – 4; 5; 6 при содержаниях никеля 10; 20; 25 % соответственно)
Пределы прочности материалов при срезе в зависимости от содержания никеля и давления горячего прессования изменяются аналогично, как и у материалов, наполненных бронзой (зависимости 1–3 на рис. 4.28). Зависимостями 4–6 выявляется изменение податливости композиций от давления горячего прессования их. Давления, при которых податливость принимает минимальные значения, зависят от количества никеля в материалах. При увеличении количества никеля увеличивается давление, при котором достигает наименьшую податливость композиций. При одинаковых давлениях горячего прессования меньшей податливостью обладают материалы с большим количеством наполнителя.
83
Характер изменения свойств материалов наполненного типа в зависимости от давления горячего прессования можно объяснить изменением адгезии фторопласта к поверхностям частиц наполнителя и ухудшением спекаемости фторопласта при повышении давлений за некоторые их значения. Проверкой последнего предположения установлено, что спекаемость фторопласта или композиций при повышенных давлениях горячего прессования достигается повышением температуры. Проявляется зависимость температуры горячего прессования от давления такая же, как и зависимость температуры термодеструкции.
4.4.Влияние количественного соотношения компонентов
иразмеров их частиц на трение и износ материалов, содержащих фторопласт
Процесс трения и износа материалов, содержащих фторопласт, определяется свойствами пленок, формирующихся на поверхности трения. Основными факторами, влияющими на формирование и параметры пленок являются: материал основы композиций или наполнителя, количество фторопласта или наполнителя в композициях, наличие и свойства других входящих компонентов, размеры частиц компонентов, условия изготовления материалов, условия и режимы трения, вызывающие механо- и термодеструкцию фторопласта, материал контртела.
Испытания проведены на установке, обеспечивающей повышенную точность определения коэффициента трения, по схеме втулка – радиально нагружаемый цилиндрический образец и на машине трения с устройством для измерения силы трения по схеме трения кольцевой образец – вращающийся диск.
4.4.1. Установка для испытания материалов на трение и износ
Установка (рис. 4.30) состоит из станины 1, на которой смонтированы привод, включающий электродвигатель постоянного тока
84
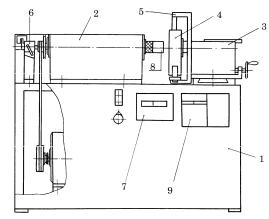
ПЗ1У4 ГОСТ 183-74, и шпиндельный узел 2, подвижная в двух направлениях бабка 3 с испытательной головкой 4 и упорами 5, удерживающими головку от проворачивания, редуктор 6 со счетчиком количества оборотов типа СК-1 с микровыключателем, тахометр 7 типа ЦАТ-3М с датчиком частоты вращения шпинделя. Внутри станины смонтированы устройства электрической схемы, обеспечивающей питание электродвигателя, датчика, регулирование частоты вращения и автоматическое отключение установки при достижении заданного пути трения в контакте.
Перемещение бабки 3 в поперечном направлении обеспечивает проведение испытаний на трение по схеме диск – пальчиковый образец с измерением радиуса трения, а перемещение в продольном направлении обеспечивает подвод образцов к диску или втулке 8, являющимися контртелами, устанавливаемыми на шпинделе привода. В зависимости от схемы трения, используемых при испытании, в бабке устанавливают соответствующую головку.
Для фиксирования температур в контакте и моментов трения на панели станины установлен самописец с усилителем 9.
Рис. 4.30. Установка для испытания материалов на трение и износ
Точность измерений коэффициента трения при радиальной схеме испытаний обеспечивается конструкцией испытательной головки с встроенным устройством нагружения (рис. 4.31).
85
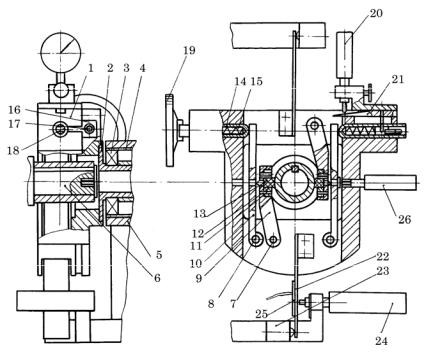
Рис. 4.31. Испытательная головка
Корпус 1 головки через цапфу 2, подшипники 3 и стакан 4 установлен в бабке 5, сцентрированной относительно шпинделя 6. В корпусе на осях 7 и 8 шарнирно крепятся рычаги 9 и 10. Штифтами 11, запрессованными в рычаги 9, фиксируют оправки 12 с образцами материалов 13. В отверстиях корпуса установлены толкатели 14 с тарированными пружинами 15. В прямоугольные направляющие корпуса установлены ползуны 16, соединенные через резьбу со стяжным винтом 17 и входящие упорами в пазы сухарей 18. Поджатие образцов к контртелу (втулке) осуществляют сжатием пружин 15 сухарями 18, получающими перемещение вместе с ползунами 16 при вращении моховика 19, закрепленного на стяжном винте.
Деформация пружин, определяющая усилия поджатия образцов, фиксируется микрометрическими головками 20 через подвижные клинья 21, соединенные с сухарями 18. Плавающая установка
86
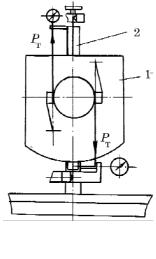
стяжного винта с ползунами в направляющих корпуса обеспечивает поджатие образцов к втулке-контртелу равными по величине и противоположно направленными силами.
Значение моментов трения определяют по деформации тарированных упругих балок 22, закрепленных на корпусе и одновременно контактирующих с упорами 23, и фиксируют микрометрической головкой 24 с ценой деления 0,001 мм, постоянно контактирующей с балкой или тензометрическими датчиками 25.
Износ материалов определяют с помощью микрометрической головки 26 или по изменению массы – взвешиванием образцов до и после испытаний.
Для испытаний материалов оправки 12 с образцами 13 устанавливают на штифты 11 рычагов 9, перемещением бабки с головкой образцы вводят в зону трения и поджимают к поверхности втулки с соответствующей режимам трения силой. Частотой вращения шпинделя задают скорость в контакте, а набором количества оборотов на счетчике (с учетом передаточного отношения червячного
редуктора) – путь трения. |
|
Противоположно направленные и рав- |
|
ные по величине силы поджатия двух об- |
|
разцов, момент трения и уравновеши- |
|
вающий двумя одинаковыми по длине и |
|
жесткости балками момент не вызывают |
|
реакции в опорных подшипниках голов- |
|
ки, что повышает точность в определении |
|
коэффициентов трения материалов неза- |
|
висимо от режимов трения, продолжи- |
|
тельности и периодичности испытаний. |
|
Головка протарирована по схеме, по- |
|
казанной на рис. 4.32. При тарировке го- |
|
ловки 1 силы Рт, создаваемые динамомет- |
|
ром 2, прикладывали непосредственно к |
Рис. 4.32. Схема тарировки |
рычагам, на которых при испытании ус- |
измерительной головки |
танавливают оправки с образцами. Линии |
|
действия тарировочных сил параллельны между собой и проходили через оси шарниров рычагов, конструктивно расположенных на
87
расстоянии равном диаметру втулки-контртела. Такое приложение сил и отсутствие в схеме блоков, через которые меняют направления действия сил, обеспечивает повышенную точность тарировки.
Тарировочный график представляет зависимость силы трения от величины деформации упругих балок головки.
4.4.2. Измерение толщины пленки на поверхности трения контртела
Толщину пленки на поверхности трения измеряли с помощью профилографа - профилометра модели 201 Б-194, предназначенного для измерения шероховатости и волнистости поверхностей изделий из металлических материалов. Возможность погружения иглы датчика прибора в поверхность пленки при снятии профилограммы, вызывающего погрешность при измерении, была проверена применением иглы с радиусом закругления 1 мм. Профилограмма, снятая датчиком с такой иглой, обеспечивает измерение толщины пленки, но не дает представления о микрорельефе поверхности и изменении его в процессе трения.
Толщину пленки можно определить по отклонениям профилограммы, снятой с поверхности участка трения, относительно профилограммы, снятой с того же участка до испытаний. При этом необходимо разграничить эти отклонения на три составляющих: отклонения от температурных влияний, от износа трущейся поверхности и образования пленки на трущейся поверхности.
На участке профилограммы, соответствующем участку трения поверхности, с которой она снята, присутствуют отклонения от влияния всех трех факторов. На участке профилограммы, относящемся к неподверженной трению поверхности, отклонение связано с температурным влиянием. Считая эту составляющую отклонения одинаковой по всей трассе датчика, можно ее исключить из суммарного отклонения сравнением этих участков профилограмм, снятых до и после испытаний с совпадающих трасс датчика прибора на исследуемой поверхности.
Составляющая отклонения от износа при трении может быть исключена анализом профилограмм, снятых с участка поверхности
88
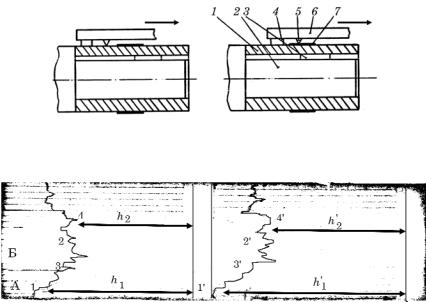
трения. Кроме того, износ контртела с твердой поверхностью в паре с образцами из материалов, содержащих фторопласт, как показывают испытания, несоизмерим с толщиной, образующейся за короткое время трения пленкой, и может быть не учтен при исследованиях относительного изменения толщины пленки от влияния технологических факторов.
Для совмещения трасс датчика прибора втулку-контртело 1 из стали 40Х13 с твердостью поверхности HR C 48…50 и шероховатостью 0,32 устанавливали на оправку 2 с фиксатором 3 (рис. 4.33). С подготовленной к испытаниям поверхности втулки снимали профилограмму 1 (рис. 4.34).
аб
Рис. 4.33. Схема установки втулки и снятия профилограмм
а б
Рис. 4.34. Профилограмма поверхности втулки с увеличением ×10000 до (а) и после (б) испытаний
После трения на пути 5000 м аналогично снималась профилограмма 2, на которой отмечались характерные участки А и Б, соответствующие положениям опоры 4 и иглы 5 датчика 6 относительно пленки 7 (см. рис. 4.33, а и б).
89
По точкам 1 и 1 ́соответствующим, одной точке на поверхности втулки участка А, относящемуся к участку трассы датчика вне поверхности трения (см. рис. 4.33, а) находят изменение радиуса втулки от температурных влияний h1 (в масштабе настройки прибора):
h1 = h1 −h1′, |
(4.14) |
где h1 – расстояние от базовой линии до характерной точки 1 на профилограмме на рис. 4.34, а, мм; h1′ – расстояние от базовой линии
до соответствующей точки 1’ на профилограмме на рис. 4.34, б, мм. По точкам 2 и 2’, соответствующим точке на поверхности трения до и после испытаний, определяют суммарную величину смещения профилограммы h2 на участке Б, относящемуся к участку трассы датчика на поверхности трения (см. рис. 4.33, б). Величина смещения или изменения радиуса втулки в сечении зоны трения (в
том же масштабе) определяется как
h2 = h2 −h2′ , |
(4.15) |
где h2 – расстояние от базовой линии до точки 2 на профилограмме на рис. 4.34, а; h2′ – расстояние от базовой линии до соответствую-
щей точки 2’ на профилограмме на рис. 4.34, б.
Суммарная величина c (в мм), включающая износ втулки и толщину пленки, определяется как
c = ( h1 − h2 )Kм , |
(4.16) |
где Kм – коэффициент увеличения настройки прибора. Измерения, проведенные с использованием иглы датчика с уве-
личенным радиусом закругления и стандартной иглы, показали значения толщин пленок, отличающихся не более чем на 4 % (в пределах погрешности прибора). Это значит, что удельное давление стандартной ощупывающей иглы датчика позволяет проводить снятие профилограммы с поверхности, покрытой пленкой, образующейся при трении материалов, содержащих фторопласт.
Сравнивая участки Б профилограмм, снятых с поверхности втулки до и после трения (см. рис. 4.34), следует отметить, что в процессе трения почти не изменяется характер и высота микронеровностей (точки 3; 3’ и 4; 4’), а изменяется их относительное расположение. Это свидетельствует о малой величине износа трущейся поверхности втулки, которую можно не учитывать при
90