
- •Foreword
- •1. General Introduction
- •2. Processes and Techniques for Droplet Generation
- •2.1.0 Atomization of Normal Liquids
- •2.1.1 Pressure Jet Atomization
- •2.1.3 Fan Spray Atomization
- •2.1.4 Two-Fluid Atomization
- •2.1.5 Rotary Atomization
- •2.1.6 Effervescent Atomization
- •2.1.7 Electrostatic Atomization
- •2.1.8 Vibration Atomization
- •2.1.9 Whistle Atomization
- •2.1.10 Vaporization-Condensation Technique
- •2.1.11 Other Atomization Methods
- •2.2.0 Atomization of Melts
- •2.2.1 Gas Atomization
- •2.2.2 Water Atomization
- •2.2.3 Oil Atomization
- •2.2.4 Vacuum Atomization
- •2.2.5 Rotating Electrode Atomization
- •2.2.7 Electron Beam Rotating Disk Atomization
- •2.2.9 Centrifugal Shot Casting Atomization
- •2.2.10 Centrifugal Impact Atomization
- •2.2.11 Spinning Cup Atomization
- •2.2.12 Laser Spin Atomization
- •2.2.14 Vibrating Electrode Atomization
- •2.2.15 Ultrasonic Atomization
- •2.2.16 Steam Atomization
- •2.2.17 Other Atomization Methods
- •3.1.0 Droplet Formation
- •3.1.1 Droplet Formation in Atomization of Normal Liquids
- •3.1.2 Secondary Atomization
- •3.1.3 Droplet Formation in Atomization of Melts
- •3.2.0 Droplet Deformation on a Surface
- •3.2.3 Droplet Deformation and Solidification on a Cold Surface
- •3.2.4 Droplet Deformation and Evaporation on a Hot Surface
- •3.2.5 Interaction, Spreading and Splashing of Multiple Droplets on a Surface
- •3.2.6 Sessile Droplet Deformation on a Surface
- •3.2.7 Spreading and Splashing of Droplets into Shallow and Deep Pools
- •4.1.0 Concept and Definitions of Droplet Size Distribution
- •4.2.0 Correlations for Droplet Sizes of Normal Liquids
- •4.2.1 Pressure Jet Atomization
- •4.2.5 Rotary Atomization
- •4.2.6 Effervescent Atomization
- •4.2.7 Electrostatic Atomization
- •4.2.8 Ultrasonic Atomization
- •4.3.0 Correlations for Droplet Sizes of Melts
- •4.3.1 Gas Atomization
- •4.3.2 Water Atomization
- •4.3.3 Centrifugal Atomization
- •4.3.4 Solidification and Spheroidization
- •4.4.0 Correlations for Droplet Deformation Characteristics on a Surface
- •4.4.1 Viscous Dissipation Domain
- •4.4.2 Surface Tension Domain
- •4.4.3 Solidification Domain
- •4.4.4 Partial Solidification Prior to Impact
- •5.1.0 Energy Requirements and Efficiency
- •5.2.0 Modeling of Droplet Processes of Normal Liquids
- •5.2.1 Theoretical Analyses and Modeling of Liquid Jet and Sheet Breakup
- •5.2.2 Modeling of Droplet Formation, Breakup, Collision and Coalescence in Sprays
- •5.2.3 Theories and Analyses of Spray Structures and Flow Regimes
- •5.2.5 Modeling of Multiphase Flows and Heat and Mass Transfer in Sprays
- •5.3.0 Modeling of Droplet Processes of Melts
- •5.3.4 Modeling of Multiphase Flows and Heat Transfer in Sprays
- •5.4.0 Modeling of Droplet Deformation on a Surface
- •5.4.1 Modeling of Deformation of a Single Droplet on a Flat Surface
- •5.4.2 Modeling of Droplet Deformation and Solidification on a Cold Surface
- •6. Measurement Techniques for Droplet Properties and Intelligent Control of Droplet Processes
- •6.1.0 Measurement Techniques for Droplet Size
- •6.1.1 Mechanical Methods
- •6.1.2 Electrical Methods
- •6.1.3 Optical Methods
- •6.1.4 Other Methods
- •6.2.0 Measurement Techniques for Droplet Velocity
- •6.3.0 Measurement Techniques for Droplet Number Density
- •6.4.0 Measurement Techniques for Droplet Temperature
- •6.5.0 Measurement Techniques for Droplet Deformation on a Surface
- •6.6.0 Intelligent Control of Droplet Processes
- •Index
106 Science and Engineering of Droplets
atomization processes. The energy efficiency is typically ~30%, as compared to ~3% and ~4% in gas and water atomization, respectively. The process also shows considerable potential for scale-up and development into a continuous process.
2.2.9Centrifugal Shot Casting Atomization
Centrifugal shot casting (CSC) atomization[189] is conceptually similar to REP in the melting stage and to EBRD in the atomization stage. In this process, a stationary or slowly revolving consumable ingot (an as-cast, rolled or extruded electrode, normally as cathode) is positioned above a water-cooled, rapidly rotating container (normally a copper crucible, as anode) which usually has a skull of the same material as that to be atomized. The electrode may be made from powder compacted materials or from scrap. In an atmosphere of argon or helium, the electrode is melted at its bottom tip by an electronic arc struck between it and the crucible, and dripped into the crucible. By the action of centrifugal forces, the molten metal flows up to the rim of the container and breaks up into droplets while ejecting off the rim. Droplets freeze in flight into powder.
CSC atomization was developed by AEA Harwell Laboratories in the UK in the early 1970’s. Initially, the CSC process was used for the atomization of refractory and oxide materials such as alumina, plutonium oxides, and uranium monocarbide in nuclear fuel applications. Since it is well-suited to the atomization of reactive metals/alloys or those subject to segregation, the CSC process has been applied to a variety of materials such as iron, cobalt, nickel, and titanium alloys and many refractory metals. The process also has potential to scale up to a continuous process.
The pressure of argon gas during atomization ranges from 0.03 to 0.1 MPa. The crucible diameter is 75 mm and its rotating speed is up to 400 radians/s. This combination of conditions gives a production rate up to 1 kg/min.[189] The CSC-atomized particles are either spherical or flaky. Spherical particles usually have smooth
Droplet Generation 107
surfaces with a wide size range (100–1500 µm). The mass median diameter of droplets may be somewhere between 150 and 1000 µm with a standard deviation of about 1.3 to 1.4. From the microstructure of solidified particles, the cooling rates of droplets are estimated to be 2 × 102 to 7 × 104 °C/s, varying with droplet size and operation conditions.
2.2.10 Centrifugal Impact Atomization
In centrifugal impact atomization, a molten metal stream (2–3 mm in diameter) and a volatile liquid coolant are introduced simultaneously to a rapidly rotating impeller. The cone of the impeller disintegrates a small portion of the liquid metal into millimetersized drops and then the vanes strike these drops into small droplets. Most of the liquid metal forms a liquid film on the leading face of the vanes, accelerates to the same speed of the vanes, and then leaves the vanes, disintegrating into small spherical droplets. While the droplets are generated, the coolant vaporizes, taking heat from the droplets and leading to rapid cooling and solidification of the droplets. The majority of the droplets are solidified before contacting the shroud. Some liquid/droplets adhere to the vanes and continue to build up mass until centrifugal forces cause their removal. Detailed mechanisms for the droplet generation and rapid solidification in this process have been discussed in Ref. 190.
The centrifugal impact atomization process was developed in the early 1980’s with patents granted to several researchers in Dow Corning Corporation.[190] In the original design, the atomization facility was capable of processing up to 0.9 kg batches and the propeller rotating speed was up to about 1250 radians/s. The process has been applied to the atomization of silicon, stainless steels (303, 304 and 316), Raney® type alloys (Ni/Al, Cu/Al and Mn/Al), nickel,
copper and a glass forming alloy (Fe81.5B14.5Si3C1). Coolants include water, liquid ammonia, methanol and hexane. The flow rate of
coolant is typically 6 × 10-4 to 2 × 10-3 m3/min. The droplet size ranges from <1 µm to >1 cm. Both fine spherical and coarse
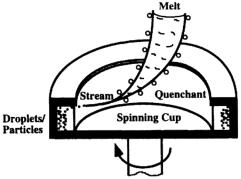
108 Science and Engineering of Droplets
irregular-shaped droplets/particles have been generated with a size range of about <1–150 µm and <1–1000 µm, respectively. The droplet size distribution depends on many variables, but the propeller rotating speed and alloy composition are the most significant. Increasing the propeller rotating speed can reduce the droplet size and the agglomeration of particles. Although this process has not yet been scaled up for important industrial applications, it offers some flexibility in operating with different coolants, and high energy efficiencies and cooling rates.
2.2.11 Spinning Cup Atomization
In single-stage spinning cup atomization (Fig. 2.23), a small stream of molten metal is introduced into a layer of liquid quenchant that is held against the inner wall of a spinning cup. The liquid metal stream is sheared and broken up by the quenchant and the atomized droplets rapidly solidify within the quenchant. The solidified particles are collected on the inner wall of the cup and then separated from the liquid quenchant during post-processing. In two-stage spinning cup atomization, a liquid metal stream is first broken up into droplets (250–1000 µm) or fine ligaments (0.1–0.2 mm in diameter) via gas atomization or conventional centrifugal atomization. It is followed by the impact of the atomized droplets/ligaments onto the spinning cup containing liquid quenchant, leading to further breakup of the droplets/ligaments.
Figure 2.23. Schematic of single-stage spinning cup atomization of melt.
Droplet Generation 109
This process, also termedrapid spinning cup (RSC) process, was invented in the early 1980’s contemporarily by Osaka University in Japan[191] and Battelle’s Columbus Division in the US.[192] Unlike water atomization where water streams or droplets are used to disintegrate a molten metal, a coherent fast-moving liquid layer is used in the RSC process. Liquid quenchants include water, oil, glycerine, and other commercial quenching liquids. The materials atomized with the spinning cup method include a wide variety of metals and alloys such as tin, lead, aluminum alloys, copper alloys, iron alloys (stainless steels and high speed tool steels), zinc alloys and superalloys.[192]
The two-stage spinning cup method exhibits some advantages over gas and water atomization.[192] First, the design of the atomization facility is relatively simple and the dimension of the facility can be small because the atomization, cooling and solidification occur within the spinning cup. Second, the RSC process can generate very fine and clean spherical particles with narrow size range. The mass median size may range from <10 µm to ~300 µm with a standard deviation of 1.5 to 1.7. Third, cooling and solidification rates are high due to the intimate contact of droplets and the liquid quenchant. Fourth, some problems associated with nozzle system and post-processing inherent in gas or water atomization can be avoided in the RSC process. In addition, the process offers a high degree of flexibility in controlling particle characteristics such as shape, size and size distribution by changing process parameters. For example, the mean particle size can be reduced by increasing quenchant velocity, and the particle morphology can be changed in many instances from spherical to irregular to platelet shapes through proper selection of quenchant composition. Detailed descriptions of the RSC process, operation parameters, powder characteristics and applications have been given in Ref. 192. Although the RSC process has not yet established significant industrial applications, it is a method of interest.