
Методичка по строй мату 1
.pdfпринципиальным схемам: стендовой, поточно-агрегатной и конвейерной.
При изготовлении изделий в неперемещаемых формах все технологические операции, от подготовки форм до распалубки готовых отвердевших изделий, осуществляются на одном месте. К этому способу относится формование изделий на плоских стендах или матрицах, в кассетах.
При изготовлении изделий в перемещаемых формах отдельные технологические операции формования или отдельный комплекс их производятся на специализированных постах. Форма, а затем изделие вместе с формой перемещаются от поста к посту по мере выполнения отдельных операций. В зависимости от степени расчлененности общего технологического процесса формования по отдельным постам различают конвейерный, имеющий наибольшую расчлененность, и поточно-агрегатный способы. Последний отличается тем, что ряд операций — укладка арматуры и бетонной смеси, уплотнение — выполняются на одном посту, т. е. сагрегированы между собой. При конвейерном способе большинство операций выполняется на соответствующих постах, образующих в совокупности технологическую линию.
§ 11.1. Способыуплотнениябетоннойсмеси
Одно из важнейших свойств бетонной смеси — способность пластически растекаться под действием собственной массы или приложенной к ней нагрузки. Это и определяет сравнительную легкость изготовления из бетонной смеси изделий самого разнообразного профиля и возможность применения для ее уплотнения различных способов. При этом способ уплотнения и свойства смеси (ее подвижность или текучесть) находятся в тесной связи. Так, жесткие нетекучие смеси требуют энергичного уплотнения, и при формовании из них изделий следует применять интенсивную вибрацию или вибрацию с дополнительным прессованием (пригрузом). Возможны также и другие способы уплотнения жестких смесей — трамбование, прессование, прокат.
Подвижные смеси легко и эффективно уплотняются вибрацией. Применение же сжимающих (прессующих) видов уплотнения — прессования, проката, а также и трамбования — для таких смесей непригодно. Под действием значительных прессующих усилий или часто повторяющихся ударов трамбовки смесь будет легко вытекать из-под штампа или разбрызгиваться трамбовкой.
Литые смеси способны уплотняться под действием собственной массы. Для повышения эффекта уплотнения их иногда подвергают кратковременной вибрации.
Таким образом, могут быть выделены следующие способы уплотнения бетонных смесей: вибрирование, прессование, прокат, трамбование и литье. Наиболее эффективным как в техническом, так и в экономическом отношениях является способ вибрирования. Его успешно применяют также в сочетании с другими способами
— 341 —
механического уплотнения — трамбованием (вибротрамбование), прессованием (вибропрессование), прокатом (вибропрокат). Разновидностью механических способов уплотнения подвижных бетонных смесей является центрифугирование, используемое при формовании полых изделий трубчатого сечения. Хорошие результаты в отношении получения бетона высокого качества дает вакуумирование смеси в процессе ее механического уплотнения (преимущественно вибрированием), однако значительная продолжительность операции вакуумирования существенно снижает ее технико-экономический эффект, и поэтому этот способ мало распространен в технологии сборного железобетона.
Рассмотрим кратко сущность приведенных выше способов уплотнения бетонных смесей.
Вибрирование — уплотнение бетонной смеси в результате передачи ей часто повторяющихся вынужденных колебаний, в совокуп-
ности выражающихся встряхиванием. В каждый момент встряхи-
вания частицы бетонной смеси находятся как бы в подвешенном состоянии и нарушается связь их с другими частицами. При последующем действии силы толчка частицы под собственной массой падают и занимают при этом более выгодное положение, при котором на них в меньшей степени могут воздействовать толчки. Это отвечает условию наиболее плотной их упаковки среди других, что в конечном итоге приводит к получению плотной бетонной смеси. Второй причиной уплотнения бетонной смеси при вибрировании является свойство переходить во временно текучее состояние под, действием приложенных к ней внешних сил, которое называется тиксотропностью. Будучи в жидком состоянии, бетонная смесь при вибрировании начинает растекаться, приобретая конфигурацию формы, и под действием собственной массы уплотняться. Третья причина уплотнения определяет высокие технические свойства бетона.
Высокая степень уплотнения бетонной смеси вибрированием достигается применением оборудования незначительной мощности. Например, бетонные массивы емкостью несколько кубометров уплотняют вибраторами с мощностью привода всего 1...1,5 кВт.
Способность бетонных смесей переходить во временно текучее состояние под действием вибрации зависит от подвижности смеси и скорости перемещения при этом частиц ее относительно друг друга. Подвижные смеси легко переходят в текучее состояние и требуют небольшой скорости перемещения. Но с увеличением жесткости (уменьшением подвижности) бетонная смесь все более утрачивает это свойство или требует соответствующего увеличения скорости колебаний, т. е. необходимы более высокие затраты энергии на уплотнение.
Скорость v (см/с) колебаний при вибрировании выражают произведением амплитуды А на частоту п колебаний: v = An. При постоянной частоте колебаний вибромеханизма (для большинства виброплощадок равной 3000 кол/мин) изменение скорости колебаний может быть достигнуто изменением величины
— 342 —
амплитуды. Практика показала, что подвижные бетонные смеси эффективно уплотняются при амплитуде колебаний 0,3...0,35 мм,
а жесткие — 0,5...0,7 мм.
На качество виброуплотнения оказывают влияние не только параметры работы вибромеханизма (частота и амплитуда), но также продолжительность вибрирования. Для каждой бетонной смеси в зависимости от ее подвижности существует своя оптимальная продолжительность виброуплотнения, до которой смесь уплотняется эффективно, а сверх которой затраты энергии возрастают в значительно большей степени, чем происходит уплотнение смеси. Дальнейшее уплотнение вообще не дает прироста плотности. Более того, чрезмерно продолжительное вибрирование может привести к расслаиванию смеси, разделению ее на отдельные компоненты — цементный раствор и крупные зерна заполнителя, что в конечном счете приведет к неравномерной плотности изделия по сечению и снижению прочности в отдельных частях его.
Естественно, что продолжительное вибрирование невыгодно и в экономическом отношении: возрастают затраты электроэнергии
итрудоемкость, снижается производительность формовочной
линии.
Интенсивность И (см2/с3) виброуплотнения, выраженная наименьшей продолжительностью вибрирования, зависит также от основных параметров работы вибромеханизма — частоты и ам-
плитуды колебаний, применяемых с учетом их взаимного сочетания скорости и ускорения колебаний: И = А2/п3.
Интенсивность виброуплотнения также возрастает, если частота вынужденных колебаний оказывается равной частоте собственных колебаний. В связи с тем что бетонная смесь имеет большой диапазон размеров частиц (от нескольких микрометров для цемента до нескольких сантиметров для крупного заполнителя)
исоответственно различия в частоте их собственных колебаний, наиболее интенсивное уплотнение смеси будет в том случае, когда режим вибрирования характеризуется различными частотами. Так возникло предложение применять поличастотное вибрирование.
Эти факторы следует учитывать для технико-экономической оценки операций формования изделий. Из сказанного следует, что эффективность уплотнения возрастает с увеличением энергии уплотнения, продолжительность уплотнения при этом снижается и производительность формовочной линии повышается. Таким образом, на основании технико-экономического анализа свойств бетонной смеси, производительности формовочной линии можно выбрать мощность виброуплотняющих механизмов.
Виброуплотнение бетонной смеси производят переносными и стационарными вибромеханизмами. Применение переносных вибромеханизмов в технологии сборного железобетона ограничено. Их используют в основном при формовании крупноразмерных массивных изделий на стендах.
Втехнологии сборного железобетона на заводах, работающих
—343 —

по поточно-агрегатной и конвейерной схемам, применяют виброплощадки. Виброплощадки отличаются большим разнообразием типов и конструкций вибраторов — электромеханические, электромагнитные, пневматические; характером колебаний — гармонические, ударные, комбинированные; формой колебаний — круговые, направленные — вертикальные, горизонтальные; конструктивными схемами стола — со сплошной верхней рамой, образующей стол с одним или двумя вибрационными валами, и собранные из отдельных виброблоков, в целом представляющих общую вибрационную плоскость, на которой располагается форма с бетонной смесью.
Для прочности крепления формы к столу площадки предусматриваются специальные механизмы — электромагниты пневматические или механические прижимы.
Виброплощадка (рис. 11.1) представляет собой плоский стол, опирающийся через пружинные опоры на неподвижные опоры или раму (станину). Пружины предназначены гасить колебания стола и предупреждать этим их воздействие на опоры, иначе произойдет их разрушение. В нижней части к столу жестко прикреплен вибровал с расположенными на нем эксцентриками. При вращении вала от электромотора эксцентрики возбуждают колебания стола, передающиеся затем форме с бетонной смесью, в результате происходит ее уплотнение. Мощность виброплощадки оценивается ее грузоподъемностью (масса изделия вместе с формой), которая составляет 2...30 т.
Заводы сборного железобетона оборудованы унифицированными виброплощадками, с частотой вращения 3000 кол/мин и амплитудой 0,3...0,6 мм. Эти виброплощадки хорошо уплотняют жесткие бетонные смеси конструкций длиной до 18 м и шириной до 3,6 м.
При формовании изделий на виброплощадках, особенно из жестких бетонных смесей на пористых заполнителях, в целях
улучшения структуры бетона используют пригрузы — статический, |
|
||||
|
вибрационный, пневматический, |
||||
|
вибропневматический. |
Величина |
|||
|
пригруза в зависимости от свойств |
||||
|
бетонной смеси составляет 2...5 |
||||
|
кПа. |
|
|
|
|
|
При формовании изделий в |
||||
|
неподвижных формах уплотнение |
||||
|
бетонной |
смеси |
производят |
с |
|
|
помощью |
|
поверхностных, |
||
|
глубинных и навесных вибраторов, |
||||
|
которые крепят к форме. При |
||||
Рис. 11.1. Одновальная виброплощад- |
изготовлении |
изделий |
в |
||
ка: |
горизонтальных |
|
формах |
||
1 — форма; 2 — вибрационная рама; 3 — применяют |
жесткие |
или мало- |
|||
пружины; 4 — вал; 5 — дебаланс; 6 — под- подвижные бетонные смеси, а при |
|||||
шипники; 7 — муфта сцепления; 8 |
формовании в вертикаль- |
|
|||
— электродвигатель |
|
||||
|
344 — |
|
|
|
|
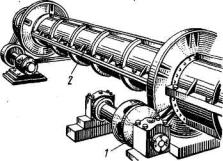
ных формах (в кассетах) применяют подвижные смеси с осадкой конуса 8...10 см.
Прессование — редко применяемый способ уплотнения бетон ной смеси в технологии сборного железобетона, хотя по техниче ским показателям отличается большой эффективностью, позволяя получать бетон высокой плотности и прочности при минимальном расходе цемента (100...150 кг/м3 бетона); Распространению спо соба прессования препятствуют исключительно экономические причины. Прессующее давление, при котором бетон начинает эффективно уплотняться, — 10...15 МПа и выше. Таким образом, для уплотнения изделия на каждый 1 м2 его следует приложить нагрузку, равную 10... 15 МН. Прессы такой мощности в технике применяют, например, для прессования корпусов судов, но стои мость их оказывается столь высокой, что полностью исключает экономическую целесообразность использования таких прессов.
В технологии сборного железобетона прессование используют как дополнительное приложение к бетонной смеси механической нагрузки при ее вибрировании. В этом случае потребная величина прессующего давления не выходит за пределы 500... 1000 Па. Технически такого давления достигают под действием статически приложенной нагрузки в результате принудительного перемещения отдельных частиц бетонной смеси.
Различают прессование штампами плоскими и профильными. Последние передают свой профиль бетонной смеси. Так формуют лестничные марши, некоторые виды ребристых панелей. В последнем случае способ прессования называют еще штампованием. Прокат является разновидностью прессования. В этом случае прессующее давление передается бетонной смеси только через небольшую площадь катка, что соответственно сокращает потребность в давлении прессования. Но здесь особую значимость приобретают пластические свойства бетонной смеси, связность ее массы. При недостаточной связности будет происходить сдвиг смеси прессующим валком и разрыв ее.
Центрифугирование— уп |
|
|||||
лотнение |
бетонной смеси в |
|
||||
результате действия центро |
|
|||||
бежных сил, возникающих в |
|
|||||
ней при вращении. Для |
|
|||||
этой цели применяют цент |
|
|||||
рифуги (рис. 11.2), пред |
|
|||||
ставляющие |
собой |
форму |
|
|||
трубчатого сечения, которой |
|
|||||
в процессе |
уплотнения со |
|
||||
общается вращение до 600... |
|
|||||
1000 мин-1. Загруженная в |
|
|||||
форму бетонная смесь (обя |
|
|||||
зательно |
подвижной |
конси |
Рис. 11.2. Центрифуга для изготовления |
|||
стенции) |
под |
действием |
||||
центробежных |
сил, |
разви- |
труб: 1 — опорные |
|||
ролики; 2 — форма |
||||||
|
|
|
|
|
||
|
|
— 345 — |
|
|
вающихся при вращении, прижимается к внутренней поверхности формы и уплотняется при этом. В результате различной плотности твердых компонентов бетонной смеси и воды из бетонной смеси удаляется до 20...30% воды, что способствует получению бетона высокой плотности.
Способ центрифугирования сравнительно легко позволяет получать изделия из бетона высокой плотности, прочности (40...60 МПа) и долговечности. При этом для получения бетонной смеси высокой связности требуется большое количество цемента (400...450 кг/м3), иначе произойдет расслоение смеси под действием центробежных сил на мелкие и крупные зерна, так как последние с большой силой будут стремиться прижаться к поверхности формы. Способом центрифугирования формуют трубы, опоры линий электропередач, стойки под светильники.
При вакуумировании в бетонной смеси создается разрежение до 0,07...0,08 МПа и воздух, вовлеченный при ее приготовлении и укладке в форму, а также немного воды удаляется из бетонной смеси под действием этого разрежения: освободившиеся при этом места занимают твердые частицы и бетонная смесь приобретает повышенную плотность. Кроме того, наличие вакуума вызывает прессующее действие на бетонную смесь атмосферного давления, равного величине вакуума. Это также способствует уплотнению бетонной смеси. Вакуумирование сочетается, как правило, с вибрированием. В процессе вибрирования бетонной смеси, подвергнутой вакуумированию, происходит интенсивное заполнение твердыми компонентами пор, образовавшихся при вакуумировании на месте воздушных пузырьков и воды. Однако вакуумирование в техническом отношении имеет важный технико-экономический недостаток, а именно: большую продолжительность процесса — 1...2мин на каждый 1 см толщины изделия в зависимости от свойств бетонной смеси и величины сечения. Толщина слоя, которая может быть подвергнута вакуумированию, не превышает 12... 15 см. Вследствие этого вакуумированию подвергают преимущественно массивные конструкции для придания поверхностному слою их особо высокой плотности. В технологии сборного железобетона вакуумирование практически не находит применения.
§11.2. Армирование железобетонных изделий
Взаводском производстве на долю арматуры приходится около 20% себестоимости железобетонных изделий, поэтому вопросы организации арматурных работ на заводах сборного железобетона являются важнейшими и в техническом, и в экономическом отношениях.
Различают армирование железобетонных изделий ненапряженное (обыкновенное) и предварительно напряженное. Операции армирования и виды арматуры, применяемые при каждом
—346 —
из этих способов армирования, имеют ряд принципиальных отличий.
Ненапряженное армирование осуществляется с помощью плоских сеток и пространственных (объемных) каркасов, изготовленных из стальных стержней различного диаметра, сва-
ренных между собой в местах пересечений. В железобетоне
различают арматуру несущую (основную) и монтажную (вспомогательную) . Несущая арматура располагается в местах изделия, в которых под нагрузкой возникают растягивающие напряжения; арматура воспринимает их. Монтажная арматура располагается в сжатых или ненапряженных участках изделия. Кроме этих видов арматуры применяют петли и крюки, необходимые при погрузочных работах, а также закладные части, крепления и связи сборных элементов между собой.
Наименьшие трудовые затраты на армирование изделий и конструкций будут при применении арматурных каркасов наибольшей степени готовности, т. е. состоящих не только из основной арматуры, но и из вспомогательной с приваренными петлями, крюками, закладными деталями. В этом случае операция по армированию сводится к установке готового арматурного каркаса в форму его и закреплению.
Арматурные сетки и каркасы изготовляют в арматурном цехе, оборудованном резательными, гибочными и сварочными аппаратами. Процесс производства строится по принципу единого технологического потока, от подготовки арматурной стали до получения готового изделия. Арматурные сетки и каркасы изготовляют в соответствии с рабочими чертежами, в которых указаны длина и диаметр стержней, их количество, расстояние между ними, места приварки закладных деталей и расположения монтажных петель. При установке и раскреплении каркасов
вформе необходима высокая точность, так как от этого зависит величина защитного слоя бетона в изделии, иначе может возникнуть коррозия арматурной стали.
Стержневую арматурную сталь диаметром до 10 мм поставляют на завод в мотках (бухтах), а диаметром от 10 мм и более — прутках длиной 6...12 м или мерной длины, оговариваемой
взаказах. Арматурную проволоку поставляют в мотках, причем каждый моток состоит из одного отрезка проволоки. Изготовление арматуры складывается из следующих операций: подготовки проволочной и прутковой стали — чистки, правки, резки, стыкования, гнутья; сборки стальных стержней в виде плоских сеток и каркасов; изготовления объемных арматурных каркасов, включая приварку монтажных петель, закладных частей, фиксаторов. Подготовка арматуры, поступающей на завод в мотках и бухтах, заключается в их размотке, выпрямлении (правке), очистке и разрезке на отдельные стержни заданной длины. Правку и резку арматурной стали осуществляют на правильноотрезных станках-автоматах.
Прутковую арматурную сталь разрезают на стержни задан-
—347 —
ной длины, а также стыкуют сваркой в целях уменьшения отходов. Стыкуют стержни посредством контактной стыковкой электросварки и только в отдельных случаях при использовании стержней больших диаметров применяют дуговую сварку. Контактную стыковую сварку осуществляют методом оплавления электрическим током торцов стержней в местах их будущего стыка. При этом стержни сильно сжимают и сваривают между собой.
При изготовлении монтажных петель, хомутов и других фигурных элементов арматуры прутковую и проволочную арматурную сталь после разрезки подвергают гнутью.
Сборку сеток и каркасов из стальных арматурных стержней производят посредством точечной контактной электросварки. Сущность ее заключается в следующем. При прохождении электрического тока через два пересекающихся стержня в местах их контакта электрическое сопротивление оказывается наибольшим, стержни в этом месте разогреваются и, достигнув пластического состояния металла, свариваются между собой. Прочной сварке способствует также сильное сжатие стержней между собой. Процесс точечной сварки может длиться доли секунды при применении тока в несколько десятков тысяч ампер.
Точечную сварку осуществляют с помощью специальных сварочных аппаратов. Они отличаются мощностью трансформатора, количеством одновременно свариваемых точек (одно- и многоточечные), характером используемых устройств для сжатия свариваемых стержней. Сварочные машины позволяют создавать в комплексе с другими машинами и установками поточные автоматические линии изготовления плоских сеток как готового арматурного элемента, так и полуфабрикатов для изготовления пространственных каркасов.
На рис. 11.3 приведена автоматическая линия для сварки широких сеток. В состав линии входят групповые бухтодержатели продольной и поперечной подачи, правильные устройства, сварочная машина МТМС с отрезным устройством. В линии предусмотрена электромагнитная система программирования подачи поперечных и дополнительных продольных стержней, пневматические ножницы для поперечной резки сетки, посты для приварки закладных деталей и устройства для фиксаторов. Поточное выполнение всех операций по изготовлению арматурных сеток на одной технологической линии значительно снижает трудоемкость процесса по сравнению с доработкой сеток на кондукторах, выполняемой обычно вручную.
Изготовление пространственных арматурных каркасов производят в основном из плоских сеток, соединяемых между собой на специальных сварочных машинах. Сборка каркасов может производиться в горизонтальном и вертикальном положениях.
Для удобства соединения узлов клещами для точечной сварки применяют вертикальный кондуктор (рис. 11.4). Плоские элементы арматуры укладывают между штырями кондуктора, которы-
— 348 —
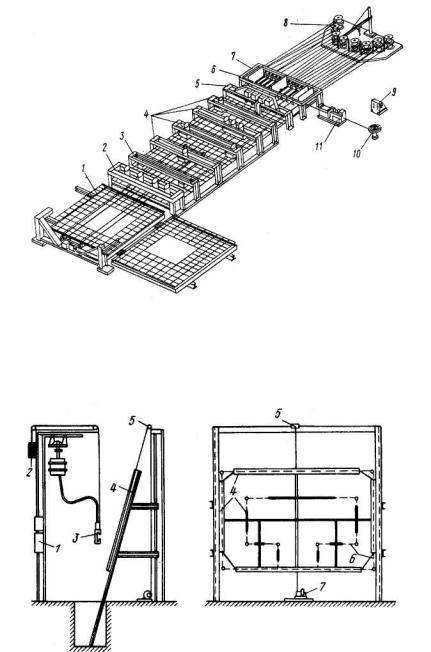
Рис. 11.3. Автоматизированная линия для сварки широких сеток: 1 —
передвижной приемный стол сеток; 1 — устройство для приварки и изгиба фиксато-ров; 3 — агрегат для приварки закладных деталей; 4 — устройство для вырубки отверстий, 5 — пневматические ножницы; 6 — сварочная машина МТМС 18×75; 7 — механизм подачи продольной арматуры; 8 — бухтодержатели с консольным краном; 9 — стыковая сварочная машина; 10 — бухтодержатель для поперечной арматуры; 11 — станок для правки и резки арматуры
Рис. 11.4. Кондуктор для сварки пространственных каркасов:
1— пульт управления; 2 — противовес; 3 — сварочные клещи; 4 — кондуктор; 5 — блок; 6
—свариваемый каркас; 7 — лебедка
ми они удерживаются на поворотной консоли, и кондуктор с арматурой можно перемещать вверх и вниз с помощью лебедки. Некоторые узлы кондуктора соединены между собой болтами. Это позволяет применять один и тот же кондуктор для сборки различных арматурных каркасов, закрепляя его элементы в соответствии с размером собираемого каркаса.
При необходимости (например, для ребристых плит) плоские сетки и каркасы можно гнуть на специальных гибочных станках.
Напряженное армирование — создание в бетоне по всему сечению или только в зоне растягивающих напряжений предварительного обжатия, величина которого превышает напряжение растяжения, возникающее в бетоне при эксплуатации. Обычно предварительное обжатие бетона 5...6 МПа, а при изготовлении железобетонных напорных труб 10...12 МПа. Обжатие бетона, как отмечалось выше, осуществляют силами упругого последействия натянутой арматуры. Это достигается силами сцепления арматуры с бетоном или с помощью анкерных устройств.
Для обеспечения обжатия бетона применяемая арматурная сталь должна находиться в пределах упругих деформаций и не превышать 85...90% от предела текучести стали, а для углеродистых сталей, не имеющих четко выраженного предела текучести, — 65..70% от предела прочности на разрыв.
В качестве основной напрягаемой арматуры применяют проволочную и прутковую арматурные стали, а в качестве вспомогательной ненапрягаемой арматуры, если она имеет место в напряженных изделиях, — сварные сетки и каркасы.
При изготовлении предварительно напряженных изделий пользуются одноосным обжатием бетона отдельными стержнями или пучками проволок, располагаемых в изделии вдоль его продольной оси, и объемным обжатием путем навивки напряженной проволоки в двух или нескольких направлениях. Можно навивать проволоку и на готовое изделие с последующей защитой арматуры слоем бетона.
Арматурные элементы, применяемые в конструкциях, состоят из собственно арматуры, устройств для закрепления арматуры при натяжении и приспособлений для обеспечения проектного расположения отдельных стержней и проволок, из которых комплектуется арматурный элемент. Конструкция устройств для закрепления арматуры связана с технологией изготовления арматурного элемента, типом натяжения машин и приспособлений. Применяют два вида этих устройств: зажимы и анкеры. В свою очередь, зажимы и анкеры подразделяют по способу закрепления арматуры на клиновые, плоские, конические, волновые, петлевые, резьбовые, шпоночные и глухие анкеры, в которых концы арматурных пучков опрессовываются в обойме из мягкой стали. Все приведенные устройства, за исключением резьбовых, применяют для закрепления как круглых стержней, так и стержней периодического профиля.
Для захвата и закрепления стержневой арматуры применяют
— 350 —