
методичка по Химии
.pdf
положению с образованием молекул воды. В результате получается новолачная смола
2)
Новолачная смола имеет линейное строение, растворяется в органических растворителях и по отношению к нагреванию является термопластичной смолой, которая при нагревании размягчается, становится пластичной, а при охлаждении снова затвердевает, сохраняя при этом прежние свойства.
Резольные смолы получают при следующих условиях реакции: берется избыток формальдегида и щелочной катализатор. Механизм реакции такой же, двухступенчатый. Однако вследствие избытка формальдегида, его присоединение происходит не только по орто-, но и по пара-положению. В результате по первой ступени реакции при температуре 20-600С получаются различные орто-пара-феноло-спирты, например
1)
По второй ступени при температуре выше 700С происходит стадия конденсации феноло-спиртов по орто и пара-положению с образованием резольной смолы, имеющей разветвленное строение, и получается вода, например
2)
90
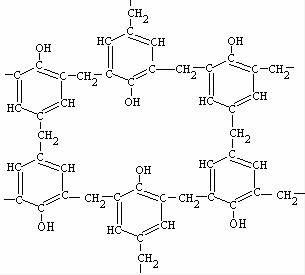
Резольная смола имеет больший молекулярный вес, чем новолачная. Число бензольных колец в ее молекулах колеблется от 6 до 15. Особенность состояния резольной смолы заключается в том, что она содержит активные спиртовые группы (метилольные) – СН2-ОН, способные к дальнейшей реакции поликонденсации. При нагреве смолы в пресс-форме происходит третья стадия переработки, дальнейшая реакция поликонденсации за счет активных спиртовых групп. При этом происходит сшивка отдельных молекул резольной смолы метиленовыми мостиками (-СН2-), образуется полимер с пространственным, сетчатым строением молекул – резит. Поэтому резольная смола является термореактивной, при нагреве затвердевает, при дальнейшем нагреве на размягчается, но при перегреве происходит ее деструкция. Строение резита можно представить следующим образом
Резит не растворяется в органических растворителях, имеет пространственное строение, является термостабильной смолой, т.е. такой смолой, которая при нагревании не плавится, а при перегреве разлагается на составляющие элементы. Для изготовления пластмасс используют в основном резольные смолы. Смолу вместе с добавками нагревают до 150-2000С, происходит отвердение резольной смолы, т.е. переход ее в резит. При нагревании фенолформальдегидных смол от 2000 до 3000С происходит их разложение (деструкция).
Вкачестве наполнителей при получении пластмасс на основе резольных смол применяют древесную муку, ткань, дерево и др.
Впоследнее время получили распространение древесносложные пластики на основе фенолформальдегидной смолы. Получают такие пластмассы путем обработки смолой древесного шпонта тонких листов древесины и последующего прессования их. Древесносложные пластмассы прочны, дешевы, используются в качестве конструкционных материалов: для изготовления шестерен и вкладышей подшипников в машиностроении, в производстве мебели.
Применяя в качестве наполнителей волокнистые материалы, получают пластмассы - волокниты, обладающие большей прочностью, чем получаемые
91
из пресс-порошка. Горячим прессованием из волокнитов готовят панели, рейки и втулки и др. детали промышленного назначения. При использовании хлопчатобумажной ткани в качестве наполнителя получается особенно прочная пластмасса - текстолит (текстильный камень). Процесс изготовления текстолита состоит из следующих операций: подготовка сырья, пропитка ткани на пропиточных машинах с последующей ее сушкой, нарезка ткани и сборка пакетов, прессование текстолита с одновременной его термообработкой и окончательная механическая доработка.
Схема технологического производства текстолита представлена на рис. 1 (стр.97).
Процесс подготовки сырья состоит из сшивания длинных отдельных кусков ткани для перемотки их в рулоны определенного веса. Их устанавливают на пропиточные машины. Затем производят пропитку ткани, для чего в ванну пропиточной машины загружают связующую смолу в виде раствора с органическим растворителем (спирт, ацетон и др.) заданной концентрации и вязкости, чтобы получить определенное количество связующей смолы в ткани. Для уменьшения вязкости пропиточного раствора ванну подогревают. Пропитка ткани производится обычно на вертикальных пропиточных машинах, имеющих коробку скоростей, для регулирования скорости движения ткани на шахте машины в пределах от 15 до 100м/ч и выше, а также снабженных устройствами для регулирования температуры по зонам. Скорость движения ткани по шахте и температура в шахте по зонам зависит от вязкости связующего вида растворителя, требуемого количества связующего в ткани, допустимого количества летучих веществ в ткани. Пропитанная ткань на специальных резательных машинах разрезается на полотнища, из пропитанной ткани собираются пакеты. Количество слоев ткани в пакете определяется требуемой толщиной текстолита и давлением прессования. Прессование текстолита производят на многоэтажных гидравлических прессах, снабженных паровым или электрическим секционным обогревом и имеющих систему водяного охлаждения. В каждый междуплиточный пролет пресса при небольшой толщине прессуемых листов можно загружать несколько пакетов. При этом каждый пакет помещается в продольные металлические листы, протертые специальной смазкой (олеиновая кислота и др.) Термообработка производится в термошкафах, снабженных принудительной вентиляцией и в некоторых случаях в прессах.
Во избежание появления вздутий термообработку проводят постепенно. Из листового и плиточного текстолита механическим путем изготовляют различные детали. Текстолит поддается механической обработке, его можно пилить, сверлить, обрабатывать на токарных и фрезерных станках. Пропитанная ткань может использоваться для приготовления сложных, но сравнительно небольших текстолитовых деталей прессованием в пресс-формах. Режимы прессования изделий отличаются от режимов прессования листового материала. Из текстолита готовят ответственные детали машин – шестерни, вкладыши подшипников, задние бабки для токарных станков и т.д. Шестер-
92
ни из текстолита обеспечивают бесшумность работы машин даже при больших скоростях. Вкладыши из текстолита работают с меньшим коэффициентом трения, чем из обычных антифрикционных сплавов и не требуют смазки, их достаточно охладить водой. И шестерни, и вкладыши подшипников из текстолита служат значительно более длительный срок, чем металлические. Если в качестве наполнителя используется бумага, получается пластмасса гетинакс. Если в качестве наполнителя используется асбест, получается пластмасса, например, с очень высоким коэффициентом трения. Она применяется для изготовления тормозных колодок вагонов, дисков сцепления в автомашинах и т.д. Текстолит используется в качестве электроизоляционного материала.
В последнее время получили распространение стеклопластики, т.е. пластмассы, содержащие стекловолокнистый наполнитель. Если наполнителем служит стеклянная ткань, то пластмасса называется стеклотекстолитом.
Вкачестве связующих в производстве стеклопластиков широко используется различный термоактивный и термопластичный материал. Но самое широкое распространение получили связующие на основе полиэфирных смол, обладающих различными специфическими физико-механическими и технологическими свойствами. Стеклопластики имеют, прежде всего, высокую механическую прочность, хорошие электроизоляционные свойства (высокие диэлектрические свойства). Стеклопластики на основе эпоксидно-фенольных связующих стойки против комплексного воздействия влажности температуры и микроорганизмов, что дает возможность использовать его в тропических условиях в качестве электроизоляционного материала, значительно повышается надежность и срок службы электрооборудования по сравнению с оборудованием, в котором используется изоляция из текстолита и гетинакса.
Вэлектрических машинах стеклотекстолиты применяют в виде клиньев для пазовой изоляции статорных обмоток машин переменного тока, роторных обмоток генераторов и асинхронных двигателей, а также якорных обмоток машин постоянного тока. В трансформаторах стеклопластики применяют в виде цилиндров, трубок, листовых материалов и фасонных деталей для изоляции обмоток друг от друга и от кожуха трансформатора. Из стеклопластиков изготавливаются корпуса специальных электроприборов и генераторов, вентиляторы для электродвигателей, изоляции для электроприводов, кабельные наконечники, щиты для высоковольтной арматуры, детали для выключателей высокого напряжения. Стеклопластики могут работать при высоких температурах. Возможность применения изделий из стеклопластиков при высокой температуре обусловлена их низкой теплопроводностью, малой горючестью, сравнительно высокой теплостойкостью, способностью пластиков выделять газы, образующие теплозащитный слой на поверхности материала. Из стеклопластиков изготавливают ряд элементов конструкции самолета: законцовки крыльев, винтов, сидения, двери, люки. В реактивных двигателях стеклопластики используются для изготовления направляющих лопаток компрессора.
93
В последнее время стеклопластики успешно начинают применяться в производстве ракет. Корпус ракеты из стеклопластика способен выдерживать действия механических и тепловых нагрузок аналогично корпусу из алюминиевых сплавов, титана или стали, причем скорость повышения температуры поверхности ракеты значительно меньше, чем при использовании металла. Кроме корпуса ракеты, из стеклопластиков изготавливают направляющее устройство ракетного двигателя, крылышки, хвостовое оперение. Благодаря хорошим радиотехническим свойствам (пропускают электромагнитные волны без искажения, с минимальным поглощением энергии) стеклопластики широко применяются в радиотехнике и в промышленности средств связи.
ПРАКТИЧЕСКАЯ ЧАСТЬ
Содержание работы заключается в изготовлении текстолита методом прессования на лабораторной установке. Прессование производится в плоской пресс-форме, состоящей из двух обогреваемых пластин (рис. 2. дет.2, 5), прикрепленных одна к верхнему упору масляного пресса и другая к плунжеру масляного пресса. Электрообогрев обеих деталей включен последовательно на 30 В и питается переменным током от трансформатора. Температура нагрева контролируется с помощью термопары, вмонтированной в нижнюю половину пресс-формы. Необходимое усилие для сжатия пресс-формы, работающей от ручного насоса, создается рукояткой насоса (рис. 2, дет. 11). Давление масла внутри цилиндра пресса контролируется с помощью манометра (рис. 2, дет. 12), а его максимальная величина, 150атм ограничивается редукционным клапаном, включенным в маслосистему пресса. Для возвращения плунжера пресса в крайнее нижнее положение необходимо выпустить масло из цилиндра пресса в резерв путем открытия запорного крана (рис. 2, дет. 13). Если плунжер пресса в таких случаях не опускается под действием собственного веса, необходимо сверху нажать с небольшим усилием на его выступающие края, с помощью рычажного механизма, смонтированного на прессе.
Последовательность операций при выполнении работы
1.При крайнем нижнем положении плунжера масляного пресса осторожно очистите рабочую поверхность пресс-формы от пыли и остатков предыдущего прессования. Для этого пользуются х/б ветошью или, в крайнем случае, деревянными скребками. Ни в коем случае нельзя скоблить поверхность пресс-формы металлическими предметами.
2.Проверьте правильность подключения электрообогрева пресс-формы
иего исправность.
3.Закройте выпускной масляный кран пресса (рис. 2, дет. 13) с помощью ручного масляного насоса, поднимите плунжер пресса вместе с подвижной частью пресс-формы до полного ее упора (при этом оберегайте
94
пресс-форму от ударов) и включите электрообогрев. Степень нагревания пресс-формы контролируйте по показаниям термопары. Нагрев пресс-формы ведется в течение 40-50 минут до температуры 125-1350С. От степени нагрева пресс-формы зависит качество получаемого изделия и продолжительность прессования.
4.Для прессования необходимо получить у лаборанта уже высушенные (пропитанные резольной смолой) заготовки бумаги или х/б ткани, разрезать их на квадраты 5х5 см, собрать пакет (4-5 шт. заготовок).
5.Пакет вставьте внутрь пресс-формы. Для этого откройте выпускной масляный клапан (рис. 2, дет. 13), опустите плунжер пресса в крайнее положение. Осторожно (чтобы не обжечь руки!) положите пакет на матрицу, закрыть выпускной клапан и поднимите плунжер пресса с помощью ручного масляного насоса (рис. 2, дет. 11).
6.Доведите давление масла в цилиндре пресса до 150 атмосфер и подержите его в течение 10-15 минут, изредка подкачивая масло ручным насосом. В течение 10-15минут произойдет полная поликонденсация смолы, и этим по существу заканчивается прессование.
7.После прессования открыть пресс-форму (как указано выше), извлеките из пресс-формы полученный лист гетинакса или текстолита. Выключите обогрев. Очистите пресс-форму.
8.Зачистите напильником края полученного образца, предъявите его преподавателю вместе с отчетом и ответьте на контрольные вопросы.
КОНТРОЛЬНЫЕ ВОПРОСЫ
1.Какие материалы называют пластмассами?
2.Что такое простые и сложные пластмассы?
3.Каковы условия получения фенолформальдегидных смол, новолачных, резольных и резитов?
4.В чем сущность механизма реакции поликонденсации?
5.Какие сложные пластмассы изготавливаются на основе резольных смол и каковы их технические достоинства перед другими материалами?
6.Какова технология производства текстолита?
7.Что такое стеклотекстолит? Каковы его свойства и применение?
БИБЛИОГРАФИЧЕСКИЙ СПИСОК
1. Коровин Н.В. Курс общей химии. - М.: Высшая школа, 2001. –
С. 450-466.
95
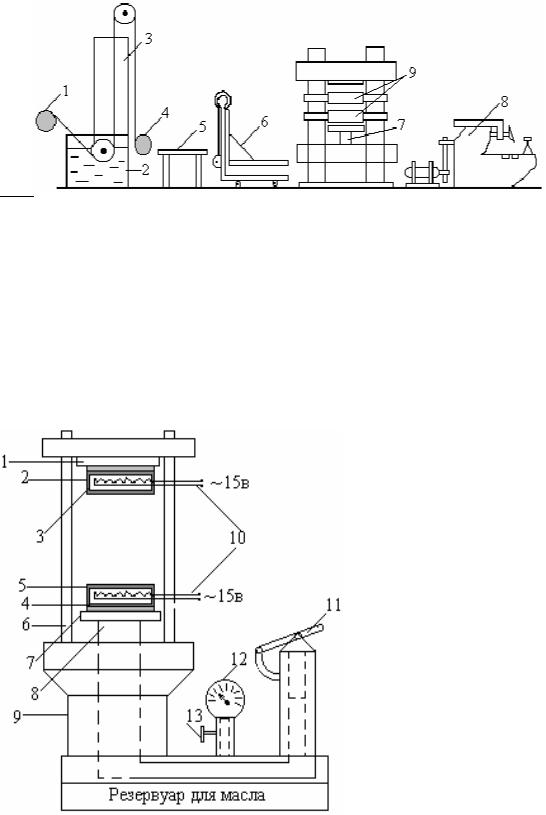
Рис. 1 Схема технологического процесса изготовления текстолита
1 – ткань для пропитки; 2 – раствор смолы; 3 – сушильный шкаф; 4 – пропитанная ткань; 5 – стол для пакетирования; 6 – подъемник; 7 - гидравлический пресс; 8 – фрезерный станок; 9 – секции пресс-формы для подогрева
__________________________________________________________________
1, 7 – плиты; 2, 5 – плиты пресс-формы;
3, 4 – теплоизоляция; 6 – направляющие стержни;
8 – гидравлический плунжер;
9 – гидравлический пресс;
10 – спираль;
11 – насос;
12 – манометр;
13 – запорный кран.
Рис. 2 Схема лабораторной установки для получения текстолита
96
ЛАБОРАТОРНАЯ РАБОТА № 34В
ДЕСТРУКЦИЯ ПЛАСТМАСС
СВЕДЕНИЯ ИЗ ТЕОРИИ
Пластмассами называются материалы, изготовленные на основе органических высокомолекулярных веществ, полимеров, способных при определенных условиях формоваться вследствие их пластичности. Полимерные соединения (макромолекулы) состоят из очень большого числа атомов углерода, и это определяет ряд их физико-химических свойств.
Помимо большого числа положительных качеств, обеспечивших широкое применение пластмасс в различных отраслях народного хозяйства, имеются отрицательные свойства. Одним из них является старение пластмасс – процесс, при котором под влиянием различных факторов изменяется состав и строение полимерных молекул. Одной из разновидностей старения является деструкция пластмасс. При деструкции происходит разрушение макромолекул высокомолекулярных соединений, сопровождающееся изменением их структуры, понижением молекулярного веса, обусловливающим изменение физико-химических, механических, электрических и других свойств.
Деструкция пластмасс может происходить под действием физических факторов: тепла (термическая деструкция); света (фотохимическая деструкция); излучения (радиационная деструкция); при механическом разрушении макромолекул (механическая деструкция), например, при дроблении, истирании, при действии ультразвука; при действии химических агентов: окислителей (окислительная деструкция) и др. веществ.
Деструкция пластмасс часто приводит к ухудшению свойств полимерных материалов; однако ее нельзя рассматривать только как отрицательное явление.
Например, она широко используется при совмещении пластмасс с различными веществами, при производстве резины и пластикатов, при получении блок – привитых полимеров и т.д.
Механизм деструкции полимеров чаще имеет радикально цепной характер. При этом происходит разрыв химической связи между атомами углерода, образующих цепь молекулы полимера, и образование всевозможных «осколков» - веществ с малым молекулярным весом.
Частным случаем деструкции пластмасс является образование молекул мономера из полимера. В этом случае происходит реакция деполимеризации.
Деполимеризация полимерных соединений происходит при нагревании, независимо от того, состоят ли цепи только из одних атомов углерода или в них входят также атомы кислорода, азота, серы и других элементов.
97
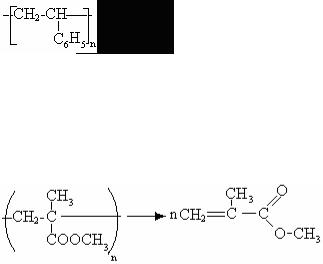
ОТНОШЕНИЕ РАЗЛИЧНЫХ ПЛАСТМАСС К НАГРЕВАНИЮ
1.Полиэтилен (-СН2-СН2-)n − белое, твердое, но эластичное вещество, легче воды. Размягчается при температуре около 1000С, разлагается при 1150С. Из этого следует, что изделия из полиэтилена следует оберегать от сколько-нибудь значительного нагревания.
2.Поливинилхлорид (винилпласт) (-СН2-СНCl-)n . Порошкообразное, нетоксичное вещество белого цвета. Еще менее термостоек, чем полиэтилен, т.к. размягчается уже при 50-600С, легко сверлится, сваривается при нагревании горячим воздухом до 2000С. При деструкции не образует мономера.
3.Политетрафторэтилен (-СF2-СF2-)n . В России известен под названием фторопласт – 4, в США – тефлон. Это белое порошкообразное вещество,
похожее на парафин. Политетрафторэтилен не плавится, но размягчается при температуре около 3000С. Изделия из политетрафторэтилена можно применять при температуре от – 700 до 2600С. При нагревании полимера в вакууме до 4900С начинается заметный его распад с образованием в основном тетрафторэтилена.
4.Полистирол:
Полистирол нетоксичное вещество. Бывает прозрачный и непрозрачный. Прозрачный полистирол внешне похож на полиметилметакрилат, но при постукивании звенит, а пленка из него дребезжит. Полистирол не стоек по отношению к нагреванию: размягчается уже при 80-900; при 1000 – подвергается деполимеризации.
5. Полиметилметакрилат (акрилат, плексиглас – органическое стекло):
Из всех пластмасс полиметилметакрилат наиболее прозрачен. Полимер размягчается при 70-800С и до 100-1250С. При нагревании до 3000С подвергается деполимеризации с выделением мономера, желтоватой жидкости со специфическим запахом.
6.Капрон (−NH−(CH2)5 −CO−)n. Термопластичный полимер плавится при 2150С. При нагревании свыше 2150С разлагается с выделением аммиака.
Ввиду того, что прядение капронового полотна производится не из раствора, а из расплава, капроновые изделия, вышедшие из употребления, снова могут быть использованы для повторной переработки.
7.Фенолформальдегидные пластмассы или фенопласты. Окрашены в
темный цвет, от темно коричневого до черного. Неплавки. При нагреве до 3000С подвергаются деструкции с выделением фенола.
98

8. Каучуки. Каучуками, эластомерами называются полимеры, сохраняющие упругие свойства в пределах широкого интервала температур. В настоящее время применяют натуральные и синтетические каучуки. Натуральный каучук представляет собой полимер изопрена:
Нагревание натурального каучука приводит к его деполимеризации с выделением изопрена. Из искусственных каучуков самым термостойким является силиконовый. Он сохраняет эластичность и механическую прочность при температурах от – 900С до 2600С. Изделия из силиконового каучука могут эксплуатироваться при температурах от – 700С до 2500С.
ПРАКТИЧЕСКАЯ ЧАСТЬ
Содержание работы заключается в осуществлении сухой перегонки пластмасс и позволяет пронаблюдать деструкцию последних. Работа выполняется в вытяжном шкафу. Сухая перегонка пластмасс производится в приборе, состоящем из сосуда (а), где производится нагревание пластмассы (этот сосуд закреплен в лапках штатива). Сосуд при помощи газоотводной трубки (б) соединяется с ловушкой (в), которая в свою очередь сообщается с сосудом – сборником продуктов деструкции (г). Назначение ловушки - не допустить засасывания раствора из сосуда-приемника в сосуд перегонки. Ловушка находится в резервуаре (д), заполненном водой и играющем роль холодильника. Этот резервуар также закреплен в лапках штатива.
Задание 1. Деструкция полихлорвинила
1.В пробирку для сухой перегонки (а) засыпьте небольшое количество (примерно на 1 см по высоте) мелко нарезанного полихлорвинила.
2.В пробирку-приемник (г) налейте небольшое количество воды с добавлением индикатора метилоранжа и в этот раствор погрузите конец отводной трубки ловушки.
3.Произведите нагревание пробирки (а) с пластмассой на спиртовке. При этом сразу же, если прибор герметичен, из конца отводной трубки, находящегося в растворе метилоранжа выделяются пузырь-
ки воздуха.
При самом непродолжительном нагревании полихлорвинил подвергается деструкции с образованием хлористого водорода в виде густых белых паров и смеси различных низкомолекулярных продуктов, среди которых мономера не обнаруживается.
99