
Методичка по строй мату 1
.pdfПроизводство известково-шлакового и известково-зольного кирпича аналогично технологической схеме производства силикатного кирпича. Шлаковый и зольный кирпич выпускают размером 250×120×140 мм и больше, марками по прочности при сжатии 25, 50 и 75, морозостойкостью такой же, как и у силикатного кирпича, плотностью 1400...1600 кг/м3, теплопроводностью
0,5...0,6 Вт/(м· °С).
Применяют известково-шлаковый и известково-зольный кирпич для возведения кладки стен зданий малой этажности (до трех этажей), а также для кладки стен верхних этажей многоэтажных зданий.
§ 8.9. Крупноразмерные изделия из силикатного бетона
Силикатным бетоном называют затвердевшую в автоклаве уплотненную смесь, состоящую из кварцевого песка (70...80%),
молотого песка (8..15%) и молотой негашеной извести (6... 10%).
Плотный силикатный бетон является разновидностью тяжелого бетона.
Силикатные бетоны, как и цементные, могут быть тяжелыми (заполнители плотные — песок и щебень или песчано-гравийная смесь), легкими (заполнители пористые — керамзит, вспученный перлит, аглопорит и др.) и ячеистыми (заполнителем служат пузырьки воздуха, равномерно распределенные в объеме изделия).
Вяжущим в силикатном бетоне является тонкомолотая из- вестково-кремнеземистая смесь — известково-кремнеземистое вяжущее, способное при затворении водой в процессе тепловлажностной обработки в автоклаве образовывать высокопрочный искусственный камень.
В качестве кремнеземистого компонента применяют молотый кварцевый песок, металлургические (главным образом доменные) шлаки, золы ТЭЦ. Кремнеземистый компонент (тонкомолотый песок) оказывает большое влияние на формирование свойств силикатных бетонов. Так, с возрастанием дисперсности частиц молотого песка повышаются прочность, морозостойкость
идругие свойства силикатных материалов.
Сувеличением тонкости помола песка повышается относительное содержание СаО в смеси вяжущего до тех пор, пока содержание активной СаО обеспечивает возможность связывания ее во время автоклавной обработки имеющимся песком в
низкоосновные гидросиликаты кальция. По данным ВНИИСтрома, при удельной поверхности молотого песка 2000...2500 см2/г содержание извести в смеси (в пересчете на СаО) составляет
20...28% от массы известково-кремнеземистого вяжущего, а при удельной поверхности песка более 2500 см2/г оптимальное содержание СаО в смешанном вяжущем может быть повышено до 33%.
—271 —
Автоклавная обработка — последняя и самая важная стадия производства силикатных изделий. В автоклаве происходят сложные процессы превращения исходной, уложенной и уплотненной силикатобетонной смеси в прочные изделия разной плотности,- формы и назначения. В настоящее время выпускаются автоклавы диаметром 2,6 и 3,6 м, длиной 20...30 и 40 м. Как изложено выше, автоклав представляет собой цилиндрический горизонтальный сварной сосуд (котел) с герметически закрывающимися с торцов сферическими крышками. Котел имеет манометр, показывающий давление пара, и предохранительный клапан, автоматически открывающийся при повышении в котле давления выше предельного. В нижней части автоклава уложены рельсы, по которым передвигаются загружаемые в автоклав вагонетки с изделиями. Автоклавы оборудованы траверсными путями с передаточными тележками — электромостами для загрузки и выгрузки вагонеток и устройствами для автоматического контроля и управления режимом автоклавной обработки. Для уменьшения теплопотерь в окружающее пространство поверхность автоклава и всех паропроводов покрывают слоем теплоизоляции. Применяют тупиковые или проходные автоклавы. Автоклавы оборудованы магистралями для выпуска насыщенного пара, перепуска отработавшего пара в другой автоклав, в атмосферу, утилизатор и для конденсатоотвода.
При эксплуатации автоклавов необходимо строго соблюдать «Правила устройства и безопасности эксплуатации сосудов, работающих под давлением».
После загрузки автоклава крышку закрывают и в него медленно и равномерно впускают насыщенный пар. Автоклавная обработка является наиболее эффективным средством ускорения твердения бетона. Высокие температуры при наличии в обрабатываемом бетоне воды в капельно-жидком состоянии создают благоприятные условия для химического взаимодействия между гидратом оксида кальция и кремнеземом с образованием основного цементирующего вещества — гидросиликатов кальция.
Весь цикл автоклавной обработки (по данным проф. П. И. Боженова) условно делится на пять этапов: 1 — от начала впуска пара до установления в автоклаве температуры 100 °С; 2 — повышение температуры среды и давления пара до назначенного минимума; 3 — изотермическая выдержка при максимальном давлении и температуре; 4 — снижение давления до атмосферного, температуры до 100 °С; 5 — период постепенного остывания изделий от 100 до 18...20 °С либо в автоклаве, либо после выгрузки их из автоклава.
Качество силикатных изделий автоклавного твердения зависит не только от состава и структуры новообразований, но и от правильного управления физическими явлениями, возникающими на различных этапах автоклавной обработки. При автоклавной обработке кроме физико-химических процессов, обеспечивающих синтез гидросиликатов кальция, имеют место физические процес-
— 272 —
сы, связанные с температурными и влажностными градиентами, определяемые термодинамическими свойствами водяного пара и изменениями физических характеристик в сырьевой смеси, а затем и в образовавшемся искусственном силикатном камне.
В составе силикатного камня преобладают низкоосновные гидросиликаты кальция, имеющие тонкоигольчатое или чешуйчатое микрокристаллическое строение типа CSH(B), и тоберморит. Однако наряду с низкоосновными могут быть и более крупнокристаллические высокоосновные гидросиликаты калиция типа
C2SH(A).
Развитие производства крупноразмерных силикатных изделий, особенно полной заводской отделки, способствует индустриализации строительства, дает возможность экономить цемент и позволяет расширить базу полносборного строительства. Наибольшее практическое распространение получили тяжелые мелкозернистые бетоны плотностью 1800...2500 кг/м3 и прочностью 15, 20, 25, 30 и 40 МПа. Можно получить силикатный бетон прочностью до 80 МПа при увеличении дисперсности и количества тонкомолотого кварцевого песка в смеси известковокремнеземистого вяжущего, сильном уплотнении и соответствующем режиме автоклавной обработки.
Прочность силикатного бетона при сжатии, изгибе и растяжении, деформативные свойства, сцепление с арматурой обеспечивают одинаковую несущую способность конструкций из силикатного и цементного бетона при одинаковых их размерах и степени армирования. Поэтому силикатный бетон можно использовать для армированных и предварительно напряженных конструкций, что ставит его в один ряд с цементным бетоном.
Из плотных силикатных бетонов изготовляют несущие конструкции для жилищного, промышленного и сельского строительства: панели внутренних стен и перекрытий, лестничные марши и площадки, балки, прогоны и колонны, карнизные плиты и т. д. В последнее время тяжелые силикатные бетоны применяют для изготовления таких высокопрочных изделий, как прессованный безасбестовый шифер, напряженно-армированные силикатобетонные железнодорожные шпалы, армированные силикатобетонные тюбинги для отделки туннелей метро и для шахтного строительства (бетон прочностью 60 МПа и более).
Коррозия арматуры в силикатном бетоне зависит от плотности бетона и условий службы конструкций; при нормальном режиме эксплуатации сооружений арматура в плотном силикатном бетоне не корродирует. При влажном и переменном режимах эксплуатации в конструкциях из плотного силикатного бетона арматуру необходимо защищать антикоррозионными обмазками.
Силикатный бетон на пористых заполнителях — новый вид легкого бетона. Твердение его происходит в автоклавах. Вяжущие для этих бетонов применяют те же, что и для плотных силикатных бетонов, а заполнителями служат пористые заполнители: керамзит, вспученный перлит, аглопорит, шлаковая пемза
— 273 —
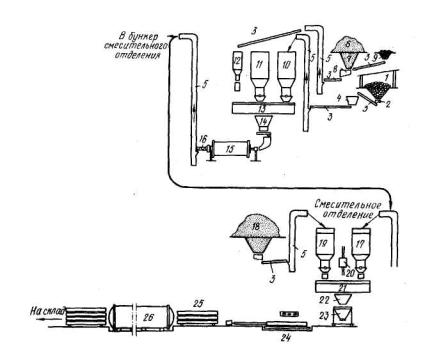
идругие пористые материалы в виде гравия и щебня. В настоящее время крупноразмерные изделия из силикатного бетона выпускают большой номенклатуры. Из силикатного бетона изготовляют крупные стеновые блоки внутренних несущих стен, панели перекрытий и несущих перегородок, ступени, плиты, балки. Элементы, работающие на изгиб, армируют стержнями
исетками.
Технология изготовления силикатобетонных изделий (рис. 8.8) состоит из следующих основных операций: добычи песка и отделения крупных фракций; добычи и обжига известняка (если известь производят на силикатном заводе), дробления извести; приготовления известково-песчаного вяжущего путем дозирования извести, песка и гипса и помола их в шаровых мельницах; приготовления силикатобетонной смеси путем смешения немолотого песка с тонкомолотой известково-песчаной смесью и водой в бетоносмесителях с принудительным перемешиванием; формования изделий и их выдерживания; твердения отформо-
Рис. 8.8. Технологическая схема производства изделий из силикатного бетона: 1 — крытый склад извести; 2 — питатель; 3 — ленточный конвейер; 4 — щековая дробилка; 5 — элеваторы; 6 — склад песка; 7 — расходный бункер песка; 8 — виброгрохот; 9 — склад гипса; 10 — расходный бункер извести; 11 — расходный бункер песка; 12 — расходный бункер гипса; 13 — бетоносмеситель С-371; 14 — бункер смеси; 15 — шаровая мельница СМ-14; 16 — шнековый питатель; 17 — бункер вяжущего; 18 — склад песка; 19 — расходный бункер песка; 20 — мерник воды; 21 — бетоносмеситель С-355; 22 — расходный бункер силикатобетонной смеси; 23 — бетоноукладчик; 24 — пост формовки; 25 — пост выдержки; 26 — автоклав
— 274 —
ванных изделий в автоклавах при температуре 174...200 °С и давлении насыщенного пара до 0,8...1,5 МПа.
Для получения плотных силикатных изделий применяют известь с удельной поверхностью 4000...5000 см2/г, а песок —
2000...2500 см2/г.
Изделия на молотой негашеной извести можно получить повышенной прочности и морозостойкости. Для этой цели регулируют сроки гидратации извести путем введения гипса, поверх- ностно-активных веществ и т. д. Молотую негашеную известь целесообразно применять для изделий, изготовленных на пластичной бетонной смеси. В таких свежесформованных изделиях гашение молотой извести не вызывает образования трещин, а увеличение объема способствует большому уплотнению изделия. Кроме того, при последующей гидратации негашеной извести гидрат оксида кальция, возникающий в уже отформованных изделиях, более активно взаимодействует с кремнеземом, чем ранее образовавшийся в гашеной извести гидрат оксида кальция. В очень уплотненных прессованием изделиях из жестких смесей гашение молотой негашеной извести может повлечь образование трещин, поэтому с увеличением степени уплотнения целесообразно проводить частичное гашение извести путем совместного помола ее с влажным песком или предварительное выдерживание известково-песчаной смеси, как это предусматривается при производстве силикатного кирпича.
Для силикатных изделий с прочностью до 10... 15 МПа песок можно применять в немолотом виде с известью 6...10% в расчете на активную СаО. Для изготовления автоклавных силикатных изделий расход извести составляет 175...250 кг на 1 м3 изделия.
Крупноразмерные изделия формуют на виброплощадках иногда с пригрузом или с вибропригрузом. Отформованные силикатные изделия подвергают запариванию в автоклавах диаметром 2,6 и 3,6 м.
Режим запаривания изделий из плотного силикатного бетона следующий: подъем давления пара до 0,8 МПа— 1,5...2 ч; выдерживание при этом давлении — 8...9 ч и спуск давления — 2...3 ч. Вибрированные крупноразмерные, силикатные изделия имеют прочность при сжатии 15...40 МПа, плотность — 1800...
2100 кг/м3, морозостойкость — 50 циклов и более. При силовом вибропрокате силикатные изделия получают прочностью до 60 МПа и плотностью до 2300 кг/м3.
Применяют плотные силикатобетонные изделия для строительства жилых, промышленных и общественных зданий; не рекомендуется использовать их для фундаментов и других конструкций, работающих в условиях высокой влажности.
§ 8.10 Ячеистые силикатные изделия
Ячеистые силикатные изделия отличаются малой плотностью и низкой теплопроводностью. Они бывают двух видов: пеносиликатные и газосиликатные.
— 275 —
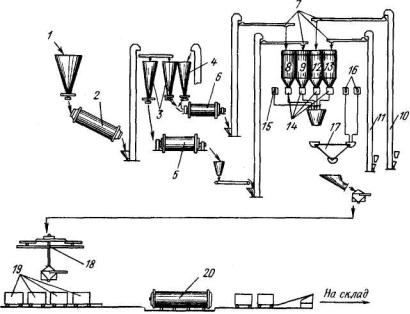
Пеносиликатные изделия |
изготовляют из смеси извести |
(до 25%) и молотого песка |
(иногда берут часть немолотого |
песка). Молотый песок можно заменить измельченным шлаком, золой. Производство пеносиликатных изделий отличается от производства других известково-песчаных смесей добавкой пенообразователя: клееканифольного, состоящего из костного или мездрового клея, канифоли, едкого натра и воды; смолосапонинового — из растительного мыльного корня и воды; пенообразователя ГК—гидролизованной боенской крови.
В газосиликатных изделиях образование ячеистой структуры происходит при введении в приготовленную смесь алюминиевой пудры.
Технологическая схема производства ячеистых силикатных пеноблоков (рис. 8.9) состоит из следующих основных операций: приготовления известково-песчаного вяжущего совместным помолом извести и части песка (количество песка берут в пределах 20...50% от массы извести); измельчения песка по сухому или мокрому способу; приготовления пеноили газобетонной массы;
Рис. 8.9. Технологическая схема производства пеноблоков на смешанном вяжущем:
1 — бункер песка; 2 — сушильный барабан СМ-45: 3 — бункера сухого песка; 4 — бункер извести; 5 — шаровая мельница для помола песка; 6 — шаровая мельница для совместного помола извести и песка; 7 — система шнеков; 8, 9 — бункера для известковопесчаной смеси и для молотого песка; 10 — элеватор подачи цемента; 11 — элеватор подачи молотой извести; 12, 13 — бункера цемента и молотой извести; 14 — дозаторы; 15 — дозатор воды; 16 — дозатор пенообразователя; 17 — пенобетоносмеситель; 18
—розлив в формы; 19 — вагонетка с формами; 20 — автоклав
—2 7 6 —

формования изделия. Приготовленную массу заливают в металлические формы с уложенными арматурными каркасами и закладными деталями. В формах газосиликатная масса вспучивается, образуя горбушку, которая затем срезается. Конец вспучивания должен совпадать с началом схватывания вяжущего.
В настоящее время на заводах ячеистого бетона все большее применение получает комплекная виброрезательная технология, которая позволяет управлять процессами структурообразования. Она имеет ряд технико-экономических преимуществ по сравнению с литьевой технологией: сокращается цикл приготовления смеси, улучшаются свойства ячеистых бетонов, снижается влажностью готовых изделий.
Схема производства изделий виброрезательной технологии
состоит из следующих операций. В виброгазобетоносмеситель СМС-40 или гидродинамический смеситель ГДС-3 подают подогретые воду и песок в виде шлама и перемешивают 2 мин, после чего поступает вяжущее и смесь перемешивается 1 мин. Затем вводят алюминиевую пудру и поверхностно-актив- ные вещества и вновь перемешивают 2 мин. Приготовленную высоковязкую смесь заливают в форму, установленную на виброплощадке. После кратковременного вибрирования массив выдерживают до 1 ч в нормальных условиях или в камере микроклимата с температурой около 50°С, при этом массив преобретает прочность 0,04...0,06 МПа. После этого бортоснастку снимают и массив разрезают с помощью машины СМ-1211 на отдельные блоки и направляют в автоклав. Из автоклава изделия поступают на склад готовой продукции. При необходимости получения изделий и высококачественной отделки последние направляют на калибровочную линию.
Линия для калибровки фрезерованием и отделки ячеистобетонных изделий (рис. 8.10) производит высококачественную отделку фрезерованием лицевых поверхностей блоков или панелей (рис. 8.11), обеспечивает получение различных рельефных
Рис. 8.10. Линия для калибровки фрезерованием и отделки ячеистобетонных панелей:
1 — фиксирующий упор; 2 — тележка; 3 — фрезерный агрегат; 4 — кантователь; 5 — привод тележки; 6 — фрезерный агрегат; 7 — I пост отделки; 8 — I сушильная камера; 9 — II пост отделки; 10 — II сушильная камера; 11 — пост снятия панели с линии
— 277 —

профилей и нанесение на них полимерминеральных составов разных цветов с приданием гладкой или шероховатой поверхности.
Состав газобетона плотностью 600 кг/м3, применяемый при виброрезательной технологии, следующий: портландцемента М400 — 95... 110 кг, извести —
110...120 кг, песка в шламе —
280 кг, смеси портландцемента с молотым песком — 110 кг, гипса двуводно-го — 6 кг, ПАК-3 — 0,5 кг и ПАВ —0,075 кг.
Водотвердое отношение — 0,38.
Изделия из ячеистых бетонов изготовляют армированными и неармированными. В армированных силикатных бетонах стальная арматура, а также закладные детали больше подвержены коррозии, чем в цементных бетонах. Поэтому стальную арматуру в ячеистых изделиях покрывают цементно-казеиновыми, полимерцементными составами, а также применяют металлизацию арматурной стали.
Ячеистые силикатные бетоны делят: на теплоизоляционные, имеющие плотность до 500 кг/м3 и прочность при сжатии до 25 МПа; конструктивно-теплоизоляционные плотностью 500...
800 кг/м3 и прочностью при сжатии 2,5...7,5 МПа; конструктивные плотностью выше 850 кг/м3 и прочностью 7,5...15,0 МПа. Изделия из ячеистого силикатного бетона достаточно морозостойки.
Применяют ячеистые силикатные изделия для наружных стен зданий, перегородок, а также для покрытий промышленных зданий; при этом эффективно используются несущие и теплоизоляционные качества ячеистых бетонов.
§ 8.11. Экономика производства и применения изделий из силикатного бетона
Объем производства силикатобетонных конструкций в одиннадцатой пятилетке достиг 6,0 млн. м3, в том числе стеновые панели из ячеистого бетона составляют — 1,3 млн. м3, мелкие блоки и перегородочные плиты — 1,75 млн. м3, теплоизоляционные плиты — 1,87 млн. м3, изделия из плотного бетона — 0,5 млн. м3.
Широкое применение силикатобетонные конструкции нашли в жилищном строительстве. Наиболее рациональным при этом является использование газосиликатных бетонов, имеющих малые плотность и теплопроводность, в качестве материала для самонесущих конструкций, наружных стен, а плотность силикатных бетонов с армированием, имеющих плотность 2000...2200 кг/м3 и
— 278 —
достаточную прочность, — для изготовления несущих панелей внутренних стен и перекрытий.
В табл. 8.5, 8.6 приводятся технико-экономические показатели перспективных конструкций наружных и внутренних стен и перекрытий из материалов, имеющих в настоящее время массовое распространение в строительстве, а также намеченных к широкому применению в ближайшие годы. Удельные капитальные вложения на единицу конструктивного элемента рассчитывались с учетом вложений в сопряженные отрасли, т. е. на изготовление основной конструкции и исходных материалов.
Как видно из табл. 8.5, наилучшие технико-экономические показатели имеют наружные стены из газосиликатобетонных панелей, а блочные конструкции из плотного силикатного бетона имеют преимущество перед конструкциями из штучной кладки. В группе внутренних стен (табл. 8.6) наиболее экономически эффективными по всем показателям являются армосиликатобетонные панели.
При анализе работы отдельных предприятий наблюдаются большие резервы снижения себестоимости производства силикатобетонных изделий. В основном эти резервы заключаются в снижении удельного расхода сырья и материалов, затраты на которые составляют около 40% всей стоимости конструкции.
Значительный экономический эффект дает организация конвейерного производства газобетона по виброрезательной технологии. Благодаря такой технологии достигается высокое качество изделий при значительном сокращении парка форм, увеличении коэффициента заполнения автоклавов, снижении издержек на автоклавную обработку в связи с сокращением расхода пара, уменьшении амортизационных расходов и затрат на текущий ремонт.
Расчеты показывают, что с применением виброрезательной технологии производства газобетона достигается снижение себестоимости в пределах 1,3...1,5 руб/м3 и удельных капитальных вложений на 2,5...3 руб/м3 по сравнению с литьевой технологией, принятой в типовых проектах. Снижение удельных капитальных вложений определяется уменьшением в 1,5...2 раза металлоемкости технологического оборудования в связи с запариванием на поддонах или специальных легких решетках, а также уменьшением количества автоклавов, поскольку сокращается цикл запаривания до 12... 15 ч и увеличивается коэффициент заполнения автоклавов.
Сопоставление технико-экономических показателей конструкций из различных материалов с конструкциями из силикатобетона показывает, что уже при современных технико-экономи- ческих показателях производства и монтажа увеличение удельного веса применения силикатобетонных крупнопанельных конструкций в общем объеме конструкций для крупнопанельного домостроения позволяет добиться значительного снижения стоимости строительства.
— 279 —
