
- •Коррозия и защита металлов строительных и конструкционных материалов.
- •Коррозия и защита металлов строительных и конструкционных материалов.
- •с методическими указаниями
- •ЛАБОРАТОРНАЯ РАБОТА № 22
- •Цель работы: изучить процесс образования электродного потенциала, измерить равновесный потенциал металла в водном растворе его соли и ориентировочно определить его химическую активность относительно водорода.
- •ЗАДАЧА ЛАБОРАТОРНОГО ИССЛЕДОВАНИЯ
- •ОПИСАНИЕ ЛАБОРАТОРНОЙ УСТАНОВКИ
- •ПОРЯДОК ВЫПОЛНЕНИЯ И ОФОРМЛЕНИЯ РЕЗУЛЬТАТОВ
- •Равновесный потенциал металла в растворах его соли
- •Раствор
- •Цинк
- •ЛАБОРАТОРНАЯ РАБОТА № 23
- •СВЕДЕНИЯ ИЗ ТЕОРИИ
- •Рис. 1. Схема коррозионного элемента
- •ЛАБОРАТОРНАЯ РАБОТА № 24 Д
- •ГАЛЬВАНИЧЕСКОЕ ЦИНКОВАНИЕ
- •СВЕДЕНИЯ ИЗ ТЕОРИИ
- •Гальванический способ нанесения цинкового покрытия
- •ПРАКТИЧЕСКАЯ ЧАСТЬ
- •КОНТРОЛЬНЫЕ ВОПРОСЫ
- •ЛАБОРАТОРНАЯ РАБОТА № 26
- •СВЕДЕНИЯ ИЗ ТЕОРИИ
- •ПРАКТИЧЕСКАЯ ЧАСТЬ
- •ЛИТЕРАТУРА
- •СВЕДЕНИЯ ИЗ ТЕОРИИ
- •КОНТРОЛЬНЫЕ ВОПРОСЫ
- •СВЕДЕНИЯ ИЗ ТЕОРИИ
- •Рис. 3. Схема измерений на лабораторной установке
- •ПРАКТИЧЕСКАЯ ЧАСТЬ
- •ОПИСАНИЕ ЛАБОРАТОРНОЙ УСТАНОВКИ
- •ПОРЯДОК ВЫПОЛНЕНИЯ И ОФОРМЛЕНИЯ РЕЗУЛЬТАТОВ РАБОТЫ
- •КОНТРОЛЬНЫЕ ВОПРОСЫ
- •ЛИТЕРАТУРА
ЛАБОРАТОРНАЯ РАБОТА № 23
ОПРЕДЕЛЕНИЕ СКОРОСТИ КОРРОЗИИ МЕТАЛЛОВ И СПЛАВОВ ПО ОБЪЕМУ ВЫДЕЛИВШЕГОСЯ ВОДОРОДА
Цель работы: определить скорость коррозии контактной пары металлов в зависимости от величины разности потенциалов, составляющих электродвижущую силу (Е) коррозионного элемента в кислой среде.
Рабочее задание: 1) испытать модели коррозионных элементов, например, металлов Zn - Pb, Zn - Cu в кислой среде. Построить графики: объем выделившегося водорода (V) - время отсчета (τ);
2)рассчитать среднюю скорость коррозии за 0,5 часа;
3)определить эффективность ингибирования коррозии (по индивидуальному заданию преподавателя).
СВЕДЕНИЯ ИЗ ТЕОРИИ
Коррозия - самопроизвольный процесс разрушения, окисления металлов и их сплавов в результате химического или электрохимического воздействия окружающей среды.
Скорость коррозии Vk - это количество окисленного металла или сплава m (г) в единицу времени t (ч) на единицу поверхности S (см2)
Vk = |
m |
, |
г |
(1) |
|
|
|
. |
|||
t S |
см2 час |
Взаимодействие различных металлов с водными растворами кислот, щелочей и солей в повседневной практике имеет большое значение. Такое взаимодействие происходит при травлении металлов с целью снятия с их поверхности окисной пленки, при различных коррозионных процессах. В особенности важно знать это при конструировании, эксплуатации и ремонте железнодорожной техники и оборудования, большая часть которых, подвержена действию различной агрессивной среды.
Всякий металл, и в особенности сплав нескольких металлов, имеет на своей поверхности участки, значительно отличающиеся друг от друга по структуре, физическим и химическим свойствам. В результате всех факторов, определяющих это различие, самопроизвольно образуется скачок необратимого потенциала на границе металл - раствор. Величина его в значительной степени изменяется при переходе от одного участка к другому на корродирующем металле. Это и определяет наличие катодных (более положительных
11

по своему потенциалу) и анодных (отрицательных) участков поверхности, соприкасающихся с коррозионной средой. Схему такого микроили макрокоррозионного элемента можно представить согласно рис.1.
|
|
Рис. 1. Схема коррозионного элемента |
|
||
В |
качестве |
катодного |
участка |
поверхности (катодной примеси) мо- |
|
гут быть, например, в чугуне зерна |
графита (Е0С = +0,2 ÷0,5 В в зависи- |
||||
мости |
от реакции), или зерна цементита в сталях (карбида |
железа |
|||
Fe3C, Е0Fe3C = +0,029В). |
|
|
|
||
В |
качестве |
анодных |
участков |
поверхности выступают |
фазы |
сплавов металлов, структурные неоднородности сплавов, например, в сталях участки (зерна) чистого железа, с наиболее отрицательным потенциалом
(Е0феррита = - 0,44 В), деформированные, механически напряженные участки поверхности, а также включения металлов с более отрицательным потенциа-
лом.
На аноде идет окисление металла. На его поверхности остаются элек-
троны, число которых равно заряду катионов, перешедших в раствор |
|
А(-) Me - 2e → Me2+ . |
(2) |
В результате этого анодный участок, отрицательный по своему знаку, получает дополнительный отрицательный заряд. Это обуславливает самопроизвольный переход электронов внутри металла с анодных участков на катодные. Потенциал катода по этой причине сдвигается в отрицательную сторону, т.е. происходит накапливание электронов на катоде. Такое явление накапливания электронов на катоде называется поляризацией катода, а процесс отвода электронов с катода - деполяризацией. Вещества, которые отводят электроны с катода и сами при этом восстанавливаются, называются деполяризаторами.
12

На катоде в кислой среде в роли деполяризатора выступают ионы водорода H+, которые непрерывно подходят к поверхности и отводят электроны с катодов по реакции
K(+) 2H+ + 2e → H2↑. |
(3) |
Следовательно, деполяризующее действие водородных ионов в коррозионных процессах заключается в реализации избыточных электронов на поверхности катодов, что, естественно, облегчает дальнейшее окисление и растворение металла. В реальных условиях эксперимента в данной работе применяются короткозамкнутые, контактные коррозионные пары, пластинок электродов Zn/Cu, Zn/Pb из пластин металлов, со следующей электрохимической схемой, например, для пары металлов Zn/Cu:
E0 |
= - 0,76В |
E0 |
= + 0,34В. |
Zn2+ / Zn |
|
Cu2+ / Cu |
|
А(-)Zn H2SO4 Cu(+)К.
Нерабочая поверхность коррозионной пары электро- и гидроизолиро-
вана.
Потенциал цинка (Е0) отрицательнее потенциала меди, поэтому цинк более активен, легче отдает электроны и окисляется. Электрод, на котором происходит окисление, во всех электрохимических процессах является анодом. В результате цинк является анодом. Тогда на электродах происходят реакции:
A(-) Zn - 2e → Zn2+
K(+) 2H+ + 2e → H2↑
Zn + 2H+ = Zn2+ + H2↑
Zn + H2SO4 = ZnSO4 + H2↑.
Скорость электрохимической коррозии металлов (Vк) зависит от величины электродвижущей силы (Е) короткозамкнутых, коррозионных элементов, коррозионных пар (КП). Э.Д.С. элемента (КП) равна разности потенциалов окислителя (потенциала катода ЕК(+) ) и восстановителя (потенциала анода ЕА(-)):
ЕКП = ЕК(+),ок-ль. – ЕА(-),восст-ль, |
(4) |
Еок-ля > Евос-ля.
ЕКП – всегда положительна.
13
Чем больше будет Е коррозионного элемента из металлов, составляющих коррозионную пару, тем скорость коррозии будет больше и наоборот.
Согласно вышеизложенному, можно отметить три весьма важных обстоятельства:
1)количество металла, растворившегося в кислоте, эквивалентно количеству (объему) выделившегося водорода, что дает возможность рассчитать скорость коррозии изучаемого металла;
2)количество выделившегося водорода, приведенное к нормальным условиям, позволяет по закону Фарадея вычислить среднюю силу электрического тока, проходящего через все электродные поверхности коррозионных элементов в изучаемых условиях;
3)процесс деполяризации с участием ионов водорода, восстанавливающихся на катодах, является необходимой составной стадией всего коррозионного процесса.
Скорость коррозии можно снизить с помощью так называемых замедлителей или ингибиторов коррозии. Ингибиторы применяют главным образом в системах, работающих с постоянным или малообновляемым объемом раствора, например, в некоторых химических аппаратах, системах охлаждения, в процессах травления металлов для удаления окалины или ржавчины. Тормозящее действие ингибиторов связано или с окислением (пассивированием) поверхности металла (нитриты, хроматы), или с образованием пленки труднорастворимых соединений (фосфаты, силикаты, бораты), или с адсорбцией (притягиванием) поверхностью металла молекул ингибитора.
Ингибиторы затрудняют катодную, анодную или обе реакции вместе. В кислой среде чаще применяют органические ингибиторы катодного действия, которые адсорбируются на катодных участках металла, затрудняют доступ деполяризатора (H+) к катоду и уменьшают коррозию металла.
Степень защиты (Z) металла от коррозии ингибитором (степень ингибирования) можно рассчитать по формуле
Z = |
Vk − Vkи |
100%, |
(5) |
|
|||
|
Vk |
|
где Vk - скорость коррозии без ингибитора; Vkи - скорость коррозии с ингибитором.
ПРАКТИЧЕСКАЯ ЧАСТЬ
Цинк по своим физико-химическим свойствам, состоянию поверхности, сравнительно легкой доступности показал себя наиболее удобным мате-
14

риалом для изучения электрохимического механизма коррозии. Кроме этого, в условиях транспорта широко используются изделия и детали, изготовленные из сплавов на основе цинка.
Для опытов используются модели коррозионных элементов: Zn - Cu, Zn - Pb.
Определение скорости коррозии цинка в кислой среде
1. Взять модели коррозионных элементов Zn - Cu, Zn - Pb (рис. 2). Мелкозернистой наждачной бумагой очистить их металлическую поверхность от жировых и других загрязнений, промыть, протерев после этого фильтровальной бумагой.
Рис. 2. Модель коррозионного макроэлемента
2. Завесить модель внутрь стеклянной воронки, как это показано на
рис.3.
3. Каждую воронку с испытуемым образцом осторожно вставить в открытый конец бюретки (рис.3 и 4).
Рис. 3. Способ подвешивания коррозионного макроэлемента в воронке
4. Заполнить дистиллированной водой разделительную склянку водяного сифона В1 (рис.4), обслуживающего установку. Для этого необходимо закрыть краны сифона - кр.1, кр.2 (рис.4) и открыть горловину склянки, через которую наливается вода при помощи воронки. После того как склянка заполнится водой, закрыть ее резиновой пробкой (без особых усилий, но достаточно герметично) и открыть кран 2. Подготовленный таким образом сифон, если он исправен, не должен подсасывать воздух из закрытых бюреток. В противном случае нужно найти и устранить неисправность.
15

5.В соответствии с полученным заданием, приготовить чисто вымытые химические стаканы емкостью на 150 мл и налить в них по 150 мл 0,25М раствора H2SO4.
6.Каждый стакан с приготовленным раствором подвести под нижний конец бюретки с воронкой, поднять вверх и под него поместить подставку таким образом, чтобы нижний край воронки не доходил до дна стакана на 3 - 5 мм. При этом необходимо следить за тем, чтобы кран (1) на верхнем конце бюретки был закрыт, испытуемый раствор не должен самопроизвольно заполнять бюретку.
7.Заполнение каждой бюретки испытуемым раствором производят, осторожно открывая кран 1 (зажим) на верхнем конце бюретки. Установив уровень раствора в верхнем конце бюретки в пределах нескольких последних делений шкалы, необходимо записать их и заметить время. С момента соприкосновения раствора с испытуемой моделью коррозионного элемента начинается процесс выделения водорода. Первоначально объем водорода в бюретках замеряется через 5 минут (см. таблицу). После двух замеров объемов водорода через 5 минут, делаются замеры через 10 минут. Таким образом, продолжительность работы коррозионных элементов составляет 0,5 часа. Объем водорода должен измеряться с точностью до 0,05 мл, глаз наблюдателя при этом должен находиться на уровне нижнего мениска раствора. Результаты измерения заносятся в таблицу.
|
|
|
|
Таблица |
|
|
|
|
|
Время отсчета t, мин |
Zn - Pb |
Zn - Cu |
||
объем Vисх |
суммарный |
объем Vисх |
суммарный |
|
(общее) |
по бюретке |
объем H2 к |
по бюретке |
объем H2 к |
|
|
концу t |
|
концу t |
0 |
|
|
|
|
5 |
|
|
|
|
10 |
|
|
|
|
20 |
|
|
|
|
30 |
|
|
|
|
По окончании работы:
1.Проверить, закрыты ли краны на водяном сифоне. После этого слить растворы из бюреток обратно в стаканы, вынув для этого воронки из нижней части бюреток.
2.Растворы из стаканов вылить, тщательно промыть бюретки, воронки и стаканы.
3.Произвести необходимые расчеты:
16
1)по результатам таблицы построить график: по оси ординат откладывают объем водорода, а по оси абсцисс - время t, за которое выделился данный объем водорода;
2)определить общий объем водорода V за t=0,5 часа для каждой испытуемой модели;
3)привести объем водорода к нормальным условиям, используя для этого формулу объединенного газового закона Бойля-Мариотта и ГейЛюссака:
|
P V |
= |
P0 V0 |
|
||||
|
|
|
|
|
, |
(6) |
||
|
T |
T |
0 |
|||||
|
|
|
|
|
|
|||
откуда |
|
|
|
|
|
|
|
|
|
V0 = |
P T0 |
|
V, |
(7) |
|||
|
0 |
|||||||
|
|
|
P T |
|
|
|
где: V0 - объем водорода, выделившийся за 0,5 часа, приведенный к нормальным условиям (мл);
V - объем водорода, выделившийся за 0,5ч., (мл);
T - температура опыта по термодинамической шкале Кельвина (T = t + 273);
P - парциальное давление водорода.
Следует учесть, что в данном случае водород насыщен водяными парами. Поэтому собственное давление водорода, или так называемое парциальное давление водорода, равно атмосферному за вычетом давления водяных паров
P = Pатм - Pводы , |
(8) |
где: Pводы - давление или упругость водяных паров (см. таблицу, прикрепленную к установке);
4) для каждой модели рассчитать скорость коррозии цинка. Для этого по объему водорода, приведенного к нормальным условиям (V0), рассчитать по закону эквивалентов весовое количество растворившегося цинка в граммах по формуле
|
|
|
|
m |
|
|
V0 |
|
|
|||
|
|
|
|
|
Zn |
= |
|
|
|
, |
|
(9) |
|
|
|
M |
|
V |
|
|
|
||||
|
|
|
|
|
экZn |
|
эквH2 |
|
|
|||
откуда |
|
|
|
|
|
|
|
|
|
|
|
|
M |
Zn |
= |
МэкZn V0 |
= |
A V0 |
, |
(10) |
|||||
|
n VэквH2 |
|||||||||||
|
|
|
|
VэквH2 |
|
|
|
|||||
|
|
|
|
|
|
|
|
17
где mZn - масса растворившегося цинка, г.;
V0 - объем выделившегося за 0,5 часа и приведенного к нормальным условиям водорода, мл;
Vэк Н2 - объем эквивалента объем водорода, равный 11200 мл/моль при нор-
мальных условиях;
МZn = A/n (А – молярная масса атома цинка(г/моль), n – степень окисления цинка, Мэк Zn – молярная масса эквивалента цинка) г/моль.
Объем эквивалента водорода - это такой объем, который занимает при нормальных условиях одна молярная масса эквивалента водорода 1 г/моль и он равен 11,2 л/моль, или 11200 мл/моль.
Определив весовое количество цинка, рассчитать скорость коррозии по объему выделившегося водорода за время t = 0,5 часа по формуле
V |
= |
mZn |
, |
(11) |
|
|
|||||
k |
S |
t |
|
|
|
|
|
|
|
где Vk - скорость коррозии, г/см2*ч; mZn - масса растворившегося цинка, г;
S - поверхность цинка, см2;
t - время, которому соответствует объем (V) водорода, ч;
5) определить силу коррозионного тока на поверхности каждого образца по закону Фарадея
Iсред |
= |
26,8 mZn |
, |
(12) |
|
||||
|
|
A t |
|
где: Iсред - сила коррозионного тока, А; 26,8 - постоянная Фарадея, А . ч;
MZn - количество растворившегося цинка за 0,5 ч; А - молярная масса атома цинка (г/моль);
n - степень окисления цинка, 2;
t - время растворения цинка, 0,5 ч.
Рассчитать Е коррозионного элемента в стационарных условиях с учетом материала катода
Е0КЭ = Е0(+)К- Е0(-)А. |
(13) |
В качестве отчета по лабораторной работе представить результаты расчетов, ответы на контрольные вопросы, сделать вывод по результатам расчетов.
18

Определение скорости коррозии цинка в кислой среде в присутствии ингибитора
Провести опыты, как описано выше, с двумя образцами одной из коррозионных пар Zn - Cu или Zn - Pb в растворе H2SO4 без ингибитора и с ингибитором. В качестве ингибитора можно использовать
уротропин (гексаметилентетрамин) C6H12N4.
Для этого приготавливают раствор (1-3%) в 0,25М
H2SO4.
По результатам эксперимента построить графики
Vводорода(мл) - t (мин), произвести расчет скорости коррозии без ингибитора Vk и с ингибитором Vkи, как описано
выше. Рассчитать степень ингибирования коррозии Z, сделать вывод о защитном действии ингибитора.
КОНТРОЛЬНЫЕ ВОПРОСЫ
1.Какова сущность электрохимического механизма коррозии? Какова сущность механизма коррозии в атмосфере, электролитах, почве?
2.Понятие о равновесных и неравновесных электродных потенциалах. Обратимые и необратимые электродные потенциалы.
3.Как влияет электродвижущая сила (Е) на скорость коррозии?
4.Что такое поляризация, деполяризация и деполяризаторы? Роль деполяризаторов в коррозионном процессе.
5.Каковы методы изучения скорости электрохимической коррозии и сущность расчетов при определении скорости коррозии по объему выделившегося водорода?
ЛИТЕРАТУРА
1.Глинка Н.Л. Общая химия/ Под ред. А.И. Ермакова. – М.: Инте-
грал-Пресс, 2003. – 728С.
2.Коровин Н.В. Общая химия. – М.: Высш. Школа, 2000. – 558 с.
3.Жук Н.П. Курс теории коррозии и защиты металлов. – М.: Метал-
лургия., 1976. – 472 с.; ил.
4.Клинов И.Я. Коррозия химической аппаратуры и коррозионностойкие материалы. – М.: Машиностроение, 1967. -468 с.; ил.
5.Справочник химика. Т.3 – М., л.: Химия. 1964. – 1005 с.
19
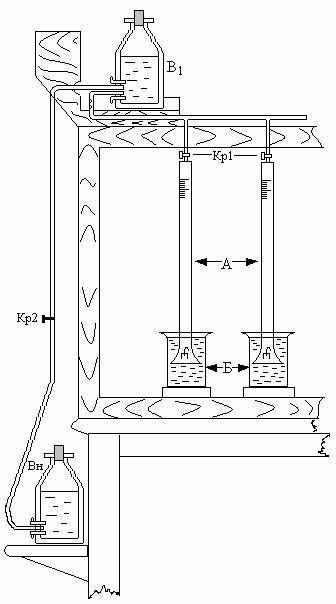
Рис. 4. Общий вид установки для объемно-метрического метода изучения скорости коррозии цинка в растворе серной кислоты
20
ЛАБОРАТОРНАЯ РАБОТА № 24а
ОКСИДИРОВАНИЕ АЛЮМИНИЯ И ЕГО СПЛАВОВ
Тема: оксидирование алюминия и его сплавов.
Цель работы: изучить сущность и освоить практические приемы осуществления электрохимического оксидирования (анодирования) алюминия и определения толщины оксидных пленок.
Рабочее задание: провести переменным током оксидирование листового алюминия в серной кислоте и определить толщину оксидных пленок на алюминии в зависимости от условий их формирования и уплотнения.
СВЕДЕНИЯ ИЗ ТЕОРИИ
Оксидирование - процесс искусственного образования на поверхности черных или цветных металлов оксидов с целью:
-защиты от коррозии;
-декоративной отделки полированных и обработанных другими механическими способами поверхностей или с целью окраски;
-грунтовки для лакокрасочных покрытий и других органических пле-
нок;
-создания подслоя для электролитических покрытий;
Оксидные пленки, образованные на поверхности черных и цветных металлов используются также для специальных целей, связанных с особыми свойствами покрытий, например, для электрической и тепловой изоляции, для условий, когда необходимы очень большая пористость и высокая степень адсорбции, или для придания твердости и износостойкости (например, в подшипниках скольжения).
Для цветных металлов наибольшее распространение получило оксидирование (анодное окисление) алюминия и его сплавов.
Пассивность алюминия и его стойкость в атмосферных условиях, несмотря на сильно электроотрицательный стандартный потенциал
( E0 |
= -1,66B), объясняется наличием на его поверхности естественной |
Al0 / Al3 +
пленки Al2O3 или Al2O3 . H2O толщиной 0,005-0,015 мкм. Эта пленка предохраняет алюминий от коррозии во многих нейтральных и слабокислых растворах. Однако в более жестких коррозионных условиях, например, в кислых и щелочных средах, в присутствии хлоридов, стойкость естественной пленки недостаточна.
Оксидирование алюминия позволяет увеличить коррозионную стойкость и износостойкость его поверхности, придает ей декоративный вид и высокие электроизоляционные свойства.
Различают химическое и электрохимическое оксидирование (анодное окисление) алюминия.
21
Химическое пассивирование (оксидирование) проводят в окисляющих растворах, например, в хроматносодовой смеси Na2CrO4 + Na2CO3 + Na2SiO3.
Электрохимические методы, несмотря на их сложность, используют чаще, т.к. получаемые при этом оксидные пленки обладают самыми разнообразными свойствами. Анодное окисление (оксидирование) можно вести как с помощью постоянного тока, так и переменного (в анодный полупериод) тока.
Оксидирование стали осуществляется химическим способом в раство-
ре, г/л: 600 - 700 NaOH, 50 - 100 NaNO3 и 200 - 250 NaNO2 при температуре
135..1400С в течение 20 - 50 минут. В результате на поверхности образуется оксидная пленка толщиной 0,6 - 0,8 мкм, состоящая в основном из магнитного оксида железа черного цвета. Для повышения защитных свойств оксидных пленок детали необходимо промасливать.
Сущность электрохимического процесса оксидирования (анодирования) алюминия
При электрохимическом оксидировании применяется процесс электролиза в растворе серной кислоты с нерастворимым алюминиевым анодом. При прохождении электрического тока через электролит на алюминиевом аноде происходит электрохимическое окисление воды по реакции
A(+) 3H2O - 6e = 6H+ + 1,5O2↑ . (1)
Кислород, полученный при этом, химически окисляет алюминиевую поверхность
2Al + 1,5O2 = Al2O3 |
(2) |
иповерхность примесей, выступающих из кристаллической решетки сплава.
Вобщем виде процесс анодного окисления алюминия можно предста-
вить уравнением |
|
2Al + 3H2O - 6e = Al2O3 + 6H+. |
(3) |
Благодаря этому поверхность алюминиевой основы полностью покрывается утолщенной пассивной пленкой, включая и дефекты ее на границах с кристаллами - примесями. Полученная утолщенная пассивная пленка на алюминии и его сплавах обладает весьма высокой твердостью.
На катоде происходит восстановление ионов водорода Н+ или молекул
воды по реакции |
|
K(-) 2H+ + 2e = H2↑ |
(4) |
или K(-) 2H2O + 2e = H2 + 2OH- . |
(5) |
Просуммировав анодную и катодную реакции, получим суммарное уравнение процесса оксидирования (окисления) алюминия
A(+) 2Al + 3H2O - 6e = Al2O3 + 6H+ |
(6) |
K(-) 6H2O + 6e = 3H2 + 6OH- |
(7) |
Σ 2Al + 3H2O = Al2O3 + 3H2↑. |
(8) |
22

Окрашивание и уплотнение оксидных покрытий
После оксидирования алюминия в серной или щавелевой кислоте на металле получается пористая пленка, обладающая сильной поглотительной (адсорбционной) способностью. Необходимо принять меры к уменьшению поглотительной способности. Это осуществляется уплотняющей обработкой, при которой безводный оксид алюминия (Al2O3) переходит в гидратированный оксид алюминия (Al2O3·H2O), который имеет больший объем, вследствие чего заполняет пустое пространство пор. Процесс уплотнения состоит в погружении в кипящую воду или в растворы бихроматов, хроматов, силикатов или солей некоторых металлов, например, никелевых и кобальтовых.
Уплотнение в горячей воде - самый простой и распространенный метод в промышленности.
ПРАКТИЧЕСКАЯ ЧАСТЬ
Приготовить два образца листового алюминия с предварительно зачищенной наждачной бумагой поверхностью и провести с ними операции, приведенные в табл. 1.
|
|
|
|
|
Таблица 1 |
|
|
|
|
Режим |
|
№ опе- |
Наименование |
|
Состав |
||
ра-ции |
операции |
|
ванн |
работы |
|
1 |
Обезжиривание |
|
|
Na3PO4-5 г/л |
t=60..700C |
|
|
|
|
NaOH-10г/л |
время 3..5 мин |
|
|
|
|
жидкое стекло-30 г/л |
Время 0,3..0,5 мин |
2 |
Промывка в холодной про- |
H2O - вода |
|||
|
точной воде |
|
|
|
i=1,0..1,5 А/дм2, |
3 |
Оксидирование |
(анодирова- |
H2SO4 - 200 г/л |
||
|
ние) при токе |
|
|
|
V=12B, t=18..250C |
|
I = i .2Sобразца |
|
|
|
Время - 20 мин |
|
|
|
Время - 20 мин |
||
4 |
Промывка в холодной про- |
вода |
|||
|
точной воде |
|
|
|
t=70..800C |
5 |
Окрашивание |
оксидной |
сода кальцинированная – |
||
|
пленки органическими |
кра- |
0,05 - 0,1 г/л, |
время - 2 мин |
|
|
сителями (подвергать |
один |
красители: оранжевый 2- |
|
|
|
образец) |
|
|
ж - 1,6 г/л, желтый 3 - |
|
|
|
|
|
0,06 г/л, черный - 0,08 |
|
|
|
|
|
г/л |
Время 0,2..0,5 мин |
6 |
Промывка в холодной про- |
вода |
|||
|
точной воде |
|
|
|
t=90..1000C |
7 |
Уплотнение оксидной |
плен- |
дистиллированная вода |
||
|
ки |
|
|
|
время - 20 мин |
8 |
Сушка |
|
|
сушильный шкаф |
t=80..900С |
|
|
|
|
|
время - 10..15 мин |
23

Испытание качества пассивной пленки, полученной оксидированием (анодированием) при различных условиях на образцах листового алюминия.
Испытанию подлежат:
-поверхность алюминия, не подвергавшегося обработке и имеющая естественную пассивную пленку;
-оксидированная, окрашенная поверхность алюминия, неуплотненная
вгорячей воде;
-оксидированная, окрашенная поверхность алюминия, уплотненная в горячей воде.
Для испытания коррозионной устойчивости оксидной пленки на поверхность каждого образца наносят (из капельницы, глазной пипеткой) 1..2 капли раствора следующего состава:
HCl (уд. вес 1,19) 25 мл;
K2Cr2O7 3,0 мл; H2O 75 мл.
Дописать реакции, происходящие при определении толщины оксидной пленки:
Al2O3 + HCl = . . . . . . . . .
Al + K2Cr2O7 + HCl = . . . . . . . . . . . . . .
Толщина оксидной пленки устанавливается по времени (по числу минут) от начала нанесения капли на образец до начала ее позеленения.
Толщину оксидной (пассивной) пленки на образцах определяют с помощью табл.2.
|
|
|
|
|
|
Таблица 2 |
|
|
|
|
|
22..26 |
|
|
|
Температура, 0С |
11..13 |
14..17 |
18..21 |
27..32 |
|||
Норма |
времени, |
10 |
8 |
5 |
4 |
|
3 |
мин |
|
|
(время в минутах указано для толщины пленки порядка 5 мкм в соответствующем интервале температур)
В качестве отчета по лабораторной работе ответить на контрольные вопросы, сделать выводы по результатам работы.
КОНТРОЛЬНЫЕ ВОПРОСЫ
1.В чем сущность методов защиты алюминия от коррозии и условия их применения?
2.Какова сущность катодного и анодного процессов при электрохимической обработке алюминия?
3.Каков порядок выполнения практической части работы?
4.Как проводится испытание качества полученной оксидной пленки?
24
ЛИТЕРАТУРА
1.Коровин Н.В. Общая химия. – М.: Высш. шк. 2000. – 558 с.
2.Гальванотехника: Справочник. – М.: Металлургия, 1987. – 736 с.
3.Прикладная электрохимия./ Под ред. А.П. Томилова. – М.: Химия, 1984.-520с
25

Рис. 1. Схема роста окисной пленки |
Рис. 2. Схема |
образования |
при химическом пассивировании |
пассивной пленки на алюминии при |
|
алюминия (теоретическая схема) |
электрохимическом |
анодировании |
|
(реальная картина) |
|
Рис. 3. Электрическая схема лабораторной установки для анодирования алюминия переменным током.
26
ЛАБОРАТОРНАЯ РАБОТА № 24В
ГАЛЬВАНИЧЕСКОЕ МЕДНЕНИЕ
Цель работы: защита металлов от коррозии методом нанесения металлических покрытий. Изучить процесс получения медного покрытия на стальных образцах гальваническим способом, путем электролиза с растворимым анодом.
Рабочее задание: получить медное покрытие, определить выход меди по току, рассчитать толщину покрытия, удельный расход электроэнергии.
СВЕДЕНИЯ ИЗ ТЕОРИИ
Защитные свойства металлических покрытий
Металлические покрытия являются одним из распространенных способов защиты металлов от коррозии в электролитах и атмосфере. По характеру этой защиты различают анодные и катодные покрытия.
К анодным покрытиям относятся такие, которые в агрессивной среде обладают более отрицательным электродным потенциалом, чем защищае-
мый металл, т.е. металл-покрытие имеет более |
отрицательный потенциал, |
он находится левее защищаемого металла |
в ряду стандартных элек- |
тродных потенциалов. Например, оцинкованное железо. Потенциал цинка
E0 |
= −0,76B, по своей величине он электроотрицательнее потенциала |
|
Zn2+ / Zn |
|
|
железа |
E 0 |
= −0,44B. Поэтому в процессе коррозии покрытие является |
|
Fe2+ / Fe |
|
анодом. Отсюда название покрытия - анодное. |
||
К катодным покрытиям относятся такие металлы, которые имеют в |
данной коррозионной среде более положительный потенциал, чем защи-
щаемый |
металл. Примером |
этого |
может |
служить |
луженое |
железо |
||
( E 0 |
+ / Sn |
= −0,136B ), |
а также |
покрытия на |
железе (или |
стали): |
медное |
|
Sn 2 |
|
|
|
|
|
|
|
|
( E 0 |
+ / Cu |
= +0,34B), |
свинцовое ( E 0 |
= 0,12B). Поэтому при возникнове- |
||||
Cu 2 |
|
|
Pb2+ |
/ Pb |
|
|
|
нии коррозионного элемента и при его работе покрытие является катодом. Отсюда название покрытия - катодное (рис. 1). Катодный тип покрытия (например, медное) применяется чаще всего как промежуточный подслой между железом и другими покрытиями, например, никелем, хромом и т.д. Медь обеспечивает хорошее сцепление между основным металлом и поверхностью покрытия. В виде самостоятельного покрытия медь применяется с целью
27
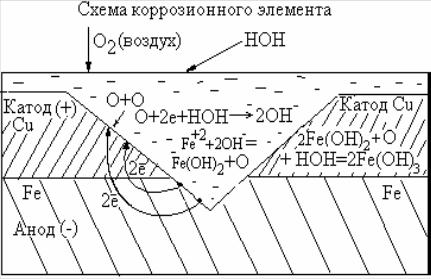
предохранения отдельных поверхностей стальных изделий от цементации, а также для повышения электропроводности стальной проволоки и ленты.
Рис. 1. Защитные свойства катодного медного покрытия
Гальваническое меднение
Гальваническое меднение производится в водных электролитах, содержащих CuSO4 и некоторые другие соединения. Наиболее простой из них так называемый "кислый" электролит. Он содержит CuSO4 и небольшое количество H2SO4. Однако в этом электролите железо на поверхности деталей реагирует с CuSO4, происходит контактное осаждение и поэтому медное покрытие не имеет достаточного сцепления с основой. Оно легко отслаивается. Железо и его сплавы хорошо покрываются медью в цианистом электролите (смесь Cu(СN)2, NaCN, Na2CO3). Но цианистые электролиты мало устойчивы, дороги и очень ядовиты. Достаточно часто в практике гальванического меднения применяются пирофосфатные электролиты (CuSO4, Na4P2O7, Na2HPO4). Этот электролит безопасен, обеспечивает хорошее качество медного покрытия. Он использован в данной работе. Корпус промышленной ванны для меднения (рис.2) обычно стальной, внутри футерован сырой резиной или винилпластом. Объем электролита - от 100 до 1000 л. На бортах ванны укреплены контактные устройства для подвески омедняемых деталей (катодов) и больших медных пластин - анодов. Получение покрытия осуществляется с помощью электролиза с растворимым анодом. Электрохимическую схему электролизной ванны можно представить в виде
A(+) Cu|CuSO4, Na2HPO4, H2O|Fe (-)K.
При пропускании постоянного тока через контактные устройства галь-
28
ванической ванны на электродах протекают следующие реакции.
На аноде происходит:
а) окисление меди по реакции
Cu0 - 2e → Cu2+ (полезный процесс); ионы меди переходят в электролит, масса анода убывает;
б) окисление воды:
2H2O - 4e → O2↑ + 4H+ (побочная реакция).
На катоде происходит:
а) восстановление катионов меди Cu2+ + 2e →Cu0 (полезная реакция);
б) восстановление ионов водорода, если электролит кислый 2H+ + 2e → H2↑ (побочная реакция);
в) восстановление молекул воды, если электролит щелочной
2H2O + 2e → H2↑ + 2OH-.
Таким образом, электрический ток расходуется не только на основные процессы (окисление меди на аноде и восстановление ее ионов на катоде), но и на побочные процессы: выделение водорода на катоде и образование кислорода на аноде. Поэтому процесс меднения проводится таким образом, чтобы свести до минимума выделение водорода и кислорода. С этой целью поддерживают определенные условия электролиза: состав электролита, его температуру, плотность тока (ik).
Для экономической оценки гальванического процесса осаждения металла введены такие понятия, как выход по току меди и удельный расход электроэнергии на получение медного покрытия.
Выход по току (ВТ) показывает долю от общего тока или количества электричества, израсходованного на полезный процесс. Выход по току есть отношение массы практически полученного металла к теоретически возможному
ВТ = |
m |
практ |
100% . |
(1) |
|
|
|
||||
mтеор |
|||||
Ме |
|
|
|||
|
|
|
Вес полученного металла (mпракт) определяется путем взвешивания деталей до меднения и после осаждения меди (в граммах).
Теоретически возможное количество меди определяется по закону Фарадея: количество вещества, окисленного на аноде, восстановленного на катоде, прямо пропорционально количеству прошедшего электричества (I τ) через границу электрод-электролит
m теор = |
I t ЭCu |
, |
(2) |
|
|||
|
F |
|
29

где I - сила тока, А;
t - время электролиза, ч;
F - число Фарадея, равное 26,8 А·ч/моль – количество электричества необходимое для окисления одного моля эквивалента вещества;
ЭCu – эквивалентная масса меди, г/моль
ЭCu = AnCu , (3)
где: АCu - атомная масса меди, г / моль;
n - число электронов, участвующих в реакции на катоде. Формула для расчета выхода меди по току (1) примет вид
|
|
mпракт 26,8 |
n |
|
|
ВТСu |
= |
|
|
100% . |
(4) |
I t AСu |
|
||||
|
|
|
|
|
Расчет расхода электроэнергии на получение единицы веса (г) металлического покрытия позволяет выбрать такие условия электролиза, которые обеспечили бы наименьшее напряжение на ванне. Для расчета количества электроэнергии W используют формулу
W = |
Q V |
= |
I t V |
, |
вт ч |
, |
(5) |
|
mпракт |
mпракт |
г |
||||||
|
|
|
|
|
где V - напряжение на ванне, В,
mСu практ. - количество полученной меди (г).
ПОРЯДОК ВЫПОЛНЕНИЯ РАБОТЫ (последовательность операций и их содержание)
1.Удостовериться в правильности сборки электрической схемы гальванического меднения согласно рис. 3.
2.Подготовить для меднения стальной образец:
-зачистить поверхность образца мелкозернистой наждачной бумагой;
-обезжирить в растворе щелочи (NaOH) в течение 2-3 минут;
-промыть в воде;
-протравить в растворе смеси кислот HCl + H2SO4 (20%) в течение 3-4 минут, промыть в воде;
-высушить фильтровальной бумагой;
-взвесить на аналитических весах, записав массу образца m1.
3. Рассчитать силу тока в цепи I при катодной плотности тока ik = 0,5 A/дм2 (500 А/м2) по формуле
I = ik·2·S,
30

где S - рабочая поверхность катода (дм2).
4. Завесить подготовленный (согласно пункту 2) катод в электролизер. С помощью реостата установить рассчитанную силу тока в цепи. Заметить время.
5. Осуществлять меднение при рассчитанной силе тока и комнатной температуре в течение 30 минут. Во время электролиза через каждые 5 минут замерять напряжение на ванне.
6. После 30 минут электролиза: - выключить выпрямитель; - вынуть медный образец; - промыть его водой;
- высушить его фильтровальной бумагой; - взвесить на аналитических весах, записав массу образца после
меднения m2.
7. Рассчитать выход по току меди согласно формуле (4).
8. Рассчитать удельный расход электроэнергии по формуле (5)
9. Определить среднюю толщину медного покрытия на основании привеса меди (mСu практ.) по формуле
δ = m Cu практ , S d
где δ - толщина покрытия, см.
mСu практ. - привес меди, г, S - площадь катода, см2;
d- удельный вес меди (d=9 г/см3).
10.В качестве отчета по лабораторной работе представить результаты расчетов выхода по току, расхода электроэнергии на 1 грамм покрытия, толщины покрытия и ответы на контрольные вопросы.
КОНТРОЛЬНЫЕ ВОПРОСЫ
1.В чем состоит сущность защиты металлов от коррозии с помощью металлических покрытий?
2.Опишите процессы, протекающие на электродах при меднении.
3.Каковы защитные свойства медного покрытия и его эффективность?
4.Приведите основные показатели эффективности процесса гальванического меднения (выход меди по току, удельный расход электроэнергии, толщину покрытия), их расчет и практическое применение.
31

Рис. 2. Разрез промышленной ванны для гальванического меднения:
1 - деревянный корпус,
2 - футеровка из сырой резины
3 - анодная штанга
4 – изоляторы
5 - медный анод
6 - катодная штанга
7 - детали на проволочной раме
8 - электролит
Рис. 3. Электрическая схема лабораторной установки для гальванического меднения
впирофосфатном электролите: а - электролизер для осаждения меди б - селеновый выпрямитель
в- понижающий трансформатор
г - амперметр д - реостат
32