
894
.pdf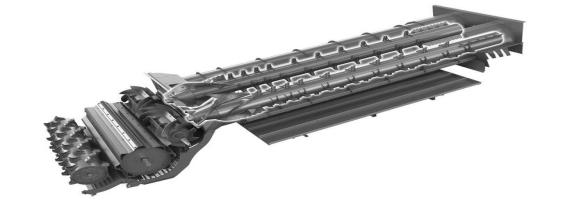
УДК 631.362
А.И. Отинов, А.М. Халитов – студенты; В.Д. Галкин – научный руководитель, профессор,
ФГБОУ ВО Пермский ГАТУ, г. Пермь, Россия
ТЕНДЕНЦИИ СОВЕРШЕНСТВОВАНИЯ СЕПАРАТОРОВ ГРУБОГО ВОРОХА ЗЕРНОУБОРОЧНЫХ КОМБАЙНОВ
Аннотация. Из обзора литературных источников установлено, что совершенствование сепараторов грубого вороха направлено на снижение потерь зерна и увеличение производительности комбайна. В настоящее время используются инновационные системы сепарации, такие как: автоматическая настройка комбайном частоты колебаний клавиш, использование эксцентрично расположенных роторов, использование отбойных битеров специальной конструкции.
Ключевые слова: сепараторы грубого вороха, тенденции совершенствова-
ния.
Качество работы соломотряса определяется, прежде всего полнотой выделения зерна и величиной его потерь. Этот рабочий орган комбайна должен обладать высокой надежностью. По возможности технологический процесс должен меньше зависеть от наклонов комбайна в вертикально-продольной и вертикальнопоперечной плоскостях, так как ему часто приходится работать в условиях сложного рельефа поля.
В настоящее время в комбайнах фирмы Сlaas. используется система сепарации ROTO PLUS. Принцип действия системы ROTO PLUS прост и чрезвычайно эффективен. Отбойный битер системы APS разделяет массу на два потока и подает их к роторам [1]. Эксцентрично расположенные роторы позволяют развивать высокие центробежные силы для отделения оставшегося зерна из соломы. Имея диаметр 445 мм и длину по 4200 мм, роторы комбайнов LEXION обеспечивают эффективное выделение зерна. Благодаря наличию скатной доски смесь зерна, соломы и половы сначала попадает на днище, а затем через ступени подается на решетный стан. Это позволяет значительно снизить на него нагрузку.
Рис. 1- Система сепарации фирмы Сlaas
291

Система сепарации фирмы New Holland Agriculture
Компания New Holland Agriculture выпускает новое поколение комбайнов серии CX: две модели с 5-клавишным соломотрясом (CX7.80 и CX7.90) и 4 модели
с6-клавишним (CX8.70, CX8.80, CX8.85 и CX8.90)
Спомощью технологий соломотряса Opti-Speed, комбайн автоматически настраивает скорость клавиш, чтобы она соответствовала максимальной пропускной способности для собираемого зерна: пшеницы, кукурузы, рапса или риса. При этом легкозаменяемые секции подбарабанья позволяют свести к минимуму время на перенастройку. В дополнение к этому система автоматически замедляет движение клавиш соломотряса при движении вверх по склону и ускоряет частоту их вращения во время движения вниз.
Система Opti-Clean увеличивает эффективность очистки в пределах 20%. Отмеченная наградами система Opti-Fan увеличивает эффективность работы системы очистки, автоматически регулируя обороты вентилятора в соответствии с углом продольного наклона комбайна. Угол зерноочистительного устройства автоматически регулируется в пределах 17%, чтобы компенсировать влияние на поток культуры, которое оказывают боковые склоны, и предотвратить скатывание зерна во время разворота в конце пол.
Рис.2 – Система сепарации фирмы New Holland Agriculture
Вывод. Совершенствование сепараторов грубого вороха направлено на снижение потерь зерна и увеличение производительности комбайна. Для обеспечения этой задачи в настоящее время используются инновационные системы сепарации, такие как: автоматическая настройка комбайном частоты колебаний клавиш, для обеспечения максимальной пропускной способности сепаратора; использование эксцентрично расположенных роторов, которые позволяют развивать высокие центробежные силы для отделения зерна из соломы; использование отбойных битеров специальной конструкции, которые позволяют разделять массу на два потока и равномерно подавать к роторам соломосепаратора.
Литература
1. Липовский М.И.Зерноуборочный комбайн: из прошлого к новому поколению./М.И. Липовский, А.Н. Перекопский.-СПб.: ИАЭП, 2015.-316 с.
292
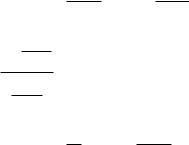
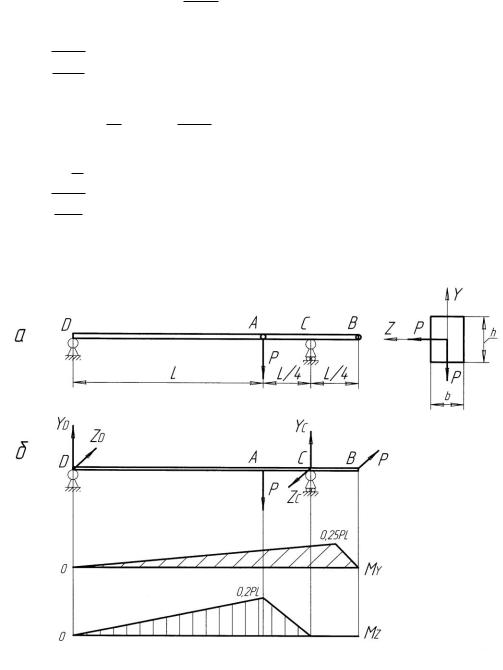
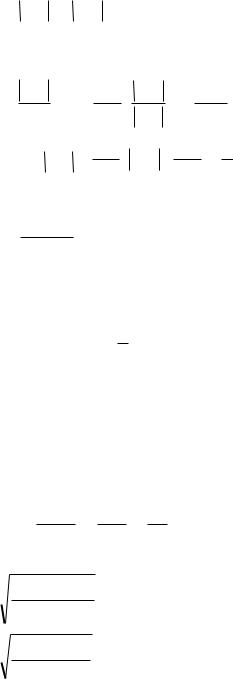
УДК 621.961
П.И. Суслопарова – студент; В.С. Кошман – научный руководитель, доцент,
ФГБОУ ВО Пермский ГАТУ, г. Пермь, Россия
ЗАКОНОМЕРНОСТИ ПРОЕКТИРОВАНИЯ И ОСОБЕННОСТИ РАСЧЕТА ГИДРАВЛИЧЕСКИХ НОЖНИЦ
Аннотация. С учетом закономерностей проектирования инженерных конструкций и устройств предложен алгоритм расчета гидравлических ножниц. Получены формулы для вычисления давления насоса и объёмной подачи насоса применительно к условиям резания металлических деталей. Приведен пример расчета гидравлических ножниц, используемых спасателями при проведении аварийно – спасательных работ.
Ключевые слова: закономерности проектирования, гидравлические ножницы, алгоритм расчета.
Как известно, языком современной техники является язык и схем, и формул, и чертежей. Однако создаваемые изделия могут быть удачными и отвечать предъявляемым требованиям, а могут и не являться таковыми. В основе проектирования технических объектов и систем лежит инженерная мысль, интеллектуальная деятельность человека. Эта деятельность плодотворна, если при опоре на накопленный опыт подчиняется определенным правилам, приемам, которые авторы теории изобретательства называют закономерностями (или законами) проектирования. В их числе, прежде всего, можно выделить следующие.
Первая закономерность отражает практическую значимость одного из важнейших физических законов - закона сохранения и превращения энергии. Техническая система сохраняет свою работоспособность, если отвечает условию “сквозного прохождения энергии” по всем ее частям.
Вторая закономерность проектирования соотносит функции технических объектов с их структурой: техническая система оказывается жизнеспособной, если ее форма подчинена внутреннему содержанию и способствует реализации предъявляемых к ней требований.
В согласие с третьей закономерностью техническая система должна отвечать естественному стремлению человека к минимизации прилагаемых им усилий (физических усилий, мыслительной деятельности, работы органов чувств и т.
п.) [1].
Целью настоящей работы является иллюстрация возможностей приложения отмеченных выше общих закономерностей проектирования при расчете гидравлических ножниц, используемых для проведения аварийно - спасательных работ. Данные ножницы однозначно отвечают отмеченному выше закону минимизации усилий.
Схема предлагаемого устройства приведена на рисунке 1.
296
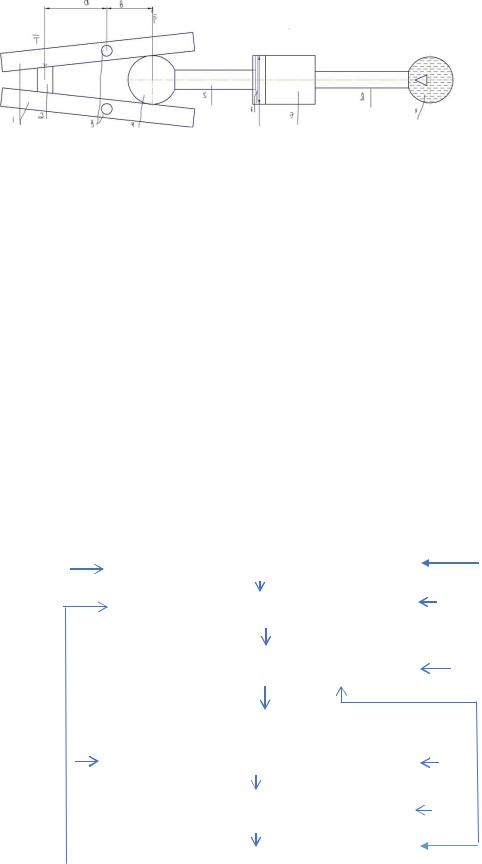
Рисунок 1 – Схема гидравлических ножниц
1 – режущие элементы; 2 – металлическая деталь; 3 – оси вращения; 4 – силовой элемент; 5 – шток; 6 – поршень; 7 – силовой цилиндр; 8 – трубопровод; 9 – насос; а и в – плечи; Р – сила давления;
Т– сила резания
Вгидравлическом инструменте жидкость выступает как рабочие тело, которое воспринимает и передает энергию. Потенциальная энергия давления, сообщаемая насосом 9 рабочей жидкости, преобразуется в работу силы резания Т, совершаемую режущими элементами 2. Это отвечает закону энергетической проводимости. В согласие же с законом соответствие функций и структуры в рассматриваемой нами конструкции жидкость от насоса 9 по трубопроводу 8 подается в подпоршневую полость силового цилиндра 7. Это приводит к перемещениям поршня 6, штока 5 и силового элемента 4. Конструкция будет работоспособной в том случае, если насос 9 (как энер-
гетическая машина) обеспечит такую величину избыточного давления Ризб. жидкости (подаваемой в подпоршневую полость силового цилиндра 7), которая обеспечит необходимую величину силы резания Т.
Порядок расчета гидравлических ножниц приведен на рисунке 2.
|
|
|
|
|
|
|
|
|
|
|
|
|
|
|
|
|
|
|
|
|
|
|
|
|
|
|
|
σд |
|
|
|
|
|
|
|
|
|
|
|
|
|
|
|
|
|
ω |
|
|
|
|
|||
|
|
|
|
|
|
1.Определение силы резания |
|
|
||||||||||||||||||
|
|
|
|
|
|
|
|
|
|
|
|
|
||||||||||||||
|
|
|
|
|
|
|
|
|
|
|
|
|
|
|
|
|
|
|
||||||||
|
|
|
|
|
|
|
|
|
|
|
|
|
|
|
|
|
|
|
||||||||
|
|
|
|
|
|
|
|
|
|
|
|
|
|
|
|
|
|
|
|
|
|
|
|
|
|
|
|
|
|
|
|
|
|
|
|
|
|
Т= К1*К2*σдоп* ω |
|
|
|
|
|
|
|
|
|
|
|||||
|
|
|
|
|
|
|
|
|
|
|
|
|
|
|
|
|
|
|
|
|
|
|
||||
|
|
|
|
|
|
|
|
|
|
|
|
|
|
|
|
|
|
|
|
|
|
|
|
|
|
|
|
|
|
|
|
|
|
|
|
|
|
|
|
|
|
|
|
|
|
|
|
|
а, в |
|
|
||
|
|
|
|
|
|
|
|
|
|
|
|
|
|
|
|
|
|
|
|
|||||||
|
|
|
|
|
|
|
|
|
|
2.Определение силы давления |
|
|
|
Т |
|
|
|
|
|
|
|
|
|
|||
|
|
|
|
|
|
|
|
|
|
Р = |
|
|
|
|
|
|
|
|
|
|||||||
|
|
|
|
|
|
|
|
|
|
|
|
|
|
|
|
|
|
|
|
|||||||
|
|
|
|
|
|
|
|
|
|
|
|
|
|
|
|
в |
|
|
|
|
|
|
|
|
|
|
|
|
|
|
|
|
|
|
|
|
|
|
|
|
|
|
|
|
|
|
|
|
|
|
|
|
|
|
|
|
|
|
|
|
|
|
|
|
|
|
|
|
|
|
|
|
|
|
|
|
|
|||
|
|
|
|
|
|
|
|
|
|
3.Определить избыточное давление |
|
|
|
|
|
|
|
|
|
|||||||
|
|
|
|
|
|
|
|
|
|
|
|
|
|
d |
|
|
||||||||||
|
|
|
|
|
|
|
|
|
|
|
|
Ризб = 4Р/ d2 |
|
|
|
|
|
|
||||||||
|
|
|
|
|
|
|
|
|
|
|
|
|
|
|
|
|
|
|
|
|
|
|
|
|
|
|
|
|
|
|
|
|
|
|
|
|
|
|
|
|
|
|
|
|
|
|
|
|
|
|
|||
|
|
|
|
ᵝр |
|
|
4.Вычесление объема жидкости, поступающего в |
|
|
|
|
|
|
|||||||||||||
|
|
|
|
|
|
|
|
Wнач |
|
|
|
|||||||||||||||
|
|
|
|
|
|
подпоршневую полость |
|
|
|
|
|
|
|
|
|
|||||||||||
|
|
|
|
|
|
|
|
|
|
|
|
|
|
|
|
|
|
|
||||||||
|
|
|
|
|
|
|
|
|
|
|
|
W= βр*Wнач*Pизб |
|
|
|
|
|
|
|
|
|
|
||||
|
|
|
|
|
|
|
|
|
|
|
|
|
|
|
|
|
|
|
|
|
|
|
|
|||
|
|
|
|
|
|
|
|
|
|
|
|
, |
|
|
|
|
|
|
|
|
|
|
|
|
||
|
|
|
|
|
|
|
|
|
|
|
|
|
|
|
|
|
|
|
|
|
|
|
|
|
|
|
|
|
|
|
|
|
|
|
|
|
|
|
|
|
|
|
|
|
|
|
|
|
|
||||
|
|
|
|
|
|
|
|
|
|
5. Вычисление объёмной подачи насоса |
|
|
|
|
|
|
|
|
|
|||||||
|
|
|
|
|
|
|
|
|
|
|
|
|
|
|
|
|
|
|
||||||||
|
|
|
|
|
|
|
|
|
|
Q = |
W/ |
|
|
|
|
|
|
|
|
|
||||||
|
|
|
|
|
|
|
|
|
|
|
|
|
|
|
|
|
|
|
||||||||
|
|
|
|
|
N |
|
|
|
|
|
|
|
|
|
|
|
|
|
|
|
|
|
|
|
|
|
|
|
|
|
|
|
|
|
|
|
6.Подбор насоса |
|
|
|
|
|
|
|
|
|
|||||||
|
|
|
|
|
|
|
|
|
|
|
|
|
|
|
|
|
|
|
||||||||
|
|
|
|
|
|
|
|
|
|
|
|
|
|
|
|
|
|
|
|
|
|
|
|
|
|
|
Рисунок 2. Порядок расчета гидравлических ножниц
297
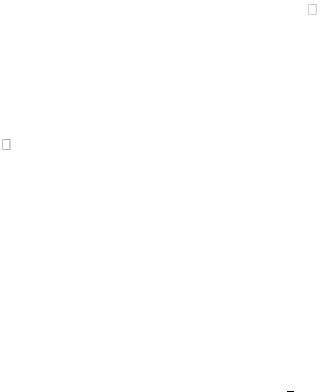
На рисунке 2 используются обозначения: - допустимое напряжение на срез; ω – площадь поперечного сечения металлической детали; К1 – коэффициент учитывающий затупление ножниц; К2 – коэффициент учитывающий увеличение зазора между режущими элементами; а и в - плечи сил; d- диаметр поршня; βр- ко-
эффициент объёмного сжатия |
жидкости; |
|
|
|
|
||
|
Wнач - начальный объём жидкости в подпоршневой полости гидроцилин- |
||||||
дра ; |
- время поступление жидкости объёмом |
W в силовой гидроцилиндр. |
|||||
|
Насос подбирается по двум параметрам: Ризб - избыточное давление и Qн- |
||||||
объёмная подача насоса. |
|
|
|
|
|
|
|
|
В согласие с приведенным выше алгоритмом расчета величину избыточ- |
||||||
ного давления Ризб можно вычислить по формуле |
|
|
|||||
|
Ризб = |
4 К1 К2 а |
, |
|
(1) |
||
|
|
|
|||||
|
|
τ |
|
|
|
|
|
|
а объёмную подачу насоса Q - по отношению |
|
|||||
|
|
QH = |
βр Wнач P |
(2) |
|||
|
|
|
|
|
. |
||
|
|
|
|
||||
|
|
|
|
|
|
||
|
Из формулы (1) видно, что избыточное давление |
Ризб будет тем больше, |
чем выше допустимое напряжение на срез , площадь поперечного сечения ме-
таллической детали и величина отношений плеч а и чем меньше диаметр d поршня,
в
и наоборот. В согласие с формулой (2) более высокой величине объёмной подачи насоса QH (при заданном времени поступления жидкости в подпоршневую полость ) способствуют более высокие числовые значения коэффициента объёмного сжатия βр, и начального объёма Wнач жидкости в подпоршневой полости и величины избыточного давления Ризб.
В качестве рабочей жидкости принимаем техническое масло марки Licota LO-5000 с коэффициентом сжимаемости βp=0.42×10-9 [Па-1] [2]. Материал металлической детали – Ст40.
При числовых значениях величин :
=1,37*108 Па; К1= 1,2; К2- 1,1; а=30 мм; =7*10-4 м2; в =100 мм; d= 0,03 м; Wнач = 3*10-4м3; = 4,5с
имеем величины избыточного давления
Ризб = |
4 1,2 1,1 30 1,37 108 7 10−4 |
= 53,8 Мпа |
||||
3,14 0,032 100 |
||||||
|
|
|
|
|||
и объемной подачи насоса |
|
|
||||
QH = |
4,2 10−10 310−4 5,38 107 |
=1, 5*10-6 |
м2/c. |
|||
|
||||||
4,5 |
|
|
|
Принимаем насос НРГ7004А, имеющий рабочие давление 70МПа и объем-
ную подачу 0,016…2,20 мл/с [3].
В заключение можно сделать вывод о том, что знание закономерностей проектирования способствует повышению качества решения инженерных задач. Действительно, предложенный с учетом выделенных выше закономерностей проектирования
298

алгоритм решения задачи по расчету гидравлических ножниц позволил выйти на числовые значения их параметров, которые близки к величинам параметров ножниц МНКГ-80 [4], которые используются при проведении аварийно-спасательных работ.
Литература
1.Хорошев А.Н. Введение в управление проектированием механических систем: учебное пособие. Белгород. 1999. 372с
2.Масло производителя Licota LO-5000 [Электронный ресурс]– Режим доступа:
URL:.[https://garagetools.ru/tovar/maslo-dlya-gidrav, http://netnado.ru/reshenie-koefficient- temperaturnogo-rasshireniya-jidkostej/page-1.htmllicheskogo-instrumenta-5l] (Дата обращения: 20.02.19).
3.Насос НРГ7004А [Электронный ресурс] – Режим доступа: URL:https://fire- man.club/statyi-polzovateley/nozhnicy-kombinirovannye-nkgs-80-i-kusachki-kgs-80-opisanie-ttx-sxemy- ustrojstvo-princip-dejstviya-i-poryadok-raboty-obsluzhivanie-vozmozhnye-neispravnosti-remont/ (Дата обращения:19.02.19).
4. Ножницы МНКГ-80 [Электронный ресурс] – Режим доступа: |
URL:https://stud- |
files.net/preview/3560282/page:2/ (Дата обращения: 20.02.19). |
|
УДК 631.363
М. С. Фотин – магистрант; М. А. Трутнев – научный руководитель, доцент,
ФГБОУ ВО Пермский ГАТУ, г. Пермь, Россия
ЭНЕРГЕТИЧЕСКАЯ ЭФФЕКТИВНОСТЬ ЭКСТРУДИРОВАНИЯ ЗЕРНА ЕСТЕСТВЕННОЙ ВЛАЖНОСТИ
Аннотация. В статье приведено описание технологии экструдирования зерна естественной влажности после комбайновой уборки и результат расчета ее энергетической эффективности.
Ключевые слова: зерновые корма, экструдирование, энергетическая эффективность.
При приготовлении комбикормов в хозяйствах зерно измельчают, смешивают с другими компонентами и, при необходимости гранулируют. При этом не происходит химических изменений кормов и животные затрачивают некоторую долю энергии на усвоение кормов, что приводит к росту затрат на производство продукции.
Этих дополнительных затрат поможет избежать экструзионная переработка корма. Ее суть заключается в воздействии на корм высокой температуры (150…180 ), давления (до 20 МПа) и сдвига, осуществляемых в канале шнека экструдера, вследствие чего происходит структурно-механические и химические изменения состава зерна. При этом белки и углеводы распадаются на более простые составляющие, причем белок за счет кратковременности воздействия не успевает коагулировать, а антипитательные вещества и патогенная микрофлора, имеющиеся в корме, уничтожаются[1].
299
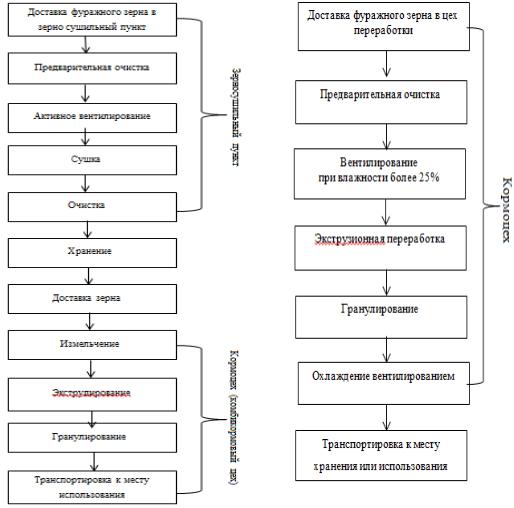
При выходе из экструдера зерно из зоны высокого давления попадает в зону атмосферного давления, из-за чего находящиеся в нем влага «взрывает» зерно, которое приобретает микропористую структуру. Это способствует в дальнейшем более полному усвоению питательных веществ корма и повышению продуктивности животных, а также улучшению качества продукции[2].
По существующей технологии зерно доставляется с поля на зерноочистительный пункт, где предварительно накапливается в бункерах активного вентилирования, затем сушиться и далее храниться на складе. Зимой зерно перед экструдированием измельчают, смачивают водой и экструдируют, а затем скармливают животным (рис 1)
Рис 1. Существующая технология |
Рис 2. Предлагаемая технология |
Мы предлагаем экструдировать зерно естественной влажности 20…25% после уборки без измельчения и без сушки [2]. Зерно накапливается в бункерах активного вентилирования, где его влажность доводится до оптимальной после предварительной очистки. При экструдировании зерно нагревается до 120 …200 за счет подвода внешнего тепла или диссипации механической энергии, а на выходе из экструдера зерно «взрывается», приобретая микропористую структуру, а излиш-
300