
Гацков Прогрессивные технологии изготовления деталей 2011
.pdf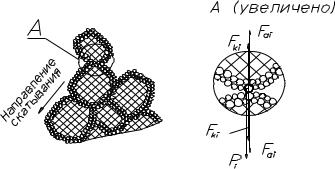
частиц и агрегатов из них при сухом смешивании в смесителе. В процессе смешивания порошковых компонентов на частицы и агрегаты действуют силы тяжести, трения и центробежные. Частицы нижних слоев порошков под действием сил трения увлекаются вверх, а затем скатываются или соскальзывают вниз, теряя сцепление с нижними слоями. В момент движения вниз на них не действует центробежная сила от вращения ёмкости смесителя.
При условии скатывания образовавшихся гранул или крупных частиц-ядер на частицы, из которых образуются оболочки, сначала действует сила тяжести скатывающейся гранулы или частицы-ядра, а затем сила адгезии Fai к грануле или частице-ядру и сила отрыва
(рис. 2.8).
Рис. 2.8. Схема действия сил в верхнем слое порошков при смешивании
Сила отрыва Foi является результирующей силы тяжести самой частицы Pi и силы адгезии или когезии Fкi этой частицы к частицам
нижележащего слоя и определится из уравнения: |
|
Foi = Pi + Fкi, |
(2.1) |
Частица будет удерживаться на поверхности ядра и гранулы, ес-
ли Fai > Foi.
Критические условия формирования оболочки или её сохране-
ния в верхнем слое смеси порошков определяют равенством: |
|
Fai = Pi + Fкi, |
(2.2) |
Силы, с которыми частицы удерживаются на поверхности, зависят от площади фактического контакта частиц. При равномерном
31

распределении контактов частиц силы адгезии (когезии) пропорциональны числу контактов, а число контактов на шероховатой поверхности пропорционально размерам частиц.
При таком допущении силы адгезии, с приближением достаточным для практического применения, можно выразить зависимостью:
Fai = Ks dэ2i Fsа, |
(2.3) |
где dэi – эквивалентный диаметр частицы неправильной формы; Ks – коэффициент соотношения диаметра частицы и площади диаметрального сечения с учётом формы (Ks ≤ π/4); Fsа – удельная сила адгезии, Па.
Эквивалентный диаметр частиц находят по их равновеликому объёму из соотношения:
dэi = 3 l b2 , |
(2.4) |
i i |
|
где li и bi – размеры частиц в двух направлениях измерений. |
|
Представляя массу частицы mri зависимостью |
|
mri = KV dэiγк, |
(2.5) |
силу тяжести выражают |
|
Рi = KV dэiγкg, |
(2.6) |
где KV – коэффициент соотношения диаметра и объёма частиц, ограниченного развитой поверхностью; γк – плотность компактного материала частиц.
Для частиц с размерами, приведёнными к эквивалентным диаметрам с небольшой погрешностью можно принять KV ≈ π/6.
Из условия, определяемого равенством (2.2) и соотношений (2.3) и (2.5) критическое значение эквивалентного диаметра dэк
находят |
|
dэк = K(Fsа – Fsк)/ γк g, |
(2.7) |
где K = Ks/KV, Fsк – удельная сила когезии (удельная сила адгезии к частицам нижерасположенного слоя смеси в смесителе), Па.
При движении гранул и частиц порошков в смесителе в результате столкновений в наружных слоях и действия гравитационных, центробежных сил и сил трения во внутренних слоях частицы, обладающие большей твёрдостью, вдавливаются в поверхность частиц с меньшей твёрдостью, уплотняются оболочки гранул,
32
увеличиваются фактические контактные поверхности частиц. Увеличиваются силы адгезии между частицами.
Размеры частиц фторопласта для материалов каркасного типа, изготовляемых с использованием эффекта взаимодействия частиц, должны быть больше критического. Это позволяет избегать их когезию.
Условия каркасообразования из металлических частиц, не образующих оболочки гранул, т.е. из частиц с размерами больше критических, в некоторой мере улучшатся при применении порошков с размерами частиц определенных соотношений.
При соизмеримости объемов частиц фторопласта с межчастичными пространствами металлических порошков, образующих каркас, в процессе прессования смесей металлические частицы будут приводиться в контакт между собой с перемещением по поверхностям частиц фторопласта, не подвергая их механодеструкции. При этом уменьшается вероятность попадания фторопласта в зону контакта металлических частиц.
При условии получения компактного материала фторопласт заполняет все поровое пространство металлического каркаса. Объемы пор, образуемых металлическими частицами, зависят от размеров частиц и плотности их упаковки. Пористость прессовок из сферических частиц находится в пределах 25,9÷47,6 %. Отсюда следует, что в порах металлического каркаса разместится 25,9÷47,6 % фторопласта (по объему).
Объем одной поры, занимаемой фторопластом, определяется зависимостью:
Vc = (Vφф)/nп, |
(2.8) |
где Vc – средний объем поры; V – объем материала; φф – объемное содержание фторопласта; nп – число пор в объеме материала.
Число пор в объеме зависит от размеров и упаковки металлических частиц при горячем прессовании, содержания фторопласта, его распределения в объеме, давления прессования. При равномерном распределении фторопласта и его содержании в пределах 25,9÷
47,6 % число пор в объеме определяется: |
|
nп = (0,75÷1,71)nм, |
(2.9) |
где nм – число частиц металлического порошка в объеме, которое определяется из соотношения
33

nм= 6V(1 – φф)/(πdc3м ), |
(2.10) |
где dсм – средний диаметр частиц металлического порошка.
Из зависимостей (2.8), (2.9) и (2.10) средний объем выразится
Vc = (0,3÷0,7)(φф dc3м )/(1 – φф). |
(2.11) |
Из уравнения (2.11) средний размер частиц фторопласта пред-
ставится зависимостью |
|
dсф = (0,83÷1,1)dсм [φф/(1 – φф) ]1/3. |
(2.12) |
Значение коэффициента выбирают в зависимости от содержания фторопласта в материалах. Меньшее значение (0,83) соответствует меньшему значению количества фторопласта и наоборот.
2.3.2. Количественное соотношение порошковых компонентов в материалах
Зависимость (2.12) определяет соотношение размеров частиц фторопласта и количественное содержание его в материалах, в которых формируется металлический каркас с сообщающимися порами, заполненными фторопластом. При формировании структур материалов каркасного и наполненного типов из гранул частиц компонентов предельные объемные соотношения их определяют из условия образования монослойной оболочки при смешивании порошков.
При сферической форме и плотноупакованном покрытии поверхности ядра частицами материала основы (рис. 2.9) объемные соотношения компонен-
тов гранулы представляют зависимо-
стью
(2.13)
где Vo – объем частиц материалаосновы (оболочки); Vя – объем части- цы-ядра гранулы; n – число частиц, образующих монослойную оболочку.
Число частиц с размерами d, с учетом несплошности поверхности образуемой оболочки определяют из соотношения площадей
34
поверхности сферы с диаметром (D+d) и диаметрального сечения частицы по зависимости
n = 4Kн (1 + D/d)2, |
(2.14) |
где Kн – коэффициент несплошности поверхности оболочки гранулы.
С учетом пластической деформации частиц в процессе горячего прессования с достаточной точностью для практики можно принять Kн = 1. При нагреве фторопласт увеличивается в объеме до 25 % [3]. С учетом этих факторов из зависимости (2.13) и (2.14) получаем
Vо /Vя = (5d/D)(1 + d/D)2. |
(2.15) |
Считая материал оболочек гранул основой композиции любого типа, а материал частиц-ядер наполнителем этой основы, соотношение (2.15) выражающее предельные условия формирования
структур композиции, в общем виде можно записать: |
|
φо/φн = (5dо/dн)(1 + dо/dн)2, |
(2.16) |
где φо и φн – объемное содержание компонентов (основы и наполнителя) в процентах (долях); do и dн – размеры частиц порошков компонентов композиции.
Уравнение (2.15) позволяет определять предельные объемные соотношения компонентов при задаваемых размерах их частиц, при которых создаются наивыгоднейшие условия для формирования структур материалов каркасного или наполненного типов.
В табл. 2.1 приведены расчетные значения предельного количества фторопласта в материалах каркасного типа в зависимости от размеров частиц порошков фторопласта и материала основы.
|
|
|
|
|
|
Таблица 2.1 |
|
Значения предельного содержания фторопласта |
|
|
|||||
в композициях каркасного типа |
|
|
|
||||
|
|
|
|
|
|
|
|
Размеры |
Предельное количество фторопласта (%) при |
||||||
частиц |
размерах частиц порошков материала основы, мкм |
|
|||||
фторопласта, мкм |
2 |
4 |
6 |
|
8 |
10 |
|
30 |
72 |
54 |
41 |
|
32 |
25 |
|
60 |
84 |
72 |
62 |
|
54 |
47 |
|
90 |
89 |
81 |
72 |
|
65 |
59 |
|
120 |
92 |
84 |
78 |
|
72 |
67 |
|
35
Рассмотренные условия создаются на стадии подготовки смесей и предопределяют структуры материалов, содержащих фторопласты.
Окончательное формирование структур и свойств материалов предопределяются рядом факторов, влияющих на процесс горячего прессования смесей, в состав которых входит фторопласт.
Контрольные вопросы
1.Какие структуры формируются при изготовлении материалов, содержащих фторопласт?
2.Как формируются структуры многокомпонентных материалов?
3.Какие условия являются предельными для формирования структур материалов?
4.Какие значения размеров частиц порошковых компонентов материалов (металлов и фторопластов) являются критическими?
5.Как определяют количественное соотношение порошковых компонентов в материалах?
36

3. ГОРЯЧЕЕ ПРЕССОВАНИЕ ПОРОШКОВЫХ МАТЕРИАЛОВ
Горячим прессованием называют совмещенный процесс прессования и спекания порошков, т.е. процесс уплотнения порошков, развития межчастичного сцепления и формирования свойств порошковых материалов.
Вработах [10, 11] обобщены результаты исследований ряда авторов в области прессования и спекания порошковых материалов, рассмотрены вопросы уплотнения порошков и формирования структуры пористых материалов при горячем прессовании.
3.1.Процессы уплотнения порошков и развития межчастичного сцепления при горячем прессовании
Вряде работ горячее прессование представлено как процесс, характеризующийся приложением быстро нарастающего до необходимой величины давления и сравнительно короткой выдержкой при повышенных температурах. Процесс, протекающий при длительной выдержке под постоянным давлением, называют спеканием под давлением. В работе [11] эти процессы сведены к двум ступеням единого процесса горячего уплотнения, так как спеканию под давлением практически всегда предшествует быстрое нагружение, а снимать нагрузку сразу не рекомендуют во избежание вредного влияния упругого последействия. Быстрое горячее прессование автор описывает уравнением, полученным им для холодного прессования, учитывая температурные влияния на характеристики материала порошков:
p = pк′ α , |
(3.1) |
где р – номинальное давление прессования; α – безразмерное контактное (критическое) сечение; pк′ – критическое (контактное)
давление прессования, которое определяют зависимостью:
pк′ = H0′ / (1−2μк α) , |
(3.2) |
где H0′ – кратковременная горячая твердость материала частиц; μк
– коэффициент Пуассона компактного материала.
37
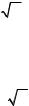
На второй стадии горячего прессования автор выделяет процессы переноса материи трёх различных типов:
1)перенос материи за счет перемещения атомов внутри объема частиц;
2)перенос материи за счет перемещения атомов по поверхности частиц;
3)перенос материи за счет взаимного перемещения частиц. Считают, что перенос материи за счет перемещения атомов по
поверхности частиц (как и перенос за счет других дефектов) не отражается на типе уравнения зависимости степени уплотнения от времени горячего прессования при постоянном давлении. Но наличие этого вида переноса материи ускоряет процесс снижения кратковременной твердости и коэффициента вязкости.
В работе приведены выведенные уравнения кинетики спекания под постоянным давлением. Изменение эффективного контактного
давления прессования ( pк′)02 представлено уравнением: |
|
( pк′)02 =0,25η H0′ / (t +t0 ) , |
(3.3) |
где η – коэффициент вязкости; t – время выдержки при постоянной температуре; t0 – эквивалентное время выдержки, учитывающее начальный период спекания, которое рассчитывают по зависимости
t0 = 0, 25ηH0′ . |
(3.4) |
Значение коэффициента вязкости и кратковременной горячей твердости уменьшается с увеличением активности порошков, т.е. с ростом подвижности атомов.
Из уравнения кинетики уплотнения при холодном прессовании, имеющего вид:
α2 |
= |
p2 |
. |
(3.5) |
|
(1−2μк α)2 |
( pк′)02 |
||||
|
|
|
Подстановкой значений ( pк′)02 из формулы (3.3) автором работы [11] получено соотношение
α2 |
= |
p2 (t +t |
) |
, |
(3.6) |
|
0 |
|
|||
(1−2μк α)2 |
0, 25 |
|
|||
|
|
|
|
где постоянны все величины, кроме α и t.
38

Из этого соотношения можно рассчитывать время выдержки при заданной температуре Т, постоянном давлении рп и известных других составляющих:
|
2 |
|
′ |
|
|
1 |
|
|
|
|
|
α |
H0 |
|
|
|
|
|
|||
t = 0, 25η |
|
|
|
|
|
− |
|
|
, |
(3.7) |
|
−2μ |
|
α)2 |
H0′ |
||||||
(1 |
к |
|
|
|
|
|||||
|
|
|
|
|
|
|
|
|
Безразмерное контактное сечение α представляют степенной за-
висимостью от относительной плотности υ вида: |
|
α = υm, |
(3.8) |
где m – показатель, зависящий от типа пористого тела, его пористости, структуры и других факторов. Для одной и той же плотности показатель может иметь различные значения.
Уравнение, описывающее изменение пористости при горячем прессовании, предложенное Муррэем, Роджерсом и Вильямсом, имеет вид:
ln |
Πн |
≈ |
3 |
|
p |
t , |
(3.9) |
4 |
|
||||||
|
Π |
|
η |
|
|
где Пн – начальная пористость; П – пористость горячепрессованного образца; t – время выдержки под давлением p.
В отличие от прессования при комнатной температуре, когда самыми твердыми и трудно деформируемыми участками в связи с их окисленностью являются внешние слои, при горячем прессовании поверхностные слои легче деформируются, снижается коэффициент взаимного трения частиц. В результате релаксации остаточных напряжений при нагреве снимается наклеп, что интенсифицирует уплотнение.
Непрерывное перераспределение напряжений, несинхронность концентраций их в результате ускоренного образования, залечивания и перемещения дефектов облегчает уплотнение при нагреве. Немалая роль в несинхронности концентраций напряжений принадлежит наложению явлений спекания под собственным капиллярным давлением, имеющим более местный, быстро меняющий направление и точки приложения характер.
Как при холодном, так и при горячем прессовании в стадии невысоких плотностей характерно преобладание межчастичной деформации. При наиболее высоких плотностях исключается
39
перемещение частиц, уплотнение происходит за счет атомов (внутричастичной деформации).
При горячем прессовании при одинаковой плотности достигается высокая прочность, что вызвано развитием межчастичного сцепления явлениями, присущими спеканию порошков.
Впроцессе спекания происходит удаление адсорбированных паров и газов, восстановление и диссоциация окисных плёнок, диффузионное перемещение атомов, исправление дефектов кристаллической решетки металлических порошков, рекристаллизация, перенос материала через газовую фазу и другие явления, в результате которых изменяется состояние межчастичных связей и структуры пористых материалов в целом.
Врезультате поверхностной диффузии атомов происходит сглаживание поверхностей соприкасающихся участков частиц, сфероидизация пор, перемещение атомов с поверхностей крупных на поверхность мелких (сообщающихся) пор, что приводит к увеличению и упрочнению межчастичных контактов. За счет объемной диффузии атомов по вакансиям (или диффузии вакансий от мелких пор к крупным) происходит поглощение мелких пор крупными. Диффузия атомов по межкристаллическим границам идет во много раз быстрее, чем по объему кристалла, поэтому процесс коагуляции пор при спекании происходит быстрее в брикетах из порошков с меньшими размерами частиц.
Спекание металлических порошков сопровождается изменением объема сформированного пористого тела, чаще всего его уменьшением.
Механизм усадки при спекании заключается в объемной деформации частиц в результате объемной диффузии атомов по вакансиям. Иногда нарушается процесс усадки, наблюдается её снижение или даже рост объема. Причинами этого являются наличие невосстанавливающихся оксидов, фазовые превращения, выделения газов, релаксация напряжений, возникших при прессовании. Рост объема спекаемых тел происходит при образовании закрытой пористости, составляющей более 7 %.
Расширение газов, находящихся в закрытых порах, препятствует уплотнению при спекании, и вызывают рост брикетов. Образова-
40