
Учебная практика
.pdfжание кобальта в процентах, например, в сплаве ВК4 содержится 4 % кобальта, остальное − карбид вольфрама. В обозначении сплавов титановольфрамовой группы число после буквы Т показывает процентное содержание карбида титана, после буквы К − содержание кобальта. Например, в сплаве марки Т5К10 содержится 5 % карбида титана, 10 % кобальта и 85 % карбида вольфрама. В сплавах титанотанталовольфрамовой группы цифра после букв ТТ показывает суммарное содержание карбидов титана и тантала, а после буквы К − содержание кобальта. Например, в сплаве ТТ7К12 содержится 7 % карбидов титана и тантала, 12 % кобальта, остальное − карбид вольфрама. Твердые сплавы обладают высокой износостойкостью и теплостойкостью (до 1250 °С), что позволяет вести обработку со скоростями резания до 15 м/с. Они широко применяются для черновой и чистовой обработки труднообрабатываемых материалов, например, коррозионно-стойких и жаропрочных сталей.
Инструментальные керамические материалы можно разделить на три группы:
1)оксидная "белая" керамика, состоящая из Аl2O3 с легирующими добавками МgО, ZrO2 и др. Основные марки - ЦМ 332 и ВО-13. Они применяются для чистовой и получистовой обработки незакаленных сталей и серых чугунов со скоростями резания до 15 м/с;
2)оксидно-карбидная "черная" керамика (ВОК-60), состоящая из
Аl2O3 (до 60 %), ТiС (до 20−40 %), ZrО2 (до 20−40 %) и других карби-
дов тугоплавких металлов. Применяют для чистовой и получистовой обработки ковких, высокопрочных, отбеленных модифицированных чугунов и закаленных сталей;
3) керамика силинит Р на основе нитрида кремния с легированием оксидами иттрия, циркония, алюминия. Применяют для получистовой обработки чугунов.
Инструментальная промышленность выпускает инструментальные композиционные материалы на основе модификаций нитрида бора (эльбор, белбор, гексанит-Р, киборит и др.) Их применяют для обработки сталей и чугунов любой твердости, твердых сплавов в условиях безударной нагрузки.
К инструментальным сверхтвердым материалам относятся природные алмазы (А) и синтетические алмазы (АСО, АСР, АСВ и др.). Резцы с такими алмазными вставками применяют при тонком точении
41

деталей из сплавов алюминия, бронз, латуней, неметаллических материалов, полупроводниковых и керамических материалов. При использовании алмазных инструментов повышается качество поверхностей деталей. Обработку ведут со скоростями резания до 20 м/с.
По характеру обработки резцы делят на черновые, получистовые и чистовые. По направлению движения подачи резцы разделяют на правые (рис. 2.5, а) и левые (рис. 2.5, б). Правые работают с движением подачи справа налево, левые − слева направо.
По конструкции резцы делят на целые, с приваренной или припаянной пластиной из режущего материала, со сменными пластинами. По форме и расположению лезвия относительно стержня резцы подразделяют на прямые (рис. 2.5, а, 2.5, б), отогнутые (рис. 2.5, в), оттянутые (рис. 2.5, г) и изогнутые (рис. 2.5, д).
а) |
б) |
в) |
г) |
д) |
Рис. 2.5. Типы резцов:
а, б – прямые; в – отогнутый; г – оттянутый; д – изогнутый
По технологическому назначению резцы делят на: проходные − для обтачивания наружных цилиндрических и конических поверхностей, расточные − для растачивания глухих или сквозных отверстий, отрезные − для резания заготовок на части и протачивания канавок, резьбовые − для нарезания наружной и внутренней резьбы любого профиля, фасонные − для обтачивания фасонных поверхностей, подрезные − для обтачивания плоских торцевых поверхностей.
42

2.4. УСТРОЙСТВО И ПРИНЦИП РАБОТЫ ТОКАРНО-ВИНТОРЕЗНОГО СТАНКА
Наибольшее распространение ввиду своих исключительно широких технологических возможностей получили токарно-винторезные станки, отнесенные по классификации металлорежущих станков к шестому типу и имеющие в своем обозначении цифру 6, например, 1К62, 1М63, 16К20 и т. д.
Рис. 2.6. Общий вид токарно-винторезного станка:
1 – станина; 2 – передняя бабка; 3 – шпиндель; 4 – задняя бабка; 5 – пиноль; 6 – коробка подач; 7 – суппорт; 8 – резцедержатель; 9 – фартук;
10 – ходовой вал; 11 – ходовой винт
Все узлы токарно-винторезного станка (рис. 2.6) смонтированы на станине 1. Слева на станине жестко закреплена передняя бабка 2, в которой помещен механизм коробки скоростей. Коробка скоростей представляет собой многоскоростную зубчатую передачу с выходным валом (шпинделем) 3, на котором закрепляются обрабатываемые заготовки.
Справой стороны станины на специальных направляющих находится задняя бабка 4, в пиноли 5 устанавливаются концевые инструменты и вспомогательная оснастка. Шпиндель 3 и отверстие пиноли 5 расположены на общей оси, называемой линией центров.
Слевой стороны станины под коробкой скоростей закреплена коробка подач 6, многоскоростная зубчатая передача, передающая вращение ходовому валу 10 и ходовому винту 11. Между передней и задней бабками по направляющим станины перемещается суппорт 7, на котором находится резцедержатель 8.
43

Суппорт состоит из нижней каретки, обеспечивающей продольную подачу; поперечных (средних) салазок, обеспечивающих поперечную подачу; и верхних салазок, которые можно установить под любым углом относительно линии центров станка.
К продольному суппорту крепится фартук 9, механизм которого состоит из системы зубчатых колес, передающих вращение от ходового валика к реечной шестерне, которая, зацепляясь с закрепленной на станине рейкой, позволяет суппорту перемещаться в продольном направлении.
2.5. ЗАКРЕПЛЕНИЕ ЗАГОТОВОК И РЕЗЦОВ
Способы установки и закрепления заготовки, обрабатываемой на токарном станке, зависят от типа станка, вида обрабатываемой поверхности, характеристики заготовки (отношения длины заготовки к диаметру), точности обработки и других факторов.
На токарно-винторезных станках для закрепления заготовок с отношением длины к диаметру L / D < 4 широко используют трехкулачковые самоцентрирующие патроны (рис. 2.7, а).
б)
а)
в) |
г) |
д) |
|
Рис. 2.7. Приспособления для закрепления заготовок на токарных станках:
а – трехкулачковый самоцентрирующий патрон; б – упорный центр; в, г – поддерживающие люнеты; д – коническая оправка
44
На корпусе 1 патрона расположены три радиальных паза, по которым перемещаются кулачки 2. Закрепление заготовок с L/D > 4 в патронах производится с одновременной поддержкой центром задней бабки.
В зависимости от условий обработки применяют разные виды центров, например, упорный (рис. 2.7, б). Заготовки с L/D > 4 могут устанавливаться на центрах с передачей крутящего момента от шпинделя через поводковый самозажимный патрон или поводковый центр.
Для снижения деформаций при обработке маложестких заготовок (L/D > 10) используют поддерживающие люнеты подвижной (рис. 2.7, в) и неподвижной (рис. 2.7, г) конструкции. Для установки заготовок втулок, колец и стаканов широко используют оправки, простейшая из которых коническая (рис. 2.7, д).
Резцы закрепляются в резцедержателе двумя болтами строго на высоте центров станка и перпендикулярно к оси изделия. При этом вылет резца из резцедержателя не должен превышать 1,5 высоты державки резца. Регулировка по высоте производится специальными прокладками.
2.6. ТОКАРНЫЕ ОПЕРАЦИИ
На рис. 2.8 даны схемы обработки поверхностей заготовок на то- карно-винторезном станке. Наружные цилиндрические поверхности обтачивают прямыми (рис. 2.8, а) или упорными проходными резцами. Упорные проходные резцы с главным углом в плане ϕ = 90° удобно использовать для обработки нежестких ступенчатых валов. Наружные (рис. 2.8, б) и внутренние резьбы нарезают резьбовыми резцами, форма режущих кромок которых определяет профиль нарезанных резьб.
Точение длинных пологих конусов производят, смещая корпус задней бабки в поперечном направлении относительно ее основания (рис. 2.8, в) или используя специальное приспособление − конусную линейку. Сквозные отверстия на токарно-винторезных станках растачивают проходными расточными резцами (рис. 2.8, г), глухие − упорными (рис. 2.8, д).
С поперечным движением подачи на токарно-винторезных станках обтачивают кольцевые канавки прорезными резцами (рис. 2.8, ж), фасонные поверхности – фасонными стержневыми резцами (рис. 2.8, з), короткие конические поверхности (фаски) − широкими резцами, у которых главный угол в плане равен половине угла при вершине кони-
45

ческой поверхности (рис. 2.8, и). Отрезание деталей от заготовки выполняют отрезными резцами (рис. 2.8, к), подрезание торцов – специальными подрезными резцами (рис. 2.8, м).
Рис. 2.8. Схемы обработки поверхностей заготовок и типы резцов:
а, в, е, и – прямые проходные; б – резьбовой; г, д – расточной; ж – прорезной; з – фасонный; к – отрезной; л – сверло; м – подрезной
46
Обработку отверстий на токарно-винторезных станках выполняют сверлами (рис. 2.8, л), зенкерами и развёртками. В этом случае обработку ведут с продольным движением подачи режущего инструмента. Обтачивание наружных (рис. 2.8, е) и растачивание внутренних конических поверхностей средней длины с любым углом конуса при вершине на токарно-винторезных станках производят с наклонным движением подачи резцов при повороте верхнего суппорта.
2.7. ТЕХНИКА БЕЗОПАСНОСТИ ПРИ РАБОТЕ НА ТОКАРНЫХ СТАНКАХ
1.Следует проверить на холостом ходу станка следующее: исправность органов управления механизмами главного движения, подачи, пуска, остановки; исправность системы смазки и охлаждения.
2.Необходимо надеть защитные очки или предохранительный щиток из прозрачного материала при отсутствии специального защитного устройства.
3.Запрещается обслуживание станка в рукавицах или перчатках, а также с забинтованными пальцами без резиновых напальчников для предупреждения захвата рук рабочего вращающимися и движущимися узлами и деталями
4.Необходимо применять те режимы резания, которые указаны в операционной карте для данной детали.
5.При закреплении детали в кулачковом патроне или при использовании планшайбы следует закреплять деталь на возможно большую длину. Не допускать, чтобы кулачки после закрепления детали выступали за пределы наружного диаметра патрона или планшайбы.
6.Запрещается придерживать рукой отрезаемый конец при отрезании части детали или заготовки большой массы.
7.Запрещается тормозить руками вращающиеся части станка и детали в процессе остановки станка. Запрещается производить замеры на вращающейся детали.
8.Устанавливать и снимать режущий инструмент следует только после полной остановки станка.
9.Необходимо своевременно удалять стружку со станка и из рабочей зоны, используя для этих целей специальные крючки и щеткисметки. Недопускатьнаматываниястружкинаобрабатываемуюдеталь.
10. Запрещается обдувать сжатым воздухом обрабатываемую деталь и станок. Производить удаление стружки и чистку станка необходимо при отключении его от сети и полной остановки всех рабочих органов.
11. Трущиеся части станка следует смазать.
47
2.8.КОНТРОЛЬНЫЕ ВОПРОСЫ
1.Что такое обработка металлов резанием?
2.Какие поверхности различают на обрабатываемой заготовке?
3.Что такое режим резания, как его определить?
4.Как классифицируют резцы?
5.Основные узлы токарного станка и их назначение.
6.Способы закрепления заготовок на токарных станках.
7.Основные токарные операции.
8.Тип резца для обработки длинных нежестких валов.
9.Способы обработки отверстий на токарных станках.
10.Растачивание ступенчатых и глухих отверстий.
11.Способы обработки наружных конических поверхностей.
48
3. ОБРАБОТКА ЗАГОТОВОК НА СВЕРЛИЛЬНЫХ СТАНКАХ
3.1. ОБЩИЕ ПОЛОЖЕНИЯ
Сверлильные станки предназначены для сверления и рассверливания отверстий, нарезания в них резьбы, зенкерования, зенкования, цекования, притирки отверстий и т. п.
Вертикально-сверлильные станки применяют для обработки отверстий в деталях сравнительно небольшого размера.
Модель 2А125 расшифровывается следующим образом: цифра 2 означает, что станок относится ко второй группе, т.е. сверлильный; буква А – модернизированный; цифра 1 указывает на принадлежность станка к первому типу токарных станков – вертикальный; цифра 25 – наибольший диаметр сверления 25 мм (технический параметр станка).
При сверлении главным движением является вращательное движение инструмента, а движением подачи – поступательное движение инструмента вдоль оси.
Общий вид вертикально-сверлильного станка показан на рис. 3.1. Станина 3 имеет вертикальные направляющие, по которым перемещается стол 2 и шпиндельная бабка 5, несущая шпиндель 4. На шпиндельной бабке расположены электродвигатель 15, механизмы привода главного движения и подач, механизм включения и отключения вращения шпинделя и органы управления. Управление коробками скоростей и подач осуществляется рукоятками 7, 16; ручная подача – штурвалом 8. Глубину обработки контролируют по лимбу 10. Фундаментная плита 1 служит опорой станка. Стол 2 перемещают по на-
правляющей станины 3.
3.2. РЕЖИМЫ РЕЗАНИЯ
Глубина резания t при растачивании и рассверливании определяется по формуле
t = (D – d)/2,
где D – наибольший диаметр касания инструмента с деталью, мм; d – наименьший диаметр касания инструмента с заготовкой, мм. При сверлении
t = D/2,
где D – диаметр отверстия, мм.
Глубина резания принимается в зависимости от величины припуска. Рекомендуется вести обработку за один проход. Минимальное число проходов определяется мощностью станка, жёсткостью детали и заданной точностью обработки.
Подачей S называют путь точки режущего лезвия инструмента относительно заготовки в направлении движения подачи за один оборот
49
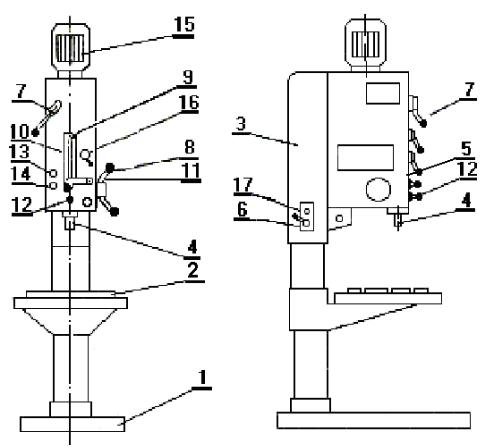
инструмента. При сверлильных работах подача имеет размерность
мм/об.
Скорость резания V для сверлильных станков рассчитывается по формуле
V = π D п/1000,
где D – диаметр сверла, мм; п – частота вращения инструмента, об/мин; 1000 – коэффициентпереводамиллиметроввметры; π= 3,14.
Рис. 3.1. Схема вертикально-сверлильного станка:
1 – плита; 2 – стол; 3 – станина; 4 – шпиндель; 5 – шпиндельная бабка; 6 – рукоятка включения двигателя; 7 – вариатор скоростей; 8 – штурвал; 9 – рукоятка установки глубины сверления; 10 – лимб глубины обработки; 11 – рукоятка включения самохода; 12 – рукоятка для выбивания инструмента; 13 – гнездо для подъёма и опускания шпиндельной бабки; 14 – гнездо для закрепления шпиндельной бабки; 15 – электродвигатель; 16 – рукоятка скорости подачи;
17 – контрольная лампочка
3.3. НАСТРОЙКА И НАЛАДКА СТАНКА
50