
Гацков Прогрессивные технологии изготовления деталей 2011
.pdfобразец. Упругую балку 13 при этом фиксируют в верхнем, а упор
– в нижнем положениях, чем обеспечивают свободный ход рычага. Величину деформации образца через назначенные отрезки времени фиксируют индикаторной головкой 16.
При испытаниях материалов на релаксацию напряжений нагружение образцов производят через упругую балку 13, а фиксирование постоянства длины образца после нагружения обеспечивают упором 15. После выдержки в течение определенного времени, заданного условием эксперимента, винтом 14 снимают нагрузку до уравновешивания сил, действующих на рычаг со стороны образца и упругой балки. Величину силы, соответствующей напряжениям в образце, находят исходя из величины силы, действующей со стороны упругой балки, которую фиксируют протарированной головкой 17, по известным зависимостям с учетом плеч рычага.
Релаксацию напряжений характеризовали относительной величиной ξσ, которую определяли соотношением
ξσ = 1 – σt /σ0 , (4.17)
где σ0 – заданное исходное напряжение, создаваемое в образцах, МПа; σt – напряжение в образцах после выдержки при их постоянных длинах в течение времени t, МПа.
Выражая напряжения через силы, действующие на образцы, при допущении сохранения площади поперечного сечения можно записать
ξσ = 1 – Рt /Р0 , |
(4.18) |
где P0 – сила, действующая на образец в начальный момент, Н; Pt – сила, соответствующая напряжениям в деформированных образцах по истечении времени t.
Для определения характеристик были изготовлены образцы материалов из смесей порошков фторопласта-4ДПТ с размерами частиц 30÷160 и 1÷15 мкм с порошками бронзы ОС 6-6 со средними размерами частиц 5, 33, 60, 90, 124, 153 и 180 мкм (предельные значения размеров 1÷10; 15÷45; 52÷72; 74÷108; 110÷132; 135÷160 и 165÷210 мкм). Из этих же порошков бронзы готовили смеси для образцов материалов на основе фторопласта-40, фторопласта-4МБ с размерами частиц 0,3÷5 мкм. Наполнитель вводили в количестве 10; 15 и 20 % по объему сухим смешиванием в механическом сме-
111
сителе. Увеличение количества наполнителя считали не целесообразным в связи с ухудшением антифрикционных свойств и увеличением жесткости, отрицательно сказывающейся на герметизирующую способность материалов. Горячее прессование осуществляли при давлении 20 МПа и температурах 650±5 К (для материалов на основе фторопласта–4ДПТ) и 570±5 К (для материалов на основе фторопластов-40 и 4МБ) с выдержкой в течение 120 мин (из расчета 10 мин на 1 мм наименьшего размера образца) и охлаждением со скоростью 180 К/ч. Образцы материалов испытывали на ползучесть и релаксацию напряжений при сжатии в течение 12 ч при напряжении 12 МПа.
Модули упругости материалов определяли по упругим составляющим деформаций, которые фиксировали при разгружении образцов в конце испытаний на ползучесть.
4.5.2. Влияние размеров частиц и количественного соотношения компонентов на модуль упругости, податливость и релаксацию напряжений
Модули упругости всех композиций увеличиваются с увеличением размеров частиц наполнителя до 90÷100 мкм (рис. 4.47). Дальнейшее увеличение размеров частиц ведет к снижению значений модуля. Это вызвано изменением удельной поверхности порошков, измерения которой показали увеличение ее с увеличением размеров частиц до 80÷100 мкм.
Изменение размеров частиц фторопласта вызывает изменение упругости материалов (зависимости 1; 3 и 4; 5). Это вызвано изменением структур материалов, формируемых при их изготовлении.
С увеличением количества наполнителя увеличивается модуль упругости, изменяется степень влияния на него размеров частиц.
Размеры частиц порошков наполнителя и фторопласта, как и их количественные соотношения, влияют на податливость материалов (рис. 4.48) и релаксацию напряжений (табл. 4.9). Податливость композиций уменьшается с увеличением размеров частиц наполнителя до 90÷120 мкм. Причем меньшей податливостью обладают материалы на основе фторопласта с размерами частиц, обеспечи-
112
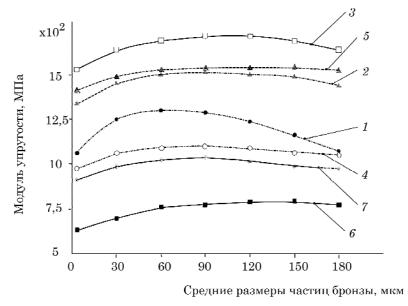
вающими выгодные условия формирования структур наполненных материалов (зависимости 4 и 5).
Рис. 4.47. Зависимость модуля упругости от размеров частиц порошков:
фторопласт-4ДПТ (dф = 30÷160 мкм) + бронза (%): 1 – 10; 2 – 15; 3 – 20;
фторопласт-4ДПТ (dф = 1÷15 мкм) + бронза (%): 4 – 10; 5 – 20; фторопласт-40 + бронза (%): 6 – 10; 7 – 20
Таблица 4.9
Значения относительных изменений напряжений в материалах на основе фторопласта-4ДПТ за 12 ч
Размеры частиц фторопласта |
Относительные изменения напряжений |
||||
dф и наполнителя d, мкм |
при количестве наполнителя |
||||
10 % |
15 % |
20 % |
|||
|
|
||||
dф = 30 ÷ 160 : |
d = 1÷10; |
0,546 |
0,494 |
0,406 |
|
|
d = 74 ÷ 108; |
0,482 |
0,452 |
0,381 |
|
|
d = 165 ÷ 210 |
0,523 |
0,471 |
0,394 |
|
dф = 1 ÷ 15 : |
d = 1÷10; |
0,502 |
0,463 |
0,386 |
|
|
d = 74 ÷ 108; |
0,458 |
0,431 |
0,368 |
|
|
d = 165 ÷ 210 |
0,469 |
0,437 |
0,373 |
113
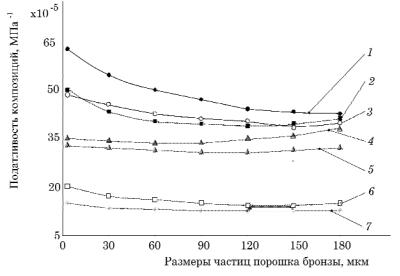
Рис. 4.48. Зависимость податливости от размеров частиц порошков:
фторопласт-4ДПТ (dф = 30÷160 мкм) + бронза (%): 1 – 10; 2 – 15; 3 – 20;
фторопласт-4ДПТ (dф = 1÷15 мкм) + бронза (%): 4 – 10; 5 – 20; фторопласт-40 + бронза (%): 6 – 10; 7 – 20
Материалы на основе фторопластов-40 и -4МБ подвергаются меньшей деформации и меньшему влиянию на податливость количества наполнителя (зависимость 6 и 7).
Скорость податливости (или ползучесть) уменьшается во времени и зависит от количества наполнителя, марки фторопласта – основы материала, размера частиц (рис. 4.49). Для наполненных фторопластов (10÷20 % наполнителя) скорость податливости уже через 6÷10 ч уменьшается до 0 (зависимости 2–7).
Чистый (без наполнителя) фторопласт обладает относительно высокой скоростью податливости (в 2,5÷5 раз выше по сравнению с наполненным) (зависимость 1). Наименьшей скоростью податливости и временем уменьшения ее до 0 обладают материалы на основе фторопласта-40 (зависимости 6 и 7). Близка к ней скорость податливости для материалов на основе фторопласта-4МБ.
114
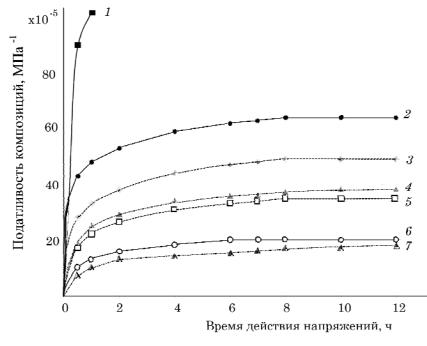
Рис. 4.49. Зависимость податливости от времени действия напряжений (6 МПа): 1 – фторопласт-4ДПТ;
2 – фторопласт-4ДПТ (dф = 1÷10 мкм) + 10 % бронзы; 3 – фторопласт-4ДПТ (dф = 80÷100 мкм) + 10 % бронзы; 4 – фторопласт-4ДПТ (dф = 1÷10 мкм) + 20 % бронзы; 5 – фторопласт-4ДПТ (dф = 80÷100 мкм) + 20 % бронзы; 6 – фторопласт-40 (dф = 10 мкм) + 10 % бронзы;
7 – фторопласт-40 (dф = 80÷100 мкм) + 10 % бронзы
Относительное изменение напряжений имеет более высокие значения для материалов на основе фторопласта-4ДПТ с размерами частиц dф = 30÷160 мкм. Значения их уменьшаются при увеличении количества наполнителя и увеличении размеров его частиц. Причем при увеличении размеров частиц значения относительных изменений напряжений достигают минимума, а затем увеличиваются (см. табл. 4.9).
Таким образом, зависимости характеристик, определяющих герметизирующую способность материалов, от размеров частиц
115
порошковых наполнителей показывают, что оптимальные размеры частиц находятся в пределах 60÷120 мкм, а лучшей основой по этим характеристикам для уплотнительных материалов является фторопласт-40 или -4МБ.
При изучении характеристик не учитывалось влияние технологических факторов, влияние которых может в определенной степени сказаться на рассмотренные зависимости, поэтому требуется проведение оптимизации количественного соотношения компонентов и размеров частиц наполнителя во взаимодействии с технологическими факторами. Необходимо также учитывать состояние и тип наполнителя.
Контрольные вопросы
1.Как определить силы адгезии частиц порошковых компонентов к поверхностям деталей?
2.В результате чего образуются агрегаты из частиц порошковкомпонентов материалов?
3.Объясните формирование структур материалов на стадиях смешивания порошковых компонентов и формования смесей.
4.Объясните формирование структуры материалов при горячем прессовании.
5.Как определить предельные значения количества фторопласта в материалах?
6.Как влияют состояние порошковых компонентов и режимы изготовления каркасных наполненных материалов и деталей из них на основные характеристики (твердость, прочность при срезе, при сжатии, коэффициент трения, износостойкость)?
7.Как влияет давление горячего прессования смесей на основные характеристики наполненных материалов на основе фторопластов?
8.Зависимость коэффициента трения и износа от количественного соотношения компонентов в материалах и режимов трения.
9.Каково устройство установки для испытания материалов на трение и износ. Как она работает?
10.Как определить толщину пленки формируемой на поверхности трения?
116
5. ОПТИМИЗАЦИЯ КОЛИЧЕСТВЕННОГО СООТНОШЕНИЯ КОМПОНЕНТОВ, РАЗМЕРОВ ИХ ЧАСТИЦ И РЕЖИМОВ ИЗГОТОВЛЕНИЯ МАТЕРИАЛОВ
5.1. Оптимизация состава и режимов изготовления материалов каркасного типа
Исходя из результатов исследований материалов каркасного типа, содержащих фторопласт, компонентом основы выбран бронзовый порошок (Бр ОС 6-6) с размером частиц 1÷10 мкм и содержанием кислорода менее 0,3 %. Наиболее удобным для формирования гранул с ядрами из фторопласта при смешивании порошковкомпонентов является порошок фторопласта-4ДПТ с размерами частиц 30÷160 мкм, имеющий высокую сыпучесть и поставляемый в таком виде промышленностью. Третьим компонентом использовали графит марки С-2 с размерами частиц до 15 мкм. Порошки смешивали последовательно: сначала фторопласт с графитом, а затем полученную смесь с порошком бронзы. Это обеспечивало формирование гранул с наружной оболочкой из порошка бронзы.
В эксперименте варьировали количеством фторопласта и графита (бронза – остальное), давлением и временем горячего прессования при температуре 550+5 К в среде водорода. Значения уровней и интервалов варьирования факторов выбирали на основе приведенных выше результатов (табл. 5.1).
Для получения уравнений (математических моделей) в степенном виде кодированные значения факторов определяли по выраже-
нию [12]
x |
= |
|
2ln xi −ln xi max |
|
+1 |
, |
(5.1) |
|
|
||||||
i |
|
|
|
|
|
||
|
|
ln xi max −ln xi min |
|
|
|
||
где xi – кодированные значения факторов; |
|
xi , xi max , xi min – нату- |
ральные значения факторов.
Образцы материалов (по 4 штуки) изготовляли по условиям опытов (табл. П1 приложения), составленным в соответствии с матрицей планирования 4-факторного эксперимента (табл. П2 приложения). Параметрами оптимизации выбраны: предел прочности
117
при срезе (τср), коэффициент трения (f) и интенсивность изнашивания (Ih), средние значения которых приведены в табл. П1.
|
|
|
|
|
Таблица 5.1 |
||
Значения уровней и интервалов варьирования факторов |
|||||||
|
|
|
|
|
|
||
|
Кодовое |
Интервал |
Уровни факторов |
||||
|
обозначе- |
верх- |
основ- |
|
|||
Факторы |
варьиро- |
нижний |
|||||
ние факто- |
ний |
ной |
|
||||
|
ров |
вания |
+ |
0 |
|
– |
|
|
|
|
|
||||
φф – содержание |
х1 |
8 |
52 |
44 |
|
36 |
|
фторопласта, % |
|
||||||
|
|
|
|
|
|
||
φс – содержание |
х2 |
2 |
8 |
6 |
|
4 |
|
графита, % |
|
||||||
|
|
|
|
|
|
||
р – удельное дав- |
х3 |
75 |
325 |
250 |
|
175 |
|
ление горячего |
|
||||||
прессования, МПа |
|
|
|
|
|
|
|
t – время выдержки |
|
|
|
|
|
|
|
при горячем прес- |
х4 |
2 |
8 |
6 |
|
4 |
|
совании на едини- |
|
||||||
|
|
|
|
|
|
||
цу высоты, мин/мм |
|
|
|
|
|
|
В результате обработки эксперимента и перехода от уравнений регрессий, полученных в кодированном виде к уравнениям в натуральном виде получены математические соотношения между параметрами и влияющими факторами.
|
|
τср = 0, 0135ϕср−1,94ϕс0,255(1−0,47 ln p) p5,519(1−0,0895ln p)t0,097 , [МПа], |
|
(5.2) |
|||||||||||||||
|
|
|
|
|
f |
14,87 |
ϕ |
−8,6(1−0,125ln ϕф ) |
p |
0,082 |
t |
0,087 |
, |
|
(5.3) |
||||
|
|
|
|
|
= e |
|
|
|
|
|
|
|
|
||||||
|
|
|
|
|
|
|
|
ф |
|
|
|
|
|
|
|
|
|
|
|
I |
|
= e |
62,816 |
ϕ |
−37,086(1−0,125ln ϕ −0,0503ln ϕ ) |
ϕ |
−4,66(1+0,18ln ϕ ) |
p |
−2,9658(1−0,26ln ϕ ) |
. |
(5.4) |
||||||||
h |
|
|
|
ф |
c |
с |
|
|
|
c |
ф |
||||||||
|
|
|
ф |
|
|
|
|
|
|
|
|
|
|
|
|
|
Полученные уравнения позволяют определить количественные соотношения компонентов в композициях, давление и время горячего прессования для получения материалов с заданными характеристиками или прогнозировать характеристики по выбранным режимам горячего прессования материалов с известным соотношением входящих порошковых компонентов. Для этого можно пользоваться
118
графическими зависимостями характеристик материалов, рассчитанных по приведенным уравнениям (5.2), (5.3), (5.4), от влияющих на них факторов или таблицами, составленными на основе уравнений.
Учитывая возможные варианты математических моделей, которые могут быть получены в результате исследования процессов постановкой экспериментов по плану второго порядка, зависимости характеристик материалов от влияющих факторов в общем виде можно выразить уравнением
A =C BK1′BK2′ |
...BKn′ |
, |
(5.5) |
u u 1 2 |
n |
|
|
где Au – значения характеристик материалов; В1, В2, …, Вn – значения влияющих факторов в выбранных пределах; Cu – коэффициенты, значения которых получают экспериментально; K1′, K2′, …,
Kn′ – показатели степени, которые имеют вид
Ki′ =α′i (1+β′i ln Bi +λ′i Bi ) , |
(5.6) |
где α′i , β′i , λ′i – коэффициенты, зависящие от свойств материалов,
входящих порошковых компонентов и факторов, зафиксированных на постоянных уровнях, значения коэффициентов получают обработкой результатов экспериментов; i – индекс фактора в экспери-
менте (i = 1, …, n).
Для определения характеристик материалов или параметров других процессов, описываемых моделью приведенного вида, пользуются программами для расчета значений характеристик по полученным уравнениям.
В табл. 5.2–5.4 приведена часть расчетных значений предела прочности при срезе, коэффициента трения и интенсивности изнашивания материалов на основе бронзы, содержащих фторопласт4ДПТ и графит, изготовленных горячим прессованием в течение 120 мин (из расчета 10 мин/мм).
Прочность материалов уменьшается при увеличении количества фторопласта и графита в композициях (табл. 5.2). Влияние давления горячего прессования зависит от количества графита в материалах. При содержании его до 3 % прочность снижается при удельных давлениях больших 300 МПа. С увеличением графита уменьшается давление, при котором обеспечивается наиболее высокая прочность композиций.
119
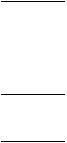
|
|
|
|
|
Таблица 5.2 |
|
Значения пределов прочности при срезе материалов |
||||||
|
на основе бронзы |
|
|
|
||
|
|
|
|
|
|
|
Давление |
Содержание |
Пределы прочности, МПа, при |
||||
горячего |
графита в |
количестве фторопласта в композиции |
||||
прессования, |
композиции, |
|
|
|
|
|
30 % |
40 % |
50 % |
|
60 % |
||
МПа |
% |
|
||||
|
48,16 |
|
|
|
||
|
2 |
84,15 |
31,24 |
|
21,63 |
|
200 |
6 |
55,4 |
31,72 |
20,7 |
|
14,32 |
|
10 |
45,65 |
26.12 |
17,03 |
|
11,81 |
|
2 |
84,13 |
48,12 |
31,2 |
|
21,52 |
300 |
6 |
52,54 |
29,91 |
19,42 |
|
13,38 |
|
10 |
41,89 |
24,13 |
15,62 |
|
10,76 |
450 |
2 |
71,56 |
41,16 |
26,72 |
|
18,73 |
6 |
42,74 |
24,58 |
15,95 |
|
11,19 |
|
|
10 |
32,80 |
18,86 |
12,24 |
|
8,58 |
Коэффициент трения уменьшается с увеличением количества фторопласта в композициях, не зависит от количества графита и увеличивается при увеличении давления и времени горячего прессования (табл. 5.3).
Таблица 5.3
Значение коэффициентов трения композиций на основе бронзы
Давление |
Время горя- |
|
Коэффициент трения при |
|
|||
чего прессо- |
|
|
|||||
количестве фторопласта в композиции |
|||||||
горячего |
вания на |
|
|
|
|
|
|
прессования, |
единицу |
|
|
|
|
|
|
|
|
|
|
|
|
||
МПа |
высоты, |
30 % |
|
40 % |
50 % |
|
60 % |
|
мин/мм |
|
|
|
|
|
|
200 |
2 |
0,238 |
|
0,179 |
0,162 |
|
0,160 |
6 |
0,258 |
|
0,194 |
0,177 |
|
0,174 |
|
|
10 |
0,269 |
|
0,203 |
0,185 |
|
0,182 |
300 |
2 |
0,246 |
|
0,185 |
0,168 |
|
0,164 |
6 |
0,266 |
|
0,201 |
0,183 |
|
0,180 |
|
|
10 |
0,279 |
|
0,210 |
0,190 |
|
0,187 |
|
2 |
0,254 |
|
0,191 |
0,173 |
|
0,170 |
450 |
6 |
0,276 |
|
0,208 |
0,188 |
|
0,185 |
|
10 |
0,289 |
|
0,218 |
0,195 |
|
0,191 |
120