
Методичка по строй мату 1
.pdf
ются с бетоном и отличаются индустриальностью производства. Плитки выпускают крупноразмерные (10×10, 10×20 см) и мелкоразмерные (48×48 мм). При производстве крупноразмерных железобетонных панелей облицовка из мелкоразмерной (ковровой) плитки оказывается менее трудоемкой и более производительной по сравнению с облицовкой крупноразмерной плиткой, которая укладывается поштучно вручную. На Ленинградском ДСК-2 для облицовки панелей используют стеклянную облицовочную плитку размером 2×2 см, которая наклеивается на картон заданных размеров. Для увеличения сцепления стеклянной поверхности плитки с раствором или бетоном ее тыльную поверхность покрывают кремнийорганическими составами типа ВН-30, которые обладают хорошей адгезией к стеклу. Стеклянные плитки выпускают различных цветов — от белого до черного. В качестве облицовочных материалов для отделки железобетонных стеновых панелей используют также цветные цементные плитки и алюминиевые листы. Последние обладают высокой атмосферостойкостью, прочностью и хорошими архитектурнодекоративными свойствами.
Цветные бетоны получают, используя неорганические мине-
ральные краски, обладающие высокой щелоче- и атмосферостой-
костью. Красная, желтая и коричневая окраски бетона могут быть получены путем добавления пигментов из оксидов железа, зеленая — при введении зеленого оксида или гидроксида хрома.
§. 11.6. Приемка и испытание железобетонных изделий
Приемка железобетонных изделий осуществляется партиями, которые состоят из однотипных изделий, изготовленных по одной
технологии в течение не более 10 дней. В зависимости от объема
изделий количество их в партии устанавливают техническими условиями и не должно превышать следующих величин:
В процессе приемки наружным осмотром проверяют внешний вид изделий, отмечают наличие трещин, раковин и других дефектов. Затем с помощью измерительных линеек и шаблонов проверяют правильность формы и габаритные размеры изделий. Если при контрольных замерах изделия будут выявлены отклонения по длине или ширине, превышающие допускаемые, то изделие бракуют.
При приемке изделий определяют и прочность бетона, которую устанавливают по результатам испытания контрольных образцов
ипутем испытания готовых изделий. Контрольные образцы с
—371 —
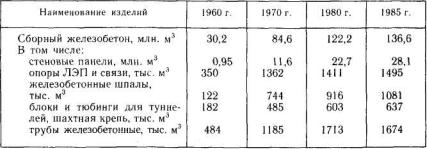
ребром 10, 15 и 20 см изготовляют в металлических разъемных формах в количестве не менее 3 шт. и не реже одного раза в смену, а также для каждого нового состава бетонной смеси. Уплотнение бетонной смеси в образцах осуществляют на стандартной виброплощадке с амплитудой 0,35 мм и частотой вращения З00 кол/мин.
Образцы должны твердеть в одинаковых условиях с изделиями. Предел прочности бетона определяют путем испытания образцов на гидравлических прессах и вычисляют как среднее арифметическое значение результатов испытания трех образцов.
Испытание готовых железобетонных изделий на прочность, жесткость и трещиностойкость производят согласно ГОСТам.
Отбор изделий для испытаний производят в количестве 1 % от каждой партии, но не менее 2 шт., если в партии менее 200 изделий. Испытание производят на специальных испытательных стендах, нагружая конструкцию гидродомкратами, штучными грузами или рычажными приспособлениями. Критерием прочности служит нагрузка, при которой изделие теряет свою несущую способность (разрушается).
В последнее время для определения прочности бетона в конструкциях пользуются методами, не разрушающими изделия, — физическими и механическими. К физическим методам относятся ультразвуковые и радиометрические. Механические методы основаны на определении величины упругой или пластической деформации. В первом случае прочность бетона оценивают по величине упругого отскока бойка от поверхности бетона; во втором прочность бетона характеризуется величиной отпечатка наконечника на поверхности бетона. Приборы этой группы получили широкое применение в строительстве.
§11.7. Экономика производства железобетонных изделий
Впоследнее время выпуск сборного железобетона в СССР как основы индустриализации строительства растет особенно быстрыми темпами (табл. 11.1).
Таблица 11.1. Производство сборных железобетонных конструкций и деталей
— 372 —

Из сборных железобетонных конструкций в настоящее время изготовляют почти целиком перекрытия жилых, гражданских и промышленных зданий, более 30% стен в государственном и кооперативном жилищном строительстве, 25...30% фундаментов зданий, более 50% каркасов одно- и многоэтажных промышленных зданий.
Расход сборного железобетона на 1 млн. руб. строительномонтажных работ в жилищном строительстве в истекшие годы быстро растет за счет увеличения удельного веса полносборных домов в общей структуре ввода жилых зданий, а также вследствие увеличения высоты сечения плит перекрытий и толщины панелей перегородок по условиям звукоизоляции, толщины панелей наружных стен в связи с ростом этажности. Существенно возрастают и общие объемы применения сборного железобетона в промышленном и жилищном строительстве.
На развитие производства сборного железобетона выделяют значительные капитальные вложения, и очень важно правильно использовать эти большие средства при проектировании новых и реконструкции действующих предприятий. Исключительно большое значение при этом имеет выбор рациональной технологической схемы производства железобетонных изделий в зависимости от мощности проектируемого завода, номенклатуры выпускаемой продукции, вида армирования, габаритов изделий и других факторов.
Анализ работы передовых предприятий показывает, что в одинаковых условиях (например, при производстве многопустотных настилов перекрытий) на узкоспециализированных производственных линиях, выпускающих по одному типоразмеру изделий, стендовая, агрегатная и конвейерная технологии дают различные технико-экономические показатели (табл. 11.2).
Как видно из приведенных данных, при стендовой технологии имеют место большие затраты труда, но минимальные удельные
Таблица 11.2. Перспективы технико-экономических показателей производственных линий с различными технологическими схемами
— 373 —
капиталовложения. Для конвейерной технологии при меньшей трудоемкости удельные капиталовложения максимальны, а для агрегатной технологии сочетаются относительно небольшие затраты труда со сравнительно низкими удельными капитальными вложениями.
При выборе технологической схемы производства цеха формования и пропаривания необходимо учитывать номенклатуру выпускаемых изделий и объемы производства, определяемые рациональным радиусом перевозки готовой продукции.
Для мелкосерийного производства железобетонных изделий на заводах малой и средней мощности наиболее выгодным оказывается поточно-агрегатный способ производства. При несложном технологическом оборудовании, небольших производственных площадях и небольших затратах на строительство агрегатный способ дает возможность получить высокий съем готовой продукции с 1 м2 производственной площади цеха. Этот метод позволяет также оперативно осуществлять переналадку оборудования и переходить к формованию от одного вида изделий к другому без существенных затрат. Производительность формовочного агрегата зависит от вида и размеров формуемых изделий и будет изменяться при переходе от одного вида изделий к другому. Это вызвано изменением продолжительности цикла формования изделий, который может колебаться в большом диапазоне (5...30 мин). Проточно-агрегатный способ наиболее распространен в современной технологии сборного железобетона.
По капитальным затратам преимущество остается за стендовым способом при формовании изделий на горизонтальных стендах. Простота оборудования, незначительная его энергоемкость, возможность легко перейти на выпуск изделий самых разнообразных типоразмеров, минимум транспортных операций — основные достоинства этого способа организации формования. Однако при горизонтальном формовании изделий на стендах оказывается значительной потребность в производственных площадях. Низкий уровень механизации влечет высокую трудоемкость, в 2...3 раза превышающую, например, трудоемкость изготовления изделий по поточно-агрегатной технологии. Применение маломощных переносных вибраторов возможно для уплотнения бетонной смеси с высокой подвижностью, что вызывает перерасход цемента.
Все эти факторы исключили целесообразность организации производства изделий массового выпуска (плит и панелей перекрытий, панелей и блоков стен, фундаментных блоков и плит) по стендовой технологии. Однако при небольшом среднегодовом объеме таких изделий стендовый способ может оказаться наиболее рациональным. Целесообразен он и при организации производства железобетонных изделий на временных полигонных установках.
Рациональность применения стендового способа возрастает с увеличением массы и размера изделий, перемещение которых по
— 374 —
отдельным технологическим постам влечет большие затраты или практически трудноосуществимо. Это относится к фермам и балкам длиной 18 м и более, пролетным строениям мостов массой до 100 т и более, аркам и другим уникальным элементам сборного железобетона значительной массы, что определяет техникоэкономические преимущества стендового способа при изготовлении указанных видов изделий. Стендовую технологию наиболее широко применяют на открытых полигонах мощностью до 10...
15 тыс. м /год.
При стендовом методе производства оборудование может быть легко демонтировано и так же легко собрано на любом участке строительства. Производительность стенда зависит от продолжительности выдерживания на нем изделия. В зависимости от вида изделий время, необходимое для выдерживания изделий на стенде, колеблется от 20 ч до 5 сут.
Конвейерный метод производства железобетонных изделий позволяет добиться комплексной механизации и автоматизации технологических процессов изготовления изделий. Организация производства по конвейерному методу обеспечивает значительное повышение производительности труда и увеличение выпуска готовой продукции при наиболее полном и эффективном использовании технологического оборудования. Однако конвейерная технология требует больших капитальных вложений. Применение этого метода рационально на заводах, выпускающих в массовом порядке изделия по ограниченной номенклатуре с минимальным количеством типоразмеров.
Кассетный способ применяют при изготовлении тонких и плоских изделий значительной площади (перегородок стен, панелей перекрытий). Удельная потребность в площадях производственного цеха при кассетном способе (в вертикальном положении) самая минимальная — в одном месте одновременно формуется до 12 изделий площадью до 12 м2 каждая. Отсутствие виброплощадок и камер пропаривания является важным достоинством кассетного способа. И все же он имеет весьма существенные недостатки. Эффективно уплотнить в кассете, имеющей глубокие отсеки, можно только смесь, достаточно подвижную, а это достигается при получении бетона заданной прочности с повышенным расходом цемента. Ограниченность номенклатуры — также недостаток кассетного способа. В кассетах многосекционной конструкции могут изготовляться только плоские изделия сплошного сечения. Технологическая схема и организация формования изделий определяются многими факторами, ведущими среди которых являются производственная мощность предприятия, вид и размеры изделий, техническая возможность и экономическая целесообразность механизации и автоматизации процессов, характер применяемых бетонных смесей при том или ином способе. Правильная оценка перечисленных факторов определяет в конечном счете рациональную технологию, наиболее выгодную для конкретных условий.
— 375 —
Важнейшая задача развития промышленности сборного железобетона на современном этапе — это повышение уровня концентрации его производства, рост технической оснащенности предприятий. Характерно, что наряду с наличием значительного количества высокомеханизированных и рентабельных предприятий в промышленности сборного железобетона существует большая группа мелких цехов и заводов, выпускающих продукцию с большими затратами и, как правило, недостаточно высокого качества. На долю мелких предприятий со среднегодовой мощностью около 10 тыс. м.3 приходится около 2/3 всех предприятий и более 1/5 продукции.
По данным Индустройпроекта МПСМ СССР, по учтенному кругу предприятий сборного железобетона, охватывающему более 4/5 продукции отрасли, себестоимость в зависимости от мощности изменялась следующим образом. Для более крупных предприятий со среднегодовой мощностью более 100 тыс. м.3 себестоимость 1 м изделий была на 1/3 меньше, чем по мелким заводам. Концентрация и специализация производства при создании специализированных предприятий мощностью 100...
150 тыс. м.3 и более с узко ограниченной номенклатурой изделий на каждом заводе позволяет снизить удельные капиталовложения примерно на 20...25%, а себестоимость продукции — на 15...20% по сравнению с действующими универсальными заводами со средней мощностью 30...50 тыс. м 3. Поэтому генеральной линией развития промышленности сборного железобетона является повышение уровня концентрации и специализации производства.
Использование действующих производственных мощностей в промышленности сборного железобетона недостаточно. Важными условиями лучшего использования основных производственных фондов являются ускорение освоения проектных производственных мощностей на основе опыта передовых предприятий по реализации резервов роста производства, увеличение объемов продукции с действующих мощностей на основе интенсификации производства и улучшение эксплуатации оборудования.
Необходимо всемерно улучшить использование оборудования, что является важнейшим резервом роста фондоотдачи и повышения рентабельности в промышленности. Хотя показатели работы оборудования в промышленности сборного железобетона в последние годы улучшились, здесь также имеются большие неиспользованные резервы.
Анализ данных табл. 11.3 показывает, что технологическое оборудование на ряде заводов сборного железобетона используется в 1,5...2 раза ниже норм технологического проектирования и уровня, достигнутого многими предприятими Москвы и Ленинграда.
На предприятиях сборного железобетона оборачиваемость ямных камер в среднем однократная в сутки, а на лучших предприятиях достигнута — почти двукратная. Цикл формования
— 376 —

изделий составляет в среднем по СССР 20...25 мин, на передовых заводах — 9... 11 мин (табл. 11.3).
Таблица 11.3. Показатели использования основного технологического оборудования промышленности сборного железобетона
Наряду с ростом часовой производительности оборудования большие резервы заключены также в повышении коэффициента сменности и сокращении внутрисменных простоев в отраслях с прерывным производством.
Важным направлением технического прогресса в промышленности строительных материалов является применение электроэнергии на технологические цели. При производстве сборных железобетонных изделий простой формы (фундаментных блоков, колонн и балок прямоугольного сечения, однослойных стеновых панелей, плоских плит покрытий и перекрытий) экономический эффект достигается в результате электропрогрева, благодаря которому расход тепла по сравнению с пропариванием сокращается в 2...4 раза. Имеется большая возможность автоматизации процесса контроля и управления на участке тепловлажностной обработки и улучшения условий труда. Устранение необходимости в сооружении котельных, теплосетей и пропарочных камер приводит к существенной экономии капитальных затрат.
Стоимость электроэнергии для прогрева 1 м3 бетонных и железобетонных изделий ниже стоимости пара, необходимого для пропаривания этих изделий.
Таким образом, основные пути снижения себестоимости предприятий сборного железобетона — это улучшение использования производственных мощностей, внедрение новой техники и технологии, улучшение организации труда, унификация конструкций, рост уровня специализации и концентрации производства, применение высокомарочных цементов, термически упрочненных сталей, совершенствование тепловлажностной обработки изделий, налаживание работы арматурных цехов, повышение уровня комплексной механизации производства, повышение качества нерудных строительных материалов.
Большие резервы увеличения эффективности производства сборного железобетона заключены в повышении уровня его концентрации и специализации, развитии реконструкции.
Расчеты эффективности предприятий сборного железобетона для жилищного строительства в зависимости от расстояния
— 377 —
доставки изделий по суммарным приведенным затратам показали, что обусловленное ростом концентрации производства увеличение затрат на перевозку конструкций для крупнопанельного домостроения автотранспортом до 100 км полностью перекрывается экономией приведенных затрат на крупных предприятиях.
В связи с ростом объемов строительства и повышением плотности потребления сборного железобетона экономически обоснованная концентрация производства в ближайшей перспективе не приводит к повышению расстояния перевозки изделий и, следовательно, снижение себестоимости продукции на крупных заводах будет, как правило, способствовать дальнейшему уменьшению стоимости жилищного строительства. Массовыми типами предприятий крупнопанельного домостроения целесообразно считать заводы годовой производительностью 140 и 160 тыс. м.2 жилой площади в год.
Рост средней мощности предприятий сборного железобетона для промышленного строительства во многом зависит от повышения уровня унификации конструкции и роста уровня сборности в промышленном строительстве в связи с увеличением объемов применения сборного железобетона. В качестве массовых типов заводов для промышленного строительства в ближайшей перспективе приняты предприятия со среднегодовой мощностью 100 и 200 тыс. м3, причем для каждого конкретного района сочетание вновь строящихся заводов, различных по мощности, устанавливается на основе специального экономического расчета. Повышение степени концентрации производства сборного железобетона является в целом одним из важнейших условий снижения себестоимости продукции и удельных капитальных вложений.
Большие резервы роста эффективности производства заключены в повышении уровня специализации производства и сокращении количества типоразмеров изделий. По данным ЦСУ СССР, съем продукции на специализированных предприятиях с 1 м2 производственных площадей равен около 20 м в год против 8...9 м3 в среднем по промышленности. На специализированных предприятиях себестоимость аналогичных изделий в 1,3...1,5 раза ниже среднего уровня. Удельный вес специализированного производства в 1965 г. составил около 35% от общего выпуска железобетонных изделий, в 1970 г. — около 45%, а в 1985 г. — более 62%. Согласно расчетам НИИЭС и Гипростроммаша, целесообразно уже в ближайшие годы довести удельный вес продукции специализированных предприятий и цехов промышленности сборного железобетона до 70...80% от общего объема производства, в том числе по спецжелезобетону — 100%, жилищ- но-гражданскому строительству — 75...80%, по промышленному строительству — 65...70% и сельскохозяйственному строитель-
ству — 55...70%.
Реальным путем повышения эффективности и снижения удельных капитальных вложений в промышленности сборного железобетона является увеличение удельного веса рациональных
— 378 —
типов реконструкции и расширения предприятий в достижении общего прироста мощности в ближайшей перспективе. Так, удельные капитальные вложения на полную реконструкцию и расширение предприятий составляют: по прогрессивным проектам по изделиям для промышленного строительства — 50 руб/м3 против 75...85 руб/м3; по изделиям для жилищного строительства — 43 руб/м3 против 70...77 руб/м3.
Таким образом, осуществление в целесообразных случаях реконструкции и расширения действующих предприятий обеспечивает экономию капитальных вложений по сравнению с вариантом нового строительства 38..45%. В ближайшей перспективе целесообразно определение структуры прироста мощностей за счет реконструкции и расширения предприятий как наиболее экономичных направлений использования капитальных вложений.

ГЛАВА 12 ЛЕСНЫЕ МАТЕРИАЛЫ
12.А. ДРЕВЕСИНОВЕДЕНИЕ
Наша страна обладает огромными запасами древесины — около 30% всей ее территории занимают леса. Особенно велики запасы древесины на Урале, в Сибири, Карельской АССР.
Древесина как строительный материал обладает рядом поло жительных свойств: она имеет относительно высокую проч ность, небольшую плотность, малую теплопроводность, легко
поддается механической обработке. Вместе с тем древесина имеет
и ряд недостатков: анизотропность древесины обусловливает различные показатели прочности и теплопроводности вдоль и поперек волокон; гигроскопичность приводит к изменению свойств; древесина подвержена загниванию и легко воспламе няется. Современная технология обработки древесины позволяет
взначительной мере снизить указанные недостатки.
Внастоящее время эффективно используются и отходы древесины: из опилок и стружек наряду с фибролитовыми и ксилолитовыми изделиями изготовляют с применением различных органических клеев прессованные плиты, доски и т. д. На передовых деревообрабатывающих комбинатах коэффициет использования древесного сырья достигает 0,98. Кроме того, древесину используют для производства целлюлозы, этилового и бутилового спиртов, бумаги, картона, органических кислот, канифоли и других продуктов для народного хозяйства. Поэтому экономное расходование древесины в строительстве является очень важной задачей.
§ 12.1. Строение дерева
Дерево состоит из ствола, кроны и корней. Корни предна значены для укрепления дерева в грунте, для всасывания влаги
ирастворенных в ней минеральных веществ и подачи их к ство лу. Ствол удерживает крону и служит для перемещения воды
ипитательных веществ от корней через ветви к листьям, а от листьев обратно к корням. Строение древесины, видимое не вооруженным глазом или при небольшом увеличении, называет ся макроструктурой, а видимое под сильным увеличением (микроскопом) — микроструктурой.
Макроструктуру древесины изучают по трем разрезам ствола дерева (рис. 1 2 . 1 ) : поперечному, радиальному продольному
(по диаметру или радиусу) и тангентальному продольному (по
хорде). В поперечном и радиальном разрезах ствола различают
— 380 —