
Гацков Прогрессивные технологии изготовления деталей 2011
.pdf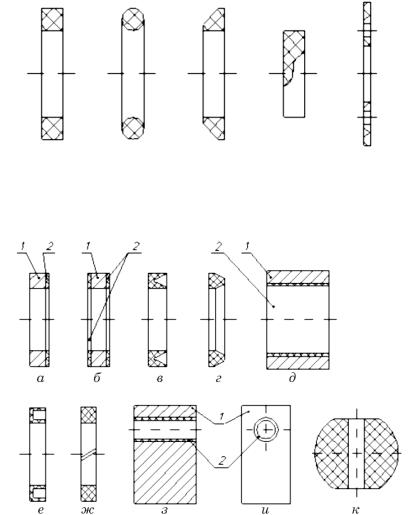
а |
б |
в |
г |
д |
|
Рис. 6.1. Уплотнения неподвижных соединений |
|
а – в виде кольца прямоугольного сечения, б - в виде кольца круглого сечения, в - в виде кольца конического сечения, г - в виде диска, д - в виде кольца с отверстиями
Рис. 6.2. Детали подвижных соединений и узлов трения:
а, б – кольца торцовых уплотнений, опорные кольца с одним или двумя рабочими слоями (2), нанесенными на армирующие кольца (1);
в, г, е – уплотнения по диаметрам валов, штокам; ж – поршневое кольцо; д – втулка подшипника скольжения из комбинированного материла; з, и – антифрикционный рабочий слой (2) в корпусных деталях (1);
к – сферический самоустанавливающийся подшипник
131
Детали подшипников скольжения изготовляют из комбинированного материала. Нагрузку воспринимает несущая часть 1, изготовленная из компактного материала или порошков. Тонкий антифрикционный слой 2 работает на трение и износ и обеспечивает долговечность подшипника.
Несущей частью подшипника скольжения может служить одновременно детали изделия, выполняющие другую функцию в нем. Малонагруженные подшипники скольжения изготовляют из наполненных фторопластов, имеющих высокую износостойкость и низкий коэффициент трения.
6.2. Технологические процессы изготовления деталей, содержащих фторопласт, горячим прессованием
Технологический процесс изготовления деталей из смесей порошков включает следующие операции:
1)подготовку порошков-компонентов смесей;
2)смешивание порошков-компонентов;
3)прессование заготовок;
4)загрузку заготовок в пресс-формы для горячего прессования;
5)загрузку пресс-форм в камеру для горячего прессования, установление режимов, выдержку на режимах, охлаждение;
6)разгрузку пресс-форм, зачистку, снятие заусениц;
7)контроль заготовок или деталей;
8)упаковку деталей.
Процесс изготовления деталей антифрикционного назначения с тонким рабочим слоем в отверстии включает операции:
1)изготовление заготовок из компактного или порошкового материала с учетом толщины рабочего антифрикционного слоя;
2)подготовку смеси для антифрикционного рабочего слоя в отверстиях деталей;
3)установление заготовки деталей в приспособление, закрепление приспособления на установке, нанесение антифрикционного слоя, освобождение приспособления;
4)установление приспособления в печь, спекание антифрикционного слоя и его припекание к заготовке;
132
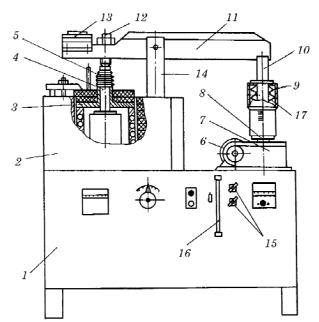
5)извлечение приспособления из печи, выдержку до полного охлаждения в термостате;
6)разбор приспособления, зачистку от облоя и заусениц;
7)контроль деталей;
8)упаковку деталей.
6.3.Оборудование для горячего прессования
6.3.1. Установка для прессования заготовок, содержащих фторопласт
Установка (рис. 6.3) состоит из корпуса 1, на котором смонтированы нагревательная камера 2 с крышкой 3, подвижным штоком 4 и герметизированным сильфоном 5. Узел нагружения содержит электродвигатель 6, червячный редуктор 7, опору 8 с демпфирующим устройством 9, толкатель 10 и рычаг 11 с регулировочным винтом 12 и электромагнитным вибратором 13.
Рис. 6.3. Установка для горячего прессования
133
Внутри корпуса смонтированы трансформатор, пусковая и регулирующая аппаратура, система подвода газовой среды. На панели установки смонтированы элементы управления и контрольные приборы.
Перед загрузкой пресс-формы в камеру и перед ее выгрузкой рычаг вместе со стойкой 14 поворачивают в горизонтальной плоскости. Положение его в вертикальной плоскости регулируют винтом 12. Открытием одного из вентилей 15 в камеру подается защитная или восстановительная среда, расход которой контролируется ротаметром 16. Создание давления на изделие производится от электродвигателя через редуктор, опору, соединенную резьбой с червячным колесом и перемещающейся вдоль оси, пружины 17 демпфирующего устройства, толкатель, рычаг, регулирующий винт, шток крышки и пуансоны пресс-форм.
Величина усилия определяется величиной деформации пружины 17 и фиксируется по шкале, нанесенной на стакане демпфирующего устройства, или приборами через тензометрические датчики. Демпфирующее устройство устраняет жесткость системы нагружения и резкое изменение давления при температурном изменении длины изделий. Наличие электромагнитного вибратора обеспечивает повышение качества изделий и производительность их изготовления.
6.3.2. Устройство для горячего прессования заготовок из порошковых смесей
Устройство предназначено для горячего прессования заготовок с усилием до 900 кН на гидравлическом прессе в восстановительной или защитной среде.
Устройство состоит из основания 1 (рис. 6.4) с изолирующей плитой 2, нагревательной камеры 3 с крышкой 4, соединенной тягами 5 с верхней плитой 6, теплоизолирующего кожуха 7, систем подвода и отвода газовой среды, питания, нагрева и контроля, объединенные блоком управления 8. Крышка 4 поднимается и удерживается в верхнем положении через тяги 5 плитой 6, которая крепится к штоку или верхней плите пресса. Поджатие крышки к
134
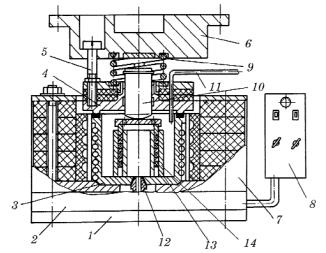
нагревательной камере осуществляется пружиной 9 при опускании плиты 6 вниз и создании давления на штоке 10.
Со штока через верхний пуансон прессформы давление передается на изготовляемые детали.
Защитный или восстановительный газ отводится из камеры через трубопровод 11, а подается в камеру через соединительный штуцер 12 с небольшим избыточным давлением.
Рис. 6.4. Устройство для горячего прессования
6.4. Установка для нанесения антифрикционного металлофторопластового слоя в отверстиях
Наиболее технологичным и эффективным признан способ формования антифрикционного слоя радиальным прессованием. Смесь порошковых компонентов 6 (рис. 6.5) подается в зазор между поверхностями заготовок 2, установленных в обойме 1, и вращающимися шнеком 3 и уплотняется конусной частью оправки 4, соединенной со шнеком и перемещающейся вдоль оси вместе с ним. Уплотненный слой 5 при температуре ниже температуры термодеструкции фторопласта спекают и одновременно припекают к заго-
135
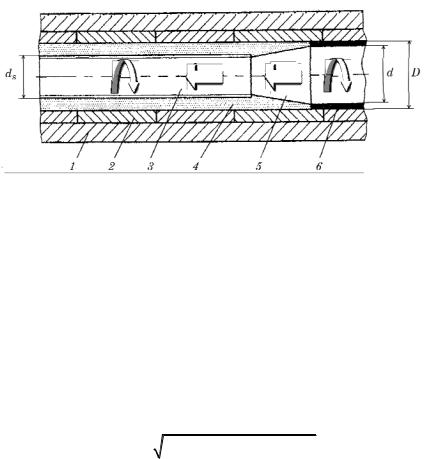
товке втулки подшипника. Между собой втулки разделяют прокладками.
Для обеспечения нормального формования слоя, его спекания и припекания в заготовке величину зазора принимают в зависимости от толщины наносимого слоя, характеристик порошковых компонентов, их процентного соотношения в смеси и параметров шнека.
Рис. 6.5. Схема нанесения антифрикционного слоя
Условие сохранения массы материала до формования (смеси компонентов) и сформованного антифрикционного слоя можно представить равенством
γк (D2 − d 2 ) = γнKу (D2 − ds2 )
где γк – плотность компактного материала слоя, кг/м3; γн – насыпная плотность смеси компонентов материала слоя, кг/м3; Ky – коэффициент уплотнения смеси в процессе подачи ее в зазор; D – диаметр отверстия под покрытие, м; d – диаметр сформированного отверстия, м; ds – наружный диаметр шнека, образующего зазор и подающего в него смесь, м.
Из равенства наружный диаметр шнека определяют соотношением
ds = D2 −(γк / γнKy )(D2 −d 2 ) .
Вышеприведенный способ нанесения антифрикционного слоя реализуется на установке (рис. 6.6), которая состоит из станины 1, на которой смонтирован корпус узла нанесения 2 с опорой 3, направляющей 4, шнеком 5 и столиком 6. В нижней части станины
136
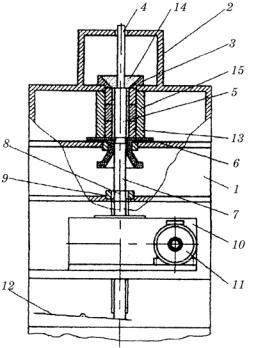
крепится червячный редуктор 10 с винтом 8, электродвигатель 11 с муфтой и педаль включения осевой подачи винта 12. В перегородке станины закреплена опорная гайка 9.
Рис. 6.6. Установка для нанесения металлофторопластового слоя
Для нанесения антифрикционного слоя на поверхности внутреннего диаметра заготовок 13 обойму 15 с заготовками устанавливают на столик 6 и поджимают верхним торцом к опоре 3. После этого на винт 8 соосно устанавливают оправку 7, шнек 5, направляющую 4 и включают вращение винта против часовой стрелки, которое передается через оправку 7 на шнек 5. Имея левое направление винтовой поверхности, шнек перемещает смесь 14 из воронки опоры зазор, образованный поверхностью шнека и поверхностями заготовок. После заполнения зазора смесью вращение шнека меняют на правое и винтовая поверхность подуплотняет смесь, и удаляет ее излишки. Нажатием на педаль 12 винт вводится в зацеп-
137
ление с гайкой и получает осевое перемещение вместе с оправкой, шнеком и направляющей. При вращении и осевом перемещении оправка своей конусной частью уплотняет смесь до необходимой плотности. При достижении конечного положения винта вращение и его перемещение автоматически прекращаются. Заготовки с обоймой и оправкой передаются на термическую обработку.
6.5. Испытание уплотнительных колец узлов торцового уплотнения
Кольца узлов торцовых уплотнений с наружным диаметром равным 85 мм, внутренним диаметром 70 мм и толщиной 10 мм изготовляются из комбинированного антифрикционного материала. Толщина антифрикционного слоя из бронзофторопластового материала с ячейчатой структурой составляет 2,5 мм. Внутренние кольца (см. рис. 6.2, б) формируются из железного порошка и подвергаются лужению. В состав смеси для антифрикционного слоя вводят фторопласт-4ДПТ (42 % по объему).
Горячее прессование проводят при давлении 250 МПа и температуре 650 ±5 К в течение 45 мин в среде водорода.
Испытание на спекание антифрикционного слоя с поверхностью внутреннего кольца проводили по известной методике срезанием слоя по границе раздела поверхностей. При испытаниях восьми колец предел прочности при срезе составил 30÷33 МПа, т.е. такой же по численным значениям, как и предел прочности при срезе материала антифрикционного слоя.
Испытания на работоспособность проводили на установке (рис. 6.7), обеспечивающей скорость в контакте с контртелом до 25 м/с.
Установка состоит из станины 1, шпиндельной головки 2 с электродвигателем постоянного тока 3, установленной на стойке 4, гидросистемы с насосом 5, измерительно-регистрирующей аппаратуры 6 и испытательной головки с устройством нагружения 7, показанной на рис. 6.8.
Для проведения испытаний уплотнительное кольцо 1 (рис. 6.8) устанавливается в оправке 2, закрепленной на шпинделе 3. Перемещением шпиндельной головки вниз образец вводится в контакт с
138

контробразцом 4, закрепленном в подвижной опоре 5, удерживаемой от проворачивания двумя упорами 6 через упругие балки 7.
Рис. 6.7. Установка для испытания материалов на трение и уплотняющую способность
Контактное напряжение создается вращением маховика 8 с валиком 9, через червячную пару редуктора 10, винт 11 со стаканом 12, пружину 13 и плунжер 14 с толкателем 15. Нагружение на кольцо обеспечивается при наличии зазора «S» между поверхностями опоры 5 и корпуса 16.
При испытаниях уплотнительных колец в полость «А», образованную поверхностями кольца 1, оправки 2, контробразца 4 и опоры 5 подается рабочая жидкость с соответствующим давлением.
Постоянство задаваемого контактного напряжения достигнуто наличием двух сообщающихся полостей «А» и «В» в опоре 5.
Коэффициент трения определяют по моменту трения, фиксируемому с помощью тензометрических датчиков, наклеенных на упругие балки 7.
139
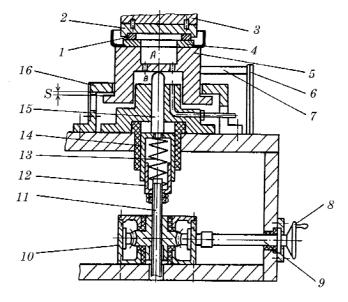
Величину износа определяют разностью размеров высоты кольца до и после испытаний или по величине перемещения опоры 5 с помощью микрометрической головки.
Рис. 6.8. Испытательная головка
Уплотняющую (герметизирующую) способность колец оценивают отношением контактного напряжения к давлению рабочей среды в полости при отсутствии ее утечки между контактирующими поверхностями.
На установке можно испытывать материалы на трение и износ в разных условиях (сухое, граничное, жидкостное трение), определять уплотняющую способность уплотнительных колец в зависимости от их геометрических параметров, точности изготовления, качества поверхностей и других факторов.
Четыре кольца предложенной конструкции испытывали в течение 1000 ч при скорости в контакте 23 м/с, давление рабочей среды 0,3 МПа и контактном напряжении 0,25 МПа. В качестве рабочей среды использовали масло индустриальное И-12А ГОСТ 20799-75. Перед испытаниями торцовые поверхности колец обрабатывали с
140