
- •Foreword
- •1. General Introduction
- •2. Processes and Techniques for Droplet Generation
- •2.1.0 Atomization of Normal Liquids
- •2.1.1 Pressure Jet Atomization
- •2.1.3 Fan Spray Atomization
- •2.1.4 Two-Fluid Atomization
- •2.1.5 Rotary Atomization
- •2.1.6 Effervescent Atomization
- •2.1.7 Electrostatic Atomization
- •2.1.8 Vibration Atomization
- •2.1.9 Whistle Atomization
- •2.1.10 Vaporization-Condensation Technique
- •2.1.11 Other Atomization Methods
- •2.2.0 Atomization of Melts
- •2.2.1 Gas Atomization
- •2.2.2 Water Atomization
- •2.2.3 Oil Atomization
- •2.2.4 Vacuum Atomization
- •2.2.5 Rotating Electrode Atomization
- •2.2.7 Electron Beam Rotating Disk Atomization
- •2.2.9 Centrifugal Shot Casting Atomization
- •2.2.10 Centrifugal Impact Atomization
- •2.2.11 Spinning Cup Atomization
- •2.2.12 Laser Spin Atomization
- •2.2.14 Vibrating Electrode Atomization
- •2.2.15 Ultrasonic Atomization
- •2.2.16 Steam Atomization
- •2.2.17 Other Atomization Methods
- •3.1.0 Droplet Formation
- •3.1.1 Droplet Formation in Atomization of Normal Liquids
- •3.1.2 Secondary Atomization
- •3.1.3 Droplet Formation in Atomization of Melts
- •3.2.0 Droplet Deformation on a Surface
- •3.2.3 Droplet Deformation and Solidification on a Cold Surface
- •3.2.4 Droplet Deformation and Evaporation on a Hot Surface
- •3.2.5 Interaction, Spreading and Splashing of Multiple Droplets on a Surface
- •3.2.6 Sessile Droplet Deformation on a Surface
- •3.2.7 Spreading and Splashing of Droplets into Shallow and Deep Pools
- •4.1.0 Concept and Definitions of Droplet Size Distribution
- •4.2.0 Correlations for Droplet Sizes of Normal Liquids
- •4.2.1 Pressure Jet Atomization
- •4.2.5 Rotary Atomization
- •4.2.6 Effervescent Atomization
- •4.2.7 Electrostatic Atomization
- •4.2.8 Ultrasonic Atomization
- •4.3.0 Correlations for Droplet Sizes of Melts
- •4.3.1 Gas Atomization
- •4.3.2 Water Atomization
- •4.3.3 Centrifugal Atomization
- •4.3.4 Solidification and Spheroidization
- •4.4.0 Correlations for Droplet Deformation Characteristics on a Surface
- •4.4.1 Viscous Dissipation Domain
- •4.4.2 Surface Tension Domain
- •4.4.3 Solidification Domain
- •4.4.4 Partial Solidification Prior to Impact
- •5.1.0 Energy Requirements and Efficiency
- •5.2.0 Modeling of Droplet Processes of Normal Liquids
- •5.2.1 Theoretical Analyses and Modeling of Liquid Jet and Sheet Breakup
- •5.2.2 Modeling of Droplet Formation, Breakup, Collision and Coalescence in Sprays
- •5.2.3 Theories and Analyses of Spray Structures and Flow Regimes
- •5.2.5 Modeling of Multiphase Flows and Heat and Mass Transfer in Sprays
- •5.3.0 Modeling of Droplet Processes of Melts
- •5.3.4 Modeling of Multiphase Flows and Heat Transfer in Sprays
- •5.4.0 Modeling of Droplet Deformation on a Surface
- •5.4.1 Modeling of Deformation of a Single Droplet on a Flat Surface
- •5.4.2 Modeling of Droplet Deformation and Solidification on a Cold Surface
- •6. Measurement Techniques for Droplet Properties and Intelligent Control of Droplet Processes
- •6.1.0 Measurement Techniques for Droplet Size
- •6.1.1 Mechanical Methods
- •6.1.2 Electrical Methods
- •6.1.3 Optical Methods
- •6.1.4 Other Methods
- •6.2.0 Measurement Techniques for Droplet Velocity
- •6.3.0 Measurement Techniques for Droplet Number Density
- •6.4.0 Measurement Techniques for Droplet Temperature
- •6.5.0 Measurement Techniques for Droplet Deformation on a Surface
- •6.6.0 Intelligent Control of Droplet Processes
- •Index
206Science and Engineering of Droplets
3.2.3Droplet Deformation and Solidification on a Cold Surface
In many droplet impact processes, heat transfer and phase change (for example, solidification or evaporation) may take place simultaneously. In these circumstances, droplet temperature and surface temperature, in addition to initial droplet diameter, velocity, and properties, may significantly influence the final splat diameter and the deformation time because solidification may limit the extent of droplet spreading.[371] The actual spreading time may range from milliseconds down to microseconds, depending on droplet diameter, impact velocity, surface conditions, and liquid properties. For large droplets at low impact velocities, spreading and solidification may take place under similar time scales so that the onset of solidification may significantly interfere with the spreading process.[371] For small droplets at high impact velocities, spreading is essentially completed before the commencement of solidification. In the initial stage, droplet spreading is controlled by fluid dynamics, primarily by the rate at which the kinetic energy of the impacting droplet is consumed to overcome the viscous forces. After a droplet has spread to a certain length, perhaps D/D0 = 2 to 3, heat transfer may take over, and the subsequent spreading is limited by the onset of solidification.
In case of droplet solidification during spreading, an increase in initial droplet velocity leads to a rapid increase in the final splat diameter and a decrease in the total solidification time (Fig. 3.22). Note that in this figure, the actual time step is the same for all three cases. However, with increasing droplet temperature and/or surface temperature, both the final splat diameter and the total solidification time increase.[52][388] Experimental studies on thermal spray droplet impact showed that the solidification time is typically two orders of magnitude longer than the flow time.[390] Even on a flat, dry surface, droplet splashing may occur if the surface temperature is below the melting temperature of the droplet.[46][52] This is due to the solidification of the lowest layer of the droplet first in contact with the cold surface as it flows radially, while the layers above the solid-liquid
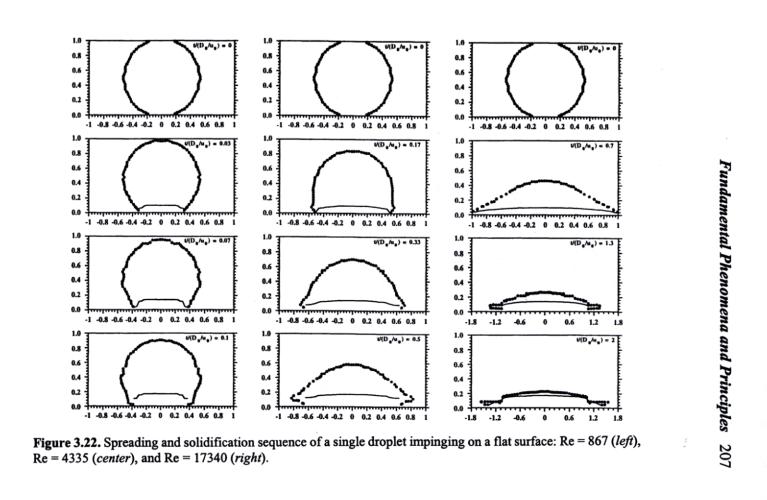
208 Science and Engineering of Droplets
interface separates from the surface and ejects away as a result of the unique velocity distribution of the liquid at the leading edge.[46][52][144][395] A higher surface temperature, and/or droplet temperature may reduce droplet splashing due to a lower solidification rate.[46] However, there exists generally an optimum combination of deformation rates and solidification rates, or in other words, impact kinetic energy and thermal energy, in terms of the minimization of droplet splashing.[52][388] If the initial droplet velocity and/or the surface temperature is sufficiently high so that extensive deformation occurs prior to significant solidification, the separation does not take place or occurs at later time. If the initial droplet velocity and/or the surface temperature is sufficiently low so that significant solidification is completed prior to extensive deformation, the contact and eventual adhesion of the splat with the surface may be worse due to less flattening. At a lower surface temperature, the separation occurs earlier. Splashing and breakup always take place on a rough surface regardless of surface temperature.[390]
A number of researchers[390][402]-[406] have conducted experimental studies on the splat formation from a metal droplet impinging on a cold surface. Extensive photographic presentations of spreading, breakup, and solidification processes of liquid metal droplets on a cold surface have been given by Houben,[407] along with detailed descriptions of collision model, splat morphology, and influences of droplet size, impact velocity, temperature, and surface temperature. These studies suggested that droplet spreading, breakup and solidification may take place in many different modes, as depicted in Fig. 3.23. The final splat geometry may be either in a regularly-shaped disk pattern or in an irregularly-shaped platelet pattern, depending on droplet impact properties (size, velocity, angle, temperature, solid fraction), substrate surface properties (temperature, roughness, wetting), and their thermophysical properties (thermal conductivity, thermal capacity, density, surface tension, droplet viscosity, contact resistance). Star-shaped patterns (with corona) may result from splashing upon impact,[402] and may always occur on rough substrate surface regardless of substrate temperature.[390] On the other hand,
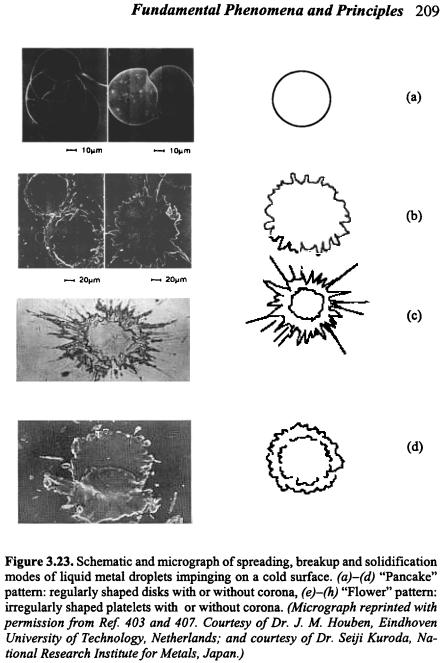
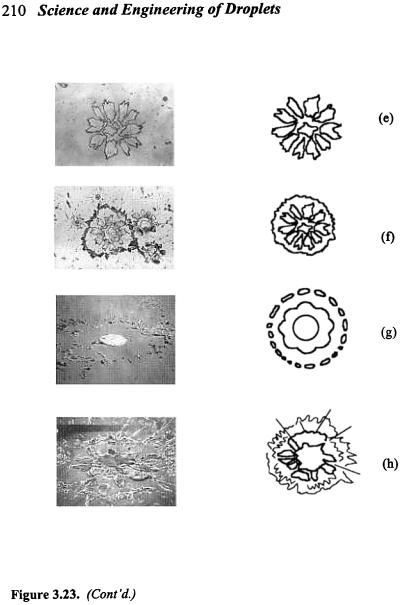
Fundamental Phenomena and Principles 211
decreasing substrate temperature may change the final splat shape from a regular disk to an irregular star. Sobolev et al.[408] identified a transition temperature that determines the splat morphology on a smooth substrate surface. At a substrate temperature below this transition temperature, droplet splashing occurs at the periphery leading to a star-shaped splat, while at a substrate temperature above this transition temperature, a regular disc-shaped splat forms. Generally, smaller droplet sizes, higher droplet velocities, higher droplet temperatures, colder and rougher substrate surfaces, and/or reduced wetting may lead to star-shaped patterns, while regularly-shaped patterns may result from larger droplet sizes, lower droplet velocities, lower droplet temperatures, and/or heated and smoother substrate.[46][390][402] Solidification, surface roughness, and wetting characteristics are among the most important factors influencing splashing and breakup of a droplet impinging on a cold surface.
It should be noted that the droplet spreading and solidification modes presented in Fig. 3.23 are more relevant to the conditions of high velocity and low thermal conditioning typical of thermal spray processes. For the conditions of low velocity and high thermal conditioning that characterize spray deposition processes, Matson et al.[409] presented an illustration of droplet impingement topology and classified droplet deposition and solidification behavior into seven modes (Fig. 3.24). The first and second modes involve rebound of a droplet off a fully solid and fully liquid substrate surface, respectively. The third mode is a thin pancake with lateral ejection of liquid. The fourth mode is a thick pancake or burst with surface oscillation or axial ejection of liquid. The fifth and sixth modes are spherical or semispherical pancake and bilaminate resulted from droplet spreading with subsequent surface recoil due to remelting, partial rebound, or bending. The seventh mode is a rigid pancake formed by surface motion or marginal spreading of a semi-solid droplet. These researchers suggested use of three additional dimensionless numbers, i.e., Stefan number (St), Impact number (I), and Freezing number
212 Science and Engineering of Droplets
(F), in addition to the Reynolds and Weber numbers, to fully describe a droplet spreading and solidification process upon impact on a substrate. They introduced two new dimensionless numbers, defined as:
Eq. (45) |
I = |
πρ L D02 u03 |
|
|
|
|
|
|
||
12 Ac h(TL |
− Tw ) |
|
|
|
|
|
||||
|
|
|
|
|
|
|
||||
and |
|
|
|
|
|
|
|
|
|
|
|
F = [ Hm (1− fs ) |
|
|
T ] |
π u |
0 |
ρ |
D2 |
||
Eq. (46) |
+ c pL |
|
|
L 0 |
||||||
6Ac h(TL − Tw ) |
||||||||||
|
|
|
|
|
|
where Ac is the contact area at the interface between a droplet and substrate, Ac = π /8 [1 + (Ds/D0)2] D02 formulated as a linear average of initial and final contact areas; h is the interface heat transfer coefficient; TL and Tw are the initial droplet temperature and initial substrate temperature, respectively; fs is the fraction solid of a droplet prior to impact; and T is the difference between initial droplet temperature and melting (liquidus) temperature. The Impact number is seen to increase with increasing impact velocity and temperature difference across the interface. It is derived conceptually from expressions describing the kinetic energy transfer rate and the heat extraction rate through the interface. The Freezing number compares numerically the solidification time to the impact time. A small Freezing number results from a low velocity, gentle impact process, or poor interface heat contact. The most critical factors in using these new dimensionless numbers are to determine the heat transfer coefficient and the contact area between an impacting droplet and substrate. This requires the information of contact resistance, droplet deformation and final splat size.
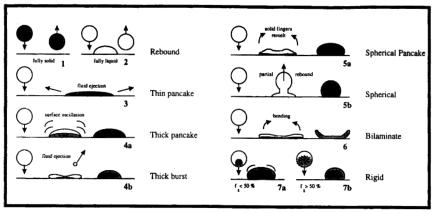
Fundamental Phenomena and Principles 213
Figure 3.24. Classification of droplet impingement topology. (Reprinted with permission from Ref. 409.)
Under the conditions of high velocity and low thermal conditioning which characterize thermal spray (detonation coating) processes, evaluation of a correlation based on the Weber number is of reduced merit with a lower significance of surface-related phenomena relative to viscous effects. Hence, in designing a topology to investigate the thermal spray processes, it is appropriate to plot the Impact number as a function of the Reynolds number to identify domains of common deposition tendency. On the contrary, under the conditions of low velocity and high thermal conditioning which characterize spray deposition processes, viscous effects are, while still of importance, secondary effects in predicting impact behavior, as indicated by the analysis of the asymptotic behavior of the Reynolds number during spreading. Thus, in designing a topology to investigate spray deposition processes, it is more appropriate to plot the Freezing number as a function of the Weber number to identify domains of common deposition tendency, as illustrated in the impingement map (Fig. 3.25). At moderate impact velocities and low
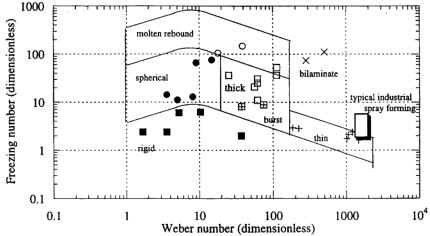
214 Science and Engineering of Droplets
fraction solid, a combined approach may be more appropriate based on the formulation of the third new, yet dependent, dimensionless number, defined as a quotient of the Impact number and the Freezing number:
Eq. (47) |
N |
Q |
= u 2 |
/ 2[ H |
m |
(1 − f |
s |
) + c |
pL |
T ] |
|
|
0 |
|
|
|
|
This number is conceptually an energy ratio, but independent of the interface heat extraction rate and thus the contact area. Since the interface heat transfer is assumed to control the solidification process of an impacting droplet, the choice of a dimensionless number should involve an evaluation of the influence exerted by this key factor. Therefore, the use of this newly defined dimensionless number is limited to an initial decision on which of the Impact number and the Freezing number is most appropriate for the application to a given material system at a know impact velocity.
Figure 3.25. Impingement map (Reprinted with permission from Ref. 409.)
Fundamental Phenomena and Principles 215
The occurrence of each deformation mode may be then correlated to a specific combination of the values of the Weber number and the Freezing number, as depicted in Fig. 3.25. The thin pancake mode is characterized by large values of the Weber number (200 < We < 1000), allowing for a large spreading, and extremely fast solidification with F ≈ 2. The liquid freezes as soon as it touches the substrate. Continuity and conservation of momentum require that the remaining liquid flow radially outward in the form of a thin sheet jet. This sheet freezes as soon as it contacts substrate, leading to the formation of a pancake with a low aspect ratio. In this case, solidification is so fast that droplet spreading may be largely retarded. Instabilities may cause the thin sheet jet to break up, leaving behind fine projections in a starburst pattern. The thick pancake mode represents the case where the heat extraction rate is sufficiently high to freeze the bottom part of a droplet while its upper part still moves and oscillates due to the conversion of kinetic energy to surface energy. This case corresponds to the conditions 1 < Ds/D0 < 3, We ≈ 80 and F ≈ 20. Bursting may occur at high velocities in the late stage of deformation when ejection is facilitated by a high impact kinetic energy. The spherical pancake mode is characterized by small values of the Weber number (We < 20), large F values (10 < F < 100), and a fully liquid droplet at impact. At a smaller F value (~10), a droplet may solidify into a semi-spherical pancake. Fingers stretching outward from the base of the semi-spherical pancake may lift up, fold inward, then remelt and finally retract into the bulk. At a larger F value (~100), the heat extraction process is very slow so that a droplet may take its equilibrium shape, i.e., spherical shape. For even larger F values (F > 100), a droplet does not freeze and is ejected upward as rebound. The bilaminate mode is characterized by a large We value (~300) and a large F value (~100). The base of a droplet freezes quickly and liquid floats on the top surface of the splat that subsequently solidifies at a slower rate controlled by the interface heat extraction rate. The upper part of the liquid region shrinks during solidification while the already solidified lower part is constrained due to the attachment to the substrate surface, leading to
216 Science and Engineering of Droplets
bending of the edges. The rigid pancake mode is encountered when a droplet solidifies after only minimum deformation with possible slight surface oscillations. This case corresponds to a small F value (F < 10), and a large fraction solid at impact. As the fraction solid increases, droplet deformation becomes more difficult as the mushy zone gets denser and stronger. During impact, the solid outer surface cracks open and the semi-solid interior flows out leaving behind a hollow shell (a half-moon shaped inclusion in the final splat). At a very large fraction solid, a droplet virtually does not deform, giving rise to a low heat extraction rate. Overall, these deformation modes may be concentrated in the impingement map and the relationship between each regime is coherent with the transition from one regime to the next following the anticipated trajectory. For example, a spherical pancake becomes a thick pancake by increasing the Weber number; A bilaminate mode becomes a thin pancake when reducing F. The transition is, however, not strictly bounded due to the many approximations made in defining the quantities such as contact area, heat transfer coefficient, and thermal physical properties. The impingement map may be useful for a wide range of engineering design applications, particularly to the investigation of porosity and oxidation level in sprayed preforms. The map presents a graphical characterization of desired operation regimes and provides guidelines for manipulating process parameters to get desired spray conditions, controlling the morphology of sprayed products, and avoiding regimes which promote poor product quality.
In addition to the deformation modes described above, there are some other modes of practical interest, for example, the cyclic spreading, recoiling, and oscillation mode typical of solder jetting process.[50] This mode leads to a final splat shape of multiple surface ripples at low substrate temperatures and hemispherical shape without surface ripples at high substrate temperatures.
Hofmeister et al.[410] employed two high-speed thermal imaging systems to record spatial and temporal temperature distributions at the splat-substrate interface, and to observe droplet spreading during impact and solidification on a quartz plate. They observed