
книги из ГПНТБ / Похмурский, В. И. Коррозионно-усталостная прочность сталей и методы ее повышения
.pdfГазовое и вакуумное борирование разработано в 50-х годах ны нешнего столетия. В настоящее время технология насыщения стали бором разработана достаточно хорошо и этот метод улуч шения свойств сталей начинает внедряться в промышленность.
В работах [48, 50, 56, 153] исследовалось влияние борирования на выносливость углеродистых сталей в различных средах. Результаты изучения усталостной прочности борированных об разцов показали (табл. 21), что порошковое контактное бориро вание примерно на 20% повышает предел усталости стали 45. Оптимальным режимом борирования, повышающим циклическую прочность стали 45 в воздухе и коррозионной среде, можно счи тать режим, обеспечивающий толщину диффузионного слоя по рядка 0,14—0,15 мм, т. е. при борировашш в течение 6 ч при 950° С.
Т а б л и ц а 21 Влияние борирования на предел усталости образцов стали 45
|
|
при |
Предел усталости |
пГ/мм1 |
|
|
|
базе 5хЮ' циклов, |
|||
|
Толщина |
гладкие образцы |
образцы с концентра |
||
Режны борирования |
диффузи |
||||
онного |
|
|
тором напряжения |
||
|
слоя, мм |
|
|
|
|
|
|
в воздухе |
в 3%-ном |
в воздухе |
в 3%-ном |
|
|
растворе |
растворе |
||
|
|
|
NaCl |
|
NaCl |
950" С, 3 ч |
0,10 |
30,5 |
8,0 |
20,0 |
3,5 |
950° С, 6 ч |
0,15 |
31,0 |
10,0 |
19,0 |
3,5 |
950° С, 10 ч |
0,19 |
30,0 |
10,0 |
21,5 |
4,0 |
Без борирования |
|
25,5 |
5,0 |
10,0 |
2,5 |
Условный предел коррозионной усталости стали 45 после бо рирования в порошках увеличивается в два раза дл я образцов
с |
толщиной |
покрытия 0,15 и 0,19 |
мм и в 1,6 раза — для образцов |
|
с |
толщиной |
слоя 0,1 мм, причем |
время до разрушения в области |
|
больших |
амплитуд напряжений увеличивается в 4—5 раз . С уве |
|||
личением |
толщины диффузионного слоя время до разрушения |
|||
в области |
больших амплитуд напряжений возрастает, что же ка |
сается условного предела коррозионной усталости, то оптималь ной толщиной слоя, обеспечивающей наибольшую выносливость, также является толщина слоя боридов 0,14—0,15 мм.
Борирование углеродистых сталей, содержащих различное ко личество углерода (0,21—0,83%), приводит к повышению предела усталости на 20—25%, причем эффект упрочнения несколько мень ше на стали с меньшим содержанием углерода. При одном и том же времени насыщения (в течение 6 ч) наибольшим условным пределом коррозионной усталости обладают образцы из стали 45, хотя время до разрушения в области высоких амплитуд на пряжений возрастает с увеличением содержания углерода в стали. Б о л ь ш у ю ограниченную выносливость стали У8 , по-видимому,
123
можно объяснить тем, что углерод, замедляя скорость диффузии бора в сталь, способствует получению более плотных и равномер ных слоев.
Б о р и р о в а н н а я среднеуглеродистая сталь после закалки и ни зкого отпуска имеет примерно в четыре раза меньший предел
усталости по |
сравнению с закаленной сталью без покрытия |
и в |
|||||||||||||||||
|
|
|
|
|
|
два |
раза |
по сравнению с борирован- |
|||||||||||
|
|
|
|
|
|
ной сталью без закалки |
(рис. 62). |
Это |
|||||||||||
|
|
|
|
|
|
явление |
можно |
объяснить |
|
наличием |
|||||||||
|
|
|
|
|
|
большого числа трещин, возникаю |
|||||||||||||
|
|
|
|
|
|
щих |
в |
слое вследствие |
различных |
||||||||||
|
|
|
|
|
|
коэффициентов |
линейного |
расшире |
|||||||||||
|
|
|
|
|
|
ния слоя и основного металла, а также |
|||||||||||||
|
|
|
|
|
|
отсутствием |
остаточных напряжений |
||||||||||||
|
|
|
|
|
|
сжатия |
из-за примерно равного |
||||||||||||
|
|
|
|
|
|
удельного объема мартенсита основ |
|||||||||||||
|
|
|
|
|
|
ного металла и боридов при нор |
|||||||||||||
|
|
|
|
|
|
мальной |
температуре. |
Борирование |
|||||||||||
|
|
|
|
|
|
с последующей закалкой и высоким |
|||||||||||||
|
|
|
|
|
|
отпуском |
снижает |
предел |
|
усталости |
|||||||||
|
|
|
|
|
|
на 20% по сравнению |
со сталью |
без |
|||||||||||
|
|
|
|
|
|
покрытия в таком же структурном |
|||||||||||||
|
|
|
|
|
|
состоянии, а по сравнению с бориро- |
|||||||||||||
|
|
|
|
|
|
ванной сталью без закалки предел |
|||||||||||||
|
|
|
|
|
|
усталостной |
прочности |
увеличива |
|||||||||||
0,05 |
|
0,51 |
5 Ю И,млн. |
ется |
на |
20%. |
Некоторое |
|
снижение |
||||||||||
Рис. 62. |
Кривые |
усталости |
предела |
усталости |
можно |
|
объяснить |
||||||||||||
наличием трещин |
в слое |
по |
указан |
||||||||||||||||
(1—4) |
и |
коррозионной |
уста |
||||||||||||||||
лости (/—IV) образцов из |
ста |
ным |
ранее |
причинам. |
Однако |
бла |
|||||||||||||
ли 45 без покрытия (1,3,1, |
III) |
годаря |
|
значительным |
остаточным |
||||||||||||||
и борированной |
(2, |
4, II, |
IV): |
напряжениям сжатия |
в слое, |
дости |
|||||||||||||
1,2,1, |
11 |
— закалка, |
низкий от |
||||||||||||||||
гающих |
около |
80 |
кГ 1мм2, |
|
а |
также |
|||||||||||||
пуск; S, 4, |
I I I , IV |
— закалка, вы |
|
||||||||||||||||
сокий отпуск. |
|
|
|
меньшей чувствительности сорбитной |
|||||||||||||||
структуры основного металла по сравнению |
с мартенситной к |
||||||||||||||||||
концентраторам |
напряжений (трещины |
в слое) снижение |
предела |
||||||||||||||||
усталости не так заметно, как в случае закалки и низкого |
отпуска. |
||||||||||||||||||
Условный |
предел коррозионной усталости после закалки |
и |
от |
||||||||||||||||
пуска (как низкого, так и высокого) увеличивается |
несущественно |
||||||||||||||||||
(см. рис. 62). Однако время до разрушения при высоких |
ампли |
||||||||||||||||||
тудах |
напряжений по |
сравнению |
с |
борированной |
сталью |
без |
за |
||||||||||||
к а л к и |
(после |
вакуумного |
отжига) |
уменьшается |
примерно |
в |
5— |
||||||||||||
6 раз . М а л а я эффективность борирования с последующей |
закалкой |
я отпуском объясняется наличием закалочных трещин в слое по указанным ранее причинам, через которые проникает коррозион ная среда к основному металлу, что приводит к его коррозионноусталостному разрушению. При отсутствии трещин, но наличии микропор в диффузионном слое среда также проникает к основ ному металлу, однако процесс коррозионно-усталостного разру -
124
шения протекает менее интенсивно, чем в случае закалки и от пуска. Из сравнения кривых коррозионно-усталостной прочности борированной стали после закалки и низкого отпуска, где внут ренние напряжения практически отсутствуют, и после з а к а л к и и высокого отпуска, где напряжения сжатия высоки, видно, что
при |
наличии |
трещин |
в |
хрупком |
диффузионном |
слое |
остаточные |
||||||||||||
н а п р я ж е н и я сжатия не оказывают существенного |
в л и я н и я |
на |
|||||||||||||||||
условный предел коррозионной усталости борированной |
стали. |
||||||||||||||||||
После электролизного борирования, проведенного по обычной |
|||||||||||||||||||
технологии |
(с |
охлаждением |
на воздухе), |
предел |
усталости |
оста |
|||||||||||||
ется |
на |
|
уровне |
образцов |
|
|
|
|
|
|
|
|
|
|
|
||||
без покрытия (рис. 63), |
|
|
|
|
|
|
|
|
|
|
|
||||||||
однако время до разруше |
|
|
|
|
|
|
|
|
|
|
|
||||||||
ния |
при |
амплитудах |
|
на |
|
|
|
|
|
|
|
|
|
|
|
||||
пряжений, |
близких к пре |
|
|
|
|
|
|
|
|
|
|
|
|||||||
делу |
усталости, |
уменьша |
|
|
|
|
|
|
|
|
|
|
|
||||||
ется в 3—4 раза. Это объяс |
|
|
|
|
|
|
|
|
|
|
|
||||||||
няется |
тем, что |
после |
на |
|
|
|
|
|
|
|
|
|
|
|
|||||
сыщения |
и |
последующего |
|
|
|
|
|
|
|
|
|
|
|
||||||
охлаждения |
|
на |
воздухе |
|
|
|
|
|
|
|
|
|
|
|
|||||
диффузионный |
слой |
пок |
|
|
|
|
|
|
|
|
|
|
|
||||||
рывается |
сеткой |
трещин, |
|
|
|
|
|
|
|
|
|
|
|
||||||
часто не видимых |
снаружи |
|
|
|
|
|
|
|
|
|
|
|
|||||||
(обнаружено при |
последо |
|
|
|
|
|
|
|
|
|
|
|
|||||||
вательном |
|
стравливании |
|
|
|
|
|
|
|
5 |
10 И,млн. |
||||||||
слоя боридов), хотя оста |
|
|
|
|
|
|
|
5 |
|
|
|
||||||||
точные |
напряжения |
сжа |
Рис. 63. Кривые усталости (а) и коррози |
||||||||||||||||
тия в слое достигают зна |
онной |
усталости |
(б) |
|
гладких |
образцов |
|||||||||||||
чительной |
величины |
(при |
(1—3) |
и |
образцов |
с |
концентраторами |
на |
|||||||||||
близительно |
50 |
кГ/мм2). |
пряжений |
(I—III) |
|
из |
стали |
45 |
после |
||||||||||
электролизного |
борирования: |
|
|
|
|||||||||||||||
По-видимому, эти трещины |
1, I — без |
покрытия; |
2, |
II |
— борирование, |
||||||||||||||
предопределяют |
место |
за |
охлаждение |
замедленное; 3, III |
— борирование, |
||||||||||||||
рождения и развития |
уста |
охлаждение на воздухе. |
|
|
|
|
|
|
|||||||||||
|
|
|
|
|
|
|
|
|
|
|
лостного излома. Более медленное охлаждение после насыщения, которое, по нашему мнению, должно было резко уменьшить коли
чество трещин вследствие релаксации |
напряжений, возникающих |
в слое, а также вследствие меньшего |
температурного градиента, |
действительно повысило предел усталости на 10—15% (см. рис. 63).
Условный предел коррозионной усталости стали после электро лизного борирования увеличивается в 1,6—1,8 раза по сравнению со сталью без покрытия и находится на уровне прочности после порошкового контактного борирования с такой же толщиной слоя боридов.
Электролизное борирование стали 38XG снижает ее предел усталостной прочности на 25% по сравнению с нормализованными или ложноборированными образцами без покрытия [37, 82]. Изо термическая закалка этой стали после борирования уменьшает предел усталостной прочности на 46% по сравнению со сталью
125
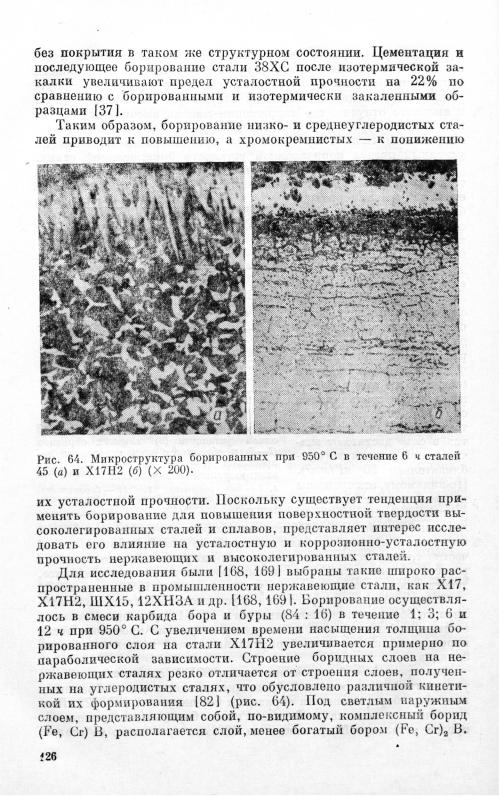
П овы ш е нн ая травимость зоны под боридным слоем обусловлена, очевидно, обогащением ее углеродом, оттесненным с поверхности стали, который, связывая частично хром, уменьшает его коли
чество в твердом растворе. Увеличение толщины боридных |
слоев |
||
выше 0,10—0,12 мм приводит к |
разрушению слоя и местному |
||
отслоению наиболее богатой бором зоны (Fe, Сг) В. |
Максимальная |
||
микротвердость боридных слоев на указанных нержавеющих |
ста |
||
л я х составляет 2200—2350 кГ/мм2. |
Результаты исследований по |
||
казали, что борирование при 950° С на глубину |
0,05—0.06 |
мм |
примерно на 10% повышает предел усталостной прочности п почти
в два раза увеличивает условный предел кор- |
|
|||||||||||
розионно-усталостной |
прочности |
стали Х17 |
|
|||||||||
при чистом круговом изгибе (рис. 65). |
|
|||||||||||
Совершенно иначе влияет борирование на |
|
|||||||||||
изменение |
|
циклической |
прочности |
стали |
|
|||||||
Х 1 7 Н 2 , предел |
|
усталостной |
прочности кото |
|
||||||||
рой резко снижается с увеличением |
времени |
|
||||||||||
борирования . |
При |
наличии |
слоя |
толщиной |
|
|||||||
0,1—0,12 |
мм предел |
усталостной |
прочности |
|
||||||||
в три раза |
меньше, |
чем у ложноборирован- |
|
|||||||||
ной стали. В коррозионной среде |
|
(3%-ный |
|
|||||||||
раствор NaCl) усталостная прочность стали |
|
|||||||||||
после борирования также снижается, однако |
|
|||||||||||
Рис. 65. Кривые усталости в воздухе |
(1—5) и |
|
||||||||||
3%-ном растворе |
|
NaCl |
(I—V) |
образцов |
из стали |
|
||||||
Х17Н2 {1—3, I—III) |
и Х17 (4, 5, IV, V). |
Отжиг при |
|
|||||||||
950° С (1, 4, I, |
IV) |
и борирование прп 950° С в тече |
|
|||||||||
ние 6 ч (3, 5, |
III, |
|
V) и 3 ч (2, |
II). |
|
0,1 0,51 |
5 N, |
|||||
|
|
|
|
|
|
|
|
|
|
|
||
толщина |
слоя |
в этом случае значительно меньше сказывается на |
||||||||||
величине условного |
предела |
коррозионно-усталостной |
прочности. |
|||||||||
Различное |
влияние |
борирования |
на циклическую |
прочность |
сталей Х17 и Х17Н2 можно объяснить различным строением диф фузионного слоя на этих сталях. Слой на стали X I 7 отличается равномерностью, в то время как на стали Х 1 7 Н 2 под основным бо ридным слоем происходит избирательная диффузия элементов по границам зерен. Это создает своего рода структурные концентра торы напряжений, являющиеся одной из основных причин отри цательного влияния борирования на усталостную и коррозионно-
усталостную прочность стали Х17Н2 . Кроме того, |
стали Х17Н2 |
|||||||
обладают |
более |
высокой |
чувствительностью |
к |
концентрации, |
|||
чем |
сталь |
Х17. Автор данной монографии совместно с В. Г. Про- |
||||||
циком |
исследовал |
влияние |
легирования среднеуглеродистой ста |
|||||
ли |
хромом, |
никелем,, марганцем, |
кремнием в |
количестве до 5% |
||||
на |
строение диффузионного |
слоя и |
коррозионную |
выносливость |
||||
после |
борирования (рис. 66). |
|
|
|
В связи с тем, что большинство деталей машин имеет разные конструктивные и технологические концентраторы напряжений,
127
в работе [82] изучено влияние диффузионных покрытий на цикли ческую прочность образцов с концентраторами напряжений . Ре зультаты испытаний образцов (теоретический коэффициент кон центрации напряжений аа = 3,22) с различной толщиной диффу зионного слоя (0,10; 0,15; 0,19 мм) показали (см. табл. 21), что после порошкового контактного борирования предел усталости увеличивается примерно в два раза по сравнению с образцами без покрытий. При этом наблюдается тенденция незначительного уве личения предела усталости с ростом толщины диффузионного слоя. Исследования борированной стали 45 (толщина слоя 0,15 мм) с концентраторами напряжений, имеющими различные радиус
закругления дна надреза (0,2; 1,0 и 5,0 мм) и теоретический |
коэф |
|||||||||||||
|
|
|
|
|
|
|
фициент |
концентрации |
на |
|||||
|
|
|
|
|
|
|
пряжений |
(3,22; 1,78 |
и |
1,21), |
||||
|
|
|
|
|
|
|
показали, |
что с |
увеличением |
|||||
|
|
|
|
|
|
|
коэффициента |
концентрации |
||||||
|
|
|
|
|
|
|
напряжений предел усталости |
|||||||
|
|
|
|
|
|
|
повышается. Значение коэф |
|||||||
|
|
1 2 |
3 |
Ц |
5 |
5,5 |
фициента упрочнения в ре |
|||||||
|
|
|
Легкие |
элементы, |
% |
зультате |
борирования |
сни |
||||||
Рис. 66. Влияние легирования на услов |
жается |
с |
уменьшением |
зна |
||||||||||
ный |
предел |
коррозионной |
усталости |
чения |
коэффициента |
концен |
||||||||
неборированной (штриховые |
кривые) и |
|||||||||||||
трации напряжений, |
|
прибли |
||||||||||||
борированной |
при 950° С в течение 6 ч |
|
||||||||||||
(сплошные кривые) стали с различным |
ж а я с ь |
|
к |
коэффициенту |
||||||||||
содержанием марганца (1), кремния (2), |
упрочнения гладких |
образ |
||||||||||||
хрома (3) |
и никеля (4). |
|
|
|
цов. Наблюдающаяся некото |
|||||||||
р а я |
разница в коэффициенте упрочнения для |
образцов, |
имеющих |
|||||||||||
радиус закругления дна концентратора 0,2 и 1,0 мм, |
объясняется |
|||||||||||||
различием в толщине диффузионного слоя у дна надреза, |
обуслов |
|||||||||||||
ленная |
спецификой |
диффузионного |
насыщения [82]. Значитель |
|||||||||||
ная |
разница |
в коэффициенте |
упрочнения для гладких |
и |
надре |
занных образцов в результате диффузионного борирования свя зана с различием в эпюрах напряжений, возникающих от действия внешней нагрузки. Действие остаточных сжимающих напряжений создает на гладких образцах асимметрию цикла (при действующем симметричном цикле нагружения) только лишь для поверхностных
слоев, нейтрализуя незначительную часть действующих |
напря |
жений. Остаточные н а п р я ж е н и я в зоне концентратора, |
близкие |
по величине градиента к напряжениям от внешней нагрузки, по зволяют, если не полностью, то в достаточно большей степени разгрузить наиболее опасное сечение образца. Именно этим объяс няется высокая эффективность борирования для образцов с кон центраторами напряжений . Предел усталости образцов с концент ратором напряжений после борирования увеличивается примерно в два раза .
Предел усталости надрезанных образцов после электролизного борирования примерно на 10% ниже, чем после порошкового контактного, что связано с некоторым ростом зерна сердцевины
128
после насыщения, так |
как |
после |
электролизного |
борирования |
вакуумный отжиг не проводился. |
|
|||
Результаты исследований остаточных напряжений после бо |
||||
рирования показали, что в |
стали |
после насыщения |
в течение 3, |
|
6 и 10 ч и последующего |
вакуумного отжига в поверхностном слое |
действуют осевые остаточные сжимающие напряжения 1-го рода ве
личиной 55—70 кГ/мм2. |
Максимального значения в данном случае |
||||||
достигают внутренние |
напряжения |
у стали, борированной |
в |
те |
|||
чение 6 ч (толщина слоя 0,15 мм). |
Увеличение толщины слоя |
до |
|||||
0,19 |
мм снизило, как |
и следовало |
ожидать, максимальное значе |
||||
ние |
остаточных напряжений, а изменение их знака |
имело |
мест) |
||||
на большей глубине, нежели у стали с толщиной слоя 0,15 |
|
мм. |
|||||
Уменьшение толщины |
слоя до 0,1 |
мм |
с учетом общих |
положений |
о влиянии толщины диффузионного слоя на величину и характер распределения остаточных напряжений должно было бы увели чить максимальное их значение, однако нами наблюдалась обрат ная картина. Такое отклонение во влиянии толщины слоя на характер распределения остаточных напряжений вызвано спе
цифичным иглообразным |
строением диффузионного |
слоя. При |
этом за сравнительно короткий промежуток времени |
насыщения |
|
не возникает, вероятно, |
сплошной слой боридов FeB |
на поверх |
ности. Поэтому наличие таких относительно «мягких» участков без боридов FeB приводит к частичной компенсации остаточных
напряжений сжатия |
за счет релаксации их на этих |
участках. |
Из сопоставления |
результатов по определению |
усталостной |
прочности и остаточных напряжений видно, что для образцов с раз личной толщиной боридного слоя величина и характер распре деления остаточных напряжений по глубине слоя практически не оказывают влияния на величину предела усталости. В то же время из сопоставления литературных данных по остаточным напряже ниям, возникающим в результате насыщения стали углеродом, азотом или после обкатки с соответствующими пределами уста лости, следует, что эффективность борирования, несмотря на вы сокие остаточные напряжения, весьма низкая по сравнению с упо мянутыми методами упрочнения. Это позволяет сделать вывод, что величина остаточных напряжений не является единственным определяющим фактором в повышении предела усталости. Д л я оценки влияния того или иного вида упрочнения необходимо учи тывать строение диффузионного (или упрочненного) слоя, характер сцепления его с основным металлом, когерентность решетки диф фузионного слоя, его прочность, пластичность, твердость, хруп кость и другие параметры. Сравнительно малый эффект упрочне ния после борирования, по-видимому, объясняется большой хруп
костью, |
а также |
спецификой |
строения диффузионного |
слоя, |
бориды |
которого в виде игл глубоко внедряются в основной |
металл |
||
и выполняют роль |
структурных |
концентраторов напряжений. |
На величину и характер распределения остаточных напря жений в борированных сталях большее влияние оказывает
9 |
3—1220 |
129 |
последующая термическая обработка, которая, мало влияя на изме нение свойств самого слоя, существенно изменяет структуру сердце вины, что приводит к перераспределению остаточных напряжений . Так, например, закалка с низким отпуском благодаря резкому увеличению удельного объема сердцевины (отпущенный мартенсит) практически полностью устраняет остаточные напряжения . При закалке и высоком отпуске, а также вакуумном отжиге величина и характер распределения остаточных напряжений изменяются незначительно.
Из сравнения результатов определения остаточных напряже ний и циклической прочности видно, что закалка с высоким от пуском несущественно изменяет максимальное значение остаточ
ных |
напряжений по сравнению |
с вакуумным отжигом, но |
приво |
|||
дит к заметному повышению выносливости, которое |
можно было бы |
|||||
отнести за счет |
упрочнения сердцевины. |
Однако закалка |
с низ |
|||
ким |
отпуском, |
в значительно |
большей |
степени |
повышающая |
|
прочность стали без покрытия, вызвала резкое снижение |
предела |
усталостной прочности борированной стали. Причина такого влия ния термообработки на выносливость борированной стали заклю
чается, по-видимому, в различной |
чувствительности сердцевины |
|||
к концентрации напряжений . Так, возникшая в довольно |
хруп |
|||
ком диффузионном слое трещина, дошедшая до перлит-ферритной |
||||
или |
сорбитной структуры, |
менее |
опасна, чем когда она |
вхо |
дит в |
более чувствительную |
к концентраторам напряжений |
мар- |
тенситную структуру. |
Кроме того, не последнюю роль в изменении |
|||||
выносливости |
будет |
выполнять |
слой, |
обогащенный |
оттесненным |
|
с поверхности |
углеродом. |
|
|
|
|
|
При наличии концентраторов |
напряжений |
(ас т = |
3,22) услов |
|||
ный предел коррозионной усталости |
стали |
после |
борирования |
|||
(с различной |
толщиной диффузионного |
слоя |
0,1; 0,15; 0,19 мм) |
увеличивается на 40—00% по сравнению со сталью без покрытия (см. табл. 21). Время до разрушения в области высоких амплитуд напряжений у борированной стали увеличивается в 4—10 раз, причем большая цифра относится к образцам с большей толщиной диффузионного слоя. С уменьшением значения коэффициента концентрации напряжений от 3,22 до 1,78 условный предел кор розионной усталости увеличивается в два раза после борирования по сравнению со сталью без покрытия. При снижении значения коэффициента концентрации до 1,21 условный предел коррозион ной усталости остается примерно на уровне образцов после бори рования с а 0 = 1,78. Ограниченная выносливость при больших амплитудах напряжений после борирования увеличивается в 3—4 раза. Условный предел коррозионной усталости образцов с кон центраторами напряжений после электролизного борирования находится на уровне выносливости после порошкового контакт ного борирования с толщиной диффузионного слоя 0,1 мм, однако при замедленном охлаждении выносливость несколько выше по сравнению с образцами, охлажденными на воздухе.
130
Таким образом, условный предел коррозионной усталости с
концентраторами напряжений (аа = |
3,22) практически не зави |
|
сит от метода борирования. |
Н и з к а я |
эффективность борирования |
образцов с концентраторами |
напряжений при испытании в 3%-ном |
растворе NaCl объясняется некоторой пористостью диффузионного слоя, обусловленной меньшей толщиной слоя боридов в вершине концентратора, а также локализацией электрохимических про цессов в зоне концентратора.
5. Силицирование
Нами исследовалась усталостная прочность среднеуглеродистой стали, силицированной в порошковой смеси ферро силиция (30 вес. % ) , окиси алюминия (8—10 вес. % ) , хлористого аммония (10—12 вес. %) с добавкой кварцевого песка. Насыщение при температуре 900° С в течение 3 ч привело к образованию сравнительно плотных диффузионных слоев с толщиной нетравящейся (в 2%-ном растворе азотной кислоты) зоны 0,1—0,15 мм.
Предел усталости силицированной стали повышается на 15— 20% по сравнению с непокрытой сталью. З а к а л к а и последующий высокий отпуск способствуют еще большему повышению предела выносливости до 25—30%. Низкий отпуск закаленной силициро ванной стали снижает ее усталостную прочность.
Коррозионно-усталостная прочность стали после силицирования заметно повышается. При испытании в 3%-ном водном рас творе NaCl с частотой нагружения 50 гц на базе 20 млн. циклов предел усталости силицированной стали увеличился почти в три раза (с 5 до 14 кГ1ммг) по сравнению с непокрытой.
9*
Г Л А В А V I
ВЛИЯНИЕ ДИФФУЗИОННОЙ МЕТАЛЛИЗАЦИИ НА УСТАЛОСТНУЮ И КОРРОЗИОННО-УСТАЛОСТНУЮ ПРОЧНОСТЬ СТАЛЕЙ
Диффузионному насыщению изделий из сталей и сплавов различными металлами в последнее время придается большое значение, так как такой способ обработки может придать деталям новые физико-механические и электрохимические свой ства, улучшить их эксплуатационные характеристики. Диффузион ное насыщение порой бывает единственно возможным методом ре
шения |
той или иной |
технической задачи. |
|
|
|
Д л я |
повышения |
коррозионной |
стойкости |
часто |
используют |
диффузионные покрытия на основе |
цинка, хрома, алюминия, ти |
||||
тана, для повышения жаропрочности и жаростойкости |
— на основе |
||||
алюминия и хрома, а д л я повышения износостойкости |
— на основе |
||||
карбидов хрома, карбидов ванадия, |
нитридов |
титана |
и т. п. Спе |
циальные покрытия на основе диффузионной металлизации для повышения усталостной и коррозионно-усталостной прочности не разрабатывались. Однако с учетом того, что большинство дета лей в процессе эксплуатации подвергается комплексному воздей ствию ряда факторов, в том числе механических циклических нагрузок и коррозионных сред, часто существенно снижающему не сущую способность деталей вследствие проявления процесса кор
розионной усталости, важно иметь сведения о влиянии |
диффузион |
||||
ной металлизации на |
выносливость сталей в различных |
средах. |
|||
1. Хромирование |
|
|
|
|
|
Несмотря на то что |
подавляющее большинство |
деталей |
|||
машин и механизмов |
(особенно |
после диффузионного |
хромирова |
||
ния) работают в условиях одновременного воздействия |
цикличе |
||||
с к и х нагрузок и различных агрессивных сред, практически |
отсут |
||||
ствуют источники, посвященные изучению коррозионной |
усталости |
||||
диффузионно хромированных сталей [44, 95, 226]. |
|
|
|
||
В работах [41, 153, 165] исследовано влияние различных тем- |
|||||
пературно-временных |
режимов |
и методов диффузионного |
хроми |
||
рования на усталостную и коррозионно-усталостную |
|
прочность |
|||
углеродистых и нержавеющих |
сталей. |
|
|
|
132