
- •Foreword
- •1. General Introduction
- •2. Processes and Techniques for Droplet Generation
- •2.1.0 Atomization of Normal Liquids
- •2.1.1 Pressure Jet Atomization
- •2.1.3 Fan Spray Atomization
- •2.1.4 Two-Fluid Atomization
- •2.1.5 Rotary Atomization
- •2.1.6 Effervescent Atomization
- •2.1.7 Electrostatic Atomization
- •2.1.8 Vibration Atomization
- •2.1.9 Whistle Atomization
- •2.1.10 Vaporization-Condensation Technique
- •2.1.11 Other Atomization Methods
- •2.2.0 Atomization of Melts
- •2.2.1 Gas Atomization
- •2.2.2 Water Atomization
- •2.2.3 Oil Atomization
- •2.2.4 Vacuum Atomization
- •2.2.5 Rotating Electrode Atomization
- •2.2.7 Electron Beam Rotating Disk Atomization
- •2.2.9 Centrifugal Shot Casting Atomization
- •2.2.10 Centrifugal Impact Atomization
- •2.2.11 Spinning Cup Atomization
- •2.2.12 Laser Spin Atomization
- •2.2.14 Vibrating Electrode Atomization
- •2.2.15 Ultrasonic Atomization
- •2.2.16 Steam Atomization
- •2.2.17 Other Atomization Methods
- •3.1.0 Droplet Formation
- •3.1.1 Droplet Formation in Atomization of Normal Liquids
- •3.1.2 Secondary Atomization
- •3.1.3 Droplet Formation in Atomization of Melts
- •3.2.0 Droplet Deformation on a Surface
- •3.2.3 Droplet Deformation and Solidification on a Cold Surface
- •3.2.4 Droplet Deformation and Evaporation on a Hot Surface
- •3.2.5 Interaction, Spreading and Splashing of Multiple Droplets on a Surface
- •3.2.6 Sessile Droplet Deformation on a Surface
- •3.2.7 Spreading and Splashing of Droplets into Shallow and Deep Pools
- •4.1.0 Concept and Definitions of Droplet Size Distribution
- •4.2.0 Correlations for Droplet Sizes of Normal Liquids
- •4.2.1 Pressure Jet Atomization
- •4.2.5 Rotary Atomization
- •4.2.6 Effervescent Atomization
- •4.2.7 Electrostatic Atomization
- •4.2.8 Ultrasonic Atomization
- •4.3.0 Correlations for Droplet Sizes of Melts
- •4.3.1 Gas Atomization
- •4.3.2 Water Atomization
- •4.3.3 Centrifugal Atomization
- •4.3.4 Solidification and Spheroidization
- •4.4.0 Correlations for Droplet Deformation Characteristics on a Surface
- •4.4.1 Viscous Dissipation Domain
- •4.4.2 Surface Tension Domain
- •4.4.3 Solidification Domain
- •4.4.4 Partial Solidification Prior to Impact
- •5.1.0 Energy Requirements and Efficiency
- •5.2.0 Modeling of Droplet Processes of Normal Liquids
- •5.2.1 Theoretical Analyses and Modeling of Liquid Jet and Sheet Breakup
- •5.2.2 Modeling of Droplet Formation, Breakup, Collision and Coalescence in Sprays
- •5.2.3 Theories and Analyses of Spray Structures and Flow Regimes
- •5.2.5 Modeling of Multiphase Flows and Heat and Mass Transfer in Sprays
- •5.3.0 Modeling of Droplet Processes of Melts
- •5.3.4 Modeling of Multiphase Flows and Heat Transfer in Sprays
- •5.4.0 Modeling of Droplet Deformation on a Surface
- •5.4.1 Modeling of Deformation of a Single Droplet on a Flat Surface
- •5.4.2 Modeling of Droplet Deformation and Solidification on a Cold Surface
- •6. Measurement Techniques for Droplet Properties and Intelligent Control of Droplet Processes
- •6.1.0 Measurement Techniques for Droplet Size
- •6.1.1 Mechanical Methods
- •6.1.2 Electrical Methods
- •6.1.3 Optical Methods
- •6.1.4 Other Methods
- •6.2.0 Measurement Techniques for Droplet Velocity
- •6.3.0 Measurement Techniques for Droplet Number Density
- •6.4.0 Measurement Techniques for Droplet Temperature
- •6.5.0 Measurement Techniques for Droplet Deformation on a Surface
- •6.6.0 Intelligent Control of Droplet Processes
- •Index
446 Science and Engineering of Droplets
Hofmeister et al.[410] used two high-speed thermal imaging systems to record spatial and temporal temperature distributions at the splat-substrate interface and to observe the droplet spreading during impact and solidification on a quartz plate. In their experimental setup, a surface-aluminized mirror was positioned below the quartz plate to allow viewing of the splat-substrate interface through an 8" view port at the end of a chamber. A Kodak Ektapro scanning array camera was operated at 40500 frames/s and a HSDA96 parallel tapped thermal imaging system was operated at 250000 frames/s. The two thermal imaging systems were positioned to simultaneously view the splat-substrate interface via a beam splitting cube. The HSDA96 was fitted with a narrow bandpass optical filter centered at 950 nm, and both instruments were calibrated for temperature measurement using a standard tungsten strip lamp. The Ektapro has a higher spatial resolution, 4096 pixels as compared to 96 active pixels in the HSDA96. However, the response time of the HSDA96 (less than one µs) is two orders of magnitude shorter than the Ektapro (about 75 µs). Thus, the two systems complement each other and together provide the necessary bandwidth and spatial resolution to capture the details of droplet spreading and solidification on a substrate surface. The imaging experiments provided detailed information on the deformation, heat transfer and solidification during droplet impingement on a surface.
6.6.0INTELLIGENT CONTROL OF DROPLET PROCESSES
Over the past decade, instrumentation has undergone substantial developments in the areas of optics, electronics and data processing software. These have led to improvements in the reliability, accuracy and ease of use of associated instruments. Particularly, the introduction of fiber optics has allowed a greater degree of flexibility in application areas. These include, for example, measurement of oil droplet dispersion in the ocean, on-line monitoring of
Measurement Techniques for Droplet Properties 447
polymer bead formation, in-flight measurement of cloud droplets pertinent to aircraft icing, measurements of droplets in rocket and automotive injectors, investigation of gas turbine fuel spray interactions with turbulent flows, paint sprays, and molten metal sprays. The optical probes employed in these applications have been designed in a variety of configurations. For example, very small probes of only 15 mm in diameter have been developed for industrial applications, and very large probes with optics of 500 mm in diameter for large-scale wind tunnel testing.
Techniques are being developed to directly measure single droplet trajectories in the Lagrangian reference frame and to provide information on their temporal variations. These have stimulated new developments in instrumentation, including instantaneous planar imaging velocimetry, and digital image analysis of high-speed photography, cinematography, videography and holography. As new experimental data are becoming available for droplet trajectories and their temporal variations in the Lagrangian reference frame, droplet processes will benefit from improving spray diagnostic techniques that will allow measurements of the joint distribution functions of droplet sizes, 3-D components of velocities, temperatures and evaporation rates.
In droplet processes, particularly spray atomization and spray forming processes, a major obstacle to achieving consistently highquality spray products has been the limited ability to accurately monitor and effectively control various operation parameters on line and in real time. For example, in monitoring and controlling spray processes, sensors used to monitor spray angle, penetration, shape and optical density may relay signals to control systems for actuation of changes in liquid and gas supply pressures and flow rates. In an effort to improve the quality of final products, various diagnostic techniques have been evaluated for monitoring spray process parameters, such as droplet size, velocity, concentration, temperature, and size distribution. Sensing techniques and instruments evaluated[713][714] include high-speed cinematography, off-axis holographic cinematography, infrared thermal imaging, PCSV-P probe, phase-Doppler particle analyzer, EPMP monitor, and other intelligent
448 Science and Engineering of Droplets
sensors.[327][715] Some methods have capabilities to provide on-line feedback of the spray parameters. Generally, laser diffraction, phase-Doppler and digital imaging instruments may be simplified for on-line monitoring of droplet size and velocity histograms and distributions. Sensors and techniques used to monitor the process parameters during spray forming have been reviewed and discerned for their usefulness in making spray atomization and deposition a more controllable process.[713]
Methods of near-field, midfield and ensemble (global) imaging and real-time visualization have been developed for monitoring gas atomization of liquid metals.[327] The primary process sensors and monitors used include high-speed video and infrared imaging systems. The process monitors allowed continuous and detailed observations of the atomization process and enabled measurements of the key parameters necessary for adequate control and optimization of the process. The sensors provided the operators with real-time information on the temperature of nozzle tip, visual characteristics of atomization plume, and gas and metal flow rates. The images can be displayed in real time, offering the potential for more responsive process control.
A number of intelligent sensors have been used for on-line monitoring of gas atomization of liquid metals.[715] These on-line sensing techniques enabled measurements of liquid metal flow rate, on-line droplet size and size distribution, as well as video imaging of spray plume. The near-field measurements provided detailed information on atomization characteristics for better understanding of the atomization process. The downstream measurements along with the near-field measurements demonstrated the applicability of on-line process monitoring and control to spray atomization and spray deposition. It was also showed that, with the diagnostic tools currently available for use in industrial gas atomization, significantly improved control over the atomization operation is achievable by implementing on-line measurements and process-product know-how.
An intelligent process diagnostics and control system has been integrated for supersonic inert gas metal atomization (SIGMA) at the National Institute of Standards and Technology (NIST) in the
Measurement Techniques for Droplet Properties 449
US.[163][676][677] An expert system based on the principle of hierarchical control was developed that features a generic structure allowing easy adaption to other processes. As schematically depicted in Fig. 6.10,[163] the diagnostics and control system consists of a product sensor (particle sizer), actuators, process sensors (temperature, pressure, etc.), a low-level (local) controller, a high-level (learning) controller, and an operator interface. The high-level controller refers to a physically remote microprocessor with which an operator can interact via the keyboard and graphics monitor of the operator interface. This controller has access to a “world model,” i.e., a database describing the performance characteristics of the atomizer as provided by knowledgeable experts and by continuous updates during atomization operations. The local low-level controller is a “stand-alone” device capable of maintaining status quo during an atomization operation and providing necessary process feedback. The product sensor is an in-situ particle sizer that is connected to the high-level controller directly, bypassing the local low-level controller, so as to improve response of the control system to changes in particle size distribution. Some fundamental issues in gas atomization that relate to process control have been studied, including fluid dynamics, process parameterization and particle size sensing. The high-level controller incorporated the results of these studies into a multiple level I/O command interface for intelligent decision-mak- ing and on-line control.
In summary, it has become increasingly evident that further technological developments, particularly in such challenging areas as real-time, on-line control, require a detailed understanding and effective control of the fundamental phenomena associated with droplet processes. The ultimate realization of the real-time process control relies on the development of robust process models and fast solution techniques and the implementation of the models on a computer coupled with sensing and control systems. Faster, more accurate, reliable and affordable systems integrating process models, monitoring sensors and control units are required to achieve final products of consistently high qualities and to optimize droplet processes.
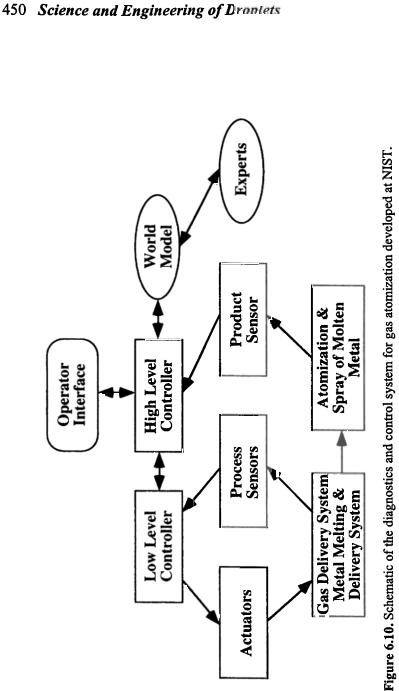
450 |
Science |
and Engineering |
of D |
.
,
rIJ |
rIJ |
rIJ |
"" |
~ |
Q |
r.J |
(/1 |
Q |
c |
"" |
~ |
~r.i) |
|
~
.s
=
-= Cj
<
~~
=-
~ ~
;~]
~c.,.~
.~ ~~
Sfe
<~
-!~E
~~
CIJCrlJ
0. ~
t";:=CIJ
OJOJ
...~ ~ o.~ ~
--OJ |
= ... |
OJ |
|
Q |
O. |
OJ~
~~Q
~
E--' 00
Z
~
'0
-g.
~
>
~
'0
5
.;j
~
.§
~
"'
~
01)
...
c.9
5
~
"'
-
0
~
o u
]~
"' u
~
o
s=o
~
:e
~
-=
"'0 u
.;j
~
s
~
-5 00
=
..,;
..c
~
=
~
~