
Гацков Прогрессивные технологии изготовления деталей 2011
.pdf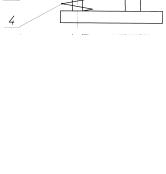
или импульсных сил. Силы отрыва между отдельными частицами или отдельными частицами и плоскостью определяют на приборах и установках, в принцип измерения которых положен маятниковый метод или деформация кварцевой пружины.
Совершенствование методов определения адгезии путем отрыва отдельных частиц достигали применением сложных и уникальных приборов.
Использование межчастичного взаимодействия для формирования агрегатов смесей из порошковых компонентов не требует определения составляющих сил адгезии и для практики достаточно ограничиться определением их средних значений.
4.1.1. Методика определения сил адгезии частиц порошковых компонентов
Для определения сил адгезии частиц порошковых компонентов антифрикционных и уплотнительных материалов к плоским поверхностям и к поверхностям частиц использован метод импульсного воздействия сил на частицы, падающие с высоты h вместе с подвижной частью 1 на опору 2 устройства (рис. 4.1) установлен-
ной на пружине 4. |
|
Для определения сил адгезии час- |
|
тиц порошков к поверхностям ком- |
|
пактных материалов частицы с разме- |
|
рами (1÷80 мкм) наносили на торцовые |
|
или боковые поверхности вставок 3, |
|
изготовленных из материалов иссле- |
|
дуемых компонентов. |
|
Для определения сил адгезии час- |
|
тиц компонентов к поверхностям час- |
|
тиц одноименных или других компо- |
Рис. 4.1. Схема устройства |
нентов последние (больших размеров) |
приклеивали к подвижной части устройства (на поверхность вставки) и на них наносили частицы первых.
Изменение импульса силы производили изменением высоты h, на которую поднимали подвижную часть устройства с частицами.
51
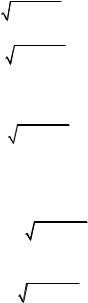
Силы отрыва, развиваемые при падении подвижной части устройства на подпружиненную опору, определяют по известной зависимости
Fоi = mri(amax + g), |
(4.1) |
где Fоi – сила отрыва, действующая на каждую частицу, Н; mri – масса частиц, кг; amax – наибольшее значение ускорения подвижной части, м·с–2; g – ускорение свободного падения, м·с–2.
Из уравнения движения подвижной части устройства под дейст-
вием пружины наибольшее значение ускорения выразится |
|
amax = схmax/m, |
(4.2) |
где xmax – наибольшая величина деформации пружины, м; m – масса подвижной части с частицами, кг; с – жесткость пружины, Н·м-¹.
Величину максимальной деформации пружины фиксируют экспериментально или находят из равенства потенциальной энергии подвижной части устройства, поднятой на высоту h (кинетической энергии в момент падения на опору с пружиной), и работы сжатия
пружины до величины xmax: |
|
|
mgh = схmax2/2. |
(4.3) |
|
Из равенства (4.3) |
|
|
хmax= |
2ghm / c. |
(4.4) |
Из уравнений (4.2.) и (4.4) получим |
|
|
amax= |
2ghc / m. |
(4.5) |
Из уравнений (4.1) и (4.5) при падении подвижной части устройства на опору с пружиной на каждую частицу порошка дейст-
вует сила отрыва |
|
Foi = mri ( 2ghc / m + g). |
(4.6) |
При условии Foi > Fadi частицы с размерами, соответствующими массам mri отрываются от поверхности вставки или других частиц.
Из критических условий (Fadi = Foi) и уравнений (4.6) и (2.5) силы адгезии частиц определяют из зависимости
Fadi = 0,523( dэ3i γ( 2ghc / m + g) . |
(4.7) |
Удельную силу адгезии из зависимостей (4.7) и (2.3) представляют уравнением
Fsi = 0,667dэi γ( 2ghc / m + g) . |
(4.8) |
52

Силы, которыми частицы удерживаются на поверхности, в значительной мере компенсируются на площади фактического контакта частиц. Трудность в определении фактического контакта частиц лишает возможности объективной оценки зависимости сил адгезии от размеров частиц порошков.
Наиболее удобно эту зависимость выявляют с помощью гравитационного коэффициента [7].
Для частиц, отрывающихся под действием сил, развиваемых при падении подвижной части с частицами на опору с пружиной, гравитационный коэффициент Ku определяют как отношение силы отрыва (или адгезии) частиц к силе гравитации
Ku = Fadi/ Pi, |
(4.9) |
где Pi – сила гравитации, действующая на частицу, Н.
Подставив известное выражение силы гравитации и зависимость силы адгезии (4.7) в соотношение (4.9), получим
Ku = 2hc / mg +1. |
(4.10) |
4.1.2.Силы адгезии и размеры частиц порошковых компонентов
Экспериментально определены силы адгезии частиц неправильной формы порошков бронзы Бр ОС 6-6, никеля электролитического и карбонильного, фторопласта-4ДПТ (ТУ 6-05-041-372-72), 4ДТ, 4ПФТ и фторопласта-40 к плоской поверхности и поверхности частиц фторопласта 4ДПТ, плоской поверхности и поверхности частиц бронзы Бр ОС 6-6.
Вопытах для каждой высоты, с которой падала подвижная часть устройства, измеряли размеры наименьших частиц порошков, и определяли средние значения эквивалентных диаметров.
Втабл. 4.1 приведены силы и удельные силы адгезии бронзовых частиц к различным поверхностям, определенные условием Fadi =
=Foi по зависимостям (4.7) и (4.8).
Близкими к результатам для бронзового порошка получены результаты для порошков никеля.
53
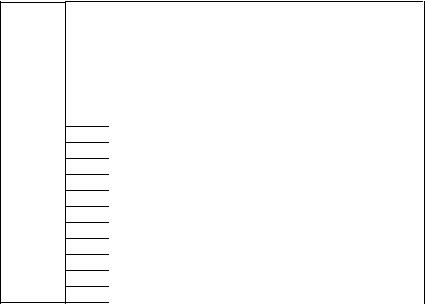
Таблица 4.1
Силы адгезии бронзовых частиц
Силы (Fadi) и удельные силы (Fsi) адгезии к поверхностям
Эквива- |
|
Бронза, |
Бронза, |
Фторопласт, |
Фторопласт, |
||||
лентные |
|
плоскость |
поверхность |
плоскость |
поверхность |
||||
диаметры |
|
|
|
частиц |
|
|
частиц |
||
частиц, |
|
|
|
(dср = 150 |
|
|
(dср = 150 |
||
мкм |
|
Fad, Н |
|
мкм) |
|
|
мкм) |
||
|
|
Fs, |
Fad, Н |
Fs, Па |
Fad, Н |
Fs, Па |
Fad, Н |
Fs, Па |
|
|
×10-10 |
Па |
×10-10 |
|
×10-10 |
|
×10-10 |
|
|
11 |
|
- |
- |
- |
- |
- |
- |
6,5 |
6,84 |
9,6 |
|
- |
- |
4,82 |
6,66 |
- |
- |
5,1 |
7,05 |
8,2 |
|
2,69 |
5,1 |
3,56 |
6,74 |
2,83 |
5,36 |
3,82 |
7,24 |
7,4 |
|
- |
- |
2,96 |
6,88 |
2,38 |
5,54 |
3,19 |
7,42 |
6,5 |
|
1,76 |
5,29 |
2,36 |
7,12 |
2,07 |
6,24 |
2,56 |
7,71 |
5,7 |
|
- |
- |
- |
- |
1,73 |
6,78 |
- |
- |
5,2 |
|
1,19 |
5,57 |
1,52 |
7,16 |
1,33 |
6,27 |
1,59 |
7,49 |
4,2 |
|
0,76 |
5,51 |
0,97 |
7,00 |
0,82 |
5,92 |
- |
- |
3,8 |
|
0,62 |
5,48 |
- |
- |
0,64 |
5,64 |
0,71 |
6,26 |
3,3 |
|
- |
- |
0,58 |
6,78 |
0,47 |
5,49 |
- |
- |
2,7 |
|
0,28 |
4,89 |
- |
- |
0,30 |
5,24 |
- |
- |
Силы адгезии увеличиваются с увеличением размеров частиц, что связано с увеличением фактической поверхности контактов. Удельная сила адгезии с изменением размеров частиц изменяется в узком интервале. Для практических целей используют среднее значение удельной силы, зависящее от контактирующих материалов и характера контактирующих поверхностей. Силы адгезии к поверхностям частиц больше, чем к плоской поверхности.
Аналогичные зависимости сил адгезии получены для частиц фторопласта к поверхностям бронзы и фторопласта (табл. 4.2) и поверхности никеля (табл. 4.3).
Из сравнения удельных сил адгезии частиц порошков к поверхностям бронзы, никеля и фторопласта видно, что наименьшие значения их относятся к частицам фторопласта, контактирующим с поверхностью фторопласта. Значительно больше они при контактировании с бронзой или никелем. Разница в значениях сил адгезии
54
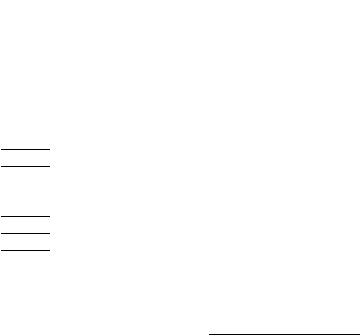
может быть использована для создания благоприятных условий образования агрегатов смесей при смешивании компонентов. При смешивании частицы фторопласта не будут соединяться между собой, а будут покрываться металлическими частицами, силы адгезии которых к фторопласту больше сил когезии фторопластовых частиц.
|
|
|
|
|
|
|
|
|
|
|
|
|
|
|
|
Таблица 4.2 |
||||
|
|
|
Силы адгезии частиц фторопласта–4ДПТ |
|
|
|
|
|
|
|
||||||||||
|
|
|
Силы (Fadi) и удельные силы (Fsi) адгезии к поверхностям |
|
|
|||||||||||||||
|
Эквива- |
|
|
|||||||||||||||||
|
|
Бронза, |
|
Бронза, |
|
Фторопласт, |
Фторопласт, |
|
|
|||||||||||
|
лентные |
|
плоскость |
|
поверхность |
|
плоскость |
поверхность |
|
|
||||||||||
|
диаметры |
|
|
|
|
|
частиц |
|
|
|
|
|
|
|
частиц |
|
|
|||
|
частиц, |
|
|
|
|
|
(dср = 150 мкм) |
|
|
|
|
|
|
(dср = 150 |
|
|
||||
|
мкм |
|
Fad, Н |
|
|
|
|
|
|
|
|
|
|
|
|
мкм) |
|
|
||
|
|
|
|
Fs, |
|
Fad, Н |
Fs, |
|
Fad, Н |
Fs, |
Fad, Н |
Fs, |
|
|
||||||
|
|
|
×10-10 |
|
Па |
|
×10-10 |
Па |
|
×10-10 |
|
Па |
×10-10 |
|
Па |
|
|
|||
|
36 |
|
56,3 |
5,53 |
|
62,6 |
6,15 |
|
- |
|
- |
|
- |
|
- |
|
|
|||
|
26 |
|
30,2 |
5,69 |
|
34,1 |
6,41 |
|
18,25 |
|
3,44 |
|
21,6 |
|
4,07 |
|
|
|||
|
19 |
|
16,6 |
5,86 |
|
18,5 |
6,53 |
|
10,12 |
|
3,51 |
12,29 |
|
4,34 |
|
|
||||
|
15 |
|
10,45 |
5,92 |
|
11,87 |
6,72 |
|
6,87 |
|
3,89 |
|
7,91 |
|
4,48 |
|
|
|||
|
13,6 |
|
8,2 |
5,64 |
|
9,39 |
6,47 |
|
5,93 |
|
4,09 |
|
6,62 |
|
4,56 |
|
|
|||
|
11,4 |
|
5,37 |
5,26 |
|
6,07 |
5,95 |
|
4,32 |
|
4,24 |
|
5,06 |
|
4,96 |
|
|
|||
|
9,6 |
|
- |
- |
|
- |
- |
|
2,95 |
|
4,08 |
|
3,24 |
|
4,48 |
|
|
|||
|
|
|
|
|
|
|
|
|
|
|
|
|
|
|
|
Таблица 4.3 |
||||
|
Силы адгезии частиц фторопласта к поверхностям никеля |
|||||||||||||||||||
|
|
|
|
|
|
|
|
|
|
|||||||||||
|
Эквивалентные |
|
|
Силы (Fadi) и удельные силы (Fsi) адгезии |
||||||||||||||||
|
|
|
|
|
|
|
|
|
Поверхность частиц |
|||||||||||
|
диаметры частиц, |
|
Плоская поверхность |
|
|
|||||||||||||||
|
|
|
никеля (dср = 150 мкм) |
|||||||||||||||||
|
мкм |
|
|
|
|
|
|
|
|
|||||||||||
|
|
|
Fad, Н ×10-10 |
Fs, Па |
|
Fad, Н ×10-10 |
|
Fs, Па |
||||||||||||
|
38 |
|
|
|
|
59,2 |
5,22 |
|
|
|
63,8 |
|
|
|
5,63 |
|
|
|||
|
27,5 |
|
|
|
32,3 |
5,44 |
|
|
|
34,12 |
|
|
|
5,75 |
|
|
||||
|
20,5 |
|
|
|
18,6 |
5,64 |
|
|
|
19,32 |
|
|
|
5,86 |
|
|
||||
|
15,2 |
|
|
10,36 |
5,72 |
|
|
|
1,95 |
|
|
|
6,04 |
|
|
|||||
|
14 |
|
|
|
|
8,47 |
5,51 |
|
|
|
8,67 |
|
|
|
5,63 |
|
|
|||
|
11,5 |
|
|
|
5,61 |
5,41 |
|
|
|
5,76 |
|
|
|
5,55 |
|
|
55
Силы адгезии металлических частиц к частицам фторопласта в процессе смешивания увеличиваются в сравнении со свободным нанесением их на поверхность частиц фторопласта (табл. 4.4).
Таблица 4.4
Адгезия бронзовых частиц к поверхности частиц фторопласта после смешивания
Параметры адгезии |
|
Значение параметров адгезии частиц |
|
||||
|
с эквивалентными диаметрами, мкм |
|
|||||
|
11,6 |
|
9 |
8,2 |
7,3 |
|
5,5 |
Сила адгезии Fadi, Н |
7,6 |
|
6,1 |
5,2 |
4,27 |
|
1,97 |
× 10–10 |
|
|
|||||
Удельная сила адге- |
7,19 |
|
9,59 |
9,86 |
10,2 |
|
8,3 |
зии Fsi, Па |
|
|
|||||
|
|
|
|
|
|
|
Увеличение сил адгезии при смешивании порошковых компонентов вызывается в основном в результате сближения частиц под действием сил, возникающих при движении порошковых масс в смесителе.
Зависимость сил адгезии от размеров частиц порошков бронзы и фторопласта представлены графическими зависимостями коэффициента гравитации (рис. 4.2 и 4.3). Гравитационный коэффициент (Ku) увеличивается с уменьшением размеров частиц всех порошковых материалов. Большей адгезией обладают частицы к поверхностям разноименных материалов в сравнении с адгезией к поверхностям одноименных материалов (когезией).
Из графических зависимостей гравитационных коэффициентов определяют критические размеры частиц порошковых компонентов, удерживающихся на поверхностях других частиц, при действии на них только сил тяжести. Для этого достаточно продолжить линии соответствующих зависимостей до пересечения с линией соответствующей значению Ku = 1.
Максимальными эквивалентными диаметрами частиц порошков бронзы, железа, меди и никеля, способных удерживаться на поверхностях частиц фторопласта, будут dэ = 12÷13 мкм.
56
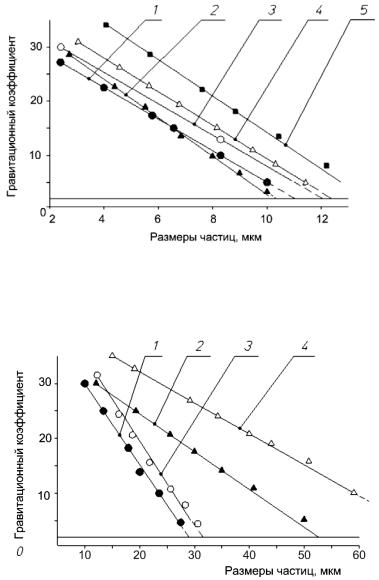
Рис. 4.2. Зависимость гравитационного коэффициента от размеров частиц бронзы:
1 – бронза, плоскость; 2 – фторопласт, плоскость; 3 – бронза, поверхность частиц; 4 – фторопласт, поверхность частиц; 5 – фторопласт, поверхность частиц после смешивания
Рис. 4.3. Зависимость гравитационного коэффициента от размеров частиц фторопласта:
1 – фторопласт, плоскость; 2 – бронза, плоскость; 3 – фторопласт, поверхность частиц; 4 – бронза, поверхность частиц
57
Для частиц фторопласта, способных удерживаться на поверхностях металлических порошков, наибольшими эквивалентными диаметрами являются dэ = 55÷60 мкм.
С учетом действия сил на частицы при смешивании сухих порошковых компонентов в механических смесителях критические размеры частиц определены по зависимости (2.7) и экспериментальным значениям удельных сил адгезии частиц (табл. 4.1; 4.2).
Размеры частиц dэ = 72÷95 мкм фторопласта и dэ = 12÷15 мкм для металлических порошков (медь, бронза, железо, никель) являются критическими. Агрегаты частиц с оболочкой из частиц порошков основы материала могут формироваться при применении порошков основы с размерами частиц, меньшими критических значений.
4.2. Влияние размеров частиц и содержания порошковых компонентов на формирование структуры материалов
4.2.1. Методика исследований формирования структуры материалов
Структура материалов, содержащих фторопласт, предопределяет их тип, физико-механические и химические свойства.
Формирование структуры материалов каркасного типа при формовании из смесей компонентов рассматривают как процесс уплотнения пористого порошкового тела, поры которых заполнены фторопластом.
Значительную часть свойств пористых тел выражают через два основных параметра – критическое сечение и относительную плотность [11].
При уплотнении пористого порошкового тела меняется степень его консолидации и все его характеристики и свойства. При уплотнении материалов из смесей, содержащих фторопласт, большинство свойств будет зависеть от степени консолидации основы материала и взаимодействия с другими компонентами.
Процесс структурообразования в зависимости от размера частиц порошковых компонентов и их содержания в смесях характеризу-
58
ют направлением изменения физико-механических характеристик при одинаковых относительных плотностях по материаламосновам при изменении содержания фторопласта.
Относительная плотность υ пористого порошкового тела определяется по известной зависимости
υ = γп/ γ′к , |
(4.11) |
где γп – плотность пористого тела, кг·мֿ³; |
γ′к – плотность ком- |
пактного материала пористого тела, кг·мֿ³.
Относительная плотность по материалу-основе определяется из зависимости
υм = (γαо/γк) 10-2, |
(4.12) |
где γ – плотность прессовок, кг мֿ³; αо – содержание материалаосновы в смеси в процентах по массе; γк – плотность компактного материала-основы, кг мֿ³.
Увеличение содержания фторопласта при одинаковых относительных плотностях по металлической фазе в прессовках вызывает уменьшение или увеличение удельного электрического сопротивления, предела прочности при срезе и других физико-механических характеристик в зависимости от размеров частиц порошковых компонентов.
Процесс формирования металлического каркаса при уплотнении смесей наиболее целесообразно характеризовать изменением удельного электрического сопротивления, так как при этом отпадает необходимость учитывать влияние фторопласта.
В прессовках смесей из мелкого металлического и крупного фторопластового порошков создаются наивыгоднейшие условия для формирования металлического каркаса и увеличение содержания фторопласта при одинаковых относительных плотностях по металлической фазе вследствие увеличения гидростатического давления в порах при уплотнении будут способствовать уплотнению металлического порошка, увеличению степени консолидации основы (каркаса) в определенных пределах содержания фторопласта, что уменьшит удельное электрическое сопротивление. Таким образом, по изменению удельного электрического сопротивления косвенно оцениваем уплотнение каркаса по металлической фазе.
59
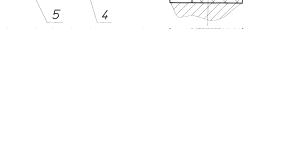
Наоборот, в прессовках смесей из крупного металлического порошка и мелкого порошка фторопласта увеличение содержания последнего из-за увеличения толщины фторопластовых оболочек агрегатов частиц будет снижать степень консолидации металлической фазы и увеличивать электрическое сопротивление.
Процесс структурообразования при формировании смесей предопределяется на стадии смешивания порошковых компонентов. Образование агрегатов частиц (гранул) на стадии смешивания легко наблюдать по изменению цвета смесей и рассмотрением отдельных агрегатов на микроскопе.
Для исследования готовили двухкомпонентные смеси из порошков бронзы, никеля с размерами частиц 1÷10 мкм и фторопласта с размерами частиц 30÷160 мкм и из порошков бронзы, никеля с размерами 30÷160 мкм и фторопласта с размерами частиц 1÷15 мкм. Содержание фторопласта в смесях изменяли от 20 до 80 % по объему. Смешивание производили в механическом смесителе по методу пересыпания.
Смеси прессовали в токонепроводящей матрице при давлениях 0,5÷120 МПа с одновременным замером электрического сопротивления по схеме, показанной на рис. 4.4, и определением высоты прессовок. По массе и объему образцов определяли плотности прессовок.
Рис. 4.4. Схема измерения электросопротивления:
1 – матрица; 2, 3 – пуансоны; 4 – мост сопротивления Р333; 5 – источник питания постоянного тока Б5-44.
При горячем прессовании повышалась степень консолидации материала основы в результате спекания частиц. Степень консолидации зависела от температуры, времени и давления горячего прес-
60