
книги из ГПНТБ / Глухов Л.Н. Подземные резервуары для светлых нефтепродуктов
.pdf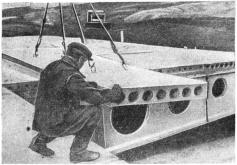
Рис. 39. Засыпка резервуара грунтом.
J — грунт, перемещенный бульдозером пз отвала; 2 — экскаватор, оборУДОранныи грейфером или бадьей; 3 — цементная стяжка; 4 — наток; 5 — бульдозер.
На основании опытных работ по строительству траншейных резер вуаров разработан проект «Технических условий на устройство оснований, изготовление, монтаж и приемку подземных резер вуаров траншейного типа», главные положения которых приво дятся в приложении 1 в конце книги.
В приложении № 2 дан «Проект норм времени и расценок па монтаж траншейного резервуара без ограждающих стен», соста вленный по материалам нормативно-исследовательской станции Воронежского совнархоза, проводившей опытное наблюдение, хронометраж и фотографирование рабочих процессов.
Дальнейшее улучшение организации работ по строительству подземных резервуаров
В процессе сооружения опытных подземных резервуаров обна ружились как недостатки самой конструкции, так и методов работ. Казематным резервуарам свойственны следующие основ ные недостатки:
1)низкая степень индустриализации строительства и большой объем работ, выполняемых вручную;
2)разнотипность строительных конструкции и элементов;
3)большой расход основных строительных материалов в со
четании с высокой трудоемкостью работ и высокой стоимостью строительства;
4)возможность загазированпя каземата парами нефтепродук тов и необходимость строительства напорно-вытяжной вентиля ции с кирпичными воздуховодами;
5)нецелесообразность применения в резервуаре ГПИ «Промстройпроект» металлического настила по железобетонным плитам покрытия против диффузии паров.
С целью устранения отмеченных недостатков авторы предла гают:
для монтажа металлического резервуара использовать завод ские рулоны, а для подпорных стен каземата — сборные бетон ные блоки пли железобетонные панели;
отказаться от строительства стационарной напорно-вытяжной вентиляции казематов, использовав передвижные вентиляционные установки (следует заметить, что за 2 года эксплуатации на опыт ных резервуарах не было вентиляции воздуха казематов, так как анализы воздуха не подтверждали наличия в нем паров бензина);
исключить листовой металл из покрытия резервуаров, заменив его сборными железобетонными плитами с устройством пароизо-
ляцпи пз неметаллических материалов; применить для любого типа подземных резервуаров сифонные
трубопроводы или погружные насосы, ликвидировав тем самым строительство глубоких камер управления задвижками.
При сооружении опытных траншейных резервуаров также были выявлены некоторые недостатки.
60
Недостаточно использовались механизмы па строительстве пес чаного основания и гидрофобного слоя, па что ушло более 15 рабо чих дней на один резервуар. Широкое применение механических катков, площадочных вибраторов и ленточных транспортеров поз волит резко сократить сроки сооружения песчаного основания и изоляционного слоя.
Неполностью соблюдались правила техники безопасности при гидроизоляции металлической оболочки. Для нормальной работы необходимо использовать специальные стопоры, ограничивающие прижатие оболочки к стенке в момент обрыва троса-ограничителя, а ручную кистевую обработку металла горячим битумом заменить механизированной.
Значительно затрудняет и удлиняет возведение резервуара множество различных строительных работ: монтаж сборных железобетонных элементов, мокрый процесс бетонирования фун даментов и отдельных мест покрытия, кирпичная заделка торцов балок и карнизов торцовых стен. Следует заменить кирпичную кладку и монолитный бетон па сборные железобетонные элементы и в первую очередь па строительстве столбовых фундаментов под металлические колонны, так как объем бетонных работ при соору жении ленточных бутобетонных фундаментов увеличился па
90м3.
Врезервуаре с металлическим каркасом нецелесообразно строить торцовые бетонные стены. Опытами установлено, что металлическая оболочка самостоятельно воспринимает давление жидкости и грунта. Кроме того, следовало бы переконструировать металлический каркас, резко сократив расход металла (замена верхних поясов ферм и связей на железобетон), и исключить устройство колонн, которые требуют больших трудовых затрат, повышенной точности при монтаже и защемляют свободно лежа щую оболочку.
При монтаже составных балок НИИ-200 применялась упро щенная траверса ВНИОМС с двумя захватами вместо специальной
траверсы |
«Стальмонтаж-5». Применение упрощенной траверсы, |
а также |
дефектность закладных металлических планок привели |
кразрушению двух составных балок при монтаже.
Впериод гидравлического испытания резервуара с бетонными стенами была отмечена незначительная деформация металли ческой облицовки с образованием местных выпучпн-карманов. Это
объясняется тем, что металлическая оболочка была неплотно пригнана к грунту в углах перехода откоса к вертикальной стенке. При дальнейшем строительстве траншейных резервуаров следует подбивать полотнища бойком в угловых переходах или изменить профиль котлована с устройством плавных (закругленных) пере ходов.
После годичной эксплуатации траншейных резервуаров (запол ненных автобензином) в 1959 г. было установлено, что покрытие из сборных железобетонных плит негерметичпо и через швы в плп-
61
тах проникали пары бензина. Повышенного избыточного давления в резервуаре также не удалось создать, а суточный перепад темпера тур газового пространства резервуара доходил до 5—6° С. Все это заставило изыскать новые способы герметизации ir термоизо ляции покрытия. По рекомендации ВНИИСТ на резервуаре с ограждающими стенами было произведено торкретирование по крытия пз цементного раствора состава 1:2с добавкой жидкого стекла (удельныйвес 1,40) в количестве 2% от веса цемента. Тор кретирование производилось по тканой стальной сетке. Для вто рого резервуара при герметизации покрытия был рекомендован ви нипласт рулонный толщиной 0,5—1 мм без приклеивания его к плптам покрытия. Склеивание полотнищ винипласта между собой и его приклеивание к металлической облицовке производится клеем № 88 пли перхлорвиниловым клеем. По винипласту пли торкретраствору укладывается слой асфальта толщиной 25—30 лл с последующей засыпкой грунтом не менее 50 см или устройством термоизоляции пз пенобетона с засыпкой на 20—30 см грунтом. Необходимо отметить, что при сооружении опытных резервуаров работниками нефтебазы строительных трестов № 25, № 118, Сварочно-монтажного треста № 65 и совнархоза был предложен ряд принципиально новых решений по организации работ. Осо бого внимания заслуживает методика изготовления, транспортиро вания п монтажа укрупненных металлических рулонов. Задача заключается в том, чтобы обобщить опыт строительства и распро странить его на другие строительные площадки.
Основные технико-экономические показатели и выводы по строительству опытных подземных резервуаров
Общий срок строительства казематного резервуара ГПИ-6 составил 17 месяцев, казематного резервуара ГПИ «Промстройпроект» — 20 месяцев.
Расход основных строительных материалов и стоимость строи тельства для казематных резервуаров приводятся в табл. 2 и 3.
Расход металла по деталям резервуара ГПИ-6 составил: на арма туру для плит покрытия — 7,55 т, на днище — 33,9 т, на кровлю — 17,48 т, на колонну и фермы — 30,5 т, па корпус — 38,58 т. Если исключить утяжеленные профили металлоконструкций и использовать проектные сечения, то общий расход металла не превысит 112,58 т, что также отразится на стоимости строи тельства резервуара, которая составит примерно 490 тыс. руб., или 112,5 руб., на 1 ле3 емкости.
Расход металла по частям конструкции «Промстройпроект» со ставил: на днище — 41,48 т, на корпус — 31,8 т, на кровлю — 15,46 т, на колонны, балки, связи — 27,58 т, па арматуру плит покрытия — 9,36 т, на арматуру стен каземата — 44,45 т и на арматуру железобетонного основания — 10,95 т. Расход бетона
62
Таблица 2
Основные технико-экономические показатели опытного казематного резервуара ГПИ-6
Показатели
Емкость резервуара, л«3.................................. |
•. . |
|
Расход бутобетона |
».......................... |
|
» бетона |
» ................................... |
|
Всего расходуется металла, |
т...................... |
В том числе, т:
Данные по |
Данные опыт |
|||
ного строитель |
||||
проекту |
||||
|
ства |
|||
|
|
|
||
всего |
на 1 .и3 проектной емкости |
всего |
на 1 м 3 фактиче ской ем кости |
|
|
|
1 |
|
|
4600 |
|
4346 |
|
|
164 |
0,034 |
160 |
0,037 |
|
50 |
0,001 |
86 |
0,002 |
|
123 |
26,8 кг |
128 |
29,3 кг |
арматуры....................................... |
6 |
1,3 кг |
7,5 |
1,5 |
» |
|
металлоконструкций.............................. |
117 |
25,5 |
» |
120,5 |
27,8 |
» |
Стоимость строительства, тыс. руб. |
. . . 464,2 |
101 |
руб. |
505,35 |
116 |
руб. |
Примечание. Данные фактического расхода металла взяты с уче том замены ряда проектных сечений профилей более тяжелыми.
Таблица 3
Основные технико-экономические показатели опытного казематного резервуара ГПИ «Промстройпроект»
|
Данные по |
Фактические |
||||
|
проекту |
|
|
данные |
|
|
Показатели |
|
на 1 |
|
|
на 1 |
м3 |
|
всего |
м3 |
всего |
фактиче |
||
|
емкости |
ской ем |
||||
|
|
|
||||
|
|
|
|
|
кости |
|
Емкость резервуара, м3............................ |
5000 |
— |
|
5083 |
__- |
|
Расход бетона, -и3................................... |
464,7 |
0,093 |
421,5 |
0,09 |
|
|
Всего расходуется металла, т . . . |
183,88 |
36,8 |
кг |
181,12 |
36,2 |
кг |
В том числе, т: |
|
|
|
|
|
|
арматуры ....................................... |
68,63 |
13,6 |
» |
64,8 |
13,0 |
» |
металлоконструкции................. |
115,25 |
23,2 |
» |
116,32 |
22,9 |
» |
Стоимость строительства, тыс. руб. |
685,24 |
137 руб. |
590,99 |
117 руб. |
||
Примечание. Данные взяты |
без устройства |
камеры |
управления |
|||
и строительства дренажной сети. |
|
|
|
|
|
|
на плиты покрытия — 97,74 jf3, на бетонную плиту днища — 99 л«3
истены каземата — 224,72 м3.
Сучетом сооружения камеры управления и устройства дренаж ной сети расход материалов характеризуется следующими дан-
63
нымп: бетона — 655,68 .и3, арматуры — 68,63 т и металлокон струкции — 165,91 т. Стоимость строительства при этом значи тельно возрастает, достигая 722,55 тыс. руб., пли 142,7 руб. на 1 м3 емкости.
Из сравнения технико-экономических показателей видно, что по траншейным опытным резервуарам они значительно выше, чем по казематным.
На сооружение железобетонного траншейного резервуара было затрачено в целом 11 месяцев, а траншейного резервуара с ме таллическим каркасом — 9 месяцев.
Трудоемкость строительства по первому резервуару составила 3200 чел.-дней (пз них на сварочно-монтажные работы 400 чел.- дней), по второму резервуару — 1900 чел.-дней (пз них па сва рочно-монтажные работы 300 чрл.-дней).
Следует отметить, что железобетонный опытный резервуар Гипроазнефти сооружался 17 месяцев, при этом общие трудовые затраты составили 4600 чел.-дней.
Дневная выработка на одного рабочего-монтажника составила: для траншейного резервуара с ограждающими стенами — 620— 750 руб., для траншейного резервуара без ограждающих стен — 730—850 руб., для наземного типового резервуара — 720—1200 руб.
Конструкции траншейных резервуаров отличаются высокой степенью сборностп и резким сокращением ответственных работ на площадке. Так, за счет укрупнения рулонов металлической обо лочки количество элементов, собираемых на площадке, для тран шейных резервуаров сведено до минимума (7 шт.), тогда как в опыт ном резервуаре Гипроазнефти их насчитывается 250 шт. Соответ ственно объем сварочных работ в траншейных резервуарах со ставил 300—500 м против 2500—3000 м для резервуара Гипроаз нефти.
Расход основных строительных материалов и стоимость строи
тельства траншейных резервуаров |
показаны в табл. |
4 и 5. |
|||
|
|
|
|
|
Таблица 4 |
Основные технико-экономические показатели |
опытного |
|
траншейного |
||
резервуара с ограждающими стенами |
|
|
|||
|
|
Данные |
Фактические |
||
|
|
данные опыт |
|||
Показатели |
|
по |
|||
|
ного строи |
||||
|
|
проекту |
|||
|
|
|
тельства |
||
|
|
|
|
|
|
Общая емкость резервуара, м3 ....................... |
• |
5200 |
|
5150 |
|
Стоимость строительства, |
тыс. руб. . . |
483,24 |
|
628,97 |
|
В том числе стоимость 1 |
м3 емкости, руб( |
92,6 |
|
121,8 |
|
Всего расходуется металла, т........................... |
. |
74,2 |
|
79,5 |
|
В том числе на 1 м3 емкости, кг ... . |
14,2 |
|
15,4 |
||
Всего расходуется бетона, м3............................ |
|
615,5 |
|
679 |
|
В том числе на 1 м3 емкости................. |
|
0,117 |
|
0,132 |
По элементам конструкции фактический расход металла соста-. вил, т\
металлическая облицовка............................... |
57,88 |
стальные конструкции ........................................ |
1,27 |
арматура сборных железобетонных элемен |
|
тов . . . ............................................................. |
20,22 |
-арматура монолитногожелезобетона . . . |
0,13 |
Всего . . |
79,5 |
Фактический расход бетона на отдельные части конструкции составляет, м3:
на |
фундаментные блоки.................................. |
84,66 |
|
» |
стеновые |
» |
411,32 |
» |
балки НИИ-200 |
|
50,60 |
» |
плиты покрытия............................................... |
119,56 |
»замоноличпвание отдельных узлов . . 12,86
Всего . . 679
Затраты по отдельным видам работ, тыс. руб.:
разработка |
котлована....................................... |
|
106,51 |
|
изоляция основания........................................... |
|
|
22,70 |
|
металлическая облицовка.............................. |
|
121,62 |
||
фундаменты и стены........................................... |
|
221,68 |
||
балки покрытия ............................................... |
|
|
42,68 |
|
плиты |
» ............................................... |
. |
. |
80,54 |
цементная стяжка и глиняный замок |
30,20 |
|||
|
Всего |
. |
. |
628,97 |
Возрастание объема бетонных работ и стоимости строительства против проектных данных объясняется использованием стеновых блоков с увеличенной толщиной.
Таблица 5
Основные технико-экономические показатели опытного траншейного резервуара без ограждающих стен
Показатели |
|
Данные по |
Фактические |
|
проекту |
данные |
|
|
|
||
Емкость резервуара, .«• |
...................................тыс . руб . . . . |
5380 |
5300 |
Стоимость строительства, |
349,64 |
531 |
|
В том числе стоимость 1 |
м 3 емкости , руб . |
64,8 |
100,0 |
Расход металла — всего, т .................................. |
|
103,73 |
102,42 |
В том числе на 1 м3 емкости, |
кг ... . |
19,3 |
19,3 |
Расход бетона — всего, л«3.............................. |
-и3 . . . |
163,7 |
305,94 |
В том числе на 1 .и3 емкости, |
0,03 |
0,058 |
|
5 Заказ 2012. |
|
|
65 |
По отдельным конструкциям резервуара фактический расход металла составил, т:
на арматуру железобетонных плит . . . |
5,5 |
||
» |
» |
фундаментов............................... |
4,82 |
» |
металлическую оболочку.......................... |
57,71 |
|
» |
металлоконструкции ................................... |
34,39 |
Всего . .102,42
Фактический расход бетона по элементам сооружения распре делился следующим образом, м3:
на фундаменты .................................................... |
161,6 |
|
» |
стеновые блоки .......................................... |
29,26 |
» |
плиты покрытия.......................................... |
99,94 |
»замонолпчиванпе отдельных участков . 15,14
Всего . . 305,94
Значительное увеличение расхода бетона по сравнению с про ектными данными объясняется устройством ленточных монолит ных фундаментов вместо сборных столбовых.
Фактическая стоимость резервуара по отдельным видам работ составила, тыс. руб.:
земляные работы ................................................ |
|
75 |
изоляция................................................................. |
|
17,4 |
фундаментные и стеновые блоки ..... |
94,94 |
|
плиты покрытия ................................................ |
. . . |
93,17 |
цементная стяжка и глиняный слой |
48,86 |
|
оболочка и металлоконструкции................. |
201,63 |
Всего . . 531,0
Надежность работы траншейных резервуаров при эксплуатации подтверждается многими фактами.
Так, длительное время резервуары находились под гидравли ческим испытанием. Прп этом нарушений конструкции и образова ния дефектов не было обнаружено.
Никаких нарушений и дефектов не было выявлено и при за полнении резервуаров продуктом, которое проводилось в ян варе— феврале 1958 г. при отрицательной температуре продукта до -20°.
Постоянные наблюдения в течение годовой эксплуатации ре зервуаров также не выявили каких-либо нарушений и изменений конструкции.
Результаты строительства и эксплуатации опытных траншейных резервуаров позволяют сделать следующие выводы:
1) строительство резервуаров возможно в любом месте Совет ского Союза независимо от климатических условий (при отсут ствии подпора грунтовых вод);
66
2)монтаж резервуаров можно вести при помощи обычных строймеханизмов (экскаваторы, автокраны, тракторы, бульдо зеры), широко применяемых в строительстве;
3)сооружение резервуаров не представляет больших трудно стей, так как основные строительные процессы заключаются лишь
вмонтаже готовых конструкций при минимальном количестве работ (особенно сварочных) на площадке;
4)при строительстве нефтебазы с траншейными резервуарами можно применить поточный метод производства работ, что резко' снизит трудовые затраты на строительство резервуаров;
5)в подземных резервуарах качественная характеристика продукта сохраняется значительно дольше, чем в наземных резер вуарах, за счет резкого сокращения потерь нефтепродуктов от испарения.
Учитывая удовлетворительные технико-экономические дан ные, надежность конструкции и сравнительную простоту соору жения, следует рекомендовать конструкции подземных траншей ных резервуаров для широкого промышленного строительства.
III. ОСОБЕННОСТИ ЭКСПЛУАТАЦИИ ОПЫТНЫХ ПОДЗЕМНЫХ РЕЗЕРВУАРОВ
В практике строительства подземных резервуаров общеприня той является схема подключения резервуаров технологическими коммуникациями к подземной насосной станции па глубине зало жения резервуаров. По этому принципу была составлена техноло гическая схема для подземного казематного резервуара Промстройпроекта, которая мало чем отличается от схемы для наземных резервуаров. Работоспособность этой схемы подтверждена прак тикой эксплуатации.
Технологические трубопроводы диаметром 250 мм проклады вали на глубине 6—7 м и подключали к гребенке управления под земной насосной станции, имеющей заглубление 7 м от поверх ности.
На высоте 30 см от днища трубопроводы врезались в резер вуар, а коренные задвижки располагались в специальном колодце управления на глубине 6 м. Зачистной трубопровод диаметром 100 мм прокладывали самостоятельно па глубине 6—7 м.
Однако для подземных резервуаров (особенно подземных неф тебаз большой емкости) такая технологическая схема не может широко применяться.
Прокладка трубопроводов на значительной глубине вызывает увеличение объема земляных работ. Устройство подземных трубо проводов обходится в 3—4 раза дороже, чем наземных, кроме того, необходимо сооружать на большой глубине колодцы упра вления задвижками.
Вследствие разности температур перекачиваемого продукта (до —40° С) п металла труб (до -f-8° С) значительно увеличивается
67:
опасность разрыва трубопроводов, при этом чрезвычайно затруд-
•■-нены поиски места разрыва и ликвидации дефектов.
Трудно также осуществить автоматическое управление боль шим количеством запорной арматуры трубопроводов, находя щейся глубоко под землей.
Учитывая серьезные недостатки, свойственные технологи ческой схеме подземных трубопроводов, ГПИ-6 в 1954—1955 гг. по предложению С. Я. Бортаковского и Е. Н. Власова разрабо тал ряд схем, основанных па использовании сифонных трубопро водов и погружных бензиновых насосов.
Перекачка нефтепродуктов по сифонным трубопроводам
Сифонными называются трубопроводы, работающие при да влении ниже атмосферного. Предельная высота сифонного трубо провода (высота всасывания) соответствует величине вакуума, создаваемого вакуум-насосом (для насосов РМК до 600—700 мм рт. ст. пли 10—12 м высоты). Для гарантийной работы сифонного трубопровода необходимо, чтобы остаточное давление в трубо проводе было больше упругости паров сливаемого продукта, а си фонный приемник или ось насоса находились ниже дна резер вуара на величину потерь на трение в трубопроводе.
Технологическая схема с сифонными трубопроводами обладает рядом положительных качеств: трубопроводы по этой схеме про кладывают на поверхности земли или па небольшой глубине; отпа дает необходимость в строительстве глубоких колодцев упра вления; при разрыве трубопроводов автоматически прекращается перекачка продукта; не вызывает трудностей и определение места разрыва и ремонт трубопроводов.
Из графиков абсолютных напоров и вакуумов рис. 40 видно, что для устойчивой работы сифонные трубопроводы необходимо проектировать ниже линии упругости паров, изображенной на графпке. Очень важно, чтобы по мере удаления трубопровода от резервуара отметки трубопровода понижались. При этом трубо провод не должен пересекать линии упругости паров бензина при максимальной температуре продукта в резервуаре. Желательно также, чтобы узлы переключения, задвижки и насосы распола гались на трубопроводе не в зоне вакуума, а в зоне избыточного давления. Ниже дается пример расчета для точки «6» сифонного ■трубопровода (график рис. 40).
Данные для |
расчета |
|
||
Производительность перекачки Q, |
м3/час . . . |
300 |
||
Продукт ............................................................................... |
|
|
|
бензин |
Удельный вес, т/м3 ............................................................................. |
|
|
|
0,72 |
Температура бензина при |
перекачке t, |
°C ... |
4-20 |
|
Упругость паров по Рейду, мм рт. ст......................... |
|
не более 500 |
||
Барометрическое давление |
» » |
» |
.... |
720 |
Гидравлический уклон (по расчету) i.................. |
|
0,009 |
68