
894
.pdf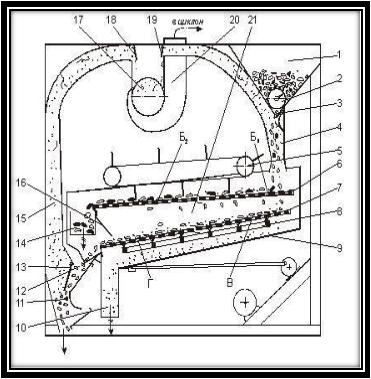
Рис .2. Машина предварительной очистки К-523Б 1 – бункер-питатель; 2 – разравнивающий шнек; 3 – регулировочная
заслонка;4 – первый пневмосепарирующий канал; 5 – скребковый транспортер; 6 – верхнее решето; 7 – нижнее решето; 8 – щеточная тележка;
9 – днище решетного стана; 10, 14 – отводящие лотки; 11 – дефлекторные стержни; 12 – подводящая воронка; 13 – качающаяся заслонка с противовесами; 16 – скатная доска; 15 – второй пневмосепарирующий канал; 17 – камера,
18, 19 – регулировочные заслонки; 20 – вентилятор; 21 – решетный стан.
Воздушная система снабжена двумя аспирационными ПСК (до и после решёт) с постоянной или регулируемой глубиной, одной или двумя осадочными камерами и радиальным вентилятором. Универсальные воздушно-решётные машины серии SR этой фирмы содержат два решётных стана по четыре яруса в каждом с общей площадью от 16 до 40 м2 при рабочей ширине от 1,0 до 2,5 м. Производительность машин при предварительной очистке с выделением крупных, мелких и лёгких примесей составляет от 100 до 250 т/ч. Машины содержат два ПСК. Канал предварительной очистки может быть соединён с атмосферой или работать с замкнутой рециркуляцией воздуха. Второй ПСК двойной с регулируемой глубиной.
Воздушно-решетный сепаратор типа К527А применяется для предварительной и интенсивной очистки зерновых, бобовых и масличных, а также иных сыпучих мелких семян (Рис.3).
Российские машины вторичной очистки МС-4,5, МС-4,5С (ОАО «Воронеж- сельмаш»),МВУ-1500, СВУ-5Б (ОАО ГСКБ «Зерноочистка»), МЗУ-20Д (ФГУП ПКБ НИИСХ Северо-востока) имеют производительность от 4,8 до 20,0 т/ч. Содержат воздушные системы с двумя ПСК, одной или двумя осадочными камерами, встроенным диаметральным вентилятором или отдельно смонтированным радиальным вентилятором, устройствами для предварительной очистки отработанного
271
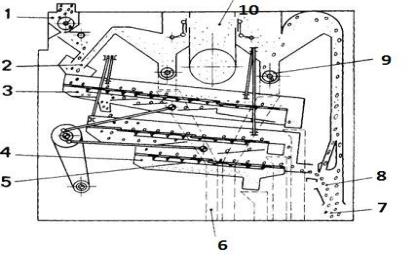
воздуха. Особенностью конструкции воздушной системы машины МВУ-1500 является то, что второй ПСК дополнительно снабжён разделительной камерой для улавливания фуражной фракции по аналогии с машиной DELTA 108 фирмы
«Cimbria» (Дания).
Рис.3. Воздушно-решётный сепаратор K-527A фирмы PETKUS
1 – питающее устройство; 2 – канал предварительного воздушного сепаратора; 3. – верхний решетный стан; 4 – нижний решетный стан;
5 – механизм очистки решет; 6 – канал главного воздушного сепаратора; 7 – выпуск чистых семян; 8 – шнек вывода отходов главного воздушного сепаратора;
9 – выпуск отходовпредварительного воздушного сепаратора;
10 – отработанный воздух.
Вывод. В результате анализа конструкций и процесса работы российских и зарубежных воздушно-решётных зерноочистительных машин выявлены следующие тенденции их развития:
–повышение производительности до 200…250 т/ч и более за счёт увеличения ширины рабочей части, площади сортировальных и подсевных решёт, производительности вентиляторов, применения фракционной технологии очистки по скорости витания и размерам частиц, использования для очистки от грубых примесей дополнительного плоского или цилиндрического решета (скельператора);
‒улучшение качества очистки зерна путём совершенствования технологического процесса и рабочих органов, применения диаметральных вентиляторов, питающих устройств активного типа, пневмосепарирующих каналов (ПСК) предварительной (до решёт) и основной (после решёт) очистки;
–разработка зерноочистительных машин для предварительной и первичной очистки, первичной и вторичной очистки, универсальных зерноочистительных машин для выполнения предварительной, первичной и вторичной очистки; расширение функциональных возможностей
Литература 1.Сычугов Н.П. Машины, агрегаты и комплексы послеуборочной обработки зерна и семян
трав. / Н.П. Сычугов, Ю.В. Сычугов, В.И. Исупов. Под. Ред. Н.П. Свчугова. Киров, изд-во ООО
ВЕСИ, 2015. 404 с.
272
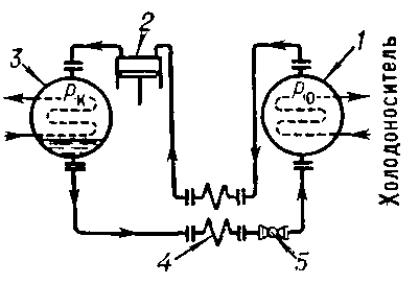
УДК 621.576
Г.А. Зыков – студент; С.Г. Гурьянов – научный руководитель, канд. техн. наук,
ФГБОУ ВО Пермский ГАТУ, г. Пермь, Россия
ВОЗМОЖНОСТЬ ИСПОЛЬЗОВАНИЯ СПИРАЛЬНЫХ КОМПРЕССОРОВ В ХОЛОДИЛЬНЫХ МАШИНАХ
Аннотация. Излагается значение охлаждения продуктов питания, рассказывается о типах холодильных машин, описывается принцип работы парокомпрессионных холодильных машин, обсуждаются конструкция и работа спиральных и поршневых компрессоров. Производится сравнительный анализ технических характеристик поршневого и спирального компрессоров.
Ключевые слова: холодильные машины, спиральные компрессоры, парокомпрессионные холодильные машины, масса газа в рабочей полости.
Низкая температура пищевой продукции - самое простое и эффективное средство консервации, не позволяющее развиваться вредным, нежелательным микроорганизмам. Охлажденные продукты питания имеют более длительный срок годности в сравнении с продуктами находящимися при положительной температуре окружающей среды. В охлажденных продуктах питания, в отличие от других консерваций, сохраняются витамины, естественные вкусовые качества, цвет и аромат.
В агропромышленном комплексе низкие температуры применяются не только для хранения продуктов, но и в процессе их переработки и транспортировки.
Основными источниками низких температур являются холодильные ма-
шины.
Холодильная машина – устройство, служащее для отвода теплоты от охлаждаемого тела при температуре более низкой, чем температура окружающей среды.
Рис. 1. Схема парокомпрессионной холодильной машины.
Основные элементы данных типов машин: 1. Испаритель; 2. Компрессор; 3. Конденсатор; 4. Теплообменник; 5. Терморегулирующий (дроссельный) вентиль.
273
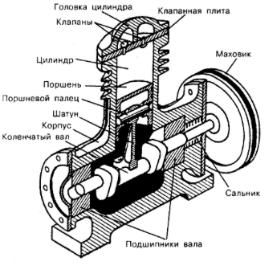
Вхолодильной технике применяется несколько систем холодильных машин, таких как: парокомпрессионные, абсорбционные, пароэжекторные и воз- душно-расширительные. Все системы холодильных машин, за исключением воз- душно–расширительных, для получения низкой температуры используют кипение низкокипящих жидкостей. Охлаждение в воздушно–расширительных машинах осуществляется за счет расширения сжатого воздуха в детандере [3].
Самыми распространенными и универсальными холодильными машинами являются парокомпрессионные. Схема парокомпрессионной холодильной машины представлена на (рис. 1).
Принцип работы представляет собой замкнутую циркуляцию хладагента. В испарителе хладагент кипит (испаряется) при пониженном давлении и низкой температуре. Теплота необходимая для кипения переходит от охлаждаемого тела, изза чего его температура понижается. Образовавшийся пар по магистрали поступает
вкомпрессор, где сжимается и нагревается до температуры выше температуры окружающей среды, далее пар подается в конденсатор, где его температура опускается до температуры насыщения и хладагент полностью конденсируется. Полученный жидкий хладагент через дроссель, в котором снижается его давление, возвращается в испаритель для повторного испарения, таким образом, замыкая цикл работы машины [3].
Взависимости от вида холодильного компрессора парокомпрессионные машины подразделяют на поршневые, винтовые, турбокомпрессорные, ротационные и спиральные.
Наиболее часто в холодильных машинах работают поршневые компрессоры. Как правило, компрессоры представляют собой отдельный агрегат с определенным технологическим процессом. Данный агрегат подразумевает в процессе эксплуатации регулярное обслуживание, ремонт и настройку. Устройство поршневого компрессора изображено на (рис.2).
Рис. 2. Устройство поршневого компрессора На (рис. 2) представлен поршневой компрессор в разрезе. В состав данного
компрессора входят такие элементы, как поршень, цилиндр, два клапана – для нагнетания и всасывания воздуха, которые находятся в крышке цилиндра.
274
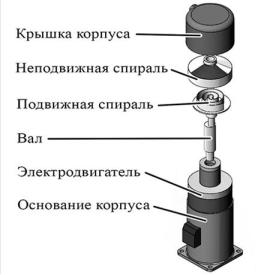
При работе компрессора, шатун, соединенный с вращающимся коленчатым валом, передает на поршень ограниченные движения по камере сжатия. В данном процессе происходит увеличение объема, находящегося между клапанами и нижней частью поршня, что приводит к разрежению [2].
Превышая сопротивление пружины, которая закрывает клапан, выполняющий всасывающие функции, атмосферный воздух открывает его и поступает в цилиндр.
Возвратное действие поршня приводит к сжиманию воздуха и возрастанию его давления. Нагнетательный клапан, который также удерживается пружиной, открывается потоком воздуха, находящегося под высоким давлением, после чего сжатый воздух попадает в нагнетательный патрубок [2].
В настоящее время инженерами разработан и внедрен новый тип компрессоров сжатие в котором происходит посредством радиального вращения спирали. Эти машины вытесняют из эксплуатации устаревшие поршневые компрессоры. Спиральный компрессор показан на (рис. 3).
Рис. 3. Устройство спирального компрессора
На рис. 3 представлены основные части спирального компрессора. Главными рабочими органами компрессора являются статическая и подвижная спирали. Нагнетание рабочего газа, в спиральных компрессорах, осуществляется двумя спиралями – подвижной и неподвижной. Неподвижная спираль закреплена в корпусе компрессора, а подвижная на эксцентрике вала. Благодаря специально подобранному профилю, между спиралями образуются камеры, по которым движется газ. При этом их форма рассчитана таким образом, чтобы они не проскальзывали, что значительно снижает уровень износа таких компрессоров.
В спиральных компрессорах, в отличие от поршневого компрессора, клапан на всасывание отсутствует, так как подвижная спираль отсекает рабочую камеру от канала всасывания. Отсутствие впускного клапана делает конструкцию проще надежнее. В линии нагнетания спирального компрессора устанавливаться динамический клапан, который предотвращает обратный поток и, как следствие, вращение
275
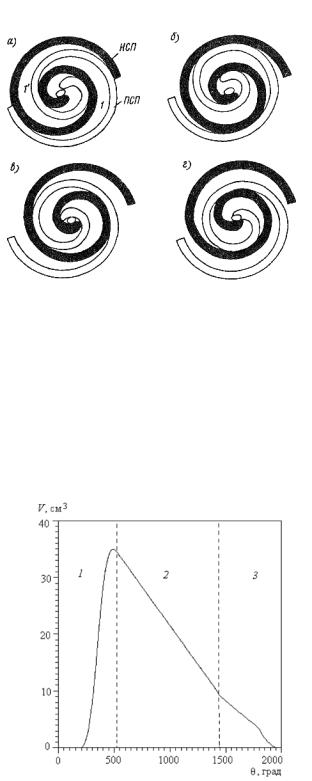
спирали под действием сжатого газа при выключенном двигателе. При этом следует учитывать, что динамический клапан создает дополнительное сопротивление в линии нагнетания.
Рис. 4. Взаимное положение спиралей с углом сдвига 90°
На (рис. 4) представлено движение спиралей НСП (неподвижная спираль), ПСП (подвижная спираль), и фазы сжатия газа 1, 1'. В спиральном компрессоре одновременно существует несколько пар рабочих полостей, в разных полостях одновременно происходят циклы всасывания, сжатия и нагнетания.
Количество одновременно рабочих полостей, а также степень сжатия и производительность зависит от величины угла закрутки спиралей [1].
При движении спирали изменение объема рабочей плоскости зависит от орбитального угла, зависимость этих параметров показана на (рис. 5).
Рис. 5. Изменение объема рабочей плоскости в зависимости от орбитального угла
На (рис. 5) представлено: 1- область цикла всасывания; 2 – область линейного сжатия; 3 – область нелинейного сжатия.
276
Если рассматривать газ в рабочей полости компрессора как идеальный, а процесс сжатия адиабатический, то будут иметь место следующие соотноше-
ния [1]:
= |
( |
0 |
) |
, = |
( |
0 |
)−1 |
, |
(1) |
|
|
||||||||
0 |
|
|
0 |
|
|
|
|
где V – объем рабочей полости при текущем значении орбитального угла; р – давление газа в рабочей полости; Т – температура газа; V0 – объем полости при окончании цикла всасывания; р0 – давление; Т0 – температура на всасывании; k – показатель адиабаты.
Массу газа в рабочей полости компрессора получим, умножив плотность газа при давлении всасывания ρ0 на объем рабочей полости V0, взятый на момент окончания цикла всасывания [1]:
= 0 0 |
(2) |
Спиральные компрессоры в сравнении с поршневыми компрессорами имеют ряд технических преимуществ, таких как:
–Высокая энергетическая эффективность, КПД достигает 80 – 86%;
–Высокая надежность и долговечность, определяемая износом подшипников;
–Низкий уровень шума при работе;
–Отсутствие мертвого объема;
–Процессы всасывания, сжатия и нагнетания растянуты по углу поворота вала, что дает малую скорость газа даже при большой частоте вращения спирали.
–Возможность работы на любом хладагенте, на любом газе и даже с впрыском капельной жидкости.
Сравнительные показатели поршневого и спирального компрессора показаны в таблице.
Таблица
Сравнительные показатели поршневого и спирального компрессора
|
|
Поршневой компрессор |
Спиральный компрес- |
|
|
Bitzer 4VCS-6.2Y-40P |
сор Bitzer ESH730BY |
|
|
|
|
Марка хладагента |
R22 |
R22 |
|
|
|
|
|
Объемная |
производительность, |
34,73 |
30 |
м3/ч |
|
||
|
|
|
|
Масса, кг |
|
129 |
85 |
|
|
|
|
Избыточное давление, бар |
28 |
28 |
|
|
|
|
|
Уровень звуковой мощности, дБ |
77,5 |
73,8 |
|
|
|
|
|
Габаритные размеры, мм |
649х306х385 |
314х338х585 |
|
|
|
|
|
В ходе сравнения, компрессоров одной производственной марки, имеющих примерно равную объемную производительность, можно выделить существенные различия по массе, спиральный компрессор легче на 34%. По уровню звуковой мощности поршневые компрессоры проигрывают на 5%. Габаритные размеры спиральных компрессоров меньше. При равных выходных показателях, в ряде технических характеристик поршневые компрессоры уступают спиральным компрессорам.
277
Анализ рабочих характеристик поршневых и спиральных компрессоров, показал, что спиральные компрессоры являются более практичными, имеют меньшее количество трущихся поверхностей, что обуславливает их долговечность. При сравнительно одинаковой стоимости спиральные компрессоры имеют лучшее техническое исполнение. Считаю возможным внедрение спиральных компрессоров в холодильные машины агропромышленного комплекса.
Литература
1.Косачевский В. А. О производительности спирального компрессора // Вестник Международной академии холода. 2016. № 4. С. 40–46.
2.Классификация компрессоров. [Электронный ресурс] https://megapredmet.ru, 2015
3.Основы теории холодильных машин. [Электронный ресурс] https://helpiks.org, 2014
УДК 621.785
А.М. Кашфуллин – старший преподаватель, М.А. Семенов, А.И. Дускаев – студенты, ФГБОУ ВО Пермский ГАТУ, г. Пермь, Россия
ТЕРМИЧЕСКАЯ ОБРАБОТКА УГЛЕРОДИСТОЙ СТАЛИ
Аннотация. В статье приведены результаты влияния вида термической обработки на твердость сталей с различным содержанием углерода для марок сталей (40, У10). Получены результаты зависимости твердости стали от скорости охлаждения и от температуры отпуска.
Ключевые слова: термическая обработка, углеродистая сталь, отжиг, нормализация, закалка, отпуск.
Всовременном машиностроении широко применяют термическую обработку стали и чугуна, а также многих цветных металлов с целью повышения прочности, улучшения технологических свойств, повышения износоустойчивости, а также изменения ряда физических свойств.
Впроцессе эксплуатации детали транспортно-технологических машин подвергаются воздействию статических, динамических и циклических нагрузок, что в свою очередь приводит их к интенсивному износу.
Целью данной работы является изучение влияния различных видов термической обработки на твердость углеродистых сталей.
Теория термической обработки стали основана на общей теории фазовых превращений, протекающих в сплавах в твердом состоянии при нагреве и охлаждении с различной скоростью, что позволяет получать сталь с необходимыми структурой и свойствами [1, 2].
На практике различают следующие виды термической обработки: отжиг; нормализация; закалка; отпуск.
Отжиг и нормализация относятся к предварительным видам термической обработки, цель которых – подготовка стали к окончательной (упрочняющей) термической или механической обработке.
278
Закалка и отпуск относятся к упрочняющим видам термической обработки, цель которых – придать стали необходимые свойства.
К параметрам процесса термической обработки относятся:
а) температура нагрева – определяется по диаграмме «железо-углерод»; б) время нагрева – зависит от способа нагрева (газовая печь, электрическая
печь, соляная ванна и т.д.), от конфигурации и размеров изделия, от состава стали, от способа укладки изделий.
Все эти параметры обычно приводятся в справочниках по термической обработке.
в) скорость охлаждения – зависит от требуемых механических свойств. Отжиг – термическая операция, заключающаяся в нагреве стали до темпера-
тур выше фазовых превращений, выдержке при этой температуре и последующем медленном охлаждении вместе с печью. После отжига сталь получает структуру в полном соответствии с диаграммой «железо-углерод» (основа – перлит).
Нормализация – разновидность отжига, но с охлаждением на воздухе. Нагрев – доэвтектоидной стали – до температуры на 30...50°С выше Ас3, – эвтектоидные и заэвтектоидные – на 30...50°С выше точки Асm. Структура сталей после нормализации – сорбит либо сорбитообразный перлит.
Закалка – заключается в нагреве выше критических точек, выдержке и последующем быстром охлаждении. Цель закалки – получение максимальной твердости, обусловленной получением мартенсита вследствие резкого охлаждения.
Различают полную закалку – с нагревом на 30...50°С выше точки Ас3, неполную закалку – с нагревом на 30...50°С точки Ас1. Доэвтектоидные стали подвергают полной закалке для растворения феррита, уменьшающего твердость. Эвтектоидные и заэвтектоидные стали подвергают неполной закалке для сохранения ЦII, повышающего общую твердость стали.
Скорость охлаждения при закалке оказывает решающее влияние на результат закалки. В качестве охладителей при закалке используются вода, масло, водные растворы солей, щелочей, расплавленные соли и т.д. Наиболее широко распространены вода и масло. Скорость охлаждения в воде при 18…600°С/с, в масле – 150°С/с, поэтому вода применяется для закалки сталей с большой критической скоростью закалки (углеродистых сталей), а в масле охлаждают стали с малой критической скоростью закалки (детали из легированных сталей и высокоуглеродистых сталей при тонких сечениях).
Отпуск – заключается в нагреве закаленной стали до температуры ниже точки А1, выдержке при этой температуре и последующем произвольном охлаждении (обычно на воздухе). Отпуск является окончательной операцией термической обработки и проводится для повышения пластичности, снижения или почти полного устранения внутренних напряжений, уменьшения хрупкости закаленной стали, стабилизации структуры и размеров закаленных деталей. В зависимости от температуры различают низкий, средний и высокий отпуск.
Низкий отпуск осуществляется при температуре 150...200°С и предназначен для снятия внутренних напряжений, снижения хрупкости закаленной стали без заметного снижения твердости. Структура стали МОТП(+АОСТ). Применяется для измерительного и режущего инструмента, для деталей, прошедших цементацию.
279
Средний отпуск осуществляется при температурах 300...400°С для получения троститной структуры и предназначен для повышения пределов упругости, выносливости. Этому виду отпуска подвергаются пружины, рессоры.
Высокий отпуск осуществляется при температурах 500...600°С с получением структуры сорбита и предназначается для получения наибольшей ударной вязкости. Этот вид отпуска применяется для деталей, работающих в условиях ударной нагрузки. Сочетание закалки с высоким отпуском называется улучшением.
Лабораторные исследования проводились на кафедре технического сервиса и ремонта машин ФГБОУ ВО Пермский ГАТУ. Образцы габаритами диаметром 10 мм, длиной 35 мм различных по содержанию углерода марок сталей (40, У10). Образцы загружали в печи и нагревали до необходимой температуры в соответствии с маркой стали, время выдержки для видов термической обработки: нормализация, закалка принято расчетным путем – 15 мин. Для проведения отжига образцы охлаждали вместе с печью до 600С с последующим охлаждением на спокойном воздухе. Нормализацию осуществляли непосредственно охлаждением образцов на спокойном воздухе при комнатной температуре. Для исследования влияния охлаждающей среды закалку проводили в двух охладителях: в воде и в масле. После каждого вида термической обработки охлажденные образцы зачищали от окалины и измеряли твердость на приборе Роквелла ТК-2М. По результатам работы строили график зависимости твердости стали от скорости охлаждения (рис.1), используя следующие значения скоростей: охлаждение с печью – 50 С/ч; охлаждение на воздухе – 30 С/с; охлаждение в масле – 150 С/с; охлаждение в воде – 600 С/с.
Нормально закаленные образцы подвергали отпуску при 200С (низкий), 400С (средний), 600С (высокий). После проведения отпуска образцы зачищали от окалины и измеряли твердость. По результатам работы строили график зависимости твердости закаленной стали от температуры отпуска (рис.2).
Таблица
Термическая обработка марок сталей: 40, У10
|
|
Структура |
|
|
|
Время |
Охла- |
HRCэ |
|||
Вид |
|
Сталь40 |
Сталь 10У |
|
|
|
Сталь40 |
Сталь 10У |
|||
|
Температура |
вы- |
ждаю- |
||||||||
термической |
|||||||||||
|
|
|
|
||||||||
|
|
нагрева, оС |
держки, |
щая |
|
|
|||||
обработки |
|
|
|
|
|||||||
|
|
|
|
|
мин |
среда |
|
|
|||
|
|
|
|
|
|
|
|
|
|||
|
|
|
|
|
|
|
|
|
|
|
|
Отжиг |
|
П+ |
П+Ц |
|
|
|
- |
Печь |
9 |
19 |
|
|
|
Ф |
|
|
|
|
|
|
|
||
|
|
|
40 – |
|
У10 – |
|
|
|
|
||
Нормализа- |
С+ |
С+Ц |
|
15 |
Воздух |
15 |
22 |
||||
830…850 |
|
770…7 |
|||||||||
ция |
|
Ф |
|
|
|
|
|
||||
|
|
°С |
|
90°С |
|
|
|
|
|||
Закалка |
|
Т+Ф |
Т+М+Ц+А |
|
15 |
Масло |
41 |
55 |
|||
|
|
|
|
||||||||
|
|
|
|
|
|
|
|
|
|
|
|
Закалка |
|
М |
М+Ц+Аост. |
|
|
|
15 |
Вода |
56 |
66 |
|
Низкий |
от- |
Мотп. |
Мотп.+Ц+А |
200 |
|
30 |
Воздух |
49 |
61 |
||
пуск |
|
|
|
|
|
|
|
||||
|
|
|
|
|
|
|
|
|
|
||
|
|
|
|
|
|
|
|
|
|||
Средний отпуск |
Т |
Т+Ц |
400 |
|
30 |
Воздух |
30 |
41 |
|||
Высокий |
от- |
С |
С+Ц |
600 |
|
30 |
Воздух |
17 |
21 |
||
пуск |
|
|
|
|
|
|
|
||||
|
|
|
|
|
|
|
|
|
|
||
|
|
|
|
|
|
|
|
|
|
|
|
|
|
|
|
280 |
|
|
|
|
|
|