
Методичка по строй мату 1
.pdfна собственном сырье, позволяют получать себестоимость 1 м2 плит до 1 руб. (на Новомосковском, Деконском и др.).
Наибольшие затраты при производстве гипсобетонных панелей приходятся на сырье и основные материалы. Наиболее дорогостоящим исходным материалом является гипс. Эффективного снижения затрат на гипс можно достигнуть за счет уменьшения потерь при транспортировке, а также сохранения качества гипса при хранении на складах. Поскольку гипс во времени быстро теряет активность, контактируя с влагой воздуха, необходимо стремиться к тому, чтобы его запасы на заводе гипсобетонных изделий были наименьшими. Более целесообразно заводы по производству гипсобетонных изделий располагать рядом с заводом по произодству гипса. Это позволяет иметь меньший запас гипса на заводском складе, в связи с чем снизятся затраты на транспортировку и создастся возможность использования гипса более высокого качества. Правильное хранение и расходование других составляющих материалов также могут снизить себестоимость готовых изделий.
На производство гипсовых и гипсобетонных изделий расходуется значительное количество воды, пара и силовой электроэнергии, причем наибольшее количество энергии расходуется на сушку (до 25% всей потребляемой предприятиями энергии). В настоящее время разработаны и все шире внедряются скоростные методы сушки гипсовых изделий. Если продолжительность сушки гипсокартонных листов на большинстве заводов составляет 70...80 мин, а плит и панелей — 20...24 ч, то при скоростных методах сушки эти сроки сокращаются соответственно для гипсокартонных листов до 12... 15 мин и перегородочных плит и пане-
лей — до 8...9 ч.
Исследованиями советских ученых установлено, что экономическая эффективность высокотемпературной сушки при производстве гипсовых плит и гипсобетонных панелей достигается за счет уменьшения расхода тепла вследствие изменения параметров теплоносителя и увеличения производительности труда и оборудования.
Анализ кинетики сушки гипсовых строительных материалов позволил установить, что без нарушения качества гипсовых и гипсобетонных изделий процесс сушки можно ускорить за счет применения высокотемпературного увлажненного теплоносителя. Так, при сушке гипсобетонных панелей можно применить начальную температуру теплоносителя 220...240°С при влагосодержании 45...50 г/кг сух. возд. против начальной температуры теплоносителя 120...130°С и влагосодержания 25...30 г/кг сух. возд. и конечную температуру влагоносителя 60...65°С с влагосодержанием 105...110 г/кг сух. возд. Эти условия позволяют интенсифицировать как внешний подвод тепла, так и движение влаги из толщи материала к поверхности.
Таким образом, сушка гипсобетонных изделий с применением высокотемпературного увлажненного теплоносителя позволяет в
— 261 —
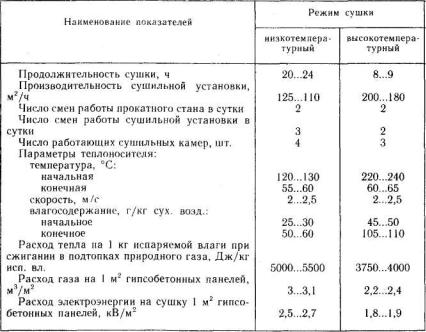
короткие сроки (за 8...9 ч) сушить гипсобетонные панели, не вызывая дегидратации гипса и, следовательно, не понижая качества изделий.
Технико-экономическая эффективность высокотемпературной сушки гипсокартонных листов достигается за счет уменьшения расхода тепла, изменения параметров теплоносителя, использования теплоносителя после первой зоны для нагревания наружного воздуха, подаваемого в смесительную камеру подтопка, разницы стоимости нагрева теплоносителя в паровых калориферах и при получении газовоздушной смеси сжигания топлива в подтопках, разницы в эксплуатационных расходах котельной установки подтопка и за счет повышения производительности труда и оборудования.
Данные о работе сушил по старому (низкотемпературному) и новому (высокотемпературному) методам сушки приведены в табл. 8.2 и 8.3.
Таблица 8.2. Данные о работе туннельных сушил для гипсобетонных панелей на низко- и высокотемпературном режимах сушки
Изложенные данные свидетельствуют о высокой экономичности применения скоростной высокотемпературной сушки в производстве гипсовых и гипсобетонных изделий.
Значительную долю в себестоимости изделий составляют затраты на заработную плату производственных рабочих, в
— 262
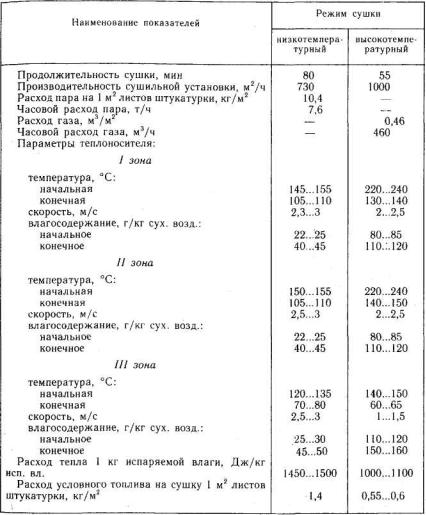
связи с чем большое значение приобретает повышение производительности труда.
Рост производительности труда должен опережать рост заработной платы, в результате чего ее доля на единицу продукции будет снижаться при росте средней заработной платы на одного рабочего. Повышению производительности труда способствуют рационализация производства, механизация и автоматизация производственных процессов.
Снижение себестоимости продукции заводов гипсобетонных
Таблица 8.3. Данные о работе шестиярусных сушил для гипсокартонных листов толщиной 10 мм на низко- и высокотемпературном режимах сушки
— 263 —
изделий может быть получено также за счет снижения цеховых расходов — рационализацией системы управления и учета. Важной задачей является снижение общезаводских расходов, связанных с затратами на содержание заводоуправления, вспомогательных цехов и служб, а также с транспортированием сырья, готовой продукции и т. п.
Главной задачей гипсовой промышленности является осуществление планомерной модернизации предприятий с созданием новых видов непрерывно действующего автоматизированного гипсоварочного оборудования, а также новых формовочных и сушильных установок. «К числу наиболее целесообразных мероприятий относятся следующие: перевод на газ и жидкое топливо основных тепловых агрегатов (котлов, барабанов, сушил); применение пневмотранспорта; установка электрофильтров; внедрение высокотемпературной скоростной сушки гипсовых и гипсобетонных изделий; более широкое производство и применение для изготовления изделий водостойких гипсоцементно-пуццола- новых вяжущих.
В ближайшие годы должна быть увеличена добыча гипсового камня на существующих горных предприятиях за счет реконструкции, а также расширена добыча гипсового камня за счет строительства новых горных предприятий, увеличено использование гипсосодержащих отходов.
Широкое применение прогрессивных гипсовых материалов и изделий позволяет повысить индустриальность строительства, улучшить эксплуатационные и эстетические показатели строительных конструкций, снизить трудоемкость и стоимость строительства. В сводном виде эффект применения новых видов гипсовых изделий дан в табл. 8. 4.
Для расширения номенклатуры гипсовых изделий, а вместе с тем и сферы применения гипсовых вяжущих необходимо промышленное производство и выпуск водостойких гипсоцементнопуццолановых вяжущих и изделий на их основе и в первую очередь прокатных перегородочных панелей, панелей оснований полов, прокатных панелей для санитарно-технических кабин и узлов, вентиляционных блоков, стеновых камней и др. Так, одной из весьма прогрессивных конструкций являются панели основания пола на гипсоцементно-пуццолановом вяжущем заводского изготовления. Они имеют гладкую поверхность, и при их укладке не требуется создания в перекрытиях трудоемких звукоизоляционных засыпок и выравнивающих стяжек, что позволяет в 1,5...2 раза снизить общую трудоемкость работ по устройству полов.
По данным предприятий, выпускающих панели основания пола, средние издержки производства составляют 2,5...10 руб/м2, а на лучших предприятиях — около 2 руб/м2. При этом наибольшие затраты в себестоимости приходятся на сырье и материалы (58...
...60 % от общих затрат на производство). Для снижения себестоимости панелей основания пола необходимо снизить трудоемкость и соответственно стоимость каркаса путем применения более
— 2 6 4 —
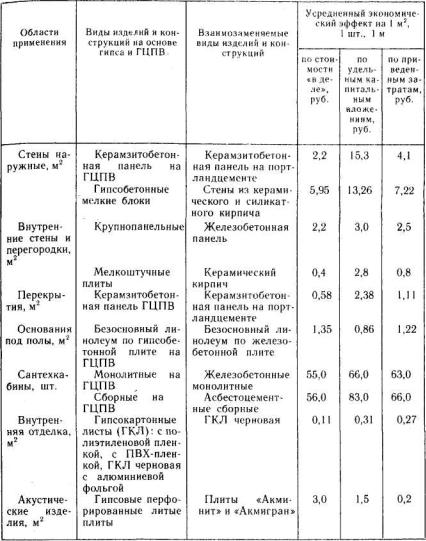
Таблица 8.4. Перспективные показатели применения прогрессивных гипсовых изделий
дешевых сортов древесины или частичной замены деревянного каркаса другими материалами, например стекловолокном.
В настоящее время большое применение в строительстве нашли санитарно-технические кабины, которые изготовляют на прокатном стане или из отдельных гипсобетонных панелей, армированных деревянным каркасом или металлической сеткой, или в специальных вертикальных формах в виде готовых объемных элементов. Кабины выпускают с санитарными узлами размером в плане:
— 265 —
совмещенные — 1,86×1,56 м, разобщенные — 2,16×1,56 м, высотой 2,39 м. Кабины изготовляют из тяжелого бетона или раствора на гипсоцементно-пуццолановом вяжущем; основанием под кабины служат железобетонные поддоны.
Хорошевский завод ЖБИ домостроительного комбината № 1 специализирован на изготовлении унифицированных санитарнотехнических кабин методом вертикального объемного формования разобщенных и совмещенных, выпускаемых на высокомеханизированных конвейерной и стендовой линиях. Применение ГЦПВ
иметода вертикального формования (одновременная заливка всех плоскостей) при изготовлении санитарно-технических кабин позволяет отказаться от тепловлажностной обработки и получать изделия с распалубочной прочностью через 1...2,5 ч после формования; получать высокую производительность (ритм конвейера 7...
...10 мин); применять местное дешевое вяжущее; уменьшить расход стали. Сушку производят горячим воздухом при температу-
ре 80...90°С в течение 10... 12 ч до влажности 10... 12%.
Уровень достигнутых технико-экономических показателей производства санитарно-технических кабин на ГЦПВ и изделий
всравнении с другими типами взаимозаменяемых конструкций позволяет рекомендовать их для массового строительства в жилых
иобщественных зданиях.
Однако на современном этапе существующая технология производства гипсовых вяжущих и изделий на их основе нуждается в дальнейшем развитии и техническом переоснащении. Наряду с совершенствованием традиционных способов производства гипса необходимо обеспечить переход на непрерывные процессы, внедрять новое оборудование. С этой целью целесообразно, например, применение способов дегидратации гипса в кипящем слое, во взвешенном состоянии, с использованием промежуточного теплоносителя для получения вяжущего β-полугидрата и особенно гидротермального способа для получения α-полуводного высокопрочного гипса.
8. Б. Изделия на основе извести
Использование извести для получения прочных и водостойких искусственных каменных изделий долгое время не находило применения, так как в естественных условиях известь твердеет очень медленно, изделия на ее основе имеют небольшую прочность (1...2 МПа) и легко размокают при действии воды.
Сущность превращения известково-песчаной смеси из легкоразмокающего и малопрочного материала в прочный и водостойкий камень заключается в следующем. При естественных условиях песок в известково-песчаных смесях инертен и не способен химически взаимодействовать с известью. Приобретение прочности извест- ково-песчаными растворами в естественных условиях достигается главным образом за счет твердения извести. Однако в среде насыщенного пара (100% влажности) и температуре 170°С и
— 266 —
выше кремнезем приобретет химическую активность и начинает быстро взаимодействовать с известью по уравнению СА(ОН)2 + + SiO2 + (n—1)Н2О = CaO·SiO2·nN2O, образуя гидросиликаты кальция — прочное и водостойкое вещество.
Из известково-песчаных смесей изготовляют крупноразмерные изделия для сборного строительства — блоки и панели для стен
иперекрытий, а также штучные изделия — силикатный кирпич
икамни для стен.
Изготовление силикатных блоков и панелей аналогично производству железобетонных изделий (см. гл. 11).
§ 8.7. Силикатный кирпич
Силикатный кирпич по своей форме, размерам и основному назначению не отличается от керамического кирпича (см. гл. 3). Материалами для изготовления силикатного кирпича являются
воздушная известь и кварцевый песок. Известь применяют в виде молотой негашеной, частично загашенной или гашеной гидратной. Известь должна характеризоваться быстрым гашением и не должна содержать более 5% MgO. Пережог замедляет скорость гашения извести и даже вызывает появление в изделиях трещин, вспучиваний и других дефектов, поэтому для производства автоклавных силикатных изделий известь не должна содержать пережога. Кварцевый песок в производстве силикатных изделий применяют немолотый или в виде смеси немолотого и тонкомолотого, а также грубомолотого с содержанием кремнезема не менее 70%. Наличие примесей в песке отрицательно влияет на качество изделий: слюда понижает прочность, и ее содержание в песке не должно превышать 0,5%; органические примеси вызывают вспучивание и также понижают прочность; содержание в песке сернистых примесей ограничивается до 1% в пересчете на SO3. Равномерно распределенные глинистые примеси допускаются в количестве не более 10%; они даже несколько повышают удобоукладываемость смеси. Крупные включения глины в песке не допускаются, так как снижают качество изделий. Состав известково-песчаной-смеси для изготовления силикатного кирпича следующий: 92...95% чистого кварцевого песка, 5...8% воздушной извести и примерно 7% воды.
Производство силикатного кирпича ведут двумя способами: барабанным и силосным, — отличающимися приготовлением из- вестково-песчаной смеси.
При барабанном способе (рис. 8. 6) песок и тонкомолотая негашеная известь, получаемая измельчением в шаровой мельнице комовой извести, поступают в отдельные бункера над гасильным барабаном. Из бункеров песок, дозируемый по объему, а известь — по массе, периодически загружаются в гасильный барабан. Последний герметически закрывают и в течение 3...5 мин производят перемешивание сухих материалов. При подаче острого пара под давлением 0,15...0,2 МПа происходит гашение извес-
— 2 6 7 —

Рис. 8.6. Технологическая схема производства силикатного кирпича по барабанному способу:
1 —барабанный грохот для сортировки песка; 2 — гасильный барабан; 3 — склад извести; 4 — дробилка; 5 — мельница; 6 — сепаратор; 7 — бункер молотой извести; 8
— весы; 9 — шнек; 10 — перемешивание и измельчение массы на бегунах; 11 — прессование кирпича; 12 — твердение кирпича в автоклаве
ти при непрерывно вращающемся барабане. Процесс гашения извести длится до 40 мин.
При силосном способе предварительно перемешанную и увлажненную массу направляют для гашения в силосы. Гашение
всилосах происходит 7...12 ч, т. е. в 10...15 раз больше, чем
вбарабанах, что является существенным недостатком силосного способа. Хорошо загашенную в барабане или силосе известковопесчаную массу подают в лопастный смеситель или на бегуны для дополнительного увлажнения и перемешивания и далее на прессование. Прессование кирпича производят на механических прессах под давлением до 15...20 МПа, обеспечивающим получение плотного и прочного кирпича. Отформованный сырец укладывают на вагонетку, которую направляют в автоклав для твердения.
Автоклав представляет собой стальной цилиндр диаметром 2 м и более, длиной до 20 м, с торцов герметически закрывающийся крышками (рис. 8. 7). С повышением температуры ускоряется реакция между известью и песком, и при температуре 174 °С она протекает в течение 8... 10 ч. Быстрое твердение происходит не только при высокой температуре, но и высокой влажности, для этого в автоклав пускают пар давлением до 0,8 МПа и это давление выдерживают 6...8 ч. Давление пара поднимают
—268 —
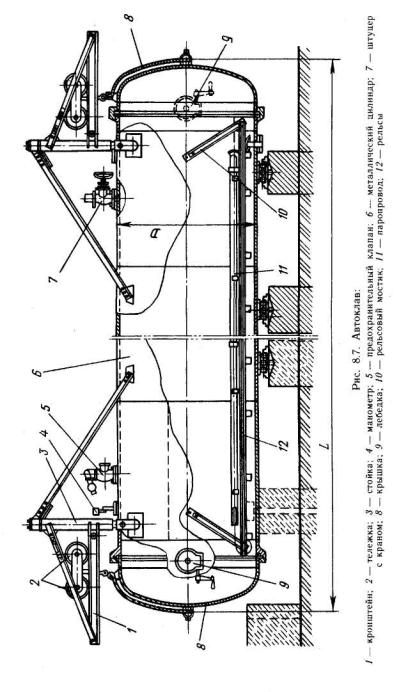

и снижают в течение 1,5 ч. Цикл запаривания продолжается
10...14 ч.
Под действием высокой температуры и влажности происходит химическая реакция между известью и кремнеземом. Образующиеся в результате реакции гидросиликаты срастаются с зернами песка в прочный камень. Однако твердение силикатного кирпича на этом не прекращается, а продолжается после запаривания. Часть извести, вступившей в химическое взаимодействие с кремнеземом песка, реагирует с углекислотой воздуха, образуя прочный углекислый кальций по уравнению
Силикатный кирпич выпускают размером 250 × 120 × 65 мм,
марок 75, 100, 125, 150, 200, 250 и З00, водопоглощением 8... 16%,
теплопроводностью 0,70...0,75 Вт/(м·°С), плотностью свыше 1650 кг/м3 — несколько выше, чем плотность керамического кирпича; морозостойкостью F15. Теплоизоляционные качества стен из силикатного кирпича и керамического практически равны.
Применяют силикатный кирпич так же, где и керамический, но с некоторыми ограничениями. Нельзя применять силикатный кирпич для кладки фундаментов и цоколей, так как он менее водостоек, а также для кладки печей и дымовый труб, так как при длительном воздействии высокой температуры происходит дегидратация гидросиликата кальция и гидрата оксида кальция, которые связывают зерна песка, и кирпич разрушается.
По технико-экономическим показателям силикатный кирпич превосходит керамический. На его производство требуется в 2 раза меньше топлива, в 3 раза меньше электроэнергии, в 2,5 раза меньше трудоемкости производства; в конечном итоге себестоимость силикатного кирпича оказывается на 25...35% ниже, чем керамического.
§ 8.8. Известково-шлаковый и известковозольный кирпич
Известково-шлаковый и известково-зольный кирпичи являются разновидностью силикатного кирпича, но отличаются меньшей плотностью и лучшими теплоизоляционными свойствами, так как в них тяжелый кварцевый песок заменен
соответственно пористым легким шлаком или золой. Для приготовления из-вестково-шлакового кирпича берут 3...12% извести и 88...97% шлака, а для известково-зольного — 20...25 % извести и 75... 80% золы. Так же как и шлак, зола является дешевым сырьевым материалом, образующимся при сжигании каменного, бурого угля и другого топлива в котельных ТЭЦ, ГРЭС и т. д. Использование шлаков и зол экономически выгодно, так как расширяется сырьевая база силикатных и других строительных материалов и снижается их стоимость.
— 270 —