
книги из ГПНТБ / Глухов Л.Н. Подземные резервуары для светлых нефтепродуктов
.pdfБолее простым оказался способ формирования углов без подрезки — путем применения местной нагрузки. В качестве нагрузки были использованы бетонные блоки весом 2 т, которые трактором С-80 протаскивались несколько раз по перегибу метал лической облицовки. Время на установку торцового рулона для бригады в 5 человек составило 3 рабочие смены, а при использо вании местной нагрузки оно уменьшилось до 2 рабочих смен.
Рис. 26. Монтаж рулонов металлической облицовки методом переворачивания.
1 — трактор С-80 (укладка металлического листа); 2 — противокоррозийная обмазка битумом; 3 — трактор С-80 (раскатка рулона); 4— якоря.
После укладки рулонов верхние их кромки вдоль продольных стенок были подтянуты внутрь котлована и закреплены тросомограничителем, что необходимо для ведения дальнейших работ — укладки стеновых блоков и гидроизоляции оболочки с наружной стороны. При подвертывании верхних кромок внутрь котлована концы полотнищ были заякорены снаружи тросами-расчалками, чтобы предупредить самопроизвольное свертывание полотнища.
Следующей стадией работ после завершения монтажа метал лической оболочки (рис. 28) была сварка нахлесточных соедине-
4 Заказ 2012. |
49 |
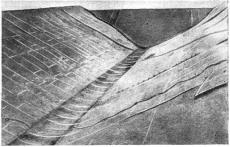
Рис. 27. Монтаж рулонов металлической облицовки методом развертыва ния.
I__ трактор С-80 (раскатывание рулона); 2 — трактор С-80 (торможение рулона); 3 — металлические рулоны.
Рис. 28. Общий вид уложенных рулонов ме таллической 'облицовки.
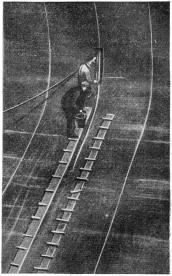
пни и испытание швов па плотность. Зазор между полотнищами не превышал 1—1,5 мм, сварка велась высококвалифицированными сварщиками непосредственно без подтяжки листов и установки прихваток (за исключением верхней части, где эту работу при шлось выполнить). Общая длина сварных монтажных швов соста вила примерно 400—500 м для резервуара с ограждающими сте нами и 250—300 м для второго траншейного резервуара.
Испытание сварных швов на плотность производилось двумя вакуум-камерами (рис. 29). Первой камерой пз плексигласа (длина 1 м, толщина 8 мм) испытывали горизонтальные и криволинейные швы с большим радиусом кривизны. Второй камерой (из целлулоида, длина 40 см, толщина 3 мм) прове ряли сварные швы в углах обо лочки и в труднодоступных местах. Вакуум-испытапию под вергались все сварные швы (заводские и монтажные).
Следует заметить, что ваку умный способ испытания свар
ных швов |
нашел |
в |
настоящее |
|
|
||||
время |
широкое |
распростране |
|
|
|||||
ние. |
По |
качеству |
|
проверки |
|
|
|||
швов он значительно превосхо |
|
|
|||||||
дит химический метод |
(приме |
|
|
||||||
нение аммиака) и испытание |
|
|
|||||||
швов |
керосином. |
По |
данным |
|
|
||||
одного |
пз |
испытаний, |
на резер |
Рис. 29. |
Испытание сварных швов |
||||
вуаре |
емкостью 400 м3 вакуум- |
||||||||
|
вакуум-ка мерой. |
||||||||
камерой было |
обнаружено 55 |
|
|
||||||
дефектов, |
и |
только |
37 дефек |
|
|
||||
тов — керосином; |
при |
испытании днища |
наземного резервуара |
(работу проводил Институт электросварки им. Е. О. Патона) 203 дефекта было обнаружено вакуум-камерой и всего 43 дефекта аммиаком.
Вакуум-агрегат был предложен в 1955 г. инж. Л. К. Хведченя. Разрежение воздуха в вакуум-камере можно создавать вакуумнасосами как с ручным, так и механическим приводом. Вакуум, создаваемый в камере при испытании, — 550—625 мм рт. ст., потребляемая мощность электроэнергии — 1,7—2,2 кет. Разре жение в камере фиксируется вакуумметром. Скорость испытания 10 м швов за 5—10 мин.
Обрезку кромки оболочки (бензорезом) и установку листов ком пенсатора для резервуара с ограждающими стенами проводили
4 |
51 |
после испытания резервуара водой. К обработанной кромке при варивали листы компенсаторов, отбортовывали их на степы, за крепляли анкерными болтами и закладывали верхними стеновыми блоками (рис. 30). Этот очень простой способ устройства металли ческого компенсатора предложен работниками б. Сварочно-мон тажного треста № 65 (В. В. Свистков и др.). ГПИ-6 разработаны два варианта компенсаторов: гидравлический и металлический с устройством закладных деталей — анкеров — в стеновых блоках пли стеновых панелях, к которым приваривается уголок, а затем формируются листы компенсатора.
После окончания сварочных работ по металлической оболочке резервуара без ограждающих стен начинался монтаж металлокон струкций. Заготовка конструкции проходила в мастерских сва рочно-монтажного треста, а укрупненная сборка элементов — на месте строительства. Первоначально монтировались металличе ские колонны рам (рис. 31). Колонны устанавливались автокраном К-32 грузоподъемностью 3 т п стрелой длиной 9 м.
Рихтовку колонн выполняли при помощи трактора С-80. Ко лонны монтировались на фундаментах по двум вариантам: с про резанием «окон» в металлической оболочке и без них. По пер вому варианту бензорезом вырезали отверстия в оболочке, зачищали кромки листов и приваривали к закладной опорной плите. После установки и рихтовки колонны башмак ее привари вали к закладной плите. По второму варианту башмак колонны приваривался непосредственно к металлической оболочке. Уста новка по второму варианту «пепрорезной» колонны оказалась менее трудоемкой.
Металлические фермы и связи монтировались трубоукладчи ком и кран-мачтой. Собранную на площадке ферму подавали к резервуару и спускали по откосу к месту установки трубоуклад чиком грузоподъемностью 10 т. Фермы устанавливались в проект ное положение кран-мачтой с электролебедкой (рис. 32).
После установки ферм уголки поясов и раскосов прижимали струбцинами и приваривали в опорных узлах к колоннам. Про дольные связи и шпангоуты монтировались также кран-мачтой. Общий вид смонтированного каркаса представлен на рис. 33.
В траншейном резервуаре без ограждающих стен функцию продольных стенок выполняла металлическая оболочка, которую при помощи трактора С-80 и автокрана К-32 заворачивали по обрамляющим уголкам шпангоутов. Металлическая стенка была рассчитана на внешнее давление грунта в пустом резервуаре и внутреннее давление жидкости при отсутствии засыпки. Двух недельное испытание резервуара, залитого на полную высоту водой, а также последующая засыпка пустого резервуара, дока зало надежность работы оболочки из металла толщиной 4 мм.
Заворачивание листов полотнища по уголкам шпангоутов выполнялось в следующем порядке. Вначале трактор С-80, со единенный тросом с кромкой листов, поджимал полотнища к обрам-
52
Рис. 30. Конструкции компенсаторов. |
|
|
I — металлический компенсатор сварочно-монтажного треста № 65: 1 — оболочка 6 = 4 |
.мм; |
2 — компенсатор; з — металлические |
анкеры; 4 — цементный раствор; б — стеновые блоки; II — гидравлический компенсатор ГПИ-6: 6 — бетонные блоки; 7 — сталь |
||
ная полоса 4 х 260 мм по всему периметру резервуара; 8 — масло; III — металлический |
компенсатор ГПИ-6 для бетонных блоков: |
|
р — компенсатор из стали 6 = 2 мм; 10 — монтажная деталь; 11 — стальная облицовка 6 = 4 |
мм; IV — металлический компенсатор |
ГПИ-6 для железобетонных панелей: 12 — стальная полоса 4 х 260 мм по всему периметру резервуара.
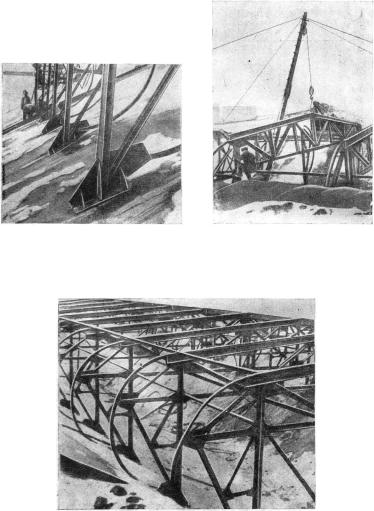
Рис. 31. Общий вид установленных |
Рис. 32. Установка ферм кран- |
колонн, со шпангоутами. |
мачтой. |
Рис. 33. Общий вид смонтированного металлическо го каркаса.
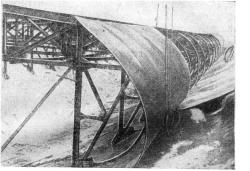
ляющим уголкам. Затем автокран К-32, скрепленный тросом
свнешней поверхностью оболочки, подтягивал полотнища вверх,
атрактор С-80 плотно прижимал их к обрамляющим уголкам (рис. 34). После окончательного поджатия оболочки сварщики крепили электроприхватками оболочку к продольным связям ферм. Заво рачивание листов продольной стенки серьезных трудностей не вызвало. На все продольные полотнища бригада мсщтажников затрачивала одну рабочую смену.
Заворачивание листов полотнища торцовых стенок резервуара
оказалось более трудоемким, что объясняется устройством со пряжения двух криволинейных поверхностей. Для выполнения
Рис. 34. Вид па завернутое полотнище обли цовки.
этой операции работники треста № 65 предложили специальное приспособление, состоящее из основной балки (двутавр № 20), уголков жесткости и ограничивающих фаркопф. Приспособление прихватывалось к торцовым полотнищам, затем при помощи трак тора С-80 листы полотнищ заворачивались и приваривались к фаркопфам. Завернутые крайние полотнища продольных стен соеди няли сваркой через угловые листы с торцовыми полотнищами. Заворачивание торцовых полотнищ было произведено за одну рабочую смену.
Одновременно со сваркой уложенных полотнищ строительные бригады монтировали стеновые п торцовые бетонные блоки. Ра боты велись по всему фронту продольных и торцовых стен с устрой ством гнезд для балок покрытия.
Торцовые степки резервуара без ограждающих стен также возводились из типовых бетонных блоков на цементном растворе. На монтаже блоков был занят кран-экскаватор Э-505, имеющий наибольший вылет стрелы 10 м, наименьший 3,7 м, грузоподъем
55
ность 2,6 т. Заделка гнезд и торцов балок, а также формирование карниза торцовых стен производились красным кирпичом на це ментном растворе. Общее количество уложенных стеновых бло ков для первого резервуара 596. Объем кирпичной кладки 25 м3.
Для несущих элементов покрытия резервуара с ограждающими стенами были использованы сборные железобетонные балки НИИ-200. Блоки этих балок, изготовлявшиеся па заводе железо бетонных конструкций, бетонировались в стальных формах. Арми рование выполнялось сварными каркасами из Ст. 5. Каналы для стержней напряженной арматуры изготовляли в процессе бетони рования блоков путем укладкп газовых (плп резиновых) труб, которые извлекались через 1,5—2 часа после бетонирования. Одновременно в блоки закладывали металлические планки для со единения смежных блоков. Блоки доставляли на стройплощадку на автомашинах и складывали у места их сборки.
Сборка блоков проводилась на специальном металлическом стенде, рассчитанном па одновременный монтаж трех балок. Ос новной деталью стенда является рама, которую собирают из отдельных секций размерами 3000 х 2600 мм и 5820 х 2600 мм. Каждая секция монтируется из двух продольных двутавровых балок, которые ставят на полозья из швеллеров и перекрывают металлическими рпгелямп. На ригелях каждой секции устана вливают узлы регулировочных винтов, при помощи которых балки выверяются в горизонтальном и вертикальном положениях. По ширине стенда расположены три ряда регулировочных винтов, что позволяет собирать одновременно три балки.
При сборке балок между блоками оставляли зазор 10 мм, кото рый заполнялся цементным раствором маркп 400-500 с добавлением хлористого кальция — до 5% от веса цемента. На отверстия ка нала в местах их соединения наклеивали резиновые кольца. Стержневую арматуру Д = 32 мм протягивали при помощи лебедки, первоначально пропуская челнок в канале, к тросу которого прикреплена арматура. Одновременно производили сварку металлических планок смежных блоков.
После затвердения раствора между блоками гидродомкратом, работавшим на высоком рабочем давлении масла (до 300 кГ/см2), создавали натяжение арматурных стержней. Тяговое усилие на стержень составляло 25 т. Гидродомкрат типа СМ-514 одно поршневой, универсальный, передвижной. Общий вес 23,7 кг. Гидродомкрат может работать от механического и ручного при вода. Все части смонтированы па одной тележке. Натяжение кон тролировалось по манометру и тарпровочному графику домкрата. В качестве зажимного приспособления для арматуры применялся стержневой анкер (хвостовик) с нарезкой и гайкой. При натяже нии арматуры шайбу зажима приваривали к хвостовику, а затем до упора навинчивали гайку.
Чтобы предохранить арматуру от коррозии и обеспечить сце пление ее с бетоном, в каналы после натяжения арматурных стерж
56
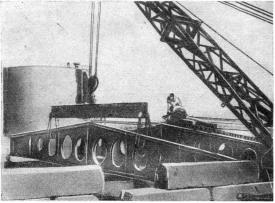
ней нагнетался под давлением цементный раствор (инъекция). Он
нагнетался через специальные тройники из тонкой |
стали — па |
|
трубки, закладываемые при бетонировании блоков. |
В состав це |
|
ментного теста для инъекции входит 62,5% |
портланд-цемента |
|
и 37,5% воды. Перед нагнетанием раствора |
капал |
заполнялся |
водой и продувался сжатым воздухом. Инъектирование произво дилось обычным растворонасосом С-251 с механическим приводом. Производительность пасоса 1 м3/час, рабочее давление 10 кПсмг.
Установка блоков па стенд и монтаж собранной балки выпол- иялись’дпзель-краиом Э-1003 со стрелой длиной 21 м (рис. 35).
Рис. 35. Монтаж балки НИП-200 дизель-краном с применением упрощенной траверсы ВНИОМС.
При наименьшем вылете стрелы грузоподъемность крана соста вляла 15 т. Высота подъема до 11 м. В качестве захватного при способления использовалась удлиненная траверса ВНИОМС. Ко личество мест захватов — два. Проектным институтом разрабо таны правила монтажа составных балок при помощи двух крановэкскаваторов Э-505 (рис. 36). При этом методе снижается стои мость эксплуатации кранов, но увеличивается трудоемкость работ.
Для покрытия резервуара использовались восьмппустотные типовые железобетонные плиты, которые монтировались краном Э-1003 с применением траверсы «Паук» пли краном-экскаватором Э-505 (рис. 37 и 38). Плиты укладывали на цементный раствор по составным балкам пли металлическим фермам. Швы между пли тами затирались цементным раствором. Поверх плит устраивали цементную стяжку состава 1 : 2 толщиной 20 мм.
Стяжка разравнивалась вручную, глиняный замок толщиной 10 см для покрытия резервуаров также выполнялся вручную.
57
На засыпке резервуара грунтом участвовали кран Э-1003 и авто кран К-32. Глина и грунт на покрытие подавались ленточным транспортером. На обсыпке резервуара грунтом и планировке площадки был занят бульдозер Д-157 (рпс. 39). Окончательное испытание резервуара на прочность п плотность состояло в запол-
Рис. 36. Монтаж балки НИИ-200 двумя кранами-экскаваторами Э-505.
1 — кран Э-505; 2 — балка НИИ-200.
Рис. |
37. Схема работы крана |
при |
монтаже плит |
покрытия. |
|
|
|
1 — многопустотные плиты; 2 — кран-экскаватор. |
|
||
нении его |
водой на полную емкость. |
Резервуар с ограждающими |
|||
стенами |
находился под водой |
более 8 месяцев, а |
второй резер |
||
вуар |
2 |
недели. |
|
|
|
За время испытания не было обнаружено деформаций обо лочки и конструкций, а также течи в металлической облицовке.
58