
863
.pdf
который перемешивается с грунтом. В результате твердения известковогрунтовой смеси формируется массив закрепленного макропористого грунта. Поглощение воды так велико, что происходит значительное осушение и укрепление окружающего водонасыщенного слабого глинистого грунта.
На завершающей стадии работ рекомендуется производить дополнительное сплошное укрепление поверхности армированного массива путем устройства коротких известковых армирующих элементов между основными упрочненными дренами. При этом прикладываемая на поверхность массива нагрузка передается на верхние части дренирующих армоэлементов, а не на расположенный между ними слабый грунт. В качестве дополнительного укрепляющего слоя можно использовать железобетонную плиту и обладающие пространственной жесткостью конструкции из слоев геосинтетики и плотного наполнителя, например, смеси песка и щебня или гравия. Метод позволяет увеличивать несущую способность и устойчивость грунтового массива, а также обеспечивает отсутствие динамических воздействий на грунт при производстве работ.
В упрочненном вертикальном элементе, образующемся в процессе твердения смеси, оказывается 50...85 % закрепленного грунта (15...50 % извести). Его прочность увеличивается в 5...20 раз по сравнению с прочностью грунта в природном состоянии. Скорость твердения зависит от температуры грунта, которая должна быть не ниже +4 °С.
Упрочненный материал известковых армоэлементов обладает в 100...1000 раз большей проницаемостью, чем природный грунт, благодаря чему армоэле-
менты |
действуют как вертикальные дрены. Для определения осадок |
|
∑ |
|
основания применяем формулу послойного суммирования. |
|
На примере инженерно-геологического разреза строительной площадки на пересечении улиц Луначарского и Островского были рассчитаны сопротивления глин текучепластичной консистенции до и после дренирования. Согласно расчетам автора статьи Коновалова В. П. [2] прочностные характеристики грунта могут увеличиваться в 5 раз.
Рассчитаем по формуле Пузыревского
[ |
( |
) |
] |
сопротивление грунта до R1=230,98 кПа и после дренирования R2=480,02 кПа Таким образом, мы видим, что расчетное сопротивление грунта увеличи-
лось более чем в 2 раза, что подтверждает эффективность использования такого метода в условиях слабых глинистых оснований.
Увеличение сопротивления в 2 раза позволяет применять более рациональные и дешевые конструкции фундамента.
Литература
1.Кочеткова Р.Г. Основания, фундаменты и механика грунтов// НИИОСП. 2012. №1.С.10-12. (Журнал).
2.Коновалов В.П., Безволев С.Г., Коновалов П.А. Основания, фундаменты и механика грунтов// НИИОСП. 2011. №6. С.22-28.(Журнал).
311
МЕХАНИЗАЦИЯ СЕЛЬСКОГО ХОЗЯЙСТВА И ТЕХНИЧЕСКИЙ СЕРВИС В АПК, ТЕХНОСФЕРНАЯ БЕЗОПАСНОСТЬ
УДК 631.22.018
А.В. Аликин – студент 3 курса В.С. Кошман – научный руководитель, кандидат технических наук, доцент ФГБОУ ВПО Пермская ГСХА
ОПРЕДЕЛЕНИЕ МИНИМАЛЬНОЙ ПЛОЩАДИ ТЕПЛООТДАЮЩЕЙ ПОВЕРХНОСТИ МЕТАНТЕНКОВ БИОГАЗОВЫХ УСТАНОВОК
На сегодняшний день для сельскохозяйственных производителей и в Пермском крае актуальными являются вопросы защиты окружающей среды от загрязнений, повышения плодородия почвы и энергообеспечения на местах. Решению этих задач способствует переработка отходов сельскохозяйственного производства, животноводства, птицеводства на биогаз. Процесс протекает в определенной последовательности при участии метанообразных бактерий в анаэробных (без доступа кислорода) условиях. Наиболее богаты питательными веществами, необходимыми для метанового сбраживания, экскременты птицы и животных. Полученный при этом в биореакторах газ (метан) является энергоносителем, а образовавшаяся в результате сбраживания исходного субстрата конечная масса является экологически чистым органическим удобрением. Как показывает практика, его использование на полях улучшает структуру почвы и повышает еѐ плодородие.
Активность метанобразующих бактерий зависит от целого ряда определяющих процесс анаэробного сбраживания факторов, в том числе и от температуры, поддерживаемой в биореакторах (метантенках). Наибольшая активность бактерий наблюдаются при температурах около 33°С и 54°С. При удалении от этих величин (особенно при резких понижениях) метаболическая активность бактерий и их способность к воспроизводству снижаются [1].
При расчете биогазовых установок с целью снижения энергозатрат на поддержание заданной температуры в биореакторах необходимо определение минимальной площади их теплоотдающих поверхностей. Рассмотрим пример решения этой задачи для случая биореактора цилиндрической формы.
Как известно, объем цилиндра V определяется по формуле
, |
(1) |
где R – радиус основания; H – высота.
Цилиндр должен иметь минимальную площадь боковой поверхности
, |
(2) |
которую и необходимо найти.
312

Из формулы (1) высоту цилиндра H выражаем через его объем V:
(3)
Подставляем это выражение в равенство (2) и получаем соотношение, связывающее объем V биореактора с площадью его поверхности F и радиусом R:
|
|
|
|
|
|
|
|
|
|
(4) |
||
|
|
|
|
|
|
|
|
|
|
|||
Экстремум функции |
|
при |
|
|
найдем, приравняв к ну- |
|||||||
лю еѐ первую производную по радиусу R: |
|
|
|
|||||||||
|
|
|
|
|
|
|
|
|
|
|
|
(5) |
|
|
|
|
|
|
|
|
|
|
|
|
|
Экстремум функции |
будет иметь место при радиусе |
|||||||||||
Поскольку вторая производная |
|
|
|
√ |
|
. |
|
(6) |
||||
|
|
|
|
|
|
|||||||
|
|
|
||||||||||
|
|
|
|
|
|
|
|
|
|
|
|
|
|
|
|
|
|
|
|
|
|
|
|
(7) |
|
|
|
|
|
|
|
|
|
|
|
|
то есть больше нуля, то точка экстремума соответствует минимуму боковой поверхности цилиндра, являющейся поверхностью теплообмена биореактора с окружающей средой.
Объем V биореактора определяется по формуле
, |
(8) |
где – объем суточной загрузки биореактора;
K – коэффициент, учитывающий долю ежесуточно заменяемого сбраживаемого субстрата;
– объем материала конструкции биореактора.
Тогда при известной величине объема V биореактора цилиндрической формы его радиус R можно определить по формуле (6), а его высоту H по соотношению (3).
Поставляя найденные величины в формулу(4), можно рассчитать площадь теплоотдающей поверхности.
Полученные в работе расчетные соотношения, на наш взгляд, представляют практический интерес и могут быть использованы при проектировании биогазовых реакторов.
Литература
1. Ковалев А.А. Технологии и технико-энергетическое обоснование производства биогаза в системах утилизации навоза животноводческих ферм: диссертация доктора технических наук/ А.А. Ковалев. – М., 1998.- 320 с.
313
УДК 621.793.669.718
Н.М. Бородин – аспирант А.И. Горчаков, профессор, Ю.В. Щербаков, профессор – научные руководители, ФГБОУ ВПО Пермская ГСХА
ВЛИЯНИЕ ЛЕГИРОВАНИЯ ЧЕРЕЗ ЭЛЕКТРОЛИТ НА ИЗМЕНЕНИЕ ТОЛЩИНЫ И СВОЙСТВ ОКСИДНОГО СЛОЯ
Микродуговое оксидирование в настоящее время является практически единственно возможным методом поверхностной обработки разнообразных деталей из алюминия и его сплавов с целью получения многофункциональных защитных покрытий. Отличительной особенностью МДО является образование в процессе формирования покрытия поверхностных микродуговых разрядов, оказывающих термическое, плазмохимическое и гидродинамическое воздействие на формирование покрытий. Состав и структура получаемых керамикоподобных слоев существенно отличаются от аналогичных характеристик основы. При эксплуатации эти слои проявляют себя лучше, чем обычные анодные оксидные пленки. [2]
Существенным преимуществом процесса МДО, по сравнению с анодированием, является его экологичность (используются слабощелочные электролиты), отсутствие необходимости в тщательной предварительной подготовке поверхности детали, а также значительное увеличение толщины получаемого оксидного слоя. Как известно [1, 2], изменение физико-механических характеристик поверхности изделия при микродуговом оксидировании происходит за счет образования оксидного слоя после подачи напряжения на электроды, одним из которых является обрабатываемая деталь, а вторым – электролит.
Благодаря хорошему сочетанию механических и электрохимических свойств формируемых покрытий МДО позволяет решать широкий круг прикладных задач. Однако практическое применение МДО требует увеличения производительности, толщины и комплексного повышения физико-механических свойств покрытий.
Рассмотренные ранее способы увеличения толщины оксидного слоя частично решают эту задачу. Наиболее доступными являются технологические факторы: токовые режимы, время получения покрытия, состав, концентрация и температура электролита.
Скорость роста покрытия увеличивается с увеличением плотности тока. Это связано с тем, что быстрее наступает стабилизация рабочего напряжения на образцах, характеризующая переход предварительных стадий процесса МДО (стадии анодирования и искрения) в рабочую стадию, при которой формируется основное покрытие. Однако увеличение плотности тока при большой продолжительности МДО приводит к увеличению мощности микродуговых разрядов, разрыхлению покрытия и, как следствие этого, снижению его качества, например, коррозионной стойкости.
314
Влияние времени оксидирования, состав, концентрация и температура электролита достаточно полно изучены и показано, что перечисленные технологические параметры имеют свои пределы по влиянию на толщину оксидного слоя.
Дополнительное решение поставленной задачи достигается путем легирования оксидного слоя через электролит. Для этого в состав электролита требуется добавление элементов, которые внедряются в структуру покрытия, обеспечивая увеличения скорости роста покрытия, его толщины и формирование уникальных свойств.
Как известно, основу покрытий, формируемых при МДО на сплавах алюминия составляют оксидные фазы α-Al2O3 и γ-Al2O3. Кроме того в покрытии содержатся гидрооксиды алюминия Al(OH)3 и AlО(OH), а также соединения элементов электролита и материала оксидируемой детали.
Для соблюдения родственной природы основного оксидного слоя и имплантантов в электролит добавляли Al2O3 (корунд), оксид хрома Cr2O3, диоксид титана TiO2.
Для снижения коэффициента трения в режиме сухого трения покрытия в качестве твердой смазки добавляли дисульфид молибдена MoS2.
Корунд в электролит вводили в виде тонких микропорошков (ГОСТ 364780) размер фракции от 3,0 до 5,0 мкм, что является сопоставимым со средним размером зерен покрытия. Концентрацию изменяли в пределах от 5 до 65 г/л. Остальные компоненты брали такой же грануляции, а концентрацию изменяли в пределах 2-10 г/л.
Покрытия формировали на образцах из алюминия Д16 размером 30х20х3 мм в электролите состава: КОН – 3 г/л; жидкое стекло Na2SiO3 модуль 4-8 г/л, перекись водорода 130 г/л, изопропиловый спирт – 25 г/л. [2] Постоянными параметрами оставались: температура электролита 20оС; время оксидирования – 40 мин.; плотность тока – 20 А/дм2. Оптимизация этих параметров была обоснована нашими предварительными исследованиями.
Обязательным условием оксидирования является равномерное распределение легирующих порошков в объеме электролита. Это достигалось активным перемешиванием в ванне электромеханическим миксером. Кроме того, непосредственно в зоне оксидирования осуществляли борботаж кислородом через шпреерный насадок, что, кроме перемешивания, способствует активизации образования оксидов.
Критериями оценки результатов исследований являлось формирование толщины слоя, его микроструктура и микротвердость, фазовый состав покрытия.
Толщину слоя и микроструктуру изучали в поперечном сечении образца на металлографическом микроскопе МИМ-8 по программе «ВидеоТест – металл 1.0». Микротвердость покрытий измеряли на микротвердомере ПМТ-3.
Износостойкость покрытий и коэффициент трения определяли по результатам испытаний на трение и износ на машине трения ИИ 5018 по схеме «дискколодочка» при трении в сухую.
315
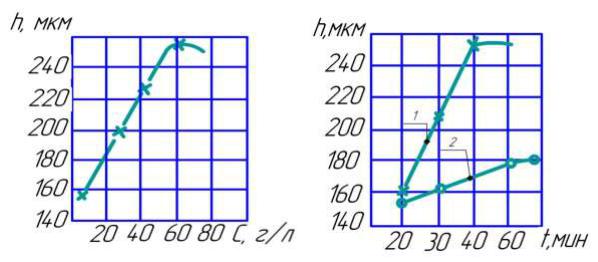
Фазовый состав покрытий изучали с помощью дифрактометра ДРОН-3М с применением методов микрорентгеноспектрального анализа в сочетании с методом растровой электронной микроскопии.
По результатам исследований установлено, что на кинетику роста толщины оксидного слоя легирование через электролит оказывает положительное влияние, рис. 1 и 2. Все имплантированные соединения увеличивают толщину слоя.
Рисунок 1. Зависимость толщины |
Рисунок 2. Зависимость толщины ок- |
оксидного слоя h, мкм от концен- |
сидного слоя h, мкм от времени окси- |
трации корунда С, г/л |
дирования τ, мкм в электролите с леги- |
Без легирования максимальная тол- |
рованием (1) и без (2) |
щина – 170 мкм |
|
Оптимизируя концентрацию корунда, было установлено, что увеличение его количества более 50 г/л не вызывает заметного роста толщины слоя, а происходит увеличение пористости, что снижает качество покрытия.
Концентрацию Cr2O3 и TiO2, а также MoS2 следует выдерживать на уровне 5 г/л, т.к. при большем содержании, как показали результаты РСА и фрактограмма морфологии слоя, образуются единичные конгломераты выходящие за пределы матричных каналов пробоя.
Результаты РСА показали, что все легирующие соединения, добавленные в электролит, содержатся в составе оксидного слоя.
Некоторое увеличение микротвердости за счет легирования, табл. 1, происходит за счет дополнительных оксидных фаз хрома и титана, которые остаются в процессе электролиза без изменения своего фазового состава.
Снижение коэффициента трения и величины износа, табл. 1., объясняется присутствием твердой смазки. Суммарный износ пары трения замеряли после 8 часов испытаний без изменения нагрузки на пару.
Таким образом, можно сделать вывод, что легирование через электролит является реальным способом увеличения толщины оксидного слоя и его эксплуатационных характеристик.
316
|
|
|
|
Таблица 1 |
|
|
Свойства покрытий МДО |
|
|||
|
|
|
|
|
|
|
Максимальная |
Микротвер- |
Величина |
Коэффициент |
|
|
дость средней |
||||
Вид электролита |
толщина слоя h, |
износа пары |
трения после |
||
зоны, |
|||||
|
мкм |
трения, мкм |
притирки пары |
||
|
HV, ГПа |
||||
|
|
|
|
||
МДО в электролите |
170 |
10 – 14 |
35 |
0,3 |
|
без легирования |
|||||
|
|
|
|
||
МДО в электролите с |
|
|
|
|
|
легирующими добав- |
295 |
14 - 18 |
21,5 |
0,12 |
|
ками |
|
|
|
|
Литература
1.Горчаков А.И. и др. Электролит для микродугового оксидирования алюминия и его сплавов. Патент на изобретение № 242 6823 от 09.03.2010 г.
2.Суминов И.В. и др. Микродуговое оксидирование. М.: Экомет, 2005.- 368 с.
УДК 621.436
П.А. Вятчанин, М.В. Софронов – студенты А.В. Россохин – научный руководитель, доцент ФГБОУ ВПО Вятская ГСХА
БИОЭТАНОЛ КАК ТОПЛИВО ДЛЯ АВТОМОБИЛЬНЫХ ДВИГАТЕЛЕЙ
Применение этанола в качестве топлива и кислородосодержащих компонентов присадок широко и давно известно. Среди различных спиртов и их смесей наибольшее распространение в качестве моторного топлива получили метанол и этанол.
Обычный топливный этанол представляет собой высокооктановый спирт, получаемый путем ферментации сахара, который получают из крахмала зерновых культур, например, кукурузы или пшеницы. Биоэтанол получают ферментацией сахаров, добываемых из растительного волокна из возобновляемых источников сырья, таких как древесина или солома.
Биоэтанол - это жидкое спиртовое топливо, который производится из сельскохозяйственной продукции, содержащей крахмал или сахар, например, из кукурузы, зерновых или сахарного тростника. В отличие от спирта, из которого производятся алкогольные напитки, топливный этанол не содержит воды и производится укороченной дистилляцией (две ректификационные колонны вместо пяти) поэтому содержит метанол и сивушные масла, а также бензин, что делает его непригодным для пищевых целей. Топливный этанол можно также производить из всего, что содержит целлюлозу (солома, опилки, трава).
В настоящее время уже более половины мирового производства этанола используется в качестве добавки к бензину для двигателей внутреннего сгорания (ДВС) и лишь около 10 % - для производства спиртных напитков [2].
Этиловый спирт (этанол) может быть использован при производстве моторных топлив в следующих видах:
317
1.Непосредственно как моторное топливо для специальных двигателей с содержанием этилового спирта до 85 % (так называемые смеси Е 85) с содержанием легких фракций углеводородов 15 %.
2.Как компонент моторных топлив для обычных двигателей с искровым зажиганием при содержании этанола от 5 до 24 % (в России - бензанолы, на западе - так называемый «газохол»).
3.Как добавка к производимым бензинам до 5 %.
4.Как октаноповышающая добавка для повышения октанового числа и очистки топливной системы с содержанием этанола до 98%.
Необходимо отметить, что «чистый» этанол крепостью 95 % и более используется в качестве моторного топлива в сравнительно небольших объемах. Чаще применяются различные смеси бензина с этанолом, содержащие от 5...10 до 85...95 % этанола, при этом в основном используется этанол, полученный из возобновляемых источников растительного сырья, называемый биоэтанолом.
С энергетической точки зрения преимущества спиртов заключаются главным образом в высоком к.п.д. рабочего процесса и их высокой детонационной стойкости. Величина к.п.д. спиртового двигателя выше бензинового во всем диапазоне рабочих смесей, благодаря чему удельный расход энергии на единицу мощности снижается.
При использовании спиртовых топлив снижается содержание контролируемых вредных компонентов отработавших газов (ОГ) двигателя. Благодаря более низким максимальным температурам горения спиртов выделяется значи-
тельно меньше, чем у бензиновых ДВС оксидов азота NOx. Одновременно вследствие улучшения полноты сгорания спиртовых смесей выбросы СО и СН также уменьшаются. Выбросы ПАУ также на порядок ниже, чем при работе двигателя на бензине.
Основными недостатками этанола по сравнению с бензинами являются пониженная теплота сгорания, высокая теплота испарения и низкое давление насыщенных паров, но в целом по моторным свойствам этанол лучше метанола. Наряду с положительной экологической эффективностью использования спиртовых топлив следует отметить и такие негативные явления, как повышенные выбросы альдегидов и испарения углеводородных соединений. Содержание альдегидов растет с увеличением концентрации спиртов в топливной смеси. И если для метанола характерны выбросы формальдегида, в то время как при сгорании этанола образуется преимущественно ацетальдегид. Их снижения добиваются при добавке к спиртам воды (до 5 %) и присадок к топливу до 0,8 % анилина, подогреве воздуха на входе в двигатель.
В качестве моторного топлива для автомобилей за рубежом этанол стал использоваться уже с начала 20 века. Так, в 1908 году Генри Форд создал модель Т, работающую на этаноле. И сейчас доля автомобилей, использующих этанол в качестве моторного топлива очень значительна и постоянно возрастает. Об этом свидетельствует и статистика мирового производства этанола и доли в нем топливного этанола для ДВС.
318
Из всего объема производимого этилового спирта в пищевых целях расходуется около 8 %, около 12 % потребляет химическая промышленность, а основная доля (80 %) идет на производство топлива для автомобилей. По прогнозам специалистов уже в 2010 году будет произведено около 60 млрд. л топливного этанола.
В этом качестве этанол используется практически во всех промышленноразвитых странах. Например, в США до 60 % товарного бензина используется при добавках этанола от 5 до 10 % (так называемый бензин Е 10, или «Газохол» с содержанием этанола 10 %).
Проанализировав жизненный цикл этанола, департамент сельского хозяйства США пришел к выводу, что он вырабатывает 134 % энергии, затрачиваемой при выращивании, уборке и переработке кукурузы. Бензин же возвращает лишь 80 % энергии, используемой в его производстве.
ВСША разработан стандарт на топливный этанол для автомобилей с искровым зажиганием (ASTM D 5798-99) (см. таблицу 2).
По данным исследования, проведенного компанией AUS Consultants, благодаря введению новых стандартов на содержание этанола в автомобильных бензинах импорт сырой нефти в США к 2012 г. сократится более чем на 250 млн. т. Наибольшее распространение газохол получил в Бразилии, где с 1975 г. осуществляется правительственная программа использования возобновляемых источников растительного сырья для производства этанола и его употребления в качестве автомобильного топлива. Сейчас уже более 90 % автомобилей в стране работают на моторном топливе, содержащем этанол [3].
Как же обстоят дела по производству топливного этанола в России. В России в 2005 году было произведено около 1 млрд. л этанола, но как топливо он не используется. В настоящее время Россия осталась одной из немногих стран в мире, где этанол не используется даже в качестве добавок к бензинам, несмотря на значительные свободные мощности по производству спирта и то, что этанол допущен как добавка к стандартным бензинам до 5 % по объему.
По ориентировочным оценкам ВНИИ НП, в России мощности по производству этанола, который может использоваться в составе бензина, составляют около 320 тыс. т (около 1 % от объема производства бензина), в том числе 200 тыс. т гидролизного и 120 тыс. т синтетического этанола.
При этом большая часть экспортируемого из России в Европу зерна, а это около 10 млн. т, идет на производство топливного этанола.
Внастоящее время разрешение на производство бензина по ТУ 38.401-58- 244-99 «Бензины автомобильные неэтилированные, содержащие этанол» имеют предприятия отрасли (ОАО «ЛУКОЙЛ - Волгограднефтепереработка», ОАО «Новокуйбышевский НПЗ») и ряд нефтебаз.
ОАО «ВНИИ НП» совместно с ЗАО НПО «Химсинтез» разработали национальный стандарт - ГОСТ Р 52201-2004 «Этанольное моторное топливо для автомобильных двигателей с принудительным зажиганием. Бензанол. Общие технические требования». На бензанолы наряду с ГОСТом разработаны и утвер-
319
ждены технические условия (ТУ 38.401-58-330-2003), в которых в зависимости от детонационной стойкости (по исследовательскому методу) предусматривается производство бензанолов трех марок: БИ-80, БИ-92 и БИ-95 [1].
Основным препятствием широкого использования этанолсодер-жащих моторных топлив является высокая стоимость этанола. Но она во многом определяется акцизным сбором, который в России, например, одинаков и для пищевого этанола, и для этанола денатурированного, используемого для технических целей, в том числе и в качестве моторного топлива. Стоимость производства топливного этанола зависит от целого ряда факторов, таких как величина налогообложения на производство спирта, урожайность сельскохозяйственных культур, из которых его производят и которые возделываются в этом регионе, степенью развитости инфраструктуры и т.д.
Таким образом, на сегодняшний день созданы все предпосылки для широкого использования этанола в качестве топлива в бензиновых ДВС, в том числе в существующих двигателях. Накопленный зарубежный опыт показывает очевидные преимущества (экономические и экологические) использования этого возобновляемого вида топлива.
Литература
1.ГОСТ Р 52201-2004. Топливо моторное этанольное для автомобильных двигателей с принудительным зажиганием. Бензанолы. Общие технические требования. - М.: Изд-во стандартов, 2004. – 130 с.
2.Этиловый спирт в моторном топливе. Под ред. В.В. Макарова, 250 с.
3.Емельянов В.Е. , Макаров В.В. Этанолсодержащее топливо // Мир нефтепродуктов. 2006. - № 1. – С. 40.
УДК 621.436
П.А. Вятчанин – студент 3 курса А.В. Россохин – научный руководитель, доцент ФГБОУ ВПО Вятская ГСХА
СНИЖЕНИЕ ДЫМНОСТИ ОТРАБОТАВШИХ ГАЗОВ ДИЗЕЛЯ С ТУРБОНАДДУВОМ 4ЧН 11,0/12,5 ПУТЕМ ПРИМЕНЕНИЯ ПРИРОДНОГО ГАЗА
Один из наиболее значимых токсичных компонентов отработавших газов (ОГ) дизелей - твердые частицы (ТЧ). Основными составляющими ТЧ являются сажа, оксиды металлов, сульфаты и вода, а также в меньших объѐмах - несгоревшие частицы топлива и моторного масла [1].
Наличие сажи в ОГ приводит к появлению неприятного ощущения загрязненности воздуха и ухудшению видимости. При вдыхании сажи ее частицы оказывают вредное воздействие на дыхательные органы человека. Они достигают альвеол легких или откладываются в носовых пазухах, трахеях или бронхах, вызывая хронические заболевания. Но основные токсические свойства сажи обу-
320