
3 курс / Фармакология / Практикум_по_промышленной_технологии_лекарственных_средств_Рубан
.pdf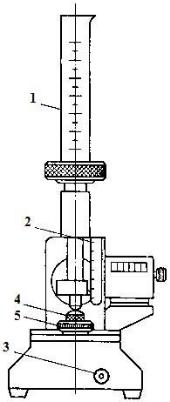
—градуированный цилиндр объемом 250 мл (цена деления - 2 мл);
масса цилиндра – (220±44) г;
—стряхивающее устройство, которое обеспечивает (250±15) со-
скоков цилиндра в минуту с высоты (3±0,2) мм, или номинально (300±15)
соскоков с высоты (14±2) мм; подставка для градуированного цилиндра,
снабженная держателем, имеет массу (450±10) г.
Рис. 10. Прибор для определения насыпной плотности сыпучих материалов 545Р-АК-3 ЖЗТО: 1 – измерительный цилиндр, 2 – шкала, 3 – тумблер,
4 – регулировочный винт; 5 – контргайка
Методика. Взвешивают 5,0 г порошка с точностью до 0,001 г и осто-
рожно, без уплотнения засыпают его в измерительный цилиндр (1) и запи-
сывают насыпной объем до усадки (V0) с точностью до ближайшей метки.
Устанавливают амплитуду колебаний (35–40 мм) посредством регулиро-
вочного винта (4) и после отметки по шкале (2) фиксируют положение
191
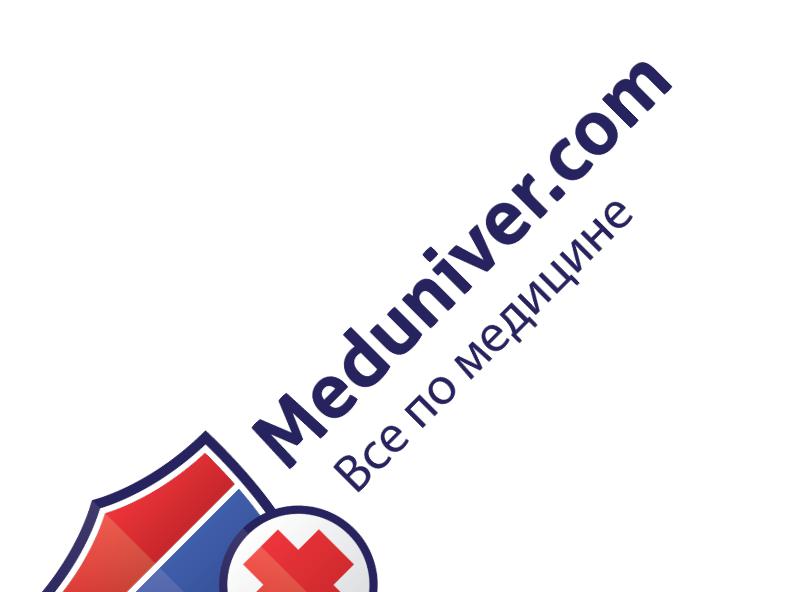
контргайкой (5). Частоту колебаний устанавливают при помощи трансфор-
матора в пределах 100-120 кол/мин по счетчику.
Прибор включают тумблером (3) и проводят 10, 500 и 1250 соскоков цилиндра на одном образце порошка, фиксируя объемы V10, V500, V1250 с точ-
ностью до ближайшей метки. Если разность между V500 и V1250 меньше 2 мл,
полученный VІ250 является насыпным объемом после усадки. Если разность между V500 и VІ250 превышает 2 мл, испытание повторяют, например, про-
водя еще 1250 соскоков цилиндра, пока разность измерений не будет со-
ставлять меньше 2 мл. Рассчитывают насыпную плотность в граммах на миллилитр, используя формулу m/Vf (где Vf - конечный объем после усадки). Обычно при исследовании этого показателя желательны повтор-
ные испытания. В результатах следует отметить высоту падения цилиндра.
В зависимости от насыпной плотности (ρн ) различают порошки сле-
дующим образом:
ρн > 2000 кг/м3 – весьма тяжелые, 1100 < ρн < 2000 кг/м3 – тяжелые,
1100 > ρн > 600 кг/м3 – средние, ρн < 600 кг/м3 – легкие.
Задание № 4. Определение текучести (сыпучести)
Определение проводят согласно методике, приведенной в ГФУ.
Метод воронки с виброустройством. Допускается проводить опре-
деление сыпучести с использованием воронки с виброустройством, что обеспечивает амплитуду колебаний от 0,04 мм до 0,1 мм при частоте 50 Гц.
Конструкция должна обеспечивать устойчивость прибора при вибра-
ции.
Методика. В сухую воронку, выходное отверстие которой закрыто заслонкой, помещают без уплотнения навеску используемого материала с
192
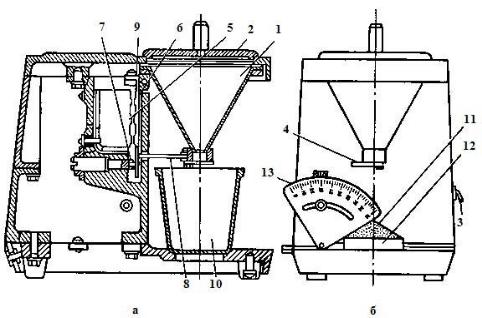
точностью 0,25 г. Включают виброустройство и через 20 с открывают за-
слонку. Определяют время, необходимое для полного высыпания образца из воронки. Проводят три определения.
Наиболее точные результаты, с хорошей воспроизводимостью полу-
чают при определении сыпучести на стандартных приборах, например, при-
боре модели GDT фирмы «Эрвека» (Германия) или вибрационном устрой-
стве модели ВП-12А Мариупольского завода технологического оборудова-
ния (рис. 11).
Рис. 11. Устройство прибора модели ВП-12А
а– измерение сыпучести; б – измерение угла естественного откоса;
1– воронка; 2 – крышка; 3 – тумблер; 4 – заслонка; 5 – электромагнит; 6 – якорь; 7 – амортизатор; 8 – тяга; 9 – шарнир; 10 – приемный стакан; 11 – горка; 12 – кольцо; 13 – угломер
Устройство состоит из корпуса, внутри которого смонтированы все функциональные узлы. В приборе предусмотрена вибрация конусной во-
ронки путем жесткого соединения ее с электромагнитным устройством, ра-
ботающим от сети переменного тока. Навеску порошка засыпают в воронку
(1), предварительно сняв крышку (2). Включают устройство тумблером (3)
при закрытой заслонке (4) и одновременно включают электромагнит (5) и
193
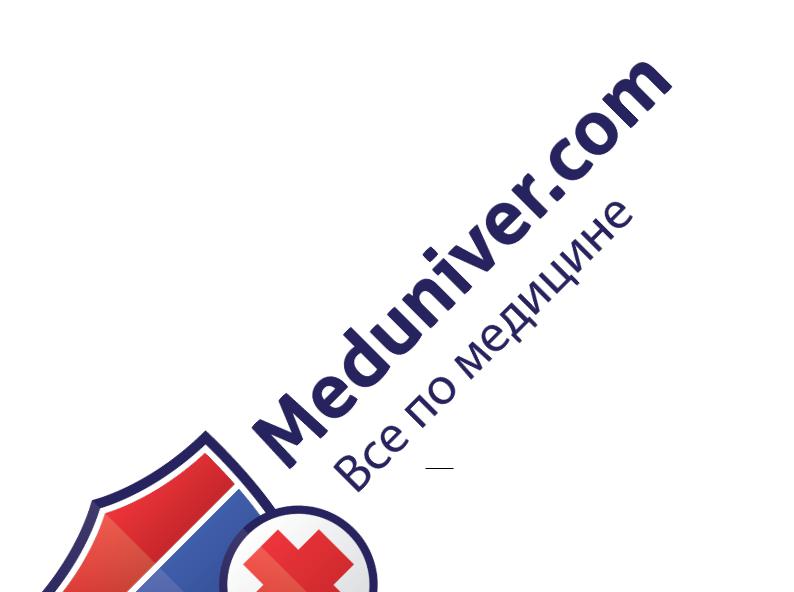
секундомер. Электромагнит притягивает якорь (6), сжимая амортизатор (7).
С частотой 50 Гц вибрация от якоря передается воронке, которая связана с якорем при помощи тяги (8) и шарнира (9). После 20 с утряски, необходи-
мой для получения стабильных результатов, открывают заслонку (4) и
наблюдают за истечением порошка из воронки в приемный стакан (10).
Точность отсчета времени истечения до 0,2 с. По окончании истечения при-
бор отключают.
Сыпучесть рассчитывают по формуле:
V |
m |
, |
|
||
c |
t 20 |
|
где: Vc – сыпучесть, г/с; m – масса навески, г;
t – полное время опыта, с;
20 – время утряски, с.
Обычно проводят 3 повторных измерения и окончательный результат вычисляют по формуле:
Vc nV ,
где: n – число повторных опытов = 3.
Косвенной характеристикой свойства сыпучести является определе-
ние угла естественного откоса – угол между образующей конуса из сыпу-
чего материала (11) и горизонтальной плоскостью (12). Данную характери-
стику определяют с помощью того же прибора. Угол естественного откоса изменяется в широких пределах от 25-35° для хорошо сыпучих и до 60-70°
для менее сыпучих материалов. Отсюда, чем меньше угол откоса, тем выше сыпучесть.
Для определения угла естественного откоса, предварительно устанав-
ливают объем порошка, который должен заполнить кольцо (12), с образо-
ванием горки (11). Затем полученный объем порошка засыпают в воронку,
194

включают виброустройство, открывают заслонку. После истечения по-
рошка выключают виброустройство, убирают излишки порошка и подводят угломер (13), определяя по шкале угол естественного откоса.
Задание № 5. Определение прессуемости
Оборудование. Для определения прессуемости материала навеску по-
рошка массой 0,3 или 0,5 г прессуют в матрице с диаметром отверстий 9
или 11 мм соответственно на гидравлическом прессе с давлением 120 МПа.
Методика. Навеску исследуемой массы отвешивают на ручных весах,
помещают в матрицу, которая поддерживается нижним пуансоном, и встав-
ляют верхний пуансон. Матрицу помещают на середину плунжера гидравли-
ческого пресса и прессуют до необходимого удельного давления, которое обозначено на манометре.
После прессования таблетку выталкивают из матрицы нижним пуан-
соном.
Полученную таблетку взвешивают на торсионных весах, высоту из-
меряют микрометром, коэффициент прессуемости (Кпресс, г/мм) вычисляют по формуле:
Kпресc Hm
где: m – масса таблетки, г (10–3 кг);
Н – высота таблетки, мм (10–3 м).
Прессуемость может быть определена по стойкости таблетки к раз-
давливанию на приборах ХНИХФИ или ТВТ фирмы «Эрвека» и выражена в кг или ньютонах.
Задание № 6. Определение силы выталкивания таблеток из мат-
риц
Методика. Для определения давления выталкивания навески по-
рошка (гранулята) массой 0,3 или 0,5 г прессуют в матрице с диаметром
195
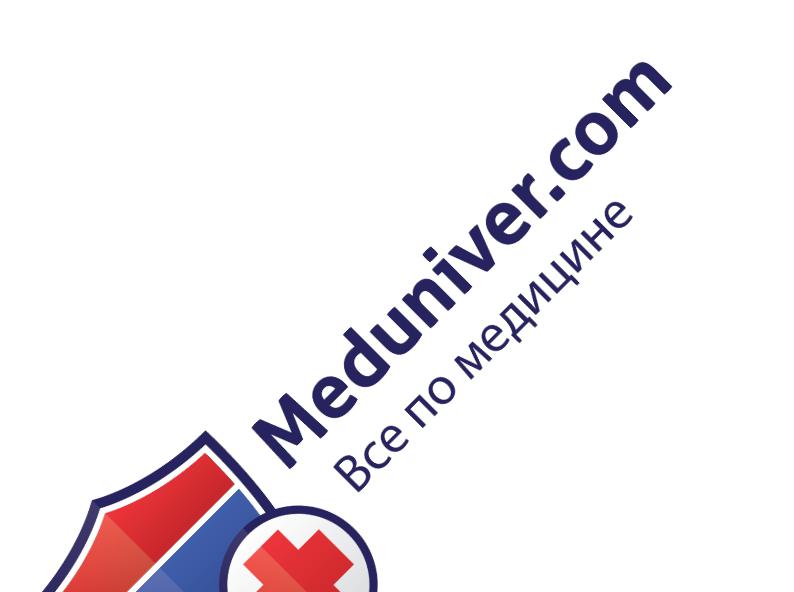
отверстий 9 или 11 мм соответственно на гидравлическом прессе с давле-
нием 120 МПа. Выталкивание запрессованной таблетки проводят нижним пуансоном. При этом на манометре пресса регистрируется усилие выталки-
вания.
Выталкивающее усилие рассчитывают по формуле:
Р |
|
Рман Sпл |
, |
|
|||
вытал |
|
Sбок |
|
|
|
где: Рвытал – давление выталкивания, МПа; Рман – данные манометра, МПа;
Sпл – площадь плунжера, равна 26,4 см2, (10–4 м2);
Sбок – площадь боковой поверхности таблетки (2 rh), м2.
Контрольные вопросы
1.Назовите физико-химические свойства порошков и гранулятов и объясните их значение.
2.Объясните влияние физико-химических свойств порошков и гра-
нулятов на фармако-технологические свойства таблеток.
3.Определение размера и формы частиц порошков.
4.Цель и метод определения фракционного состава порошка и гра-
нул.
5. Влияние размера частиц порошка и гранул на процесс таблетиро-
вания.
6.Влияние влагосодержания порошков на процесс прессования.
7.Определение насыпной плотности порошков.
8.Влияние физико-химических свойств на насыпную плотность.
9.Определение сыпучести и влияние данного параметра на процесс таблетирования.
10.Прессуемость порошкообразных материалов.
196
11. Значение давления выталкивания при производстве таблеток.
Лабораторное занятие №14
Тема: Получение таблеток с использованием метода прямого
прессования
Цель: Изучить получение таблеток методом прямого прессования с использованием вспомогательных веществ и без них
Вопросы для самоподготовки
1. Таблетки как лекарственная форма. Положительные и отрицатель-
ные свойства таблеток.
2. Устройство пресс-инструмента и требования, предъявляемые к
нему.
3. Охарактеризуйте строение пресс-инструмента и принцип работы эксцентриковых и ротационных таблеточных машин.
Информационный материал
Таблетки – твердая дозированная лекарственная форма, которая со-
держит одну дозу одного или больше действующих веществ и получена прессованием определенного объема частиц.
В зависимости от назначения и способа применения различают сле-
дующие виды таблеток:
1.Oriblettae – применяемые перорально.
2.Solublettae – используемые для приготовления полосканий, сприн-
цеваний и других растворов, применяемых в медицинской практике.
3.Injectablettae – асептически приготовленные.
4.Resoriblettae – всасывающиеся слизистой оболочкой рта.
5.Implantablettae – используемые для имплантации.
6.Dulliblettae – сладкого вкуса, применяемые в детской практике.
7.Bacilli, boli, uretratoria, vagitoria – прессованные уретральные и ва-
гинальные.
197
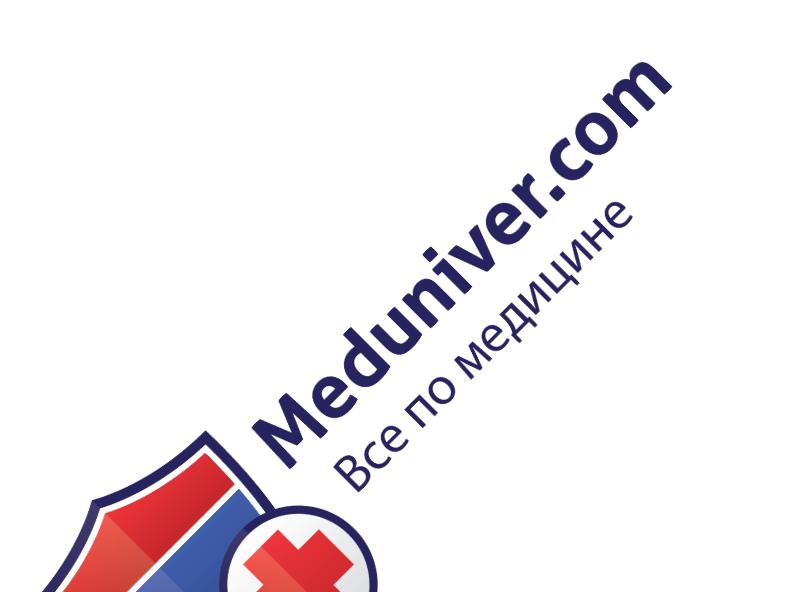
Таблетки для орального применения могут быть классифицированы
как:
–таблетки без оболочки;
–таблетки, покрытые оболочкой;
–таблетки «шипучие»;
–таблетки растворимые;
–таблетки диспергированные;
–таблетки, диспергированные в роговой полости;
–таблетки с модифицированным высвобождением;
–таблетки кишечно-растворимые;
–таблетки для применения в полости рта;
–оральные лиофилизаты.
По способу приготовления таблетки делятся на:
прессованные – Tabulettae compressae;
формованные – Tabulettae friabiles.
Для большинства фармацевтических препаратов технология произ-
водства таблеток состоит из следующих разрозненных операций: взвеши-
вания исходного материала, измельчения, просеивания, смешивания, гра-
нуляции, таблетирования (прессования), нанесения покрытия. Некоторые из перечисленных операций при производстве таблеток могут отсутство-
вать. Основные стадии производства таблеток показаны на рис. 12.
Прямое прессование – это совокупность различных технологических приемов, позволяющих улучшить основные технологические свойства таб-
летируемого материала – сыпучесть и прессуемость, и получить из него таб-
летки, минуя стадию грануляции. Оно имеет ряд преимуществ:
а) сокращается время технологического процесса производства таб-
леток;
б) в ряде случаев уменьшается количество вводимых в состав табле-
ток вспомогательных веществ;
198
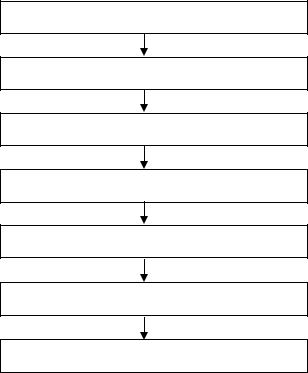
в) сокращаются трудозатраты, энергоресурсы, оборудование, произ-
водственные площади;
г) снижается стоимость таблеток.
Взвешивание исходного материала
Измельчение
Просеивание
Смешивание
Гранулирование*
Таблетирование (прессование)
Нанесение покрытия*
* – операция может отсутствовать.
Рис. 12. Основные стадии производства таблеток
Наиболее распространены три общие технологические схемы получе-
ния таблеток: с применением влажной грануляции, сухой грануляции и пря-
мого прессования (рис. 13).
В настоящее время таблетирование без грануляции осуществляют по следующим направлением:
1) с предварительно направленной кристаллизацией прессуемого ве-
щества; 2) с применением специальных вспомогательных веществ, улучшаю-
щих технологические свойства лекарственных порошков;
199
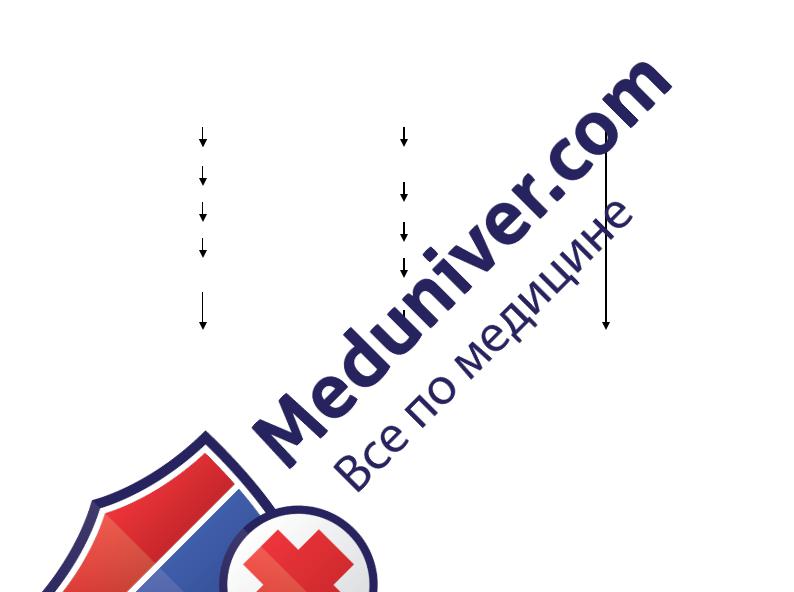
3) с использованием новых дозирующих устройств роторных табле-
точных машин, обеспечивающих стандартную массу таблеток (использова-
ние вакуума в матрицах, применение вибраторов и ворошителей в загрузоч-
ных воронках).
Влажная грануляция |
Сухая грануляция |
Прямое прессование |
Смешивание |
Смешивание |
Смешивание |
Увлажнение |
Компактирование или |
|
|
сухая грануляция |
|
Влажная грануляция |
|
|
|
Измельчение |
|
Сушка |
|
|
|
Просеивание |
|
Опудривание |
|
|
смешивание |
Опудривание |
|
|
смешивание |
|
Таблетирование |
Таблетирование |
Таблетирование |
а |
б |
в |
Рис. 13. Общие технологические схемы получения таблеток: а – с применением влаж-
ной грануляции; б – с применением сухой грануляции; в – прямым прессованием.
Прямому таблетированию без применения вспомогательных веществ подвергаются лекарственные субстанции, имеющие кристаллы изодиамет-
рической структуры, а именно: аммония бромид, аммония хлорид, калия бромид, калия хлорид, натрия бромид, цинка сульфат, сера, антифибрин,
гексаметилентетрамин, мочевина.
Для прямого прессования сульфадимезина, фенобарбитала, эфедрина гидрохлорида, кислоты аскорбиновой, натрия гидрокарбоната требуется добавление лактозы, аэросила или смеси одной части магния стеарата и 9
частей талька.
Для таблетирования без грануляции квасцов алюмокалиевых, кис-
лоты ацетилсалициловой, бромкамфоры, панкреатина и пепсина требуется
200